凸凹模固定板加工工艺过程
冲裁模(冲压模具)课程设计 说明书

弓形连接固定片复合模设计零件名称:弓形连接固定片生产批量:中批量材料:零件材料为08钢,厚度为1.5mm图1-1一、零件工艺性分析弓形双孔连接固定块片是家用发电风扇中的一连接固定零件,零件的精度要求较低,具有较高的强度和刚度。
外形最大尺寸为70mm,属于小型零件。
该零件应中批量生产,外精度不高,只需平整,外轮廓是该零件需要保证的重点。
该零件用到的冲压工序有冲孔、落料,因此可设计冲孔落料复合模生产此零件。
二、工序设计及工艺计算1、排样毛坯最大尺寸70mm,不算太小,为保证冲裁件的质量,模具寿命和操作方便,采用有搭边,单排排样,如下图2-1所示,冲裁件之间的搭边值a=1.5mm,冲裁件与条料件侧边之间的搭边值a=2.3mm。
1图2-1-1计算条料的宽度:B=70+2×2.3+c=74.7(mm)其中c为调料可能的摆动量,c=0.1mm计算条料的步距:A=20+1.5=21.5(mm)图2-1-2一个步距内材料的材料利用率:η=985.182/(74.7*21.5)×100%= 61.34%2、压力中心确定和压力机的选择(1)、冲裁力的计算冲裁力 F p=Lt σb Kp (2-2-1) 其中:由图2-2知,周长L=213.057mm;=900Mpa, 此时,Kp=1,则:材料:08F钢板,查表,σbFp=213.057X1X900X1=191.75(kN) (2-2-2) 根据以上模具结构类型,采用弹性卸料和漏料出件,卸料力F q=KF,取K=0.05,则:F q =0.05×191.75=9.59(kN) (2-2-3)推料力Fq1=nK1Fp,去凹模刃壁垂直部分高度h=5mm,t=1mm,n=5/1=5;取K1=0.06,则:F q1=5X0.06X191.75=57.53(kN) (2-2-4)顶件力Fq2=K2Fp,K2=0.06,则:Fq2=0.06X191.75=11.51 (kN) (2-2-5) 本套模具用到的由压力机提供的有冲裁力和推料力,因此:总冲压力F=FP+ F q1总=191.75+57.53=249.28(kN) (2-2-6) (2)、压力中心的确定压力中心在两小圆垂直中心线上(3)、压力机的选择,取系数为1.3,则选用的压力机公称压力P≥(1.1~1.3) F总=1.3×249.28=324(kN)P≥1.3F总初选压力机公称吨位为400kN,型号为J23-40,其主要工艺参数如下:公称压力:400KN;滑块行程:100mm;行程次数:80次∕分;最大闭合高度:300mm;最大装模高度:220mm;闭合高度调节量:80mm;工作台尺寸(前后×左右):150mm×300mm;模柄孔尺寸:直径50mm,深度70mm;工作垫板:厚度80mm,孔径200mm;电动机功率:1.5kW。
带凸缘拉伸件

带凸缘拉深件模具设计摘要拉深是利用模具使平板毛坯变成为开口的空心零件的冲压方法,用拉深工艺可以制成筒形、阶梯形、锥形、抛物面形、盒形和其他不规则形状的薄壁零件,其中又以筒形件简单和多见,而有凸缘筒形件又分为宽凸缘和窄凸缘件。
只有加强拉深变形基础理论的研究,才能提供更加准确、实用、方便的计算方法,才能正确地确定拉深工艺参数和模具工作部分的几何形状与尺寸,解决拉深变形中出现的各种实际问题,从而,进一步提高制件质量。
在拉深工艺设计时,必须知道冲压件能否一次拉出,这就引出了拉深系数的概念。
拉伸系数决定于每次拉深时允许的极限变形程度。
在多次拉深中,对于宽凸缘拉深件,则应在第一次拉深时,就拉成;零件所要求的凸缘直径,而在以后各次拉深中,凸缘直径保持不变。
为了保证以后拉深时凸缘不变形,宽凸缘拉深件首次拉入凹模的材料应比零件最后拉深部分实际所需材料多3%~5%,这些多余材料在以后各次拉深中,逐渐将减少部分材料挤回到凸缘部分,使凸缘增厚,从而避免拉裂。
