生产指令单管理规定
生产指令管理规程

1. 目的保证血清生产与与生产工艺规程一致,避免口头传达错误,规范生产而制定。
2. 范围新生牛血清生产指令和包装指令。
3. 职责3.1. 生产部经理:负责下达生产、批包装指令的起草、审核、放行。
3.2. 生产车间:负责指令的实施和归档。
3.3. 质量管理部:负责指令的存档。
3.4. 总经理:负责本规程的批准。
4. 定义无5. 引用标准无6. 材料6.1. 仪器设备无6.2. 器械、用具7. 流程图无8. 内容8.1. 生产指令时间、批号、生产数量、批准、放行等内容。
8.1.1. 下达指令方式以书面的形式下发。
8.1.2. 落实指令是以:批生产记录形式。
8.2. 生产指令的下达工作程序8.2.1. 生产指令单按照文件管理的要求,经批准生效后将基准空白表存放于企业生产负责人办公室。
不许由车间管理基准空白指令。
8.2.2. 生产指令一旦生效下发,即为车间组织生产的唯一合理依据,生产不得任意变更或修改,必须严格遵照执行。
同时,要杜绝任何无指令的生产和拖延生产的现象发生。
8.3. 生产指令的使用与复核8.3.1. 各操作人员在生产过程中要严格执行各项操作指令,认真填写批生产记录(批包装记录)的有关部分,同时要将各种有关的凭证附于批记录之后。
8.3.2. 各工序的操作人员及复核人要分别确认某项操作已经完成,分别签字,注明日期。
8.3.3. 本批产品生产结束,经车间班组长收集、清点、确定无遗漏后,交生产部经理审核。
8.3.4. 上述签字后的批记录及生产指令一并上交质量管理部门汇入批记录,由质量管理部门进行批审核评价,作为产品是否放行的依据之一。
9. 注意事项无10. 附录及派生记录10.1. 生产指令单F-SMP-SC002-0110.2. 包装指令单F-SMP-SC002-0111. 相关文件无12. 修订记录。
生产指令的编制与管理规程

生产指令的编制与管理规程
目的:
建立生产指令的编制规程,使生产指令的编制规范化、标准化。
确保生产按正常秩序进行。
范围:
每个产品批量生产均应有正式批准的生产指令。
责任:
质保部负责组织编制;
质保部部长审核;
主管生产的副总经理批准;
生产部工艺技术员、生产车间负责执行。
内容:
1.生产指令是能够准确地再现产品工艺规程中的生产方法、工艺要求、技术质量标准、使用的设备,进而明确生产地点、作业条件和程序等,用以规范药品生产作业活动的指令性技术文件。
2.编制依据
2.1产品法定标准及注册(批复)批准文件
2.2产品的验证文件
2.3工艺规程
2.4有关的标准操作规程(SOP)
3.编制基本内容
3.1批生产指令单内容包括:生产指令单号、指令依据、产品名称、规格、生产批量、
产品批号、生产开始时间、生产结束时间、填表人、填表日期、审核人、审核日期、批准人、批准日期、物料指令领用量。
3.2批记录指令性内容包括:包括生产工序、批记录文件号、指示内容、生产条件、操作条件等。
4. 生产指令标准管理
4.1生产指令必须在生产前三天下发到车间。
4.2车间必须在生产前一天下发到各工序。
5.附件:生产指令收发记录TG-Q71-008-01。
药品生产指令制定和执行管理规定
