化工原理吸收实验
(化工原理实验)吸收实验

100%
吸收操作
开启恒温水浴,使吸收塔内温度 恒定。将配制好的吸收剂从塔顶 缓慢加入,保持塔内液面稳定。
80%Βιβλιοθήκη 数据记录在实验过程中,定时记录气体流 量、塔内温度、压力以及吸收剂 液位等关键数据。
数据记录与处理
01
数据整理
将实验过程中记录的各项数据整理成表格,便于后续分析。
02
数据处理
根据实验原理,对数据进行处理,如计算吸收速率、吸收效率等关键指
实验注意事项
实验前准备
熟悉实验流程,了解设备构造及 功能,检查实验装置是否完好,
确保实验条件符合安全要求。
操作规范
严格遵守实验操作规程,避免误 操作引发事故。
数据记录
认真记录实验数据,确保数据真 实可靠,为后续分析提供依据。
安全防护措施
个人防护
实验人员需佩戴合适的防护用品,如实验服、护目镜、手套等, 以降低化学品对皮肤和眼睛的伤害。
数据处理结果
通过数据处理,得到了不同条 件下的吸收率和传质系数,为 后续结果分析和讨论提供了依 据。
结果分析与讨论
吸收率分析
01
分析了不同操作条件下吸收率的变化规律,探讨了温度、压力、
流量等因素对吸收率的影响。
传质系数讨论
02
讨论了传质系数与操作条件的关系,以及传质系数对吸收过程
的影响。
结果合理性判断
03
根据实验结果和理论分析,判断了实验结果的合理性,并对可
能存在的误差进行了分析。
与理论预测比较
理论预测模型
介绍了用于预测吸收过程的理论模型,包括传质方程、热力学模 型等。
实验结果与理论预测比较
将实验结果与理论预测进行了比较,分析了两者之间的差异和原因。
氧解析-化工原理-吸收-实验报告

氧解析-化工原理-吸收-实验报告一、实验目的1. 学习氧解析法的基本原理和实验操作。
2. 了解化学吸收法的原理及其在氧解析中的应用。
3. 掌握氧解析实验中的基本操作技能。
二、实验原理1.氧解析原理氧解析的原理是利用红色五价铁离子与氧气发生氧化反应的原理,通过测定铁离子还原的电位差来确定氧气的含量。
具体反应式如下:Fe2+ + 1/4O2 + 2H+ → Fe3+ + 1/2H2O由于1mol电子交换可产生1.23V电势,通过测定铁离子还原电位和标准电极电位的差值,即可得到氧气的含量。
2.化学吸收原理化学吸收法是通过某种吸收剂与被测气体的化学反应来去除被测气体中的某种成分的方法。
吸收剂可选择性地吸收被测气体中的某种成分,然后通过吸收前后吸收剂的质量差来确定该成分的含量。
在氧解析中,选择NaOH作为吸收剂,用于吸收氧气。
三、实验步骤1. 洗涤仪器:将氧解析仪、吸收瓶、饱和盐水瓶和试管用酒精清洗干净。
2. 理顺连接线:将氧解析仪与吸收瓶通过橡胶软管连接,吸收瓶与饱和盐水瓶通过橡胶软管连接,饱和盐水瓶与试管通过橡胶软管连接。
3. 加入吸收剂:将20mL的0.1mol/L NaOH溶液倒入吸收瓶中。
4. 预处理:将氧解析仪的样品室和参比室用稀硝酸洗涤干净,然后用蒸馏水冲洗干净。
5. 校准:用样品室中的氧气校准氧解析仪,通过调节样品室中的Hg电极电势,使得氧解析仪显示的氧气浓度与标准气体浓度一致。
6. 吸氧:将被测气体(氮气与氧气混合气体)通过饱和盐水瓶并以一定流速进入吸收瓶,其中氧气被NaOH吸收,剩余的氮气流经氧解析仪,接着通过排气口排出实验室。
7. 计算:通过测定吸收剂的重量差和转化率计算氧气的含量。
四、实验结果与分析实验中测得的吸收剂重量差为0.23g,转化率为95%,因此氧气的含量为100%-95%=5%。
