橡胶制品产生的气泡原因分析
硅胶产生气泡的原因
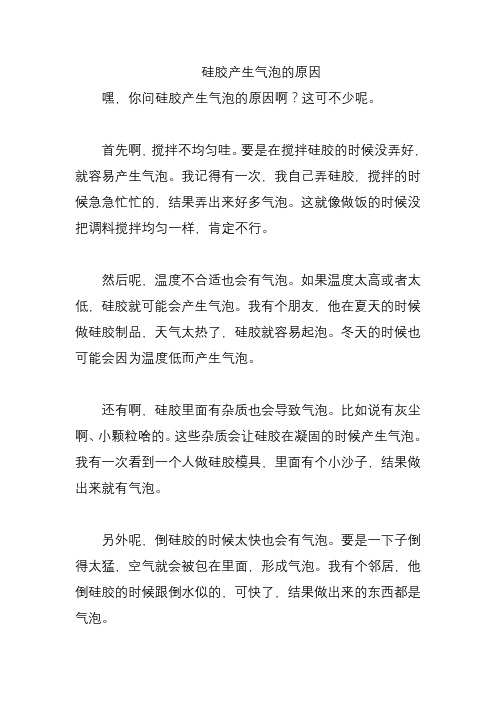
硅胶产生气泡的原因
嘿,你问硅胶产生气泡的原因啊?这可不少呢。
首先啊,搅拌不均匀哇。
要是在搅拌硅胶的时候没弄好,就容易产生气泡。
我记得有一次,我自己弄硅胶,搅拌的时候急急忙忙的,结果弄出来好多气泡。
这就像做饭的时候没把调料搅拌均匀一样,肯定不行。
然后呢,温度不合适也会有气泡。
如果温度太高或者太低,硅胶就可能会产生气泡。
我有个朋友,他在夏天的时候做硅胶制品,天气太热了,硅胶就容易起泡。
冬天的时候也可能会因为温度低而产生气泡。
还有啊,硅胶里面有杂质也会导致气泡。
比如说有灰尘啊、小颗粒啥的。
这些杂质会让硅胶在凝固的时候产生气泡。
我有一次看到一个人做硅胶模具,里面有个小沙子,结果做出来就有气泡。
另外呢,倒硅胶的时候太快也会有气泡。
要是一下子倒得太猛,空气就会被包在里面,形成气泡。
我有个邻居,他倒硅胶的时候跟倒水似的,可快了,结果做出来的东西都是气泡。
还有哦,硅胶的质量也有关系。
如果买的硅胶质量不好,就容易产生气泡。
我有一次买了便宜的硅胶,结果做出来全是气泡,后来换了好一点的硅胶就好了。
我给你讲个事儿吧。
有一次我去一个工厂,看到他们在做硅胶产品。
有一批产品就有很多气泡,后来一检查,发现是搅拌不均匀,温度也有点高。
从那以后,他们就注意这些问题了。
所以啊,硅胶产生气泡的原因有搅拌不均匀、温度不合适、有杂质、倒得太快、质量不好等。
下次你用硅胶的时候,可别犯这些错误哦。
橡胶挤出缺陷的原因
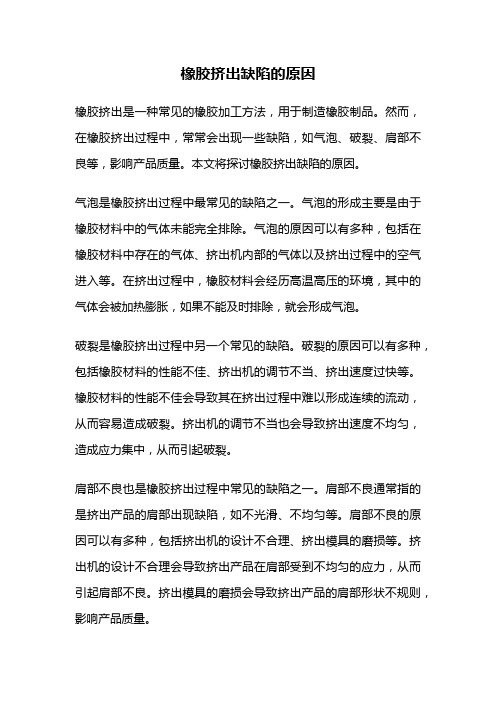
橡胶挤出缺陷的原因橡胶挤出是一种常见的橡胶加工方法,用于制造橡胶制品。
然而,在橡胶挤出过程中,常常会出现一些缺陷,如气泡、破裂、肩部不良等,影响产品质量。
本文将探讨橡胶挤出缺陷的原因。
气泡是橡胶挤出过程中最常见的缺陷之一。
气泡的形成主要是由于橡胶材料中的气体未能完全排除。
气泡的原因可以有多种,包括在橡胶材料中存在的气体、挤出机内部的气体以及挤出过程中的空气进入等。
在挤出过程中,橡胶材料会经历高温高压的环境,其中的气体会被加热膨胀,如果不能及时排除,就会形成气泡。
破裂是橡胶挤出过程中另一个常见的缺陷。
破裂的原因可以有多种,包括橡胶材料的性能不佳、挤出机的调节不当、挤出速度过快等。
橡胶材料的性能不佳会导致其在挤出过程中难以形成连续的流动,从而容易造成破裂。
挤出机的调节不当也会导致挤出速度不均匀,造成应力集中,从而引起破裂。
肩部不良也是橡胶挤出过程中常见的缺陷之一。
肩部不良通常指的是挤出产品的肩部出现缺陷,如不光滑、不均匀等。
