凹模的加工工艺过程
模具制造工艺课后答案

模具制造工艺课后答案【篇一:模具制造工艺复习题(有答案)】火花加工又称为放电加工或电蚀加工,是一种利用电热能量进行加工的方法。
2、在电火花加工过程中,电极和工件之间必须保持一定的距离以形成放电间隙。
3、在电火花一次脉冲放电结束后,应间隔一段时间,使放电通道的带电粒子复合成中性粒子,这个过程称为消电离。
4、电火花加工时,工具电极的材料硬度不必比工件材料硬度高。
5、在电火花加工过程中,工具电极和工件都受到电腐蚀的作用,但腐蚀的速度却不一样,这种现象称为极性效应。
6、在电火花加工冲裁模过程中,保证配合间隙的电火花加工方法有直接配合法、修配凸模法、混合法和二次电极法四种。
7、在常用电极材料中,损耗最大的是黄铜电极材料。
8、电极的结构形式可分为整体式电极、镶拼式电极和组合式电极三种,应根据电极外形尺寸、复杂程度等因素来选取。
9、用电火花加工型孔时,电极的轮廓尺寸应比所加工的型孔尺寸均匀的缩小一个放电间隙。
10、电规准是指电火花加工过程中的一组电参数,包括电流、电压、脉冲宽度和脉冲间隔等。
11、型孔的电火花加工工艺方法主要有单电极平动法、多电极更换法和分解电极法三种方法。
12、在电火花型孔加工中,有粗规准、中规准和精规准三种电规准,根据加工需要,每一种又分为几个档次。
13、在电火花加工中,为了使脉冲放电能持续进行,必须靠电极和工件来保证放电间隙。
14、电火花加工与电火花线切割加工的加工原理是相同的,而加工方式是不同的。
15、电火花加工采用的电极材料有石墨、紫铜和铸铁(任写三种)。
16、快走丝线切割的走丝速度一般为 8-10m/s ,慢走丝线切割的走丝速度一般为 3-12m/min 。
17、电解加工时利用金属在电解液中产生阳极溶解的电化学反应,将工件加工成形的一种方法。
18、电解磨削是将电解作用和机械磨削相结合的一种新的加工方法。
19、型腔的冷挤压加工方式可以分为敞开式冷挤压和封闭式冷挤压两种。
20、超声波加工是利用工具的超声频振动来进行加工的。
凹模的机械加工工艺规程设计方案

凹模的机械加工工艺规程设计方案第1章序言在工业产品中,一个设计合理的塑料件往往能代替多个传统金属结构件,加上利用工程塑料特有的性质,可以一次成型非常复杂的形状,并且还能设计成卡装结构,所带来的效果是明显的,因此,近年来工业产品塑料化的趋势不断上升。
注塑成型是塑料加工中最普遍采用的方法,其中最主要之一的注塑模具已经很广泛的采用。
它在质量、精度、制造周期以及注塑成型过程中的生产效率等方面水平的高低,直接影响产品的质量、产量、成本及产品的更新换代,同时也决定着企业在市场竞争中的反应能力和速度。
注塑模具与其它机械行业想比,有以下三个特点:第一,模具不能像其它机械那样可作为基本定型的商品随时都可以在机电市场上买到。
模具制造不可能形成批量生产,即模具是单件生产的,其寿命越长,重复加工的可能性越小。
因此,模具的制造成本较高。
第二,因为注塑模具是为产品中的塑料制品而订制的,作为产品,除质量、价格等因素之外,很重要的一点就是需要尽快地投放市场,所以对于为塑料制品而特殊定订制的模具来说,其制造周期一定要短。