五、实验结论本实验通过氧解析法和化学吸收法,成功测定了氧气的含量。
实验结果表明本实验的测量结果较为准确,具有较高的稳定性和重复性,可有效满足实际应用需求。
化工原理实验报告吸收实验
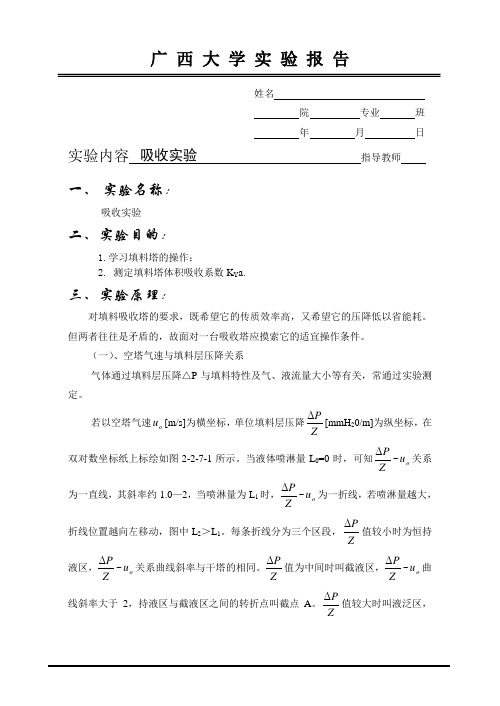
姓名院 专业 班 年 月 日 实验内容 指导教师一、 实验名称:吸收实验二、实验目的:1.学习填料塔的操作;2. 测定填料塔体积吸收系数K Y a .三、实验原理:对填料吸收塔的要求,既希望它的传质效率高,又希望它的压降低以省能耗。
但两者往往是矛盾的,故面对一台吸收塔应摸索它的适宜操作条件。
(一)、空塔气速与填料层压降关系气体通过填料层压降△P 与填料特性及气、液流量大小等有关,常通过实验测定。
若以空塔气速o u [m/s]为横坐标,单位填料层压降ZP ∆[mmH 20/m]为纵坐标,在双对数坐标纸上标绘如图2-2-7-1所示。
当液体喷淋量L 0=0时,可知Z P ∆~o u 关系为一直线,其斜率约1.0—2,当喷淋量为L 1时,ZP ∆~o u 为一折线,若喷淋量越大,折线位置越向左移动,图中L 2>L 1。
每条折线分为三个区段,Z P ∆值较小时为恒持液区,Z P ∆~o u 关系曲线斜率与干塔的相同。
Z P ∆值为中间时叫截液区,ZP ∆~o u 曲线斜率大于2,持液区与截液区之间的转折点叫截点A 。
Z P ∆值较大时叫液泛区,吸收实验姓名院 专业 班 年 月 日 实验内容 指导教师 ZP ∆~o u 曲线斜率大于10,截液区与液泛区之间的转折点叫泛点B 。
在液泛区塔已无法操作。
塔的最适宜操作条件是在截点与泛点之间,此时塔效率最高。
图2-2-7-1 填料塔层的ZP ∆~o u 关系图图2-2-7-2 吸收塔物料衡算(二)、吸收系数与吸收效率本实验用水吸收空气与氨混合气体中的氨,氨易溶于水,故此操作属气膜控制。
若气相中氨的浓度较小,则氨溶于水后的气液平衡关系可认为符合亨利定律,吸收姓名院 专业 班 年 月 日 实验内容 指导教师 平均推动力可用对数平均浓度差法进行计算。
其吸收速率方程可用下式表示: m Ya A Y H K N ∆⋅⋅Ω⋅= (1) 式中:N A ——被吸收的氨量[kmolNH 3/h];Ω——塔的截面积[m 2]H ——填料层高度[m]∆Y m ——气相对数平均推动力K Y a ——气相体积吸收系数[kmolNH 3/m 3·h]被吸收氨量的计算,对全塔进行物料衡算(见图2-2-7-2):)()(2121X X L Y Y V N A -=-= (2) 式中:V ——空气的流量[kmol 空气/h]L ——吸收剂(水)的流量[kmolH 20/h]Y 1——塔底气相浓度[kmolNH 3/kmol 空气]Y 2——塔顶气相浓度[kmolNH 3/kmol 空气]X 1,X 2——分别为塔底、塔顶液相浓度[kmolNH 3/kmolH 20]由式(1)和式(2)联解得:mYa Y H Y Y V K ∆⋅⋅Ω-=)(21 (3) 为求得K Y a 必须先求出Y 1、Y 2和∆Y m 之值。
最新化工原理实验报告吸收实验要点
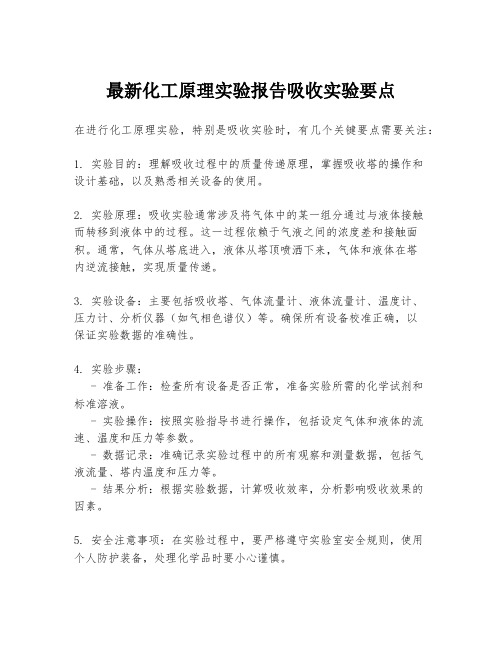
最新化工原理实验报告吸收实验要点在进行化工原理实验,特别是吸收实验时,有几个关键要点需要关注:1. 实验目的:理解吸收过程中的质量传递原理,掌握吸收塔的操作和设计基础,以及熟悉相关设备的使用。
