粉末冶金材料工艺与设备课程设计指导书详解
粉末冶金工艺过程及参数
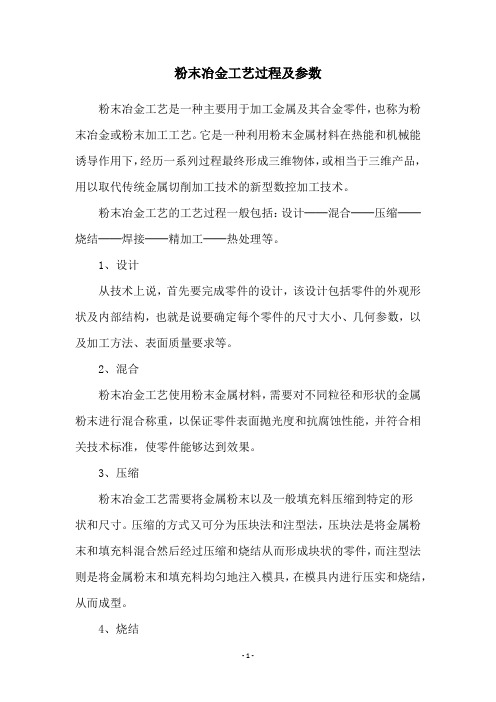
粉末冶金工艺过程及参数粉末冶金工艺是一种主要用于加工金属及其合金零件,也称为粉末冶金或粉末加工工艺。
它是一种利用粉末金属材料在热能和机械能诱导作用下,经历一系列过程最终形成三维物体,或相当于三维产品,用以取代传统金属切削加工技术的新型数控加工技术。
粉末冶金工艺的工艺过程一般包括:设计──混合──压缩──烧结──焊接──精加工──热处理等。
1、设计从技术上说,首先要完成零件的设计,该设计包括零件的外观形状及内部结构,也就是说要确定每个零件的尺寸大小、几何参数,以及加工方法、表面质量要求等。
2、混合粉末冶金工艺使用粉末金属材料,需要对不同粒径和形状的金属粉末进行混合称重,以保证零件表面抛光度和抗腐蚀性能,并符合相关技术标准,使零件能够达到效果。
3、压缩粉末冶金工艺需要将金属粉末以及一般填充料压缩到特定的形状和尺寸。
压缩的方式又可分为压块法和注型法,压块法是将金属粉末和填充料混合然后经过压缩和烧结从而形成块状的零件,而注型法则是将金属粉末和填充料均匀地注入模具,在模具内进行压实和烧结,从而成型。
4、烧结烧结是粉末冶金工艺中最重要也是最关键的一步。
烧结是给零件提供形状和尺寸,同时还可以改善部件的力学性能、物理性能和物理性能。
它的烧结参数有温度、时间、压力、含气量等,具体的参数要根据零件的材料特性和要求而确定。
5、焊接焊接是在烧结后把多个零件组合在一起,使之成为一个整体零件,焊接可以在零件表面形成一个均匀的钎焊层,从而改善零件的力学性能,并且可以把不同物料,如钢、镍和铝等,进行组合。
6、精加工精加工指的是将零件的表面处理成符合要求的精度,使其精度达到一定的精度。
一般来说,可以采用两种方法,用机械加工方法或用化学抛光方法,来达到精度的要求。
7、热处理热处理是指将零件在一定温度和一定时间的作用下,利用物理或化学变化,改变或增强零件的物理性能,从而提高零件的使用性能。
粉末冶金工艺是一种重要的加工工艺,由于它比传统加工方法具有更高的效率、更低的成本,可以根据客户的要求制造唯一的三维零件,所以它在工业制造中越来越受到重视。
粉末冶金手册

粉末冶金手册粉末冶金是一种将金属或非金属粉末通过压制、烧结等工艺加工成成型品的制造工艺。
粉末冶金具有高效、低成本、可成型性好、材料利用率高等优势,因此在航空航天、汽车工业、电子行业等领域得到广泛应用。
本手册将介绍粉末冶金的基本原理、工艺流程、材料选择、设备介绍等内容。
一、粉末冶金的基本原理粉末冶金的基本原理是将金属或非金属物质经过粉碎或原料特殊制备得到的粉末,经过压制成型或注射成型,再经过高温烧结得到所需产品。
这种工艺利用了粉末颗粒之间的相互扭曲和扩散,从而实现了物质的成型。
同时,由于粉末冶金是一种非液态冶金工艺,不需要溶解和凝固过程,避免了材料在液态下的气体、夹杂物等问题,因此可以获得更高的材料纯度和均匀性。
二、粉末冶金的工艺流程粉末冶金的一般工艺流程分为原料制备、混合、成型、烧结和后处理等步骤。
1.原料制备:原料制备阶段主要包括选料和粉末制备。
选料是指根据成品的要求选择合适的原料,如金属、合金、陶瓷或复合材料等。
粉末制备可以通过粉碎、化学方法、电化学方法等得到所需粉末。
2.混合:将所选的原料粉末按照一定比例进行混合。