关键词:筒形,模具设计,拉深,冲压AbstractThe extension is a mould to make the plate blank into the stamping method for hollow parts of the opening, thin-walled parts with deep drawing process can be made into a cylinder shape, ladder shaped, cone, parabolic, box and other irregular shapes, and the case of cylindrical parts simple and rare, and flange cylindrical parts is divided into wide flange and narrow flange.Only by strengthening the basic theory research of deformation calculation method of drawing, can provide more accurate, practical and convenient, can correctly determine the geometry and size of drawing process parameters and working parts of die, to solve the actual problems, drawing deformation in order to further improve the quality of workpieces.In the process design of deep drawing, must know whether a stamping out, this leads to the concept of drawing coefficient. Limit drawing coefficient depends on each drawing the allowable deformation degree. Many in the drawing, for wide flange drawing parts, should be in the first drawing, pull into; the diameter of the flange parts required, and after each time depth, the diameter of the flange remain unchanged. In order to ensure the flange without deformation after drawing, wide flange drawing parts for the first time into the die material should be better than the last part of the actual parts drawing materials needed for multiple 3%~5%, these extra materials after various times of deep, gradually will reduce part material out back to the flange portion, the flange thickened, so as to avoid cracking.Keywords: cylinder, mold design, drawing, stamping目录摘要 (I)Abstract (II)前言 (1)第1章加工零件的工艺分析 (3)零件分析 (3)冲压件的工艺分析 (3)制定冲压工艺方案 (4)第2章模具总体设计 (6)模具类型的选择 (6)操作方式 (6)卸料、出件方式 (6)卸料方式 (6)出件方式 (6)第3章模具设计计算 (7)工艺参数的确定及计算 (7)确定拉伸次数 (7)排样及材料的利用率 (8)排样方法 (8)材料的利用率 (9)第4章冲压模具设计 (9)确定冲压类型及结构形式 (9)计算工序压力、选择压力机 (9)落料力 (9)卸料力 (9)拉伸力 (9)压边力 (10). 计算模具压力中心 (10). 计算模具零件主要工作部分刃口尺寸 (11)第5章模具零件的选用 (12)模架的选择 (12)冲压设备的选用 (12)第6章模具制造技术要求 (13)表面粗糙度及标准 (13)配合要求 (14)第7章编写技术条件 (15)第8章设计并绘制模具总装图及选取标准件 (17)毕业设计小结 (17)结论 (18)参考文献 (20)前言冲压模具在实际工业生产中应用广泛。
冷冲压模具装配工艺规范

冷冲压模具装配工艺规范操作者必须受过冲压模具装配的专业培训,并通过专业考核合格取得上岗证后,才有资格进行冲压模具装配,在模具装配的过程中,必须遵守以下规程:一、技术要求:.装配好的模具其外形尺寸应符合图纸规定的要求;.上模座的上平面与下模座的底面必须平衡,一般要求在长度上误差不大于上模沿导柱上下滑动应平稳、灵活、无阻滞。
.凸模和凹模的配合间隙应符合图纸要求,周围间隙应均匀一致;凸凹模的工作行程应符合技术要求;.对于圆孔凹模,在钻线切割工艺孔时,应一并将漏料孔钻出(若有因工艺问题不能预先钻出,则按工艺要求执行);装配好的模具,落料孔或出屑槽应畅通无阻,保证制件或废料能自由排出;.模柄的圆柱部分应与上模座上平面垂直;.导柱和导套之间的相对滑动平稳而均匀,无歪斜和阻滞现象;.钻孔、铰孔、攻丝的技术要求:1)对需进行镗削加工的精密孔,在其预孔时应按下表留取镗削余量;2)作固定销孔时,应按如下的要求执行:①程序:先钻预孔(留~余量),然后扩孔(留~余量);最后铰削至所需的孔径要求(包括精度和粗糙度)。
②原则:a.对于定位要求较高的模具(如两器端板冲孔切角模),其固定销孔钻,扩后应采用手工铰出,以保证精度要求;对于其它模具,可采用机铰方式铰出,但应选择合适的加工参数;. 对于淬硬件的固定孔,应在淬硬前在相应的位置上个铰预配镶件(材料钢)装上,然后再在镶件上制出销孔(要保证对中)。
.各零件外形棱边(工作棱边除外)及销孔,螺钉沉孔必须倒角;.冲裁模具,其凸凹模具在装配前必须先用油石进行修磨;.各种附件应按图纸要求装配齐备;.模具在压力机上的安装尺寸需符合选用设备的要求,起吊零件安全可靠;.模具应在生产的条件下试模,试模所得制件应符合工序图要求,并能稳定地冲出合格的制件。
二、装配程序:.装配前必须仔细分析研究图纸,根据模具的结构特点和技术要求,确定合理的装配程序和装配方法。
.装配前须认真按图检查模具零件的加工质量,合格的投入装配,不合格返工或重制。
冲裁弯曲拉深设计案例DOC
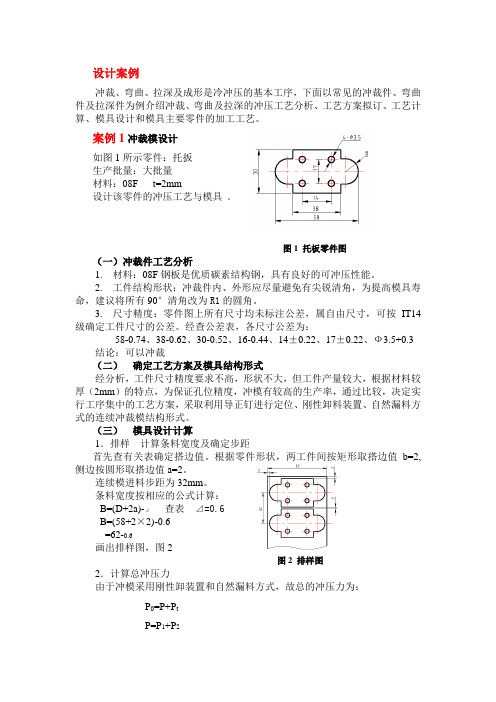
设计案例冲裁、弯曲、拉深及成形是冷冲压的基本工序,下面以常见的冲裁件、弯曲件及拉深件为例介绍冲裁、弯曲及拉深的冲压工艺分析、工艺方案拟订、工艺计算、模具设计和模具主要零件的加工工艺。
案例1冲裁模设计如图1所示零件:托扳生产批量:大批量材料:08F t=2mm设计该零件的冲压工艺与模具。
图1 托板零件图(一)冲裁件工艺分析1. 材料:08F钢板是优质碳素结构钢,具有良好的可冲压性能。
