热轧板材质量缺陷分析
热轧质量缺陷及产生原因
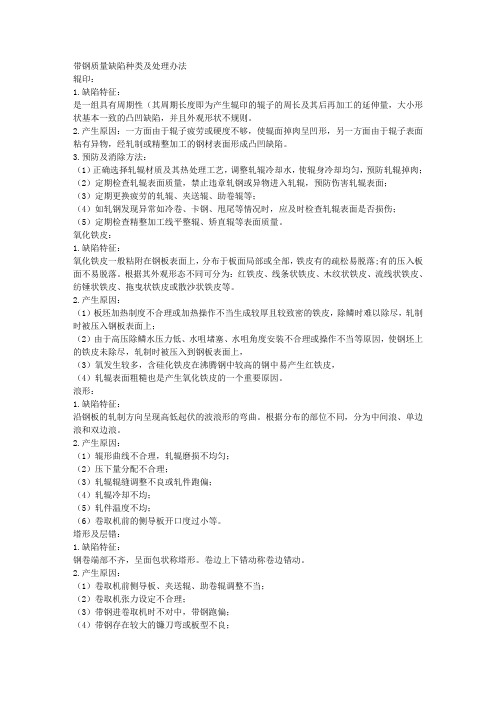
带钢质量缺陷种类及处理办法辊印:1.缺陷特征:是一组具有周期性(其周期长度即为产生辊印的辊子的周长及其后再加工的延伸量,大小形状基本一致的凸凹缺陷,并且外观形状不规则。
2.产生原因:一方面由于辊子疲劳或硬度不够,使辊面掉肉呈凹形,另一方面由于辊子表面粘有异物,经轧制或精整加工的钢材表面形成凸凹缺陷。
3.预防及消除方法:(1)正确选择轧辊材质及其热处理工艺,调整轧辊冷却水,使辊身冷却均匀,预防轧辊掉肉;(2)定期检查轧辊表面质量,禁止违章轧钢或异物进入轧辊,预防伤害轧辊表面;(3)定期更换疲劳的轧辊、夹送辊、助卷辊等;(4)如轧钢发现异常如冷卷、卡钢、甩尾等情况时,应及时检查轧辊表面是否损伤;(5)定期检查精整加工线平整辊、矫直辊等表面质量。
氧化铁皮:1.缺陷特征:氧化铁皮一般粘附在钢板表面上,分布于板面局部或全部,铁皮有的疏松易脱落;有的压入板面不易脱落。
根据其外观形态不同可分为:红铁皮、线条状铁皮、木纹状铁皮、流线状铁皮、纺锤状铁皮、拖曳状铁皮或散沙状铁皮等。
2.产生原因:(1)板坯加热制度不合理或加热操作不当生成较厚且较致密的铁皮,除鳞时难以除尽,轧制时被压入钢板表面上;(2)由于高压除鳞水压力低、水咀堵塞、水咀角度安装不合理或操作不当等原因,使钢坯上的铁皮未除尽,轧制时被压入到钢板表面上,(3)氧发生较多,含硅化铁皮在沸腾钢中较高的钢中易产生红铁皮,(4)轧辊表面粗糙也是产生氧化铁皮的一个重要原因。
浪形:1.缺陷特征:沿钢板的轧制方向呈现高低起伏的波浪形的弯曲。
根据分布的部位不同,分为中间浪、单边浪和双边浪。
2.产生原因:(1)辊形曲线不合理,轧辊磨损不均匀;(2)压下量分配不合理;(3)轧辊辊缝调整不良或轧件跑偏;(4)轧辊冷却不均;(5)轧件温度不均;(6)卷取机前的侧导板开口度过小等。
塔形及层错:1.缺陷特征:钢卷端部不齐,呈面包状称塔形。
卷边上下错动称卷边错动。
2.产生原因:(1)卷取机前侧导板、夹送辊、助卷辊调整不当;(2)卷取机张力设定不合理;(3)带钢进卷取机时不对中,带钢跑偏;(4)带钢存在较大的镰刀弯或板型不良;(5)卷取机卸卷时将钢卷头部拽出。
热轧工序典型质量缺陷产生原因与预防措施

预防措施
加强原材料质量检查,去除夹杂物;加强生 产过程控制,及时清除金属氧化物和其他夹 杂物。
03
热轧工序质量缺陷预防措施
提高原料质量
01
总结词:优化源头
02
详细描述:选用质量稳定的原料 ,控制原料的化学成分、物理性 能等指标,确保原料质量稳定, 为热轧工序打下良好的基础。
优化热轧工艺参数
要点一
热轧钢板内部存在气泡缺陷,影响产品质量和使用性能。
产生原因:熔炼和连铸过程控制不当、坯料加热时间过长或加热温度 过高、轧制速度过快。
预防措施:加强熔炼和连铸过程控制、合理控制坯料加热时间和温度 、降低轧制速度。
案例五:某钢厂热轧带钢表面翘曲预防措施
热轧带钢表面翘曲
产生原因:轧制温度和 冷却速度控制不当、坯 料厚度和成分不均。
案例三
01
热轧圆钢表面划痕
02
热轧圆钢表面存在划痕等缺陷, 影响产品外观和使用性能。
产生原因:轧辊表面损伤、坯料 表面质量差、冷却不均匀。