混合的目的是使各种材料的粒子均匀分散,以获得更高的均匀性。
3.成型:将混合好的粉末通过压制成型,可以使用冷压、热压或注射成型等方法。
成型一般可以分为干压成型和液相成型两种方式。
4.烧结:成型件通过高温烧结,使粉末颗粒之间发生结合,形成致密的材料。
烧结温度和时间根据材料种类、成型件形状等因素确定。
5.后处理:烧结后的材料可以进行表面处理、热处理、加工等工艺。
目的是使产品达到所需的性能和尺寸要求。
三、粉末冶金的材料选择粉末冶金可以应用于各种金属和非金属材料的制备,包括纯金属、合金、陶瓷、塑料等。
在选择材料时需要考虑材料的物理性质、化学性质、应用环境等因素。
例如,对于需要高强度和耐磨性的零件可以选择使用金属粉末冶金制备的合金材料;对于需要绝缘性能和耐高温的零件可以选择使用陶瓷粉末冶金制备的材料。
《材料加工工艺和设备》课程教学大纲

课程讲 授、作 业、讨论
课程讲 授、作 业、讨论
课程讲 授、作 业、讨论
教学内容 学时 教学方式 作业及要求
基本要求
考查方式
材料加工工艺
与设备基础
2
课堂讲授
掌握材料加工工艺 和设备特点;与材 料 加 工 原 理 的 关 课堂提问 系;与过程控制的关 系
材料加工工艺 设计方法
《材料加工工艺和设备》课程教学大纲
课程基本信息(Course Information)
课程代码 (Course Code)
MT340
*学时 (Credit Hours)
32
*学分 (Credits)
2
*课程名称 (Course Name)
材料加工工艺和设备 Materials manufacture processing and apparatus
课堂提问讨 工艺与性能的关系 以 及 工 艺 优 化 方论和作业 法。
齿轮钢的表面
处Байду номын сангаас工艺(或
其它表面改 性、微纳器件
2
制备的问题及
工艺设计)
课堂讲授
材料加工过
程控制基础
6
课堂讲授
过程控制中 的传感技术
2 课堂讲授
了解齿轮钢的 碳、渗氮和碳氮 渗工艺的设计
共渗课 论作堂业提
问
讨
掌握材料加工过程
控制的原理、组成、课 堂 提 问 讨
*课程目标与毕业要 求对应关系
(relationship between learning
outcomes and graduation
requirements)
毕业要求
粉末冶金材料工艺设计和设备课程设计报告指导书1.doc
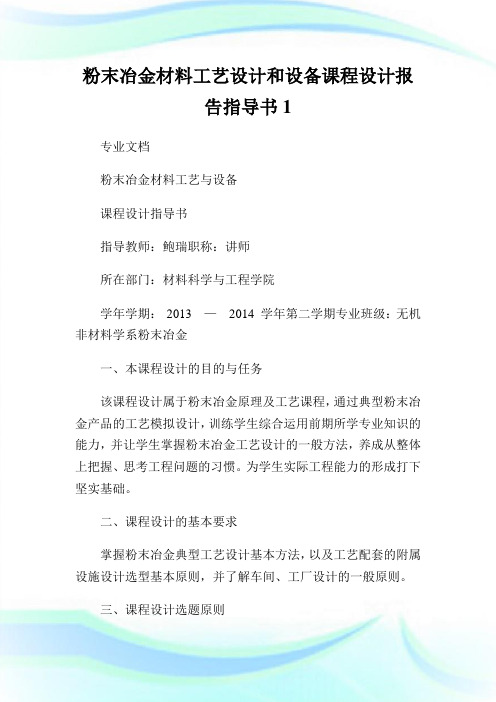
粉末冶金材料工艺设计和设备课程设计报告指导书1专业文档粉末冶金材料工艺与设备课程设计指导书指导教师:鲍瑞职称:讲师所在部门:材料科学与工程学院学年学期:2013 —2014 学年第二学期专业班级:无机非材料学系粉末冶金一、本课程设计的目的与任务该课程设计属于粉末冶金原理及工艺课程,通过典型粉末冶金产品的工艺模拟设计,训练学生综合运用前期所学专业知识的能力,并让学生掌握粉末冶金工艺设计的一般方法,养成从整体上把握、思考工程问题的习惯。
为学生实际工程能力的形成打下坚实基础。
二、课程设计的基本要求掌握粉末冶金典型工艺设计基本方法,以及工艺配套的附属设施设计选型基本原则,并了解车间、工厂设计的一般原则。
三、课程设计选题原则根据课程内容,结合生产选择粉末冶金工程的典型工艺,进行工艺的模拟设计。
