混炼硅橡胶的配合技术_五_
硅橡胶配合技术

第 2 9卷 第 2期
硅 橡 胶 配 合 技 术
・5 1・
硅 橡 胶 配 合 技 术
王作 龄 编 译
中图分类号 : TQ3 3 9 3.3
文 献 标 识 码 : E
文 章 编 号 : 0 0 4 0 2 0 ) 2 0 5 一J 1 0 4 8( 0 2 0 — 0 1 ( 9
术 有 很 大 关 系 , 主 要 还 是 取 决 于 硅 橡 胶 纯 胶 但
2 原 材 料 的 性 能
硅 橡 胶 制 品 具 有 耐 热 、 寒 、 候 性 、 绝 耐 耐 电 缘 性 和 弹 性 等 多 项 优 异 性 能 。 它 使 用 温 度 范 围 宽 广 、 缩 永 久 变 形 小 。 些 性 能 虽 然 与 配 合 技 压 这
批 量 小 , 且 用 白炭 黑 作 补 强 剂 需 要 专 用设 备 而
进行 配 炼加 工 ( 以免混 入 普通 炭 黑 、 老剂 等异 防
种 成 分 而 降 低 成 品 物 理 性 能 及 外 观 质 量 ) 用 户 。 在配 炼 时 所受 的 限制 条 件较 多 。 硅 橡胶 按 其 外 观 、 联 机理 等 有 多种 等级 , 交 大 致 可 分 为 以 聚 合 度 5 001 , 0 , 0 — 0 0 0的 线 型 硅 氧 烷 聚合 物 ( 胶 状 ) 主要 成 分 的混 炼 型和 以 生 为 聚 合 度 为 1 O2 0 0的 线 型 硅 氧 烷 聚 合 物 ( 一 ,0 O 油 状 ) 主 要 成 分 的 液 体 状 态 两 类 ( 1 。下 文 重 为 表 ) 点 对 } 炼 型 硅 橡 胶 及 其 制 品 的 配 合 技 术 进 行 介 昆
ห้องสมุดไป่ตู้
在 橡 胶 制 品 加 工 厂 中 硅 橡 胶 制 品 一 般 品 种 多 而
混炼硅橡胶的配合技术_一_

将 100 份胶料与 0 5 份2, 5 - 二甲基- 2, 5 - 二叔丁基过氧化己 烷在双辊炼胶 机上混炼均 一, 在 165 10 min 条件下热压硫 化; 然后 在 200 4 h 条件下二次硫化, 制得 2 mm 厚 的试片。测其物理机械性能, 结果见表 1。
技术讲座
, 2006, 20 ( 1) : 42~ 47 SI LICON E M AT ER IAL
混炼硅橡胶的配合技术 ( 一)
黄文润
( 中蓝晨光化工研究院, 成都 610041)
摘要: 介绍了混炼硅橡胶的基本配合过程和硫化体系, 着 重比较了 间歇法和连 续法两种 混炼工艺的 生
产效率及对硅橡胶硫化胶性能的影响, 讨论了 6 种过氧化物硫化剂的特点及适应范围。
采用间歇配制工艺配制混炼硅橡胶多在捏合 机及密炼机中进行。在工业化生产中, 为大批制 取混炼硅橡胶, 常使用装有 2 个混合桨的大型捏 合机, 捏合机的容量达数立方米; 为使原料混合 均一, 需要较长的混炼时间。采用槽内装有 2 个 旋桨、上部装有加压块、能使原料在压缩状态下 混炼的密炼机可在较短时间内制得混合均匀的混 炼硅橡胶[ 1] 。但这种加 压式密炼机的 有效容积 最大仅数百升, 不能满足大批量生产的要求。采 取先在密炼机中混炼、再在捏合机中热处理的方 法, 可高 效、大 批 量生 产 混炼 硅 橡 胶胶 料[ 2] 。 即先将硅橡胶生胶、补强填料白炭黑、结构化控 制剂等在 150 下用密炼机混合均匀, 再在氮气 保护下或减压的捏合机中于 150~ 200 下处理。
混炼硅橡胶结构化

混炼硅橡胶结构化摘要:一、混炼硅橡胶的概述二、混炼硅橡胶的结构化过程三、结构化对混炼硅橡胶性能的影响四、如何提高混炼硅橡胶的结构化性能五、总结与应用正文:混炼硅橡胶作为一种高性能的橡胶材料,因其优异的耐高温、耐腐蚀、电绝缘等性能在众多领域得到广泛应用。
