第8章 混炼工艺
第八章 炼乳的加工

九、振荡 如果灭菌操作不当,或使用了热稳定性较低 的原料乳。则淡炼乳常常出现软的凝块。振荡可 使凝块分散复原成均匀的流体。使用振荡机振荡, 应在灭菌后2~3d内进行,每次振荡1~2min,通常 1min以内。 十、保温检查 淡炼乳出厂之前,一般还要经过保藏试验。 可将成品在25~30℃下保温贮藏3~4周,观察有无 膨罐,并开罐检查有无缺陷。必要时可抽取一定 量的样品于 37℃下保藏7~10d,并加以观察及检 查。保温检查合格的产品即可装箱出厂。
• 砂状炼乳 • 褐变 • 盐类沉淀
第二节 淡炼乳的生产
• 淡炼乳是将牛乳浓缩至原容积的1/2.5后, 装罐、密封,并经灭菌的制品。淡炼乳需 经高温灭菌,故维生素B、C受到损失,如 果加以补充,则其营养价值几乎与新鲜乳 相同。而且由于经高温处理,使其成为软 凝块乳。经过均质处理,使脂肪球微细化, 因而容易消化吸收。
五、调整黏度及防止变稠
• 过热处理:在浓缩将近终点之前直接吹入蒸气,使 罐内温度上升到75~85℃,再继续浓缩达到要求的 浓度。 • 添加一部分前批的成品 :在预热时按原料乳3%加 人经过8~12个月以上贮存的炼或在40~45℃保藏 7~10d,则在产品保藏中可以抑制黏度上升。 • 均质处理 :原料乳在预热前或预热后通过均质可 使脂肪球变小,增加与乳蛋白质的接触面积,从而 提高制品的黏度,并缓和变稠现象。 • 添加稳定剂或缓冲剂 :为了防止变稠,可在产品 中添加柠檬酸钠、磷酸氢二钠或磷酸氢二钾等。
六、冷却及乳糖结晶
1.冷却的目的 加糖炼乳的冷却不仅使浓缩乳达到冷 却的目的,同时尽量使过饱和的乳糖呈微 细的结晶析出。也就是说,防止产品出现 砂状结晶而使组织细腻。当结晶时,结晶 越快则晶体越小,但是溶液中乳槽的浓度 是随着晶体的形成而减低,这就使得进一 步的结晶过程减缓,由于结晶过程速度减 缓,结果形成了大的结晶。
混炼胶生产工艺

混炼胶生产工艺混炼胶是将天然橡胶或合成橡胶与添加剂等原料混合,经过炼胶机的拉、剪、折等作用,使其成为固态胶料的工艺过程。
混炼胶主要分为两种类型:开炼和封闭式混炼。
开炼是将胶料与添加剂放入开炼机中,通过辊子的旋转和挤压,使胶料与添加剂彻底混合。
开炼机分为两辊机和三辊机,其中三辊机是最常用的。
开炼机中的三个辊子分别是主辊、副辊和辅助辊,通过调整辊子的转速和间距,可以控制胶料的温度、时间和剪切力。
开炼的优点是可以灵活调整添加剂的比例和炼胶温度,适用于生产各种不同性能的橡胶制品。
封闭式混炼是将胶料和添加剂放入封闭式混炼机中,通过高速旋转的螺杆将胶料和添加剂挤压、剪切和折叠,使其混合均匀。
封闭式混炼机具有密闭性好、能耗低、工艺简单等优点,适用于大批量生产相同性能的胶料。
混炼胶的生产工艺主要包括以下几个步骤:1. 胶料准备:将天然橡胶或合成橡胶切碎,并经过清洗、脱水等工艺处理,除去杂质和水分,使其达到生产要求。
2. 添加剂配方:根据橡胶制品的要求,制定合适的添加剂配方,包括硫化剂、活性剂、助剂等。
3. 混合:将胶料和添加剂按照一定比例放入混炼机中,通过机械作用,使其混合均匀。