03
预防措施:检查和修复轧辊表面 损伤、加强坯料检查和加热控制
、调整冷却制度。
04
案例四:某钢厂热轧钢板内部气泡控制措施
01 02 03 04
热轧钢板内部气泡
01
02
03
04
热轧带钢表面存在翘曲 缺陷,影响产品平整度 和使用性能。
预防措施:合理控制轧 制温度和冷却速度、加 强坯料检查和控制。
THANK YOU
质量缺陷分类
根据缺陷的性质和产生原因,可 将热轧工序的质量缺陷分为材质 缺陷、工艺缺陷、设备缺陷和外 观缺陷等。
质量缺陷对产品的影响
影响使用性能
如强度、韧性等力学性能下降, 导致产品在使用过程中出现早期
热轧工序典型质量缺陷产生原因与预防措施
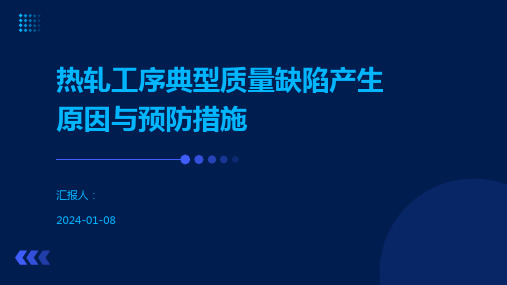
工艺参数设置不合理、工艺流程不完善等工艺因素是导致热轧工序质量缺陷的 重要原因。
详细描述
加热温度、轧制速度、道次压下量等工艺参数的设置对热轧产品的质量有显著 影响。工艺流程中的不合理之处,如冷却速度控制不当、轧制道次不足等,也 可能导致产品出现各种缺陷。
设备因素
总结词
设备故障、维护不当等设备因素是热轧工序中常见的质量缺 陷原因。
热轧工序典型质量缺陷产生 原因与预防措施
汇报人: 2024-01-08
目录
• 热轧工序简介 • 典型质量缺陷类型 • 产生原因分析 • 预防措施 • 案例分析 • 结论与展望
01
热轧工序简介
热轧工序的定义和重要性
定义
热轧工序是将金属材料在高温下 进行轧制的过程,目的是改变材 料的形状并获得所需的机械性能 。
钢材内部碳化物分布不均,导致钢材 性能不均一。
03
产生原因分析
原料因素
总结词
原料质量不均、成分偏析等原料因素 是导致热轧工序质量缺陷的主要原因 之一。
详细描述
原料的化学成分、微观组织结构、夹 杂物含量等因素可能影响热轧过程中 的流动性和变形行为,从而导致产品 出现裂纹、孔洞、夹杂等缺陷。
工艺因素
板形不良产生的原因可能是轧辊磨损严重、轧 制工艺参数设置不合理,或者是来料温度和厚 度波动过大。
厚度超差产生的原因可能是轧辊间隙调整不当 、轧制过程中张力控制不准确,或者是轧制润 滑条件不佳,导致金属流动不均匀。
预防措施实施效果评估
对于表面裂纹,通过优化轧制温 度和润滑条件,加强轧辊检查和 维护,可以显著减少裂纹的产生
2
针对这些质量缺陷,需要采取有效的预防措施, 如控制工艺参数、优化设备参数和加强质量检测 等。
热、冷轧板带材质量缺陷类别、原因及措施

1.粉末烧结板坯密度不均匀;2.由于热轧开坯时道次加工率小造成不均匀变形,致使产生分层,带入冷轧。3.中间退火不均匀。
1.保证板坯质量;2.控制好热轧工艺;3.改进退火工艺
10
针孔
由于环境卫生不好,粉尘颗粒落到轧件表面,轧制时致使压透箔材而形成微波孔眼
保持良好的环境卫生,加强文明生产。轧前坯料要认真清洗和检查
冷轧板、带材常见缺陷及消除方法
序号
缺陷名称
产生原因
消除方法
1
表面裂纹
1.来料表面裂纹未清除干净,冷轧时继续扩展;
2.来料表面脆性吸气层未清除,轧制时表面层与内层金属变形不一致,使表面被拉裂;
3.压下规程不合理,道次加工率过小,道次太多,使表面硬化太快,轧制时开裂;
4.道次加工率分配不均,造成严重地不均匀变形使局部拉裂。
11
