硅橡胶混炼工艺
硅胶混炼胶生产工艺(防静电)

硅胶混炼胶生产工艺1、备料根据生产单排出胶料的生产顺序,并根据密炼岗位实际的生产情况安排生产。
在称量生胶或白炭黑之前应仔细阅读工艺配方表,确定所需原料的种类、型号指标及数量,以保证原材料的准确性。
称量前应先校对称量器械,以保证称量的准确性。
在称量过程中,不可将硬物(如切胶刀、小刀、秤砣、簸箕等)或其它物品放在生胶桶或白炭黑袋上,以防止误入捏合机中。
在所有原料都备齐之后,应核对原料的种类、型号指标及数量,并对其原始批号作出完整记录,以备查验。
在控制备料机缸体上升时,应面对控制台,以防止按错控制键。
将缸体上升后,将生胶及固态配合剂一次性投入缸中,白炭黑及液态配合剂应按生产配方工艺单规定分批加入。
在投料过程中,不可将硬物(如切胶刀、小刀、秤砣、簸箕、扳手等)或其它物品放在缸沿上,以防止掉入缸中而损坏机器。
缸内的胶料在机器剪切作用下成为较大块状后方可再次投入白炭黑,在投白炭黑过程中,应注意防止包装袋上的杂质被带入胶料中。
当白炭黑全部投入且胶料已成为大块后,便可进行真空热炼阶段。
机器在运转过程中,切不可开缸盖观察,以防止白炭黑或胶料喷出。
出料时,在机器转子未停稳之前,不可将手或其它工具伸入机器内取料。
2、养生对于某些性能要求较高或特殊工艺配方的胶料在备料后应进行养生。
养生是将捏合机所出的备料放置24小时以上,目的是让生胶大分子链慢慢的舒展开,使其与白炭黑达在物理或化学方面达到更好的融合,从而提高胶料的综合性能。
在实际操作过程中,由于料斗的数量较少,往往经过开炼机打卷后堆放于码板上,同时须将填写好的流程卡压好,整板养生胶上各批胶的流程卡应放在同一角上;整板养生胶应用塑料方片包好,并在最上面贴上写有本板养胶的型号、批号、及养生日期的标签。
3、真空密炼开机捏合过程中应密切注意料温。
当胶料捏合成大团,温度已超过130℃,应尽量控制料温,白炭黑补加完以后,须在白炭黑全部被“吃”掉后捏合5~10min 再开始抽真空,以防止胶料被抽散。
硅橡胶生产工艺流程

硅橡胶生产工艺流程硅橡胶是一种以二氧化硅(SiO2)为主要原料制备而成的橡胶,具有优良的耐高温、耐寒、耐候性能,因此广泛应用于航空、航天、电子、化工等领域。
以下是一种常见的硅橡胶生产工艺流程:1.原料准备首先,需要准备硅橡胶的主要原料,二氧化硅。
一般情况下,原料可以来自石英石的石英粉或石英砂,也可以利用硅石(如硅灰石)经酸浸提、电石法或硅酸盐合成法获得。
此外,还需要准备硅橡胶的固化剂、助剂和填充剂等辅助材料。
2.混炼将预先配好的原料放入混炼机(如开放式橡胶混炼机或密炼机)中进行混炼。
混炼的目的是将各种原料充分混合,并加热使得原料软化,使其更容易塑性变形。
混炼的温度和时间根据不同的工艺和产品要求确定。
3.成型混炼好的硅橡胶块通过热压或挤出等成型工艺,制备成所需的硅橡胶制品。
成型工艺的选择取决于产品的形状、尺寸和精度要求。
例如,对于平板、管材等简单形状的制品,常采用热压成型工艺;对于异型制品或高精度制品,可采用挤出工艺。
4.硬化成型后的硅橡胶制品进行硬化处理,使其具有良好的物理性能和耐用性。
一般来说,硬化是指在高温下进行的固化过程。
主要有两种硬化方法:自然硬化和热硬化。
自然硬化是通过长时间的自然老化使硅橡胶固化;热硬化则是通过在高温烘烤箱中加热硅橡胶制品,使其固化。
硬化时间和温度根据硅橡胶的类型和厚度确定。