肩部不良的原因可以有多种,包括挤出机的设计不合理、挤出模具的磨损等。
挤出机的设计不合理会导致挤出产品在肩部受到不均匀的应力,从而引起肩部不良。
挤出模具的磨损会导致挤出产品的肩部形状不规则,影响产品质量。
除了以上几种常见的缺陷外,还有一些其他缺陷也会在橡胶挤出过程中出现。
例如,表面粗糙、收缩、断面不均匀等。
这些缺陷的形成原因各不相同,但都与橡胶挤出过程中的操作参数、材料性能以及挤出设备的状态有关。
为了避免橡胶挤出过程中的缺陷,可以采取一些措施。
首先,要选择合适的橡胶材料,确保其性能符合产品要求。
其次,要合理调节挤出机的操作参数,如温度、压力、速度等,以保证橡胶材料能够均匀流动。
此外,还需要定期检查和维护挤出设备,确保其状态良好。
橡胶挤出缺陷的原因包括气泡、破裂、肩部不良等。
这些缺陷的形成与橡胶材料的性能、挤出机的调节、挤出过程的操作等有关。
为了避免这些缺陷的出现,可以采取合适的措施,如选择合适的橡胶材料、合理调节挤出机的操作参数以及定期检查和维护挤出设备。
注塑常见缺陷和原因分析
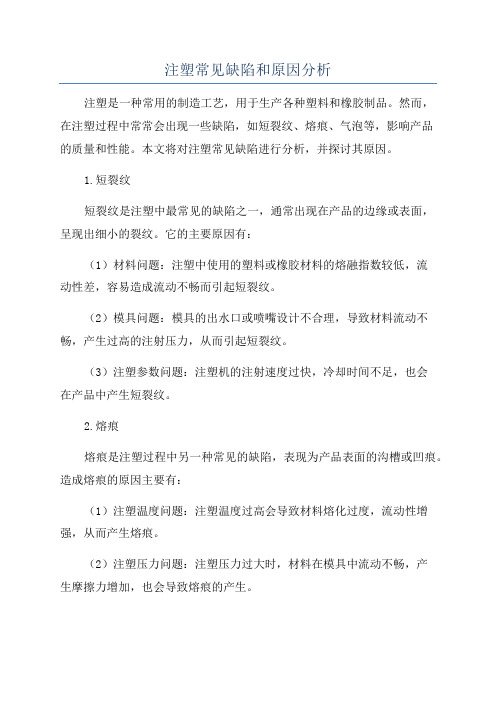
注塑常见缺陷和原因分析注塑是一种常用的制造工艺,用于生产各种塑料和橡胶制品。
然而,在注塑过程中常常会出现一些缺陷,如短裂纹、熔痕、气泡等,影响产品的质量和性能。
本文将对注塑常见缺陷进行分析,并探讨其原因。
1.短裂纹短裂纹是注塑中最常见的缺陷之一,通常出现在产品的边缘或表面,呈现出细小的裂纹。
它的主要原因有:(1)材料问题:注塑中使用的塑料或橡胶材料的熔融指数较低,流动性差,容易造成流动不畅而引起短裂纹。
(2)模具问题:模具的出水口或喷嘴设计不合理,导致材料流动不畅,产生过高的注射压力,从而引起短裂纹。
(3)注塑参数问题:注塑机的注射速度过快,冷却时间不足,也会在产品中产生短裂纹。
2.熔痕熔痕是注塑过程中另一种常见的缺陷,表现为产品表面的沟槽或凹痕。
造成熔痕的原因主要有:(1)注塑温度问题:注塑温度过高会导致材料熔化过度,流动性增强,从而产生熔痕。
(2)注塑压力问题:注塑压力过大时,材料在模具中流动不畅,产生摩擦力增加,也会导致熔痕的产生。
(3)模具设计问题:如果模具中的出水口或喷嘴设计不合理,也会在产品表面形成熔痕。
3.气泡气泡是注塑中常见的缺陷,表现为产品内部或表面的空腔。
气泡的形成原因有:(1)材料问题:注塑材料中含有过多的水分或挥发性物质,注塑过程中被加热蒸发,生成气泡。
(2)注塑温度过高:高温会导致材料熔化过度,容易产生气泡。
(3)注塑压力问题:过高的注塑压力会使材料在注塑过程中产生剧烈的振动,从而引起气泡。
(4)模具问题:模具中存在堵塞或不良的冷却系统,也会导致气泡的产生。