表面粗晶和条状组织
经挤压、锻造的钼及其合金板坯,如果加工率不足或以后退火时,未能达到充分再结晶,轧时易出现此类缺陷
开坯时要给予足够的变形,提高退火温度或增长保温时间,使再结晶充分进行
12
厚度超差
1.量尺寸时不精确或量具不准确,误差过大;2.压下装置未调整好或指针不准确。
1.测量应细心,量具要准确;2.调整好压下装置,校正压下指针。
7
裂边
1.来料裂边未除净,轧制扩展了;2.冷轧加工率过大,边部被拉裂;
3.轧辊曲线配置不当;4.退火不均匀。
1.来料剪裂边要除净;2.调整压下规程;
3.配置好轧辊曲线;4.改进退火工艺。
8
表面起皮
1.道次加工率过小,轧制道次过多;
2.粉末烧结板坯,烧结密度偏低。
1.调整压下规程;2.保证板坯质量。
9
热轧带钢表面质量缺陷原因分析
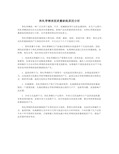
热轧带钢表面质量缺陷原因分析热轧带钢是一种广泛应用于建筑、汽车、机械制造等行业的金属材料。
在生产过程中,热轧带钢表面往往会出现各种质量缺陷,影响产品的质量和使用寿命。
对热轧带钢表面质量缺陷的原因进行分析,具有重要的理论和实际意义。
热轧带钢的表面质量缺陷主要包括:铁锈、麻粒、划痕、表面凹痕、擦伤、氧化皮等。
这些质量缺陷的产生原因多种多样,可以从以下几个方面进行分析:1. 原料质量不合格:热轧带钢的生产是通过将钢坯在高温条件下压延而成的,因此钢坯的质量对于热轧带钢的表面质量有着重要影响。
如果钢坯表面已经存在质量缺陷,如铁锈、氧化皮等,则在热轧过程中很容易形成对应的表面缺陷。
2. 设备状况和操作方式:热轧带钢的生产需要涉及到一系列设备,如热轧机、冷却装置等。
如果设备存在故障或者磨损,会导致带钢表面质量缺陷。
操作人员的技术熟练程度和操作方式也对热轧带钢的表面质量有着直接影响。
如果操作不规范或者技术水平不高,很容易导致带钢表面质量缺陷的产生。
3. 温度控制不当:热轧带钢的生产需要在一定的温度范围内进行。
如果温度控制不当,过高或者过低都会导致带钢表面质量缺陷的产生。
温度过高会导致带钢表面出现氧化皮、烧焦等问题,温度过低则会导致带钢表面出现裂纹等问题。
4. 轧辊磨损:热轧带钢的生产离不开轧辊的使用,轧辊磨损是导致带钢表面质量缺陷的一个重要因素。
轧辊的磨损会导致带钢表面出现凹凸不平、划痕等问题,直接影响产品质量。
5. 冷却方式选择不当:热轧带钢生产过程中,冷却方式的选择对于产品的表面质量有着重要的影响。
如果冷却方式选择不当,如冷却速度过快或者过慢,都会导致带钢表面质量缺陷的产生。
热轧带钢的表面质量缺陷产生原因是多方面的,需要从原料质量、设备状况和操作方式、温度控制、轧辊磨损以及冷却方式等方面进行综合分析和控制。
只有在整个生产过程中各个环节得到有效控制,才能够最大程度地减少热轧带钢表面质量缺陷的产生,提高产品质量和使用寿命。
热轧产品缺陷
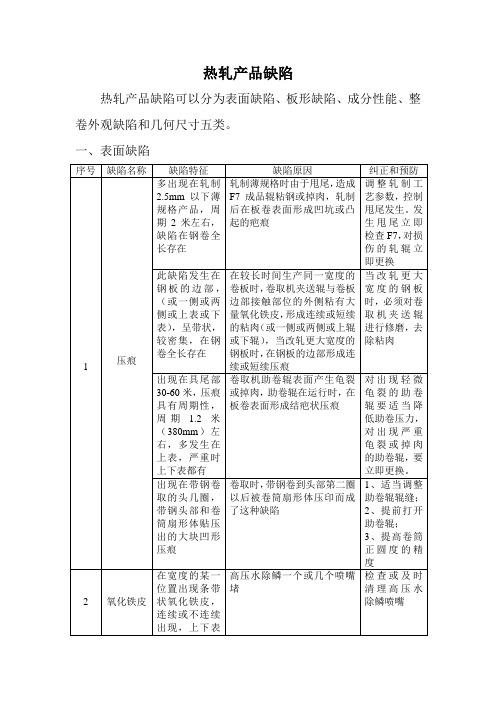
此缺陷发生在钢板的边部,(或一侧或两侧或上表或下表),呈带状,较密集,在钢卷全长存在
在较长时间生产同一宽度的卷板时,卷取机夹送辊与卷板边部接触部位的外侧粘有大量氧化铁皮,形成连续或短续的粘肉(或一侧或两侧或上辊或下辊),当改轧更大宽度的钢板时,在钢板的边部形成连续或短续压痕