5.喷涂或涂覆在一些情况下,硅橡胶制品需要进行喷涂或涂覆处理,以增加其表面的密封性和耐腐蚀性。
喷涂或涂覆材料通常是硅橡胶树脂或其他防护材料,通过喷涂或涂覆工艺施加到硅橡胶制品表面。
6.检验和包装以上是一种常见的硅橡胶生产工艺流程,具体的工艺流程可能会有所不同,根据不同的产品和生产要求进行相应调整。
混炼硅橡胶的配合技术_十_

SiO χ 9 SiO χ 6
C H3 C H3
31 101 41 2 添加有机硅表面活性剂
内径 16 mm 、外径 24 mm 的硅橡胶管 , 再连续 进入 250 ℃ 的热风硫化炉硫化 18 s , 观察硫化制 加成 型 挤 出 成 形 混 炼 硅 橡 胶 制 品 内 部 产 生 [ 106 ] 品有无气泡 。结果列于表 57 。 气泡 。 为比较 , 将混炼硅橡胶 11 中的聚醚改性硅 C H3 C H3 油换成 01 5 份结构如式 4 ( m = 10 , n = 5 , a = 6 , ( C H3 ) 3 SiO SiO χ m SiO χ n Si ( C H3 ) 3 b = 0 , R = C H3 ) 的聚醚改性硅油 , 其它相同 , C H3 C3 H6 O ( C2 H4 O ) a ( C3 H6 O ) b R 配成加成型挤出成形混炼硅橡胶 12 ; 将聚醚改 ( 4) 性硅油换成 11 0 份结构如式 4 ( m = 27 , n = 3 , a 添加结构如式 4 的 聚醚改性硅油可以抑制
在双辊机上返炼塑化 , 配成胶料 ; 然后 , 加入 11 0 份二叔丁基过氧化己甲酰 ( 结构如式 2) , 不 加 或 加 入 01 5 份 ( C H3 ) 3 SiO1/ 2 链 节 封 端 、 Si H 基含量为 11 6 mol/ 100 g 的甲基含氢硅 油 , 在双辊机上混合 , 配成挤出成形混炼硅橡胶 1~2 。将混炼硅橡胶与直径 41 0 mm 的镀锡软铜 芯线用挤出机挤出成形 , 制成硅橡胶层厚度为 1
不加氯铂酸二乙烯基四甲基二硅氧烷配合物其它相同配成混炼硅橡胶17进行性能评价结果列于表58ch3hch33siosio3ch3sio5ch3sich335表58有机过氧化物对加成型挤出成形混炼硅橡胶性能的影响混炼硅橡胶编号151617硅橡胶胶条有无气泡表里硬度差硅橡胶电线芯线附近硫化状况无无有0良好不好良好513111不需二次硫化的混炼硅橡胶混炼硅橡胶经过定形硫化后硫化剂的分解产物仍残留在硅橡胶制品中需经过热空气加热除掉这一过程称为二次硫化或二段硫化后硫化
硅橡胶混炼工艺

硅橡胶混炼工艺硅橡胶混炼工艺:1.开炼机混炼双辊开炼机辊筒速比为1.2~1.4:为宜,快辊在后,较高的速比导致较快的混炼,低速比则可使胶片光滑。
辊筒必须通有冷却水,混炼温度宜在40℃以下,以防止焦烧或硫化剂的挥发损失。
混炼时开始辊距较小(1~5mm),然后逐步放大。
加料和操作顺序:生胶(包辊)—→补强填充剂—→结构控制剂—→耐热助剂—→着色剂等—→薄通5次—→下料,烘箱热处理—→返炼—→硫化剂—→薄通—→停放过夜—→返炼—→出片。
胶料也可不经烘箱热处理,在加入耐热助剂后,加入硫化剂再薄通,停放过夜返炼,然后再停放数天返炼出片使用。
混炼时间为20~40分钟(开炼机规格为φ250mm×620mm)。
如单用沉淀白炭黑或弱补强性填充剂(二氧化钛、氧化锌等)时,胶料中可不必加入结构控制剂。