2. 工件结构形状:冲裁件内、外形应尽量避免有尖锐清角,为提高模具寿命,建议将所有90°清角改为R1的圆角。
3. 尺寸精度:零件图上所有尺寸均未标注公差,属自由尺寸,可按IT14级确定工件尺寸的公差。
经查公差表,各尺寸公差为:58-0.74、38-0.62、30-0.52、16-0.44、14±0.22、17±0.22、Ф3.5+0.3 结论:可以冲裁(二)确定工艺方案及模具结构形式经分析,工件尺寸精度要求不高,形状不大,但工件产量较大,根据材料较厚(2mm)的特点,为保证孔位精度,冲模有较高的生产率,通过比较,决定实行工序集中的工艺方案,采取利用导正钉进行定位、刚性卸料装置、自然漏料方式的连续冲裁模结构形式。
(三)模具设计计算1.排样计算条料宽度及确定步距首先查有关表确定搭边值。
根据零件形状,两工件间按矩形取搭边值b=2,侧边按圆形取搭边值a=2。
连续模进料步距为32mm。
条料宽度按相应的公式计算:B=(D+2a)-⊿查表⊿=0.6B=(58+2×2)-0.6=62-0.6画出排样图,图2图2 排样图2.计算总冲压力由于冲模采用刚性卸装置和自然漏料方式,故总的冲压力为:P0=P+P tP=P1+P2而式中 P 1--------落料时的冲裁力P 2--------冲孔时的冲裁力 按推料力公式计算冲裁力:P 1=KL t τ 查τ=300MPa=2.2[2(58-16)+2(30-16)+16π]*2*300/10000 =12.6 (t )P 2=2.2*4π*3.5*2*300/10000 =3.4(t)按推料力公式计算推料力P t :P t =nK t P 取n=3,查表2-10,K t =0.055 P t =3*0.055*(12.6+304)=2.475(t) 计算总冲压力P Z : P Z =P 1+P 2+P t=12.6+3.4+2.475 =18.475(t)3.确定压力中心:根据图3分析,因为工件图形对称,故落料时P 1的压力中心在O 1上;冲孔时P 2的压力中心在O 2上。
镶拼式结构的凸、凹模的固定方法

镶拼式结构的凸、凹模的固定方法有哪些?各适用于哪些场合?形状复杂和大型的凹模与凸模选择镶拼结构,可以获得良好的工艺性,局部损坏更换方便,还能节约优质钢材,对大型模具可以解决锻造困难和热处理设备及变形的问题,因此被广泛采用。
镶拼式凸、凹模的固定方法主要有:平面固定法,嵌入固定法、压入固定法、斜楔固定法及低熔点合金固定法。
(1)平面固定法这种方法是把拼好的镶块,用销钉和螺钉直接在模板上定位和固定,其结构形式如图1所示。
图a、b所示结构用销钉定位,螺钉固定,用于冲裁件厚度小于1.5mm的大型凸、凹模;图c所示结构用销钉定位,螺钉加上止推键将拼块固定在模板上,用于冲裁件厚度为1.5~2.5mm的大型冲模;图d所示结构利用销钉、螺钉将镶拼的凸、凹模固定在模板的凹槽内,止推强度更大,用于冲裁件厚度大于2.5皿大型冲模的固定;图6;用螺钉固定,适用于大型圆凸模;图纟适用于大型剪切凸模;图g适用于孔距尺寸很小的多排矩形孔的冲裁凸模。
图1 镶拼式凸、凹模平面固定结构形式1—凹模镶块 2—螺钉 3—销钉 4—模板 5—止推键 6—凸模镶块(2)嵌入固定法这种方法是把拼合的镶块嵌人两边或四周都有凸台的模板槽内定位,采用基轴制过渡配合K7/h6,然后用螺钉、销钉或垫片与禊块(或键)紧固,如图2所示。
图a为螺钉固定嵌人结构;图b为用垫片嵌入固定结构;图c为楔块、螺钉固定嵌入结构。
这类结构侧向承载能力较强,主要用于中、小型凸、凹模的固定。
图2 嵌人式镶拼固定法a)螺钉、销钉固定 b)垫片嵌人固定 c)楔块螺钉固定(3)压入固定法这种方法是将拼合的凸、凹模,以过盈配合U8/h7压人固定板孔或模板槽内固定,如图3 所示,适用于形状复杂的小型冲模以及拼块较小不宜用螺钉、销钉紧固的情况。