1、卷取机前侧导板位置安装不当,使对带钢的导向出现偏差;
2、卷取机卷筒张紧过大,致使卷筒收缩后,卷筒与板卷内圈仍然紧紧接触,卸卷时将内几圈带出,形成塔形
1、定期检查更换侧导板;
2、优化卷取工艺操作。
15
松卷
卷板层与层之间出现较大缝隙,多出现在轧制厚规格产品当中
1、卷取速度、辊道速度的匹配出现偏差;
2、卷取张力出现大的波动;
划伤出现在卷板的下表面,发亮
1、精轧出口与卷取机之间、精整线上个别辊道运转不正常;
2、拆卷时带钢下表与地辊表面摩擦,下表面被划伤。
检查运输辊道的运转情况,及时排除故障
4
啃伤
只发生在拆卷的卷板外层,横向短长条,发亮,上下表均可能发生
主线拆卷时,地辊和压紧辊的作用下,发生层与层之间的错动啃伤。
1、及时更换地辊,保证两个地辊平衡
花纹的基板有明显的凸起与凹陷,呈鱼鳞状,沿板面分布
花纹板在卷取过程中,由于助卷辊压力过大,使内层花纹对外层板面有一个相当大的作用力,导致板面(基板)不平
1、降低卷取温度;
2、降低助卷辊压力,减轻助卷辊对板面饿作用力
三、整卷外观缺陷
序号
缺陷名称
缺陷特征
缺陷原因
纠正和预防
14
塔形
象塔一样的形状,多出现在轧制厚规格产品中
热轧板材质量缺陷及技术提升

热轧板材质量缺陷及技术提升摘要:热轧钢板是冶金领域一种非常重要的产品,其在船舶、汽车、家电制造业及建筑业等均有着大量的应用,其产品的品质对于各个领域运用质量的可靠性与安全性起到着决定性的影响。
伴随计算机技术的不断发展,运用计算机视觉技术,融合模式识别与数字图像处理技术达到热轧板材表面缺陷自动划分与辨别是目前研究的焦点问题。
关键词:热轧板材;质量;提升引言:近些年,随着我国轧钢技术及工艺的不断自主研发及应用,国内热轧生产工艺已取得突破性发展,热轧板材质量缺陷的原因分析更加精确,相关措施也越来越完善。
然而在实际生产过程中,成品质量还是不能完全达到理想标准。
这就要求我们对常见的热轧板材质量缺陷采取有效的控制措施,采用分类分析的方法,制定出系统的控制方案。
对缺陷的分类差别,可实现缺陷的快速分析,及时更好地控制板材质量。
1.热轧板材出现表面质量缺陷的原因1.1头尾流渣出现的原因钢坯火焰切割时用两个割枪从外到内切割,两个割枪不对中或者切割后头尾残留切割瘤,切割瘤在铸坯下线前不取毛刺时,头尾的切割瘤在粗轧轧制时压入中间坯上,进精轧机组前飞剪切头尾能切除一部分不能完全切净,有部分压延到成品上下表面或内部,冷轧再减薄时形成分层或翘皮,流渣严重影响成品表面质量。
1.2划伤现象出现的原因通过对划伤现象进行分析,可以得出大部分划伤缺陷都位于距轧板材两侧五十毫米的范围之内,其产生原因是由于对连铸坯进行宽度轧制工艺时,连铸坯的形状会发生变化,两侧会出现明显的隆起现象,随着压力的增大,隆起的高度会随着上升,当顶部和立辊凹环进行接触时,会出现压力增大的情况,从而导致二者出现接触划痕。
1.3侧翻现象出现的原因热轧板材的生产质量的决定因素为生产的工艺流程,对侧翻缺陷裂痕进行分析之后,可以发现缺陷的以下基本特点:缺陷为深度0.01到0.04毫米的沟槽状缺陷,缺陷处基本都会存在Fe2O3,可能的出现原因为粗轧立辊收缩量大连铸坯侧面的折皱由于侧翻现象到正面,留下了这部分氧化铁。
热轧质量缺陷及产生原因
