数控机床加工精度分析与应用.
数控机床的加工精度误差分析与精度校正技巧
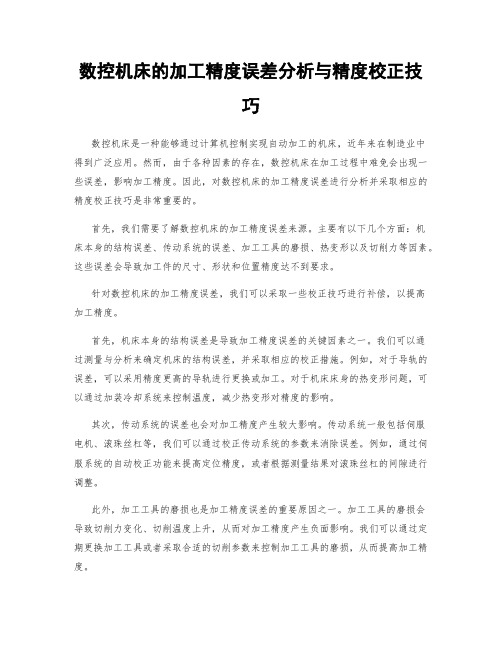
数控机床的加工精度误差分析与精度校正技巧数控机床是一种能够通过计算机控制实现自动加工的机床,近年来在制造业中得到广泛应用。
然而,由于各种因素的存在,数控机床在加工过程中难免会出现一些误差,影响加工精度。
因此,对数控机床的加工精度误差进行分析并采取相应的精度校正技巧是非常重要的。
首先,我们需要了解数控机床的加工精度误差来源。
主要有以下几个方面:机床本身的结构误差、传动系统的误差、加工工具的磨损、热变形以及切削力等因素。
这些误差会导致加工件的尺寸、形状和位置精度达不到要求。
针对数控机床的加工精度误差,我们可以采取一些校正技巧进行补偿,以提高加工精度。
首先,机床本身的结构误差是导致加工精度误差的关键因素之一。
我们可以通过测量与分析来确定机床的结构误差,并采取相应的校正措施。
例如,对于导轨的误差,可以采用精度更高的导轨进行更换或加工。
对于机床床身的热变形问题,可以通过加装冷却系统来控制温度,减少热变形对精度的影响。
其次,传动系统的误差也会对加工精度产生较大影响。
传动系统一般包括伺服电机、滚珠丝杠等,我们可以通过校正传动系统的参数来消除误差。
例如,通过伺服系统的自动校正功能来提高定位精度,或者根据测量结果对滚珠丝杠的间隙进行调整。
此外,加工工具的磨损也是加工精度误差的重要原因之一。
加工工具的磨损会导致切削力变化、切削温度上升,从而对加工精度产生负面影响。
我们可以通过定期更换加工工具或者采取合适的切削参数来控制加工工具的磨损,从而提高加工精度。
另外,热变形也是影响加工精度的重要因素。
随着机床的连续工作,温度会逐渐升高,导致机床的热变形。
我们可以通过在机床上安装温度传感器,监测温度的变化,然后根据变化的温度对加工精度进行校正。
此外,通过改进机床的散热系统,减少热量的积聚,也可以有效地降低热变形对加工精度的影响。
最后,我们还可以通过控制切削力来提高加工精度。
切削力对加工精度具有较大的影响,对切削力的控制可以通过调整切削参数(如切削速度、进给量等)来实现。
4--数控铣床的性能指标与功能
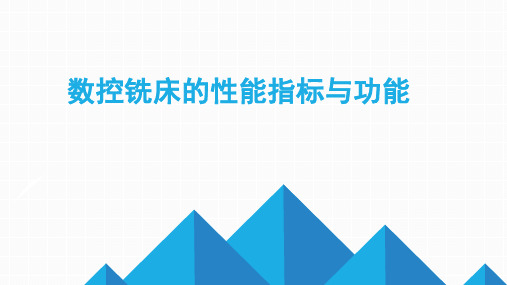
• 6、模态、非模态指令 模态指令也称续效指令,一经程序段中指 令,便一直有效,直到以后程序段中出现同组另一指令或被其它 指令取消是才失效。
• 三、程序编制的分类 • 1.编程的两大方法 • 1)手工编程:由操作者或程序员以人工方式完成整个加工程序编制工作的
方法。
• 2)自动编程:主要由计算机及其外围设备组成的自动编程系统完成加工程 序编制的方法。
• 3、坐标行程
