熔炼车间工艺流程图
铅熔炼工艺流程图 (铅系统)

铅烟尘
木质磺酸钙
净 化
干 燥
转 化
压 滤 浇铸锅 滤 液 滤 饼 滤 饼 直线铸锭机 浆 化 氧化渣 1#电铅 阳极泥浆 始极片制备 水 洗 压 滤 铅阴极始极片 洗 水 阳 极 泥 贵金属车间(待定) 阴阳极板排距 铅阳极始极片 污 水 排到污酸污 水车间处理 铅 卷 送铅熔炼系统 薄片机 供锌系统使用
压 滤
吸 收
尾 气
滤 液 排到污水处理站
成品硫酸
外 售
供分厂使用
SO2Байду номын сангаас体
呼伦贝尔驰宏矿业有限公司工艺流程图
离子液吸附
图 名
解 析
铅冶炼工艺流程图
设 计
纯净空气 外 排 纯净的SO 2气体
中国恩菲工程公司
制 图
梁艳辉(技术部)
日 期
审 核
李衍林(技术部)
2012.7.23
铅精矿 硫酸铅渣 石灰石 铅烟尘 铅硫渣 石英石
配 料 套 喷 枪 氧 筒 风 气 风
SO2烟气
水 圆盘制粒
铅精矿 Ausmelt炉氧化阶段熔炼 粗 铅 配 料 氧化后渣 粗 铅 Ausmelt炉还原1阶段熔炼 粗 铅 还原1段后渣 喷枪风 粗 铅 Ausmelt炉还原2阶段熔炼 套筒风 还原2段后渣 铅 松 香 铅锅(火法精炼) 转炉粗铅 合格铅液 铜浮渣 送铜浮渣处理车间 烟 气 终 渣 硫 磺 粗 铅 锌厂运 的冷渣 沉降后渣 粉 煤 锅 焦 粒 电热前床沉降
SO2烟气
块 煤 粉 煤
套 喷 枪 氧 筒 风 气 风
SO2烟气 SO2 烟气
锅炉余热回收
NaOH
残 极
SO2烟气
铅烟尘
静电收尘 烟化炉还原 空 气
熔铸工艺流程图

铸轧、铸造的相关知识肖立隆(晟通技术总顾问)1熔铸工艺流程图:电解铝液铝锭(含废料、中间合金等)熔化扒渣调温调成分其他固态金属取样分析精炼转炉调温精炼静置在线精炼变质过滤2炉子准备:烘炉烘炉曲线升温过程中不损害炉子寿命3炉料要求和加料顺序:炉料要求: 无吸水,无油污加料顺序:废料中间合金铝锭化平后铜、锌等镁添加剂取样4 熔化:TM TQ= C1dT +L+ C2dT20 1TM 2C1——固体比热:卡/ 克0C ;C 2——液体比热:卡/ 克0C L——熔化潜热:卡/ 克0C黑度:5熔化时的增气反应:铝和水发生反应:2Al+3H 2O=Al2O3+6[H] 火焰炉燃烧时发反应:C m H n+O2 CO+CO 2+H2O6熔体中氢的平衡溶解度:S=K P H 27影响熔体含气量的因素:1)合金元素影响:V MeO / V Me > 1 < 1 = 1α氧化铝膜密度3.47 克/ ㎝3,致密,可防止继续氧化:γ氧化铝膜表面疏松,存在φ 50—100×10-10 m的小孔,在熔炼温度下含有1—2%的水分;在9000C 以上时,γ完全变成α氧化铝,密度增到3.97 克/ ㎝3,体积收缩13%,氧化铝易被搅入铝液中。
2)熔体温度影响:3) 熔体停留时间影响:4) 空气湿度影响:8 熔化时的造渣反应:有关化学元素的氧化物生成自由能几种氧化物和熔融铝可能发生的化学反应式:3SiO2 + 4Al = 2Al 2O3 + 3Si 3FeO + 2Al = Al 2O3 + 3FeCr2O3 + 2Al = Al 2O3 + 2Cr SiO 2 + 2Mg = 2MgO +9 电解铝液的情况:温度高:900——9300C炉内停留时间长:24 小时以上含气量高,氧化夹渣多,结晶核心钝化1 0 调成分调温:1) 加入废料、中间合金、铝锭; 2 )加入铜、锌等其他金属3) 加入镁和其他添加剂;4 ) 快速升温5) 取样分析11精炼:基本原理:1)吸附净化:依靠精炼剂产生的吸附作用达到去氧化夹杂和气体的目的。