2. 实验原理:吸收实验通常涉及将气体中的某一组分通过与液体接触而转移到液体中的过程。
这一过程依赖于气液之间的浓度差和接触面积。
通常,气体从塔底进入,液体从塔顶喷洒下来,气体和液体在塔内逆流接触,实现质量传递。
3. 实验设备:主要包括吸收塔、气体流量计、液体流量计、温度计、压力计、分析仪器(如气相色谱仪)等。
确保所有设备校准正确,以保证实验数据的准确性。
4. 实验步骤:- 准备工作:检查所有设备是否正常,准备实验所需的化学试剂和标准溶液。
- 实验操作:按照实验指导书进行操作,包括设定气体和液体的流速、温度和压力等参数。
- 数据记录:准确记录实验过程中的所有观察和测量数据,包括气液流量、塔内温度和压力等。
- 结果分析:根据实验数据,计算吸收效率,分析影响吸收效果的因素。
5. 安全注意事项:在实验过程中,要严格遵守实验室安全规则,使用个人防护装备,处理化学品时要小心谨慎。
6. 实验结果分析:通过对收集到的数据进行分析,可以确定吸收塔的效率和操作条件对吸收效果的影响。
此外,还可以通过对比理论值和实验值,来评估实验的准确性和可靠性。
7. 结论:基于实验结果和分析,得出关于吸收过程效率和操作参数对吸收效果影响的结论。
同时,提出可能的改进措施和建议。
8. 参考文献:列出实验报告中引用的所有文献和资料,确保信息来源的准确性和可靠性。
以上是吸收实验的主要内容要点,每个实验报告的具体内容可能会根据实验的具体要求和条件有所不同。
化工原理 欧贝尔 吸收实验

化工原理欧贝尔吸收实验化工原理是化学工程学科中的一门基础课程,主要研究化工生产过程中涉及的基本原理和方法。
欧贝尔吸收实验是化工原理实验中的一种重要实验,主要用于研究气体吸收过程中不同操作条件对吸收效果的影响。
本文将介绍欧贝尔吸收实验的实验目的、实验原理、实验步骤以及实验结果分析。
一、实验目的欧贝尔吸收实验的主要目的是:1.掌握气体吸收的基本原理和方法;2.研究不同操作条件对吸收效果的影响;3.学习使用化工原理实验仪器设备。
二、实验原理气体吸收是化工生产中常见的过程之一,主要通过将气体混合物通过液体吸收剂来分离其中某些组分。
欧贝尔吸收实验采用的是物理吸收法,即利用吸收剂对目标气体的物理亲和力来达到分离效果。
本实验选用二氧化碳和水作为吸收剂,通过测定不同操作条件下二氧化碳的吸收量来研究吸收效果。
三、实验步骤1.准备实验仪器和试剂:二氧化碳钢瓶、欧贝尔吸收装置、流量计、压力表、温度计、吸收剂(水或碱性溶液)、二氧化碳纯度分析仪等;2.将欧贝尔吸收装置连接至二氧化碳钢瓶,确保密封性良好;3.将流量计和压力表连接到吸收装置上,以便测量二氧化碳流量和压力;4.将温度计插入吸收液中,监测吸收液的温度;5.打开二氧化碳钢瓶阀门,调整流量计和压力表,使二氧化碳以一定流速进入吸收装置;6.观察并记录不同时间节点的二氧化碳流量、压力和温度数据;7.在实验结束后,关闭二氧化碳钢瓶阀门,拆下连接管道和仪表;8.对实验数据进行整理和分析。
四、实验结果分析通过实验数据可以得出以下结论:1.二氧化碳的吸收量随时间的增加而增加;2.吸收液的温度对吸收效果有显著影响,温度升高有助于二氧化碳的吸收;3.吸收液的流量对吸收效果也有影响,适当增加流量可以提高吸收速率;4.压力对二氧化碳的吸收影响较小,但在高压条件下,二氧化碳的溶解度较大,有助于提高吸收效果。
通过对实验结果的分析,可以进一步探讨不同操作条件对气体吸收效果的影响机制。
