切屑的种类及形成
第二章第1节-金属切削过程及切屑类型分析

lfi
lfo
切屑与前刀面的摩擦
第一节 金属切削过程及切屑类型
积屑瘤
在切削速度不高而又能形成连续切屑的情况下,加工一般钢
料或其它塑性材料时,常常在前刀面处粘着一块剖面呈三角
状的硬块,称为积屑瘤。
它的硬度很高,通常是
工件材料的2—3倍,在
切屑
处于比较稳定的状态时,
能够代替刀刃进行切削。
积屑瘤
刀具
积屑瘤
切屑的种类
名称
带状切屑
切屑类型及形成条件
挤裂切屑
单元切屑
崩碎切屑
简图
形态 变形
形成 条件
影响
带状,底面光滑 ,背面呈毛茸状
剪切滑移尚未达 到断裂程度
加工塑性材料, 切削速度较高, 进给量较小, 刀具前角较大
切削过程平稳, 表面粗糙度小, 妨碍切削工作, 应设法断屑
节状,底面光滑有裂 纹,背面呈锯齿状
变形程度表示方法
变形系数
切削层经塑性变形后,厚度增加,长度缩小,宽度基本 不变。可用其表示切削层的变形程度。
◆ 厚度变形系数
h
hch hD
◆ 长度变形系数
L
LD Lch
Lch LD
切屑与切削层尺寸
第一节 金属切削过程及切屑类型
根据体积不变原理,则
h
lc lch
hch hDOMຫໍສະໝຸດ sin(90 OM sin
第二章 金属切削基本理论及应用
第一节 金属切削过程及切屑类型
金属切削过程是指在刀具和切削力的作用下形成切屑的过 程,在这一过程中,始终存在着刀具切削工件和工件材料抵抗切 削的矛盾,产生许多物理现象,如切削力、切削热、积屑瘤、刀 具磨损和加工硬化等。
切屑种类及断屑

其中带状屑连绵不断,经常缠绕工件或刀 具表面,且不易清除。不仅划伤工件表面、 损坏刀具,而且极易伤人。因此,除特殊 情况下,应尽量避免带状屑。
通常采用断屑的方法、即将带状屑折断成 为粒状、半环形状、螺旋状等。
1.车削切削层参数
如图所示,刀具车削工件外圆时,切削刃 上任一点走的是一条螺旋线运动轨迹,整 个切削刃切削出一条螺旋面。工件旋转一 周,车刀由位置I移动到位置II,移动一个 进给量f ,切下金属切削层。此点的参数是 在该点并与该点主运动方向垂直的平面内 度量。
(1) 切削层公称厚度hD 在主切削刃选定点的基面内,垂直 于过渡表面的切削层尺寸,称为切削层公称厚度。切削层截面 的切削厚度为
hD = f sinκr
κr为刀具主偏角,即刀具主切削刃与进给 方向的夹角。根据上式可以看出,进给量f 或刀具主偏角κr增大,车削切削层厚度hD 增大。
(2) 切削层公称宽度bD 在主切削刃选 定点的基面内,沿过渡层表面度量的切削
层尺寸,称为切削层公称宽度。切削层截 面的公称切削宽度为
bD = ap/sinκr
工件材料脆性越大, 刀具前角越小,切削 深度和进给量越大, 越易产生此类切削
(1)切屑的形态可随切削条件不同而改变
(2)可控制切削条件,使切屑形态向有利于生产的
方面转化,保证切削加工的顺利进行和工件的加工
质量
使粒状切屑、
增大前角
节状切屑向带 状切屑转化
提高切 削速度
减小进给量
有利于
使切削过 程平稳
带状切屑是一种连绵 不断的、底面光滑、背 面呈毛茸状的切屑。
切屑的种类及形成.

