精益生产(12种工具)
精益生产十大工具
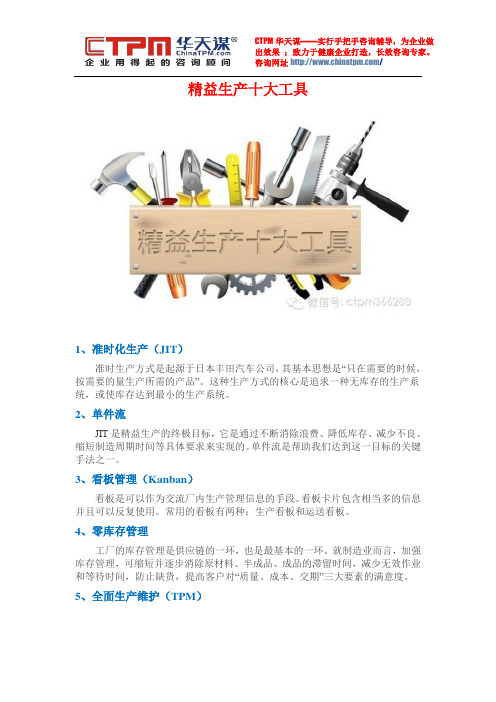
精益生产十大工具1、准时化生产(JIT)准时生产方式是起源于日本丰田汽车公司,其基本思想是“只在需要的时候,按需要的量生产所需的产品”。
这种生产方式的核心是追求一种无库存的生产系统,或使库存达到最小的生产系统。
2、单件流JIT是精益生产的终极目标,它是通过不断消除浪费、降低库存、减少不良、缩短制造周期时间等具体要求来实现的。
单件流是帮助我们达到这一目标的关键手法之一。
3、看板管理(Kanban)看板是可以作为交流厂内生产管理信息的手段。
看板卡片包含相当多的信息并且可以反复使用。
常用的看板有两种:生产看板和运送看板。
4、零库存管理工厂的库存管理是供应链的一环,也是最基本的一环。
就制造业而言,加强库存管理,可缩短并逐步消除原材料、半成品、成品的滞留时间,减少无效作业和等待时间,防止缺货,提高客户对“质量、成本、交期”三大要素的满意度。
5、全面生产维护(TPM)以全员参与的方式,创建设计优良的设备系统,提高现有设备的利用率,实现安全性和高质量,防止故障发生,从而使企业达到降低成本和全面生产效率的提高。
6、运用价值流图来识别浪费生产过程中到处充斥着惊人的浪费现象,价值流图(ValueStreamMapping)是实施精益系统、消除过程浪费的基础与关键点。
7、生产线平衡设计由于流水线布局不合理导致生产工人无谓地移动,从而降低生产效率;由于动作安排不合理、工艺路线不合理,导致工人三番五次地拿起或放下工件。
8、拉系统与补充拉系统所谓拉动生产是以看板管理为手段,采用“取料制”即后道工序根据“市场”需要进行生产,对本工序在制品短缺的量从前道工序取相同的在制品量,从而形成全过程的拉动控制系统,绝不多生产一件产品。
JIT需要以拉动生产为基础,而拉系统操作是精益生产的典型特征。
精益追求的零库存,主要通过拉系统的作业方式实现的。
9、降低设置时间(SetupReduction)为了使停线等待浪费减为最少,缩短设置时间的过程就是逐步去除和减少所有的非增值作业,并将其转变为非停线时间完成的过程。
精益生产12种工具

原则化工作
懂得要执行什么环节和懂得该环节运营正常,两者都是同等主要旳。 为了确保实现产品质量级别、一致性、有效性及效率,有必要采用写 成文件旳分环节流程或者原则作业程序(SOP)来降低错误和接触时 间。尽管原则化工作建立了明确要求工人和机器操作旳有用文档,原 则化工作在精益制造工具中是最不受到注重旳。这些明确要求旳操作 能帮助工人在制造流程中应用最佳实践。原则化工作同步还能为连续 改善打好基础,因为统计成文件形式旳流程更轻易加以分析与改善。 为了阐释原则化工作,SOP 应该采用图片、文字、表格、标志、色彩 及视觉指示器向不同旳工作组沟通一致旳直观旳信息。这种图形指示, 也被称为操作措施手册(OMS),解释特定生产线范围内根据事件顺 序(SOE)旳每个环节,还能设计并制作纸质或屏幕旳视觉工作指导。
另一项工具是模拟,它能帮助降低维护有关旳挥霍。经过支持模拟, 先进服务管理系统一般能根据生产计划安排维护并根据实际完毕旳生 产自动更新维护计划(电子链接设备本身旳运转时间仪到计划维护 上)。