熔铸车间工艺流程

熔铸车间工艺流程熔铸车间是金属加工行业中至关重要的环节之一,它涉及到金属材料的熔化、浇铸、冷却等一系列工艺流程。
本文将详细介绍熔铸车间的工艺流程,包括原料准备、熔炼、浇铸、冷却和检验等环节。
一、原料准备熔铸车间的原料主要包括金属合金、矿石、石墨等。
在开始熔铸工艺之前,首先需要对原料进行准备。
原料的准备包括筛选、称重、配比等工作。
合理的原料配比是保证产品质量的关键。
二、熔炼熔炼是熔铸车间的核心工艺环节。
在熔炼过程中,原料被加热至其熔点以上,使其熔化成液态金属。
常用的熔炼设备包括电炉、高频感应炉等。
熔炼温度和时间的控制对于产品质量具有重要影响。
三、浇铸熔炼完成后,液态金属被倒入预先准备好的铸型中进行浇铸。
铸型可以是砂型、金属型等不同类型。
浇铸时要注意控制浇注速度和温度,以避免产生缺陷,确保产品的准确形状和尺寸。
四、冷却浇铸完成后,需要对铸件进行冷却。
冷却的方式可以是自然冷却或者通过水冷等方式进行加速冷却。
冷却的时间和速度对于产品的组织结构和性能有着重要影响,需要根据具体产品要求进行合理控制。
五、清理和检验冷却完成后,铸件需要进行清理和检验。
清理包括去除铸件表面的氧化物、砂粒等杂质。
检验则是通过外观检查、尺寸测量、力学性能测试等手段,对铸件进行质量检测。
只有通过检验合格的产品才能进入下一道工序。
六、包装和出货经过清理和检验的合格产品将进行包装,以保证在运输过程中不受损。
包装可以采用木箱、纸箱等不同形式。
包装完成后,产品将被装车并出货。
七、设备维护和安全措施熔铸车间的设备维护和安全措施是保证工艺流程正常运行和员工安全的重要环节。
定期对熔炼设备进行检修和保养,确保其正常运行。
同时,要加强安全教育和培训,提高员工的安全意识,严格执行操作规程,防止事故的发生。
总结:熔铸车间工艺流程涉及到原料准备、熔炼、浇铸、冷却、检验、包装和出货等一系列环节。
每个环节都需要严格控制和操作,以保证产品的质量和安全。
同时,设备维护和安全措施也是熔铸车间工作的重要方面。
熔铸车间工艺流程
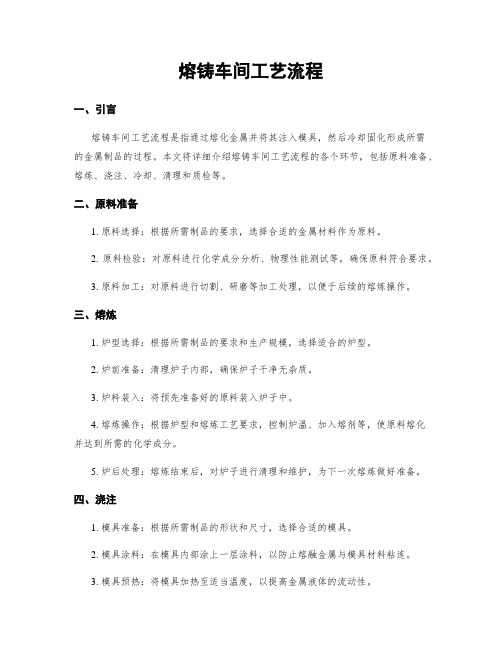
熔铸车间工艺流程一、引言熔铸车间工艺流程是指通过熔化金属并将其注入模具,然后冷却固化形成所需的金属制品的过程。
本文将详细介绍熔铸车间工艺流程的各个环节,包括原料准备、熔炼、浇注、冷却、清理和质检等。
二、原料准备1. 原料选择:根据所需制品的要求,选择合适的金属材料作为原料。
2. 原料检验:对原料进行化学成分分析、物理性能测试等,确保原料符合要求。
3. 原料加工:对原料进行切割、研磨等加工处理,以便于后续的熔炼操作。
三、熔炼1. 炉型选择:根据所需制品的要求和生产规模,选择适合的炉型。
2. 炉前准备:清理炉子内部,确保炉子干净无杂质。
3. 炉料装入:将预先准备好的原料装入炉子中。
4. 熔炼操作:根据炉型和熔炼工艺要求,控制炉温、加入熔剂等,使原料熔化并达到所需的化学成分。
5. 炉后处理:熔炼结束后,对炉子进行清理和维护,为下一次熔炼做好准备。