切屑的种类及形成
一、带状切屑
带状切屑是最常见的—种切屑。
它的内表面是光滑的,外表面是毛茸状的;如用显微镜观察,在侧面上也可以看到剪切面的条纹,但每个层片薄,肉眼看起来大体是平整的。
一般加工塑性金属材料,切削厚度较小,切削速度较高,刀具前角较大,得到的往往是这类切屑。
它的切削过程比较平稳,切削力波动较小,已加工表面粗糙度较小。
二、节状切屑
节状切屑,又称挤裂切屑,和带状切屑不同之处在于外弧表面成锯齿形,内弧表面有时有裂纹。
这种切屑大都在切削速度较低、切屑厚度较大的情况下产生。
三、粒状切屑(单元切削)
当切屑形成时,如果整个剪切面上剪应力超过了材料的破裂强度,则整个单元被切离,成为梯形的粒状切屑。
由于各粒形状相似,所以又叫单元切屑。
四、崩碎切屑
切削脆性金属时,由于材料的塑性很小、抗拉强度较低,刀具切入后,切削层内靠近切削刃和前刀面的局部金属末经明显的塑性变形就在张应力状态下脆断,形成不规则的碎块状切屑,同时使工件加工表面凹凸不平。
工件材料越是硬脆,切削厚度越大时,越容易产生这类切屑。
前三种切屑是切削塑性金属时得到的。
形成带状切屑时切削过程最平稳,切削力的波动最小,形成粒状切屑时切削力波动最大。
在生产中—般最常见到的是带状切屑;当切削厚度大时,则得到节状切屑,单元切屑比较少见。
在形成节状切屑的情况下,改变切削条件:进一步减小前角,或加大切削厚度,就可以得到单元切屑;反之,如加大前角,提高切削速度,减小切削厚度,则可得到带状切屑。
这说明切屑的形态是可以随切削条件而转化的。
切屑种类

资料由:提供!!
切屑种类
(1)带状切屑这是最常见的一种切屑,外形连续不断呈带状,底面光滑。
背面呈毛茸状。
一般以大前角的刀具、较高的切削速度和较小的进给璧切削塑性材料时,形成此类切屑。
其最大的优点是切削过程平稳.切削力变化小,加工表面粗糙度小。
但切屑连续容易产生缠绕.划伤已加工表面,因此耍采取断屑措施。
(2)挤裂(节状)切屑切屑接触面有裂纹,外表面呈锯齿形。
常在以较小前角的刀具.低速和较大进给量切削中等硬度的钢材时产生。
形成挤裂切屑时,切削力会产生一定的波动,造成切削过程不平稳,使加工表面较粗糙。
(3)单元(粒状)切屁在挤裂切屑产生的前提下,当切削速度进一步降低、进给量进一步增大、前角进一步减小时,挤裂切屑的裂纹将会扩展到整个断面上.整个变形单元则被分离,成为梯形的单元切屑。
此时,切削过程更不稳定,加工表面更粗糙。
以上资料由:成都食品包装机械-食品包装机,加工设备,封口机,夹层锅系列-年糕机,河粉
机,米线机,夹层锅,食品包装机,真空包装机,自动灌装机,自动封口机,饮料包装机,内脂豆腐,封口机,锁口机,封盖机,收缩膜机,烧烤机,汤煮炉,开水器,开水炉,水处理设备推荐··。
第三节金属切削过程中的变形
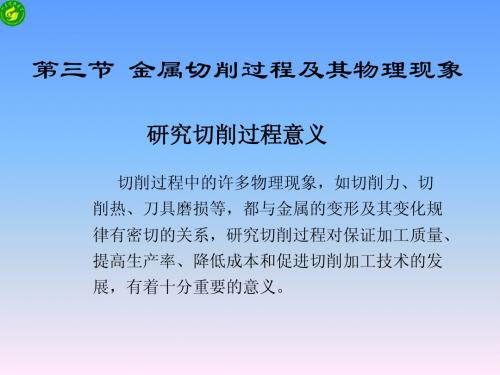
2、第二变形区(纤维化) 第二变形区(纤维化)