• 数控机床坐标轴 X 、 Y 、 Z 的行程大小,构成数控机床的空间加工范围,即加 工零件的大小。
• 4、刀库容量和换刀时间
• 刀库容量是指刀库能存放加工所需要的刀具数量。目前常见的中小型加工中心多 为16~60把,大型加工中心达100 把以上。
• 换刀时间指有自动换刀系统的数控机床,将主轴上使用的刀具与装在刀库上的下 一工序需用的刀具进行交换所需要的时间。目前国内生产的数控机床的换刀时间可 达到4∽5s。
数控机床的加工精度误差分析与校正方法
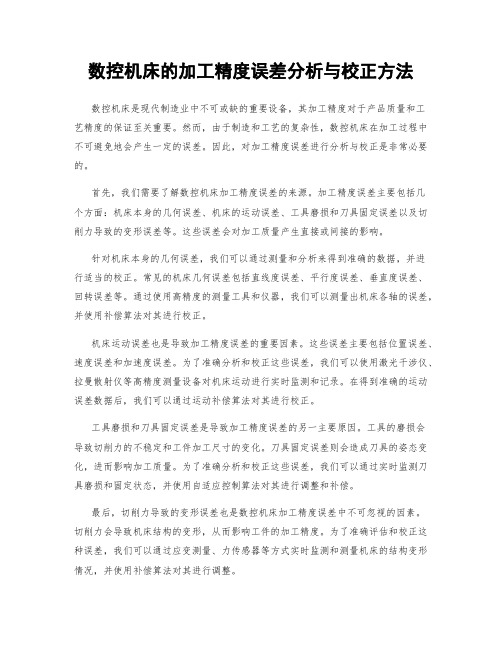
数控机床的加工精度误差分析与校正方法数控机床是现代制造业中不可或缺的重要设备,其加工精度对于产品质量和工艺精度的保证至关重要。
然而,由于制造和工艺的复杂性,数控机床在加工过程中不可避免地会产生一定的误差。
因此,对加工精度误差进行分析与校正是非常必要的。
首先,我们需要了解数控机床加工精度误差的来源。
加工精度误差主要包括几个方面:机床本身的几何误差、机床的运动误差、工具磨损和刀具固定误差以及切削力导致的变形误差等。
这些误差会对加工质量产生直接或间接的影响。
针对机床本身的几何误差,我们可以通过测量和分析来得到准确的数据,并进行适当的校正。
常见的机床几何误差包括直线度误差、平行度误差、垂直度误差、回转误差等。
通过使用高精度的测量工具和仪器,我们可以测量出机床各轴的误差,并使用补偿算法对其进行校正。
机床运动误差也是导致加工精度误差的重要因素。
这些误差主要包括位置误差、速度误差和加速度误差。
为了准确分析和校正这些误差,我们可以使用激光干涉仪、拉曼散射仪等高精度测量设备对机床运动进行实时监测和记录。
在得到准确的运动误差数据后,我们可以通过运动补偿算法对其进行校正。
工具磨损和刀具固定误差是导致加工精度误差的另一主要原因。
工具的磨损会导致切削力的不稳定和工件加工尺寸的变化。
刀具固定误差则会造成刀具的姿态变化,进而影响加工质量。
为了准确分析和校正这些误差,我们可以通过实时监测刀具磨损和固定状态,并使用自适应控制算法对其进行调整和补偿。
最后,切削力导致的变形误差也是数控机床加工精度误差中不可忽视的因素。
切削力会导致机床结构的变形,从而影响工件的加工精度。
为了准确评估和校正这种误差,我们可以通过应变测量、力传感器等方式实时监测和测量机床的结构变形情况,并使用补偿算法对其进行调整。
总结来说,数控机床的加工精度误差分析与校正是确保产品质量和工艺精度的关键步骤。
在这个过程中,我们需要准确地识别和分析加工精度误差的来源,并采取相应的校正措施。
数控机床的精度与应用范围
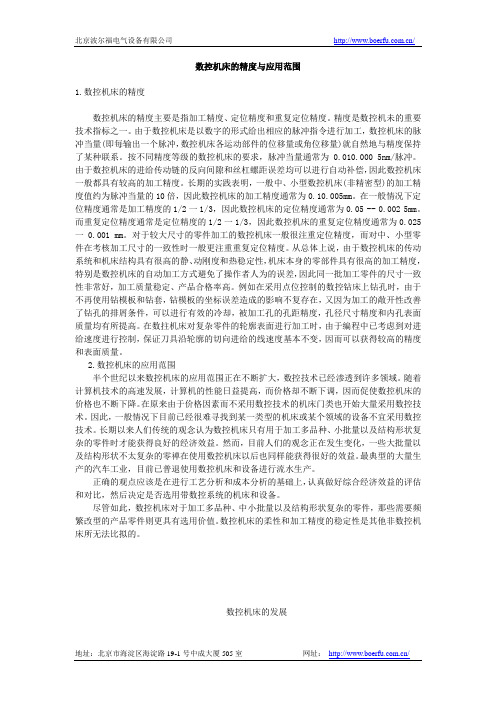