应缓慢加入填料,以防止填料和生胶所形成的球状体浮在堆积胶的顶上导致分散不均。
如果要加入大量的填料,最好是分两次或三次加入,并在其间划刀,保证良好的分散。
发现橡胶有颗粒化的趋势,可收紧辊距以改进混炼。
落到接料盘上的胶粒应当用刷子清扫并收集起来,立即返回炼胶机的辊筒上,否则所炼胶料中含有胶疙瘩而导致产品外观不良。
增量性填料应当在补强性填料加完之后加入,可采用较宽的辊距。
装胶容量(混炼胶):φ160mm×320mm 炼胶机为1~2 kg;φ250mm×620mm炼胶机为3~5kg。
硅橡胶在加入炼胶机时包慢辊(前辊),混炼时则很快包快辊(后辊),炼胶时必须能两面操作。
由于硅橡胶胶料比较软,混炼时可用普通赋子刀操作,薄通时不能象普通橡胶那样拉下薄片,而采用钢、尼龙或耐磨塑料刮刀刮下。
为便于清理和防止润滑油漏入胶内,应采用活动挡板。
气相白炭黑易飞扬,对人体有害,应采取相应的劳动保护措施。
如在混炼时直接使用粉状过氧化物,必须采取防爆措施,最好使用膏状过氧化物。
如在胶料中混有杂质、硬块等,可将混炼胶再通过滤胶机过滤,过滤时,一般采用80~140目筛网采用开炼机混炼,它包括:1)包辊:生胶包于前辊;2)吃粉过程:把需要加入的助剂按照一定的顺序加入,加入时要注意堆积胶的体积,少了难于混合,多了会打滚不容易混炼。
二、炼胶工艺

二、炼胶工艺本工艺主要包括有混炼胶的(密)混炼、热炼、加硫、返炼等四个工序的生产工艺。
通过对生胶及其配合剂的混合、分散、热处理等过程,使配合剂完全而均匀地分散到生胶中,并产生结合橡胶,同时消除结构化现象,制备出性能均匀、一致,具有一定工艺可塑性的混炼胶,供注射成型使用。
生产过程所使用的设备必须是经检查完好且正常运转。
1.操作程序1.1(密)混炼工艺按照产品的配方及混炼工艺要求,将各种配合剂(硫化剂除外)通过密炼机均匀分散到生胶(硅橡胶)中。
1.1.1 开机前检查机器、设备、风压及冷却水等是否正常。
检查清理(密)混炼室、转子及上顶栓等部件,清理干净余胶或杂物。
一切正常方可开机操作。
1.1.2 通知配料人员将已配好的生胶、配合剂、粉料、白碳黑等材料运到混炼作间,经检查无误后停放待用。
1.1.3 按上表中的程序进行胶料的(密)混炼操作。
1.2 薄通工艺对密炼机排下的胶料进行补充加工,使胶料分散更均匀。
1.2.1 每辊混炼胶按重量均匀分成二份,每份混炼胶称作“一辊胶”(约为20kg)。
1.2.2 清理开炼机辊筒、挡板及盛料盘,应无粉尘、油污或杂物,无上辊胶留下的余胶。
1.2.3 启动开炼机,通冷却水,调节辊距至≤0.5mm,辊温≤50℃,将一辊混炼胶分成适当的小块逐一投入开炼机进行薄通。
1.2.4 每辊胶薄通次数不少于3遍,但不多于10遍,每遍操作时间约为15分钟。
1.2.5 薄通结束后,调大辊距,将胶料压片下料停放,胶料须存放8小时后方可投入下工序使用。
1.3 热炼工艺对未加硫的混炼胶进行热处理,通过热炼时辊筒传递的热量,使混炼胶内有害的低分子物质及水份能够充分挥发,并消除胶料的结构化现象,同时使配合剂在胶料中进一步均匀分散。
1.3.1 清理开炼机辊筒、挡板及盛料盘,应无粉尘、油污或杂物,无上辊胶留下的余胶。
1.3.2 启动开炼机,调节配电柜的控制电流(或温度控制仪器表),将辊筒温度预热至120~135℃。
110 甲基乙烯基硅橡胶 生产工艺