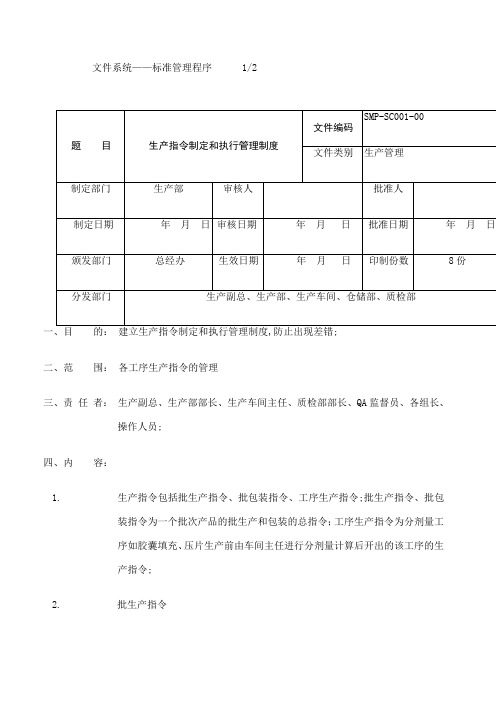
文件系统——标准管理程序 1/2二、范围:各工序生产指令的管理三、责任者:生产副总、生产部部长、生产车间主任、质检部部长、QA监督员、各组长、操作人员;四、内容:1. 生产指令包括批生产指令、批包装指令、工序生产指令;批生产指令、批包装指令为一个批次产品的批生产和包装的总指令;工序生产指令为分剂量工序如胶囊填充、压片生产前由车间主任进行分剂量计算后开出的该工序的生产指令;2. 批生产指令制订与发放:生产部根据生产计划开具一式三份批生产指令,生产部部长审核批准后,下发给仓库、车间,原件作为基准文件留存,满一年校期后销毁;车间主任将批生产指令单连同整理好的空白生产记录交生产的起始工序组长,据此开具领料单,仓库保管员核对批生产指令单领料单一致后方可发放物料;指令内容:1产品名称、代码、规格、批量、批号、执行日期、制订依据;2)原辅材料的名称、批号、用量,检验编号3备注3.批包装指令制订与发放:由车间主任根据待包产品开出批包装指令一式四份,经QA审核无误签字后,交生产部部长在半个工作日内签字批准,正本生产部留底,一份副本交仓储部,另两份交内包工序和外包工序;指令内容:1产品名称、代码、规格、批量、批号、执行日期2待包产品和包材的名称、批号、用量、检验编号;标签类包材如需预先打印批号、有效期,则由车间主任开出批号打印指令单,注明打印批号、生产日期或有效期及打印数量,经QA复核签字后一份留存,一份交批号打印人员作为领取包装材料和操作的依据,并附于打印记录上; 固体制剂的内包装操作,必须凭半成品检验报告单由车间主任开出该工序指令单,内容包括内包装规格,印制批号及所需内包材数量,经QA复核签字后,一份留存,一份交该工序作为操作依据; 批包装指令单包材用量的折算:包材的理论需要量根据工艺规程规定的标准批用量的100%进行折算,领用量限额根据工艺规程规定的工艺消耗定额进行折算,凡超出限额的包装材料须使用补料单以示区别;4.工序生产指令:制订与发放:生产前由车间主任进行分剂量计算后开出工序的生产指令,一式两份,QA复核后一份留存,一份传递给相应工序组长;内容:1产品名称、代码、规格、批量、批号、执行日期2工序名称3分剂量计算及注意事项;分剂量计算要求:必须按标示量的100%进行折算,装量差异与重量差异以内控标准中规定的为依据;5. 生产指令号编制方法:编码+批号;编码规则:批生产ZS;批包装ZB;制粒ZZ;总混ZH;压片ZY;充填ZC;内包装ZN;外包装打印指令ZD;例:生产指令号:ZS-110901 表示为批号为110901的批生产指令;6.所有的指令均要保留或收集于批生产记录中存档;每批产品生产结束后,本批的生产指令和各岗位的生产记录等一并由有关管理人员收集、整理、审核并按程序递交,由质量保证部进行终审,作为产品放行的依据;批生产指令文件编码:RD-TSZ001-00批包装指令文件编码:RD-TSZ002-00制粒工序指令文件编码:RD-TSZ003-00本指令一式两份,车间一份,岗位一份;总混指令文件编码:RD-TSZ004-00压片充填指令文件编码:RD-TSZ005-00内包装指令单文件编码:RD-TSZ006-00外包装打印指令单文件编码:RD-TSZ007-00。
