酸洗磷化工艺流程及配槽维护
酸洗磷化操作规程

酸洗磷化操作规程
酸洗、磷化、皂化操作规程
工艺:开包整理——酸洗——高压水冲洗——磷化——水清洗——皂化——干燥——吊运堆放
1 .酸洗前的准备:根据生产单,检验原料的批号或炉号、规格和表面质量等,如有异常情况,即通知生产部负责人。
2 .剪断打包带,Ф 10 及以下的 2 吨以上线材必须一开为二,绑上绑腰线。
3 .酸洗:室温下,盐酸池中浸泡约 15 分钟左右,一般先浸低浓度酸,后浸
高浓度酸,粗细钢丝要分别对待,做到无氧化铁皮。
4 .高压水冲洗:尽量冲洗干净钢丝上的附着物,再浸入清水池。
5 .磷化:磷化温度: 7 5 ~ 80 ℃。
磷化时间: 5 ~1 0 分钟(不同材料时间
不同)。
磷化后钢丝表面的颜色为灰色或暗灰色,磷化膜应是牢固、细密。
6 .水清洗:高压水冲洗(特别是下面磷化渣一定要冲掉)再进入清水池,水池的水要保持中偏碱性。
7 .皂化:皂化温度 7 0 ~8 0 ℃,皂化时间:2 ~5 分钟。
皂化后钢丝的表面
为一层乳白色的膜层。
8 .皂化后钢丝要放在吹风机前吹干(特别是Ф 10 及以下的线材),然后分牌号和规格定点堆放或吊运到指定地点。
9 .随时注意调整三池液面的高低,浓度变低时要加料或更换盐酸。
10 .定期打捞磷化池中的沉淀,一般在早晨上班即进行打捞。
磷化处理工艺程序及操作方法
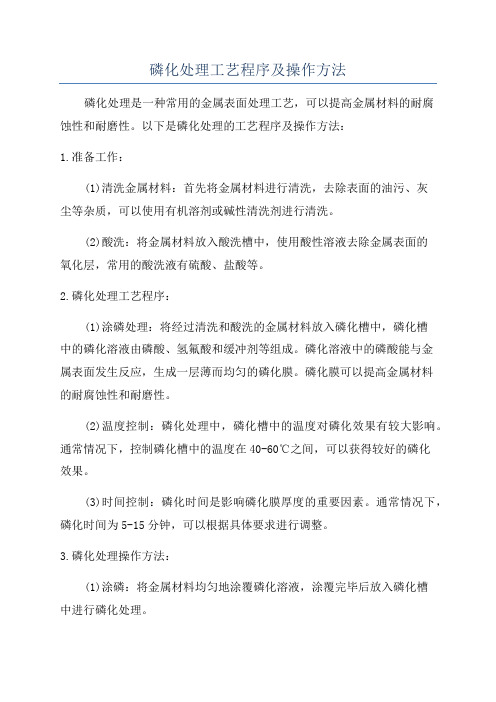
磷化处理工艺程序及操作方法磷化处理是一种常用的金属表面处理工艺,可以提高金属材料的耐腐蚀性和耐磨性。
以下是磷化处理的工艺程序及操作方法:1.准备工作:(1)清洗金属材料:首先将金属材料进行清洗,去除表面的油污、灰尘等杂质,可以使用有机溶剂或碱性清洗剂进行清洗。
(2)酸洗:将金属材料放入酸洗槽中,使用酸性溶液去除金属表面的氧化层,常用的酸洗液有硫酸、盐酸等。
2.磷化处理工艺程序:(1)涂磷处理:将经过清洗和酸洗的金属材料放入磷化槽中,磷化槽中的磷化溶液由磷酸、氢氟酸和缓冲剂等组成。
磷化溶液中的磷酸能与金属表面发生反应,生成一层薄而均匀的磷化膜。
磷化膜可以提高金属材料的耐腐蚀性和耐磨性。
(2)温度控制:磷化处理中,磷化槽中的温度对磷化效果有较大影响。
通常情况下,控制磷化槽中的温度在40-60℃之间,可以获得较好的磷化效果。
(3)时间控制:磷化时间是影响磷化膜厚度的重要因素。
通常情况下,磷化时间为5-15分钟,可以根据具体要求进行调整。
3.磷化处理操作方法:(1)涂磷:将金属材料均匀地涂覆磷化溶液,涂覆完毕后放入磷化槽中进行磷化处理。
(2)温度控制:调节磷化槽中的加热设备控制温度在40-60℃之间。
(3)时间控制:根据具体要求,控制磷化时间在5-15分钟之间。
(4)清洗:磷化处理完毕后,将金属材料从磷化槽中取出,使用清水进行冲洗,去除残留的磷化溶液和杂质。
(5)干燥:将清洗干净的金属材料放置在通风干燥的地方,等待其自然晾干。
4.注意事项:(1)操作安全:在进行磷化处理时,应佩戴个人防护装备,如手套、护目镜等,以保护自己的安全。
(2)剂量控制:在磷化溶液的配置中,应根据具体要求精确计量,以确保磷化效果的一致性。