四、浇注1. 模具准备:根据所需制品的形状和尺寸,选择合适的模具。
2. 模具涂料:在模具内部涂上一层涂料,以防止熔融金属与模具材料粘连。
3. 模具预热:将模具加热至适当温度,以提高金属液体的流动性。
4. 浇注操作:将熔融金属倒入模具中,控制浇注速度和温度,确保金属液体充分填充模具的空腔。
5. 冷却:待金属液体冷却固化后,取出模具,得到所需的金属制品。
五、冷却和清理1. 冷却时间:根据金属制品的厚度和形状,确定适当的冷却时间。
2. 冷却方式:可以采用自然冷却或辅助冷却设备,以加快冷却速度。
3. 清理工艺:将冷却后的金属制品进行切割、研磨、抛光等,以去除可能存在的缺陷和表面不平整。
六、质检1. 外观检查:对金属制品的表面进行目测,检查是否存在瑕疵、裂纹等问题。
2. 尺寸检测:使用测量工具对金属制品的尺寸进行精确测量,确保符合要求。
3. 化学成分分析:取样金属制品,进行化学成分分析,确保符合设计要求。
4. 物理性能测试:对金属制品进行硬度、拉伸强度等物理性能测试,确保符合要求。
熔铸工艺流程图

铸轧、铸造的相关知识——肖立隆(晟通技术总顾问)1 熔铸工艺流程图:电解铝液调温调成分交货2 炉子准备:烘炉烘炉曲线升温过程中不损害炉子寿命3 炉料要求和加料顺序: 炉料要求: 无吸水,无油污加料顺序:废料 中间合金 铝锭 化平后铜、锌等 镁 添加剂 取样4 熔化: Q=dT C TM ⎰201+L+dT C TTM⎰2C 1——固体比热:0.215卡/克0C ; C 2——液体比热:0.198卡/克0C L ——熔化潜热:94.6卡/克0C 黑度:0.25 熔化时的增气反应:铝和水发生反应: 2Al+3H 2O=Al 2O 3+6[H]火焰炉燃烧时发反应: C m H n +O 2 CO+CO 2+H 2O 6 熔体中氢的平衡溶解度:S=K 2H P7 影响熔体含气量的因素:1) 合金元素影响:V MeO / VMe> 1 < 1 = 1α氧化铝膜密度3.47克/㎝3,致密,可防止继续氧化:γ氧化铝膜表面疏松,存在φ50—100×10-10 m的小孔,在熔炼温度下含有1—2%的水分;在9000C以上时,γ完全变成α氧化铝,密度增到3.97克/㎝3,体积收缩13%,氧化铝易被搅入铝液中。
2) 熔体温度影响: 3) 熔体停留时间影响: 4) 空气湿度影响:8 熔化时的造渣反应:有关化学元素的氧化物生成自由能几种氧化物和熔融铝可能发生的化学反应式:3SiO2 + 4Al = 2Al2O3+ 3Si 3FeO + 2Al = Al2O3+ 3FeCr2O3+ 2Al = Al2O3+ 2Cr SiO2+ 2Mg = 2MgO + Si9 电解铝液的情况:温度高:900——9300C炉内停留时间长:24小时以上含气量高,氧化夹渣多,结晶核心钝化10 调成分调温:1)加入废料、中间合金、铝锭; 2)加入铜、锌等其他金属3)加入镁和其他添加剂; 4)快速升温5) 取样分析11 精炼:基本原理:1)吸附净化:依靠精炼剂产生的吸附作用达到去氧化夹杂和气体的目的。
炼铁工艺流程图描述

