焊接自动化智能化的关键-焊缝的查找、自动跟踪寻位引导-激光焊缝跟踪传感器
焊缝自动跟踪系统中的智能控制

焊缝自动跟踪系统中的智能控制作者:关泰林李学名来源:《电子乐园·上旬刊》2019年第01期摘要:为了保障焊接工作顺利进行,必须实行正確的焊缝自动跟踪技术。
焊缝自动跟踪系统就是基于对焊缝技术的研究,采取前馈随动系统,进行焊接工作。
前馈随动系统可以减少工程工作中的人力物力的浪费,使得焊接工作更加简单方便,同时还可以实现焊缝自动跟踪功能。
智能控制在焊缝自动跟踪系统中有广泛应用,随着传感器越来越具有高精度特性,焊接效果也越来越好。
焊缝自动跟踪系统中的智能控制有模糊控制和神经网络两种,本文介绍了焊缝自动跟踪系统,并对焊缝自动跟踪系统中的模糊控制和神经网络两种应用做简单概述,希望能给相关人士提供借鉴。
关键词:焊缝自动跟踪系统;智能控制;传感器;模糊控制与传统的人工焊接技术相比,如今的焊接技术融入更多智能化技术,凭借焊接机器人设备为工作载体,实现焊缝自动跟踪。
焊缝自动跟踪系统是一种借助传感器的应用系统,系统的智能化水平很大程度上依赖于传感器的效能,这项改进可以使焊接工作不再过分依赖于高技术焊接技术人员,机器就可以生产高质量的焊接产品。
一、焊接跟踪系统分析从宏观上来看,焊接跟踪系统由两个类别,分别为程序控制系统和前馈随动系统[1]。
程序控制系统指的是早期产生的简单的焊接系统,程序控制系统采用实现预定焊接轨迹的方法,该系统大都应用在焊接成果为固定矩形的加工工件上,此类型工件显著特征为不用调节任何形状。
程序控制系统对于人力物力的耗费极大,因为他要求高精度的焊接成果,并且有一些焊接成果形状难以用几何数学的方法求得。
为了解决这个弊端,近代以来,对于焊接工作科研人员提出一种新型的焊接系统为前馈随动系统。
前馈随动系统可以对焊接工件进行实时控制,利用高精度传感器将焊接过程记录下来。
这种实时系统由三个部件构成,分别为控制器、偏差信号传感器和跟踪机构。
系统的控制有三个信号决定:参考输入、被控量和噪声干扰项。
焊缝自动跟踪系统的难点在于如何实现自动踉踪以及保证跟踪的准确度,在工作中变化最大的就是焊接线的变化。
(完整word版)激光焊接机器人焊缝跟踪方法
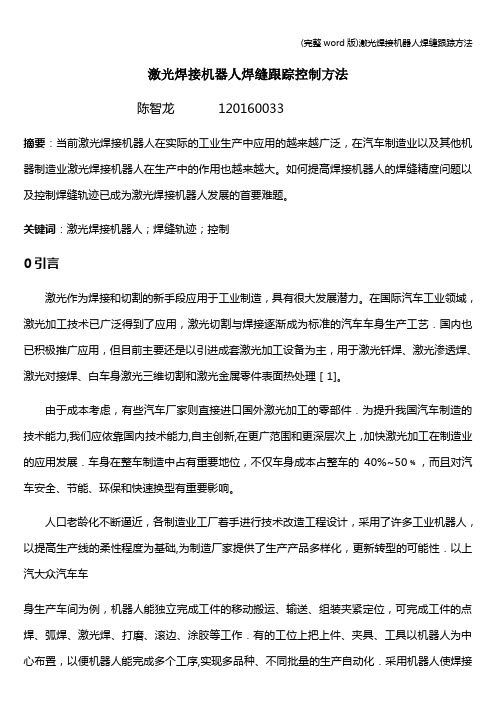
激光焊接机器人焊缝跟踪控制方法陈智龙120160033摘要:当前激光焊接机器人在实际的工业生产中应用的越来越广泛,在汽车制造业以及其他机器制造业激光焊接机器人在生产中的作用也越来越大。
如何提高焊接机器人的焊缝精度问题以及控制焊缝轨迹已成为激光焊接机器人发展的首要难题。
关键词:激光焊接机器人;焊缝轨迹;控制0引言激光作为焊接和切割的新手段应用于工业制造,具有很大发展潜力。
在国际汽车工业领域,激光加工技术已广泛得到了应用,激光切割与焊接逐渐成为标准的汽车车身生产工艺.国内也已积极推广应用,但目前主要还是以引进成套激光加工设备为主,用于激光钎焊、激光渗透焊、激光对接焊、白车身激光三维切割和激光金属零件表面热处理[1]。