(3)注意通风:磷化处理过程中会产生一定数量的有害气体,应选择通风条件良好的场所进行操作,以确保作业人员的健康安全。
(4)储存注意:磷化溶液应储存在阴凉、干燥的地方,并防止日晒和雨淋,避免阳光直射引起溶液质量变化。
酸洗磷化工艺流程及配槽维护

中各表调
工业碱与水的比例按1%比例加入槽中搅均,钛盐表调剂按千分之四比例先用水化开倒入槽中搅拌均匀,工件放入槽中时间在3—5分钟,槽液PH值在12—14,太低可适当加碱,太脏要及时更换。
6
磷化
B剂按6%比例加入槽中搅均,工业碱按千分之一点六比例先用水化开再加入池中,C剂按千分之二比例加入槽中,工件放入时间在30-40分钟。夏天可缩短至20—25分钟,槽液使用一段时间会产生一些灰渣,可倒槽清理去除,补加水、磷化液PH值在3,每天应根据工作量补充磷化液及促进剂C剂.
7
水洗
清洁水,水面流通,PH值在6-8,太低或太脏应及时更换。
8
表调
回上上表调槽中,时间与维护与上一艺同步。
9
干燥
风干或烤干,热水烫干。
三、时间控制:
脱脂:25-30分钟,油污太重可延长;水洗:3-4分钟;酸洗:15—25分钟,可适当处长但不能太长。
中和表调:3—5分钟;磷化:20-25分钟(夏季),冬季可处长时间(30—40分钟)。
酸洗磷化工艺流程及配槽维护
一、工艺流程:
脱脂①→水洗③→酸洗④→水洗③→中和表调②→磷化⑥
①→③→④→③→②→⑥→⑤→②→干燥
二、配槽及维护:
1
脱脂槽
脱脂剂按6%比例,先算出水的总量,再用水把脱脂剂化开加入池中,每一百公斤水兑6公斤脱脂剂,温度应控制在40℃左右,有特殊情况可以适当提高温度。工件放入时间在25—30分钟,油污太重可延长时间,槽液每使用半月到一个月视工作量添加脱脂剂,添加量为1%—2%,当槽面浮油太多,可以用勺子捞去,使用三个月以后应倒槽清理油污与灰渣,补加水、脱脂剂。
2
水洗
清洁水,水面流通无污物,PH,也可以加一部分水,防止酸雾过大,工件放进去时间可以把锈除尽为准则,当去锈时间太长时,应换新酸或补加新酸(应注意购买盐酸的质量)。
酸洗磷化工艺流程

酸洗磷化工艺流程酸洗磷化是一种常用的表面处理工艺,主要用于金属制品的防腐蚀和增加表面硬度。
这种工艺可以有效地改善金属制品的表面性能,延长其使用寿命,提高其耐腐蚀性能。
下面我们将详细介绍酸洗磷化的工艺流程。
1. 原料准备。
首先,我们需要准备酸洗磷化所需的原料和设备。
原料主要包括酸洗溶液、磷化溶液、除油剂、表面活性剂等。
设备主要包括酸洗槽、磷化槽、清洗槽、干燥设备等。
2. 表面处理。
首先将金属制品进行表面处理,包括去除油污、锈蚀物和其他杂质。
这一步骤非常重要,因为只有清洁的金属表面才能保证酸洗磷化的效果。
3. 酸洗。
将经过表面处理的金属制品放入酸洗槽中,使用酸性溶液进行酸洗。
酸洗的目的是去除金属表面的氧化物和其他杂质,使金属表面变得光滑、干净。
4. 清洗。
酸洗后的金属制品需要进行清洗,以去除残留的酸性溶液和其他杂质。
清洗可以使用水或者碱性溶液进行。
5. 磷化。
清洗后的金属制品放入磷化槽中,使用磷化溶液进行磷化处理。
磷化的目的是在金属表面形成一层磷化物,增加金属表面的硬度和耐腐蚀性能。