4. 调温:根据橡胶和添加剂的特性,控制炼胶机的温度,使其达到最佳炼胶温度。
5. 炼胶:开炼或封闭式混炼机通过旋转、挤压、剪切等作用,将胶料和添加剂进行彻底混合,形成固态的胶料。
6. 切割和离心:经过炼胶机的处理,胶料被切割成块状,并通过离心机的旋转,将胶料中的水分去除。
7. 成型:将炼胶后的胶料放入成型机中,进行定型,形成成品。
混炼胶生产工艺的关键是控制炼胶机的温度、时间和剪切力。
温度过高或时间过长会导致胶料老化,性能下降;剪切力过大会使胶料的结构破坏,影响性能。
因此,在生产中需要严格控制这些参数,以获得符合要求的胶料。
混炼胶混炼工艺最终版本

DF混炼胶生产工艺发布日期:2012年3月12日实施日期:批准人:批准日期:实施日期:文件编号:发放编号:控制状态:持有人:大连巅峰集团2012年3月12日综述混炼胶概念及质量要求通过适当的加工将配合剂与生胶均匀的混合在一起制成质量均一的混合物,完成这一加工操作的工艺过程叫做混炼,混出的胶料叫混炼胶。
对混炼胶质量有两方面要求:一、是胶料应具有良好的物理机械性能。
二、是胶料本身具有良好的工艺加工性能。
为保证混炼胶质量、结合本公司的实际情况特此制订炼胶工艺规程。
炼胶工艺规程包括以下方面:①、生产工艺流程图②、原材料加工工艺③、配料工艺④、切胶工艺⑤、塑胶工艺⑥、混炼工艺⑦、一段,二段混炼胶在每一种胶料中应用⑧、返炼操作方法及要求⑨、不合格胶处理1、生产工艺流程图天然胶合成胶配合剂干燥扒皮加工切胶切胶塑炼检验(可塑度)配合制混炼胶取片检验制片沾浆冷却挂牌存放2、原材料加工工艺2.1 粉碎:固体的石蜡每块不大于50g.石油树脂、古马龙每块不大于50g, 松香每块不大于50g,所用设备为人工锤或万能粉碎机。
2.2筛选:硫磺供应厂家要用自制滚动筛选机筛选标准为100目全过。
2.3 加热过滤:机油加热120℃、时间24H,要求供应厂家要过滤120目×2。
2.4加热:松焦油10月1日到次年5月1次加热100℃以上,时间:24H 2.5干燥:烘干室温度: 50~~60℃。
烘干时间:24H~72H烘干范围: 天然胶 (5月1日-10月1日不烘胶).2.5.1技术要求:(1) 天然胶送加温室前必须将表面泥砂、木屑等杂质清理干净,发霉、发臭、腐烂变质的胶块不得送入车间。
(2) 被加温的生胶不得直接接触暖气片等加热热源,防止局部过热流淌。
(3) 生胶等级不得混杂,胶块不落地。
(4)加温后的生胶按先后顺序使用.2.5.2质量标准:(1) 烘完的生胶应保证内外温度均匀一致, 中心温度不低于25℃(2) 烘完的生胶表面无发霉变臭、无杂物和水迹。
钢铁是怎样炼成第八章的主要内容

钢铁是怎样炼成第八章的主要内容第八章:钢铁炼制一、钢铁炼制的历史1、中国古代钢铁炼制(1)早在春秋时期,由于技术发展,已有不完全熔炼的钢铁制造,打击成以太刀、镰刀、斗钱、棍棒等武器;(2) 汉代出现著名的白铁,可用于炼锅,在古代经常用于冶炼金属;(3) 唐代出现大规模的冶炼,形成了熔炼、浇铸、连铸等工艺,制成了著名的“燕山铁”,也产生了许多优秀的钢铁铸造工艺。
