冲压模具角度调整
冲压模具调试板料流入量影响因素分析
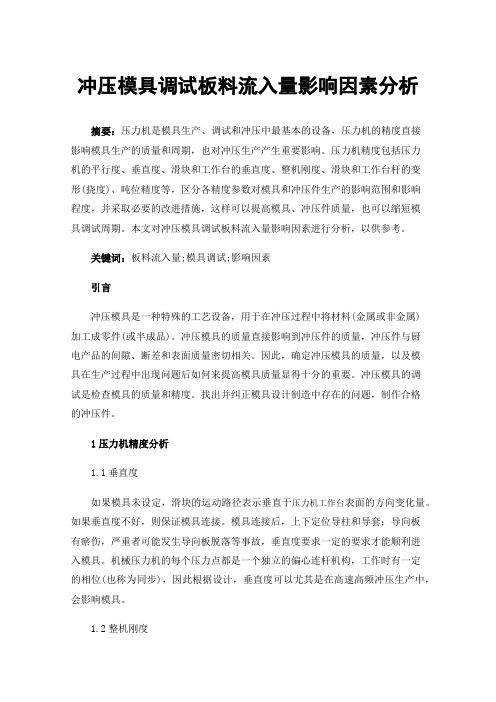
冲压模具调试板料流入量影响因素分析摘要:压力机是模具生产、调试和冲压中最基本的设备,压力机的精度直接影响模具生产的质量和周期,也对冲压生产产生重要影响。
压力机精度包括压力机的平行度、垂直度、滑块和工作台的垂直度、整机刚度、滑块和工作台杆的变形(挠度)、吨位精度等,区分各精度参数对模具和冲压件生产的影响范围和影响程度,并采取必要的改进措施,这样可以提高模具、冲压件质量,也可以缩短模具调试周期。
本文对冲压模具调试板料流入量影响因素进行分析,以供参考。
关键词:板料流入量;模具调试;影响因素引言冲压模具是一种特殊的工艺设备,用于在冲压过程中将材料(金属或非金属)加工成零件(或半成品)。
冲压模具的质量直接影响到冲压件的质量,冲压件与厨电产品的间隙、断差和表面质量密切相关。
因此,确定冲压模具的质量,以及模具在生产过程中出现问题后如何来提高模具质量显得十分的重要。
冲压模具的调试是检查模具的质量和精度。
找出并纠正模具设计制造中存在的问题,制作合格的冲压件。
1压力机精度分析1.1垂直度如果模具未设定,滑块的运动路径表示垂直于压力机工作台表面的方向变化量。
如果垂直度不好,则保证模具连接。
模具连接后,上下定位导柱和导套;导向板有瘀伤,严重者可能发生导向板脱落等事故,垂直度要求一定的要求才能顺利进入模具。
机械压力机的每个压力点都是一个独立的偏心连杆机构,工作时有一定的相位(也称为同步),因此根据设计,垂直度可以尤其是在高速高频冲压生产中,会影响模具。
1.2整机刚度当在压力机工作台和滑块底部的预定范围内将均匀分布的载荷施加到与条件力相对应的静载荷上时,将条件力分为工作台和滑块指定位置的平均相对变形、整机加载条件力时的综合变形、框架变形、减少每个连杆、曲轴变形和连接辅助间隙压缩、保护缸内油压缩返回距离,不能调整后期使用,变形时滑块下平面和工作台平面之间的距离变化是恒定的。
也就是说,加载4点数字时变化一致,对模具调试的影响有限。
模具装配与调试实训心得
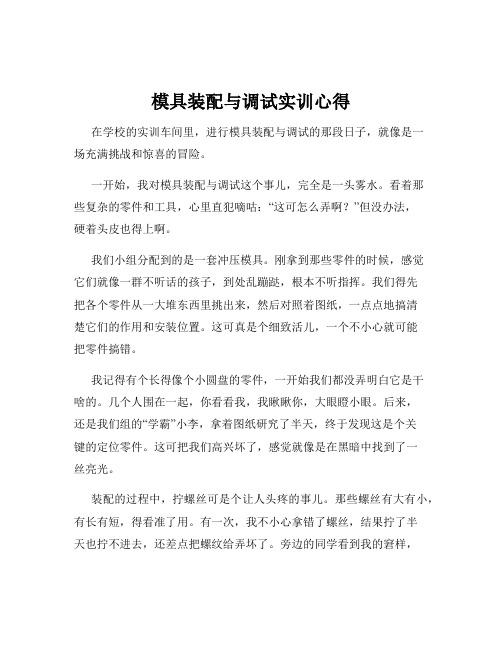
模具装配与调试实训心得在学校的实训车间里,进行模具装配与调试的那段日子,就像是一场充满挑战和惊喜的冒险。
一开始,我对模具装配与调试这个事儿,完全是一头雾水。
看着那些复杂的零件和工具,心里直犯嘀咕:“这可怎么弄啊?”但没办法,硬着头皮也得上啊。
我们小组分配到的是一套冲压模具。
刚拿到那些零件的时候,感觉它们就像一群不听话的孩子,到处乱蹦跶,根本不听指挥。
我们得先把各个零件从一大堆东西里挑出来,然后对照着图纸,一点点地搞清楚它们的作用和安装位置。
这可真是个细致活儿,一个不小心就可能把零件搞错。
我记得有个长得像个小圆盘的零件,一开始我们都没弄明白它是干啥的。
几个人围在一起,你看看我,我瞅瞅你,大眼瞪小眼。