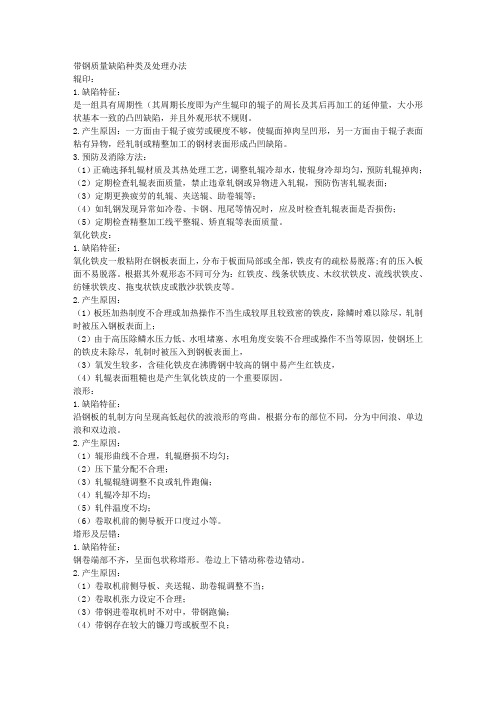
带钢质量缺陷种类及处理办法辊印:1.缺陷特征:是一组具有周期性(其周期长度即为产生辊印的辊子的周长及其后再加工的延伸量,大小形状基本一致的凸凹缺陷,并且外观形状不规则。
2.产生原因:一方面由于辊子疲劳或硬度不够,使辊面掉肉呈凹形,另一方面由于辊子表面粘有异物,经轧制或精整加工的钢材表面形成凸凹缺陷。
3.预防及消除方法:(1)正确选择轧辊材质及其热处理工艺,调整轧辊冷却水,使辊身冷却均匀,预防轧辊掉肉;(2)定期检查轧辊表面质量,禁止违章轧钢或异物进入轧辊,预防伤害轧辊表面;(3)定期更换疲劳的轧辊、夹送辊、助卷辊等;(4)如轧钢发现异常如冷卷、卡钢、甩尾等情况时,应及时检查轧辊表面是否损伤;(5)定期检查精整加工线平整辊、矫直辊等表面质量。
氧化铁皮:1.缺陷特征:氧化铁皮一般粘附在钢板表面上,分布于板面局部或全部,铁皮有的疏松易脱落;有的压入板面不易脱落。
根据其外观形态不同可分为:红铁皮、线条状铁皮、木纹状铁皮、流线状铁皮、纺锤状铁皮、拖曳状铁皮或散沙状铁皮等。
2.产生原因:(1)板坯加热制度不合理或加热操作不当生成较厚且较致密的铁皮,除鳞时难以除尽,轧制时被压入钢板表面上;(2)由于高压除鳞水压力低、水咀堵塞、水咀角度安装不合理或操作不当等原因,使钢坯上的铁皮未除尽,轧制时被压入到钢板表面上,(3)氧发生较多,含硅化铁皮在沸腾钢中较高的钢中易产生红铁皮,(4)轧辊表面粗糙也是产生氧化铁皮的一个重要原因。
浪形:1.缺陷特征:沿钢板的轧制方向呈现高低起伏的波浪形的弯曲。
根据分布的部位不同,分为中间浪、单边浪和双边浪。
2.产生原因:(1)辊形曲线不合理,轧辊磨损不均匀;(2)压下量分配不合理;(3)轧辊辊缝调整不良或轧件跑偏;(4)轧辊冷却不均;(5)轧件温度不均;(6)卷取机前的侧导板开口度过小等。
塔形及层错:1.缺陷特征:钢卷端部不齐,呈面包状称塔形。
卷边上下错动称卷边错动。
2.产生原因:(1)卷取机前侧导板、夹送辊、助卷辊调整不当;(2)卷取机张力设定不合理;(3)带钢进卷取机时不对中,带钢跑偏;(4)带钢存在较大的镰刀弯或板型不良;(5)卷取机卸卷时将钢卷头部拽出。
- 1、下载文档前请自行甄别文档内容的完整性,平台不提供额外的编辑、内容补充、找答案等附加服务。
- 2、"仅部分预览"的文档,不可在线预览部分如存在完整性等问题,可反馈申请退款(可完整预览的文档不适用该条件!)。
- 3、如文档侵犯您的权益,请联系客服反馈,我们会尽快为您处理(人工客服工作时间:9:00-18:30)。
热轧板材质量缺陷分析许国超2007-7-5摘要:在热轧厂,对于企业板材的轧制板材质量直接关系到经济利益,同时也是轧钢的水平的体现,轧制板材质量在各钢厂故十分重视,对于热轧板材的质量成因分析便十分必要,在经验及理论总结上,做出适当的分析十分必要的,本文是提供参考。
关键字:热轧板材板材缺陷板材质量热轧板材质量影响主要有以下几种:因近年来国家钢铁行业形势,热轧板材线也先后上了不少,预计未来的产能在板材中占有主导地位。
特别是先进的轧线应用不但大大提高了钢铁行业的整体装配水平,也提升了技术水平,缩短了与国外先进技术的差距,但是也为热轧工作的工人素质提出了更高的要求,对于掌握并吸收先进技术的程度也有了更高的要求。