2、欧洲古代钢铁炼制(1) 早在古希腊时期,就有钢铁制造,经过熔解,可以生产耐磨性能良好的宝曜钢铁;(2) 公元前1000年,古罗马拥有大规模的钢铁炼制体系,著名的“罗马钢”是由它所制造;(3) 中世纪至文艺复兴时期,欧洲的冶炼技术得到了大大的提高,大量的新型钢铁都出现在市面上。
二、钢铁炼制的过程1、熔炼(1) 钢铁炼制过程中,熔炼是最基本的步骤,它是采用火焰烧结法,将有色金属和有机物质熔融,得到金属料的工艺过程;(2) 熔炼时,需要有 mix 、blast 、furnace 等器材来支持;(3) 在熔炼过程中,需要保持温度、控制熔化时间、打碎团块,并熔炼分解成液体;(4) 熔炼的具体步骤主要有:添加金属原料→熔融分解→蒸气化→熔炼焙烧→清除杂质→冷却固化→采样测试→清洗包装。
2、浇注(1) 浇注是将熔炼得到的金属液,经过浇注机械装置将其浇入模具内,使模具内的铸型完成成型,然后冷却成型的工艺;(2) 浇注的步骤包括:加热钢铁料→装置模具→浇注金属料→冷却固化→锻模出品→试验抽检→消磨磨光→包装出厂;(3) 浇注机械可分为木模注、多出料口下型、舵轮机油门系统、浓度系统等,模具可根据形态和尺寸进行不同的设计,包括金属模具、砖模具、外轮廓法兰或断铣法兰,甚至还有了模具加工系统,使模具的成型更加规范,产品性能更加稳定。
3、连铸(1) 连铸工艺有得天独厚的优势,是一种“从一连”铸造钢材的连续工艺,是从一个连续凝型机液态化学铸造,一次不断地制造出批量品种;(2) 主要由三个部分组成:熔炼、凝固和成型,凝固和成型的步骤由凝型机周转到冷却槽实现;(3) 优点在于,大大减去了用量,更省时间,更省能源,提高了产量;(4) 连铸的弊端是,不能把某种特定的花纹带到产品上,需要研磨和清洗环节,更多耗时耗能耗费。
橡胶混炼工艺介绍.优质PPT文档

内容简介:
混炼工艺是橡胶制品生产过程的第一步,它 的任务就是将配方中的生胶与各种原材料混合 均匀,制成符合性能要求的混炼胶胶料,包括生胶 的塑炼加工和胶料的混炼加工两个主要过程.塑 炼加工是为混炼加工做准备的.故塑炼和混炼通 称为炼胶工艺.
3.机械增塑法 利用机械的剪切破坏作用增加生胶可塑性的方法
叫机械增塑法。该方法使用最广泛,可以单独用于塑 炼加工。若与物理增塑法或化学增塑法配合使用,可 进一步提高机械塑炼效果和生产效率。
一、生胶的增塑方法和机理
(二)、生胶塑炼的增塑机理
1.机械力的作用 高分子链之间的整体相互作用远远超过其单个
C-C键能。机械力作用尚未克服大分子链之间相互作 用之前,早已超过了分子链中单个化学键的键能,从 而使其断裂破坏。
橡胶混炼工艺介绍
作用及要求
混炼胶对胶料的后序加 工和制品的质量起着决定性 的作用,混炼不好,胶料会出 现配合剂分散不均匀、可塑 度过高或过低、焦烧、喷霜 等现象,使后序加工难以正 常进行,且会导致产品质量 不均.所以,混炼工艺是橡胶 制品生产中最重要的基本工 艺过程之一. 另外针对挤出制品尤其是外 观件来说,混炼工艺的好坏 尤其决定挤出产品的好坏, 譬如表面麻点焦烧粒等
利用低分子物质对大分子的化学破坏作用降低其 选胶 生胶进厂后在加工前需进行外观检查,并注明等级品种,对不符合等级质量要求的应加以挑选 和分级处理。
所以,混炼工艺是橡胶制品生产中最重要的基本工艺过程之一.