数控机床的精度与应用范围1.数控机床的精度数控机床的精度主要是指加工精度、定位精度和重复定位精度。
精度是数控机未的重要技术指标之一。
由于数控机床是以数字的形式给出相应的脉冲指令进行加工,数控机床的脉冲当量(即每输出一个脉冲,数控机床各运动部件的位移量或角位移量)就自然地与精度保持了某种联系。
按不同精度等级的数控机床的要求,脉冲当量通常为0.010.000 5nm/脉冲。
由于数控机床的进给传动链的反向间隙和丝杠螺距误差均可以进行自动补偿,因此数控机床一般都具有较高的加工精度。
长期的实践表明,一般中、小型数控机床(非精密型)的加工精度值约为脉冲当量的10倍,因此数控机床的加工精度通常为0.10.005mm。
在一般情况下定位精度通常是加工精度的1/2一1/3,因此数控机床的定位精度通常为0.05 -- 0.002 5mm。
而重复定位精度通常是定位精度的1/2一1/3,因此数控机床的重复定位精度通常为0.025一0.001 mm。
对于较大尺寸的零件加工的数控机床一般很注重定位精度,而对中、小型零件在考核加工尺寸的一致性时一般更注重重复定位精度。
从总体上说,由于数控机床的传动系统和机床结构具有很高的静、动刚度和热稳定性,机床本身的零部件具有很高的加工精度,特别是数控机床的自动加工方式避免了操作者人为的误差,因此同一批加工零件的尺寸一致性非常好,加工质量稳定、产品合格率高。
例如在采用点位控制的数控钻床上钻孔时,由于不再使用钻模板和钻套,钻模板的坐标误差造成的影响不复存在,又因为加工的敞开性改善了钻孔的排屑条件,可以进行有效的冷却,被加工孔的孔距精度,孔径尺寸精度和内孔表面质量均有所提高。
在数拄机床对复杂零件的轮廓表面进行加工时,由于编程中已考虑到对进给速度进行控制,保证刀具沿轮廓的切向进给的线速度基本不变,因而可以获得较高的精度和表面质量。
2.数控机床的应用范围半个世纪以来数控机床的应用范围正在不断扩大,数控技术已经渗透到许多领域。
数控机床的加工精度达到多少

数控机床的加工精度达到多少数控机床加工精度是指零件加工后的实际几何参数(尺寸、形状和位置)与图纸规定的理想几何参数符合的程度。
这种相符合的程度越高,加工精度也越高。
加工精度高数控机床的加工精度一般可达0.050.1MM,数控机床是按数字信号形式控制的,数控装置每输出一脉冲信号,则机床移动部件移动一具脉冲当量(一般为0.001MM),而且机床进给传动链的反向间隙与丝杆螺距平均误差可由数控装置进行曲补偿,因此,数控机床定位精度比较高,不过目前各个数控机床的加工精度根据机床品牌,机床类型,数控机床操作人员技术等因素都会造成数控机床的加工精度差异。