对于轧制出的产品质量控制也有了更高的要求,热轧板材主要的质量问题有:卷形不良、氧化铁皮卷、折边、辊印、划伤、边裂、浪形、规格偏差、其他等。
1.卷形不良1.1塔形卷塔形卷是一种带钢边部卷绕不平齐,一处或多处呈螺旋状出边的不良卷形。
主要分为头塔和尾塔两种。
头塔是由于带钢头部偏离轧制中心线或2—3圈后从轧制中心线偏离导致的。
尾塔是由于带钢尾部偏离轧制中心线或2—3圈后从轧制中心线偏离导致的。
1.2塔形卷形成原因(1) 带钢自身原因来料镰刀弯、楔形、异常凸度以及波浪、气泡、头部温度低,材质硬度大等都容易产生头部塔形。
对策是要求精轧调压下水平,卷取操作方面应尽早打开助卷辊,(2)操作上的原因导板夹力过大,带钢弓起,运行不平稳,以及带钢中心偏离导板中心进入卷取机,对策是采用适当的夹紧力、夹紧方法,以及适当的导板开口度。
(3) 设备上的原因侧导板的部分松动以及动作不一致,夹紧力不足、侧导板偏心、下夹送辊不水平、夹送辊左右辊缝不平衡。
由于带钢尾部从精轧抛出时,带钢张力比正常状态低,因此,平时因为高张力而未能表现出来的使带钢横向移动的力就变得明显,使带钢横向移动后卷取,有时可以通过改变减速点来达到控制尾部张力。
1.3松卷松卷是指钢卷没有卷紧,处于松散状况的缺陷卷根据带钢的厚度、宽度、材质、卷取温度、卷取速度设定合适的张力。
1.4锯齿卷指整个钢卷的端面不规则大量出边2.氧化铁皮卷氧化铁皮是影响热轧带钢表面质量的重要因素之一,氧化铁皮压入的板材酸洗后,严重影响后工序冷轧板的表面质量,造成产品质量下降。
2.1 一次氧化铁皮钢坯表面与高温炉气生成的炉生氧化铁皮称为一次氧化铁皮, 一次氧化铁皮压入缺陷呈小斑点、大块斑痕和带状条纹形式不规则地分布在带钢上,常伴有粗糙的麻点状表面.2.1.1一次氧化铁皮压入产生的原因(1)加热方面的原因:加热温度高加热时间长;炉内气氛不好,供入风量过大;炉内形成负压,吸入冷风;炉内加热温度低于规程规定的最低温度过多。
在加热过程中,若出现上述情况的一种或数种,在出钢轧制时,氧化铁皮便会粘在钢坯、钢板上,不容易被清除掉,从而形成一次氧化铁皮压入缺陷。
(2)除鳞设备方面原因高压水压不足;喷嘴磨损严重,能力小;高压水嘴堵塞;高压水未能集中喷射到钢坯表面上;除鳞喷嘴(喷嘴角度)装配不当;喷射距离不佳;除鳞时序不当;设备投入不足。
(3)板坯化学成分的影响,如含硫、硅、铝过多这里主要是钢坯本身性质决定的,应该加强上一工序精炼及连铸水平(4) 生产指挥不当(5) 轧制计划安排不合理2.2二次氧化铁皮在轧制过程中表面氧化铁皮脱落,热的金属表面与水和空气接触,会生成新的氧化铁皮,称为二次氧化铁皮二次氧化铁皮呈颗粒状压入,分布多象分散的盐.2.2.1二次氧化铁皮压入产生的原因二次氧化铁皮产生的主要原因为开轧温度过高,除鳞时序不当,及精轧、粗轧除鳞设备(除鳞设备原因上同)原因。
无法高速轧制,在精轧机内进行轧制时间长,加快氧化铁皮的增长2.3轧辊磨损氧化铁皮在精轧机内由于轧辊的表面氧化形成的氧化铁皮称为轧辊磨损氧化铁皮。
轧辊磨损氧化铁皮呈黑褐色,小舟状,相对密集、细小、散沙状、细摸有手感。