由于成本考虑,有些汽车厂家则直接进口国外激光加工的零部件.为提升我国汽车制造的技术能力,我们应依靠国内技术能力,自主创新,在更广范围和更深层次上,加快激光加工在制造业的应用发展.车身在整车制造中占有重要地位,不仅车身成本占整车的40%~50﹪,而且对汽车安全、节能、环保和快速换型有重要影响。
人口老龄化不断逼近,各制造业工厂着手进行技术改造工程设计,采用了许多工业机器人,以提高生产线的柔性程度为基础,为制造厂家提供了生产产品多样化,更新转型的可能性.以上汽大众汽车车身生产车间为例,机器人能独立完成工件的移动搬运、输送、组装夹紧定位,可完成工件的点焊、弧焊、激光焊、打磨、滚边、涂胶等工作.有的工位上把上件、夹具、工具以机器人为中心布置,以便机器人能完成多个工序,实现多品种、不同批量的生产自动化.采用机器人使焊接生产线更具柔性化、自动化,使多种车身成品可在一条车身装焊生产线上制造,实现多车型混线生产.因此,焊接生产线必须很容易地因产品结构、外形的改变而改变,具有较高的柔性程度[2].由于柔性车身焊接生产线可以适应汽车多品种生产及换型的需要,是汽车车身制造自动化的必然趋势,特别是进入上世纪90年代以后,各大汽车厂家都在考虑车身焊接生产线柔性化。
视觉传感技术在焊缝跟踪中的研究及应用
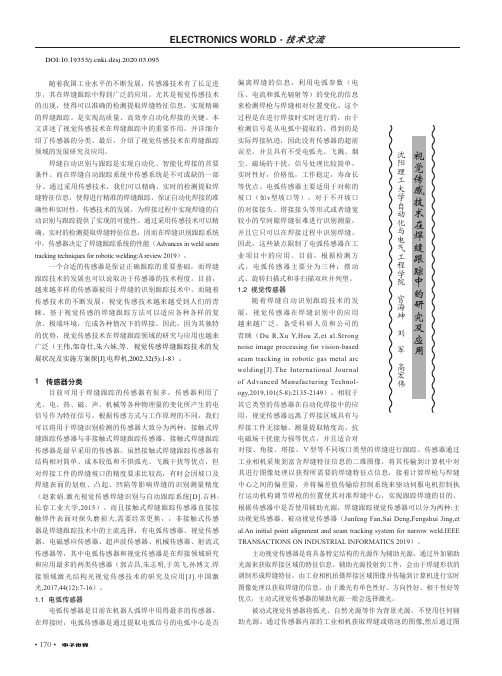
• 170 •
偏离焊缝的信息,利用电弧参数(电
压、电流和弧光辐射等)的变化的信息
来检测焊枪与焊缝相对位置变化。这个
过程是在进行焊接时实时进行的,由于
检测信号是从电弧中提取的,得到的是
实际焊接轨迹,因此没有传感器的超前 误差。并且具有不受电弧光、飞溅、烟 尘、磁场的干扰,信号处理比较简单, 实时性好,价格低,工作稳定,寿命长 等优点。电弧传感器主要适用于对称的 坡口(如v型坡口等),对于不开坡口 的对接接头、塔接接头等形式或者缝宽 较小的窄间隙焊缝很难进行识别测量, 并且它只可以在焊接过程中识别焊缝。 因此,这些缺点限制了电弧传感器在工 业项目中的应用。目前,根据检测方 式,电弧传感器主要分为三种:摆动 式、旋转扫描式和非扫描双丝并列型。 1.2 视觉传感器
ELECTRONICS WORLD・技术交流
DOI:10.19353/ki.dzsj.2020.03.095
随着我国工业水平的不断发展,传感器技术有了长足进 步,其在焊缝跟踪中得到广泛的应用。尤其是视觉传感技术 的出现,使得可以准确的检测提取焊缝特征信息,实现精确 的焊缝跟踪。是实现高质量、高效率自动化焊接的关键。本 文讲述了视觉传感技术在焊缝跟踪中的重要作用,并详细介 绍了传感器的分类。最后,介绍了视觉传感技术在焊缝跟踪 领域的发展研究及应用。
中心之间的偏差量,并将偏差值传输给控制系统来驱动伺服电机控制执
行运动机构调节焊枪的位置使其对准焊缝中心,实现跟踪焊缝的目的。
根据传感器中是否使用辅助光源,焊缝跟踪视觉传感器可以分为两种:主
动视觉传感器、被动视觉传感器(Junfeng Fan,Sai Deng,Fengshui Jing,et
焊缝跟踪和焊缝寻位的原理

焊缝跟踪和焊缝寻位的原理
一、焊缝跟踪原理
焊缝跟踪是焊接过程中的一项重要工作,它能够确保焊接质量和工艺
参数的一致性。
其原理是通过焊缝检测传感器或视觉传感器对焊接过
