生产指令单
生产指令单

□自制
■焊装
销售订单号
产品名称
******有限公司
生产指令单
下单日期:
NO.:
文件编号:QR-MFG-051
■涂装
■总装
■改良
客户名称
要求完成时间
产品编号
生产数量
生产要求:
座椅:
发动机型号:
面漆颜色:
警灯:
控制器型号:
空调:
电机型号:
其他:
电池:
充电机:
其它要求: 1、配随车工具、充电机、合格证、备胎每台各1件; 2、整车车门线条均衡一致(包含:两侧共4扇门,后尾门的间隙都要调试好);
9、发车前要对整车内外清理和清洗。
10、前后安装“**”车牌;
11、配天能胶体电池;
12、注意整车的品质,做好细节,确保按时交货。
制单
审核
批准
发布:生产部 采购部 财务部 品管部 物控 仓库
版本:A/0保ຫໍສະໝຸດ 年限:2年3、电池必须具备在寒冷冬天0度以下低温时能正常使用,在0度以下-负10度时以40Km匀速续驶的一次充 电追的续驶里程一定要达到80Km;
4、必须保证仪表盘安装整齐美观。
5、必须保证整车油漆的品质崭新光亮。
6、车两侧挡板涂胶必须保证美观和均匀。 7、前包围的2个网罩保证硬度和美观。
8、必须保证车门胶条无磨损痕迹。
生产指令单
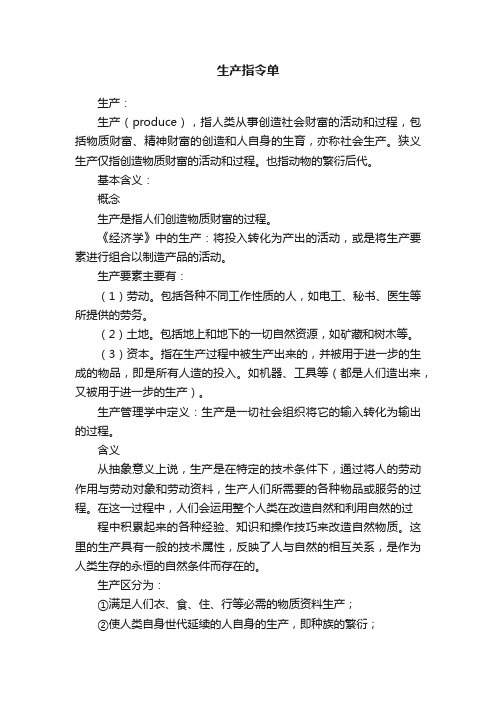
生产指令单生产:生产(produce),指人类从事创造社会财富的活动和过程,包括物质财富、精神财富的创造和人自身的生育,亦称社会生产。
狭义生产仅指创造物质财富的活动和过程。
也指动物的繁衍后代。
基本含义:概念生产是指人们创造物质财富的过程。
《经济学》中的生产:将投入转化为产出的活动,或是将生产要素进行组合以制造产品的活动。
生产要素主要有:(1)劳动。
包括各种不同工作性质的人,如电工、秘书、医生等所提供的劳务。
(2)土地。
包括地上和地下的一切自然资源,如矿藏和树木等。
(3)资本。
指在生产过程中被生产出来的,并被用于进一步的生成的物品,即是所有人造的投入。
如机器、工具等(都是人们造出来,又被用于进一步的生产)。
生产管理学中定义:生产是一切社会组织将它的输入转化为输出的过程。
含义从抽象意义上说,生产是在特定的技术条件下,通过将人的劳动作用与劳动对象和劳动资料,生产人们所需要的各种物品或服务的过程。
在这一过程中,人们会运用整个人类在改造自然和利用自然的过程中积累起来的各种经验、知识和操作技巧来改造自然物质。
这里的生产具有一般的技术属性,反映了人与自然的相互关系,是作为人类生存的永恒的自然条件而存在的。
生产区分为:①满足人们衣、食、住、行等必需的物质资料生产;②使人类自身世代延续的人自身的生产,即种族的繁衍;③满足人们必需的文化生活的精神生产(见物质生产与精神生产)。
马克思和恩格斯在《德意志意识形态》第1卷第1章中,将这三种生产分别称为“自己生命的生产”,“他人生命的生产”,“思想、观念、意识的生产”。
动物不进行物质资料的生产,它仅仅利用外部自然界,单纯地以自己的存在来改变自然界;也没有精神生产。
人类则必须通过劳动改变自然界,创造自己生活所需要的物质资料。
只有人类才进行物质和精神生产。
种族的繁衍作为自然行为是人和动物共有的,但人类的繁衍有一定的社会生活的组织形式。