黏度,增加其塑性流动性,称为化学增塑法。以上两 以上两种方法都不能单独用来塑炼生胶,只能用其他塑炼方法配合使用,起到辅助增塑作用。
一、生胶的增塑方法和机理
聚合物合成工艺-第8章

8.2实施方法
8.2.2 溶液缩聚
将单体和聚合物溶解在溶剂中进行缩聚反应的方法。
该法适用于不宜采用熔融缩聚法生产的缩聚物,如芳族、
芳杂环类缩聚物的生产。
8.2.3界面缩聚 将可以进行缩聚反应的两种有高反应 活性的单体分别溶于两种互不相溶的溶剂当中,使反应
在两相的界面上进行的方法,如PC的生产。
物,如PET、PBT、尼龙6、尼龙-66等。 先采用熔融缩聚生产预聚物,当分子量达到一定程度,
体系的黏度太大,用熔融缩聚法已经很难再使反应继续 进行下去时,改用固相缩聚法进行进一步的缩聚。
固相缩聚的一般工艺 将具有适当分子量的预聚物粒料
(颗粒体积一般要求<0.03cm3)或粉料,在设备中于真 空下或惰性气流中,在Tg~Tm之间进行反应。
γ=NA/NB
1,Xn=1/(1-p)
②原料的配比及纯度要求严格
设反应的转化率为100%
P
1时,Xn=(1+γ)/(1-γ)
缩聚反应的工艺特点与理论基础
③封端的重要性
单官能团物质的封端作用
A.调节分子量 B.起黏度稳定剂的作用
封端后的大分子不再进行缩合反应,可以起到分子 量稳定剂的作用;否则两官能团之间还会在成型加 工时进行反应,使黏度增加(进一步缩聚)或缩小 (发生解聚)。
各种聚合方法的比较
特点 优
点
熔融缩聚
生产工艺过程简单,生 产成本低。可连续法直 接纺丝。聚合设备的生
产能力较高。
溶液缩聚
可降低反应温度避免单体 和产物分解。反应平稳, 易控制。聚合物溶液可直
接用作产品。
界面缩聚
反应条件缓和, 反应不可逆,对 两种单体的配比
第八章 电炉炼钢

⑶ 熔化期 目的:将固体炉料熔化成液体,以便在氧化期和还原期改 变钢液成分,去除有害杂质(硫、磷、碳、氧、氮和氢)和非金 属杂物。在熔化期还应减少钢液的吸气。去除部分硫、磷,去 除炉料中的硅、锰、铝等元素。 熔化期:指从通电开始到炉料全部熔清为止。熔化期占总 冶炼时间的50%~70%左右,耗电量占全炉总电耗的60~80 %左右。 任务:在保证炉体寿命的前提下,将抉状的固体炉料快速 熔化,并加热升温至氧化温度;造好熔化期炉渣,以便稳定 电弧,早期去磷,减少钢液吸气与挥发。 熔化过程分为:启弧、穿并、电极抬升、熔化未了四个阶 段。
④ 温度控制 还原期必须控制好钢水的温度,使脱氧、脱硫能顺利地进行, 脱氧产物及其他的非金属夹杂物能从钢液中分离,出钢后能 顺利浇注。一般出钢温度比钢的熔点100~140℃。 ⑤ 终脱氧和出钢 当钢液脱氧良好,成分和温度合格,熔渣流动性良好时,即 可进行终脱氧操作。常用的终脱氧剂为铝,在出钢前2 ~ 3 min用铁棒插入钢液。 电弧炉出钢方法有两种:先出钢后出渣或者钢渣混出。