四、所需具备的基础知识工程制图、粉末冶金原理、机械设计五、设计所需工具和准备工作制图板、绘图工具等,或安装有制图软件的计算机。
查阅工厂设计的手册和相关资料。
六、粉末冶金工艺课程设计一般方法(一)概论设计是任何一项工程在动工前必先完成的一项技术性很强、而又非常仔细的技术工作。
工厂设计的内容一般包括厂址选择、厂区总图及运输,工艺流程的选择,产品方案的设计,物料平衡计算,设备的选型与数量的计算,生产检查与质量控制,理化检测,房屋建筑,工厂动力,采暖通风,劳动组织及定员,工厂经济概算与成本的预算,技术安保与环境保护,及有关生活设施。
对所作设计的要求是投资少、建厂快,布局合理,经济技术指标先进,经济效益好。
设计任务的来源一般由上级主管部门或地方政府或工矿企业予以委托,以设计任务书的形式下达给设计单位。
设计单位接收任务后,指定工程设计的总负责人,会同各有关专业科室的工程负责人组成设计组,开展设计工作。
工厂设计一般分为三个阶段进行,即初步设计,技术设计和施工图纸。
初步设计是按照工厂设计的有关内容和章节,进行初步的设计和计算,概算其建厂投资是否合理,并对设计中有关的一些基本技术问题作出决策。
粉末冶金工艺(共17张PPT)

粉末冶金工艺过程
• 粉末冶金材料是指不经熔炼和铸造,直接 用几种金属粉末或金属粉末与非金属粉末, 通过配制、压制成型,烧结和后处理等制 成的材料。粉末冶金是金属冶金工艺与陶 瓷烧结工艺的结合,它通常要经过以下几 个工艺过程:
一、粉料制备与压制成型
• 常用机械粉碎、雾化、物理化学法制取粉 末。制取的粉末经过筛分与混合,混料均 匀并加入适当的增塑剂,再进行压制成型, 粉粒间的原子通过固相扩散和机械咬合作 用,使制件结合为具有一定强度的整体。 压力越大则制件密度越大,强度相应增加。 有时为减小压力合增加制件密度,也可采 用热等静压成型的方法。
三、后处理
• 一般情况下,烧结好的制件能够达到所需 性能,可直接使用。但有时还需进行必要 的后处理。如精压处理,可提高制件的密 度和尺寸形状精度;对铁基粉末冶金制件 进行淬火、表面淬火等处理可改善其机械 性能;为达到润滑或耐蚀目的而进行浸油 或浸渍其它液态润滑剂;将低熔点金属渗 入制件孔隙中去的熔渗处理,可提高制件 的强度、硬度、可塑性或冲击韧性等。
粉末冶金工艺的基本工序
• 1、原料粉末的制备。现有的制粉方法大体 可分为两类:机械法和物理化学法。而机 物理化学法又分为:电化腐蚀法、还原法、化合法、还原-化合法、气相沉积法、液相沉积法以及电解法。
粉末冶金方法起源于公元前三千多年。 从民用工业到军事工业;
械法可分为:机械粉碎及雾化法;物理化 现有的制粉方法大体可分为两类:机械法和物理化学法。
将低熔点金属渗入制件孔隙中去的熔渗处理,可提高制件的强度、硬度、可塑性冲击韧性等。 3、由于粉末冶金工艺在材料生产过程中并不熔化材料,也就不怕混入由坩埚和脱氧剂等带来的杂质,而烧结一般在真空和还原气氛中进行,不 怕氧化,也不会给材料任何污染,故有可能制取高纯度的材料。
粉末冶金工艺及材料课程设计

粉末冶金工艺及材料课程设计1. 研究背景和目的粉末冶金是一种先进的成型工艺,它利用粉末制造成型。
粉末冶金具有高成形性、高精度、高可靠性和节约原料等优点,被广泛应用于汽车、航空、电子、医疗器械等领域。
本次课程设计的目的是为了深入掌握粉末冶金工艺及材料的相关知识,通过实践操作来加深对该工艺的理解和掌握。