例如,在温度较高的情况下,二氧化碳在水中的溶解度增加,因此提高温度可以促进二氧化碳的吸收;而在压力较低的情况下,二氧化碳更容易从气相进入液相,因此增加压力有助于提高吸收效果。
化工原理实验报告吸收实验
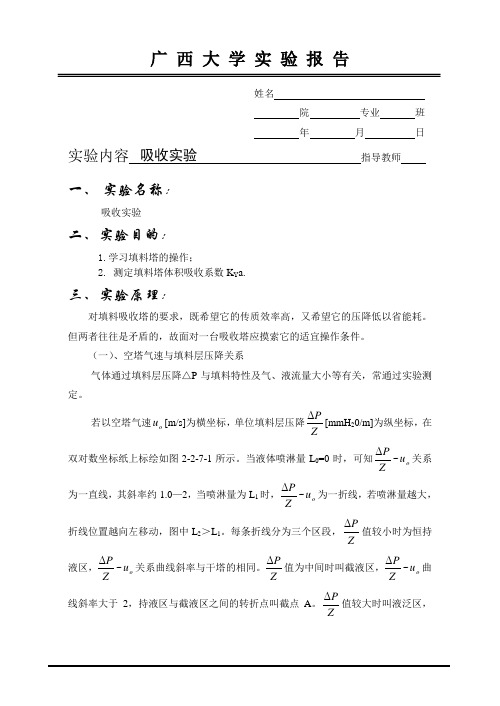
姓名院 专业 班 年 月 日 实验内容 指导教师一、 实验名称:吸收实验二、实验目的:1.学习填料塔的操作;2. 测定填料塔体积吸收系数K Y a .三、实验原理:对填料吸收塔的要求,既希望它的传质效率高,又希望它的压降低以省能耗。
但两者往往是矛盾的,故面对一台吸收塔应摸索它的适宜操作条件。
(一)、空塔气速与填料层压降关系气体通过填料层压降△P 与填料特性及气、液流量大小等有关,常通过实验测定。
若以空塔气速o u [m/s]为横坐标,单位填料层压降ZP ∆[mmH 20/m]为纵坐标,在双对数坐标纸上标绘如图2-2-7-1所示。
当液体喷淋量L 0=0时,可知Z P ∆~o u 关系为一直线,其斜率约1.0—2,当喷淋量为L 1时,ZP ∆~o u 为一折线,若喷淋量越大,折线位置越向左移动,图中L 2>L 1。
每条折线分为三个区段,Z P ∆值较小时为恒持液区,Z P ∆~o u 关系曲线斜率与干塔的相同。
Z P ∆值为中间时叫截液区,ZP ∆~o u 曲线斜率大于2,持液区与截液区之间的转折点叫截点A 。
Z P ∆值较大时叫液泛区,吸收实验姓名院 专业 班 年 月 日 实验内容 指导教师 ZP ∆~o u 曲线斜率大于10,截液区与液泛区之间的转折点叫泛点B 。
在液泛区塔已无法操作。
塔的最适宜操作条件是在截点与泛点之间,此时塔效率最高。
图2-2-7-1 填料塔层的ZP ∆~o u 关系图图2-2-7-2 吸收塔物料衡算(二)、吸收系数与吸收效率本实验用水吸收空气与氨混合气体中的氨,氨易溶于水,故此操作属气膜控制。
若气相中氨的浓度较小,则氨溶于水后的气液平衡关系可认为符合亨利定律,吸收姓名院 专业 班 年 月 日 实验内容 指导教师 平均推动力可用对数平均浓度差法进行计算。
其吸收速率方程可用下式表示: m Ya A Y H K N ∆⋅⋅Ω⋅= (1) 式中:N A ——被吸收的氨量[kmolNH 3/h];Ω——塔的截面积[m 2]H ——填料层高度[m]∆Y m ——气相对数平均推动力K Y a ——气相体积吸收系数[kmolNH 3/m 3·h]被吸收氨量的计算,对全塔进行物料衡算(见图2-2-7-2):)()(2121X X L Y Y V N A -=-= (2) 式中:V ——空气的流量[kmol 空气/h]L ——吸收剂(水)的流量[kmolH 20/h]Y 1——塔底气相浓度[kmolNH 3/kmol 空气]Y 2——塔顶气相浓度[kmolNH 3/kmol 空气]X 1,X 2——分别为塔底、塔顶液相浓度[kmolNH 3/kmolH 20]由式(1)和式(2)联解得:mYa Y H Y Y V K ∆⋅⋅Ω-=)(21 (3) 为求得K Y a 必须先求出Y 1、Y 2和∆Y m 之值。
化工原理实验吸收.ppt
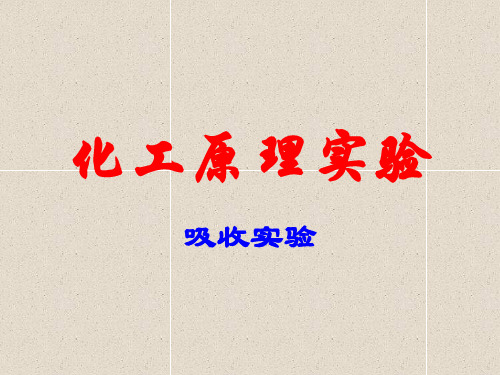
吸收实验
(一) 实验目的及认为
1、 熟悉填料吸收塔的结构与操作 2、 观察填料吸收塔流体力学状况,测定压降与
气速的关系曲线 3、 掌握总传质系数Kya的测定方法及影响因素