4.缩短问题缩短是指产品在冷却过程中出现尺寸缩小的现象。
产生缩短的主要原因有:(1)注塑温度过低:低温会使注塑材料的熔融程度不足,流动性降低,产生缩短。
(2)冷却时间不足:注塑材料冷却时间不足会导致产品未完全固化,容易产生缩短。
(3)注塑压力问题:过大的注塑压力会使产品产生内部的应力,引起尺寸缩小。
(4)模具问题:模具中存在过多的冷却系统,会导致材料过度冷却而使产品缩短。
橡胶产品基本缺陷产生原因及解决措施

浇口设计不合理
浇口设计不合理,导致充型困难或产 生气孔等缺陷。
模具加工精度低
模具加工精度不高
导致模具配合不良,出现飞边、 溢料等问题。
模具表面粗糙
模具表面粗糙导致制品表面质量差 。
模具材料不当
使用不当材料制作模具,导致制品 不符合要求。
设备性能不良
注射机精度不高
注射机精度不高,导致注射不稳 定,制品出现气泡、银纹等缺陷
配方比例不当
橡胶配方中各种原材料的 比例不当,会影响橡胶产 品的性能。
配方设计不合理
硫化体系不合理
硫化体系是橡胶配方设计 的重要部分,硫化剂、促 进剂等配比不当,会影响 橡胶产品的性能。
补强体系不合理
补强剂的种类和用量不当 ,会影响橡胶产品的强度 和耐磨性等性能。
增塑体系不合理
增塑剂的种类和用量不当 ,会影响橡胶产品的柔软 度和耐寒性等性能。
建立完善的设备维护和保养制度 ,定期对设备进行检查、维修和
更换。
保持生产环境的清洁和卫生,减 少污染和杂质对产品质量的影响
。
加强产品使用及环境监控
对产品使用进行严格的监管和控制,避免滥用和误用。 对产品使用环境进行评估和监控,确保其符合产品要求。
建立完善的质量检测和监控体系,对产品进行定期检查和测试。
压力不均
总结词
压力不均是指在橡胶加工过程中,压力 分布不均匀,导致橡胶制品出现鼓包、 厚度不均等问题。
VS
详细描述
压力不均的原因包括模具设计不合理、压 力控制不稳定、注射速度过快或过慢等。 此缺陷会导致橡胶制品形状变形、精度降 低,影响使用性能和外观质量。
时间控制不当
总结词
时间控制不当是指在橡胶加工过程中,时间控制过长或过短,导致橡胶制品出现老化、不耐用等问题。
橡胶产品表面有气泡的原因分析

橡胶产品表面有气泡的原因分析橡胶硫化后样品表面总是有些气泡,大小不等,切开后,样品中间也有少数气泡。
橡胶产品表面有气泡的原因分析
1、橡胶混炼不均匀,操作工不规范。
2、橡胶胶片停放不规范,环境不卫生。
管理不规范。
3、材料有水份(混炼时加点氧化钙)
4、硫化不充分,不熟看起来有气泡。
5、硫化压力不足。
6、硫化剂杂质较多,小分子的杂质提前变成分解,气泡残留制品中
7、模具本身排气设计不合理,胶料冲线时气不能及时排出!