本文将详细介绍混炼硅橡胶的结构化过程,分析其对硅橡胶性能的影响,并探讨如何提高结构化性能,以期为混炼硅橡胶的生产和应用提供参考。
一、混炼硅橡胶的概述混炼硅橡胶是由硅橡胶生胶、填充剂、催化剂、抗磨剂等原材料经过混合、炼胶、硫化等工艺制得的一种弹性材料。
它具有较高的耐热性、耐寒性、耐腐蚀性和电绝缘性能,适用于制作各种高要求的密封件、绝缘件和耐磨件等。
二、混炼硅橡胶的结构化过程混炼硅橡胶的结构化过程主要包括两个方面:硫化交联和硅橡胶分子链的分支、交联。
硫化交联是通过硫化剂使硅橡胶生胶中的硅醇基团发生化学反应,形成三维网络结构。
而硅橡胶分子链的分支、交联则是通过分子间的硅醇基团互相作用,形成更加稳定的结构。
三、结构化对混炼硅橡胶性能的影响结构化程度对混炼硅橡胶的性能有很大影响。
结构化程度适中时,混炼硅橡胶具有较好的强度、弹性和耐磨性能。
然而,当结构化程度过高时,材料的硬度和脆性会增加,降低其耐疲劳性和耐磨性能。
因此,在生产过程中,需要控制硫化程度,使混炼硅橡胶达到最佳的性能。
四、如何提高混炼硅橡胶的结构化性能1.选择合适的硫化剂:不同的硫化剂对硅橡胶的结构化程度影响较大。
通过选择合适的硫化剂,可以有效提高混炼硅橡胶的结构化性能。
2.调整填充剂的种类和比例:填充剂可以改善硅橡胶的物理性能和耐磨性能。
合理选择填充剂的种类和比例,有助于提高混炼硅橡胶的结构化性能。
3.控制炼胶温度和时间:炼胶过程中,控制温度和时间对硅橡胶的结构化程度有很大影响。
适当的炼胶温度和时间可以促进硅橡胶分子链的交联,提高结构化性能。
4.采用动态硫化技术:动态硫化技术可以在较低的温度下使硅橡胶发生交联,提高结构化性能。
硅橡胶混炼胶
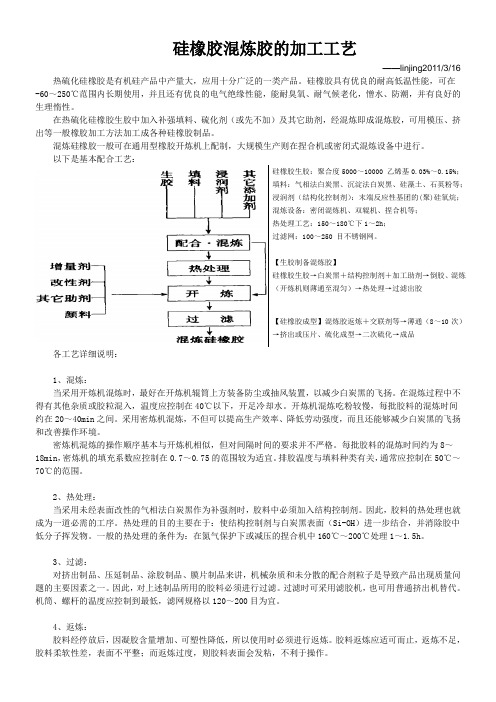
硅橡胶混炼胶的加工工艺——linjing2011/3/16 热硫化硅橡胶是有机硅产品中产量大,应用十分广泛的一类产品。
硅橡胶具有优良的耐高低温性能,可在-60~250℃范围内长期使用,并且还有优良的电气绝缘性能,能耐臭氧、耐气候老化,憎水、防潮,并有良好的生理惰性。
在热硫化硅橡胶生胶中加入补强填料、硫化剂(或先不加)及其它助剂,经混炼即成混炼胶,可用模压、挤出等一般橡胶加工方法加工成各种硅橡胶制品。
混炼硅橡胶一般可在通用型橡胶开炼机上配制,大规模生产则在捏合机或密闭式混炼设备中进行。
以下是基本配合工艺:硅橡胶生胶:聚合度5000~10000 乙烯基0.03%~0.15%;填料:气相法白炭黑、沉淀法白炭黑、硅藻土、石英粉等;浸润剂(结构化控制剂):末端反应性基团的(聚)硅氧烷;混炼设备:密闭混炼机、双辊机、捏合机等;热处理工艺:150~180℃下1~2h;过滤网:100~250 目不锈钢网。
【生胶制备混炼胶】硅橡胶生胶→白炭黑+结构控制剂+加工助剂→倒胶、混炼(开炼机则薄通至混匀)→热处理→过滤出胶【硅橡胶成型】混炼胶返炼+交联剂等→薄通(8~10次)→挤出或压片、硫化成型→二次硫化→成品各工艺详细说明:1、混炼:当采用开炼机混炼时,最好在开炼机辊筒上方装备防尘或抽风装置,以减少白炭黑的飞扬。
在混炼过程中不得有其他杂质或胶粒混入,温度应控制在40℃以下,开足冷却水。
开炼机混炼吃粉较慢,每批胶料的混炼时间约在20~40min之间。
采用密炼机混炼,不但可以提高生产效率、降低劳动强度,而且还能够减少白炭黑的飞扬和改善操作环境。
密炼机混炼的操作顺序基本与开炼机相似,但对间隔时间的要求并不严格。
每批胶料的混炼时间约为8~18min,密炼机的填充系数应控制在0.7~0.75的范围较为适宜。
排胶温度与填料种类有关,通常应控制在50℃~70℃的范围。
2、热处理:当采用未经表面改性的气相法白炭黑作为补强剂时,胶料中必须加入结构控制剂。
硅橡胶混炼工艺