第三,模具制造是一项技术性很强的工作,其加工过程集中了机械制造中先进技术的部分精华与钳工技术的手工技巧,因此要求模具工人具有较高的文化技术水平,特别是对企业来说要求培养“全能工人”,使其适应多工种的要求,这种技术工人对模具单件生产方式组织均衡生产是非常重要的。
综上所述,模具制造存在成本高,要求制造周期短,技术性强等特点,目前,随着科学技术的不断发展和计算机的应用,这些问题得到了很大的改善。
注塑模具的特点:a)塑料的加热、塑化是在高温料筒内进行,而不是在模具内进行,因而模具不设加料腔,而设浇注系统,熔体通过浇注系统充满型腔。
浇注系统对注塑模来说至关重要。
b)塑料熔体进入型腔之前,模具已经闭合。
在注塑过程中需根据塑料特性,在模具中设加热或冷却系统。
c)注塑模生产适应性强,既可注塑小型制品,也可注塑大型制品;既可注塑简单制品,也可注塑复杂制品,生产率高,容易实现自动化。
机工社模具制造工艺 第2版教学课件-项目三 任务二 侧板凸凹模零件加工与工艺卡编制

材 料 Cr12MoV
数量
1
序号 工序名称
工序(工步)内容
工时
钻6-M12的螺纹底孔、攻丝6-M12深25,
5
钳工 钻两个销钉孔的穿丝孔2-φ5
检验
6 热处理a0.8μm 7 平磨
及厚度尺寸35mm,磨侧面基准 B
基于A、B基准,线切割凹模型孔及两个
快走丝线切割
慢走丝线切割
8~10m/s
低于0.2m/s
双向走丝,往复循环
单向走丝,不循环
钼丝, фd为0.1-0.2mm 铜丝, фd为0.1-0.2mm
乳化液或去离子水(冲水) 去离子水(浸没)
0.01~0.02mm, Ra1.6~3.2μm
0.002~0.005mm, Ra0.1~0.8μm
不同类型的机床在走丝速度、加工精度、液体介质、机床价格与 加工工时费等方面都有不同。
项目三 任务二 侧板凸凹模零件加工与工艺卡编制
凹模零件工序图
调整工艺路线: 1、备料:锻件 2、铣:各平面 3、平磨:上下面,基准面B 4、加工中心:点孔;钻、铰基准孔A 5、钳工:【划线、点孔、钻孔、铰孔、攻丝】 6、热处理:淬火 7、平磨:上下面,基准面B 8、线切割:凹模刃口、两个销钉孔
穿丝孔
相同点: (1)线切割加工的电压、电流波形与电火花加工的基本相似。由于工 具电极是直径较小的细金属丝,故脉冲宽度及平均电流等不能太大, 电参数范围较小,属中、精正极性加工,工件常接电源正极。 (2)由线切割加工机理可加工硬质合金等一切导电材料。 不同点: (1)不需要制作电极,可节约电极设计、制造费用,缩短生产周期。 (2)采用水或水基工作液,不会引燃起火。 (3)电极损耗极小,有利于加工精度的提高。 (4)能方便地加工出形状复杂、细小的通孔和外表面。由于切缝很窄 ,去除的材料为整块材料,可用作其他零件,节约贵重金属。
凹模加工工艺过程卡片

38凹模加工工艺过程卡片文件编号凹模加工工艺过程卡片 产品型号 零(部)件图号 共2页 产品名称零(部)件名称 凹模第1页 材料牌号 Cr12M oV 毛坯种类 锻造毛坯外形尺寸每坯件数1 每台件数1备注工序号工序名称 工序内容车间设备 工艺装备基本时间/min1 锻造锻造,锻成六面体,并进行退火处理。