类型生产类型是指根据生产过程的不同特点划分的类别。
生产指令单
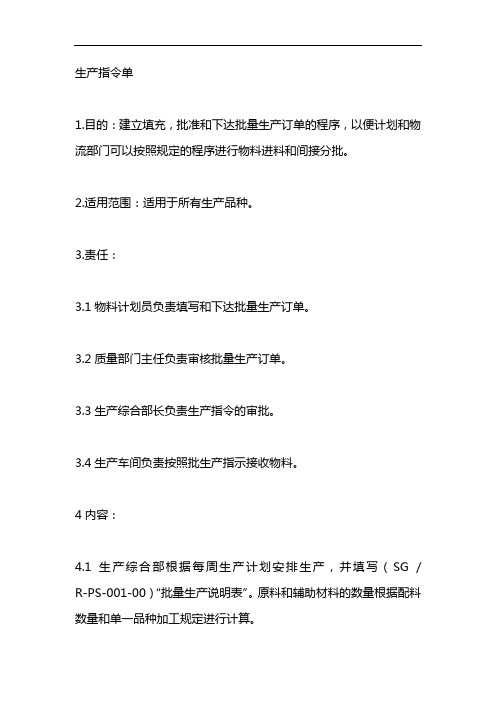
生产指令单1.目的:建立填充,批准和下达批量生产订单的程序,以便计划和物流部门可以按照规定的程序进行物料进料和间接分批。
2.适用范围:适用于所有生产品种。
3.责任:3.1物料计划员负责填写和下达批量生产订单。
3.2质量部门主任负责审核批量生产订单。
3.3生产综合部长负责生产指令的审批。
3.4生产车间负责按照批生产指示接收物料。
4内容:4.1生产综合部根据每周生产计划安排生产,并填写(SG / R-PS-001-00)“批量生产说明表”。
原料和辅助材料的数量根据配料数量和单一品种加工规定进行计算。
4.2完整的批量生产说明表应由质量部部长审查,并在综合生产部长批准后发布。
填写的内容应包括名称,批号,规格,生产能力以及准备用的原辅材料的名称,规格和剂量。
4.3批量生产说明书的说明书应明确注明产品名称,理论用量和固定用量,并规定计划工作时间4.4批准的批生产说明表一式四份,其中第一页是首页,由生产综合部门保存,第二页发送到计划后勤部门进行材料准备,第三页发送到车间。
带有批生产记录,第四个发送给质量控制人员。
4.5规划后勤部应在收到批量生产订单后准备材料。
4.6生产综合部门下达批量生产指导书后,车间领料员应按照指导书中规定的材料填写物料申请表,只有经车间主任批准后方可进行领料,仓库应根据请购单发出材料。
4.7提货时,提货成员应检查名称,规格,批号和数量。
检验正确后,仓库主管,仓库管理员和拣配人员应在物料拣配清单上签名以进行确认。
4.8物料拣选人员应将物料送到车间,以移出外室,清洁外包装,并执行《进入洁净区的物料提纯管理标准》(SG / SMP-CS-010-00)。
4.9配料人员应按批生产说明书领料,核对每种物料的名称,规格和数量,正确后在领料单上签名,交还领料员;车间主任应按照批量生产说明书和该品种的生产工艺规程组织生产。
4.10批量生产订单应在该品种生产前两天发布批量生产记录。
4.11如果任何部门在执行批量生产订单时遇到特殊情况而无法正常执行,则应向生产综合部门报告解决方案。
鞋厂生产指令单样本

12 120 180 180 180 660
序 号
部件
1 外头
材料名称
D7纹二层皮
耗量 单位
0.443 SF
工艺
印压
SBL黑2黑色
颜色 SBL- SBL红3白色 蓝5蓝色
采购单
SBL1金3灰色
材料名称
黑色D7纹二层皮
数量 单位
105 SF
2 内头
D7纹二层皮
0.127 SF
红色 白色 蓝色 灰色 红色D7纹二层皮
2双 1双
白/红 白/红 白/兰 白/金 灰色D7PU合3.5mm切片 黑色D7PU合3.5mm切片
白色 白色 白色 白色 红色D7PU合3.5mm切片 蓝色D7PU合3.5mm切片
7
m2
5
m2
7
m2
7
m2
34
35
36
37
38
39 40 舌面布标 41
置码 标
42
43
制 杜自孟
0.121 0.039 0.124 0.028 0.012 0.017
SF SF Y(S0F.3 8Y3(S0F.)2 3SYF)
电绣 N印IK刷E 印刷 画线 画线
黑色 红色 红色 红色 黑色 红色
