冷冲模设计
冷冲模设计设计(一)_百度文库汇总
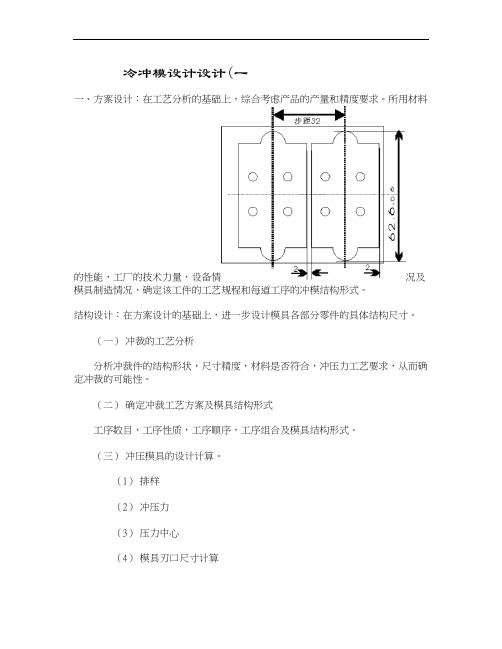
冷冲模设计设计(一一、方案设计:在工艺分析的基础上,综合考虑产品的产量和精度要求。
所用材料的性能,工厂的技术力量,设备情况及模具制造情况,确定该工件的工艺规程和每道工序的冲模结构形式。
结构设计:在方案设计的基础上,进一步设计模具各部分零件的具体结构尺寸。
(一)冲裁的工艺分析分析冲裁件的结构形状,尺寸精度,材料是否符合,冲压力工艺要求,从而确定冲裁的可能性。
(二)确定冲裁工艺方案及模具结构形式工序数目,工序性质,工序顺序,工序组合及模具结构形式。
(三)冲压模具的设计计算。
(1)排样(2)冲压力(3)压力中心(4)模具刃口尺寸计算(5)确定各主要零件的外形尺寸(6)计算模具的闭合高度(7)确定所用冲床(四)绘制冲模总装图从冷冲模标准中选取标准件,将标准编号写入详细表。
(五)绘制非标准零件图二、设计实例(一)冲裁件工艺分析1、材料:08F是优质碳素钢,具有良好的冲压性能。
2、结构形状:冲裁件内,外形要尽量避免尖锐清角。
3、尺寸精度:未标注按IT14级,查标准公差表。
(二)确定工艺方案及模具形式:采用具有导正钉定位的连续冲裁模。
(三)模具设计计算1、排样:按表2-8查:a:手动送料按图形a=2b: 手动送料按图形b=2条料宽度:B=(d+2a- =(58+4-0.6=62-0.6步进:30+2=32画出排样图2、计算总冲压力P总=P冲裁+P推件=P冲孔+P落料+P推件P冲孔=1.3Lt=4*3.14*3.5*2*390=34000NPt=Kt.Pn取n=3 Kt=0.055(查表2-5Pt=0.055*(126000+34000*3=26400=186400N=186.4KN3、压力中心在O1上,P2压力中心在O上。
离O1距离为X根据压力中心两边边距相等的条件:P1X=(32-X)P2X=6.84、冲模刃口尺寸计算(1)落料凹、凸模尺寸,按配合加工,只计算凹模尺寸。
外形尺寸都属于尺寸变大的情况:凸模尺寸按相应的凹模实际尺寸配作,保证双边间隙:0.246-0.360(2)冲孔时的凸凹模尺寸计算。
基于S olidWorks的冷冲模模架库设计

基于S olidWorks的冷冲模模架库设计冷冲模是一种常见的模具类型,广泛应用于汽车、家电、航空航天等领域。
为了提高模具制造的效率和减少生产成本,模具制造厂商普遍采用了基于CAD/CAM软件的数字化设计技术。
SolidWorks作为一款功能强大的机械制图软件,可以帮助设计师快速、高效地完成冷冲模模架库的设计。
一、设计准备工作在进行冷冲模模架库的设计前,需要对模架库的结构和设计要求有充分的了解。
此外,还需要对使用的材料、尺寸精度、生产工艺等方面进行详细的考虑。
只有充分考虑这些因素,才能保证设计出具有完整性、精度和可靠性的冷冲模模架库。
二、构建三维模型在进行冷冲模模架库的设计时,首先需要构建三维模型。
在SolidWorks中,可以通过“装配体”功能来实现模型的组装和细节设计。
在创建装配体时,需要按照实际的设计要求设置约束和关系,保证各个零部件之间的连接和协调。
模型的建立完成后,还需要对模型进行检查和优化,确保模型的结构和性能符合设计要求。