6. 清洗。
磷化后的金属制品需要进行再次清洗,以去除残留的磷化溶液和其他杂质。
清洗后的金属制品需要进行干燥处理。
7. 干燥。
经过清洗的金属制品需要进行干燥处理,以去除表面的水分。
干燥可以使用空气干燥或者加热干燥的方法。
8. 检验。
最后,经过酸洗磷化处理的金属制品需要进行质量检验,包括表面质量、硬度、耐腐蚀性能等方面的检测。
只有通过检验的金属制品才能出厂。
总结。
酸洗磷化工艺流程是一种常用的金属表面处理工艺,可以有效地改善金属制品的表面性能,延长其使用寿命,提高其耐腐蚀性能。
通过严格的工艺流程和质量控制,可以生产出高质量的酸洗磷化金属制品,满足不同领域的需求。
希望通过本文的介绍,能够让读者对酸洗磷化工艺有更深入的了解。
磷化处理(常温)工艺操作规程

宜昌昌耀变压器有限公司磷化处理工艺规范文件前处理的工件既有氧化皮和锈蚀较严重的热轧件,又有油膜保护的冷轧薄板件,根据车间的场地、配套设备等具体条件,拟采用如下的前处理工艺。
工艺流程:除油除锈——流动水洗——冲洗——表面调整——磷化——冲洗——表调水洗——干燥。
工件装篮时,尽量使工件不重叠;装挂形状复杂的工件时尽量保证工件在酸洗时不要形成气囊,酸液易排空。
工艺规范:一、除油除锈槽液组成(以1m3为例):工业盐酸:450公斤Phodull8812除油除锈添加剂:50公斤水:余量控制参数:游离酸度:450点~650点处理温度:室温处理时间:30分钟左右(油、锈除尽为原则)槽液配制:先在槽内盛1/3体积水,先加入计算量的Phodull-8808除锈添加剂,再慢慢加入计算量的工业盐酸,最后加水至工作液面,检测游离酸度即可投入使用。
槽液管理:定期测量游离酸度,当除锈能力下降时必须补加盐酸,在每立方槽液中补加1kg盐酸游离酸度上升1.0点,同时少量补加Phodull8808除锈添加剂(按每处理1000m2工件补加6kg)。
当每m3槽液处理量达2~3万m2后,或槽液中铁含量(Fe2+、Fe3+)超过60克/升时,除锈速度很慢,应更换槽液。
操作要点:1、除油除锈时应经常上下吊动,使工件除油除锈均匀;2、处理完后,应将工件让酸液基本沥干后,然后进入水洗槽;3、经常打捞液面油污、槽底沉淀物。
质量标准:目测:经酸洗后的工件表面不得有锈蚀物、氧化皮、油污等杂质。
二、流动水洗采用流动水清洗,水洗时间约30秒。
保证工件得到充分清洗。
操作要点:水洗时,应上下吊动工件,使工件水洗彻底。
建议该槽每周换水一次。
三、冲洗冲洗时间:约1分钟。
操作要点:迅速将工件彻底冲洗并尽快进入表调槽,以免工件再次生锈。
质量标准:1、除水洗后工件下端滴水部位以外的任何部位用广泛试纸测定,只允许呈微酸性,PH值为4~6。
2、水冲洗后的工种,应有一层连续均匀的水膜,20秒钟水膜不破裂。
磷化处理工艺程序及操作方法
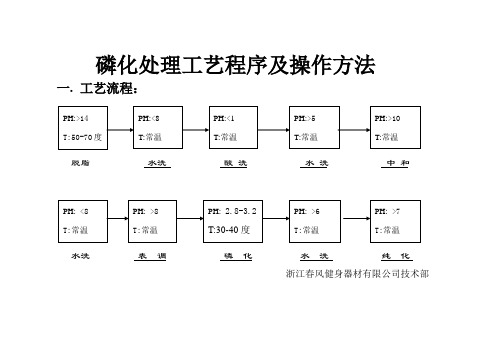
作用:除去工件表面锈蚀及氧化皮.
工作状态控制:用盐酸或硫酸,PH值<1,常温,时间在5-10分钟;
添加量:视效果酌量添加;
检测方法:目测.工件经酸洗后应无锈,无氧化皮,否则应添加;
其他要求:应经常漂浮污物,并定期翻槽去污.