图3 压入式镶拼(4)斜楔固定法这种方法主要是采用斜楔紧固拼块,如图4所示。
其特点是装拆、调整较方便,凹模因磨损间隙增大时,可将其中一块拼合面磨去少许,使其恢复正常间隙。
模具设计制造及验收技术要求

技术协议附件三模具设计制造及验收技术要求1.大体技术条件1.1.模具设计的大体技术条件1.1.1.工法图设计和模具结构设计必需按用户确认的《钣金件模具设计标准》及提供的《冲压设备技术参数》和冲压生产布线要求。
用户将对冲压工艺方案、冲压设备选用情形、模具结构方案进行认可性会签。
1.1.2.所需卖方开发模具的零件:W=2490车身的驾驶室总成(包括仪表板总成和流水槽)、需要制作弯曲成形类模具的型材和前保险杠总成等与驾驶室同时过油漆线的零件。
1.1.3.按A级标准开发模具的钣金件是:全数外覆盖件(包括:左/右车门外板、前保险杠、顶盖、左/右后侧围外板、左/右前柱外板和后围外板等)、大型或复杂钣金件(包括:后围内板、左/右车门内板、左/右边围内板、地板鼓包等)、t≥的厚板料钣金件(包括:左/右前纵梁、左右后纵梁等);其余钣金件、滚压件和型材按B级标准开发模具。
1.1.4.卖方提供给用户的模具冲出制件的材料利用率必需达到车门为70%,地板为90%,平均为80%以上。
如卖方在冲压工艺要领图设计时,如有发觉材料利用率不能达到要求时,应进行CAE分析,提供出科学准确的材料利用率数据供用户确认。
1.1.5.模具工作部份的材料选用原那么及热处置要求:1.1.6.模具的安装应方便快捷,中大型模具采纳托杆快速定位,应能利用快速安装夹紧装置。
1.1.7.所有模具应考虑得手工操作的平安合理性(如:良好的视野,足够的操作空间和操作区域),便于操作、维修、搬运与寄存,坯件的送进掏出方便,坯件的定位靠得住,废料的排出平安通畅;模具的零部件应考虑防松、防崩、防脱落、防冲击等方法;活动零部件应有平安方法,应有行程限位器、寄存限位器、平安块、防护板、防护罩等。
1.1.8.模具的导柱均安装在下模座上,模具的起重和翻转应在设计时考虑。
1.1.9.模具的气动接头采纳快换接头,接头的安放位置及尺寸规格与压机匹配,并应备有堵塞和换向阀及调压阀;接头插座的顺序排列为定位装置升起、下降、托料装置升起、下降。
冲压模具设计全套步骤和流程总算是弄明白了

冲压模具设计全套步骤和流程总算是弄明白了一起探讨,一起学习,一起进步。
大家的每一次点赞,每一次评论,每一次转发。
都是我创作的动力,期待你的加入一、取得必要的资料根据相关资料分析共建的冲压工艺性,对工件进行工艺审核及标准化审核。
1)取得注明具体技术要求的产品零件图样。
了解工件的形状、尺寸与精度要求。
关键孔的尺寸(大小和位置),关键表面,分析并确定工件的基准面。
其实,冲压件的各项工艺性要求并不是绝对的。
尤其在当前冲压技术迅速发展的情况下,根据生产实际的需要和可能,综合应用各种冲压技术,合理选择冲压方法,正确进行冲压工艺的制定和模具结构的选择,使之既满足产品的技术要求,又符合冲压工艺的条件。
2)收集工件加工的工艺过程卡片。
由此可研究其前后工序间的相互关系和在各工序间必须相互保证的加工工艺要求及装配关系等。
3)了解工件的生产批量。
零件的生产对冲压加工的经济性起着决定性的作用,为此,必须根据零件的生产批量和零件的质量要求,来决定模具的型式、结构、材料等有关事项,并由此分析模具加工工艺的经济性及公建生产的合理性,描绘冲压工步的轮廓。
4)确定工件原材料的规格及毛料情况(如板料、条料、卷料、废料等),了解材料的性质和厚度,根据零件的工艺性确定是否采用少无废料拍样吗,并初步确定材料的规格和精度等级。
在满足使用性能和冲压性能要求的前提下,应尽量采用廉价的材料。
5)分析设计和工艺上对材料纤维方向的要求、毛刺的方向。