硅橡胶混炼工艺硅橡胶混炼工艺:1.开炼机混炼双辊开炼机辊筒速比为1.2~1.4:为宜,快辊在后,较高的速比导致较快的混炼,低速比则可使胶片光滑。
辊筒必须通有冷却水,混炼温度宜在40℃以下,以防止焦烧或硫化剂的挥发损失。
混炼时开始辊距较小(1~5mm),然后逐步放大。
加料和操作顺序:生胶(包辊)—→补强填充剂—→结构控制剂—→耐热助剂—→着色剂等—→薄通5次—→下料,烘箱热处理—→返炼—→硫化剂—→薄通—→停放过夜—→返炼—→出片。
胶料也可不经烘箱热处理,在加入耐热助剂后,加入硫化剂再薄通,停放过夜返炼,然后再停放数天返炼出片使用。
混炼时间为20~40分钟(开炼机规格为φ250mm×620mm)。
如单用沉淀白炭黑或弱补强性填充剂(二氧化钛、氧化锌等)时,胶料中可不必加入结构控制剂。
应缓慢加入填料,以防止填料和生胶所形成的球状体浮在堆积胶的顶上导致分散不均。
如果要加入大量的填料,最好是分两次或三次加入,并在其间划刀,保证良好的分散。
发现橡胶有颗粒化的趋势,可收紧辊距以改进混炼。
落到接料盘上的胶粒应当用刷子清扫并收集起来,立即返回炼胶机的辊筒上,否则所炼胶料中含有胶疙瘩而导致产品外观不良。
增量性填料应当在补强性填料加完之后加入,可采用较宽的辊距。
装胶容量(混炼胶):φ160mm×320mm 炼胶机为1~2 kg;φ250mm×620mm炼胶机为3~5kg。
硅橡胶在加入炼胶机时包慢辊(前辊),混炼时则很快包快辊(后辊),炼胶时必须能两面操作。
由于硅橡胶胶料比较软,混炼时可用普通赋子刀操作,薄通时不能象普通橡胶那样拉下薄片,而采用钢、尼龙或耐磨塑料刮刀刮下。
为便于清理和防止润滑油漏入胶内,应采用活动挡板。
气相白炭黑易飞扬,对人体有害,应采取相应的劳动保护措施。
如在混炼时直接使用粉状过氧化物,必须采取防爆措施,最好使用膏状过氧化物。
如在胶料中混有杂质、硬块等,可将混炼胶再通过滤胶机过滤,过滤时,一般采用80~140目筛网采用开炼机混炼,它包括:1)包辊:生胶包于前辊;2)吃粉过程:把需要加入的助剂按照一定的顺序加入,加入时要注意堆积胶的体积,少了难于混合,多了会打滚不容易混炼。
混炼硅胶的工艺和配方

混炼硅胶的工艺和配方嘿,朋友们!今天咱就来唠唠混炼硅胶的工艺和配方。
你说这混炼硅胶啊,就像是一位神奇的魔法师,能变幻出各种各样的奇妙形态和用途。
它的工艺和配方那可真是有讲究的。
先来说说工艺吧,就好像是做菜一样,得掌握好火候和步骤。
混炼的过程就像是一场精心编排的舞蹈,各种原材料要恰到好处地融合在一起。
温度不能太高也不能太低,搅拌的力度和时间也得拿捏得死死的。
不然,出来的东西可就不是我们想要的啦!这就好比跳舞的时候节奏乱了,那整个舞蹈不就垮掉了嘛!再讲讲配方,这可真是核心机密啊!不同的配方能做出性能各异的混炼硅胶。
就像是不同的调料搭配能做出不同口味的菜肴一样。
有些配方能让混炼硅胶变得特别柔软,像棉花糖一样;有些能让它超级耐磨,就像穿着铁鞋在走路;还有些能让它具备特殊的性能,比如耐高温或者耐低温。
你想想,这得多神奇呀!咱就说,要是没有合适的工艺和配方,那混炼硅胶能有这么多好用处吗?那肯定不能啊!就好比盖房子没有好的设计和材料,能盖出坚固漂亮的房子吗?在实际操作中,那可得细心再细心。
一点点的偏差都可能导致结果大不同。
这就像走钢丝,稍微不注意就可能掉下去。
所以啊,从事混炼硅胶工作的人都得是高手,得有一双敏锐的眼睛和一双灵巧的手。
而且啊,这混炼硅胶的应用那可广泛了去了。
从医疗领域到电子行业,从日常生活用品到高科技产品,哪儿都有它的身影。
它就像是一个无处不在的小精灵,默默地为我们的生活提供便利和保障。
你看那些医疗设备上的硅胶部件,不就是靠这精湛的工艺和配方制造出来的吗?它们可是关乎着人们的健康和安全呢!还有那些电子产品的密封件,要是没有好的混炼硅胶,那电子产品还能正常工作吗?总之,混炼硅胶的工艺和配方可真是一门大学问。