(2)剪切角Φ与前刀面上摩擦角β的关系 作用在切屑上的力有 前刀面上的法向力Fn、摩擦力Ff、剪切面上的正压力Fns和剪应力Fs。 简化后作用在切屑上的力 Fr为切削合力、 Φ为剪切角、 β是Fn与Fr之间的夹角摩擦角、Fz是切 削运动方向的分力、和Fy是与运动方向垂直的分力。
a)积屑瘤的形成 切削加工时,切屑与前刀面发生强烈摩擦而形成新鲜表面接触。当接触面具 有适当的温度和较高的压力时就会产生粘结(冷焊)。于是,切屑底层金属 与前刀面冷焊而滞留在前刀面上。连续流动的切屑从粘在刀面的底层上流过 时,在温度、压力适当的情况下,也会被阻滞在底层上。使粘结层逐层在前 一层上积聚,最后长成积屑瘤。 所以积屑瘤的产生以及它的积聚高度与 金属材料的硬化性质有关,也与刃前区 演示1 积屑瘤形成过程 演示2 演示3 的温度和压力分布有关。一般说来,塑 性材料的加工硬化倾向愈强,愈易产生 积屑瘤;温度与压力太低,不会产生积 屑瘤;反之,温度太高,产生弱化作用, 也不会产生积屑瘤。走刀量保持一定时, 积屑瘤高度与切削速度有密切关系。
二、切削层金属的变形
以直角自由切削方式切削塑性材料为基础模型研究切屑形成过程。
大量的实验和理论分析证明,塑性金属切削过程中切 屑的形成过程就是切削层金属的变形过程。
二、切削层金属的变形
1、变形区划分 2、第一变形区(剪切滑移) 第一变形区(剪切滑移) 3、第二变形区(纤维化) 第二变形区(纤维化) 4、第三变形区(纤维化与加工硬化) 第三变形区(纤维化与加工硬化)
1、变形区划分
根据实验,切削层金属在刀具作用下变成切屑的形态大体可划分为三个变形区 第一变形区(剪切滑移) 第二变形区(纤维化) 第三变形区(纤维化与加工硬化)
机械加工切屑形成过程及种类

机械加工切屑形成过程及种类机械加工是指利用机床进行金属材料切削、锉削、抛光等工艺,将工件加工成所需形状和尺寸的加工方法。
在机械加工过程中,由于工具与工件之间的相对运动,会产生切屑。
切屑是指在机械加工过程中,由于切削力的作用和切削部分和工件材料之间的摩擦力的作用,使金属材料脱离工件而形成的废料。
1.切削过程:在机械加工过程中,工具相对于工件进行切削。
切削过程是切屑形成的起点。
切削过程中切削刀具与工件的摩擦力和切削力作用于工件上。
2.金属切错:由于切削刀具和工件的相互作用力,金属材料会发生切削变形,切削很薄的切片和切削薄片之间的间距,即切削错觉。
这种切削错觉会导致材料分离和产生切削切,形成切削筹码。
3.切削筹码分离:随着切削过程的进行,切削刃不断深入工件的表面,形成足够深度的切削面。
在切削过程中,切削筹码被切削刃压向后方,并在切削刃之后分离。
4.切屑形成:随着切削刃逐渐深入工件,切削刃与工件接触的接触面积逐渐增加。
切削刃生成的切削面与工件表面接触,金属材料开始被分离,形成切插和切插在切削刃上的切插形成切屑。
切屑根据其形状和特点可以分为以下几类:1.螺旋卷屑:螺旋卷屑是机械加工中最常见的切屑形式之一、它的形状类似于螺旋形。
螺旋卷屑形成是因为切削刃与工件表面之间的摩擦力和切削力,使金属材料呈螺旋形状被分离。