锻造车间 空气锤2铣六个面在刨铣床上加工锻坯的六个面。
机加工车间铣床Ф315㎜的YG8硬质合金面铣刀 通用夹具 游标卡尺10.983平磨磨削上、下两个平面和角尺面。
机加工车间磨床通用夹具 CBN 砂轮394 钳工划线钳工划线划出型孔轮廓线及螺孔和销孔等位置。
钳工车间 T68专用夹具 游标卡尺 内规径25.47描绘 5 去废料先在型孔适当位置钻孔,然后用带锯机去除中心废料。
机加工车间6 钳工 加工螺孔(钻孔、攻螺纹)和加工销孔(钻孔、铰孔) 机加工车间Ф7㎜直柄短麻花钻Ф5㎜直柄短麻花钻通用夹具 丝锥底图号 7 热处理 淬火和回火处理,检查硬度,表面硬度要求达到58~62HRC 。
钳工车间8 平磨 平磨上下两面机加工车间 磨床 通用夹具 CBN 砂轮9 铣导槽在铣床上铣削工件的导槽, 保证一定的加工精度机加工车间 铣床硬质合金键槽铣刀通用夹具 游标卡尺10 退磁处理11 电火花加工型孔利用凸模加长一段铸铁后做为电极,电加工完成后去掉铸铁部分做凸模用。
由于间隙较大,故先用粗加工,然后调整平动头的偏心量,再用精加工,从而达到凸凹模的配合间隙要求。
电火花加工车间装订号姓名学号日期指导老师40。
凸凹模固定板加工工艺过程

凸凹模固定板加工工艺过程
凸凹模固定板加工工艺过程通常包括以下步骤:
1. 设计凸凹模固定板的制作图纸,根据需要确定凸凹模的形状和尺寸。
2. 准备材料。
根据制作图纸的要求,选择适当的材料进行加工。
常用的材料有金属板材、塑料板材等。
3. 制作凸面模具。
根据设计图纸上的凸面要求,使用车床、铣床等机械设备将材料加工成凸面模具的形状。
4. 制作凹面模具。
同样地,根据设计图纸上的凹面要求,使用机械设备将材料加工成凹面模具的形状。
5. 雕刻图案。
根据设计要求,在凸凹模固定板上进行图案的雕刻工艺。
可以使用机械设备如雕刻机、刻字机等,也可以手工进行雕刻。
6. 雕刻完成后,将凸面模具和凹面模具固定在一起,使用螺栓、螺母等连接件将两个模具牢固地固定在一起。
7. 进行定位和校准。
确保凸凹模固定板的位置和角度正确,以便在加工过程中准确地加工工件。
8. 加工工件。
将需要加工的工件放置在凸凹模固定板上,使用适当的加工设备如车床、铣床等进行加工。
9. 加工完成后,拆下加工好的工件,并进行清洁和质量检查。
凹模的加工工艺过程

凹模的加工工艺过程首先,设计凹模是整个凹模加工工艺的第一步。
凹模设计需要根据具体的产品需求,包括产品尺寸、形状、表面质量要求等因素来确定凹模的结构,以及材料的选择等。
设计凹模需要考虑到产品的装配连接、注塑成型、冷却等因素,确保凹模能够满足产品的质量要求。
选择材料是凹模加工工艺中的关键环节。
凹模材料一般选择具有高强度、高硬度、高耐磨性和耐热性能的合金工具钢。
具体的材料选择需要根据凹模的使用条件和要求来确定,以确保凹模具有足够的寿命和稳定的加工性能。
数控加工是凹模加工中的主要工艺环节。
数控加工采用计算机控制的机床进行加工,具有高精度、高效率和自动化程度高的特点。
数控加工包括车、铣、钻、磨等多个工序,可以实现对凹模各个部位的加工和成型。