8. 制品太厚,胶料过少,橡胶传热慢,外表硫化后,橡胶流动性下降,造成缺料,所以就可能产生气泡。
9.硫化过程中排气没排好。
10、配方问题,硫化体系要改善。
解决办法:
在硫化压力和时间上加以改善
1、延长硫化时间或提高硫化速度。
2、硫化前薄通几次。
3、硫化时排气次数多一点。
—1 —。
橡胶产品基本缺陷产生原因及解决措施

•引言•橡胶产品常见缺陷概述•产生缺陷的原因分析•解决措施及建议目•案例分析与应用•结论与展望录背景介绍本文旨在分析橡胶产品生产过程中可能出现的缺陷及其产生原因,并提出相应的解决措施。
这有助于提高产品质量、降低生产成本、增强市场竞争力,同时保障使用安全。
通过深入探讨和研究,我们将更好地了解橡胶产品的性能和特点,为进一步优化其生产工艺和提高产品质量提供理论支持和实践指导。
目的和意义原因原材料中含有水分或挥发性物质硫化过程中产生的气体未完全排胶料混合不均匀或炼胶时间过长解决措施确保原材料干燥、无挥发性物质优化硫化工艺,增加排气时间控制炼胶时间和温度,确保胶料混合均匀原因橡胶老化或劣化应力集中或外部应力作用02030102030430102 030102橡胶硬度不均优化橡胶制品结构设计,确保厚度均匀和稳定性橡胶材料质量差配合剂问题填充剂问题030201材料因素加工工艺不合理模具设计不当设备问题人员操作问题材料选择与控制是解决橡胶产品基本缺陷的重要手段之一。
详细描述应基于产品的性能要求和工艺条件,选择适宜的橡胶材料,并严格控制其成分和性能指标,避免因材料问题而导致缺陷的产生。
对于重要的橡胶部件,可以考虑添加适量的增塑剂、补强剂、抗氧剂等助剂,以改善其加工性能和耐久性。
总结词材料选择与控制VS工艺优化及改进总结词详细描述其他措施和建议总结词详细描述针对以上原因,可以采取以下措施:严格控制原材料的质量和配方;适当延长硫化时间;优化模具设计,确保模具排气顺畅。
案例一:某橡胶密封圈的气泡问题解决措施解决措施原因原因橡胶轮胎出现龟裂可能是由于原材料质量问题、硫化时间不当、氧化老化、使用环境恶劣等因素导致的。
要点一要点二解决措施为改善橡胶轮胎的龟裂问题,可以采取以下措施:严格把控原材料的质量和配方;合理调整硫化时间;加强生产过程中的质量控制和老化试验;提高产品的抗老化性能和使用寿命;同时,在使用过程中定期检查和维护。
PVC胶产生气泡的原因及控制措施

PVC胶产生气泡的原因及控制措施
首先,材料的问题是引起PVC胶产生气泡的主要原因之一、PVC材料
中可能含有水分、溶剂、挥发物等揮發性物质,在胶料制备过程中,这些
物质会释放出来,产生气泡。
此外,如果使用的PVC材料本身质量不过关,可能会含有较多的杂质,这些杂质在加工过程中也会形成气泡。
其次,工艺问题也是导致PVC胶产生气泡的原因之一、例如,当工作
温度过高时,胶料中的挥发物会挥发得更快,导致产生气泡的概率增加。
此外,如果搅拌不充分,胶料中的杂质无法得到均匀分散,也容易形成气泡。
为了控制PVC胶产生气泡,可以考虑以下措施:
1.优化材料选择:选用质量可靠的PVC材料,减少杂质的含量,降低
材料中挥发性物质的含量。
慎重选择添加剂,并确保其质量可靠。
2.控制工艺参数:合理控制胶料的加工温度和时间,避免过高的温度,适当延长加工时间,确保材料充分熔融,挥发物释放均匀。
3.充分搅拌:确保胶料在制备过程中充分搅拌,使其内部的杂质得到
均匀分散,减少气泡产生的可能性。