我们可不能小瞧了它,得好好去研究、去探索。
说不定哪天,你就能发现一个新的配方或者工艺,让混炼硅胶发挥出更大的作用呢!这难道不是一件特别酷的事情吗?难道你不想去尝试一下吗?所以啊,大家都加把劲,让我们一起在混炼硅胶的世界里创造更多的精彩吧!。
硅胶混炼工艺技术
硅胶混炼工艺技术硅胶混炼(Silicone Rubber Mixing)是一种常见的工艺技术,用于将硅胶材料混合和加热,以制备各种硅胶制品。
硅胶混炼工艺技术广泛应用于电子、医疗、化工和汽车等行业。
硅胶混炼工艺技术的关键是选择适当的硅胶材料和混炼设备。
硅胶是一种由有机矽氧烃构成的高分子化合物,具有优异的耐热、耐寒、耐化学腐蚀和电绝缘性能。
常用的硅胶材料有室温硫化型和高温固化型两种。
在硅胶混炼过程中,首先将硅胶料投入混炼机内,然后加入适量的硅胶添加剂,如流化剂、助剂和填充剂等。
这些添加剂可改善硅胶的粘度、流动性和硬度等性能。
随后,使用加热系统对混炼机内的硅胶料进行加热,以提高混炼效果。
硅胶混炼的关键环节是设备的选配和操作控制。
混炼机通常是由一个旋转的主轴和配有刮板的容器组成。
主轴的旋转使硅胶材料能够均匀混合,而刮板则可以将硅胶从容器壁上刮下,以确保混炼的均匀性。
硅胶混炼的控制参数包括混炼温度、混炼时间和混炼速度等。
混炼温度通常由加热系统控制,其取决于硅胶的材料和加工要求。
混炼时间一般为几十分钟至几个小时,取决于硅胶的材料和混炼负荷。
混炼速度是由主轴的旋转速度控制,其取决于硅胶的粘度和混炼效果要求。
硅胶混炼的主要优点是可以制备出具有各种硬度、形状和尺寸的硅胶制品。
硅胶材料的耐高温性能使得硅胶制品可以用于高温工况下的密封、隔热和绝缘等应用。
此外,硅胶混炼还可以将硅胶与其他材料进行复合,用于改善硅胶的物理和化学性能。
然而,硅胶混炼也存在一些挑战和难点。
例如,硅胶材料的混炼过程需要一定的控制参数和经验知识,以确保混炼的均匀性和质量稳定性。
此外,硅胶混炼还需要加热系统和混炼设备的投资和维护成本。
综上所述,硅胶混炼是一种重要的工艺技术,用于制备硅胶制品。
通过选择适当的硅胶材料和混炼设备,并控制混炼参数,可以获得具有优异性能和高质量的硅胶制品。
随着科技的不断进步和创新,硅胶混炼工艺技术将在更多领域得到应用和发展。
硅橡胶混炼工艺
硅橡胶混炼工艺硅橡胶混炼工艺:1.开炼机混炼双辊开炼机辊筒速比为1.2~1.4:为宜,快辊在后,较高的速比导致较快的混炼,低速比则可使胶片光滑。
辊筒必须通有冷却水,混炼温度宜在40℃以下,以防止焦烧或硫化剂的挥发损失。
混炼时开始辊距较小(1~5mm),然后逐步放大。
加料和操作顺序:生胶(包辊)—→补强填充剂—→结构控制剂—→耐热助剂—→着色剂等—→薄通5次—→下料,烘箱热处理—→返炼—→硫化剂—→薄通—→停放过夜—→返炼—→出片。
胶料也可不经烘箱热处理,在加入耐热助剂后,加入硫化剂再薄通,停放过夜返炼,然后再停放数天返炼出片使用。
混炼时间为20~40分钟(开炼机规格为φ250mm×620mm)。
如单用沉淀白炭黑或弱补强性填充剂(二氧化钛、氧化锌等)时,胶料中可不必加入结构控制剂。
应缓慢加入填料,以防止填料和生胶所形成的球状体浮在堆积胶的顶上导致分散不均。
如果要加入大量的填料,最好是分两次或三次加入,并在其间划刀,保证良好的分散。
发现橡胶有颗粒化的趋势,可收紧辊距以改进混炼。
落到接料盘上的胶粒应当用刷子清扫并收集起来,立即返回炼胶机的辊筒上,否则所炼胶料中含有胶疙瘩而导致产品外观不良。
增量性填料应当在补强性填料加完之后加入,可采用较宽的辊距。
装胶容量(混炼胶):φ160mm×320mm 炼胶机为1~2 kg;φ250mm×620mm炼胶机为3~5kg。
硅橡胶在加入炼胶机时包慢辊(前辊),混炼时则很快包快辊(后辊),炼胶时必须能两面操作。