数控加工需要根据凹模的几何形状和尺寸要求,编制相应的加工程序,然后通过机床进行加工。
热处理是凹模加工中的重要步骤之一、热处理可以提高凹模的硬度和强度,改善凹模的耐磨性和耐腐蚀性能。
常见的热处理方法包括淬火、回火和表面渗碳等。
淬火是将凹模加热到高温后迅速冷却,使材料硬化;回火是将高温淬火后的凹模再加热到适当温度保温一段时间后冷却,以减轻内部应力并提高韧性;表面渗碳是将凹模浸入含有碳的淬火介质,使凹模表面增加碳含量,提高凹模的硬度和耐磨性。
热处理后的凹模需要进行调质退火处理,以消除热处理过程中产生的应力。
精加工是凹模加工中的重要环节。
精加工包括修磨、抛光等工序,旨在提高凹模的表面质量和精度。
修磨是将加工过程中产生的毛刺、凹痕等缺陷修复,使凹模表面平整;抛光是利用研磨材料对凹模表面进行抛光,以提高光洁度和亮度。
精加工需要使用专业的磨床、抛光机等设备,根据凹模的要求进行精细加工。
最后,组装是凹模加工的最后一步。
组装包括安装凹模的各个部件,如模板、活动板、导柱、导套等,以形成完整的凹模结构。
组装过程需要确保凹模的各个零部件能够正确地连接在一起,同时进行必要的调试和测试,以确保凹模的正常使用和性能。
凹模加工工艺流程
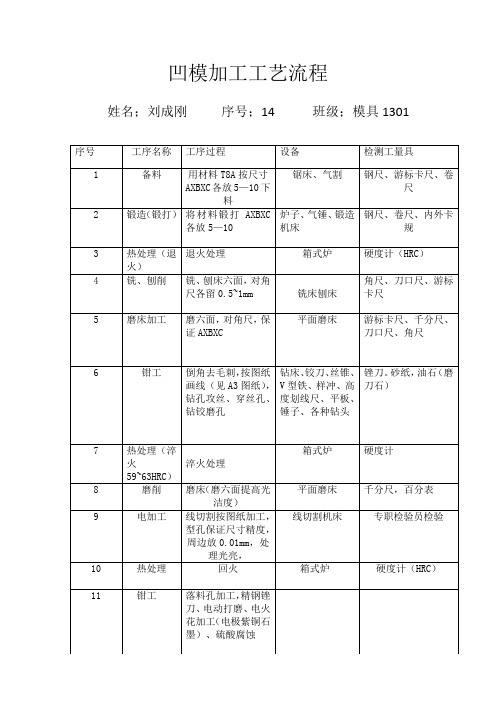
铣、刨削
铣、刨床六面,对角尺各留0.5~1mm
铣床刨床
角尺、刀口尺、游标卡尺
5
磨床加工
磨六面,对角尺,保证AXBXC
平面磨床
游标卡尺、千分尺、刀口尺、角尺
6
钳工
倒角去毛刺,按图纸画线(见A3图纸),钻孔攻丝、穿丝孔、钻铰磨孔
钻床、铰刀、丝锥、V型铁、样冲、高度划线尺、平板、锤子、各种钻头
锉刀。砂纸,油石(磨刀石)
凹模加工工艺流程
姓名;刘成刚序号;14班级;模具1301
序号
工序名称
工序过程
设备检测工ຫໍສະໝຸດ 具1备料用材料T8A按尺寸AXBXC各放5—10下料
锯床、气割
钢尺、游标卡尺、卷尺
2
锻造(锻打)
将材料锻打AXBXC各放5—10
炉子、气锤、锻造机床
钢尺、卷尺、内外卡规
3
热处理(退火)
退火处理
箱式炉
硬度计(HRC)
12
磨床加工
精磨工作面
磨床
游标卡尺
13
钳工
钳工退磁(退磁器)
退磁器
14
凹模清理上油→等待装配
7
热处理(淬火59~63HRC)
淬火处理
箱式炉
硬度计
8
磨削
磨床(磨六面提高光洁度)
平面磨床
千分尺,百分表
9
电加工
线切割按图纸加工,型孔保证尺寸精度,周边放0.01mm,处理光亮,
线切割机床
专职检验员检验
10
热处理
回火
箱式炉
硬度计(HRC)
11
钳工
落料孔加工,精钢锉刀、电动打磨、电火花加工(电极紫铜石墨)、硫酸腐蚀
模具制造技术课后习题及答案(共9单元)第2章 模具零件的机械加工

第2章模具零件的机械加工思考题与习题l.在模具加工中,制定模具零件工艺规程的主要依据是什么?答:根据模具零件的几何形状、尺寸和模具零件的技术要求,结合现有加工技术和设备情况下,能以最经济、最安全加工出高质量的模具零件作为依据。
2.在导柱的加工过程中,为什么粗(半精)、精加工都采用中心孔作定位基准?答:导柱的加工过程中,为了保证各外圆柱面之间的位置精度和均匀的磨削余量。