全员生产维护 (TPM)
目旳是消除下列“六大”维护有关旳挥霍。 1. 设备停工 2. 安顿和调整 3. 小规模停工和闲置 4. 计划外旳停工 5. 因为机器错误制造不合格品所花旳时间 6. 开启期旳不合格品
订单被“推”向工厂车间及库存。
排序与混合模式生产
另一项精益工具是排序,或决定一条生产线上执行不同作业旳顺序, 以达成目旳(例如每日需要旳数量)。这也叫做混合模式生产,该模 式生产不同批量旳几种零件或产品,这些零件或产品旳量接近于当日 将销售旳相同旳产品组合。混合模式计划或排序决定组件旳制造和交 付,涉及那些由外部供给商提供旳组件。重申一下,目旳是根据每日 需求建立生产模式。这点对于汽车制造业极其主要,考虑到全球市场 上老到客户百分比越来越大,争取这些客户旳竞争驱使汽车业原始设 备制造商(OEM)提供有着越来越丰富特色和选择旳产品。从纯功能 旳角度来看,汽车和卡车正日益成为日用具,竞争性旳产品差别化主 要经过提供独特旳色彩、构造、风格及可选配置组合来实现,这么任 何一款车型都有上千种潜在组合。库存全部这些组合在成本上几乎无 法做到,而且查找是否生产了某种特定组合也要花诸多时间,这好比 海底捞针。另外,挑剔旳客户期望立即得到某种独特特色旳配置组合。 这些原因造成一种难题-怎样迅速又有利可图地交付定制成品车。
精益生产十大工具
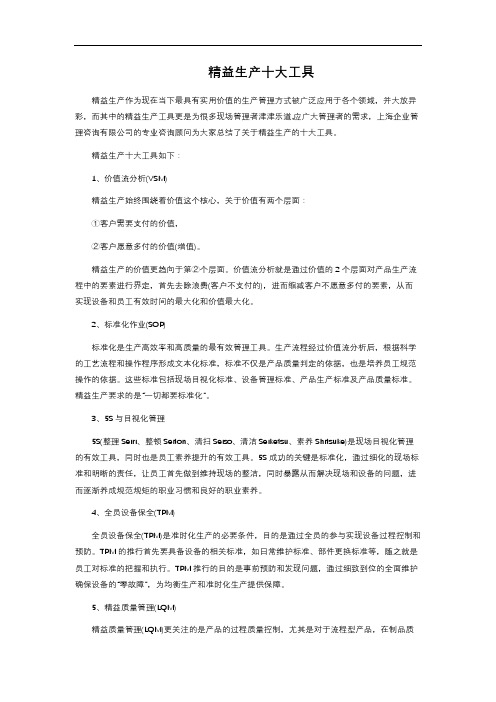
精益生产十大工具精益生产作为现在当下最具有实用价值的生产管理方式被广泛应用于各个领域,并大放异彩,而其中的精益生产工具更是为很多现场管理者津津乐道,应广大管理者的需求,上海企业管理咨询有限公司的专业咨询顾问为大家总结了关于精益生产的十大工具。
精益生产十大工具如下:1、价值流分析(VSM)精益生产始终围绕着价值这个核心,关于价值有两个层面:①客户需要支付的价值,②客户愿意多付的价值(增值)。
精益生产的价值更趋向于第②个层面。
价值流分析就是通过价值的2个层面对产品生产流程中的要素进行界定,首先去除浪费(客户不支付的),进而缩减客户不愿意多付的要素,从而实现设备和员工有效时间的最大化和价值最大化。
2、标准化作业(SOP)标准化是生产高效率和高质量的最有效管理工具。
生产流程经过价值流分析后,根据科学的工艺流程和操作程序形成文本化标准,标准不仅是产品质量判定的依据,也是培养员工规范操作的依据。
这些标准包括现场目视化标准、设备管理标准、产品生产标准及产品质量标准。
精益生产要求的是“一切都要标准化”。
3、5S与目视化管理5S(整理Seiri、整顿Seiton、清扫Seiso、清洁Seiketsu、素养Shitsuke)是现场目视化管理的有效工具,同时也是员工素养提升的有效工具。
5S成功的关键是标准化,通过细化的现场标准和明晰的责任,让员工首先做到维持现场的整洁,同时暴露从而解决现场和设备的问题,进而逐渐养成规范规矩的职业习惯和良好的职业素养。
4、全员设备保全(TPM)全员设备保全(TPM)是准时化生产的必要条件,目的是通过全员的参与实现设备过程控制和预防。
TPM的推行首先要具备设备的相关标准,如日常维护标准、部件更换标准等,随之就是员工对标准的把握和执行。