2.3.1轧辊磨损氧化铁皮压入产生的原因⑴轧机在轧制过程中,出现辊面氧化膜剥落被碾入带钢表面;⑵剥落后的粗糙辊面对带钢表面产生类似犁沟作用,促进带钢自身表面氧化铁皮形成;⑶精轧机组每架或部分轧机之间无清除氧化铁皮装置。
(4)温度和机械疲劳造成工作辊表面微裂纹,会导致氧化铁皮的积累此外轧辊控制不当,比如轧辊落水、温度和机械疲劳造成工作辊表面微裂纹,会导致氧化铁皮的积累,这些氧化铁皮粘在轧辊上,然后传到并压在带钢表面上;有无使用轧制油轧制等等,都影响到氧化物的产生。
3. 规格偏差3.1宽度超差宽度超过标准范围(0—+20mm)从设备上看粗轧机组是决定宽度的基准,也是轧制中宽度变化最大的地方,在控制上良好一般超差不会在这里,粗轧机组各种工艺参数和设备参数的变动以及中间坯沿长度方向上尺寸、温度不同,都会引起带钢宽度的变化,立轧机是对宽度中的重要设备,现在一般是液压伺服控制,精度比较高,AWC控制技术也成熟。
精轧机组各种工艺参数和设备参数的变动以及中间坯沿长度方向上尺寸、温度不同,都会引起带钢宽度的变化。
精轧机组影响宽度变化的主要因素有:(1) 水平轧制矩形件引起的宽度增加。
由中间坯轧制成成品带钢, 随着厚度的不断减小, 必然要伴随着一定量的自然宽展。
(2) 精轧机架间张力引起的宽度减小。
带钢因宽厚比值很大, 轧制时对拉应力极为敏感, 易被过渡拉伸而变窄。
实践表明, 只要轧制时带钢的单位张力超过13~17M Pa, 带钢将出现明显的拉窄。
在精轧机组中, 由于各种因素造成的轧机速度不平衡和活套套量变化, 机架间张力都要发生波动, 从而引起宽度变化。
(3) 板凸度对宽度的影响。
板凸度变化时要伴随着一定量金属横向流动, 尤其是薄板,宽度随板凸度变化更加明显。
(4) 水印的影响。
沿板坯长度方向水印处的温度低, 与板坯其它部位的温差可达50~100℃。
由于水印处变形抗力大且板宽方向温差大, 使它在精轧机组水平轧制过程中宽展量增加。
(5) 当在精轧机组前设置小立辊时, 其宽度压下和随后的水平辊轧制将引起宽度变化。
精轧宽度自动控制技术是最新的热连轧宽度控制技术, 它是整个热连轧宽度控制系统的补充和完善。
在精轧宽度自动控制系统中, 机架间设置了测宽仪, 利用宽度变化预测模型估算机架出口宽度, 通过控制机架间的张力来调节各个机架的出口偏差。
该技术的应用大大地改进了带钢宽度精度, 有效地利用金属资源, 提高经济效益。
与防止边部减薄技术及轧连技术相结合, 可望实现生产无需切边的热轧带钢。
因此, 精轧宽度自动控制技术具有广阔地应用前景。
3.2厚度超差厚度超过标准范围(见标准)从设备上:AGC板厚自动控制是基于对板厚偏差大小和方向的估测,处理成消除厚度偏差所需要的校正信号,通过执行机构动作,达到所要求的厚度精度的过程。
调节量可以是辊缝、张力和轧制速度。
轧制过程中,影响板厚的主要因素有以下四大类:①辊系因素。
轧辊偏心、轧辊磨损、轧辊弯曲、轧辊热膨胀、油膜厚度变化等;②来料因素,来料厚度、宽度、硬度变化、轧制区摩擦系数变化;③轧制过程参数变化。
轧制力、张力、轧制速度的变化;④控制模型误差和检测仪表误差。
针对以上因素,发展出了以下几种AGC控制方式:反馈式、厚度计式、前馈式、直接辊缝检测式、张力式和秒流量计式等厚度自动控制系统。
可根据工艺需求选择或改进。
3.3长度偏差板坯尺寸误差、进入精轧机组前切头飞剪切头切尾过大,都会造成长度偏差。