2. 实验设备和工具2.1 设备清单•模具•压力机•真空炉•机械制粉设备2.2 工具清单•计量器具:千分尺、平行垫片、游标卡尺•砂纸、磨具•清洁工具:毛刷、棉布3. 实验流程3.1 实验材料•钨粉•铜粉•石墨粉•异丙醇3.2 模具准备采用数控车床分别制作钨铜合金模具(正方体、圆柱体),并使用砂纸、磨具进行打磨,确保模具表面光滑平整。
3.3 粉末制备采用机械制粉设备对钨、铜、石墨粉进行混合制粉,并对制作好的粉末进行筛分。
3.4 热压制备将经过筛分的混合粉末填充至模具中,使用压力机将粉末进行热压制备,以形成具有预定外形的试件。
3.5 组织分析采用多种手段和方法对制备好的试件进行微观组织分析和性能测试。
包括金相分析、差热分析、拉伸试验和硬度测试。
4. 实验结果与分析通过实验结果的分析,得到如下结论:4.1 热压条件的影响热压温度和压力是影响试件制备过程及其微观结构的重要因素。
当热压温度和压力较高时,制备的试件通常具有更好的致密性和更细致的晶粒尺寸。
4.2 材料的物理化学性质的影响钨铜合金的合金成分、粉末的形态和加工条件对样品的微观结构具有重要影响,不同的物理化学性质条件下,试件的晶粒尺寸差异明显。
5. 实验结论通过实验得出,热压制备钨铜合金试件,其微观组织 (晶粒细度、晶粒分布和相结构等) 受到多种因素的影响,其粉末合成、制备工序、制备条件和后续处理等工艺均对最终试件的性能及应用具有重要影响。
6. 参考文献•[1] 王晶, 宋学锋, 黎艳秋. 粉末冶金材料. 北京: 科学出版社, 2005.•[2] 刘立军, 叶庆华, 高占安. 热压法制备高强、高导银铜复合粉末.粉末冶金技术, 2011(3): 51-53.•[3] 陈巧雁, 吕宏光, 杨辉辉. 粉末冶金复合材料的界面组织与性能.粉末冶金材料科学与工程, 2014(2): 23-28.。
粉末冶金行业用书

汇集了日本粉末冶金的测试方法等标准23个。(每本102本)
2
JIS Z2550—1989机械结构零件用烧结材料
(内部资料、仅供参考)
日本标准协会发行
本标准规定了机械结构零件用烧结材料的机械性能测试方法。(每本44本)
(内部资料、仅供参考)
102
3
金属粉末和粉末冶金产品测试方法标准
本标准汇集了60个测试方法标准。为2002年最新版本。由美国金属粉末工业联合会出版发行。(内部资料、仅供参考)
158
4
JIS Z2550—1989机械结构零件用烧结材料
本标准规定了机械结构零件用烧结材料的机械性能测试方法标准。(内部资料、仅供参考)
25
11
粉末冶金应用200例
本书由科研单位提供的粉末冶金零件在农业机械、汽车工业、机床工业、仪器仪表工业、轻工业、冶金、矿山机械及其他方面的应用。
20
12
汽车粉末冶金零件应用
(内部资料、仅供参考)
本书分析、评价了汽车粉末冶金零件在国内外应用水平和技术水平,提供精选的世界各国汽车粉末冶金实例266例,每例均有实物、图片、简要说明及名称、材料、密度、单重等数据。
52
4
粉末冶金电阻炉设计
(内部资料、仅供参考)
张丽英
吴成义
主要介绍粉末冶金工业常用的电阻炉,即空气电阻炉、真空电阻炉、保护气氛电阻炉等的结构。1995年出版。
95
5
陶瓷基复合材料导论
(内部资料、仅供参考)
贾成厂
主要包括复和材料的基本理论、陶瓷基复合材料的原材料及其性能、界面与表面、加工与封接、检验与评价以及应用等。
韩凤麟主编