后来,还是我们组的“学霸”小李,拿着图纸研究了半天,终于发现这是个关键的定位零件。
这可把我们高兴坏了,感觉就像是在黑暗中找到了一丝亮光。
装配的过程中,拧螺丝可是个让人头疼的事儿。
那些螺丝有大有小,有长有短,得看准了用。
有一次,我不小心拿错了螺丝,结果拧了半天也拧不进去,还差点把螺纹给弄坏了。
旁边的同学看到我的窘样,笑着说:“你这是在跟螺丝较劲呢!”我只能无奈地笑笑,重新找对螺丝继续干。
调试模具的时候,那才叫紧张呢。
我们小心翼翼地把模具安装到机器上,启动机器的那一刻,心都提到了嗓子眼儿。
就怕哪里出问题,“砰”的一声,零件飞得到处都是。
幸运的是,第一次调试还算顺利,只是冲压出来的产品有点小瑕疵。
于是,我们又开始反复调整模具的间隙和压力。
这时候,就得靠我们的手感和经验了。
有时候,就那么轻轻转动一下调节螺丝,效果就完全不一样。
经过无数次的尝试和改进,终于,我们冲压出了完美的产品。
那一刻,那种成就感简直无法用言语来形容。
在实训的过程中,也不是一帆风顺的。
有一次,我们为了赶进度,装配的时候粗心大意了一些,结果在调试的时候出了大问题。
模具卡住了,怎么也动不了。
我们急得满头大汗,不得不把已经装好的部分又重新拆开检查。
这一折腾,浪费了不少时间和精力。
压铸铝拔模角度标准
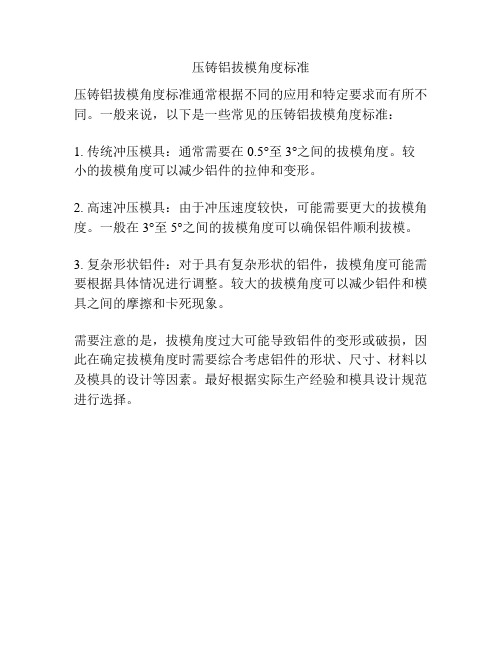
压铸铝拔模角度标准
压铸铝拔模角度标准通常根据不同的应用和特定要求而有所不同。
一般来说,以下是一些常见的压铸铝拔模角度标准:
1. 传统冲压模具:通常需要在0.5°至3°之间的拔模角度。
较小的拔模角度可以减少铝件的拉伸和变形。
2. 高速冲压模具:由于冲压速度较快,可能需要更大的拔模角度。
一般在3°至5°之间的拔模角度可以确保铝件顺利拔模。
3. 复杂形状铝件:对于具有复杂形状的铝件,拔模角度可能需要根据具体情况进行调整。
较大的拔模角度可以减少铝件和模具之间的摩擦和卡死现象。
需要注意的是,拔模角度过大可能导致铝件的变形或破损,因此在确定拔模角度时需要综合考虑铝件的形状、尺寸、材料以及模具的设计等因素。
最好根据实际生产经验和模具设计规范进行选择。
冲压线模具斜楔气源角度及传感器角度设置方法
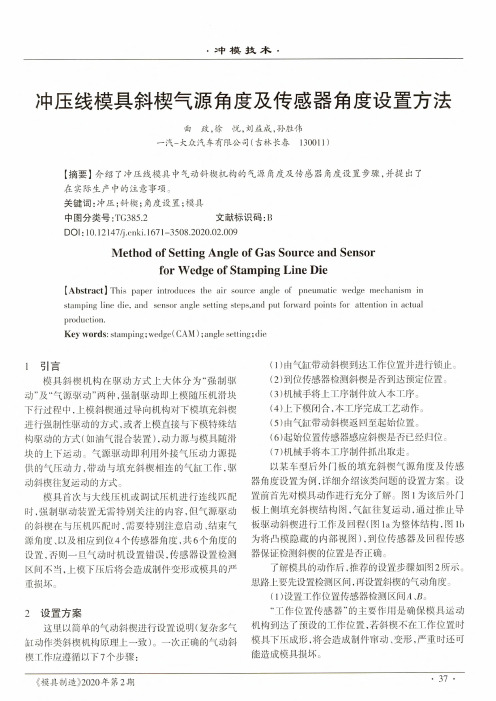
•冲模技术•冲压线模具斜楔气源角度及传感器角度设置方法曲政,徐悦,刘益成,孙胜伟一汽-大众汽车有限公司(吉林长春130011)【摘要】介绍了冲压线模具中气动斜楔机构的气源角度及传感器角度设置步骤,并提出了在实际生产中的注意事项。