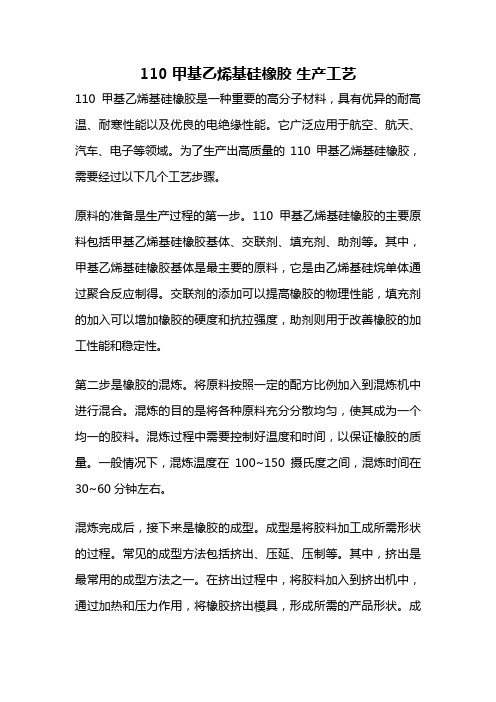
110 甲基乙烯基硅橡胶生产工艺110甲基乙烯基硅橡胶是一种重要的高分子材料,具有优异的耐高温、耐寒性能以及优良的电绝缘性能。
它广泛应用于航空、航天、汽车、电子等领域。
为了生产出高质量的110甲基乙烯基硅橡胶,需要经过以下几个工艺步骤。
原料的准备是生产过程的第一步。
110甲基乙烯基硅橡胶的主要原料包括甲基乙烯基硅橡胶基体、交联剂、填充剂、助剂等。
其中,甲基乙烯基硅橡胶基体是最主要的原料,它是由乙烯基硅烷单体通过聚合反应制得。
交联剂的添加可以提高橡胶的物理性能,填充剂的加入可以增加橡胶的硬度和抗拉强度,助剂则用于改善橡胶的加工性能和稳定性。
第二步是橡胶的混炼。
将原料按照一定的配方比例加入到混炼机中进行混合。
混炼的目的是将各种原料充分分散均匀,使其成为一个均一的胶料。
混炼过程中需要控制好温度和时间,以保证橡胶的质量。
一般情况下,混炼温度在100~150摄氏度之间,混炼时间在30~60分钟左右。
混炼完成后,接下来是橡胶的成型。
成型是将胶料加工成所需形状的过程。
常见的成型方法包括挤出、压延、压制等。
其中,挤出是最常用的成型方法之一。
在挤出过程中,将胶料加入到挤出机中,通过加热和压力作用,将橡胶挤出模具,形成所需的产品形状。
成型温度和压力的控制是保证成型质量的关键。
成型完成后,还需要对橡胶进行硫化处理。
硫化是将橡胶中的硫和交联剂反应,形成硫化交联网络的过程。
硫化可以提高橡胶的强度、耐磨性和耐温性能。
常用的硫化方法有热硫化和加热硫化两种。
热硫化是将成型的橡胶制品放入硫化炉中,在一定的温度下进行硫化。
加热硫化是将成型的橡胶制品放入加热板中,通过加热板的加热作用,使橡胶硫化。
经过硫化处理的橡胶制品需要进行后处理。
后处理的目的是去除硫化产物和改善橡胶的表面性能。
常见的后处理方法有洗涤、除臭、热处理等。
洗涤是将橡胶制品放入洗涤机中,用清洁剂进行清洗,去除硫化产物。
除臭是通过加热处理橡胶制品,使其产生挥发性物质,从而去除橡胶的异味。
硅橡胶混炼胶生产流程
硅橡胶混炼胶生产流程硅橡胶是一种用途广泛的橡胶制品,其具有耐高温、耐低温、耐老化、耐臭氧等优点,因此在航空航天、汽车工业、电子电气领域广泛应用。
硅橡胶的生产过程需要经过混炼胶工艺,下面将为大家介绍硅橡胶混炼胶的生产流程。
一、原料配方硅橡胶的配方根据生产需要确定,一般包括硅橡胶基料、填料、助剂、硫化剂等。
硅橡胶基料是生产硅橡胶制品的主要原料,填料用于改善硅橡胶的性能,助剂用于改善硅橡胶的加工性能,硫化剂用于硅橡胶的固化过程。
各种原料的比例和质量严格把控,以确保生产出的硅橡胶符合特定的技术指标。
二、橡胶预处理硅橡胶的生产过程通常需要进行橡胶预处理,以便提高硅橡胶的加工性能和均匀性。
橡胶预处理的主要工艺包括橡胶粗破、橡胶精破、橡胶粉碎、橡胶混料等。
通过橡胶预处理,可以有效提高硅橡胶的塑化性能和加工性能,有利于后续混炼工艺的进行。
三、混炼胶工艺1. 混炼胶机混炼胶是硅橡胶生产的关键环节,混炼胶的好坏直接影响硅橡胶制品的质量和性能。
混炼胶通常采用混炼机进行,混炼机是一种用于将橡胶原料混合、塑化、均匀分散的设备。
混炼机主要由料斗、滚筒、传动装置、加热冷却系统等部分组成,根据生产需要可以选择开式混炼机、密炼机等不同类型的混炼机。
2. 混炼工艺参数混炼胶的工艺参数包括混炼温度、混炼时间、混炼压力、滚筒转速等。