该书刊登了粉末冶金关键零件的有关标准以及国际ISO3252粉末冶金术语。ISO5755烧结金属材料规范和我国GB/T4136粉末冶金还原铁粉标准。2001年出版。
粉末冶金模具设计说明书

前言材料是中国四大产业之一,它包括有机高分子材料、复合材料、金属材料及无机非金属材料。
粉末冶金技术作为金属材料制造的一种,以其不可替代的独特优势与其它制造方法共同发展。
粉末冶金相对其它冶金技术来说具有:成本低;加工余量少;原料利用率高;能生产多孔材料等其它方法不能生产或着很难生产的材料等优势。
粉末冶金是制取金属粉末以及将金属粉末或金属粉末与非金属粉末混合料成型和烧结来制取粉末冶金材料或粉末冶金制品的技术。
粉体成形是粉体材料制备工艺的基本工序。
模具是实现粉体材料成形的关键工艺装备。
模具的设计要尽可能的接近产品的形状,机构设计合理表面光滑,减少应力集中,避免压坯分层、开裂。
模具本身要有一定的强度保证压制的次数,不易变形。
粉体模压成形模具主要零件包括:阴模、芯杆、模冲。
模具设计首先要厂家提供产品图,再确定成型的方式,收集压坯设计的基本参数(包括:松装密度、压坯密度、粉体的流动性、及烧结收缩系数等。
)来算得压坯的尺寸。
根据压坯形状尺寸以及服役条件和要求来设计出成型模具尺寸,校核模具强度。
最后在用模具试压,若压坯合格,则此模具复合要求。
本次课程设计之前,我们已经学习了《热处理原理与工艺》、《金属物理与力学性能》、《粉末冶金原理》、《硬质合金生产原理》等相关课程的知识。
这次在老师的指导下,和同学的相互讨论,自己查阅资料,基本上懂得了模具设计的步骤和方法。
相信经过这次设计后,对以后的工作会有很大的帮助。
1 设计任务本课程设计的任务是生产一批有色金属扁材拉制模坯,其形状和尺寸如下图:型号 D H a b h h1h2R r e 42-14×5.9 45 20 14.6 5.9 3 3 6 4 1 1.51.1 产品分析由产品图可知H/D<3,因此,该产品适合单向压制。
产品的斜边角度不大,因此,装粉比较容易,可用单从头压制。
产品内部的斜角可直接做在芯杆上。
菱角的倒角不长,可适合用上冲头压制。
1.2 材质的选择该模具生产的产品用于拉制模坯,对产品的强度及耐磨性能要求很高,再根据客户所提供的要求,综合考虑选用硬质合金材料YG8作为材质。
- 1、下载文档前请自行甄别文档内容的完整性,平台不提供额外的编辑、内容补充、找答案等附加服务。
- 2、"仅部分预览"的文档,不可在线预览部分如存在完整性等问题,可反馈申请退款(可完整预览的文档不适用该条件!)。
- 3、如文档侵犯您的权益,请联系客服反馈,我们会尽快为您处理(人工客服工作时间:9:00-18:30)。
粉末冶金材料工艺与设备课程设计指导书指导教师:鲍瑞职称:讲师所在部门:材料科学与工程学院学年学期:2013 —2014学年第一学期专业班级:无机非材料学系粉末冶金一、本课程设计的目的与任务该课程设计属于粉末冶金原理及工艺课程,通过典型粉末冶金产品的工艺模拟设计,训练学生综合运用前期所学专业知识的能力,并让学生掌握粉末冶金工艺设计的一般方法,养成从整体上把握、思考工程问题的习惯。
为学生实际工程能力的形成打下坚实基础。
二、课程设计的基本要求掌握粉末冶金典型工艺设计基本方法,以及工艺配套的附属设施设计选型基本原则,并了解车间、工厂设计的一般原则。
三、课程设计选题原则根据课程内容,结合生产选择粉末冶金工程的典型工艺,进行工艺的模拟设计。