关键词:冲压;斜楔;角度设置;模具中图分类号:TG385.2文献标识码:BDOI:10.12147/ki.l671-3508.2020.02.009Method of Setting Angle of Gas Source and Sensorfor Wedge of Stamping Line Die[Abstract]This paper introduces the air source angle of pneumatic wedge mechanism instamping line die,and sensor angle setting steps,and put foi-ward points for attention in actualproduction.Key words:stamping;wedge(.CAM);angle setting;1引言模具斜楔机构在驱动方式上大体分为“强制驱动”及“气源驱动”两种,强制驱动即上模随压机滑块下行过程中,上模斜楔通过导向机构对下模填充斜楔进行强制性驱动的方式,或者上模直接与下模特殊结构驱动的方式(如油气混合装置),动力源与模具随滑块的上下运动。
气源驱动即利用外接气压动力源提供的气压动力,带动与填充斜楔相连的气缸工作,驱动斜楔往复运动的方式。
模具首次与大线压机或调试压机进行连线匹配时,强制驱动装置无需特别关注的内容,但气源驱动的斜楔在与压机匹配时,需要特别注意启动、结束气源角度、以及相应到位4个传感器角度.共6个角度的设置,否则一旦气动时机设置错误,传感器设置检测区间不当.上模下压后将会造成制件变形或模具的严重损坏。
冲压模具疑难问题解决方案

冲压模具疑难问题解决方案一、废料跳穴1、冲头长度不够,按冲头刃口切入凹模一个料厚加1mm更换冲头2、凹模间隙过大,割入子减少间隙或用披覆机减小间隙3、冲头或模板未去磁,将冲头或模板用去磁器去磁二、废料堵穴1、落料孔小或落料孔偏位加大落料孔,使落料顺畅2、落料孔有倒角,加大落料孔去除倒角3、刀口未放锥度,线割锥度或反面扩充孔减小直壁位长度4、刀口直壁位过长,反面钻孔,使刀口直壁位缩短5、刃口崩,造成披锋大,堵料重新研磨刃口三、披锋不良1、刃口崩,造成披锋过大重新研磨刃口2、冲头与凹模间隙过大,线割入块,重新配间隙3、凹模刀口光洁度差,抛光刀口直壁位4、冲头与凹模间隙过小,重新省模,配间隙5、顶料力过大,反向拉出披锋换弹簧,减小顶料力四、切边不齐1、定位偏移调整定位2、有单边成型,拉料加大压料力,调整定位3、设计错误,造成接刀不平重新线割切边刀口镶块4、送料不准调整送料器5、送料步距计算有误重新计算步距,重定接刀位五、冲头易断1、闭合高度过低,冲头切入刀口部位过长调整闭合高度2、材料定位不当,造成冲孔冲头切单边,调整定位或送料装置因受力不均断裂3、下模废料堵死刀口,造成冲头断重新钻大落料孔,使落料顺畅4、冲头的固定部位(夹板)与导向部位修配或重新线割入块使冲头上下顺畅(打板)偏移5、打板导向不良,造成冲头单边受力重新修配打板间隙6、冲头刀口太短,与打板干涉重换冲头,增长刀口部分长度7、冲头固定不好,上下窜动重新固定冲头使之不能上下窜动8、冲头刃口不锋利重新研磨刃口9、冲头表面拉伤,脱料时受力不均重新换冲头10、冲头过细,过长,强度不够重新换冲头类型11、冲头