生产指令单
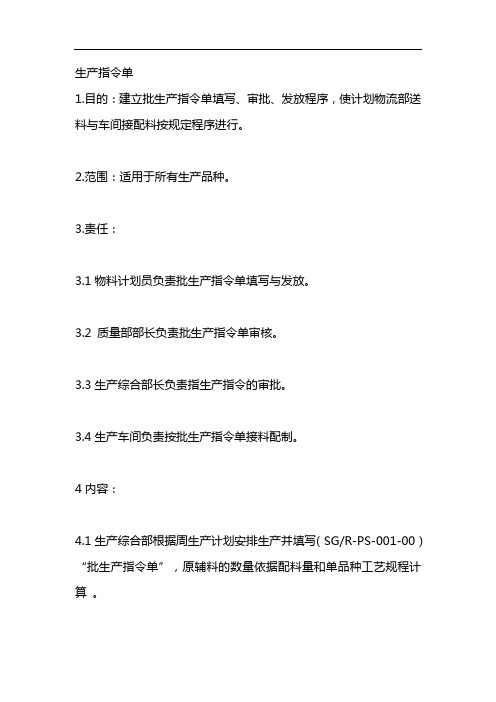
生产指令单1.目的:建立批生产指令单填写、审批、发放程序,使计划物流部送料与车间接配料按规定程序进行。
2.范围:适用于所有生产品种。
3.责任:3.1物料计划员负责批生产指令单填写与发放。
3.2 质量部部长负责批生产指令单审核。
3.3生产综合部长负责指生产指令的审批。
3.4生产车间负责按批生产指令单接料配制。
4内容:4.1生产综合部根据周生产计划安排生产并填写(SG/R-PS-001-00)“批生产指令单”,原辅料的数量依据配料量和单品种工艺规程计算。
4.2填写好的批生产指令单由质量部部长审核,生产综合部长批准后下发,填写内容应有品名、批号、规格、生产量及配制用原辅料的品名、规格、用量等。
4.3批生产指令单的指令单要明确规定产品名称,理论用量,与定额用量,并规定出计划工时4.4经批准的批生产指令单,一式四份,一份为首页,由生产综合部留存,第二份发计划物流部备料,第三份随批生产记录发至车间,第四份发质控员。
4.5计划物流部接到批生产指令单后备料。
4.6 生产综合部下达批生产指令后,车间领料员按指令单规定的物料填写物料领用单,经车间主任批准,方可领料,库房按领料单发料。
4.7 领料时领料员要核对品名、规格、批号、数量,检验无误后,由仓储主管、库管员、领料员在物料领用单上签字确认。
4.8领料员将物料送至车间脱外间,清洁外包装,执行“物料进入洁净区净化管理标准”(SG/SMP-CS-010-00)。
4.9配料人员凭批生产指令单接料,核对各项物料的品名、规格、数量,无误后在领料单上签字,返给领料员;车间主任根据批生产指令单按该品种生产工艺规程组织生产。
4.10批生产指令单在生产该品种前二天随批生产记录下发。
4.11任何部门在批生产指令单执行过程中遇到特殊情况不能正常执行时,上报生产综合部解决。
生产指令流转管理规程

目的:建立生产指令流转管理的标准规程,明确生产指令的标准,使生产过程的指令信息畅通无误,保证车间生产严格按生产指令操作,避免人为差错。
范围:一个批次产品生产指令流转的全过程。
责任者:成药事业部负责实施,提取制剂仓储部门负责执行。
内容:1 生产指令是成药事业部根据市场需求情况以及原辅料、包装材料供应情况和设备生产能力情况,并严格按照产品工艺规程下达给成药事业部生产车间及仓库的命令,车间和仓库必须认真执行。
而生产指令单是生产指令内容的物料控制数量和工艺流程的确定,以及生产所要执行的工艺依据和岗位操作依据。
2 生产指令流转程序:2.1 生产指令是以指令单的形式出现,其具体内容:批生产指令单、配料指令单、批包装指令单。
2.2 成药事业部调度员根据生产计划提前制定批生产指令单、配料指令单、批包装指令单,经成药事业部经理审核、批准后,下发给生产车间。
2.3 车间主管收到批生产指令单、配料指令单、批包装指令单并确认后发给车间物料核算员,由物料核算员根据批生产指令单和批包装指令填写需料领料单,经车间主管批准后,交给仓库备料。
仓库保管员按单准备物料,保证物料的正常使用。
2.4 核算员填写需料领料单后,及时将批生产指令单、配料指令单、批包装指单返回交给车间工艺员。