4.水洗:
作用:除去工作表面的酸液.
工作状态控制:槽液PH值>5,常温,使用开循环流水;
工作状态控制:槽液PH值=7-8,温度>60度,时间1分钟;
检测方法:用PH值测试纸检测,超出状态区域,应换槽或添加;
其他要求:在温度未达到状态下操作,出水后应用排风扇等对工件迅速吹干.
烘干:产品通过以上几道工序处理完毕,须进入烘箱进行烘干处理,温度调整为130度.
喷塑流水线:烘箱温度控制在190-210度之间,运行转速视工件面积而定,一般调节为900-1200转.
添加量:除油效果下降时,每次按10kg/T添加;
检测方法:目测.工作经脱水洗后,表面水膜均匀,则油污已洗尽,否则应添加脱脂剂;
其他要求:应经常捞去漂浮污物,并定期换槽.
2.水洗:
作用:漂洗要件表面脱脂液.
工作状态控制:槽液PH值<8,常温,使用开循环流水;
检测方法:用PH值测试纸检测,PH值>8时应清理或换水.
常见的现象处理措施:
<工件不上膜>
A.槽液酸度偏低,应添加磷化剂;B.促进剂浓度偏低,应添加促进剂;C.槽液酸度偏高,应加碱中和.
<上膜不均匀>
A..槽液酸度偏低,应添加磷化剂;B.油未除尽,应调脱脂槽.
<工件出槽返黄>
A..槽液酸度偏高,应加碱中和.B.磷化水洗槽,酸度偏高,应换水洗槽;C.表调浓度偏低,应添加或换槽液.
酸洗磷化作业指导书

酸洗磷化作业指导书
一.酸洗工序:使用二合一酸洗液原液或者加水不超过25%,清洗时
间以除净油污为止,不是以除净锈为准,轻锈一般为3-5分钟,重锈时间稍微长一点,油脂的时间更长,操作工应经常上下吊动筐子,使工件的每个地方与药液充分接触并起反应,这样才能清洗干净。
要求:工件表面有金属光泽,无油花。
二.水洗工序:采用两步水洗,目的是为了保护磷化液。
如果将酸洗
液带入磷化液中,磷化液将会停止反应。
并且水池的水应该经常更换,以测试PH值为准,当PH值小于5时,就应该立即更换水。
三.磷化工序:此工序一般需要10分钟左右,操作工应经常上下吊动
筐子,使工件的每个地方与药液充分接触,在摆放晾干工件时,如果发现有磷化不到位的地方,应采用抹布蘸磷化液擦拭一遍,保证其磷化效果,这个步骤十分重要,必须引起高度重视。
四.干燥工序:工件捞出后,平铺开,不得有工件积压等现象,然后
用抹布擦拭干净或者用风扇吹干,工件表面不得有水流痕迹,若发现有磷化不好的地方,用抹布蘸磷化液擦拭。
五.喷涂时,若发现工件中的某些角落存有渣滓,必须用砂布打磨出
金属光泽方能喷涂。
若工件表面有浮锈,也必须用砂布打磨然后喷涂。
六.擦干后的工件,必须马上喷涂,春秋时间不得超过24小时,夏冬
不得超过12小时,否则必须重新磷化。
编制审核批准。
酸洗磷化工艺

酸洗磷化工艺公司标准化编码 [QQX96QT-XQQB89Q8-NQQJ6Q8-MQM9N]酸洗磷化工艺一、目的:除去线材表面的氧化膜,并且在金属表面形成一层磷酸盐薄膜,以减少线材抽线以及冷墩或成形等加工过程中,对工模具的擦伤。
二、作业流程:(一)、酸洗:将整个盘元分别浸入常温、浓度为20-25%的三个盐酸槽数分钟,其目的是除去线材表面的氧化膜。
(二)、清水:清除线材表面的盐酸腐蚀产物。
(三)、皮膜处理:将盘元浸入磷酸盐,钢铁表面与化成处理液接触,钢铁溶解生成不溶性的化合物(如Zn2Fe(Po4)24H2o),附着在钢铁表面形成皮膜。
(四)、清水:清除皮膜表面残余物。
(五)、润滑剂:由于磷酸盐皮膜的摩擦系数并不是很低,不能赋予加工时充分的润滑性,但与金属皂(如钠皂)反应形成坚硬的金属皂层,可以增加其润滑性能。