分析
4、 同过实验了解p—u曲线和传质系数Kya对工程 设计的重要意义
5、 学习对气液连续接触的填料塔利用传质速率方 程处理传质问题的方法
(二)基本原理
• 1、 填料塔流体力学特性
• 气体通过干填料层时,液体流动引起的压降 和湍流流动引起的压降规律相一致。
• 在双对数坐标系中压 降对气流做图得到一 条斜率为1.8—2的直 (图中a—a线)。
(图7—1 填料层压降— 空塔气速关系示意图 )
log p
d
a
c
ba
log u
• 而有喷淋量时,在低气速时,(c点以前)压 降也比例于气速的1.8~2次幂,但大于同一气速 下干填料的压降(图中bc段)。
4).单位时间氨吸收量 GA GA G(Y1 Y2 )
5).进气浓度 Y1
Y1
n1 n2
n 2 ——空气摩尔数
即:
Y1
V0 V0
6).尾气浓度 Y2
n1 n2
n1——氨气摩尔浓度;n 2 ——空气摩尔浓度
即: 式中
Y2
V
NS VS (T0 ) / 22.4
T
NS——加入分析盒中硫酸当量浓度[N];
VS ——加入分析盒中硫酸溶液体积[ml]
V——湿式气体流量计所量得的空气体积[ml];
T0 ——标准状态下空气温度[K];
T——空气流经湿式气体流量计时的温度[K]。
7).对数平均浓度差 (Y)m
(化工原理实验)吸收实验

本实验将介绍吸收实验的目的、原理、吸收塔的介绍,以及操作条件对吸收 效果的影响等内容。同时,还将探讨吸收剂的种类及选择,以及吸收剂的循 环使用方法。
实验步骤
1. 准备实验装置,并确保安全 2. 根据实验要求,执行操作步骤 3. 记录实验过程中的数据和观察结果 4. 对实验结果进行数据处理和误差分析 5. 总结实验结果,并讨论实验的应用和价值
吸收剂的种类及循环使用
物理吸收剂
如水、有机溶剂等。可 以通过循环使用来提高 吸收效率。
化学吸收剂
如酸碱溶液等。通过反 应物不断参与吸收过程, 需要周期性更新。
选择适合的吸收剂
需考虑反应速率、选择 性、价格等因素,以满 足实验或生产的要求。
实验安全注意事项
• 佩戴适当的个人防护装备,如实验服和手套。 • 确保实验室通风良好,以避免有害气体积聚。 • 严格按照实验操作步骤进行,避免潜在的危险。 • 注意化学品的正确使用和储存。
吸收过程的优缺点
• 优点:高效去除有害气体,可实现大规模生产。 • 缺点:操作复杂,消耗能源,产生废液等环境问题。
吸收过程与其他分离技术的比较
分离技术 蒸馏 萃取 结晶
原理
依靠液体的沸点差异进行 分离
利用溶剂对物质的选择性 溶解性
通过物质的溶解度差异实 现分离
适用场景 适用于易挥发物质分离
适用于溶剂可分离的混合物
适用于固溶体或溶剂晶体 分离
吸收剂的再生方法
1
萃取再生
2
通过将吸收剂与合适的溶剂混合,
利用两者的溶解度差异来实现分离
与再生。
3
蒸馏再生
通过加热吸收液体,使其中的溶质 蒸发并收集,再作为吸收剂。
- 1、下载文档前请自行甄别文档内容的完整性,平台不提供额外的编辑、内容补充、找答案等附加服务。
- 2、"仅部分预览"的文档,不可在线预览部分如存在完整性等问题,可反馈申请退款(可完整预览的文档不适用该条件!)。
- 3、如文档侵犯您的权益,请联系客服反馈,我们会尽快为您处理(人工客服工作时间:9:00-18:30)。
精馏实验报告姓名:班级:学号:同组人:实验时间:一、 报告摘要本实验利用乙醇-正丙醇混合物进行精馏,达到分离和提纯的效果。