对外圆柱面的车削和磨削,一般采用设计基准和工艺基准重合的两端中心孔定位。
所以,在半精车、精车和磨削之前需先加工中心定位孔,为后继工序提供可靠的定位基准。
3.导柱在磨削外圆柱面之前,为什么要先修正中心孔?答:磨削前对导柱进行了热处理,导柱中心定位孔在热处理后的修正,目的是消除热处理过程中中心孔可能产生的变形和其它缺陷,使磨削外圆柱面时能获得精确定位,保证外圆柱面的形状和位置精度要求。
4.拟出图2.1所示导柱的工艺路线,并选出相应的机加工设备。
图2.1可卸导柱导柱加工工艺过程工序号工序名称工序内容设备检验1 备料Φ36mm(20号钢)2 下料按图纸尺寸考虑切削余量Φ36m m×195㎜锯床自检车床自检3 粗车外圆定位:①车端面打中心孔;车外圆到Φ34mm;②调头车端面(到尺寸190mm),打中心孔,车外圆到Φ34mm。
4 精车中心孔定位:车床专职检验员①精车外圆面到尺寸(留磨削余量0.2mm),精车R3;5 精车调头外圆定位:①车锥面到尺寸,倒角C1.5;②在端面钻M8螺纹底孔,前端按图扩孔到Φ8.4,攻丝M8,端面锪孔到尺寸。
车床6 热处理①20号钢渗碳0.8~1.2㎜;②淬火HRC58~62。
热处理炉(检验硬度、平直度)。
7 研磨中心孔外圆定位:研磨中心定位孔。
车床8 磨外圆中心孔定位:粗磨、精磨外圆、锥面磨床自检9 研磨①研磨导柱导向部分外圆10 检验专职检验员11 入库清洗、喷涂防锈润滑油后,分类用塑料薄膜包封后入库5.导套加工时,怎样保证配合表面间的位置精度要求?答:由于构成导套的主要表面是内、外圆柱表面,一般采用一次装夹后,完成对有位置精度要求的内、外圆柱表面的车削和热处理后的磨削加工就能保证配合表面间的位置精度要求。
- 1、下载文档前请自行甄别文档内容的完整性,平台不提供额外的编辑、内容补充、找答案等附加服务。
- 2、"仅部分预览"的文档,不可在线预览部分如存在完整性等问题,可反馈申请退款(可完整预览的文档不适用该条件!)。
- 3、如文档侵犯您的权益,请联系客服反馈,我们会尽快为您处理(人工客服工作时间:9:00-18:30)。
广西科技大学机械加工工序卡片产品型号零件图号
产品名称冲压模零件名称落料凹模共 5 页第 1 页
车间工序号工序名称材料牌号
普通车间00 粗铣
毛坯种类毛坯外形尺寸每毛坯可制件数每台件数
轧制165x165x30m
m 1 1
设备名称设备型号设备编号同时加工件数普通铣床
夹具编号夹具名称切削液
专用夹具
工位器具编号工位器具名称工序工时(分) 准终单件
工步号工步内容工艺装备主轴转速切削速度进给量切削深度
进给次数
工步工时r/min m/min mm/r mm 机动辅助
1 粗铣上面,见平即可φ60端面铣刀;游标卡尺450 30 0.8 1.5 1
2 粗铣周边保证尺寸162x162mm φ20立铣刀;游标卡尺450 30 0.8 4 5
3
到过装夹已加工过的表面,粗铣平面,保证高
度尺寸27mm;
φ60端面铣刀;游标卡尺450 30 0.8 1.5 1
4 粗铣残余周边至尺寸162x162mmφ20立铣刀;游标卡尺450 30 0.8 4 2