红色 红色 红色 白色 白色 白色
黑色 蓝色 蓝色 蓝色 蓝色 蓝色
金色 金色D7纹二层皮 灰色 灰色D7纹二层皮 灰色 红色D7高剥纹太空合0.8mm丽心 灰色 黑色D7高剥纹太空合0.8mm丽心 金色 白色D7高剥纹太空合0.8mm丽心 灰色 蓝色D7高剥纹太空合0.8mm丽心
D7PU合3.5mm切片 0.036 m2
黑色 红色 蓝色 灰色 黑色丝光布合0.3cm海面+可特 11 Y
生产指令单模板

生产指令单
订单编号
产品编号
计划产量
产品名称
产品规格
ML
产品批号
指令对象
生产班组
日期
包材订单信息
序号
包材名称
规格
单位
生产用量
消耗定额%
批号
备注
1
瓶子
个
5%
2
喷头
个
5%
3
中罩
个
2%
4
外盖
个
2%
5
内盖(塞)
个
2%
6
肩座
个
2%
7
小盒(彩盒)
个
2%
8
内衬、吸塑
个
2%
9
瓶标/瓶底标
个
5%盒(展示盒)
个
2%
11
中包(箱)
个
2%
12
外箱
个
1%
13
挂件及附件
个
2%
14
小膜(OPP)
个
5%
15
其它
个
2%
16
17
18
备注:1.严格按产品质量标准、各工序标准操作法进行操作;
2.瓶身标要贴正,不能翘标、有气泡,位置按照产品资料标准要求粘贴;
3.不可漏装、少装,包装箱内不可存在碎玻璃、刀片、虫蚁、金属等有害物质!
生产指令单
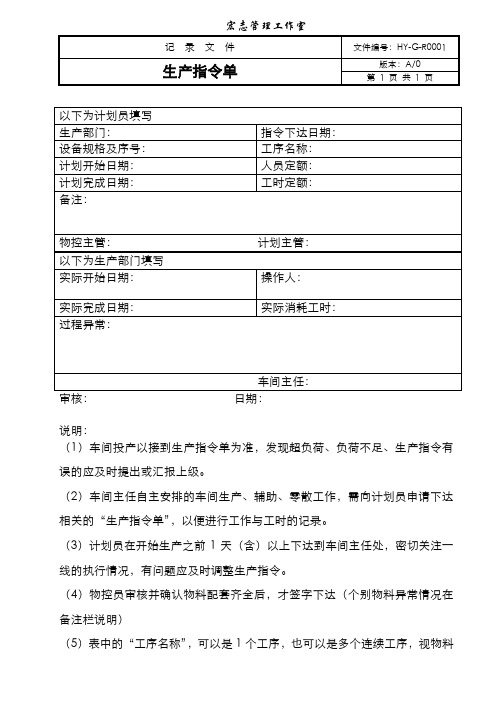
说明:
(1)车间投产以接到生产指令单为准,发现超负荷、负荷不足、生产指令有误的应及时提出或汇报上级。
(2)车间主任自主安排的车间生产、辅助、零散工作,需向计划员申请下达相关的“生产指令单”,以便进行工作与工时的记录。
(3)计划员在开始生产之前1天(含)以上下达到车间主任处,密切关注一线的执行情况,有问题应及时调整生产指令。
(4)物控员审核并确认物料配套齐全后,才签字下达(个别物料异常情况在备注栏说明)
(5)表中的“工序名称”,可以是1个工序,也可以是多个连续工序,视物料
到位情况而定
(6)完工后,车间须如实填写指定内容,签字确认,并提交到计划员处(7)计划员核算工时效率(并汇总整机工时效率),审核,归档,保存期1年。
需计算车间月度累计工时效率和单机工时效率。
生产指令单
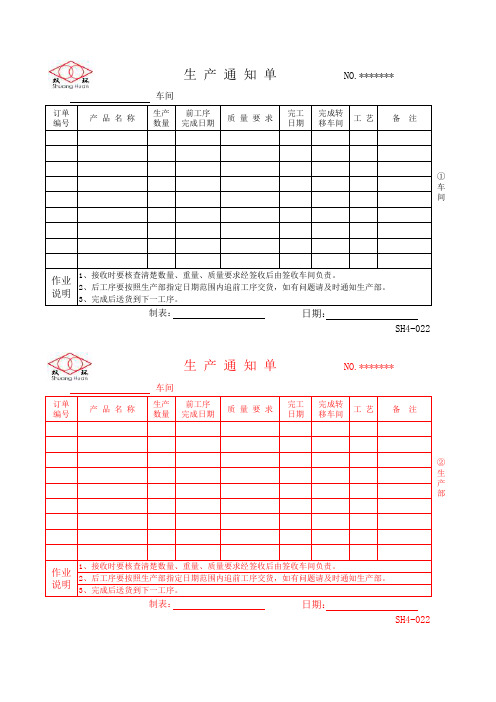
NO.*******
订单 编号
产品名称
车间
生产 前工序 数量 完成日期
质量要求
完工 日期
完成转 移车间
工艺
备注
① 车 间
作业 说明
1、接收时要核查清楚数量、重量、质量要求经签收后由签收车间负责。 2、后工序要按照生产部指定日期范围内追前工序交货,如有问题请及时通知生产部。 3、完成后送货到下一工序。
制表:
日期:
SH4-022
生产通知单
NO.*******
订单 编号
产品名称
车间
生产 前工序 数量 完成日期
质量要求
完工 日期
完成转 移车间
工艺
备注
② 查清楚数量、重量、质量要求经签收后由签收车间负责。 2、后工序要按照生产部指定日期范围内追前工序交货,如有问题请及时通知生产部。 3、完成后送货到下一工序。
制表:
日期:
SH4-022
生产指令单