通过这次实验能进一步掌握精馏的单元操作方式,利用测得的塔板组成数据求出全塔效率和单板效率,从而进一步地加深对精馏操作机理的掌握。
实验中也用到了阿贝折光仪来测算塔板各部位的组成,同过多次使用阿贝折光仪,能进一步熟练对其的使用。
同过实验的操作和数据的处理,我们可以加深对精馏操作的理解,掌握了一项我们化工行业耐以生存的一项基本技能。
二、 实验目的及任务1. 熟悉精馏的工艺流程,掌握精馏实验的操作方法。
2. 了解板式塔的结构,观察塔板上汽-液接触情况。
3. 测定全回流时的全塔效率及单板效率。
4. 测定全塔浓度分布。
5. 测定塔釜再沸器的沸腾给热系数。
三、 实验基本原理在板式精馏塔中,有塔釜产生的蒸汽沿塔逐板上升与来自塔顶逐板下降的回流液,在塔板上实现多次接触,进行传热与传质,使混合液达到一定程度的分离。
回流是精馏操作得以实现的基础。
塔顶回流量与采出量之比,称为回流比。
回流比是精馏操作的重要参数之一,其大小影响着精馏操作的分离效果和能耗。
回流比存在两种极限情况:最小回流比和全回流。
若塔在最小回流比下操作,要完成分离任务。
则需要有无穷多块塔板的精馏塔。
当然,这不符合工业实际,所以最小回流比只是一个操作限度。
若操作处于全回流时,既无任何产物采出,也无原料加入,塔顶的冷凝液全部返回塔中,这在生产中无实验意义。
但是,由于此时所需理论板数最少,又易于达到稳定,故常在工业装置的开停车、排除故障及科学研究时采用。
实际回流比通常取最小回流比的1.2~2.0倍。
在精馏操作中,若回流系统出现故障,操作情况会急剧恶化,分离效果也将恶化。
板效率是体现塔板性能及操作状况的主要参数,有以下两种定义方法。
(1)总板效率EeN E N = (4-25)式中 E —总板效率 N —理论板数; e N —实际板数 (2)单板效率E mln 1nml n 1nx x E x x -*--=- (4-26)式中 E ml —以液相浓度表示的单板效率;x n ,x n-1—第n 块和第(n-1)块板的液相浓度; n x *—第n 块板气相浓度相平衡的液相浓度。
总板效率与单板效率的数值通常由实验测定。
单板相率是评价踏板性能优劣的重要参数。
物系性质、板型及操作负荷是影响单板效率的重要因数。
当物系与板型确定后,可通过改变气液负荷达到最高的板效率;对于不同的板型,可以在保持相同的物系及操作条件下,测定其单板效率,以评价其性能的优劣。
总板效率反映全塔各塔板的平均分离效果,常用于板式塔设计中。
若改变塔釜再沸器中电加热的电压,塔内上升蒸汽量将会改变,同时,塔釜再沸器电热器表面的温度将发生变化,其沸腾给热系数也将发生变化,从而可以得到沸腾给热系数与加热量的关系。
由牛顿冷却定律,可知m Q A t =α∆ (4-27) 式中 Q —加热量,kW;α—沸腾给热系数,kW/(m 2·K ); A —传热面积,m 2;m t ∆—加热器表面与温度主体温度之差若加热器的壁面温度为t s ,塔釜内液体的主体温度为t w ,则式(4-27)可改写成s w Q A(t t )=α- (4-28) 由于塔釜再沸器为直接电加热,则其加热量Q 为2U Q R= (4-29)式中 U —电热器的加热电压,V ; R —电加热器的电阻,Ω。
四、 装置和流程本实验的流程如图4-11所示,主要由精馏塔、回流分配装置及测控系统组成。