程中的焊缝进行实时监测,根据预置的规程控制焊接电流和速度实现
焊接质量的稳定性。
焊缝跟踪系统一般由控制器、传感器、信号接口等组成。
其中,传感
器可分为近红外传感器、激光传感器、摄像头传感器等,根据不同的
焊接场景选择相应的传感器。
通过掌握焊接过程中的实时参数,如焊
接速度、电流强度、电压等,可以及时调整焊接参数,确保焊接质量。
二、焊缝寻位原理
焊缝寻位是焊接前的重要工作,它可以在焊接前精确定位焊接部位,
降低焊接质量测评成本,提高焊接效率。
焊缝寻位技术可以通过机械
手臂、计算机视觉、激光测量等方式实现。
消费电子产品采用的主要焊缝寻位技术是机械手臂寻位,通过机械臂
精确控制焊枪位置,实现对焊接部位的寻位。
另外,一些大型生产厂
家也使用了激光测量的方法,在焊接前使用激光传感器对焊接部位进行测量,确定焊接位置。
三、焊缝跟踪与焊缝寻位的关系
焊缝跟踪和焊缝寻位是两个不同的概念,但它们在焊接中有着密切的关系。
首先,焊缝寻位可以为焊缝跟踪提供准确的焊接部位信息,避免焊接过程中出现偏差。
同时,焊缝跟踪技术也可以为焊缝寻位的自动化提供支持,通过对焊接过程中的数据分析,优化焊缝寻位方案,提高寻位精度和效率。
总之,焊缝跟踪和焊缝寻位是两项相互依存的技术,在焊接过程中都发挥着重要作用,提高焊接质量,降低成本。
焊接自动化智能化的关键-焊缝的查找、自动跟踪寻位引导-激光焊缝跟踪传感器

焊接自动化、智能化的关键问题是焊缝的自动查找、自动跟踪寻位-焊缝跟踪传感1.焊接行业发展趋势焊接行业是关乎工业制造生产与维护服务的核心行业之一,是大型安装工程建设期间的一项关键工作,其进度直接影响到计划的工期,其质量的好坏直接影响到工程的安全运行和使用寿命,其效率的高低直接影响工程的建造周期和建造成本。
为了减少人为因素对焊接质量的影响、提高生产效率就需要使焊接过程更加自动化和智能化,这也是焊接行业发展的必然趋势。
焊接自动化、智能化的关键问题是焊缝的自动查找、自动跟踪,苏州博智慧达自主研发的3D激光焊缝跟踪系统可以轻松获取焊缝位置、焊缝偏转角度、焊缝宽度、高度、深度等信息,并支持市面上大部分机器人品牌的数据通讯,如FANUC、ABB、KUKA、安川、川崎等。
将数据实时反馈至上位机,已达到最佳工艺控制要求。
焊缝自动跟踪系统的作用是精确检测出焊缝的位置和形状信息并传递给焊枪(机器人)控制系统,控制系统根据检测结果调整焊枪位置,从而实现焊缝自动跟踪。
2.工作原理激光焊缝跟踪传感器采用激光三角反射式原理,即激光束被放大形成一条激光线投射到被测物体表面上,反射光透过高质量光学系统,被投射到成像矩阵上,经过计算得到传感器到被测表面的距离(Z轴)和沿着激光线的位置信息(X轴)。
移动被测物体或轮廓仪探头,就可以得到一组三维测量值。
所获得的信息可用于焊缝搜索定位、焊缝跟踪、自适应焊接参数控制、焊缝成形检测并将信息实时传递到机械手单元,完成各种复杂焊接,避免焊接质量偏差,实现无人化焊接。
传感器通过复杂的程序算法完成对常见焊缝的在线实时检测。
对于检测范围、检测能力以及针对焊接过程中的常见问题都有相应的功能设置。