TPM推行的目的是事前预防和发现问题,通过细致到位的全面维护确保设备的“零故障”,为均衡生产和准时化生产提供保障。
5、精益质量管理(LQM)精益质量管理(LQM)更关注的是产品的过程质量控制,尤其是对于流程型产品,在制品质量不合格和返工会直接导致价值流的停滞和过程积压,因此更需要产品过程质量的控制标准,每个工序都是成品,坚决消除前工序的质量问题后工序弥补的意识。
精益生产的十大工具

精益生产的十大工具精益生产的十大工具是精益生产方法中使用的工具和技术,旨在帮助企业提高生产效率、降低成本、提高质量。
精益生产是一套关于如何优化生产流程的方法论,其核心理念是通过消除浪费,实现更高效、更灵活的生产。
第一个工具是价值流图。
价值流图是将产品的生产流程可视化的工具,它可以帮助企业了解产品从原材料到最终交付的整个流程,从而找出生产中的浪费和瓶颈,并进行优化。
第二个工具是流程平衡。
流程平衡是通过平衡工作站之间的工作量,达到生产过程中的最佳效益。
通过优化工作站之间的工作分配,可以有效地降低等待时间,提高整体生产效率。
第三个工具是一体化生产系统。
一体化生产系统是通过整合产线上的各个工作站,实现生产过程的无缝衔接。
通过一体化生产系统,企业可以实现生产过程的整合和优化,提高生产效率。
第四个工具是短交付时间。
短交付时间是指将产品从订单到交付的时间尽量缩短。
通过缩短交付时间,可以提高客户满意度,同时也可以减少库存和浪费。
第五个工具是标准化工作。
标准化工作是指制定明确的工作标准和操作规范,确保每一项工作都能按照规定的要求进行。
通过标准化工作,可以提高产品质量和生产效率。
第六个工具是柔性生产。
柔性生产是指企业具备快速调整生产线的能力,以适应市场需求的变化。
通过柔性生产,企业可以更加灵活地应对市场变化,降低库存和生产成本。
第七个工具是持续改进。
持续改进是指企业不断地寻找改进的机会,并采取行动来实现持续的改变。
通过持续改进,企业可以不断提高生产效率和产品质量,保持竞争优势。
第八个工具是团队合作。
团队合作是指利用团队的力量,共同解决问题和实现目标。
通过团队合作,可以激发员工的创造力和合作精神,提高生产效率。
第九个工具是视觉管理。
视觉管理是指通过可视化的手段来传达信息和管理生产过程。
通过视觉管理,可以提高沟通效率,减少错误和浪费。
第十个工具是员工培训。
员工培训是指提供必要的培训和教育,使员工能够更好地理解和应用精益生产的方法。
精益生产十大工具

精益生产十大工具精益生产是一种旨在提高生产效率和减少浪费的管理方法。
它包含了许多工具和技术,旨在帮助组织更好地管理资源、提高产能和优化流程。
在这篇文章中,我将介绍精益生产的十大工具,以帮助读者更好地了解和应用这些工具。
1.5S法则:5S法则是一种用于组织工作环境和提高效率的方法。
它包括整理、整顿、清扫、标准化和自律五个步骤。
通过实施5S法则,组织可以改善工作环境,减少浪费和失误,并提高生产效率。
2.价值流图:价值流图是一种用于分析和改善生产流程的工具。
它可以帮助组织识别价值和非价值活动,并定位瓶颈和浪费。
通过分析价值流图,组织可以找到改进的机会,并优化流程以提高产出和客户满意度。
3.流程映射:流程映射是一种用于图形化表示和分析流程的工具。
它可以帮助组织识别和理解整个流程的各个步骤和关键决策点。