由于硅橡胶胶料比较软,混炼时可用普通赋子刀操作,薄通时不能象普通橡胶那样拉下薄片,而采用钢、尼龙或耐磨塑料刮刀刮下。
为便于清理和防止润滑油漏入胶内,应采用活动挡板。
气相白炭黑易飞扬,对人体有害,应采取相应的劳动保护措施。
如在混炼时直接使用粉状过氧化物,必须采取防爆措施,最好使用膏状过氧化物。
如在胶料中混有杂质、硬块等,可将混炼胶再通过滤胶机过滤,过滤时,一般采用80~140目筛网采用开炼机混炼,它包括:1)包辊:生胶包于前辊;2)吃粉过程:把需要加入的助剂按照一定的顺序加入,加入时要注意堆积胶的体积,少了难于混合,多了会打滚不容易混炼。
混炼硅橡胶常见问题及解决方法
混炼硅橡胶常见问题及解决方法1、生胶吃粉慢原因:1、生胶分子量偏高,2、DMC中含有三官能基团轻微交联的硅橡胶生胶处理:1、选择合适的生胶分子量或降低生胶分子量使用2、在混炼时适当添加500cs~1000cs二甲基硅油或低分子或水2、混炼胶透明度差原因:1、白炭黑颗粒粗难分散。
2、低分子未除尽,硫化胶内有雾状3、包辊遍数不够4、原材料存脏物5、环境卫生差6、设备密封差,抽真空时脏物进入胶中7、热炼时高温时间短8、充氮气操作不当3、胶外观不一致原因:1、白炭黑批次间出现色差2、冷炼时间不一致3、辅料外观有差异处理:1、热炼时间,温度要统一2、留意白炭黑批次之间的色差,出现后及时更换3、发货时应将同一时间的胶料发出,以防胶料存储时间长与空气发生反应,胶变色。
4、原材料统一4、胶料不包辊原因:1、胶料塑性值高2、辊温过低处理:1、提高辊温,关闭冷却水2、控制适当炼胶时间3、加入适当助剂5、回弹性差原因:1、生胶乙烯基配方不合理2、助剂过多3、开炼时间不够,白炭黑与生胶浸润差4、冷炼温度高处理:1、适量加入多乙烯基硅油,提高乙烯基2、分散剂量适当3、白炭黑吃完后,冷炼延长至45min4、保证冷炼温度6、撕裂强度差原因:1、生胶乙烯基不合理2、白炭黑粗,比表面积小3、硫化不熟4、胶发脆处理:1、用多乙烯基硅油或选用乙烯基生胶调整乙烯基含量2、更换白炭黑填料,选用比表面积大,性能好的白炭黑,更换质量档次高的产品3、调整硫化剂量和硫化时间4、降低乙烯基,用甲基硅油或低乙烯基生胶调整7、胶粘原因:1、生胶聚合不好,低分子物过多,或生胶分子量过低2、抽真空不好3、助剂量过大4、脱模剂少5、硫化不熟6、模具清理不干净处理:1、换货或发高分子量生胶进行拼用2、真空度控制得当3、减少分散剂量,胶与胶拼用4、补加脱模剂5、提高硫化胶温度,延长硫化时间6、定期清理模具7、使用另类型脱模剂8、永久变形大原因:1、配胶配比不合理,低分子量低乙烯基胶过多2、乙烯基偏低3、真空不好4、硫化时间短处理:1、加入高乙烯基生胶,提高乙烯基含量,或适当添加助剂2、延长真空时间3、延长高温捏合时间9、胶黄原因:1、生胶中含有NH2和CL-离子2、白炭黑含有Fe3+多3、高温温度不够,真空时间短4、白炭黑选择不合理,外观黄5、抽真空或充氮气不好1、加入含氢硅油等抗黄,目的是与NH2和CL-离子反应,生成NH3和HCL抽真空时抽尽2、保证高温时间和温度,否则助剂与NH2和CL-离子反应不充分3、改用其它牌号白炭黑4、保证抽真空和充氮气时间10、混炼时难吃粉原因:1、结构剂量少2、结构剂中羟基含量过低3、生胶分子量高,且分子量分布过窄4、生胶中有微交联的硅橡胶生胶5、白炭黑与助剂加入量不成比例6开炼或捏合温度过低处理:1\增加结构剂2、选用分子量分布均匀的生胶3、加料时与结构剂成比例加入4适当提高开炼或捏合温度。
混炼硅橡胶结构化
混炼硅橡胶结构化摘要:一、混炼硅橡胶的概述二、混炼硅橡胶的制备方法三、混炼硅橡胶的应用领域四、结论正文:一、混炼硅橡胶的概述混炼硅橡胶是一种高性能的弹性材料,它具有优异的耐高低温、耐氧化、耐老化和电绝缘等性能。