硬度过高,冲头材质不对更换冲头材质,调整热处理硬度六、铁屑1、压筋错位重新计算压筋位置或折弯位置2、折弯间隙过小,挤出铁屑重新调整间隙,或研磨成型块,或研磨成型冲头3、折弯凸模太锋利修R角4、接刀口材料太少重新接刀口5、压筋太窄重新研磨压筋七、抽芽不良1、抽芽底孔中心与抽芽冲子中心不重合造确定正确中心位置,或移动抽芽冲子位置,或移成抽芽-边高-边低甚至破裂动预冲孔位置,或调整定位2、凹模间隙不均匀,造成抽芽-边高-边修配抽芽间隙低甚至破裂3、抽芽底孔不符合要求,造成抽芽高度及重新计算底孔孔径,预冲孔增大或减少直径偏差,甚至破裂八、成型不良1、成型模凸模太锋利,造成材料拉裂成型凸模修R角,刀口处适当修R角2、成型冲头长度不够,造成未能成型计算冲头正确长度调整冲头实际长度以达成型要求3、成型冲头过长,成型处材料压变形,甚确定冲头正确长度,调整冲头实际长度以达到要求至冲头断裂4、成型处材料不够造成拉裂计算展开材料,或修R角,或降低成型高度5、定位不良,造成成型不良调整定位或送料装置6、成型间隙太小造成拉裂或变形调配间隙九、折弯尺寸1、模具没调到位造成角度误差导致尺寸偏调整闭合高度不良或角度差不良2、弹力不够造成角度不良导致尺寸偏差换弹簧3、材质不符合要求造成角度不良导致尺寸换材料或重新调整间隙偏差4、材料厚度偏差引起角度不良导致尺寸偏确定料厚,换材料或重新调整间隙差5、定位不当导致尺寸偏差调整定位使尺寸OK6、设计或加工错误造成折弯公拼块间有间補焊研磨,消除拼块间的间隙,导致折弯尺寸小7、成型公无R角,在角度及其他正常情况成型公修R角下折弯高度偏小8、两边折弯尺寸偏大加压筋9、单边折弯拉料造成尺寸不稳定加大弹簧力,调整定位10、间隙不合理,引起角度不良和尺寸偏差修配间隙11、折刀高度不够,折弯冲头合入折刀太短增加折刀高度,使折弯冲头尽可能合入折刀部队位造成角度不良多一些12、折弯时速度太快,造成折弯根部变形调整速比控,选择合理转速13、结构不合理,折刀未镶入固定模板,重新铣槽,将折刀镶入模板冲压时,造成间隙变大14、成型公热处理硬度不够,造成压线崩或重制成型公压线打平十、不卸料1、定位不当或送料不当调整定位或送料装置2、避位不够修磨避位3、内导柱拉伤,造成打板活动不畅更换内导柱4、冲头拉伤或表面不光滑更换冲头5、顶料销摆布不合理重新摆布顶料销位置6、顶料力不够,或脱料力不够更换顶料弹簧或脱料弹簧7、冲头与夹板打板配合不顺畅修配打板和夹板使冲头配合顺畅8、成型滑块配合不畅修整滑块与导向槽使之配合顺畅9、打板热处理不适,冲压一段时间后变形重新研磨打板,矫正变形10、冲头过长或顶料销长度不够增加顶料销长度或换用长度合适之冲头11、冲头断更换冲头12、模板未云磁,工件往上带给模板去磁十一、送料不顺1、模具没架正,导致料带与送料器及模具重架模具或调整送料器不在同一条直线上2、料带不平调整校平机或更换材料3、不卸料造成送料不顺参照不卸料解决对策4、定位太紧调整定位5、导正销太紧或直壁位太