在混炼过程中,需要根据硅橡胶的具体特性和生产要求确定合适的混炼工艺参数,以确保将原料充分混合、塑化,达到均匀分散的目的。
一般来说,较高的混炼温度和较长的混炼时间有利于提高硅橡胶的塑化性能和加工性能。
3. 混炼过程控制在混炼过程中需要对混炼温度、混炼时间、滚筒转速等参数进行监控和调整,以确保混炼过程的稳定性和可控性。
同时,需要定期对混炼机的各项设备进行维护和保养,确保混炼机的正常运转。
四、混炼胶检验混炼胶生产完成后需要进行检验,以确保混炼胶达到预期的技术指标。
混炼胶的检验包括外观检查、拉伸性能测试、硫化性能测试、硅橡胶混炼胶成分分析等。
实验课程 硅橡胶炼塑实验
聚合物成型工艺学实验讲义(一级实验指导书)橡胶混炼(硅橡胶混炼)实验1.实验目的掌握软硅橡胶的混炼与塑化,学习双辊塑炼机设备的结构与工作原理;熟悉双辊炼塑机的规范操作技术。
2.原料硅橡胶(9份),碳酸钙粉料(1份)。
3.准备工作开车前必须戴好手套、口罩,穿实验服,应避免腰系绳、带、胶皮等,严禁披衣操作。
仔细查看辊筒间有无杂物。
混料操作前必须按紧急刹车装置,检查制动是否灵敏可靠(空机制动后,前辊回转不得超过四分之一周),正常操作时严禁用紧急刹车装置关机。
如两人以上共同操作时,必须相互呼应,确认无任何危险后,方可开车。
辊筒预热升温要掌握温升速度,尤其是在北方寒冷的冬季,辊筒外部与室温相一致,辊内突然加热,内外温差可能在120℃以上,温差造成辊筒应力可达到130.0~~I 50.OMPa,这已超过铸铁的U.1=140.OMPa,所以加热前应确保双辊之间有一定的间隙,以防加热过程中热胀冷缩而破坏辊面。
如过早的加上胶料,在横压力的叠加作用下,辊面也非常容易受到破坏。
为了安全起见,应当在加料前预热,升温速度不宜过快。
本次实验所用设备为程序升温,按要求设定温度即可。
因硅橡胶混温度不超过30 ℃,温度的影响不大。
投料前对胶料也应检查,若混有硬的金属杂物,随胶料投入炼胶机,致使横压力突然加大,易造成设备损坏。
2:操作步骤1.首先要调整好辊距,保持辊距的平衡。
若两端辊距调节的大小不一,造成辊筒偏载,极损坏设备,这是严格禁止的。
12.加料习惯上都从动力传入端加入,其实这是不合理的。
从弯矩图和扭矩图上着眼,加料应在速比齿轮端。
由于传动端的合成弯矩和扭矩均大于速比齿轮端,在传动端首先加入硬的大块胶料,当然更容易损伤设备。
当然更不要首先把大块的硬胶料加在辊筒中间断面,此处合成弯矩更大,达2820吨厘米。
3.加料量要逐渐增加,加料块重不得超过设备使用说明书上的规定,投料顺序由小到大陆续添加。
如图省事,大块胶料突然添入辊距,会造成过载冲出,不仅易使安全垫片损坏,而且,一旦安全垫片失灵,就会危及辊筒。
硅胶生产流程
东莞崇信硅胶制品有限公司,主要生产硅胶键盘保护膜,硅胶奶嘴,硅胶杯套等产品的硅胶制品厂。
硅橡胶的生产制程有哪些呢,下面小编带大家去详细了解下。
它的生产工艺过程主要包括:原材料准备→塑炼→混炼→成型→硫化→休整→检验1.预备材料橡胶制品的主要材料有生胶、配合剂、纤维材料和金属材料。
其中生胶为基本材料;配合剂是为了改善橡胶制品的某些性能而加入的辅助材料;纤维材料(棉、麻、毛及各种人造纤维、合成纤维)和金属材料(钢丝、铜丝)是作为橡胶制品的骨架材料,以增强机械强度、限制制品变型。