由于其独特的结构和性能,混炼硅橡胶被广泛应用于航空航天、电子、汽车、医疗等领域。
二、混炼硅橡胶的制备方法混炼硅橡胶的制备主要采用开炼机和密炼机进行混炼。
在制备过程中,需要注意以下几点:1.选用合适的硅橡胶生胶:硅橡胶生胶的选用对混炼硅橡胶的性能影响很大。
通常情况下,选用高分子量的硅橡胶生胶可以提高混炼硅橡胶的耐磨性和耐老化性能。
2.控制混炼温度:混炼过程中的温度对硅橡胶的结构和性能影响很大。
一般来说,混炼温度不宜过高,以避免硅橡胶发生降解。
3.合理选择添加剂:为了改善混炼硅橡胶的性能,可以加入适量的添加剂,如硫化剂、补强剂、耐磨剂等。
4.控制混炼时间:混炼时间的长短会影响硅橡胶的结构和性能。
通常情况下,混炼时间越长,硅橡胶的强度和耐磨性越好,但过长的混炼时间会导致硅橡胶变硬。
三、混炼硅橡胶的应用领域混炼硅橡胶由于其独特的性能,被广泛应用于以下几个领域:1.航空航天:混炼硅橡胶可用于制作航空航天器的密封件、油封等部件,其优异的耐高低温性能可保证航空航天器在极端环境下正常工作。
2.电子行业:混炼硅橡胶可用于制作电子元器件的密封件,如密封圈、O 型圈等,以保护电子元器件免受潮湿、氧化等环境因素的影响。
3.汽车行业:混炼硅橡胶可用于制作汽车的密封件、油封等部件,以保证汽车在各种工况下的正常运行。
4.医疗行业:混炼硅橡胶可用于制作医疗器件,如硅胶管、硅胶塞等,其良好的生物相容性可确保医疗器件的安全性。
四、结论混炼硅橡胶作为一种高性能的弹性材料,具有优异的耐高低温、耐氧化、耐老化和电绝缘等性能,被广泛应用于航空航天、电子、汽车、医疗等领域。
- 1、下载文档前请自行甄别文档内容的完整性,平台不提供额外的编辑、内容补充、找答案等附加服务。
- 2、"仅部分预览"的文档,不可在线预览部分如存在完整性等问题,可反馈申请退款(可完整预览的文档不适用该条件!)。
- 3、如文档侵犯您的权益,请联系客服反馈,我们会尽快为您处理(人工客服工作时间:9:00-18:30)。
数 0123 %] , 60 份粘度 (30~120) ×106 mPa·s 的 甲基乙烯基硅橡胶生胶 [ ( CH3) 2SiO 链节摩尔分 数 99102 %、( CH3) ( CH2 CH) SiO 键节摩尔分 数 0108 %] , 2 份粘度 30 mPa·s 的 α, ω - 二羟 基聚二甲基硅氧烷 , 015 份乙烯基三乙氧基硅烷 (V TES) , 35 份经二甲基环硅氧烷处理 、比表面 积 200 m2/ g 的气相法白炭黑 , 120 份平均粒径 1μm 的 氢 氧 化 铝 ( A TH) 及 35 份 平 均 粒 径 10μm的粉碎石英粉 , 室温下混炼均一 ; 再加入 013 份硬脂酸铝 (随意成分) 、0188 份炭黑质量 分数为 50 %的硅橡胶生胶黑色母胶 、1125 份2 ,5 - 二甲基 - 2 ,5 - 二 (叔丁基过氧) 乙烷 (简称双 二五) , 在双辊炼胶机上混合均一 , 在 177 ℃× 15 min 条件下热压成形 。测其性能为 : 邵尔 A 硬度 70 度 , 拉伸强度 519 M Pa , 伸长率 188 % , 撕裂强度 B 1419 kN/ m , 相对密度 1156 , 电气 强度 21 MV/ m , 耐 漏 电 起 痕 性 ( ASTM - D 2303) 300 min , 耐 漏 电 起 痕 性 ( IEC - 587 ) 415 kV , 疏水恢复性 24 h 。疏水恢复性是根据 硫化的硅橡胶试片 ( 15214 mm ×15214 mm × 119 mm) 的表面经电晕处理前后水的接触角的 变化确定的 。即经 381 μm 间隙电晕放电 40 次 后 , 硅橡胶试片疏水性恢复的时间 。
和 H 42 M) , 其它条件不变 , 配成胶料 4 ; 胶料
1 配方中 , 仅使用 180 份平均粒径 8 μm 的硅烷