生产制造命令单生产制造命令单日期_____________ 生产部门生产单号产品名称产品规格使料号品名规格单位用材生产日期产品编号生产数量料标准用量SPARE 备注单机用量制造方法完成日期移交单位生产计划主管生产计划员生产指令单主要包括:要生产的物品、生产的工位或机台、生产用时、工期要求、要生产工件的数量物料使用等;1、地面水泥砂浆找平层。
2、内墙抹水泥砂浆找平层,刮防水腻子,刷乳胶漆。
3、顶棚清理,刷白水泥浆。
4、订做及安装塑钢门窗及铝合金百叶风口。
5、增加钢楼梯及栏杆。
6、增加排水沟盖板。
注:本指令单所指令施工的内容均属较紧急的项目,施工单位在接到本指令单后应立即答复是否按指令执行,否则按默认认定;涉及到隐蔽工程或以后无法计量的工程,施工单位须在动工前通知计划部现场核查,并形成原始记录,附在签证单后。
工作指令单编号:建设单位:河北东都房地产开发有限公司分部分项工程锅炉房土建工程监理单位:河北远大工程咨询有限公司跟踪审计单位:部位北京市建壮咨询有限公司地基处理施工单位:承德隆泰建设工程有限责任公司指令标题:锅炉房施工指令人:日期:签发人日期:签收人日期:根据地基验槽记录,基槽曾被雨水浸泡过,建议将浸软土清除后依处理方案处理,处理方案如下:基地下300 厚土层挖除,换C15 砼浇注。
注:本指令单所指令施工的内容均属较紧急的项目,施工单位在接到本指令单后应立即答复是否按指令执行,否则按默认认定;涉及到隐蔽工程或以后无法计量的工程,施工单位须在动工前通知计划部现场核查,并形成原始记录,附在签证单后。
工作指令单编号:建设单位:河北东都房地产开发有限公司分部分项工程锅炉房土建工程监理单位:河北远大工程咨询有限公司跟踪审计单位:部位北京市建壮咨询有限公司锅炉房外防水施工单位:承德隆泰建设工程有限责任公司指令标题:锅炉房施工指令人:日期:签发人日期:签收人日期:根据图纸会审记录,增加锅炉房外墙防水,以防明水灌入室内。
- 1、下载文档前请自行甄别文档内容的完整性,平台不提供额外的编辑、内容补充、找答案等附加服务。
- 2、"仅部分预览"的文档,不可在线预览部分如存在完整性等问题,可反馈申请退款(可完整预览的文档不适用该条件!)。
- 3、如文档侵犯您的权益,请联系客服反馈,我们会尽快为您处理(人工客服工作时间:9:00-18:30)。
m2黑色红色蓝色灰色11Y 23舌面布标1双白/红白/红白/兰白/金
50Y 24舌里标1
双6m 225鞋带11双白色白色白色白色2m 226鞋带21双黑色红色黑色金色26Y 27中底1
双10Y 28大底1
双白/红白/红白/兰白/金12m 229跟1
双27Y 30天皮2
双白/红白/红白/兰白/金7m 231防水台1
生产指令单
品名低帮楦型8283数量
下单日期
36373839404136373839404136373839404136373839404112332112SBL-2黑红102030302010120SBL-3白红153045453015180SBL-5蓝黑
153045453015180SBL-13灰金
15304545301518055
55
SBL-2黑红SBL-3白红SBL-5蓝黑SBL-13灰金
数量单位
1外头0.443SF 印压黑色