熔炼工艺流程及简介1 熔炼炉生产概况熔炼炉是制铁工艺流程的主体,它是由耐火砖砌筑的竖立圆筒炉体,外壳钢枝制作,外壳与耐火砖之间有冷却设备,我公司450m3熔炼炉冷却壁共有348块,共分12层冷却壁;一层冷却板;1-3层为光板冷却壁、材质耐热铸铁冷却壁;4-12层为镶砖冷却壁材质是铁素体球墨铸铁冷却壁;6-7层冷却壁之间有一层冷却板,炉喉有18块水冷炉喉钢砖,炉缸有一个铁口、2个渣口、14个风口;从其上部装入矿石,熔剂和燃料向下运动,下部鼓入被加热的空气。
熔炼炉生产的主要产品是生铁,副产品有炉渣和煤气,炉渣可用来制作水泥,保温材料、建筑材料和肥料,煤气可以做为燃料供给各用户。
1.1熔炼炉生产的主要工艺过程:1.1.1供料熔炼炉冶炼用的主要原燃料:块矿、烧结矿、石灰石、焦炭,有K1、J1皮带机把原燃料送到1#转运站,经K2、J2皮带机、分料车运到指定的矿槽。
1.1.2上料由料仓输出的原料,燃料和熔剂,经仓下给料机、振动筛、经筛分、称量后,用料车按一定比例一批一批有序地送到熔炼炉炉顶,并卸入炉顶受料斗。
1.1.3装料炉顶装料设备的任务就是把提升到炉顶的炉料,按一定的工作制度装入熔炼炉炉喉。
1.1.4冶炼熔炼炉冶炼主要是还原过程,把铁氧化物还原成含有碳、硅、锰、硫、磷、镍、铬等杂质的铁合金。
由鼓风机连续不断地把冷风送到热风炉加热到1100~1250℃,再通过炉缸周围的风口进入熔炼炉,由炉顶加入的焦炭和风口鼓入的热空气燃烧燃料,产生大量的煤气和热量,使矿石源源不断地熔化还原,产生的铁水和熔渣贮存在熔炼炉炉缸内,定期地由铁口和渣口排出。
1.1.5产品处理在渣铁处理中,出铁前先从渣口放出溶渣,流入冲渣沟进行粒化后,以脱水器脱水,有皮带运到渣仓。
设有一个应急用干渣坑,出铁时,用液压开口机打开铁口,使铁水流入铁水罐车运到铸铁机铸成铁块,出完铁后用液压泥炮把铁口堵上。
经熔炼炉顶部导出的煤气通过重力除尘器、布袋除尘过滤后,经调压阀组调压后输往各煤气用户使用,从重力除尘器、布袋除尘器排出的炉尘,经过处理回收运往焙烧厂作为烧结原料。
熔铸工艺流程图
铸轧、铸造的相关知识——肖立隆(晟通技术总顾问)1 熔铸工艺流程图:电解铝液调温调成分交货2 炉子准备:烘炉烘炉曲线升温过程中不损害炉子寿命3 炉料要求和加料顺序: 炉料要求: 无吸水,无油污加料顺序:废料 中间合金 铝锭 化平后铜、锌等 镁 添加剂 取样4 熔化: Q=dT C TM ⎰201+L+dT C TTM⎰2C 1——固体比热:0.215卡/克0C ; C 2——液体比热:0.198卡/克0C L ——熔化潜热:94.6卡/克0C 黑度:0.25 熔化时的增气反应:铝和水发生反应: 2Al+3H 2O=Al 2O 3+6[H]火焰炉燃烧时发反应: C m H n +O 2 CO+CO 2+H 2O 6 熔体中氢的平衡溶解度:S=K 2H P7 影响熔体含气量的因素:1) 合金元素影响:V MeO / VMe> 1 < 1 = 1α氧化铝膜密度3.47克/㎝3,致密,可防止继续氧化:γ氧化铝膜表面疏松,存在φ50—100×10-10 m的小孔,在熔炼温度下含有1—2%的水分;在9000C以上时,γ完全变成α氧化铝,密度增到3.97克/㎝3,体积收缩13%,氧化铝易被搅入铝液中。