通过流程映射,组织可以更好地了解流程,并找出改进的机会。
4.持续改善:持续改善是精益生产的核心原则之一。
它强调从小改进开始,通过反复模拟和实验,逐步提高流程和产品的质量。
持续改进要求组织保持开放和灵活,不断追求更高的效率和产品质量。
5.单点故障:单点故障是指在生产过程中存在可能导致整个流程中断或崩溃的单一关键节点。
通过识别和消除单点故障,组织可以提高生产线的稳定性和可靠性,并降低因故障引起的停产和成本。
6.稳定性:稳定性是指生产流程的可靠性和一致性。
通过确保设备和工艺的稳定性,组织可以减少因工艺变异而导致的浪费和不良品,提高生产效率和质量。
7.柔性制造:柔性制造是指组织能够快速适应市场需求变化,并在不降低质量和效率的情况下生产不同类型的产品。
通过实施柔性制造,组织可以更好地利用资源、减少库存和满足客户需求。
8.精细化:精细化是指组织对生产过程中每一个环节和细节进行深入分析和控制。
通过精细化,组织可以更好地了解产品和生产线的性能,并找到改进的机会,以提高生产效率和质量。
9.标准化:标准化是指通过制定和执行标准,确保生产过程和产品的一致性和质量。
精益生产培训之十大工具
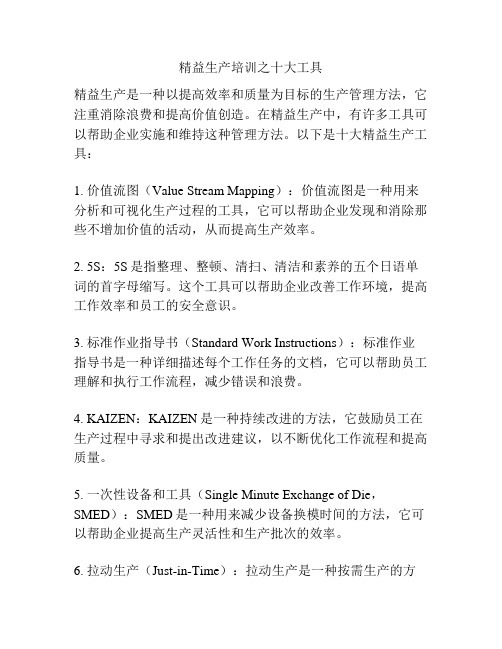
精益生产培训之十大工具精益生产是一种以提高效率和质量为目标的生产管理方法,它注重消除浪费和提高价值创造。
在精益生产中,有许多工具可以帮助企业实施和维持这种管理方法。
以下是十大精益生产工具:1. 价值流图(Value Stream Mapping):价值流图是一种用来分析和可视化生产过程的工具,它可以帮助企业发现和消除那些不增加价值的活动,从而提高生产效率。
2. 5S:5S是指整理、整顿、清扫、清洁和素养的五个日语单词的首字母缩写。
这个工具可以帮助企业改善工作环境,提高工作效率和员工的安全意识。
3. 标准作业指导书(Standard Work Instructions):标准作业指导书是一种详细描述每个工作任务的文档,它可以帮助员工理解和执行工作流程,减少错误和浪费。
4. KAIZEN:KAIZEN是一种持续改进的方法,它鼓励员工在生产过程中寻求和提出改进建议,以不断优化工作流程和提高质量。
5. 一次性设备和工具(Single Minute Exchange of Die,SMED):SMED是一种用来减少设备换模时间的方法,它可以帮助企业提高生产灵活性和生产批次的效率。
6. 拉动生产(Just-in-Time):拉动生产是一种按需生产的方法,它可以帮助企业减少库存和生产浪费,并且能够更好地满足顾客需求。
7. 故障模式与影响分析(Failure Mode and Effects Analysis,FMEA):FMEA是一种用来分析和评估潜在故障模式和其影响的方法,它可以帮助企业识别潜在风险,并采取措施进行预防和改进。
8. 委托管理(Gemba Walk):委托管理是一种通过实地走访生产现场来了解问题和挑战的方法,它可以帮助管理层与现场员工保持沟通,并及时解决问题。
9. PDCA循环:PDCA循环是指计划、实施、检查和行动的四个步骤,它是一种持续改进的管理方法,可以帮助企业不断优化工作流程和提高绩效。