以下为几种的的状态的橡胶:1、生胶要在60--70℃烘房内烘软后,再切胶、破胶成小块;2、块状配合剂如石蜡、硬脂酸、松香等要粉碎;3、粉状配合剂若含有机械杂质或粗粒时需要筛选除去;4、液态配合剂(松焦油、古马隆)需要加热、熔化、蒸发水分、过滤杂质;5、配合剂要进行干燥,不然容易结块、混炼时旧不能分散均匀,硫化时产生气泡,从而影响产品质量;2.塑炼生胶富有弹性,缺乏加工时的必需性能(可塑性),因此不便于加工。
为了提高其可塑性,所以要对生胶进行塑炼;这样,在混炼时配合剂就容易均匀分散在生胶中;同时,在压延、成型过程中也有助于提高胶料的渗透性(渗入纤维织品内)和成型流动性。
将生胶的长链分子降解,形成可塑性的过程叫做塑炼。
生胶塑炼的方法有机械塑炼和热塑炼两种。
机械塑炼是在不太高的温度下,通过塑炼机的机械挤压和摩擦力的作用,使长链橡胶分子降解变短,由高弹性状态转变为可塑状态。
热塑炼是向生胶中通入灼热的压缩空气,在热和氧的作用下,使长链分子降解变短,从而获得可塑性。
3.混炼为了适应各种不同的使用条件、获得各种不同的性能,也为了提高橡胶制品的性能和降低成本,必须在生胶中加入不同的配合剂。
混炼就是将塑炼后的生胶与配合剂混合、放在炼胶机中,通过机械拌合作用,使配合剂完全、均匀地分散在生胶中的一种过程。
混炼是橡胶制品生产过程中的一道重要工序,如果混合不均匀,就不能充分发挥橡胶和配合剂的作用,影响产品的使用性能。
混炼硅橡胶的配合技术(九)
硫化剂种类1 )
硫化剂用量/ %
D B DBDB pB DB DB nB PB 以 p 刃B cP CpCP Cp Cp cP CPC p 卫 / / Cp
07 . 5 06 02/. 09 . .பைடு நூலகம் 4 . 5 5 5 09 04/. 07 . 50 4 . 5 07 . 5
以卫P 07 .5
I二P XB 06 .5
胶, 硅橡胶生胶的塑性值应控制在 1 一 8, 5 0 2 1
凝胶斜率应小于 2 ;补强填料最好使用经疏水 5 处理的气相法白 炭黑或水分含量较低的气相法白 炭黑,因为水分或经基都是引起制品内部产生气 泡的原因;为避免制品表面发粘、改善挤出性, 还须在胶料配方、 配制工艺上采取一些措施。 , 2 4 二氯过氧化苯甲酞 ( C P 一 D B )是挤出成形用 混炼硅橡胶最常用的硫化剂, 其优点是在所有能 用于硅橡胶的过氧化物硫化剂中硫化速度最快。 尽管 D B 在使用中会副产 24 二氯联苯等对 CP ,一 人体有害的物质及氯化苯甲酸等对金属有腐蚀性 的物质, 目 但 前尚没有更好的硫化剂完全取代。 采用含氢硅油作交联剂、铂配合物作催化剂
3r 挤出 . o 成形用混炼硅橡胶的配制 甲基乙烯基混炼硅橡胶采用挤出成形方法可 制成胶管、 实心胶条、 异形截面密封胶条、电 线 电缆等, 其邵尔 A硬度一般为5 一 0 0 7 度。胶料
测试项 目
硬度太低时, 塑性太小, 易粘附, 故影响制品的 表面质量;而胶料硬度太高时,由于填料用量 大、塑性高,口 模小时挤出困 难。常用的 挤出 成 形用混炼硅橡胶的品级及性能列于表4 。 7
巧 ℃的 。 硅树脂可提高胶料的塑性值,改进其挤
出 且硫化制品的物理性能良 侧。 性; 好〔 所选用
- 1、下载文档前请自行甄别文档内容的完整性,平台不提供额外的编辑、内容补充、找答案等附加服务。
- 2、"仅部分预览"的文档,不可在线预览部分如存在完整性等问题,可反馈申请退款(可完整预览的文档不适用该条件!)。