4.提高工作环境的控制:尽量控制制备PVC胶的工作环境中的湿度,
避免湿气进入胶料中引起气泡。
保持相对稳定的温湿度,符合制备要求。
5.完善包装条件:在包装过程中,尽量避免产生气泡过程,并采取措
施确保胶料包装密封,防止外界湿气和杂质污染导致密封措施破裂。
总之,对于PVC胶产生气泡的原因和控制措施,需要从材料的选择、工艺参数的控制以及工作环境的管理等多个方面进行综合考虑和改进,以减少气泡产生,提高产品的质量。
硅胶 低温 气泡

硅胶低温气泡
硅胶在低温下可能会产生气泡,主要原因有以下几点:
1.排气不足:在硅胶原料放置于成型模具后,如果排气处理不当,可能导致空气被困在硅胶原料中,从而在成型后产生气泡。
2.硫化温度过低:硫化温度是硅橡胶成型的重要参数,通常设定在160~200℃。
但当硫化温度过低时,会导致成型时间延长,硅胶在未完全硫化的情况下易产生气泡。
3.硫化温度过高:过高的硫化温度可能使硅胶原料在成型过程中就开始硬化,导致空气被困在硅胶原料中,从而产生气泡。
4.硫化时间过短:硫化时间的长短决定了硅胶能否被完全硫化,时间过短可能导致部分硅胶未完全硫化,从而产生气泡。
5.配合剂问题:某些配合剂,特别是增塑剂(包括软化剂),在硅胶中可能会产生气泡。
这是因为这些配合剂含有低温挥发物和水份,当温度升高时,这些物质可能会挥发或产生气体,导致硅胶中出现气泡。
为了减少硅胶中的气泡,可以采取以下措施:
1.优化模具设计,使模具具有合理的气孔位置和足够的排气孔数,以及保证胶料在模具中能均匀受热受压。
2.控制硫化温度和时间,使其达到最佳的硫化状态。
3.控制填料的粒径和添加量,减少填料与其它组分产生
的化学反应。
4.避免使用含有易挥发物质或易产生气体的配合剂。
5.在生产过程中加强操作和管理,避免混入杂质或空
气。
6.对于已经产生气泡的硅胶制品,可以通过后处理如热
处理、真空处理等方式来减少气泡。
总之,要减少硅胶中的气泡,需要从原料、配方、生产工艺和设备等方面进行综合考虑和优化。
- 1、下载文档前请自行甄别文档内容的完整性,平台不提供额外的编辑、内容补充、找答案等附加服务。
- 2、"仅部分预览"的文档,不可在线预览部分如存在完整性等问题,可反馈申请退款(可完整预览的文档不适用该条件!)。
- 3、如文档侵犯您的权益,请联系客服反馈,我们会尽快为您处理(人工客服工作时间:9:00-18:30)。
一、模压制品产生气泡的原因分析:
主要原因有:
1、材料的问题,橡胶材料来混炼、储存、使用过程中有湿气,湿气未排除,导致产生气泡,或天气变化原因受潮。
大多数原因可能是原材料有问题,我们以前也出现过类似情况,换另外一个批次材料就好了;
2、模具排气孔设置不当或者堵塞也会产生气泡,排气的时候没有排好。
原材料在炼胶中,空气被裹附在材料内部,导致在加工的过程中,材料和空气一起进入模具,假如模具没加排气槽或加工中没有设置排气工艺的话,空气很容易被困在模具里面,使得产品产生气泡或气孔。
3、生产橡胶制品,硫化后有气泡,可能是橡胶配方中的问题,可以找技术人家给调整一下配方。
二、橡胶制品硫化时有气泡原因
1、橡胶混炼不均匀,操作工不规范。
2、橡胶胶片停放不规范,环境不卫生。
管理不规范。
3、材料有水份(混炼时加点氧化钙)
4、硫化不充分,不熟看起来有气泡。
5、硫化压力不足。
6、硫化剂杂质较多,小分子的杂质提前变成分解,气泡残留制品中
7、模具本身排气设计不合理,胶料冲线时气不能及时排出!