⑵ 装料 装料对冶炼时间,特别是熔化时间、合金元素的烧损及炉衬 的寿命都有很大影响。 装料应做到:快速装料,炉料密实,布料合理,并尽可 能一次装完。 ① 快速装料 目前大多数采用炉顶装料。炉盖移开后,炉膛温度从1500℃ 左右迅速降低到800℃左右,因此,必须快速加料并且尽可 能一次加完,避免大量散热。
第八章 电炉炼钢
8.1 8.2 8.3 8.4 概述 电弧炉炼钢设备 碱性电弧炉氧化法冶炼工艺 电弧炉炼钢的新技术及发展趋势
8.1 概述
常用冶金电炉有:电弧炉、感应炉、电渣炉等,目前世界 上95%以上的电炉钢是电弧炉尤其是碱性电弧炉冶炼的。 电炉炼钢:主要指电弧炉炼钢(指碱性电弧炉炼钢)。 电弧炉炼钢原理:主要是利用电极与炉料间放电产生电弧 发出的热量来炼钢。 分类:氧化法、不氧化法和返回吹氧法。
橡胶混炼工艺介绍
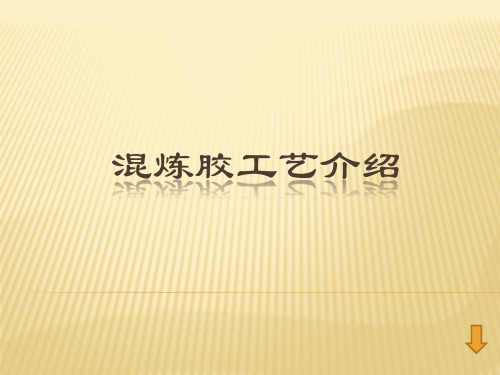
塑炼的目的:
生胶塑炼的目的主要是使胶料的 工艺性能得以改善。塑炼后的生胶弹 性减小,可塑性增大;混炼时配合剂 容易在胶料中混合分散均匀,压延挤 出速度快,收缩率小,并改善胶料对 骨架材料的渗透与结合作用;硫化时 容易流动充满模型。随着塑炼程度的 增加,其硫化胶的力学强度、耐磨耗 和耐老化性能降低,永久变形增加, 使硫化胶物理机械性能受到损害。塑 炼程度越大,损害程度也越大。故生 胶的塑炼 程度必须根据胶料的加工 性能要求和硫化胶性能要求综合确定。
二、机械塑炼工艺
2、 开炼机塑炼工艺
(1).包辊塑炼法 胶料通过辊距后包于前辊表面,随辊筒转动重新回到辊筒
上方并再次进入辊距,这样反复通过辊距,受到捏炼,直至 达到可塑度要求为止。
二、机械塑炼工艺
2、 开炼机塑炼工艺
(2).薄通塑炼法 薄通塑炼法的辊距在1mm以下,胶料通过辊距后不包辊,
而直接落盘,等胶料全部通过辊距后,将其扭转90°角推到 辊筒上方再次通过辊距,这样反复捏炼,直至达到要求的可 塑度为止。
一、生胶的增塑方法和机理
(二)、生胶塑炼的增塑机理
4.化学塑解剂 的作用 在生胶机械塑炼过程中,加入某些低分子化学物
质可通过化学作用增加机械塑炼效果,这些物质称为 化学塑解剂。
一、生胶的增塑方法和机理
(二)、生胶塑炼的增塑机理
5.电与臭氧的作用 用开炼机塑炼时因辊筒表面与胶料之间的剧烈摩
擦会产生静电,并在胶料表面积累,到一定程度便产 生静放电,生成臭氧和原子氧,对橡胶的氧化裂解作 用更大。
d.在保证胶料质量的前提下,尽可 能缩短混炼时间,以提高生产效率, 减少能量消耗.
内容简介:
混炼工艺是橡胶制品生产过程的第一步,它 的任务就是将配方中的生胶与各种原材料混合 均匀,制成符合性能要求的混炼胶胶料,包括生胶 的塑炼加工和胶料的混炼加工两个主要过程.塑 炼加工是为混炼加工做准备的.故塑炼和混炼通 称为炼胶工艺.