三、细节设计细节设计是指对模型的零件进行具体的制图和参数设置,以便于进行生产和加工。
在进行细节设计时,必须根据实际情况对模具的尺寸、材料、加工方式等各项参数进行认真的考虑,以确保模具的性能和质量符合要求。
四、增强设计功能为了提高冷冲模模架库的设计效率和精度,可以使用SolidWorks的增强设计功能。
比如可以使用“尺寸驱动”或“方程式驱动”功能,将模型的各个参数关联起来,使得其可以根据不同的尺寸要求自动调整。
此外,还可以使用“组件图库”功能,将常用的零部件进行分类和存储,方便以后的设计和使用。
五、验证和优化在设计完成后,还需要对模型进行验证和优化。
SolidWorks提供了多种仿真和分析工具,可以快速、准确地分析模具在使用过程中面临的各种力学、工艺和失败情况。
通过这些工具的分析,可以及时的发现并解决设计上的问题,提高模具的可靠性和性能。
六、总结综上所述,在设计冷冲模模架库时,SolidWorks是一个功能强大、易于使用的工具。
模具毕业设计80冷冲模课程设计
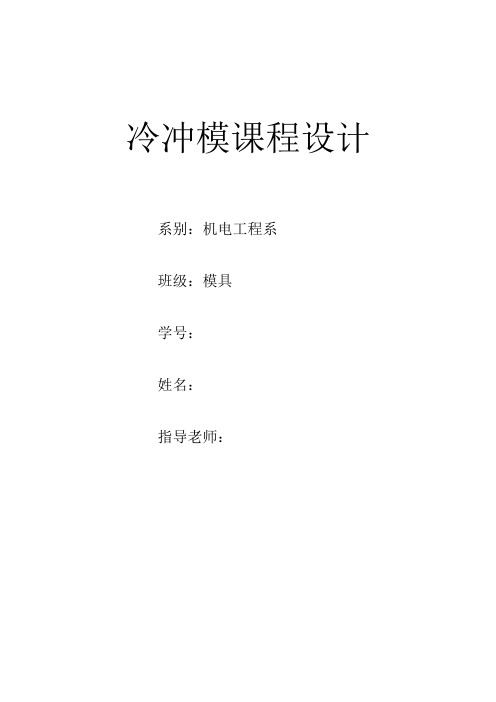
冷冲模课程设计系别:机电工程系班级:模具学号:姓名:指导老师:前言冷冲模设计是模具设计与制造专业学生在学完基础课理论课,技术基础课和专业课的基础上,所设置的一个重要的实践性教学环节。
其目的是:1.应用本专业所学课程的理论和生产实际知识,进行一次冷冲模设计工作的实际训练,从而培养和提高学生工作的能力。
2.巩固与扩充“冷冲模设计”等课程所学的内容,掌握冷冲模设计的方法和步骤。
3.掌握冷冲模设计的基本技能,如计算,绘图,查阅设计资料和手册,熟悉标准和规范等4.希望通过本次冷冲模设计答辩能够更好的熟悉和掌握里面所学的知识点。
希望在本次答辩能够在老师的指正下和同学的帮助下迷补不足之处。
由于初学者水平能力有限,设计中难免有不足和错误之处,恳请老师、同学给予批评指正。
目录一、冲压工艺分析 (4)二、确定冲压工艺方案 (4)三、排样方案的确定 (5)四、压力中心的确定 (6)五、计算冲压力 (7)六、模具工作部分尺寸计算 (9)七、凹模尺寸的确定及凸模的设计与校核 (12)八、模具其它零件的设计与计算 (14)九、压力机相关参数的校核 (14)十、零件图 (15)十一、装配图 (18)一、冲压工艺分析材料:QBe2料厚:1.5mm大批量生产1. 材料为QBe2具有良好的冲裁性能适合冲裁2.精度等级:IT11级。
利用普通冲裁可以实现要求。
3.结构尺寸:结构简单、形状对称,水平两圆圆心距为12.5 0.1。
竖直两圆其圆心距为12±0.05,制件底部宽为47±0.15,上部宽为24.5±0.1,4个圆的直径为三段圆弧半径分别为R47.501.0_、R44.201.0_、R68014.0_其余为注公差属于自由尺寸。
结论:此制件适合冲裁。
二、确定冲压工艺方案该制件包括落料和冲孔两道工序,可以有以下三种方案:方案一:先落料后冲孔,采用单工序模生产方案二:冲孔---落料连续冲压,采用级进模生产方案三:冲孔---落料复合冲压,采用复合模生产方案一模具结构简单,但因该零件有落料、冲孔两道工序,需要2套模具,且需要进行两次定位,带来定位累计误差,导致孔的位置精度不高,而且生产效率低,不适合大批量生产。