四、所需具备的基础知识工程制图、粉末冶金原理、机械设计五、设计所需工具和准备工作制图板、绘图工具等,或安装有制图软件的计算机。
查阅工厂设计的手册和相关资料。
六、粉末冶金工艺课程设计一般方法(一)概论设计是任何一项工程在动工前必先完成的一项技术性很强、而又非常仔细的技术工作。
工厂设计的内容一般包括厂址选择、厂区总图及运输,工艺流程的选择,产品方案的设计,物料平衡计算,设备的选型与数量的计算,生产检查与质量控制,理化检测,房屋建筑,工厂动力,采暖通风,劳动组织及定员,工厂经济概算与成本的预算,技术安保与环境保护,及有关生活设施。
对所作设计的要求是投资少、建厂快,布局合理,经济技术指标先进,经济效益好。
设计任务的来源一般由上级主管部门或地方政府或工矿企业予以委托,以设计任务书的形式下达给设计单位。
设计单位接收任务后,指定工程设计的总负责人,会同各有关专业科室的工程负责人组成设计组,开展设计工作。
工厂设计一般分为三个阶段进行,即初步设计,技术设计和施工图纸。
初步设计是按照工厂设计的有关内容和章节,进行初步的设计和计算,概算其建厂投资是否合理,并对设计中有关的一些基本技术问题作出决策。
在初步设计作完之后,必要时,可召开有关专家参加的设计审定会予以审定。
技术设计是在批准了初步设计的基础上进行的。
其内容和章节与初步设计基本相同。
但对初步设计中所提出的问题应当予以修改。
各章节比初步设计编制得更详尽、更完善、更准确。
要求能作为施工图纸的基础。
施工图纸的编制是在初步设计和技术设计的基础上进行的,是前面设计的具体化,其深度以满足施工要求为原则。
其内容包括房屋建筑图,设备安装图,各种设施,如电气、供排水、采暖通风收尘等系统安装图,非标准设备的制作加工图。
设计者应注意,如有标准设计的,应尽量采用标准设计,而不需另行设计。
粉末冶金的工艺设计人员,除了参加粉末冶金工厂的正规设计外,往往还需作一些粉末冶金的车间设计,与主机所需的粉末冶金零件配套生产,如纺织机械厂常设立铁、铜基粉末冶金零件生产车间,刃具量具厂常设立硬质合金生产车间等。
粉末冶金的车间设计与工厂设计基本相类似,但又有差别。
说它们很相似,是指工厂设计的基本的、主要的内容,车间设计都需要,如工艺流程的选择,产品方案的设计,设备的选型与计算,物料衡算,水、电、汽、气等设施都需要进行设计。
说它们有差别,是指车间仅是一个企业的组成部分,设计内容只管车间内部的生产工艺及所需设施,而不牵涉到外部条件和生活福利设施。
(二)产品方案制定产品方案的设计包括产品产量、品种、质量、牌号及规格的设计。
是粉末冶金工厂设计的重要内容。
产品的总产量由设计任务书规定,产品质量按国家标准规定(或企业标准、或用户要求)。
具体的产品品种、牌号、规格及数量由工艺设计人员确定。
其确定的原则是:1.国内外的现状,生产水平及发展趋势。
2.要适合国情,根据市场的需求。
3.根据工厂条件,尽量采用新技术,提高质量、增加品种,满足用户的需要。
产品方案设计的好坏,直接关系到将来产品的综合利用,产品销售和工厂的经济效益。
(三)工艺流程的选择(1)工艺流程及其表示方法所有产品的生产,均需要经过若干个加工工序才能完成。
为了清晰和表达的方便,往往将产品加工的各个工序及相应工序的半成品,按加工顺序进行排列,然后,用箭头将它们联系起来,而绘制成图。
这种按各工序组成的顺序图,称之为生产工艺流程图。