设备通过计算检测到的焊缝与焊枪之间的偏差,输出偏差数据,由运动执行机构实时纠正偏差,精确引导焊枪自动焊接,从而实现对焊接过程中焊缝的智能实时跟踪。
支持多种焊接类型3.激光焊缝跟踪系统的优点1.整套软件系统采用自主技术,无版权风险,具有开源的软件架构,用户可自行添加通讯协议与各种机器人进行配合。
焊缝跟踪技术的应用探析

焊缝跟踪技术的应用探析摘要:在焊接生产过程中,不同的产品通常需要特定的焊接设备及工装夹具,需要设计不同类型的生产线及生产流程,即便是同类产品,由于型号不同,通常也需要更换工装夹具。
同时由于工件在组对过程中存在组对误差,加工过程存在加工误差,因此会导致实际焊接的工件与设计图样存在差异,工件一致性较差,对于机器人焊接来说简单的示教通常存在较大的误差。
在焊接过程中的热形变也会引起误差,造成焊接缺陷。
以上问题在一般工业生产中普遍存在,这就需要焊接自动化生产线具有精确定位工件和纠正偏差的能力,同时在焊接过程中能够对焊缝实时检测,调整焊接的路径,纠正焊接的偏差,保证焊接的质量,这样也可以大幅降低操作人员的工作量,提高焊接效率,降低制造成本,实现智能的柔性制造。
关键词:焊缝跟踪技术;应用;分析下文综合了近年来焊缝跟踪领域相关文献及新技术、新应用,分析了各种焊缝跟踪方式的特点,指出基于激光结构光的焊缝定位及跟踪方式将有更大的优势及更宽广的发展空间。
分析展望了未来基于激光结构光的焊缝跟踪新技术与新应用。
1 焊缝跟踪技术的应用现状在实际焊接行业中,由于机械式接触传感技术存在精度差、易磨损的问题,应用已经较为少见。
目前,在实际生产中应用最为广泛的是非接触式的电弧跟踪及基于视觉传感器的跟踪方法。
1.1电弧跟踪电弧跟踪的基本原理是检测焊接电流和电弧电压的变化,来表达电弧长度的变化,从而推算焊枪与焊缝的相对高度及与焊接坡口的相对位置关系,通过焊接执行机构的实时调节,实现焊接过程中的实时电弧跟踪。
但是在实际中电弧长度与焊接电流、电弧电压之间的精准数学模型难以确定,特别是在熔化极电弧焊接过程中,焊接坡口的准确尺寸也难以在线实时检测,以及电弧跟踪需要角接焊缝、摆动焊接等限制条件,因此电弧实时跟踪的应用具有较大的局限性。
1.2基于三角测距原理的激光结构光检测该方法具有对比度高、精度高、实时性强、无接触等特点,得到了广泛应用。
在实际使用中,激光结构光有多种类型,如单线结构光、多线结构光、圆形及椭圆结构光、点阵等。
激光焊接机器人焊缝跟踪方法

激光焊接机器人焊缝跟踪方法激光焊接机器人焊缝跟踪控制方法陈智龙 120160033摘要:当前激光焊接机器人在实际的工业生产中应用的越来越广泛,在汽车制造业以及其他机器制造业激光焊接机器人在生产中的作用也越来越大。
如何提高焊接机器人的焊缝精度问题以及控制焊缝轨迹已成为激光焊接机器人发展的首要难题。
关键词:激光焊接机器人;焊缝轨迹;控制0引言激光作为焊接和切割的新手段应用于工业制造,具有很大发展潜力。