冷冲模设计题目一百道(含答案)

冲压工艺及模具设计1影响金属塑性和变形抗力的因素有哪些?答:影响金属塑性的因素有如下几个方面:1 )、化学成分及组织的影响;2 )、变形温度;)变形速度;4 )、应力状态;2.请说明屈服条件的含义,并写出其条件公式。
答:屈服条件的表达式为:,其含义是只有当各个应力分量之间符合一定的关系时,该点才开始屈服。
3 .什么是材料的机械性能?材料的机械性能主要有哪些?答:材料对外力作用所具有的抵抗能力,称为材料的机械性能。
板料的性质不同,机械性能也不一样,表现在冲压工艺过程的冲压性能也不一样。
材料的主要机械性能有:塑性、弹性、屈服极限、强度极限等,这些性能也是影响冲压性能的主要因素。
4.什么是加工硬化现象?它对冲压工艺有何影响?答:金属在室温下产生塑性变形的过程中,使金属的强度指标( 如屈服强度、硬度) 提高、塑性指标( 如延伸率) 降低的现象,称为冷作硬化现象。
材料的加工硬化程度越大,在拉伸类的变形中,变形抗力越大,这样可以使得变形趋于均匀,从而增加整个工件的允许变形程度。
如胀形工序,加工硬化现象,使得工件的变形均匀,工件不容易出现胀裂现象。
5 .什么是板厚方向性系数?它对冲压工艺有何影响?答:由于钢锭结晶和板材轧制时出现纤维组织等因素,板料的塑性会因为方向不同而出现差异,这种现象称为板料的塑性各项异性。
各向异性包括厚度方向的和板平面的各向异性。
厚度方向的各向异性用板厚方向性系数r 表示。
r 值越大,板料在变形过程中愈不易变薄。
如在拉深工序中,加大r 值,毛坯宽度方向易于变形,而厚度方向不易变形,这样有利于提高拉深变形程度和保证产品质量。
通过对软钢、不锈钢、铝、黄铜等材料的实验表明,增大r 值均可提高拉深成形的变形程度,故r 值愈大,材料的拉深性能好。
6 .什么是板平面各向异性指数Δ r ?它对冲压工艺有何影响?答:板料经轧制后,在板平面内会出现各向异性,即沿不同方向,其力学性能和物理性能均不相同,也就是常说的板平面方向性,用板平面各向异性指数Δ r 来表示。
3.2.1-1 《冷冲模设计实训》课程标准——金璐玫
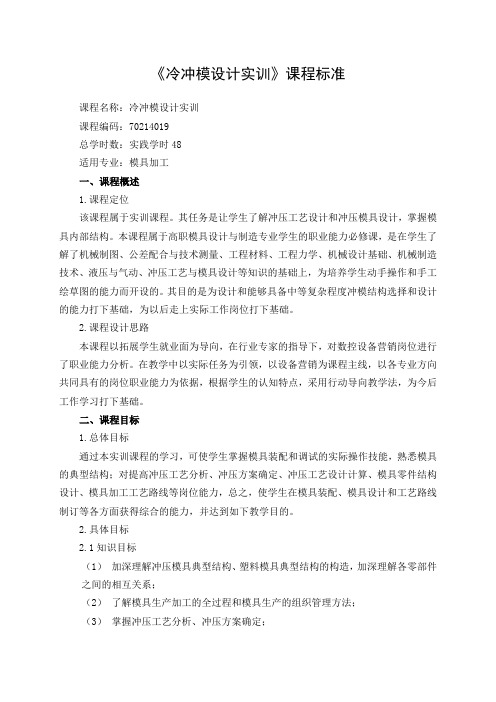
《冷冲模设计实训》课程标准课程名称:冷冲模设计实训课程编码:70214019总学时数:实践学时48适用专业:模具加工一、课程概述1.课程定位该课程属于实训课程。
其任务是让学生了解冲压工艺设计和冲压模具设计,掌握模具内部结构。
本课程属于高职模具设计与制造专业学生的职业能力必修课,是在学生了解了机械制图、公差配合与技术测量、工程材料、工程力学、机械设计基础、机械制造技术、液压与气动、冲压工艺与模具设计等知识的基础上,为培养学生动手操作和手工绘草图的能力而开设的。
其目的是为设计和能够具备中等复杂程度冲模结构选择和设计的能力打下基础,为以后走上实际工作岗位打下基础。
2.课程设计思路本课程以拓展学生就业面为导向,在行业专家的指导下,对数控设备营销岗位进行了职业能力分析。
在教学中以实际任务为引领,以设备营销为课程主线,以各专业方向共同具有的岗位职业能力为依据,根据学生的认知特点,采用行动导向教学法,为今后工作学习打下基础。