- 3、如文档侵犯您的权益,请联系客服反馈,我们会尽快为您处理(人工客服工作时间:9:00-18:30)。
硅橡胶混炼工艺
硅橡胶混炼工艺:
1.开炼机混炼
双辊开炼机辊筒速比为1.2~1.4:为宜,快辊在后,较高的速比导致较快的混炼,低速比则可使胶片光滑。
辊筒必须通有冷却水,混炼温度宜在40℃以下,以防止焦烧或硫化剂的挥发损失。
混炼时开始辊距较小(1~5mm),然后逐步放大。
加料和操作顺序:生胶(包辊)—→补强填充剂—→结构控制剂—→耐热助剂—→着色剂等—→薄通5次—→下料,烘箱热处理—→返炼—→硫化剂—→薄通—→停放过夜—→返炼—→出片。
胶料也可不经烘箱热处理,在加入耐热助剂后,加入硫化剂再薄通,停放过夜返炼,然后再停放数天返炼出片使用。
混炼时间为20~40分钟(开炼机规格为φ250mm×620mm)。
如单用沉淀白炭黑或弱补强性填充剂(二氧化钛、氧化锌等)时,胶料中可不必加入结构控制剂。
应缓慢加入填料,以防止填料和生胶所形成的球状体浮在堆积胶的顶上导致分散不均。
如果要加入大量的填料,最好是分两次或三次加入,并在其间划刀,保证良好的分散。
发现橡胶有颗粒化的趋势,可收紧辊距以改进混炼。
落到接料盘上的胶粒应当用刷子清扫并收集起来,立即返回炼胶机的辊筒上,否则所炼胶料中含有胶疙瘩而导致产品外观不良。
增量性填料应当在补强性填料加完之后加入,可采用较宽的辊距。
装胶容量(混炼胶):φ160mm×320mm 炼胶机为1~2 kg;φ250mm×620mm炼胶机为3~5kg。
硅橡胶在加入炼胶机时包慢辊(前辊),混炼时则很快包快辊(后辊),炼胶时必须能两面操作。
由于硅橡胶胶料比较软,混炼时可用普通赋子刀操作,薄通时不能象普通橡胶那样拉下薄片,而采用钢、尼龙或耐磨塑料刮刀刮下。
为便于清理和防止润滑油漏入胶内,应采用活动挡板。
气相白炭黑易飞扬,对人体有害,应采取相应的劳动保护措施。
如在混炼时直接使用粉状过氧化物,必须采取防爆措施,最好使用膏状过氧化物。
如在胶料中混有杂质、硬块等,可将混炼胶再通过滤胶机过滤,过滤时,一般采用80~140目筛网采用开炼机混炼,它包括:1)包辊:生胶包于前辊;2)吃粉过程:把需要加入的助剂按照一定的顺序加入,加入时要注意堆积胶的体积,少了难于混合,多了会打滚不容易混炼。
吃粉后会包后辊。
其中加料顺序一般为:生胶→补强剂→结构控制剂→耐热助剂;3)翻炼过程:能更好、更快、更均匀的混炼。
刀法:a、斜刀法(八把刀法)b、三角包法; c、打扭操作法;d、捣胶法(走刀法)还要考虑的问题有,开炼机的装胶容量;辊筒的温度:小于50度;混炼时间:没有具体的规定,看操
作员的熟练程度。
使用捏炼机,别的过程控制跟密炼机差不多的,按捏炼机的容量,硬度,投入一定的生胶。
白碳黑。
脱模剂,增白剂,硅油。
密炼两个半小时,再抽真空半小时左右。
倒出即可。
冷却,称一定的重量,按比例加硫化剂。
如果直接混炼胶买来。
直接加硫化剂即可
2.密炼机混炼
采用此法可提高生产效率和改善劳动条件。
试验表明,密闭式混炼胶料的性能与开放式混炼胶料的性能相似。
用试验室2L密炼机的混炼时间为6~16分钟,混炼无特殊困难。
采用φ160mm开炼机当装料系数为0.74时,混炼也能正常进行。
排料温度与补强填充剂的类型有关:当采用弱补强性填充剂和沉淀白炭黑时,排胶温度在50℃以下;当使用气相白炭黑时,排胶温度为70℃左右。