- 1、下载文档前请自行甄别文档内容的完整性,平台不提供额外的编辑、内容补充、找答案等附加服务。
- 2、"仅部分预览"的文档,不可在线预览部分如存在完整性等问题,可反馈申请退款(可完整预览的文档不适用该条件!)。
- 3、如文档侵犯您的权益,请联系客服反馈,我们会尽快为您处理(人工客服工作时间:9:00-18:30)。
四、结合橡胶 • 2.影响结合橡胶生成量的因素 ①填料性质 a .表面性质 b. 粒子大小 c . 结构性 ②生胶的化学活性 ③混炼时间 ④混炼温度
第四节 混炼胶的质量检查及质量毛病
一、意义 二、混炼胶 的快速检验 保证胶料在以后各工序中的工 艺性能和最终产品的质量,以及发 现问题能及时补救。
1.测试项目 ★可塑度测定 ★比重测定 ★ 硬度测定
2.检验结果 及原因分析举例
检验结果及原因分析举例 序 料重 号 1 2 3 4 5 正常 正常 增大 增大 偏低 比重 可塑度 有高 有高 有低 有低 正常 正常 大 小 正常 小 大 正常 硬度 有高 有低 有高 有低 高 低 硫化 不熟 低 可能 处理方法 原因 混炼不均 补充 匀 混炼 补充 硫化剂分 散不均 混炼
六、常见的质量毛病及其产生原因
配合剂结团 喷霜 焦烧 欠硫
二、开炼机混炼的工艺条件
6.加料顺序 • 一般原则: 用量少,难分散的配合剂先加;用量大,易分 散的后加;为了防止焦烧,硫黄和超速促进剂一 般都放在最后加入。 • NR胶料通常采用的加料顺序: 塑炼胶,再生胶,母炼胶→固体软化剂→促进 剂、活性剂、防老剂、防焦剂→补强填充剂→液 体软化剂→硫黄、超速促进剂
填料多加 生胶或软 化剂多加 少加或漏 加硫化剂 少加硫化 剂 实验室进 一步检验
同上 同上 同上
6
偏低
正常
正常
三、用硫化仪进行快速检验 (实验室、定性、实用) 硫化仪是一种测量胶料流动性能和硫化特性 的新型仪器,可连续地测出生胶料的初始粘度, 焦烧时间,正硫化时间,硫化速度,硫化平坦性 等工艺参数。 四、混炼胶分散程度的测定(实验室、定性) 五、混炼胶的物理机械性能测定(实验室)
二、粉状 配合剂的干燥
三、粉状 配合剂的筛选
其目的是除去混夹在配合剂 中的机械杂质,配合剂本身的 大颗粒及结团等。 筛选设备有振动筛、鼓式筛 选机和螺旋式筛选机等。 低熔点固体软化剂可将其加 热熔化,达到干燥脱水和降低 粘度作用,再经过滤去掉其中 的机械杂质。
四、软化剂 的预热和过滤
五、膏剂与母炼胶的制造
磨耗/(cm3/106转)
2
4
8
16
100 11.7 25 530 —
71.4 99.3 100 14.3 12.6 12 21.6 25.5 26 460 530 540 289 142 136
• 分散率:橡胶颗粒团块小于6um的百分数
四、结合橡胶
• 混炼时,橡胶分子能与活性填料(主要是炭 黑)的粒子结合生成不溶性的炭黑—橡胶凝胶, 称为结合橡胶。 1. 形成结合橡胶的原因
• 1. 定义 ①膏剂:液体软化剂与易飞扬配合剂混合制成 的膏状混合物。 ②母炼胶:某些配合剂以较大的剂量预先与生 胶混炼在一起制成简单组分的混合物料,称为 该配合剂的母炼胶。最常见的有促进剂母胶、 炭黑母胶、化学塑解剂母胶等。 • 2.膏剂的制造 配合剂:软化剂=2.5:1 • 3.母炼胶的制造 干法 ;湿法