有时将进料中的原料和辅助材料以及出料中的半成品和反应物与返回料的处理方法都一一在图上标明。
在图中,流程的开头是待加工的物料或半成品,最末尾是成品。
为了使流程图中的加工工序与中间产品能区别开来,可以采用不同的图示符号来表示。
其具体表示方法如图一所示。
除了“图一”的表示方法之外,还有将工艺流程中各工序所使用的主要设备示意图画出,以形象地表示该工序加工的名称和内容,这种以设备组成的流程图叫设备工艺流程图。
(2)工艺流程的选择原则选择工艺流程应采用多种方案,全面地进行技术经济的比较是很有必要的,在比较时应考虑下列原则及要求:1.原材料的特点和性质2.辅助材料的来源、特点和性质3.各项重要的技术经济指标的比较4.原始资料及数据的可靠性5.设备的选型、机械化、自动化6.新老工艺的比较总之,对新工艺流程的要求是,应力争生产效率高、投资少、建厂快、成本低、质量高、技术指标先进、设备容易解决,经济效益好,设计产量能保证。
简言之,就是要达到技术上先进、经济上合理、投产后可靠。
(3)工艺流程的说明在工艺流程选定和论证之后,除用图示法表示外,还要对流程的各个工序依次作详细的说明,即从流程的第一个工序开始,到流程最终的成品结束。
所需要说明的内容大致如下:1.设置该工序的目的和用途。
2.对原辅材料的性质、成分、规格及其他要求。
3.简单叙述工序的过程实质及物理化学原理。
4.简单叙述生产的工艺条件,如温度、压力、保温时间、气体和冷却水的流量,电流密度、电流、电压、功率的大小,溶液浓度、装料量、混合物的成分等。
5.简单地叙述加工设备及对设备的要求。
6.指出过程及质量控制的因素。
7.指出过程中存在的危害性及危险性。
在工艺流程叙述之后,常需要拟出生产工艺规程和各工序设备操作规程。
不同的产品,其工艺规程也不一样。
目前尚无统一的标准格式。
但大致的内容包括:1.产品图及技术要求。
2.产品生产的详细工艺流程图。
3.所用原辅材料的牌号、化学成分、配方及技术要求。
4.各工序使用的主辅设备型号、数量,量程范围、精度等级等。
5.各工序的工艺控制参数,质量控制指标和控制措施。
6.成品性能检查的内容及对包装的要求。
所谓操作规程,一般指设备的操作顺序。
所制定的操作规程一般包括如下内容:1.设备开动前应检查的内容和注意事项。
2.设备启动时的动作顺序。
3.设备运行的安全及额定操作指标,如电流、电压、温度、压力、转速、功率、加料量、装料量等。
4.设备运行的工艺参数,以满足产品质量的要求。
5.设备的正确维护,以保证设备的安全和使用寿命。
所写操作规程一般以条文形式列出,避免冗长繁杂,力求简明扼要,易学易记。
(四)物料平衡计算(1)物料平衡计算所需的原始资料1详细的工艺流程图流程图是物料平衡计算的基本依据。
由流程图可以看出,整个生产过程中物料运行的路线,生产工序的数量及其相互关系。
2. 日产量又叫昼夜处理量。
该数据的来源,是由设计任务书所规定的该厂的年产量,再除以全年的工作日数即得日产量。
这是因为全年任务的完成,必须是每昼夜按计划完成的任务积累所 得。
日产量=年产量/全年工作日数单位:公斤/日,或吨/日全年工作日数可分为两种情况来考虑。
在连续生产的情况下,全年工作日数等于 365天减去设备的检修日数。
设备的修理一般 分为大修、中修、小修与检查。
不同的设备其检修的量也不一样。
因此,修理日数应根据设 备的寿命和生产的实际情况而定,一般的修理日数定为两个月左右,即年工作日数定为 280天到330天。