在国际汽车工业领域,激光加工技术已广泛得到了应用,激光切割与焊接逐渐成为标准的汽车车身生产工艺.国内也已积极推广应用,但目前主要还是以引进成套激光加工设备为主,用于激光钎焊、激光渗透焊、激光对接焊、白车身激光三维切割和激光金属零件表面热处理[1].由于成本考虑,有些汽车厂家则直接进口国外激光加工的零部件.为提升我国汽车制造的技术能力,我们应依靠国内技术能力,自主创新,在更广范围和更深层次上,加快激光加工在制造业的应用发展.车身在整车制造中占有重要地位,不仅车身成本占整车的40%~50﹪,而且对汽车安全、节能、环保和快速换型有重要影响。
人口老龄化不断逼近,各制造业工厂着手进行技术改造工程设计,采用了许多工业机器人,以提高生产线的柔性程度为基础,为制造厂家提供了生产产品多样化,更新转型的可能性.以上汽大众汽车车身生产车间为例,机器人能独立完成工件的移动搬运、输送、组装夹紧定位,可完成工件的点焊、弧焊、激光焊、打磨、滚边、涂胶等工作.有的工位上把上件、夹具、工具以机器人为中心布置,以便机器人能完成多个工序,实现多品种、不同批量的生产自动化.采用机器人使焊接生产线更具柔性化、自动化,使多种车身成品可在一条车身装焊生产线上制造,实现多车型混线生产.因此,焊接生产线必须很容易地因产品结构、外形的改变而改变,具有较高的柔性程度[2]。
由于柔性车身焊接生产线可以适应汽车多品种生产及换型的需要,是汽车车身制造自动化的必然趋势,特别是进入上世纪90年代以后,各大汽车厂家都在考虑车身焊接生产线柔性化。
自动焊焊缝追踪精度提升方法论述

自动焊焊缝追踪精度提升方法论述摘要:焊接自动化具有提高生产效率,优化产品质量,改善劳动条件等优点而被企业广泛应用。
其核心技术就是通过激光焊缝追踪装置对焊接坡口进行追踪,建立闭环反馈系统。
在激光追踪装置识别坡口路径时,由于外界环境干扰导致焊接轨迹出现跑偏情况产生。
本文针对车间现场实际生产的情况,通过创新方法理论手段对该问题进行原因分析、求解并提出可行性意见,从合理化、经济化、适用性的角度来解决该问题的产生。
关键词:焊接自动化激光追踪装置焊接轨迹随着智能制造浪潮的兴起,老牌制造企业也逐渐开始从原始机械到智能机械进行过渡。
焊接自动化是焊接生产的“智能”体现,也是保证焊接质量、提高作业效率的重要手段。
焊接自动化主要装置就是利用焊缝追踪系统对焊缝路径进行实施规划,从而完成焊接工作,该系统一般有传感器、控制器和执行机构三大部分组成。
根据传感器进行分类可以分为接触式传感器焊缝追踪装置和非接触式传感器焊缝追踪装置。
接触式传感器结构简单,成本低,但其灵敏度不高,扫描范围小,与工件接触的接头容易受到磨损。
非接触式传感器焊缝追踪装置可分为电磁感应式传感器焊缝追踪装置、视觉传感器焊缝追踪装置、电弧传感器焊缝追踪装置等,它们具有自动化匹配程度高、灵敏度好等特点。
一个优秀的焊缝追踪装置,它应该具有以下特点:传感器灵敏,系统具有实时性;控制器功能强,成本低,能进行多自由度运动控制;执行机构结构简单,轻便运动灵活。
一、激光焊缝跟踪原理激光焊缝跟踪研究开始于20世界80年代初。
1985年保加利亚的kov提出了用模糊模型来描述弧焊过程的不确定性,同时利用激光传感器用模糊控制推理对示教机器人的运动进行预测和控制,进而实现焊缝追踪。
1989年日本的S.Mursaami利用电弧传感弧焊机器人焊缝跟踪的模糊控制,该控制系统根据焊枪的振幅位置同焊丝与工件的距离关系判断焊点的水平和垂直位移,并在强烈的弧光、高温、烟尘的条件下,利用模糊滤波器和模糊控制器来设计焊缝跟踪控制系统,取得了较好效果。