4、板形问题通常指板带的平直度(波浪形和瓢曲)和凸度(横向厚度)4.1波浪形浪形分为边浪、中间浪、特殊浪形主要由于轧辊的热膨胀及轧辊本身的弹性变形边浪:轧辊中间呈凹形,易产生带钢侧边浪形(单边浪、双边浪)中间浪:轧辊中间呈凸形,易产生中间浪4.2 瓢曲带钢不同截面一边凸一边凹的变形,主要是由于钢板两侧冷却不均加上最后机架压延量过小造成。
4.3凸度指钢板中心轴线或者是凸峰处由于两侧的厚差。
影响热凸度的主要原因:1)当轧机停轧一段时间又重新开动时,在极端情况下轧辊没有热凸度,实际产生中虽然通常通过烫辊等措施使轧辊有一定的热凸度,但仍较稳定值小得多。
只有轧制数卷后,才形成热凸度。
2)如果某机架工作辊损坏,必须更换新辊,在极端情况下也没有热凸度。
3)不同产品常常要求由一种轧制规程变到另一种轧制规程,随之而来得是热凸度需要由一个稳定状态过渡到另一个稳定状态。
其一、张力改变对轧辊热凸度发生影响,特别是后张力影响更大,因而调整张力是控制板形的手段之一。
其二、张力对轧制压力发生影响,根据轧制理论,由于张力变化,特别是后张力变化,对轧制压力有很大影响,而轧制压力变化必然导致轧辊弹性变形发生变化,所以必然对板形产生影响。
其三、张力分布对金属横向流动发生影响。
这个问题今年来已引起人们的广泛注意。
研究表明,当张力沿横向分布不均时,会使金属发生明显的横向流动,即使对于板材轧制这种宏观看来近于平面变形的情况也是如此。
在一定的高向板形下,横向流动的结果必然改变横向的延伸分布,因而必然改变板带的板形。
与板形这一概念密切相关的另一个重要的概念是所谓的板凸度(Cro wn)。
热轧及冷轧板带材往往具有共同的特点,除板带边部外,90%的中间带材断面大致具有二次曲线的特征,而在接近边部处,厚度突然迅速减小,这种现象称为边部减薄(Edge dorp),其实质是钢板轧制时,宽度上的各处在厚度方向上不均匀压缩塑性变形,或由于带钢冷却不均而导致其在宽度方向上纤维产生不均匀延伸。
由于各纤维内部相互制约,形成了轧件内部的拉压应力,因而造成带钢不平,出现质量问题。
一般所指的板凸度,严格来说,是针对除去边部减薄区以外的部分。
边部厚度是以接近边部但又在边部减薄区以外的一点的厚度来代表,板凸度即为板中心处的厚度与边部代表点处的厚度之差。
5、辊印辊印主要是由于轧辊表面有缺陷而造成的。
主要有沾肉和掉肉两种(网纹也归入其中)。
辊印的判断主要是根据带钢表面的缺陷形状来进行的。
如果是有规律的缺陷(这里一般是缺陷的间隔长度一定),那么一般都是轧辊上产生的,再可以根据间隔的长度来判断是什么样的轧辊产生的。
工作辊、夹送辊、助卷辊、托辊。
在周期性载荷作用下,材料会发生疲劳磨损。
该过程包括在受压工具表面下剪切应力的产生。
重复加载导致微裂纹产生,常常也是出现在表面以下,在随后的加载和卸载过程中,微裂纹会扩展。
当裂纹达到一定的尺寸后,它会改变方向扩展到达材料的表面,从而出现扁平片状粒子的剥离(起层),如果分离的粒子很大,则称为剥落(Spalling)。
小规模的表面疲劳叫做微腐蚀(Micropitting)。
在热轧中会出现被称为开裂或热裂的破坏性热疲劳,该过程会产生交错镶嵌的裂纹网,就是网纹。
6、划伤划伤为带钢轧制过程中与硬物接触,带钢表面(下表较容易产生)产生一条或多条痕迹。