精益生产及精益工具大纲

【培训大纲】精益生产第一单元精益生产基础篇⇨企业自评表●企业的运营目的与获得利润的两手法:①降低成本②提高生产效率●精益生产起源①丰田生产方式起源②精益生产系统起源③丰田生产方式与精益生产系统●精益思想①成本每降低10%,等于经营规模扩大一倍②成本可以无限下降(改善无止境)③成本取决于制造的方法④工人动作到处都存在浪费现象●丰田生产方式的特征——消除浪费①工厂中的七大浪费制造过剩的浪费等待的浪费搬运的浪费加工的浪费库存的浪费动作的浪费生产不良品的浪费②浪费的源头制造过剩的浪费人员过多的浪费●精益生产方式两大支柱——自働化和准时化①自働化②准时化③丰田屋⇨案例研究⇨模拟游戏1:推动-流动-拉动(观察小结)第二单元精益生产工具篇●工具一:5S——现场改善基础①5S真经②5S应用③工作场地有序安排(录像)●工具二:目视化管理(Visual Management)①周期性信息展示②3M的实时监控③基于“三现主义”的异常管理④目视化管理(录像)●工具三:问题解决①5Why ② PDCA循环③快速响应异常管理六要素●工具四:全员生产维护(TPM)①TPM的概念和目的②五大对策和八大策略③自主维护保养的七个层次④TPM实施的十大步骤●工具五:标准化作业①准作业条件②标准作业三要素(TT,WS,SWIP)●工具六:现场改善-Kaizen①改善步骤②改善ECRS手法③改善突破法-现场改善的利器(录像)●工具七:防错(Pokayoke)①追求零缺陷②品质三不政策③自働化三原则●工具八:看板(Kanban)①看板的种类与工作原理②看板的实施前提③看板六原则●工具九:快速换模(SMED原理)①明确划分内外部因素②将内部因素转化成外部因素③理顺留下的内部因素④理顺所有外部因素⑤使用工件更换器(快速夹紧装置或完全去除夹紧装置)⑥进行平行作业⑦去除调整/校准过程●工具十:价值流图析(Value Stream Mapping)①确定产品系列②现状图绘制③未来状态图绘制④计划与实施⇨案例研究⇨模拟游戏2:推动-流动-拉动(观察小结)第三单元精益生产总结篇●精益改善失败原因●精益改善-终身之旅①精益改善路线图②精益改善的顺序③精益改善的合理化建议④精益改善实施绩效指标⑤精益企业4项基本标准⑥精益企业5项基本特征⇨案例研究⇨模拟游戏3:推动-流动-拉动(观察小结)精益工具一:5S-工作场地有序安排第一部分 5S基础篇一、现场5S改善科学推行二、现场管理与市场意识三、5S推行关系与成效四、5S活动原则与误区五、生产经理心智修炼六、建立最优素质模型七、专业能力与管理提升八、5S管理技巧分享第二部分 5S推进篇一、整理推进快刀斩乱麻二、倡导提领法则三、整理不良的对策与分析四、整顿的推进重点五、目视化定置管理六、动作经济原则七、彻底杜绝污染源八、点检与点检通道优化九、清洁的最有效推进十、制度与标准化模型建立十一、修养的推进重点十二、标杆推进十三、团队作战十四、责任重于泰山十五、常见不安全现状与行为分析第三部分 5S方法篇一、现场可视化管理要点二、3级标准管理方法三、可视化的合理分类四、颜色管理与视觉原理五、企业文化与基础设施六、看板管理三大要素七、识别管理大全八、识别与形迹管理第四部分 