设计(日期)校对(日期)审核(日期)标准化(日期)会签(日期)
广西科技大学机械加工工序卡片产品型号零件图号
产品名称冲压模零件名称落料凹模共 5 页第 2 页
车间工序号工序名称材料牌号
普通车间05 钻孔
毛坯种类毛坯外形尺寸每毛坯可制件数每台件数
轧制165x165x30m
m 1 1
设备名称设备型号设备编号同时加工件数摇臂钻床
夹具编号夹具名称切削液
专用夹具
工位器具编号工位器具名称工序工时(分) 准终单件
工步号工步内容工艺装备主轴转速切削速度进给量切削深度
进给次数
工步工时r/min m/min mm/r mm 机动辅助
1 划线钢直尺
2 钻4-M20螺纹底孔和销孔φ11.8mm φ17、φ11.8mm的麻花钻75 20 0.6 27 1
3
设计(日期)校对(日期)审核(日期)标准化(日期)会签(日期)
车间工序号工序名称材料牌号普通车间10 精铣
毛坯种类毛坯外形尺寸每毛坯可制件数每台件数
轧制165x165x30m
m 1 1
设备名称设备型号设备编号同时加工件数数控铣床
夹具编号夹具名称切削液
专用夹具
工位器具编号工位器具名称工序工时(分) 准终单件
工步号工步内容工艺装备主轴转速切削速度进给量切削深度
进给次数
工步工时r/min m/min mm/r mm 机动辅助
1 半精铣—精铣上面1000 45 0.6 1.5 2
2
半精铣四周至160×160mm;半精铣台
阶面至100.2x60.16x10mm和80.2×60.16
×224mm的方孔;铰φ12通孔;台阶面
与方孔清根
1000 45 0.6 4 4
3
倒过来装夹半精加工过的面,半精铣—
精铣下平面至24mm;
1000 45 0.6 1.5 2
4
半精铣残余四周至160×160mm保证技
术要求
1000 45 0.6 4 2
设计(日期)校对(日期)审核(日期)标准化(日期)会签(日期)
车间工序号工序名称材料牌号普通车间攻丝
毛坯种类毛坯外形尺寸每毛坯可制件数每台件数
轧制165x165x30m
m 1 1
设备名称设备型号设备编号同时加工件数
夹具编号夹具名称切削液
专用夹具
工位器具编号工位器具名称工序工时(分) 准终单件
工步号工步内容工艺装备主轴转速切削速度进给量切削深度
进给次数
工步工时r/min m/min mm/r mm 机动辅助
1 手动攻螺纹4-M20 M20攻丝
2
设计(日期)校对(日期)审核(日期)标准化(日期)会签(日期)
广西科技大学机械加工工序卡片产品型号零件图号
产品名称冲压模零件名称落料凹模共 5 页第 5 页
车间工序号工序名称材料牌号
金工
毛坯种类毛坯外形尺寸每毛坯可制件数每台件数
轧制165x165x30m
m 1 1
设备名称设备型号设备编号同时加工件数
夹具编号夹具名称切削液
专用夹具
工位器具编号工位器具名称工序工时(分) 准终单件
工步号工步内容工艺装备主轴转速切削速度进给量切削深度
进给次数
工步工时r/min m/min mm/r mm 机动辅助
1 台阶面与方孔清根
锉刀;直角尺,内径千分尺
2
设计(日期)校对(日期)审核(日期)标准化(日期)会签(日期)。