红色蓝色金色105SF 2内头0.127SF 红色白色蓝色灰色220SF 3前护眼0.088SF 黑色红色蓝色金色23SF 4后护眼0.127SF 红色红色蓝色灰色171SF 6边侧饰0.121SF 黑色
0.066Y 黑色白色白色白色7Y 16内头补强0.011m 2白色白色黑色白色7Y 17后方补强0.028Y 白色白色黑色白色3Y 18外头补强0.026Y 白色白色黑色白色7Y 19后棉0.017m 2白色白色白色白色13Y 20前衬0.019Y 白色白色白色白色13Y 21后衬0.021Y 白色白色白色白色15Y 22面衬
0.8mm布底PU合3mm海棉+可特D7高剥纹太空合0.8mm丽心布牛津布梦缘鞋业有限公司生产指令单
序号部单材料名称
配色
金色D7纹二层皮D7纹二层皮D7纹二层皮蓝色D7纹二层皮D7纹二层皮D7纹二层皮D7纹二层皮黑色D7纹二层皮红色D7纹二层皮白色D7纹二层皮灰色0.8mm布底PU合3mm海棉+可特耗量黑色D7高剥纹太空合0.8mm丽心布鞋图
黑色1.2mm切片过不干胶1.0mm海棉1.2mm低温港宝
白色1.2mm切片过不干胶蓝色0.8mm布底PU合3mm海棉+可特红色0.8mm布底PU合3mm海棉+可特红色0.8mm布底PU 灰色0.8mm布底PU
白色丝光布合0.3cm海面+可特白色牛津布黑色丝光布合0.3cm海面+可特1.0mm低温港宝1.0mm低温港宝黑色0.8mm布底PU合3mm海棉+可特白色D7高剥纹太空合0.8mm丽心布蓝色0.8mm布底PU 金色D7高剥纹太空合0.8mm丽心布灰色D7高剥纹太空合0.8mm丽心布白色0.8mm布底PU合3mm海棉+可特1.2mm切片过不干胶1.0cm海棉0.8mm布底PU合3mm海棉+可特0.8mm布底PU 丝光布合0.3cm海面+可特丝光布合0.3cm海面+可特0.8mm布底PU 1.3mm切片过不干胶D7高剥纹太空合0.8mm丽心布D7纹二层皮D7纹二层皮
5m 232大底外线
白色白色白色白色
7m 2337
m
234353637383940414243
1.1m长椭圆形鞋带(放)D7PU合3.5mm切片1.1m长椭圆形鞋带(穿)8283#中底舌面布标置码标
8283#跟杜自孟
蓝色D7PU合3.5mm切片
黑色D7PU合3.5mm切片8283#防水台红色D7PU合3.5mm切片批次客人号码配码大底号码冲刀号码鞋楦号码灰色D7PU合3.5mm切片黑色牛津布
2012-02-15
黑色0.8mm布底PU 灰色D7纹二层皮
红色D7高剥纹太空合0.8mm丽心布蓝色D7高剥纹太空合0.8mm丽心布SBL-13灰金
SBL-2黑红
SBL-3白红
SBL-5蓝黑
红色黑色金色118SF 8上后方0.039SF 电绣NIKE 红色红色蓝色灰色75SF 9下后方0.124
SF
印刷红色红色蓝色灰色4Y 5边肚0.028Y(0.383SF)
印刷红色白色蓝色灰色2Y 7领口0.012Y(0.23SF)
画线黑色白色蓝色金色8Y 10舌面0.017Y
画线红色
白色蓝色灰色8Y 11舌里0.017Y 黑色红色蓝色灰色4Y 12后里0.051Y 黑色红色蓝色灰色2Y 13包跟皮0.017Y 红色红色蓝色灰色6Y 14头里0.025Y 黑色白色白色白色4Y 15边里