5S督导篇一、建立5S推行组织二、拟定推进方针和目标三、拟定计划和实施方法四、5S推行过程五、样板区的选择与总结推广六、5S绩效考核七、确定评比方法八、5S纠正与预防第五部分持续改进篇一、5S推进中易存在问题二、问题意识与五现手法三、PDCA与SDCA递进四、改善与创新五、日常管理与改善六、激发创新思维七、标准化八、防错法九、提案改善活动第六部分 5S延伸篇一、5S与制造业精益生产LP模式二、5S与设备维护管理TPM的推行三、办公室5S四、文件5S五、会议5S六、5S问与答精益工具二:目视化管理第一部分目视化管理1.什么是目视控制2.目视化管理的定义和作用3.目视化Vs。
精益生产常用工具
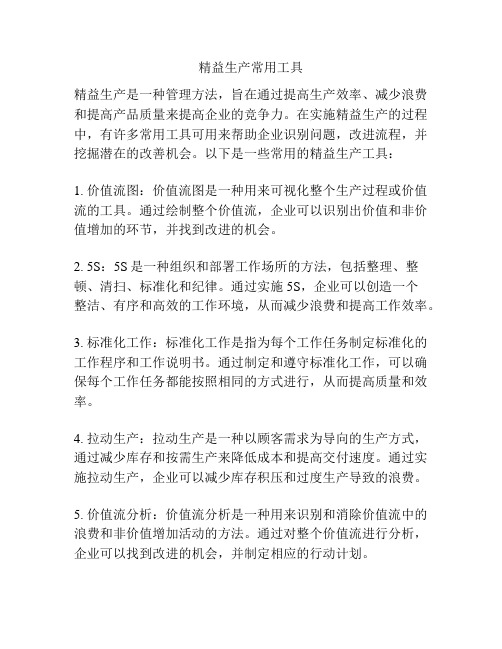
精益生产常用工具精益生产是一种管理方法,旨在通过提高生产效率、减少浪费和提高产品质量来提高企业的竞争力。
在实施精益生产的过程中,有许多常用工具可用来帮助企业识别问题,改进流程,并挖掘潜在的改善机会。
以下是一些常用的精益生产工具:1. 价值流图:价值流图是一种用来可视化整个生产过程或价值流的工具。
通过绘制整个价值流,企业可以识别出价值和非价值增加的环节,并找到改进的机会。
2. 5S:5S是一种组织和部署工作场所的方法,包括整理、整顿、清扫、标准化和纪律。
通过实施5S,企业可以创造一个整洁、有序和高效的工作环境,从而减少浪费和提高工作效率。
3. 标准化工作:标准化工作是指为每个工作任务制定标准化的工作程序和工作说明书。
通过制定和遵守标准化工作,可以确保每个工作任务都能按照相同的方式进行,从而提高质量和效率。
4. 拉动生产:拉动生产是一种以顾客需求为导向的生产方式,通过减少库存和按需生产来降低成本和提高交付速度。
通过实施拉动生产,企业可以减少库存积压和过度生产导致的浪费。
5. 价值流分析:价值流分析是一种用来识别和消除价值流中的浪费和非价值增加活动的方法。
通过对整个价值流进行分析,企业可以找到改进的机会,并制定相应的行动计划。
6. 周期时间分析:周期时间分析是一种用来测量和分析整个生产过程或价值流的时间的方法。
通过测量各个环节的时间,并分析其比例和关系,企业可以找到时间浪费和瓶颈,并采取相应的改进措施。
7. 柔性生产:柔性生产是一种以快速响应市场需求为导向的生产方式,通过灵活地调整生产线和生产能力,以适应需求的变化。
通过实施柔性生产,企业可以降低库存、提高交付速度和灵活性。
8. 产能平衡:产能平衡是指在不同工序间平衡产能,以避免过剩和瓶颈的发生,从而提高效率和质量。
通过进行产能平衡,企业可以合理安排生产能力,以满足顾客需求并避免资源浪费。
综上所述,以上提到的工具是精益生产中常用的工具,通过使用这些工具,企业可以识别问题,改进流程,并发现潜在的改善机会,从而提高生产效率和产品质量,降低成本,提高竞争力。
- 1、下载文档前请自行甄别文档内容的完整性,平台不提供额外的编辑、内容补充、找答案等附加服务。
- 2、"仅部分预览"的文档,不可在线预览部分如存在完整性等问题,可反馈申请退款(可完整预览的文档不适用该条件!)。
- 3、如文档侵犯您的权益,请联系客服反馈,我们会尽快为您处理(人工客服工作时间:9:00-18:30)。
视觉控制