6)分析工(模)具车间制造模具的技术能力和设备条件以及可采用的模具标准件的情况。
7)熟悉冲压车间的设备资料或情况。
8)研究消化上述资料,初步构思模具的结构方案。
必要时可对既定的产品设计和工艺过程提出修改意见,使产品设计、工艺过程和模具设计与制造三者之间能更好的结合,以取得更加完善的效果。
二、确定工艺方案及模具结构型式工艺方案的确定是冲压件工艺性分析之后应进行的一个最重要的环节。
它包括:1)根据工件的形状特征、尺寸精度及表面质量的要求,进行工艺分析,判断出它的主要属性,确定基本工序的性质。
头盔外壳成形模凸、凹模的加工工艺方法
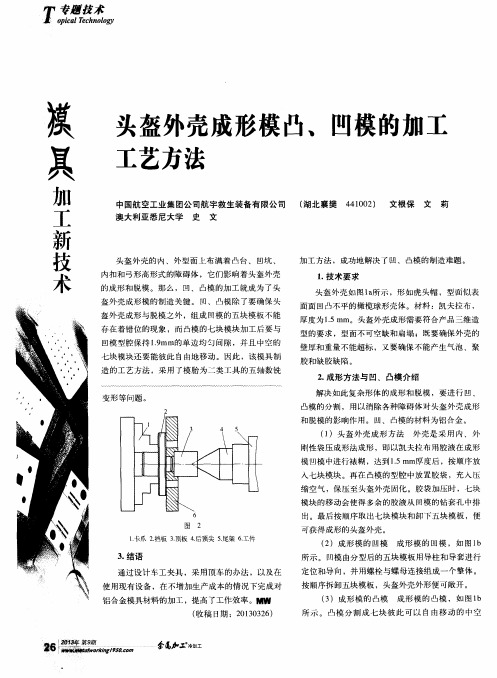
头盔外壳成形模凸 凹模的加工 工艺方法
中国航 空工业集 团公司航 宇救生装 备有限公 司 ( 湖北 襄樊 澳大利亚 悉尼大学 史 文 4 4 1 0 0 2 ) 文根保 文 莉
头 盔 外 壳 的 内 、外型 面 上 布 满 着 凸台 、凹坑 、 内扣 和 弓形 高 形 式 的障 碍 体 ,它 们影 响着 头 盔 外壳 的 成 形和 脱模 。那 么 ,凹 、 凸模 的加 工 就 成 为 了头 盔 外 壳 成 形模 的 制 造 关 键 。 凹 、 凸模 除 了要 确 保 头
图
2
1 . 卡爪 2 . 挡板 3 . 顶板 4 . 后顶尖 5 . 尾架 6 . 工件
3 . 结语 通过设计车工夹具 ,采用顶车的办法 ,以及在 使用现有设备 ,在不增加生产成本的情况下完成对
铝合金模具材料 的加工 ,提高 了工作效率 。MW ( 收稿 日 期 :2 0 1 3 0 3 2 6 )
参磊
籼工
T
凸台 “ 障
o
地 从 凹模 中 放 入 与 取 出 , 它 们 分 型 面 之 间应 制 成 3 。 的脱 模 斜 度 。 同 时 ,可 防止 胶 液 进 入 分 型 面 的
间隙 之 中 。
3 . 成形模 凹 凸模 的加 工工艺
如何制订 成形模 凹、 凸模的加工 工艺 ,便成
所示。凹模 由分型后的五块 模板用导柱和导套进行
定位和导 向,并用螺栓与螺母连接组成一个整体 。 按顺序拆卸五块模板 ,头盔外壳外形便可敞开 。
( 3 )成形模 的凸模 成形 模的 凸模 ,如 图1 b
所 示 。凸模 分割成 七块彼 此可以 自由移 动的 中空
r
i 9 5 o ; c o m
- 1、下载文档前请自行甄别文档内容的完整性,平台不提供额外的编辑、内容补充、找答案等附加服务。
- 2、"仅部分预览"的文档,不可在线预览部分如存在完整性等问题,可反馈申请退款(可完整预览的文档不适用该条件!)。
- 3、如文档侵犯您的权益,请联系客服反馈,我们会尽快为您处理(人工客服工作时间:9:00-18:30)。
凸凹模固定板加工工艺过程
凸凹模固定板加工工艺过程通常包括以下步骤:
1. 设计凸凹模固定板的制作图纸,根据需要确定凸凹模的形状和尺寸。
2. 准备材料。
根据制作图纸的要求,选择适当的材料进行加工。
常用的材料有金属板材、塑料板材等。
3. 制作凸面模具。
根据设计图纸上的凸面要求,使用车床、铣床等机械设备将材料加工成凸面模具的形状。
4. 制作凹面模具。
同样地,根据设计图纸上的凹面要求,使用机械设备将材料加工成凹面模具的形状。
5. 雕刻图案。
根据设计要求,在凸凹模固定板上进行图案的雕刻工艺。
可以使用机械设备如雕刻机、刻字机等,也可以手工进行雕刻。
6. 雕刻完成后,将凸面模具和凹面模具固定在一起,使用螺栓、螺母等连接件将两个模具牢固地固定在一起。
7. 进行定位和校准。
确保凸凹模固定板的位置和角度正确,以便在加工过程中准确地加工工件。
8. 加工工件。
将需要加工的工件放置在凸凹模固定板上,使用适当的加工设备如车床、铣床等进行加工。
9. 加工完成后,拆下加工好的工件,并进行清洁和质量检查。