τm ——表示橡胶由粘弹性变形转为完
全塑性流动所需要的时间。
2. 温度 3.切变速率(外力作用速率)
ቤተ መጻሕፍቲ ባይዱ
二、配合剂的混炼性及表面活性剂的作用
1.亲水性 的配合剂 2.疏水性 的配合剂 3.添加表 面活性剂
其粒子表面的分子特性与生胶 不同,两者界面极性相差较大, 不易被橡胶所湿润。
其表面张力与油相近,能与油亲和, 易为橡胶所湿润,混炼时易分散。 提高亲水性的配合剂与橡胶的 亲和性,改善其分散性能。此外, 表面活性剂又是一种良好的稳定剂。
四、结合橡胶
• 3.结合橡胶的作用 ①有利于配合剂在胶料中分散 ②有利于填料与橡胶作用
五、混炼胶的结构
混炼胶是由粉状配合剂分散于生胶中组成的多相 混合分散体系 。
分散系按分散质颗粒大小分类 类型 分散质颗粒直径 粗分散体(悬浮液,乳浊液) >100nm 溶胶(胶体溶液) 1~100nm 分子分散体系(高分子溶液,真溶液) <1nm
• 三.密炼机的混炼工艺 • 优点:混炼容量大,混炼时间短,效率高; 投料、捏炼、加压和排料操作易于机械化、 自动化,劳动强度低,操作安全性大,配 合剂损失、粉尘飞扬状况得到改善,胶料 质量和环境卫生条件好。 • 缺点:混炼时温度较高,对温度敏感的胶 料易发生焦烧,需要对排胶进行补充加工。
三、密炼机的混炼工艺
三、填料混炼的工艺过程 • 1.湿润阶段(吃粉) • 要求: 生胶:可塑度大,门尼粘度低, 流动性好。 炭黑:粒子大(比表面积小), 结构性低。
附聚物
三、填料混炼的工艺过程
• 2.分散阶段
• 要求: C 生胶:可塑度小 炭黑:粒子大,结构性高。
Re
•
炭黑在胶料中的分散程度对性能的影响
混炼时间/min 分散率/% 300%定伸应力/MPa 拉伸强度/MPa 拉断伸长率/%
二、生胶的混炼性
㈠生胶混炼时常出现的流动状态
第一种状态:不能紧包前辊 原因:混炼温度低,胶料的可塑性小。
第二种状态:紧包前辊 原因:温度适宜,胶料的可塑性中。 第三种状态:脱辊——出兜 原因:温度略高,胶料的可塑性略大。 第四种状态:粘流态包辊 原因:温度太高,可塑度太大
(二)影响因素
1.生胶本身的粘弹性能
• 2.两段混炼 • (1)传统两段混炼法 • 用高速高压密炼机进行第一段的粗混炼,使 橡胶与配合剂混炼制成母胶,下片后经停放 一段时间后,再送入低速密炼机加硫黄和促 进剂进行混炼,再经压片机补充加工胶片。 • (2)分段投胶两段混炼法 • 第一段混炼时,把80%左右的生胶投入进行 与传统两段混炼法一样的混炼,制备母胶。 在第二段混炼时将剩余20%左右的生胶投入 母胶中混炼,均匀后排胶。
六、配合剂的 称量与配合 ⑴要求: 精密、准确、不漏、不错 ⑵称量操作 手工称量 ;自动称量
第二节 混炼工艺
• 一 混炼胶的结构 • 混炼胶是由粒状配合剂(如炭黑、促进剂、填充 剂等)分散于生胶中组成的分散体系。在分散体 系中,生胶的分散呈连续状态,称为分散质,粒 状配合剂为分散相。 • 混炼胶不同于一般的胶体分散体系: • (1)橡胶的粘度很高,胶料的热力学不稳定性在 一般情况下不太显著; • (2)某些组分(如再生胶、增塑剂等)与橡胶能 互容,从而构成了混炼胶的复合分散介质; • (3)粒状配合剂(如炭黑合促进剂等)与橡胶在 接触界面上产生了一定的物理和化学结合,这对 胶料和硫化胶的性能起着重要的影响。