图4-11 精馏装置和流程示意1—塔顶冷凝器;2—回流比分配器;3—塔身;4—转子流量计;5—视盅;6—塔釜;7—塔釜加热器;8—控温加热器;9—支座;10—冷凝器;11—原料液罐;12—缓冲罐;13—进料泵;14—塔顶放气阀1.精馏塔精馏塔为筛板塔,全塔共八块踏板,塔身结构尺寸为:塔径φ(57×3.5)mm,塔板间距80mm;溢流管截面积78.5mm2,溢流堰高12mm,底隙高度6mm;每块塔板开有43个直径为1.5mm的小孔,正三角形排列,孔间距为6mm。
为了便于观察塔板上的汽-液接触情况,塔身设有一节玻璃视盅,在第1~6块塔板上均有液相取样口。
蒸馏釜尺寸为φ108mm×4mm×400mm。
塔釜装有液位计、电加热器(1.5kW)、控温电加热器(200W)、温度计接口、测压口和取样口,分别用于观测釜内液面高度,加热料液,控制电加热量,测量塔釜温度,测量塔顶与塔釜的压差和塔釜液取样。
由于本实验所取试样为塔釜液相物料,故塔釜可视为一块理论板。
塔顶冷凝器为一蛇管式换热器,换热面积0.06m2,管外走蒸汽,管内走冷却水。
2.回流分配装置回流分配装置由回流分配器与控制器组成。
控制器由控制仪表和电磁线圈构成。
回流分配器由玻璃制成。
它由一个入口管、两个出口管及引流棒组成。
两个出口管分别用于回流和采出。
引流棒为一根φ4mm的玻璃棒,内部装有铁芯,塔顶冷凝器中的冷凝液顺着引流棒下,在控制器的控制下实现塔顶冷凝器的回流或采出操作。
即当控制器电路接通后,电磁线圈讲引流棒吸起,操作处于采出状态;当控制器电路断路时,电磁线圈不工作,引流棒自然下垂,操作处于回流状态。
此回流分配器即可通过控制器实现手动控制,也可通过计算器实现自动控制。
3.测控系统在本实验中,利用人工智能仪表分别测定塔顶温度、塔釜温度、塔身伴热温度、塔釜加热温度、全塔压降、加热电压、进料温度及回流比等参数,该系统的引入,不仅使实验更为简便、快捷,又可实现计算机在线数据采集与控制。
4.物料浓度分析本实验所采用的体系为乙醇-正丙醇,由于这两种物质的折射率存在差异,且其混合物的质量分数与折射率有良好的线性关系,故可通过阿贝折光仪分析料液的折射率,从而得到浓度。
这种测定方法的特点是方便快捷、操作简单,但精度稍低;若要实现高精度的测量,可利用气相色谱进行浓度分析。
混合料液的折射率与质量分数的关系如下。
25℃D=-m58.21442.017n30℃D=-m58.40542.192n40℃D=-m58.54242.373n式中 m—料液的质量分数;n—料液的折射率(以上数据为实验测得)。
D五、实验操作要点1.对照流程图,先熟悉精馏过程的流程,并搞清仪表柜上按钮与各仪表相对应的设备与测控点。
2.全回流操作时,在原料贮罐中配置乙醇含量20%~25%(摩尔分数)左右的乙醇-正丙醇料液,启动进料泵,向塔中供料至塔釜液面达250~300mm。
3.启动塔釜加热及塔身伴热,观察塔釜、塔身、塔顶温度及塔板上的气液接触状况,发现塔板上有料液时,打开塔顶冷凝器的冷却水控制阀。
4.测定全回流情况下的单板效率和及全塔效率。
在一定回流量下,全回流一段时间,待该塔操作参数稳定后,即可在塔顶、塔釜及相邻两块塔板上取样,用阿贝折光仪进行分析,测取数据(2次)并记录各操作参数。
5.实验完毕后,停止加料,关闭塔釜加热及塔身伴热,待一段时间后,切断塔顶冷凝器及釜液冷却器的供水,切断电源,清理现场。
六、实验数据整理1.实验过程记录首先对精馏塔进行加料,加到合适的液位后,停止加料,启动加热器,把加热电压调到一百左右。
加热后,塔釜温度持续攀升,塔顶温度没有明显变化,全塔压降也在不断升高。