二、课程目标1.总体目标通过本实训课程的学习,可使学生掌握模具装配和调试的实际操作技能,熟悉模具的典型结构;对提高冲压工艺分析、冲压方案确定、冲压工艺设计计算、模具零件结构设计、模具加工工艺路线等岗位能力,总之,使学生在模具装配、模具设计和工艺路线制订等各方面获得综合的能力,并达到如下教学目的。
2.具体目标2.1知识目标(1)加深理解冲压模具典型结构、塑料模具典型结构的构造,加深理解各零部件之间的相互关系;(2)了解模具生产加工的全过程和模具生产的组织管理方法;(3)掌握冲压工艺分析、冲压方案确定;(4)掌握冲压工艺设计计算;(5)掌握模具零件结构设计;(6)熟悉模具模具总装图和零件图的绘制;(7)掌握并独立完成中等模具设计过程和步骤;(8)掌握模具的装配和调试。
2.2素质目标(1)能及时发现工作中出现的问题,并分析问题和提出解决方案;(2)具有团队协作精神和良好的交流能力;(3)具有较强的工作责任心、良好的社会责任感。
冷冲压模具结构与设计实例
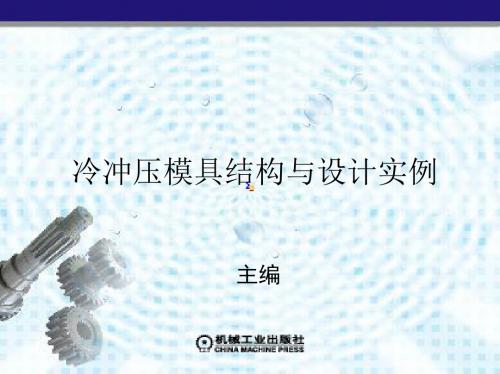
一、制件工艺性要求
图1-2 冲裁件尺寸工艺性
一、制件工艺性要求
表1-2 钢材制件一般冲孔模可以冲压的最小孔径
表1-3 一般冲裁件剪断面的表面粗糙度值
二、制件的工艺分析
内容二 制订工艺方案及确定模具结构
一、制定冲压工艺方案 二、复合模的概念与分类 三、正装式复合模和倒装式复合模的性能比较 四、复合模工作零件的位置关系 五、复合模具的结构形式
五、复合模具的结构形式
表1-7 卸料螺钉的尺寸(单位:mm)
五、复合模具的结构形式
图1-12 刚性推件(顶件)装置 1—模柄 2—打杆 3—上模座 4—推板 5—垫板 6—连接推杆
7—拆分式卸料块 8—冲孔凸模 9—落料凹模
五、复合模具的结构形式
图1-13 复合模推件装置的工作原理 1—限位螺钉 2—打料横梁 3—打杆 4—推板 5—连接推杆 6—卸料块
一、计算零件毛坯尺寸
表1-11
二、排样与材料利用率
表1-12 低碳钢的搭边a
二、排样与材料利用率
图1-26 排样图
二、排样与材料利用率
图1-27 对排落料排样图
二、排样与材料利用率
图1-28 复合模排样图
二、排样与材料利用率
图1-29 排样图
二、排样与材料利用率
图1-30 步距与有效面积示意图
二、确定落料凹模尺寸
表1-25
表1-26 螺钉直径选用
二、确定落料凹模尺寸
图1- 41 常见凹模板固定形式
二、确定落料凹模尺寸
图1- 42 凹模轮廓尺寸示意图
二、确定落料凹模尺寸
表1-27 凹模壁厚c
二、确定落料凹模尺寸
表1-28 螺纹孔、销钉孔及刃口边的最小距离(淬火件)(单位:mm)
冷冲模冷冲压模具的结构与设计1课件
工作零件
工艺零件 定位零件
冲裁模零部件
卸料与推件零部件
结构零件 导向零件 连接与固定零件
其它零件
二、模具零件的结构与设计
1、凸模组件及其结构设计 2、凹模设计 3、定位零件 4、卸料与推件零件 5、模架
1、凸模组件及其结构设计
凸模组件:凸模、凸模固定板、垫板和防转销、 上模座、螺钉、销钉固定
倒装模凸凹模的最小壁厚: 查p.102表4-4
3、定位零件