处理氢氧化铝 , 其它成分不变 , 150 ℃热处理
3 h , 配成胶料 5 ; 胶料 1 配方中 , 仅使用 180 份
平均料径 1 μm 的硅烷处理氢氧化铝 , 5 份甲基
采取 2 种不同平均粒径且经硅烷处理的氢氧 化铝组合使用 , 可以显著改善绝缘子的耐电晕 性 、耐电弧性和耐漏电起痕性 。即平均粒径为 015~115μm 的硅烷处理氢氧化铝与平均粒径为 8~15μm 的硅烷处理氢氧化铝按质量比 60∶40~ 40∶60 混合 , 100 份甲基乙烯基硅橡胶生胶中的 总添加量为 100~300 份 。氢氧化铝的表面处理 剂可使用乙烯基三烷氧基硅烷 、四甲基二乙烯基 二硅氮烷 、六甲基二乙烯基三硅氮烷等含乙烯基 的硅烷偶联剂 ; 1 g 处理后的氢氧化铝中含 110 ×10 - 5~110 ×10 - 8mol 的乙烯基 。
711
1817
85
69
612
1911
耐漏电起痕性 / min 380 334 360 292 343 182 287 127
由表 28 可见 , V TES 及 A TH 的用量增加 , 硅橡胶的耐漏电起痕性相应增加 。硅烷偶联剂除 采用乙烯基三乙氧基硅烷外 , 还可以用乙烯基三 甲氧基硅烷 、甲基丙烯酰氧丙基三甲氧基硅烷 。 A TH 的粒径应在 10 μm 以下 ; 用量过多会影响 绝缘子部件的加工性 , 适宜的用量为 100 份甲基 乙烯基硅橡胶生胶中加 50~200 份 。气相法白炭 黑为补强剂 , 适宜的用量为 100 份硅橡胶中加 20~80 份 。配方中的石英粉为促进气相法白炭 黑与 A TH 在生胶中充分混合 、分散及赋予硅橡 胶导热性的成分 , 混炼硅橡胶的着色剂可以根据 实际需要选择炭黑 、红色氧化铁 、黄色氧化铁 、 黑色氧化铁及白色氧化钛 。混炼硅橡胶的塑性值 应控制在 250~350 , 以便于成形加工 。
- 718 18 018 210
大量添加氢氧化铝粉末可以提高硅橡胶的电 性能 , 满足高电压电绝缘体的要求 ; 但混炼硅橡 胶的加工性能会变差 , 硫化后的物理机械性能 低 。配方中添加适量的偏硼酸或原硼酸 , 使其在 混炼过程中与结构化控制剂反应 , 可促进混炼硅 橡胶的各组分混炼均匀 , 使胶料的加工性能得到 改善 , 硫化硅橡胶的机械强度提高 ; 其添加量为 100 份硅橡胶生胶中加 0101~110 份 。在配制胶 料过程中 , 应在 80~200 ℃下加热混炼 , 以促进 胶料的各组分均匀分散 。
裙构成 , 具有质量轻 、安全可靠 、抗无线电干 扰 、耐污性好 、安装费用低等优点 , 适用于高 压 、超高压输变电工程 , 自 20 世纪 60 年代后期 以来 , 作为瓷与玻璃绝缘子的有效替代物已得到 普遍应用[29 - 30 ] 。硅橡胶伞裙在合成绝缘子芯棒 的外面起承受高电场及保护芯棒的作用 ; 因此 , 对硅橡胶的性能要求是具有电绝缘性 、耐漏电起 痕 、耐电弧 、耐候 、阻燃 、耐低温及实用的物理 机械性能 。其中 , 耐漏电起痕性和电蚀损性是最 重要 的 性 能 指 标 , 通 常 都 是 按 IEC - 587 和 ASTM D 2303 测定 , 我国相应的标准为 GB/ T 6553 —1986 。漏电起痕是绝缘材料表面在有电位 差的部位形成炭化导电通路而使材料受到破坏的 一种现象 。材料耐漏电起痕性的优劣主要取决于 材料的结构与添加剂的种类 。硅橡胶的分子主链 由 Si —O 键 构 成 , Si —O 键 的 键 能 高 达 450 kJ / mol ; 因而耐热性好 , 即使在高温下也只 产生不导电的 SiO2 残渣 , 难以形成导电通路 , 所以具有很好的耐漏电起痕性 。与其它耐漏电起 痕材料一样 , 添加氢氧化铝粉末可使硅橡胶的升 压法 耐 漏 电 起 痕 等 级 ( SMAX) 达 到 最 高 级 610 kV [31 - 40 ] 。