待塔釜温度相对稳定后,塔顶温度开始攀升,全塔压降也在稳定上升。
而后发现塔板上出现料液,打开冷凝器。
而塔板上的液体呈喷射状和泡沫状之间,说明上升蒸汽和下降液体处于一个良好的传质状态。
最后塔釜温度稳定在88℃左右,塔顶温度稳定在79℃左右,全塔压降也稳定在0.9kPa.2.实验数据处理(1)实验原始数据(2)数据处理由式D m 58.54242.373n =-得: 塔顶液相质量分数组成组成D m 58.54242.373 1.35960.846=-⨯= 塔顶液相摩尔组成D D D D m 0.8464646x 0.878m 1m 0.84610.84646604660===--++同理可分别求得塔釜、第4块塔板和第5块塔板的液相摩尔组成: 塔釜液相组成 W x 0.186=第4块塔板的液相组成 4x 0.657= 第5块塔板的液相组成 5x 0.593=90.663 0.799 10 0.844 0.914 111 1将以上数据用相平衡方程xy 1(1)xα=+α-拟合,在Origin 上y-x 关系图,由于本次试验是全回流,操作线为直线y=x ,同样作在y-x 关系图上。
从塔顶浓度D x 开始,用作图法作出阶梯图以求取理论板数,以塔釜浓度Wx 结束。
如图1所示:图1 图解法求理论塔板数由图1可知,总共能作出5个阶梯图,即理论板数为5,而实际板数为8,则可据此求得全塔效率:e N 5E 0.625N 8===由拟合数据可知,相对挥发度α为2.08。
相平衡方程可整理为: nn ny x (1)y =α-α-操作线方程为: n 1n y x +=∴与第5块板气相浓度相平衡的液相浓度 54554y x 0.657x 0.480(1)y (1)x 2.08(2.081)0.657*====α-α-α-α---⨯∴单板效率45ml 45x x 0.6570.593E 0.362x x 0.6570.480*--===--七、 实验结果及结论通过这次实验,我们测得精馏塔的塔顶液相摩尔组成为0.878,塔顶温度为79.2℃;塔釜液相摩尔组成为0.186,塔釜温度为87.8;第4块塔板的液相组成为0.657,第5块板的液相组成为0.593;通过计算得到全塔效率为0.625,单板效率为0.362。
从以上结果可以看出,精馏塔能对原料各组分都进行一定程度的提浓,塔顶的液相组成高,因此塔顶温度接近轻组分的泡点,物料在塔顶能完成对轻组分乙醇的精制;而塔釜则能完成对重组分的精制,塔釜温度接近重组分丙醇的泡点。
而每块塔板则能对物料各组成进行一次提浓。
在全回流的情况下,由于没有进料,精馏塔没有精馏段和提馏段之分,操作线为直线y=x ,所需理论板数最少。
八、 分析与讨论本组实验塔顶液相组成没能超过0.9,塔底组成没有低于0.1,塔板效率偏低,全塔效率不高,说明这次精馏实验无论是从单板的角度还是从全塔的角度,对各组分的提浓都不够充分。
原因可能有一下几点: (1) 气速或液速过快,经过塔板的气体或液体没能经过充分时间的接触就离开塔板,传质不够充分;(2) 塔板的气液接触状态没能达到理想状态,使气液接触不够充分; (3) 操作可能出现一些失误,导致情况恶化; (4) 精馏塔本身提浓能力的局限。
虽然这次实验的结果不太理想,但是我们通过操作基本掌握了精馏这一型基本的单元操作,加深了对精馏机理的理解,也通过这次实验提高了自己发现问题解决问题的能力,希望能吸取这次实验的教训,力争以后做得更好。