横向定位装置:使条料由正确的送进方向
导料销、导料板及侧压装置
纵向定位装置:控制条料在冲裁中送进步距
挡料销、导正销、侧刃
定位板和定位钉
横向定位装置
导料销
导料销两个,位于条料的同侧
导料板
两导料板之间距离L=条料最大宽度+间隙值 导料板厚度H=材料厚度t或挡料销高度+(2∽8) 整体式导料板其长度和宽度与凹模板外形尺寸
缺点:模具结构复杂,材料有额外消耗,定位 精度不高。
连续模排样
连续模排样设计:
1、零件精度对排样要求:
精度要求高——尽量减少工位数 孔距公差较小——尽量同一工位冲出
2、模具结果对排样要求:
零件较大或较小但工位多——采用连续复合排样
3、模具强度对排样要求:
孔距小——分布冲 工位间凹模壁厚小——增设空工位 外形复杂——分布冲
动力由压力机传递给 模具
相关链接:动力
第一节 冲压模的分类
一、按工序组合程度分 二、按上下模导向方式分 三、按凹模位置分 四、按自动化程度分
一、按工序组合程度分
1、单工序模(简单模)
单工序模是指压力机在一次行程中只完成一道工序的冲裁模
2在、一多副模工具中序,模在模具的同一位置上能同时完成数种 工序的模具 (在压力机的一次行程中,在模具的同一位置上同时 完成A几、道连工序续的模冲(模)级进模、跳步模) 在一副模具中,材料在模具的不同位置上能同时完成各 自工(B序是、指复压合力机模在一次行程中依次在几个不同的位置上 同时完成多道工序的冲模)
冷冲压模具设计与制造
冷冲压模具设计与制造1. 引言冷冲压模具是冷冲压工艺的关键部件,用于在金属材料加工过程中对其进行塑性变形。
冷冲压技术具有高效、高精度、低能耗等优点,广泛应用于汽车、电子、家电等行业。
本文将介绍冷冲压模具的设计与制造方法。
2. 冷冲压模具设计冷冲压模具设计最重要的是确定模具的结构和尺寸。
以下是冷冲压模具设计的几个关键步骤:2.1 确定模具结构冷冲压模具通常由上模、下模、导向机构、定位机构等组成。
在设计模具结构时,需要考虑加工工件的形状和尺寸,以及冷冲压机的型号和性能。
2.2 确定模具尺寸模具尺寸的确定与工件的形状、尺寸和厚度有关。
需要考虑到材料的强度和可加工性,在满足工件要求的前提下,尽量减小模具的尺寸。
2.3 设计模具零件根据模具结构和尺寸,设计各个零部件的形状和尺寸。
主要包括上模、下模、导柱、导套、顶杆等零件。
在设计过程中,需要考虑零件的材料选择、工艺性能和加工精度。
2.4 确定模具的工装冷冲压模具的工装通常包括导向套、切断装置、定位装置等。
根据工件的特点和加工要求,选择合适的工装,并合理布置在模具上。
3. 冷冲压模具制造冷冲压模具的制造需要经过以下几个步骤:3.1 材料准备选择适合的模具材料,通常使用优质合金工具钢。
根据模具的使用要求,选择合适的材料硬度和韧性。
3.2 切削加工根据模具设计的零部件图纸,进行车、铣、磨等切削加工。
确保模具的尺寸和形状符合设计要求。
3.3 加工热处理通过热处理过程,提高模具材料的硬度和耐磨性。
常见的热处理方法包括淬火、回火等。
3.4 组装和调试将各个零部件按照设计要求组装成完整的模具,并进行调试。
确保模具的各个部位协调运动,完成工件的加工过程。
3.5 表面处理对模具进行表面处理,提高模具的耐磨性和表面光洁度。