表 29 氢氧化铝粒径对混炼硅橡胶耐湿性能的影响
1
2
3
4
5
70 310 350 815 ×1014 30 318 010380
72 410 250 312 ×1014 32 316 010372
70 318 290 318 ×1014 29 318 010435
65 310 360 312 ×1014 29 412 010410
氧化铝改为 90 份 , 其它条件不变 , 配成胶料 2 ;
胶料 1 配方中 , 将平均粒径 8μm 的硅烷处理氢
氧化铝改为 70 份 , 平均粒径 1μm 的硅烷处理氢
氧化铝改为 110 份 , 其它条件不变 , 配成胶料
3 ; 为比较 , 胶料 1 配方中 , 将硅烷处理氢氧化
铝改为未处理的氢氧化铝 (型号分别为 H 32 M
例 如 : 100 份 甲 基 乙 烯 基 硅 橡 胶 生 胶 [ (CH3) 2 (CH2 CH) SiO1/ 2链节封端 , (CH3) 2SiO链 节摩尔分数 99187 %、(CH3) (CH2 CH) SiO 链 节摩尔分数 0113 % , 平均聚合度约 5 000 ] 中 , 加入 25 份表面经二甲基二氯硅烷处理 、比表面 积 220 m2/ g 的气相法白炭黑 , 0105 份原硼酸 , 415 份粘度 30 mPa·s 的 α, ω- 二羟基聚二甲基 硅氧烷 , 在捏合机中混炼均一 , 再于 175 ℃下热
三甲基硅烷 , 其它成分不变 , 150 ℃处理 3 h ,
配成胶料 6 。
在胶料 1~6 中 , 分别加入 110 份双二五质
量分数为 40 %的双二五/ 甲基乙烯基硅橡胶生胶
/ 气相法白炭黑膏状物 , 在双辊炼胶机上分散均
匀 ; 在 165 ℃×10 min条件下热压硫化成厚度为
2 mm 及 1 mm 的试片 , 按下列方法评价性能 ,
配方中 V TES 及 A TH 的添加量对硫化硅橡 胶的耐漏电起痕性及其它物理性能的影响见表 28 , 其它成分及工艺条件不变 。
收稿日期 : 2005 - 10 - 11 。
第5期
黄文润. 混炼硅橡胶的配合技术 (五)
· 269 ·
V TES 用量 /份
1 015
1 015
1 015
1 015
72 315 250 511 ×1014 33 319 010381
+ 0128 813 ×1014
29 319 010562
+ 0130 512 ×1014
30 318 010402
+ 0125 412 ×1014
29 317 010430
+ 0188 211 ×108
15 918 01095
+ 0191 712 ×106
胶料编号
初期性能 邵尔 A 硬度/ 度 拉伸强度/ MPa 伸长率/ % 体积电阻率/Ω·cm 电气强度/ MV·m - 1 介电常数 (60 Hz) 介质损耗因数 (60 Hz) 浸水后的性能 质量变化率/ % 体积电阻率/Ω·cm 电气强度/ MV·m - 1 介电常数 (60 Hz) 介质损耗因数 (60 Hz) 浸硝酸后的性能 质量变化率/ % 邵尔 A 硬度/ 度 拉伸强度/ MPa 伸长率/ %
例 如 : 100 份 甲 基 乙 烯 基 硅 橡 胶 生 胶 [ (CH3) 2 (CH2 CH) Si1/ 2链节摩尔分数 01025 %、 (CH3) (CH2 CH) SiO 链节摩尔分数 0115 %、 (CH3) 2 SiO 链节摩尔分数 991825 %、平均聚合度 约 8 000 ]中 , 加入 5 份平均聚合度 10 的α, ω二 羟 基 聚 二 甲 基 硅 氧 烷 , 10 份 比 表 面 积 200 m2/ g的 气 相 法 白 炭 黑 , 110 份 平 均 粒 径