8. 制品太厚,胶料过少,橡胶传热慢,外表硫化后,橡胶流动性下降,造成缺料,所以就可能产生气泡。
9.硫化过程中排气没排好。
10、配方问题,硫化体系要改善。
解决办法:在硫化压力和时间上加以改善
1、延长硫化时间或提高硫化速度。
2、硫化前薄通几次。
3、硫化时排气次数多一点。
三、橡胶产品表面有气泡的原因分析
1.有水份(混炼时加点氧化钙);
2.未充分硫化,不熟看起来有气泡;
3.硫化剂杂质较多,小分子的杂质提前变成分解,气泡残留制品中;
4.模具本身排气设计不合理,胶料冲线时气不能及时排出;
5.分散不良;
6.胶料塑炼时间长,产品硫化时也有气泡。
四、硅胶成型产生气泡是什么原因呢?
1、排气不足,硅胶原料放置于成型模具后,在合模的瞬间会带入许多空气,而空气是不可能与硅胶原料融为一体的,如果没有将这些空气排放出来,就会造成硅胶按键成型后表面产生气泡。
2、硫化温度过低,硫化温度是硅橡胶成型时的一项重要参数,通常的硅胶制品都设定在160~200摄氏度,但有时候由于模外操作时间太长或其他原因使模具长时间未开入硫化机加温,导致硅胶成型模具的温度偏低与硅胶的硫化温度,此时就会造成成型后产品气泡。
对此我们只需加高成型温度,或者将空模开入机器加温一段时间在操作即可解决问题了。
3、硫化温度过高,刚刚说了硫化温度过低会造成硅胶成型气泡,其实,很多时候成型温度过高同样会造成硅胶成型气泡。
为什么呢?个人是这么理解的,成型温度过高时,在合模加压的过程中表面的硅胶原料已经开始成型,此时的空气已经被困在里面很难排出,所以会造成成型气泡。
针对此原因,只需将成型温度适当降低即可。
4、硫化时间过短,跟硫化温度一样,硫化时间也是硅胶成型的重要参数之一,硫化时间的长短决定了硅胶是否能被完全硫化。
如果硫化时间过短,不仅造成硅胶成型后发软,更容易造成表面气泡。
出现此类不良可适当延长硅胶的硫化时间。
5、模具的结构不合理,硅胶成型模具的设计不太合理也会造成硅胶成型产生气泡,例如模具中产品的排列方式、分区方式、模具分模方式,模具大小的设计等都会造成气泡不良,但开一套模具的成本很高,且修改起来也不太容易,如果因为模具的结构造成硅胶成型气泡,那么通常都是从上面所提到的几点想办法下手解决。
公司简介
佛山市南方橡塑有限公司成立于1986年,是一家从事研发和生产橡胶制品的技术型的生产企业,主要生产各类:橡胶模压制品、橡胶挤出制品、橡胶发泡制品、热塑性弹性体制品、软性PVC挤出制品、热塑性弹性体制品、密封条、硅胶管、发泡管、发泡条、EPDM胶条、橡胶管、橡胶挤出制品、橡胶发泡制品、密封圈、硅胶板等产品。
本公司是获得ISO9001:2000质量管理体系认证的生产研发型企业,为保证我们公司所生产的产品符合客户对原料到生产以及出货等环节的环保与技术要求(RoHS,FDA,UL等),公司对生产设备与产品研发技术、检测等部门的设备进行不断更新升级;为实现与配合客户产品的研发与功能的完善,公司独立设置了工程研发部门并为其配备了独立的产品设计开发实验室,独立的模具制作部门、配方试制室、理化试验室、模拟运输试验室、模拟生产实验室等,因此很多国内外客户选择我们公司成为他们的合作伙伴。
生产部门设备有油压橡胶硫化机、橡胶、橡塑挤出机及其连续硫化和连续生产线、试制和生产使用的开放式炼胶机、密封式炼胶机、模具制造专用的车床、铣床、磨床以及火花机等。
检测部门设备有拉力试验机、热空气老化试验箱、高温试验箱、火花试验机、耐电压测试仪、直流双臂电桥、投影仪、百分厚度计、邵尔硬度计、快速可塑测试机、阿克隆磨耗试验机、读数显微镜以及振台等。
检测部门设备有拉力试验机、热空气老化试验箱、高温试验箱、火花试验机、
耐电压测试仪、直流双臂电桥、投影仪、百分厚度计、邵尔硬度计、快速可塑测试机、阿克隆磨耗试验机、读数显微镜以及振台等。
(欢迎广大C新老客户来电、来邮、来图、来样定做各类橡胶橡塑制品,我们竭诚为您提供优质的产品和服务。
)我们将歇尽所能为客户提供质量放心和有保障的优质产品和服务!。