常见的表面处理方法包括硬质激光熔覆、电火花加工等。
4. 模具试产与调试完成冷冲压模具的制造后,需要进行试产和调试。
通过试产,测试模具的性能和质量,同时对模具进行优化和调整,以满足工艺要求和工件质量要求。
冷冲压模具设计要点
冷冲压模具设计要点
1.材料选择:冷冲压模具所使用的材料应具有高强度、耐磨损和耐腐
蚀的特性,一般常用于模具制作的材料有工具钢、硬质合金、高速钢等。
2.结构设计:冷冲压模具的结构设计应考虑到模具的强度、刚性和稳
定性,以保证模具在使用过程中能够承受大的载荷和高频的工作循环,同
时也要考虑到模具的拆卸和维护方便。
3.设计尺寸:模具设计的尺寸应根据产品的形状、尺寸和要求来确定,其中应考虑到材料的伸缩性、弹性以及工艺的要求等因素,确保成形后的
产品尺寸精度和表面质量。
4.几何形状:冷冲压模具的几何形状应符合产品的要求,具有合理的
结构,以利于金属材料在成形过程中的流动和填充,同时也要避免产生应
力集中和变形等问题。
5.寿命和耐磨性:冷冲压模具在使用过程中会受到金属材料的冲击和
磨损,因此需要具备良好的耐磨性和长寿命,可以通过表面涂层、热处理
以及硬质合金加工等方式来提高模具的寿命。
6.润滑和冷却:在冷冲压过程中,为了减少摩擦和热量的产生,需要
对冷冲压模具进行润滑和冷却处理,以保证模具的正常工作和生产效率。
7.精度和控制:冷冲压模具的设计要考虑到产品的精度和控制要求,
包括成形厚度、尺寸公差、直角度、表面平整度等,以保证产品的质量和
性能。
8.模具标准和规范:对于冷冲压模具的设计,应按照相关的标准和规
范进行设计,以确保模具的质量和安全性。
冷冲压模具设计的要点主要包括材料选择、结构设计、设计尺寸、几何形状、寿命和耐磨性、润滑和冷却、精度和控制,以及模具标准和规范等方面。
只有综合考虑以上要点并灵活运用,才能设计出高质量、高效率的冷冲压模具。
冷冲压模具设计标准
冷冲压模具设计标准
冷冲压模具是一种用于金属材料成形加工的工具,其设计标准对于产品质量和
生产效率具有重要的影响。
在进行冷冲压模具设计时,需要考虑多种因素,包括材料选择、结构设计、加工工艺等方面。
本文将从这些方面对冷冲压模具的设计标准进行详细介绍。
首先,材料选择是冷冲压模具设计的关键。
模具的材料需要具有足够的硬度和
耐磨性,以保证长时间的使用寿命。
同时,材料还需要具有较高的强度和韧性,以承受冲击和挤压的力量。
常见的冷冲压模具材料包括工具钢、硬质合金等,设计者需要根据具体的工件材料和加工工艺来选择合适的模具材料。
其次,结构设计是冷冲压模具设计的重要环节。
模具的结构需要合理布局,以
确保工件的成形精度和表面质量。
在设计模具结构时,需要考虑到模具的开合方式、导向装置、顶出装置等,以及模具的冷却系统和润滑系统。
合理的结构设计可以提高模具的使用寿命,减少维护成本,提高生产效率。
另外,加工工艺也是冷冲压模具设计的重要内容。
模具的加工工艺需要考虑到
模具的制造成本、加工难度和加工精度。
在进行模具加工时,需要选择合适的加工设备和工艺,保证模具的尺寸精度和表面质量。
同时,还需要进行模具的热处理和表面处理,以提高模具的硬度和耐磨性。
综上所述,冷冲压模具设计标准涉及到材料选择、结构设计和加工工艺等多个
方面。