2) 熔体温度影响: 3) 熔体停留时间影响: 4) 空气湿度影响:8 熔化时的造渣反应:有关化学元素的氧化物生成自由能几种氧化物和熔融铝可能发生的化学反应式:3SiO2 + 4Al = 2Al2O3+ 3Si 3FeO + 2Al = Al2O3+ 3FeCr2O3+ 2Al = Al2O3+ 2Cr SiO2+ 2Mg = 2MgO + Si9 电解铝液的情况:温度高:900——9300C炉内停留时间长:24小时以上含气量高,氧化夹渣多,结晶核心钝化10 调成分调温:1)加入废料、中间合金、铝锭; 2)加入铜、锌等其他金属3)加入镁和其他添加剂; 4)快速升温5) 取样分析11 精炼:基本原理:1)吸附净化:依靠精炼剂产生的吸附作用达到去氧化夹杂和气体的目的。
熔铸车间工艺流程
熔铸车间工艺流程引言概述:熔铸车间是金属加工行业中重要的环节之一。
熔铸工艺流程是将金属材料加热至熔点后,通过浇注到模具中冷却凝固,最终形成所需的金属制品。
本文将详细介绍熔铸车间工艺流程的五个大点,并分别从三至五个小点进行详细阐述。
正文内容:1. 原材料准备1.1 选择合适的金属材料:根据产品要求和性能要求,选择合适的金属材料,如铁、铜、铝等。
1.2 原材料分类和分选:对原材料进行分类和分选,确保质量和成份符合要求。
1.3 温度控制:控制原材料的温度,确保熔化时达到所需的熔点。
2. 熔炼和熔化2.1 熔炼设备准备:准备熔炼设备,如电炉、高频炉等,确保设备正常运行。
2.2 熔炼操作:将原材料放入熔炼设备中,通过加热使其熔化,并控制熔化温度和时间。
2.3 熔炼温度控制:根据金属材料的特性和要求,控制熔炼温度,确保熔化的金属材料符合要求。
3. 浇注和冷却3.1 模具准备:准备模具,包括选择合适的模具材料和制作模具。
3.2 浇注操作:将熔化的金属材料倒入模具中,确保浇注过程中不浮现气泡和杂质。
3.3 冷却和凝固:等待熔化的金属材料在模具中冷却和凝固,形成所需的金属制品。
4. 清理和处理4.1 模具清理:将已凝固的金属制品从模具中取出,并进行模具的清理和维护。
4.2 修整和处理:对冷却凝固后的金属制品进行修整和处理,如切割、打磨等,以满足产品要求。
4.3 检查和质量控制:对金属制品进行检查,确保产品质量符合要求,并进行必要的质量控制措施。
5. 包装和出库5.1 包装准备:准备适当的包装材料和包装工具,确保金属制品在包装过程中不受损。
5.2 包装操作:将金属制品进行包装,并标明相关信息,如产品型号、数量等。
5.3 出库和储存:将包装好的金属制品出库,并储存到指定的地方,以备后续使用或者销售。
总结:综上所述,熔铸车间工艺流程包括原材料准备、熔炼和熔化、浇注和冷却、清理和处理以及包装和出库五个大点。
在每一个大点中,我们详细阐述了三至五个小点,从而全面介绍了熔铸车间工艺流程的具体步骤和操作要点。
熔铸车间工艺流程
熔铸车间工艺流程引言概述:熔铸车间是金属加工工业中至关重要的环节之一。
它涉及到将金属材料加热至液态状态,然后倒入模具中进行冷却和凝固,最终得到所需的金属制品。
本文将详细介绍熔铸车间的工艺流程,以帮助读者更好地了解这一重要的生产环节。
一、原料准备1.1 原材料选择:根据所需制品的要求,选择适当的金属材料。
常用的金属材料包括铁、铜、铝、锡等。
1.2 原料质量检查:对原材料进行质量检查,包括外观检查、化学成分分析、物理性能测试等,确保原材料符合工艺要求。
1.3 原料预处理:根据需要,对原材料进行预处理,如切割、研磨、清洗等,以便于后续的熔炼和铸造过程。
二、熔炼过程2.1 熔炼炉选择:根据熔炼的金属材料和工艺要求,选择合适的熔炼炉,常见的熔炼炉有电弧炉、感应炉等。