N
α
O
Q
P
O’
τα
N’
后辊
前辊
要使T>Q
二、开炼机混炼的工艺条件*
1.装胶容量:理论量 V=0.0065DL 2.辊距:4~8mm为宜,实验室2~3mm 3.辊速和速比 辊速一般为16~18 r/min 适宜速比:1:1.1~1.2 4.辊温:一般控制50~60℃, 前后辊温度差ΔT=5~10℃ 5.混炼时间:应根据胶料的配方和操作的 熟练程度而定。
密炼机混炼 的工艺条件
• • • •
(一)密炼机混炼工艺操作方法 1.一段混炼法 (1)传统一段混炼法 把塑炼胶和各种配合剂逐步分次加入,每 次加料后,放下上顶栓,加压程度视具体 情况而定。 • 传统一段混炼法的混炼程序一般为:
橡胶(生胶、塑炼胶、再生胶等)→ 硬脂酸 → 促进剂、活性剂、防老剂 → 补强填充剂 → 液 体软化剂 → 排胶 →压片机加硫黄和超速促进剂 → 下片 → 冷却、停放
• (2)分段投胶一段混炼法 • 分批加入生胶,以强化炭黑的分散,达到 改善合提高胶料的工艺性能及硫化较的物 理机械性能。 • 具体操作:投入60%~80%生胶和配合剂 (硫化剂和超促进剂除外),在70~120℃ 混炼温度下,混炼到总混炼时间的70~80%, 再把其余生胶并同硫化剂和超促进剂一起 投入,再混炼1~2min后,排胶下片。
混炼胶与一般悬浮液不同的特征
混炼胶具有动力学稳定性,不具有热力学稳定性
第三节开炼机的混炼工艺
• 一般操作方法是先让生胶包于前辊,并在 辊距的上方留有适量的存胶,再按规定加 料顺序往存胶上依次加入配合剂。当配合 剂完全混入生胶后立即进行切割翻炼,以 保证混合均匀,再经薄通后下片。
– 混炼过程分为包辊、吃粉和翻炼
密炼机混炼 的特点 密炼机的 混炼历程 周向流动 轴向流动 •湿润阶段 •分散阶段 •捏炼阶段 (塑化阶段)
装胶容量:可根据填充系数f值来确定 上顶栓压力:一般控制在6×105Pa以上 转子转速与混炼时间:40~60r/min, 4~5min 混炼温度: 100~130℃。 加料顺序:生胶 → 活性剂、固体软化剂、防老剂、 普通促进剂→炭黑→液体软化剂→硫磺和超速促进 剂
– 翻炼时,周向:混炼最均匀;轴向:不均匀; 径向:均匀性最差
周向:混炼最均匀; 轴向:不均匀; 径向:均匀性最差
一、开炼机混炼过程
1.包辊 2.吃粉
3.翻炼
(1)斜刀法 (八把刀法)
即湿润阶段。 四种包辊状态: 咬胶角(接触角α) (2)三角包法 控制条件: 不能包辊 紧包前辊,辊筒上方有 紧包前辊 (3)走刀法 适量的堆积胶. 脱辊 (捣胶法) 粘流态包辊 (理论上要堆到32~45°之间) 吃粉时,在胶料包辊,加入配合剂之前,要使辊距 上端保留适当的堆积胶,适量的堆积胶是吃粉的必 要条件。
• 3.逆混(倒混)炼法 • 先把除硫黄和促进剂以外的所有其它配合 剂全部装入密炼机中,然后再投入生胶进 行混炼。 • 优点:充分利用装料容积,改善分散性, 缩短混炼时间。适用于生胶挺性差和高炭 黑合高油量配合胶料的混炼,如BR、 EPDM等。