设计者需要综合考虑这些因素,以确保模具具有良好的使用性能和经济性。
只有在严格遵循设计标准的基础上,才能设计出高质量、高效率的冷冲压模具,满足不同工件的加工需求。
- 1、下载文档前请自行甄别文档内容的完整性,平台不提供额外的编辑、内容补充、找答案等附加服务。
- 2、"仅部分预览"的文档,不可在线预览部分如存在完整性等问题,可反馈申请退款(可完整预览的文档不适用该条件!)。
- 3、如文档侵犯您的权益,请联系客服反馈,我们会尽快为您处理(人工客服工作时间:9:00-18:30)。
目录
1:设计题目
2:原始数据
3:零件的工艺分析
4:确定总裁工艺方案
5:工艺与设计计算
6::定位零件的设计与标准
7:模具总体设计
冷冲模设计
1:设计题目
简单垫片冲裁模
2:原始数据
冲压材料:08钢,进度t=2mm.
对凸凹
零件图:如下图
3:零件的工艺分析
该零件对称形简单,形状规则,适于总裁加工。
材料为08钢、厚度t=2mm的碳素钢,抗拉强度为324~441MP,零件尺寸无特殊要求,按IT14(即∆=0.52mm)级选取,利用普通总裁方式可达到图样要求。
4:确定总裁工艺方案
总裁该工件只需落料一个基本工序,因此采用单工序摸生产即可满足条件。
5:工艺与设计计算
(1):冲裁力的计算
根据零件图可采用普通平刃口模具冲裁,冲裁力F可按下式计算:
F=KLtτb
式中:F——冲裁力;
L——冲裁周边长度;
t——材料厚度;
τb——材料抗剪强度;
K——系数。
(一般取K=1.3)
其中L=52.06+0.39×2+14.7=67.54mm
τb=300MP
所以F=1.3×67.54×2×300N=52681.2N
(2):卸料力、推件力和顶件力
卸料力:Fx=Kx×F=0.03×52681.2=1580.436N
推件力:Ft=nK T×F=0.040×52681.2=2107.248N 顶件力:F D=K D×F=0.05×52681.2=2634.06N
n=h/t
式中:F——冲裁力;
Kx、K D、K T——卸料力、推件力及顶件力系数(可查表2.17);
n——同时卡在凹模内的冲裁件(或废料)的个数;
h——凹模刃壁垂直部分高度,mm;
t——板料厚度。
(3):压力中心的计算
压力中心分析图如下图所示:
由圆弧段压力的压力中心按下式
y=Rs /b
求得:y=11×14.7/52.06=3.106mm;
由零件图分析可知,该工作是对称零件,其重心定在对称线AB上,且在中心线CD以上,由上式计算所得到的值是重心到中心线CD的距离,其压力中心即为重心,取整可得y=3mm.即工件的压力中心在中心线CD以上的3mm处。
(4):计算各主要零件的尺寸
i:凸凹模刃口尺寸的确定
落料模应以为基准,间隙取在凸模上,即冲裁间隙通过减小凸刃口尺寸来取得。
(冲裁间隙一般选用最小合理间隙Z min)
落料凹模:D A=(D max-x∆)0+δA
落料凸模:D T=(D A-Z min)0-δT=( D max-x∆-Z min)0-δT
式中:D A
、D T——落料凹、凸模刃口尺寸,mm;
D max——落料件的最大极限尺寸,mm;
∆——冲裁件制造公差,mm;
δT、δA——凸、凹模的制造公差,可查表2.10;(或取