粉末冶金工厂大多取 300天或330天。
在间断生产时,则年工作日数等于 365天减去全年的星期天(52天)、国家法定假日及其他停工事件,约为 300天左右。
不论采用何种工作制度, 都应合理地组织生产,充分发挥人的积极因素,例如,采用假 日检修,临时抢修等措施,尽量减少检修停工的时间,增加全年工作日数,从而,提高设备 的利用率,减少固定资产的投资。
3. 各工序的产出率和损失率这些数据一般应根据同类企业生产实践中的实际数据,有关文献资料的报道及科学实验的结果,综合考虑确定。
在经过努力可以达到的情况下,所定指标应尽量先进。
因为,这些 指标,是衡量一个设计是否经济合理先进的重要指标之一, 但也要根据实际情况, 不能盲目追求高指标。
工序产出率为某一工序的产量与进入该工序的原料量之比,即工序的损失率分为两种,因为在生产实践中,各道工序的加工总会有这样或那样的损失, 而这些损失,有的是可以在本工序返回处理的,如压制废品, 其损失量,即可返回料量与该工序进料量之比称为可返回损失率,其计算公式是:有的损失则是在本工序或本车间不能处理的物料,如烧结废品。
或者是本工序不可避免的损失,如还原粉末时的化学损失,操作过程中的机械损失等统称为不可返回损失, 其损失量与该工序进料量之比,称为不可返回损失率,即:工序产出率工序产量 工序进料量100%可返回损失率工序可返回料量 该工序进料量100%由上可知,工序的产出率总大于零而小于1。
工序的总损失率等于可返回损失率与不可返回损失率之和。
在同一工序中,工序损失率与该工序产出率之和恒为 100%。
将以上数据按各道工序经过换算或者计算之后, 再进行整理,以表格的形式列出,以利查找,例如表1所示。
表合金的产出率、损失率(以 为例)(2)物料平衡计算的方法、步骤及注意事项首先介绍 自下而上”的计算步骤与方法:1 •按实际情况确定年工作日数,根据任务书中规定的年产量计算出日产量(公斤或吨) ,该日产量即为工艺流程中最后一道工序的产出量。
2•由本工序的产出量和产出率计算出本工序的进料量(公斤或吨)。
本工序进料量 二本工序产出量(公斤或吨)本工序产出率3.由本工序已知的可返回损失率与不可返回损失率,计算出本工序可返回损失量、不可返回损失量。
即:可返回损失率=本工序进料量X 本工序可返回损失率 (公斤) 不可返回损失量=本工序进料量X 本工序不可返回损失率(公斤)4•由本工序的进料量和可返回料量计算出本工序的实际进料量,即本工序实际进料量=本工序进料量-本工序可返回料量(公斤)5•如果本工序实际进料为多组成分,则应按每一组分的百分量分别计算出它们的进料量, 如例1所示。
例1: YT 合金生产流程中的复杂碳化物生产工序 假设已知条件为:工序产出量:48.69公斤复杂碳化物 工序总损失率:1.3%不可返回损失率不可返回损失量 该工序进料量100%其中,可返回损失率1.0% 不可返回损失率0.3%工序产出率:98.7%由此可计算:本工序的进料量二48.69 100二49.33kg98.7可返回料量=49.33 X1%=0.49kg不可返回料量=49.33 X0.3%=0.15kg本工序实际进料量=49.33-0.49=48.84kg (复杂碳化物)以上计算所得48.84kg为本工序的实际进料量,其中,0.15kg在生产中被损失掉,故实际产出量为48.69kg。