长调整导正销6、冲头固定不好或太长与料带干涉换长度合适之冲头重新固定7、顶料销太短,料带与成型入块相干涉调整顶料销长度,避免干涉8、浮升块位置排配不当调整浮升块位置十二、铆合不良1、模具闭合高度不当铆合不到位调整闭合高度2、工件未放到位,定位偏差调整定位3、铆合前工件不良确认抽芽孔,参考抽芽孔不良解决对策处理确认铆合孔是否倒角,如无倒角则增加倒角4、铆合冲头长度不够换用长度合适之冲头5、铆合冲头不符合要求确认并用符合要求之铆合冲头十三、漏装或装1、不小心组立时细心错冲子2、冲子无方向标记有方向性的冲子做上记号十四、装错螺丝1、不知道模板的厚度了解模板的厚度太长或太短2、不够细心,经验不足选用适当的螺丝十五、拆装模具1、销钉孔没有擦干净将销孔,销钉擦干净,拆模时应先拆定位销时容易损坏装模时,应先用螺丝导正,后打定位销钉孔2、装拆模具程序不对打落销钉时不要碰伤销钉孔十六、定位销1、孔壁拉毛,刮伤致使太紧组模时,细心检查销钉孔是否拉毛,否则应将打不出来销孔重新铰孔2、销孔偏位或下面没有逃孔追加定位销逃孔十七、弹簧太长1、没有注意弹簧孔深度量好弹簧孔深度,算好弹簧的压缩量,重新选择无法下压到2、不够细心,经验不足合适的弹簧下死点。
五金模具冲压成型角度设计标准

五金模具冲压成型角度设计标准五金模具冲压成型角度设计是模具设计中非常重要的一部分,它直接关系到产品的成型质量和效率。
以下是五金模具冲压成型角度设计的标准:1. 冲压成型角度应符合产品的设计要求和工艺要求。
不同产品的冲压成型角度有所不同,需要根据具体产品的形状和尺寸来确定。
2. 冲压成型角度应根据材料的性质来确定。
不同材料的成型性能和行为有所不同,需要考虑材料的硬度、弹性模量等因素来确定冲压成型角度。
3. 冲压成型角度应尽量保持一致。
尽量避免在一个模具中设计过多的不同角度,这样可以提高模具的制造和使用效率。
4. 冲压成型角度应适当放大。
考虑到材料的弹性变形,在模具设计中可以适当放大冲压成型角度,以确保产品的成型质量。
5. 冲压成型角度应考虑到模具的制造和使用方便。
为了方便模具的加工和使用,冲压成型角度的设计应避免过于复杂和困难。
6. 冲压成型角度应考虑到工装夹具的设计。
冲压成型角度的设计也需要考虑到工装夹具的设计,以确保夹具和模具的配合精度。
7. 冲压成型角度应考虑到产品的表面质量要求。
在模具设计中,还需要考虑产品的表面质量要求,例如是否需要凹凸纹路等。
8. 冲压成型角度应根据模具的材料和制造工艺来确定。
不同的模具材料和制造工艺对冲压成型角度的设计有一定的要求。
9. 冲压成型角度应结合实际生产情况进行优化。
在模具设计中,可以根据实际生产情况对冲压成型角度进行优化,以提高生产效率和降低成本。
总之,五金模具冲压成型角度设计是一个非常重要的环节,需要综合考虑产品的设计要求、工艺要求、材料特性、模具制造和使用等方面因素,在实际设计中灵活运用,以达到最佳的成型效果。
冲压模具:影响回弹因素、回弹计算公式计算