酸洗1) 盐酸溶液浓度一般控制在5%~25%。
每天开始工作前要检查酸洗液浓度,并检查每槽酸液位,当酸槽液位不够时,需根据酸槽浓度添加酸或加水,补充到所需液位;当亚铁粒子浓度较高时,一般不再加入新酸。
当酸液浓度小于5%,氯化亚铁含量大于150克/升时,需更换新酸。
2) 两个盐酸槽中配置不同浓度的盐酸,分别为5%<低浓度≤10%,10%<中等浓度≤20%,线材经过酸池顺序为低浓度到中等浓度,对退火后中碳合金钢只在低浓度酸液中酸洗。
酸洗时间与温度、酸液浓度、氧化皮厚度形态及盘料的粗细等有关,3) 为了盘料在酸池中浸泡时间的同步,退火线和非退火线、氧化皮厚与氧化皮薄的盘料不准安排在同一吊钩上生产;4) 待酸洗的材料上不能沾上油污,尤其要防止行车滴油污染材料。
5) 酸洗时要松捆酸洗,不要扎腰。
操作中要认真检查、勤翻料。
6) 对于退火异常线材表面氧化皮难以除去或表面污垢难以去除的线材应在弱酸中浸泡10~20分钟后进行水洗,水洗过后放在酸洗区域外生锈1~2天后,再次酸洗;7) 酸洗作业中,若遇行车损坏或停电等其他特殊状况而不能继续操作时,要注意浸泡在酸中线材的品质,并向主管反映处理。
- 1、下载文档前请自行甄别文档内容的完整性,平台不提供额外的编辑、内容补充、找答案等附加服务。
- 2、"仅部分预览"的文档,不可在线预览部分如存在完整性等问题,可反馈申请退款(可完整预览的文档不适用该条件!)。
- 3、如文档侵犯您的权益,请联系客服反馈,我们会尽快为您处理(人工客服工作时间:9:00-18:30)。
水洗
清洁水,水面流通无污物,PH值6-8,太脏应及时更换。
3
酸洗
工业盐酸,可使用纯酸,也可以加一部分水,防止酸雾过大,工件放进去时间可以把锈除尽为准则,当去锈时间太长时,应换新酸或补加新酸(应注意购买盐酸的质量)。
4
水洗
清洁水,水面应流通,可适当加入一些工业碱,PH值在6以上,无污物,太脏应及时更换。
7
水洗
清洁水ቤተ መጻሕፍቲ ባይዱ水面流通,PH值在6-8,太低或太脏应及时更换。
8
表调
回上上表调槽中,时间与维护与上一艺同步。
9
干燥
风干或烤干,热水烫干。
三、时间控制:
脱脂:25-30分钟,油污太重可延长; 水洗:3-4分钟; 酸洗:15-25分钟,可适当处长但不能太长。
中和表调:3-5分钟; 磷化:20-25分钟(夏季),冬季可处长时间(30-40分钟)。
一、工艺流程:
脱脂①→水洗③→酸洗④→水洗③→中和表调②→磷化⑥
①→③→④→③→②→⑥→⑤→②→干燥
二、配槽及维护:
1
脱脂槽
脱脂剂按6%比例,先算出水的总量,再用水把脱脂剂化开加入池中,每一百公斤水兑6公斤脱脂剂,温度应控制在40℃左右,有特殊情况可以适当提高温度。工件放入时间在25-30分钟,油污太重可延长时间,槽液每使用半月到一个月视工作量添加脱脂剂,添加量为1%-2%,当槽面浮油太多,可以用勺子捞去,使用三个月以后应倒槽清理油污与灰渣,补加水、脱脂剂。
5
中各表调
工业碱与水的比例按1%比例加入槽中搅均,钛盐表调剂按千分之四比例先用水化开倒入槽中搅拌均匀,工件放入槽中时间在3-5分钟,槽液PH值在12-14,太低可适当加碱,太脏要及时更换。
6
磷化
B剂按6%比例加入槽中搅均,工业碱按千分之一点六比例先用水化开再加入池中,C剂按千分之二比例加入槽中,工件放入时间在30-40分钟。夏天可缩短至20-25分钟,槽液使用一段时间会产生一些灰渣,可倒槽清理去除,补加水、磷化液PH值在3,每天应根据工作量补充磷化液及促进剂C剂。