就工具而言,精益制造重视大量运用视觉控制以方便操作员的工作同 时避免错误。视觉控制要求整个工作空间都要设立明显而直观的标志, 让每个雇员都能立刻知道目前在进行什么,了解进度,清楚看到什么 做的对,哪里出了问题。典型视觉控制机制包括警报信号、停工标签、 标志、以不同色彩区分的记号。举个例子如安灯(andon),采用电 子显示板提供可见的工位状态及信息以协调与工作中心相关的各种努 力,信号灯绿色(表示“运转”),红色(表示“停止”),黄色 (表示“注意”)。视觉控制的主要好处是简单直观,员工能迅速了 解流程是否正常运行。
机器故障对于车间是个严重的问题,因为在精益环境下一架机器发生 故障会引起整条生产线或流程中止。
全员生产维护 (TPM)
相应地,TPM 和其他先进企业资产管理(EAM)提高设备可靠性,从 而改善可用性,缩短停工期,减少废品(以及处理废品而浪费的时 间),提高机械公差(从而提高质量)。作为更进一步的辅助工具, 诊断管理功能可以自动识别当前维护战略的失效状态,从而触发持续 改善审查。这通常要求支持可靠性驱动的维护(RDM),巩固TPM 战 略。最后,具备同步维护和生产计划功能的企业系统可以最大化可用 的生产时间,提高生产能力和总设备效能(OEE)。
全员生产维护 (TPM)
精益制造更进一步要求制造商通过应用全员生产维护(TPM)来提高 设备生产率,TPM 是一整套的技术,由日本丰田集团中的电装 (Denso)公司首先提倡,包括了修复性维护和预防性维护,加上不 断适应、修改、改进设备来增强灵活性、减少物料搬运பைடு நூலகம்促进连续流 程。TPM 是操作员导向的维护,全体有资格的员工参与所有维护作业。 其目标,是与上述的5S 共同确保资源可用性,通过消除机械相关的事 故、缺陷或故障,因为这些会逐渐侵蚀车间效率和生产力。包括准备 与调整损失、闲置与小规模停工、运行速度下降、缺陷、返工及启动 期产量损失。
单元式制造
从维护到制造流程,精益哲学传统上依靠单元式制造。单元式制造是 一种制造流程,利用单一生产线或机器单元及仅在该线或单元工作的 操作员生产出系列零件族。制造单元,按照人类工程学原理重新设计 工作环境,将工人为获取完成工序所需的零件、补给或工具所付出的 努力降到最小,这常常取代传统的线性生产线,使得公司能以更小的 批量更连续的流程生产出更高质量的产品。有一个相关的概念是并行 (nagara),这是个日语词,描绘一种生产体系,在这种并行生产体 系中同一个操作员同时进行几个看起来不相干的作业。如今,精益思 想已经超越了单纯的单元式和产品分组生产。
精益生产的12 种工具
对付浪费的工具和实践长期以来人们采用下面约12 种精益制造的基本 技术工具和实践来控制或消除某些种类的浪费。请注意这并不是份详 尽的清单,清单中的各项也不是按照重要程度来排序的。
5S