冲压模具:影响回弹因素、回弹计算公式计算回弹,设计师都会遇到,而且无法避免,只能想办法补偿或者降低影响。
那什么是回弹呢?金属材料在塑性弯曲时总是伴随著弹性变形,因此当弯矩去掉之后,弯曲件的弯曲半径变得与模具尺寸不一致,这种现象称为回弹。
而回弹的大小通常用角度回弹量∆a和曲率回弹量∆q来表示。
一.影响回弹的因素:1.材料的力学性能:回弹角的大小与材料的屈服点S与a正比,与弹性模数E成反比.2.相对弯曲半径r/t愈大,则表示变形程度愈小,回弹愈大.3.弯曲中心角a:a愈大,则∆a愈大4.弯曲方式,校正弯曲的回弹角小于自由弯曲的回弹角.5.制件形状:u形状回弹角小于v形件,复杂的弯曲件, 一次弯曲成形,弯角数量越多,回弹量就越小.6.模具间隙:u形弯曲模的凸.凹每侧间隙z/h越大,则回弹与越大,z/2<t时,可以发生负回弹.二.回弹的计算由于影响回弹角的因素较多,因此要在理输上计算回弹角是有困难的,在模具设计时通常按实验总结的数据不修正,或经试衝后再修正.(一).当r/t<5时,直接放角度回弹即可不必缩R角.1).当t≤0.3,⍬=90º时,如图所示,分两次折弯且第一次折弯时,折弯点外移0.1~0.22).当t>0.3, ⍬=90º时,所图所示,分两次折弯,第一次折弯时,折弯点不用外移3). ⍬=90º时,一般一次成形,根据材质,料厚的不同,提供以下数据供参考.(4)U二)U当R/t≥5时,曲率回弹量比较大,需缩R角,其计算公式见R角回弹计算设计规范,在模具设计时,弯曲凸模圆角半径,R一般要比计算值R凸小,然后再加一步整形即可.产品回弹比较复杂,即使是相同材质的情况下,自身材料不同厚度、折弯角度、折弯内R都会对回弹产生很大影响。
不同材质就更不用说了。
因此,回弹并非一个公式即可完全解决,需要我们在理论的基础上进行实践调试,以得到最终合格产品。
解决冲压塌边的方法
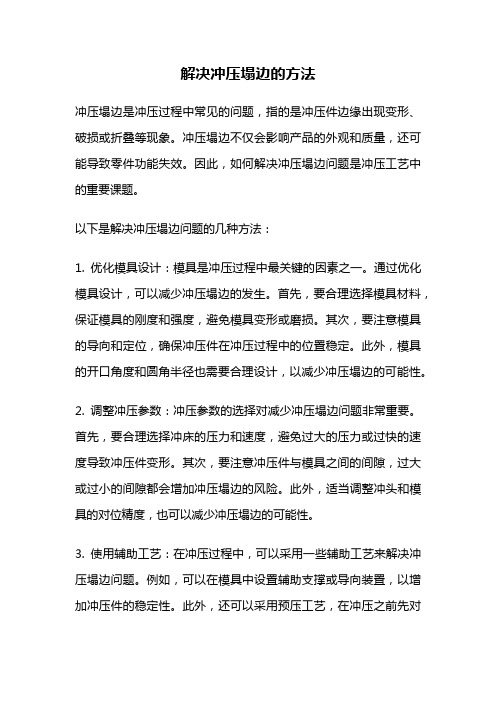
解决冲压塌边的方法冲压塌边是冲压过程中常见的问题,指的是冲压件边缘出现变形、破损或折叠等现象。
冲压塌边不仅会影响产品的外观和质量,还可能导致零件功能失效。
因此,如何解决冲压塌边问题是冲压工艺中的重要课题。
以下是解决冲压塌边问题的几种方法:1. 优化模具设计:模具是冲压过程中最关键的因素之一。
通过优化模具设计,可以减少冲压塌边的发生。
首先,要合理选择模具材料,保证模具的刚度和强度,避免模具变形或磨损。
其次,要注意模具的导向和定位,确保冲压件在冲压过程中的位置稳定。
此外,模具的开口角度和圆角半径也需要合理设计,以减少冲压塌边的可能性。
2. 调整冲压参数:冲压参数的选择对减少冲压塌边问题非常重要。
首先,要合理选择冲床的压力和速度,避免过大的压力或过快的速度导致冲压件变形。
其次,要注意冲压件与模具之间的间隙,过大或过小的间隙都会增加冲压塌边的风险。
此外,适当调整冲头和模具的对位精度,也可以减少冲压塌边的可能性。