工艺员根据批生产指令单、批包装指令单下发批生产记录、批包装记录,由各工段长签收。
2.5 工段长接到指令后,根据指令内容填写本次工作状态标识,并将批生产记录、批包装记录下发到岗位操作人员手中。
2.6 岗位操作人员在生产过程中严格按批生产记录、批包装记录中有关指令的内容操作,并将检验报告单、清场合格证等有关凭证附在批生产记录、批包装记录上。
2.7 生产结束后,工段长将各岗位批生产记录、批包装记录收集审核后上交车间工艺员。
工艺员清点无遗漏后填写批生产记录审核单(CY-F-PR-107-00),再交车间主管审核签字,装订后送交成药事业部审核。
2.8 成药事业部审核无误后在成品放行审核单上签字,然后交给质量技术部进行复核,以此作为决定产品放行的主要依据。
XX公司生产指令下达管理规程
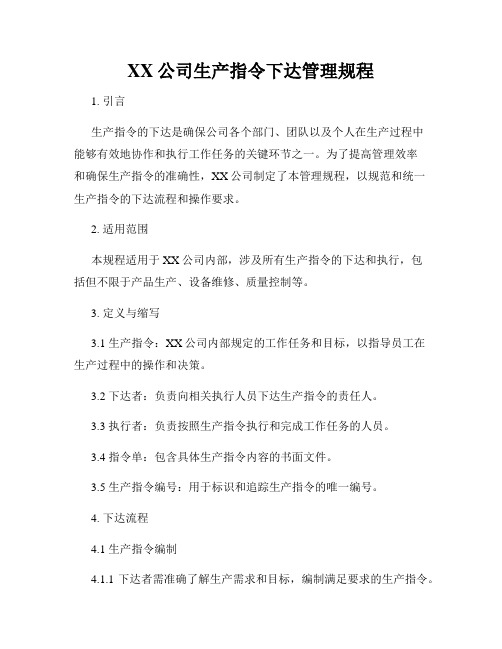
XX公司生产指令下达管理规程1. 引言生产指令的下达是确保公司各个部门、团队以及个人在生产过程中能够有效地协作和执行工作任务的关键环节之一。
为了提高管理效率和确保生产指令的准确性,XX公司制定了本管理规程,以规范和统一生产指令的下达流程和操作要求。
2. 适用范围本规程适用于XX公司内部,涉及所有生产指令的下达和执行,包括但不限于产品生产、设备维修、质量控制等。
3. 定义与缩写3.1 生产指令:XX公司内部规定的工作任务和目标,以指导员工在生产过程中的操作和决策。
3.2 下达者:负责向相关执行人员下达生产指令的责任人。
3.3 执行者:负责按照生产指令执行和完成工作任务的人员。
3.4 指令单:包含具体生产指令内容的书面文件。
3.5 生产指令编号:用于标识和追踪生产指令的唯一编号。
4. 下达流程4.1 生产指令编制4.1.1 下达者需准确了解生产需求和目标,编制满足要求的生产指令。
4.1.2 生产指令应包括但不限于以下内容:a) 生产指令编号;b) 生产任务的具体要求和工作步骤;c) 相关人员、部门或团队的责任和权限;d) 生产指令的执行期限;e) 监督和检查要点;f) 附件或参考文件,如相关图纸、规范等。
4.2 生产指令审批4.2.1 下达者应将编制完成的生产指令提交给上级主管部门或领导进行审批。
4.2.2 审批人员应仔细审阅生产指令,核对内容的合理性和准确性,如有需要,可提出修改意见或补充要求。
4.2.3 下达者应及时响应审批人员的意见和要求进行修改,并重新提交审批。
4.3 生产指令下达4.3.1 一旦生产指令通过审批,下达者应及时将指令传达给相关执行者。
4.3.2 下达方式可以采用口头、书面或电子邮件等形式,但需确保下达的内容明确准确,并且能够被执行者准确理解。
5. 生产指令执行与监督5.1 执行者在接收到生产指令后,应认真阅读和理解指令内容,并按照要求制定相应的工作计划。
5.2 执行者应全力配合,确保按时按量完成指令要求的工作任务。
制药企业生产作业指令管理规程(GMP)
目的:本程序依据《药品生产质量管理规范》(2010修订版)规定了生产作业指令管理程序。
范围:本程序适用于生产作业指令管理。
职责:质量管理部、生产部
内容:
1生产作业指令的下达