δT<=0.4(Z max-Z min), δA<=0.6(Z max-Z min);
x——磨损系数,在0.5~1之间,与工件精度有关,可查
表2.11或按下列值选取。
工件精度IT10以上,x=1;
工件精度IT11~IT13,x=0.75;
工件精度IT14以下,x=0.5。
由零件所标的尺寸可知Ø220-0.52、14.70-0.43、190-0.52;
凸凹模制造公差取δT=0.2∆Z=0.008,δA=0.4∆Z=0.016
D A1=(22-0.5×0.52)0+0.016=21.740+0.016
D T1=(22-0.5×0.52-0.14)0-0.008=21.60-0.008
D A2=(14.7-0.5×0.43) 0+0.016=14.480+0.016
D T02=(14.7-0.5×0.43-0.14) 0-0.008=14.340-0.008
D A3=(19-0.5×0.52)0+0.016=18.740+0.016
D T30=(19-0.5×0.52-0.14)+0.0160=18.60+0.016
ii:凹模厚度: H=kb(=>15mm)
凹模壁厚:C=(1.5~2)H(=>30~40mm)
式中:b——凹模刃口的最大尺寸,mm
k——系数,考虑板料厚度的影响,可查表 2.22
(k=0.42)。
由上式可计算得:凹模厚度为:H=0.42×22=9.24取整为15mm
凹模壁厚为:C=2H=30mm。
凹模的外形尺寸;(2C+22)×(2C×22)即82×82取整80×80mm,凹模的结构图如下图示:
iii:凸模固定板的厚度。
H1=0.7H=21mm,取整数为:20mm。
iiii:垫板的采用与厚度:是否采用垫板,心承压面较小的凸模进行计
算,冲近似圆形孔的凸模承压面的尺寸如下图所示。
所以其承压应力为:
σ=F/A=205.99>[σp],所以须采用垫板,垫板厚度取8mm. iV:卸料弹簧的自由高度。
根据工件材料厚度为2mm,冲裁时凸模进入凹模深度取1mm,考虑模具维修时刃磨留余量2mm,再考虑开启时卸料板高出凸模1mm,则总的工作行程,h工件=10mm,弹簧的自由高度为:
h自由=h工件/(0.25~0.3)=27~32mm
取h自由=32mm
模具在组装时弹簧的预压量为:
h预=(10%~15%)×h自由=3.2~4.8mm
取h预=4mm。
由此可算出模具中安装弹簧的空间高度尺寸为
6:定位零件的设计与标准
1:导料销、导料板:导料销(板)的作用是导正材料的送进方向。
可用于单工序模。
由材料厚度为2mm,这里的导料销高度取3mm,导料板高度为6~8mm。
2:挡料销:挡料销用于限定条料送进距离、挡住条料的搭边或工件轮廓,起定位作用。
(挡料销有固定挡料销、活动挡料销和始用挡料销)这里为了不削弱凹模强度,采用固定钩形的挡料销。
3:卸料板:卸料板用于卸掉卡在凸模上的或凸凹模上的冲裁件或废料。
这里采用弹压卸料装置,其既起卸料作用又起压料作用,由于板料厚度为2mm,故凸模与卸料板的双面间隙取0.5mm。
4:导柱、导套的选用
根据需要查标准。
7:模具总体设计
有了上述步计算所得的数据及确定的工艺方案后,便可以对模具进行总体设计模具总装图如装配图示。