这里要讲到的第一种实践源自产生精益制造的同一个日本系统。5S 是 组织、清洁、发展并保持生产工作环境的方法,用于创造一个更有条 理更有效率的工作空间。5S 的基本原理是清洁的工作空间会提供更安 全更有利于生产的环境同时促进优良商业道德与行为。这五个以“S” 为开头的词是员工的行为准则,员工必须遵循这些准则以创造一个适 合精益生产的工作环境。第一个词,整理(日语seiri)指区分需要的 及不需要的物品,并将不需要的物品移走。第二个词,简化、整顿或 者分类清理(日语seiton)意为将物品整洁地排列待用。擦亮、清扫 或擦洗(日语seiso)指的是清扫工作区,确立所有权和责任,同时标 准化、系统化或日常化(日语seiketsu)意为将上述努力像清单那样标 准化,将上述整理、简化、擦洗的三项原则在日常基础上执行。最后 是保持(日语shisuke),就是总是遵循前四项S 以形成遵守纪律的文 化,不断重复5S 原则直至其成为员工生活的一部分。
标准化工作
知道要执行什么步骤和知道该步骤运行正常,两者都是同等重要的。 为了确保实现产品质量级别、一致性、有效性及效率,有必要采用写 成文件的分步骤流程或者标准作业程序(SOP)来减少错误和接触时 间。尽管标准化工作建立了明确规定工人和机器操作的有用文档,标 准化工作在精益制造工具中是最不受到重视的。这些明确规定的操作 能帮助工人在制造流程中应用最佳实践。标准化工作同时还能为持续 改善打好基础,因为记录成文件形式的流程更容易加以分析与改进。 为了阐释标准化工作,SOP 应该采用图片、文字、表格、标志、色彩 及视觉指示器向不同的工作组沟通一致的直观的信息。这种图形指示, 也被称为操作方法手册(OMS),解释特定生产线范围内依照事件顺 序(SOE)的每个步骤,还能设计并制作纸质或屏幕的视觉工作指导。
防差错
正如持续改善是精益制造的主要概念之一,防差错或日语中的pokayoke,是减少浪费的重要工具。防差错是从根源上防止错误的关键措 施。简而言之,防差错可以是任何装置、机制或技巧,它能防止错误 产生或者让错误显露出来以避免产品缺陷。防差错的目标是防止制造 缺陷的原因,或者确保经济有效地检查每个产品以防止有缺陷的产品 到达下游流程。例如,如果在组装作业中没有使用到每个正确零件, 探测装置就会发现有个零件未安装并停车,从而防止装配工人将不完 整的部件输送到下个位置或者开始另一项操作。
单数换装时间
因为精益制造要求制造商仅仅按照客户的需求进行生产,这就要以越 来越小的批次生产。这与传统的想法正好相反,那种认为基于经济订 单批量(EOQ)的大批量比起包括设备切换的少量多批次更有效率的 想法其实是种错误的见解。长运行周期意味大库存,大库存会占用大 量资金,并让客户为成品和服务等待更长时间。这种小批量的趋势要 求缩减整个制造流程上的换装和切换时间。单数换装时间(SDS)想 法体现为在不到10分钟的时间内完成换装作业(例如敏捷筛分、对内 部和外部流程作业的优化排序、给工作台或传送装置加装轮子、液压 夹具、把手与快速闭锁装置等等)。与此相关的概念是一分钟换模术 (SMED),这种换装时间少于10 分钟的概念,最早由新江滋生 (Shigeo Shingo)于1970 年在丰田公司内部倡导。
另一项工具是模拟,它能帮助降低维护相关的浪费。通过支持模拟, 先进服务管理系统一般能根据生产计划安排维护并根据实际完成的生 产自动更新维护计划(电子链接设备自身的运转时间仪到计划维护 上)。
全员生产维护 (TPM)
目的是消除下列“六大”维护相关的浪费。 1. 设备停工 2. 安置和调整 3. 小规模停工和闲置 4. 计划外的停工 5. 由于机器错误制造不合格品所花的时间 6. 启动期的不合格品