1.1生产作业计划:由生产部根据下月的产品销售计划及排产计划,合理制定各生产分厂生产作业计划,作业计划的安排以各生产分厂为单位,下达生产品种、批次/批号、数量以及生产完成时间,并下发至各生产分厂及有关部门,各生产分厂按计划组织实施。
1.2批生产指令:由生产部根据作业计划,下达各品种各批次批生产指令,明确产品品名、批次、规格、下达时间,工艺要求,随批生产记录流转,并与生产分厂建立批生产指令移交记录。
1.3批包装指令:由生产部根据作业计划,在产品包装前下达批包装指令,明确产品品名、批次、规格、包装、下达时间,包装要求及包材预计耗用数量,随批生产记录流转,并与车间建立批包装指令移交记录。
1.4特殊要求指令:对工序除按正常工艺规程及岗位标准操作程序执行外,有特殊要求可在批指令备注栏中注明或生产部直接下达生产作业指导书。
1.5分厂作业指导书:
1.5.1各生产分厂根据批指令,下达工序作业指导书,经分厂厂长审核后执行。
1.5.2有特殊要求时,由分厂厂长下达作业指导书,各工序班组长监督落实。
2各分厂、各工序如遇对生产指令不明,有疑问,应确认后再执行。
3指令变更
3.1如下达的指令在某分厂因特殊原因需要变动,生产部须对特殊原因进行了解核实,确认需改动,则由生产部下达变更指令。
3.2根据市场需要对已下达的计划进行调整或变更,应下达补充计划并予以说明。
4生产分厂不得随意变更生产计划,无法执行时,应报告生产部。
SMP-SC002-01生产指令(包装指令)管理规程
SMP-SC002-01⽣产指令(包装指令)管理规程⽬的:为保证⽣产有计划,有依据,有⽬的地进⾏,建⽴⽣产指令管理规程,确保⽣产系统畅通⽆误。
适⽤范围:批⽣产批令、批包装指令。
责任⼈:⽣产部⼈员及相关⼈员严格执⾏本规程;⽣产部主管负责本规程实施过程的指导与检查;]QA负责本规程实施过程的监控。
内容:1、⽣产指令是指导⽣产的重要⽂件,是⽣产车间的执⾏⽣产命令的唯⼀依据。
除特殊原因外,⽣产指令⼀经批准⽣效,任何⼈不得随意变更或修改,必须严格遵照执⾏。
2、⽣产指令包括批⽣产指令和批包装指令。
3、⽣产部根据⽣产计划下达⽣产指令。
由⽣产部管理⼈员填写《批⽣产指令单》、《批包装指令单》,经⽣产部主管审核,签字后⽣效。
4、《批⽣产指令单》、《批包装批令单》⼀式三份,品质部⼀份,⽣产车间⼀份,⽣产部留底⼀份。
5、仓库依据批⽣产指令单(批包装批令单)备料;⽣产车间依据批⽣产指令单(批包装批令单)组织⽣产;品质部依据批⽣产指令单(批包装批令单)组织质量监控和质量检验。
6、⽣产结束后,⽣产车间的批⽣产指令单(批包装批令单)归⼊批⽣产记录(批包装记录)中,存档保存。
7、批⽣产指令(批包装指令)单号的编制⽅法7.1批⽣产指令单号由“⼤写字母S-成品代码-⽣产年号后两位阿拉伯数字-该产品本年累计流⽔号(三位数)”组成。
成品代码:强体蛋⽩粉为01;成长⾼蛋⽩粉为02;7.2包装指令单号由“⼤写字母B-成品代码-包装年号后两位阿拉伯数字-该产品本年累计流⽔号(三位数)”组成。
成品代码:强体蛋⽩粉为01;成长⾼蛋⽩粉为02;8、相关记录《批⽣产指令单》、《批包装指令单》。
批生产指令管理规程(含表格)
文件制修订记录
1.目的:
规范生产指令的制定、下达程序,确保生产、质量、物料等部门间协调运作。
2.适用范围:
批生产指令单、批包装指令单。
3.职责:
生产管理部、质量管理部、供应链部对本规程的实施负责。
4.控制要求:
4.1编制:生产管理部根据生产计划和待包装产品数量,提前一天制订并填写批生产指令单和批包装指令单。
填写好的批生产指令单和批包装指令单由生产管理部负责人、QA、质量管理部负责人审核签字后下发。
所有审核人员的签字同意,即代表各自部门已做好相应的准备工作,可以按时完成生产和检验、管理工作。
4.2指令内容
4.2.1生产指令单的内容包括产品名称、产品代码、规格、产品批号、批量、生产日期、原辅料编码、原辅料名称、原辅料包装规格、指令用量、检验单号、指令编定人、指令下达日期、指令编号、批准人。
4.2.2批包装指令单的内容包括产品名称、产品代码、规格、产品批号、批量、包装规格、包装日期、主要包装材料编码、包材名称、指令用量、检验单号、指令编定人、批准人、指令下达日期。
4.3执行:经批准的批生产指令单和批包装指令单为一式两份,一份发生产车间,与批生产记录一起保存,一份发仓库,负责按批生产指令单和批包装指令单准备检验合格的物料。
生产指令一经下达,所有相关部门应积极配合,保证生产计划的按时完成。
4.4变更:遇到特殊情况,需要撤销或变更已发出的生产指令单时,由生产管理部对原指令单收回、销毁,重新下发新的生产指令单,不可在原指令单上修改后继续使用
5.记录
批生产指令单
批包装指令单
批生产指令单
批包装指令单。
生产指令下达管理规程
生产指令下达管理规程
一、目的:
建立生产指令下达的标准工作程序,确保生产过程中的指令信息系统畅通无误
二、范围:
一个批次产品生产的全过程
三、责任者:
生产部、各车间主任
四、正文
1.生产指令的内容
1.1生产指令单(包装指令单);
2.生产指令的制定依据
2.1月度生产计划及内外贸部的临时要求;
2.2设备生产能力(经验证已达到的能力);
3.3工序人员操作能力。
4.生产指令号
以7位阿拉伯数字表示。
第一、二位为年份,第三、四位为月份,最后三位为本月所下的生产指令的序列号(OOl〜999之间)。
例:生产指令号:第1305008号,表示为2013年5月的第008号该工序的生产指令。
5.生产指令下达的工作程序
5.1生产车间班组长根据生产计划规定的品种和批次计划编制生产指令单,一式两份,经车间主任审查,于生产前下达到生产岗位和质量保证部;车间在中间产品待包装时,根据实际产量开出包装指令单,一式两份,经车间主任审查,于包装前下达到生产岗位和质量保证部,车间领料员持领料单向仓库领取包装材料。
车间主任根据批生产指令、批包装指令上生产加工时间及周期要求,结合实际情况安排本车间生产操作。
4.2生产指令一经生效下发,即为操作人员进行操作的基准文件,必须严格遵照执行,任何人不得任意变更和修改。
5.生产指令的使用与复核
5.1生产车间根据生产(包装)指令单开领料单,经车间主任批准后,由车间领料员持单交仓库备料。
车间领料员凭生产指令单、包装指令单接收上车间或上工序转来的中间产品。
- 1、下载文档前请自行甄别文档内容的完整性,平台不提供额外的编辑、内容补充、找答案等附加服务。
- 2、"仅部分预览"的文档,不可在线预览部分如存在完整性等问题,可反馈申请退款(可完整预览的文档不适用该条件!)。