2.螺纹形卷屑:螺纹形卷屑与螺旋卷屑类似,但具有螺纹形状。
螺纹形卷屑主要在对内螺纹切削中产生。
3.花形卷屑:花形卷屑是螺旋卷屑的一种特殊形式。
它的形状类似于花瓣,具有很高的韧性和弯曲性。
花形卷屑主要在刃具前部有圆角的切削中产生。
4.细末卷屑:细末卷屑是切削薄片脱离工件表面时变形和分离的结果。
这种切屑形态常见于高速切削和高速铣削等加工过程。
5.碎屑:碎屑是在没有明显的切削形状的情况下产生的废料。
碎屑主要在金属材料脆性较高时产生。
总结起来,机械加工切屑的形成过程可以概括为切削过程、金属切错、切削筹码分离和切屑形成。
第一章 金属切削基本知识
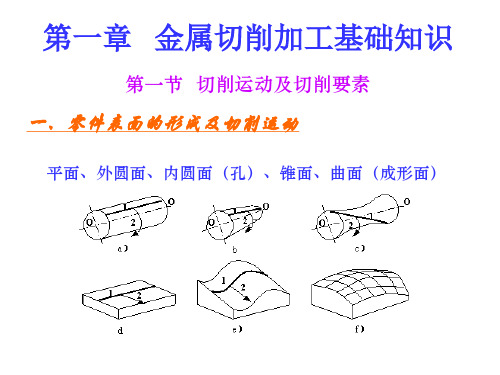
刀具角度对加工过程的影响
1. 前角(0) ① 减小切屑的变形;
作用 ② 减小前刀面与切屑之间的摩擦力。
a .减小切削力和切削热; 所以 0 : b .减小刀具的磨损;
c .提高工件的加工精度和表面质量。
0
0选择:
加工塑性材料和精加工—取大前角( 0 ) 加工脆性材料和粗加工—取小前角(0 )
前角(0)可正、可负、也可以为零。
➢ 偏挤压:金属材料一部分受挤压时 ,OB线以下金属由于母体阻碍,不 能沿AB线滑移,而只能沿OM线滑移
F
B
O
a)正挤压
45° M A F
BO
b)偏挤压
➢ 切削:与偏挤压情况类似。弹性变
M
形→剪切应力增大,达到屈服点→产 生塑性变形,沿OM线滑移→剪切应
O F
力与滑移量继续增大,达到断裂强度
c)切削
后角( 0)只能是正的。
精加工: 0= 80~120 粗加工: 0= 40~80 3 . 主偏角(kr)
作用:改善切削条件,提高刀具寿命。
减小kr:当ap、f 不变时,则 aw 、ac — 使切削条件得到改善,提高了刀具寿命。
dw
ap
dm
但减小kr
Fy 、
n
Fx ,加大工件的变形
挠度,使工件精度降
化学惰性
低 惰性大 惰性小 惰性小 惰性大
耐磨性 低 加工质量
低
较高
高 最高
最高
很高
一般精度 Ra≤0.8 Ra≤0.8 IT7-8 IT7-8
高精度 Ra=0.1-0.05
IT5-6
Ra=0.4-0.2
IT5-6 可替代磨削
低速加 加工对象 工一般
机械制造基础第十章金属切削加工基础知识
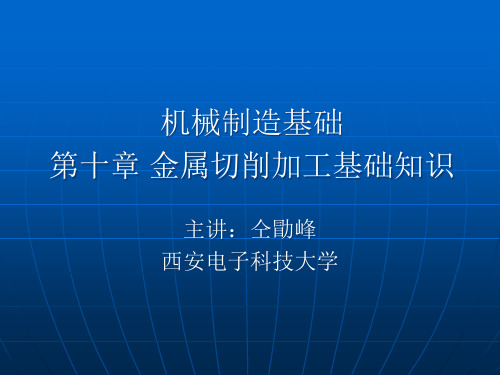
3、切削用量
2)进给量f(mm/r) 指(车)刀具相对于工件旋转一转,在进
给方向的位移量。单位为:mm/r或mm/str。
3、切削用量
3)背吃力量ap(mm) 指工件上已加工表面与待加工表面之间的垂直
距离,单位为:mm。
aP=
Dd 2
式中:d 为已加工表面的直径(mm)。
生产中为提高效率一般对工件分粗、精加工阶
5、刀具结构
5、刀具结构
5、刀具结构
切削过程录像
四、金属切削过程
1、切屑形成及种类 1)切屑形成 塑性材料的切屑过程是一个:挤压变