2.2 熔炼操作:将原材料放入熔炼炉中,通过加热使其达到液态状态。
在熔炼过程中,需要控制温度、搅拌熔体、除去杂质等。
2.3 熔炼结束处理:熔炼结束后,对熔体进行处理,如除去浮渣、调整化学成分等,以得到符合要求的熔体。
三、铸造过程3.1 模具准备:根据所需制品的形状和尺寸,选择合适的模具,并进行模具准备工作,如涂抹模具释模剂、安装模具芯等。
3.2 熔体倒注:将熔体倒入模具中,注意控制倒注速度、温度等参数,以确保熔体充分填充模具腔体,并避免产生气泡和缺陷。
3.3 冷却凝固:待熔体充分填充模具后,等待熔体冷却凝固,以得到所需的金属制品。
冷却时间和方式会根据金属材料的特性和制品要求进行调整。
四、后处理4.1 模具拆卸:待金属制品冷却凝固后,拆卸模具,取出金属制品。
4.2 清理和修整:对金属制品进行清理和修整工作,如去除余渣、修整表面等,以提高制品的质量和外观。
4.3 检验和质量控制:对金属制品进行检验,包括尺寸、外观、力学性能等方面的检测,确保制品符合要求。
五、产品交付5.1 包装和标识:对金属制品进行包装,并进行标识,以便于运输和使用。
5.2 存储和运输:将金属制品存储在适当的环境中,以防止腐蚀和损坏,并进行安全可靠的运输。
熔铸车间工艺流程
熔铸车间工艺流程1. 背景介绍熔铸是一种重要的金属加工方法,用于制造各种金属零件和产品。
熔铸车间是进行熔铸工艺的关键环节,本文将详细介绍熔铸车间的工艺流程。
2. 原料准备熔铸车间的工艺流程首先涉及原料准备。
根据产品要求,选择合适的金属材料,并进行配比。
原料通常以金属块、粉末或合金形式存在。
在准备过程中,需要确保原料的质量和纯度,以保证最终产品的性能。
3. 熔炼熔炼是熔铸车间的核心环节。
首先,将准备好的金属原料放入熔炉中,然后加热至适当的温度。
通过控制熔炉的温度和加热时间,使金属原料完全熔化,并保持在一定的熔融状态。
在熔炼过程中,需要注意控制熔炉的气氛,以避免金属氧化或其他不良反应的发生。
4. 净化熔炼后的金属液通常包含杂质和气泡。
为了提高产品的质量,需要对金属液进行净化处理。
常用的净化方法包括过滤、除杂剂添加和真空处理等。
过滤可以去除金属液中的固体杂质,除杂剂可以吸附金属液中的杂质,真空处理可以去除金属液中的气泡。
5. 浇注净化后的金属液需要通过浇注工艺注入到模具中。
模具根据产品的形状和尺寸进行设计和制造。
在浇注过程中,需要注意控制金属液的温度和流动速度,以确保金属液能够充分填充模具的空腔,并获得所需的形状和尺寸。
6. 冷却浇注后,金属液会逐渐冷却固化。
冷却速度对于产品的性能和组织结构有重要影响。
通常,可以通过控制冷却介质的温度和流速,以及调整模具的设计和结构,来控制产品的冷却速度。
冷却过程中,还需要注意避免产生应力集中和缺陷。
7. 脱模冷却后,固化的金属产品需要从模具中脱模。
脱模过程需要小心操作,以避免产品损坏或变形。
通常,可以通过机械力、冲击力或化学方法等方式进行脱模。
8. 后处理脱模后,金属产品通常需要进行后处理。
后处理包括修整、清洁、热处理、表面处理等工序,以提高产品的表面质量、机械性能和耐腐蚀性能。
后处理工序根据产品的要求和用途来确定,并严格按照相关标准进行操作。
9. 检验和质量控制在整个熔铸车间的工艺流程中,检验和质量控制是非常重要的环节。