- 3、如文档侵犯您的权益,请联系客服反馈,我们会尽快为您处理(人工客服工作时间:9:00-18:30)。
1 目的
通过对指令单的管理,使整个生产进度处于受控状态
2范围
本规定适用于机加车间的零部件加工过程指令单和装配车间的压缩机装配过程指令单的管理。
3术语
无
4职责、规定、流程
4.1职责
生产部计划员负责指令单的编制
质量部负责对生产过程中不合格信息的及时反馈,并对不合格品评审意见进行跟踪
生产部车间负责指令单的实施
规定
4.2.1下单:
A、下单数量:根据月度生产计划中日计划数量和前期指令单的完成情况(目的是控制月度实际生产
进度和车间在制品数量)确定下单数量
B、下单产品型号、图号及名称:根据月度生产计划和生产准备情况下单。
当零部件备料(用ERP
中的生产需求分析工具进行分析)、刀具、工装等生产准备符合要求后,编制指令单。
C、下单周期:机加车间指令单每周一、三、五各下一次,装配车间指令单每天下一次。
D、下单时间:应提前一天以上下单给仓库、车间,便于仓库备料、车间进行生产准备。
市场急需时,
下单时间可变更。
例:星期三、星期四机加车间的指令单应在星期一16:00至星期二9:00前下发
星期三装配车间的指令单应在星期一16:00至星期二9:00前下发
4.2.2配料:
A、配料及补料数量:配料是根据新指令单和车间反馈的前期指令单实际完成情况(目的是控制车间
在制品数量)按指令单配套发料,并同时打印《领料单》(ERP自动下账)。
补料是装配车间因零部件不合格,需补发物料到车间补料仓(应确保补料仓的物料控制在规定的范围内)。
车间班组长应提前通知仓库,仓库补料、打印《补料单》(ERP自动下账)。
B、配料产品标识:机加产品应每配料箱或筐内放置《产品跟踪卡》。
装配车间应每配料箱或筐内放置
《产品标识卡》
C、物流要求:按不同班组对应的物流工位器具目视表要求配料。
D、配料地点:机加车间的零部件配料到相应班组的毛坯存放区。
装配车间需清洗的零件配料到清洗
车间的待洗区;装配不需清洗的零件应配送到车间对应零件的配料缓冲区(见地面标识)。
E、配料时间:每天下午3:00后将车间第二天需求的物料发到车间(车间收料后,应及时在相应的单
据上签字确认)。
部分物料可第二天早上9:00前配送到车间(前提是不能影响车间的正常生产)
4.2.3生产:
A、生产进度:按指令单完工时间安排生产的先后顺序。
B、生产数量:车间应严格按指令单的数量安排生产。
机加车间应确保发出数量全部完工入库。
装配
车间应确保按指令单数量完工。
装配过程中,当有不合格品产生而影响完工数量时,应从补料库中取料确保完成指令单规定的数量。
C、不合格品管理:能返工、返修的产品均应当班安排返修。
机加车间的不能当班返工、返修的不合
格品,装配车间返工、返修后的不合格零部件均应及时交予交检验员,检验员对不合格品进行标识、隔离,并当天退质量部不合格品库。
D、产品标识:完工的产品应按要求进行标识
4.2.4结单:
仓库按ERP要求对指令单进行结单。
对本月不能结的单应在25日、30日分别予以上报。
流程
4.3.1 机加车间流程
5相关文件
6支持性表单
《指令单》
《补料单》
《不合格品评审单》
《废品单》。