形切离过程;经历了:弹性变形、塑性变形、挤 裂和切离四个阶段。 2)切屑的种类 ①带状切屑 ②节状切屑 ③崩碎切屑
2、积屑瘤
2、积屑瘤对切削过程的影响 优点: ①硬化刀刃保护刀具; ②增大前角γ利切削; ③粗加工时利用之。 不足:时积时流使工件表面粗糙;精加工时,予以限制。
2、切削运动 1)三个表面 在切削加工过程中,工件上存在三个不断变化的表面,
即:已加工表面、待加工表面和过渡表面。 (1)待加工表面 工件上即将切去切屑的表面。 (2)已加工表面 工件上已切去切屑的表面。 (3)过渡表面 工件上由切削刃形成的那部分表面,
即已加工表面和待加工表面之间的过渡表面。
2、切削运动
4、车刀的几何角度及其作用
2)后角αo 指主后刀面与切削平面之间的夹角。 作用:减小后刀面与工件之间的摩擦,它也和
前角一样影响刃口的强度和锋利程度。 选择原则:与前角相似,一般后角值为6~8
度。 3)主偏角 γ 指主切削平面与假定工作平面间夹角。
作用:影响切削刃工作长度、背向力、刀尖强 度和散热条件;主偏差越小,背向力越大,切削 刃工作长度越大,散热条件越好。
- 1、下载文档前请自行甄别文档内容的完整性,平台不提供额外的编辑、内容补充、找答案等附加服务。
- 2、"仅部分预览"的文档,不可在线预览部分如存在完整性等问题,可反馈申请退款(可完整预览的文档不适用该条件!)。
- 3、如文档侵犯您的权益,请联系客服反馈,我们会尽快为您处理(人工客服工作时间:9:00-18:30)。
切屑的种类及形成
一、带状切屑
带状切屑是最常见的—种切屑。
它的内表面是光滑的,外表面是毛茸状的;如用显微镜观察,在侧面上也可以看到剪切面的条纹,但每个层片薄,肉眼看起来大体是平整的。
一般加工塑性金属材料,切削厚度较小,切削速度较高,刀具前角较大,得到的往往是这类切屑。
它的切削过程比较平稳,切削力波动较小,已加工表面粗糙度较小。
二、节状切屑
节状切屑,又称挤裂切屑,和带状切屑不同之处在于外弧表面成锯齿形,内弧表面有时有裂纹。
这种切屑大都在切削速度较低、切屑厚度较大的情况下产生。
三、粒状切屑(单元切削)
当切屑形成时,如果整个剪切面上剪应力超过了材料的破裂强度,则整个单元被切离,成为梯形的粒状切屑。
由于各粒形状相似,所以又叫单元切屑。
四、崩碎切屑
切削脆性金属时,由于材料的塑性很小、抗拉强度较低,刀具切入后,切削层内靠近切削刃和前刀面的局部金属末经明显的塑性变形就在张应力状态下脆断,形成不规则的碎块状切屑,同时使工件加工表面凹凸不平。
工件材料越是硬脆,切削厚度越大时,越容易产生这类切屑。
前三种切屑是切削塑性金属时得到的。
形成带状切屑时切削过程最平稳,切削力的波动最小,形成粒状切屑时切削力波动最大。
在生产中—般最常见到的是带状切屑;当切削厚度大时,则得到节状切屑,单元切屑比较少见。
在形成节状切屑的情况下,改变切削条件:进一步减小前角,或加大切削厚度,就可以得到单元切屑;反之,如加大前角,提高切削速度,减小切削厚度,则可得到带状切屑。
这说明切屑的形态是可以随切削条件而转化的。