- 1、下载文档前请自行甄别文档内容的完整性,平台不提供额外的编辑、内容补充、找答案等附加服务。
- 2、"仅部分预览"的文档,不可在线预览部分如存在完整性等问题,可反馈申请退款(可完整预览的文档不适用该条件!)。
- 3、如文档侵犯您的权益,请联系客服反馈,我们会尽快为您处理(人工客服工作时间:9:00-18:30)。
焊接自动化、智能化的关键问题是焊缝的自动查找、自动跟踪寻位-焊缝跟踪传感
1.焊接行业发展趋势
焊接行业是关乎工业制造生产与维护服务的核心行业之一,是大型安装工程建设期间的一项关键工作,其进度直接影响到计划的工期,其质量的好坏直接影响到工程的安全运行和使用寿命,其效率的高低直接影响工程的建造周期和建造成本。
为了减少人为因素对焊接质量的影响、提高生产效率就需要使焊接过程更加自动化和智能化,这也是焊接行业发展的必然趋势。
焊接自动化、智能化的关键问题是焊缝的自动查找、自动跟踪,苏州博智慧达自主研发的3D激光焊缝跟踪系统可以轻松获取焊缝位置、焊缝偏转角度、焊缝宽度、高度、深度等信息,并支持市面上大部分机器人品牌的数据通讯,如FANUC、ABB、KUKA、安川、川崎等。
将数据实时反馈至上位机,已达到最佳工艺控制要求。
焊缝自动跟踪系统的作用是精确检测出焊缝的位置和形状信息并传递给焊枪(机器人)控制系统,控制系统根据检测结果调整焊枪位置,从而实现焊缝自动跟踪。
2.工作原理
激光焊缝跟踪传感器采用激光三角反射式原理,即激光束被放大形成一条激光线投射到被测物体表面上,反射光透过高质量光学系统,被投射到成像矩阵上,经过计算得到传感器到被测表面的距离(Z轴)和沿着激光线的位置信息(X轴)。
移动被测物体或轮廓仪探头,就可以得到一组三维测量值。
所获得的信息可用于焊缝搜索定位、焊缝跟踪、自适应焊接参数控制、焊缝成形检测并将信息实时传递到机械手单元,完成各种复杂焊接,避免焊接质量偏差,实现无人化焊接。
传感器通过复杂的程序算法完成对常见焊缝的在线实时检测。
对于检测范围、检测能力以及针对焊接过程中的常见问题都有相应的功能设置。
设备通过计算检测
到的焊缝与焊枪之间的偏差,输出偏差数据,由运动执行机构实时纠正偏差,精确引导焊枪自动焊接,从而实现对焊接过程中焊缝的智能实时跟踪。
支持多种焊接类型
3.激光焊缝跟踪系统的优点
1.整套软件系统采用自主技术,无版权风险,具有开源的软件架构,用户可自行添加通讯协议与各种机器人进行配合。
2.焊缝目标识别加入了机器学习算法,提高了识别率和识别精度
3.自主设计的机器人和传感器标定算法,精度较高,标定流程简单易用
4.优化了抗电磁干扰系统,使系统稳定性得到了提升,抗弧光和飞溅,实时跟踪,焊缝宽度自动适应
5.系统整体精度在±0.5mm以内,可提高现有焊接作业场所的焊接器人工作效率50%以上,节省人工30%以上。
6 .非接触,支持多种焊接类型
7 .提高生产效率和焊接质量,提高生产率
8 .确保焊缝成型美观牢固;可使焊枪处于理想位置;可实现一致的和可复现的焊接效果;
9 .IP67防护等级,全系标配防护三件套。