3. 使用辅助工艺:在冲压过程中,可以采用一些辅助工艺来解决冲压塌边问题。
例如,可以在模具中设置辅助支撑或导向装置,以增加冲压件的稳定性。
此外,还可以采用预压工艺,在冲压之前先对冲压件施加一定的压力,以增加其刚度和稳定性,减少冲压塌边的可能性。
4. 优化材料选择:材料的选择对于减少冲压塌边问题也有一定的影响。
首先,要选择适合冲压的材料,具有良好的可塑性和韧性。
其次,要注意材料的厚度和硬度,过大或过小的厚度都会增加冲压塌边的风险。
此外,还可以考虑在冲压件边缘添加特殊的涂层或涂料,以增加其抗塌边性能。
5. 加强质量控制:冲压塌边问题往往与质量控制不严密有关。
因此,加强质量控制是解决冲压塌边问题的关键。
首先,要建立完善的质量检测体系,对冲压件进行全面的检测和测试,确保其符合设计要求。
其次,要加强对冲压工艺的监控,及时发现和解决冲压塌边问题。
此外,还可以通过培训和技术交流,提高操作人员的技术水平和质量意识。
- 1、下载文档前请自行甄别文档内容的完整性,平台不提供额外的编辑、内容补充、找答案等附加服务。
- 2、"仅部分预览"的文档,不可在线预览部分如存在完整性等问题,可反馈申请退款(可完整预览的文档不适用该条件!)。
- 3、如文档侵犯您的权益,请联系客服反馈,我们会尽快为您处理(人工客服工作时间:9:00-18:30)。
弹簧片冲压工程
冲床模具调整手顺:
1.拔出9度角只冲压12度角,以确认12度角的整体差异,还要确认其正反面差异性,冲压时是在没有气压的状态下进行确认。
如果角度不是稳定的那就是下模送料槽左右高低不平或底部不平,需进行调整或修理翻模,如稳定则是由气压太大所造成的角度异常需减小气压。
2.拔出12度角只冲压9度角,以确认9度角的整体差异,同时还要确认其反面差异性,冲压时是在没有气压的状态下进行确认。
如果角度不是稳定的那就是下模送料槽左右高低不平或底部不平,需进行调整或修理翻模,如稳定则是由气压太大所造成的角度异常需减小气压。
3.如果正面整体差异大则减小气压及冲程,检查夹具上下跳动幅度是否过大(减小气压以上下运动灵活不停滞不延迟为好),如果气压调得太小可能会使夹具跳起的行程不够而将产品撞变形。
冲程调整到上下模刚接触没有大的碰撞声为止,再次确认角度是否在公差内且稳定。
4.如果正反面差异大则应先测量上模平面度(包括限位柱,角度成型凸台及平台,定位PIN平台),相差应在0.002以内;如是平台或柱有高度差则应垫高至相同高度(注:不能麿平,这样就会使整体高度下降而造成新的问题)。
5.如是角度成型凸台所造成的左右差异大,则在相对应的一侧垫适当的垫片,再进行测量相应的高度(相差40分时大概可垫0.01的厚度)使凸台呈一边高一边低然后锁紧螺丝,锁螺丝时要保证剥离器运动灵活,如果不灵活会造成产品角度差异大,如果剥离器的弹力太小会造成产品压痕,应调整剥离器的弹簧力使弹力大一些为好。
作成:HU JIAN
日期:2012/1/10。