数控机床的加工精度一般可达0.050.1MM,数控机床是按数字信号形式控制的,数控装置每输出一脉冲信号,则机床移动部件移动一具脉冲当量(一般为0.001MM),而且机床进给传动链的反向间隙与丝杆螺距平均误差可由数控装置进行曲补偿,因此,数控机床定位精度比较高。
数控机床在进行加工过程中难免会受到各种各样因素的影响,使得其加工精度产生一定的偏差,给生产生活带来一些不便。
怎样提高数控机床加工精度是工程师们很关心的事情。
数控机床加工中的位置误差对加工精度的影响位置误差是指加工后零件的实际表面、轴线或对称平面之间的相互位置相对于其理想位置的变动量或偏离程度,如垂直度、位置度、对称度等。
数控机床加工中的位置误差通常指死区误差,产生位置误差的原因主要在机床零件加工时由于传动时产生的间隙和弹性变形导致加工误差,以及在加工中,机床的刀头需要克服摩擦力等因素导致产生位置误差。
在开环系统中位置精度受到的影响是很大的,而在闭环随动系统中,则主要取决于位移检测装置的精度和系统的速度放大系数,一般影响较小。
数控机床加工中由于几何误差导致的加工精度误差数控机床加工中,由于刀具和夹具在受外力和加工中产生的热量等外界因素的影响下,机床的几何精度受到影响,机床上加工的零部件产生几何变形,从而导致产生几何误差。
解析数控车床加工精度的影响因素及提高措施
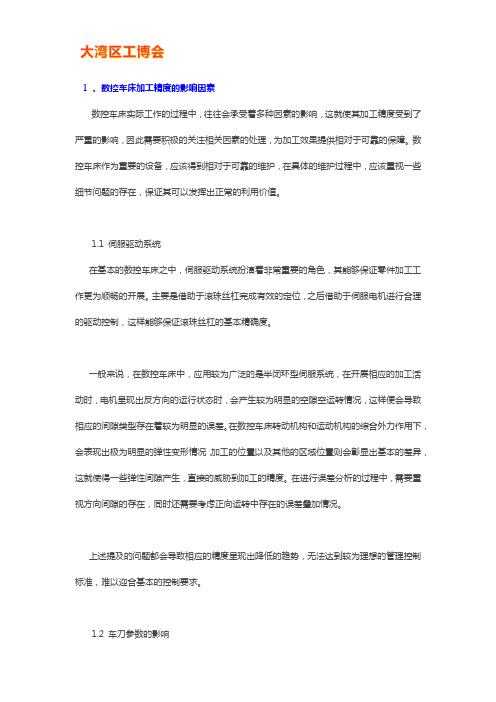
1 、数控车床加工精度的影响因素数控车床实际工作的过程中,往往会承受着多种因素的影响,这就使其加工精度受到了严重的影响,因此需要积极的关注相关因素的处理,为加工效果提供相对于可靠的保障。
数控车床作为重要的设备,应该得到相对于可靠的维护,在具体的维护过程中,应该重视一些细节问题的存在,保证其可以发挥出正常的利用价值。
1.1 伺服驱动系统在基本的数控车床之中,伺服驱动系统扮演着非常重要的角色,其能够保证零件加工工作更为顺畅的开展。
主要是借助于滚珠丝杠完成有效的定位,之后借助于伺服电机进行合理的驱动控制,这样能够保证滚珠丝杠的基本精确度。
一般来说,在数控车床中,应用较为广泛的是半闭环型伺服系统,在开展相应的加工活动时,电机呈现出反方向的运行状态时,会产生较为明显的空隙空运转情况,这样便会导致相应的间隙类型存在着较为明显的误差。
在数控车床转动机构和运动机构的综合外力作用下,会表现出极为明显的弹性变形情况,加工的位置以及其他的区域位置则会彰显出基本的差异,这就使得一些弹性间隙产生,直接的威胁到加工的精度。
在进行误差分析的过程中,需要重视方向间隙的存在,同时还需要考虑正向运转中存在的误差叠加情况。
上述提及的问题都会导致相应的精度呈现出降低的趋势,无法达到较为理想的管理控制标准,难以迎合基本的控制要求。
1.2 车刀参数的影响通常来讲,在数控车床的加工实践中,往往是借助于编程控制的基本手段落实车刀的调整,保证可以更加顺畅的开展零部件的切削工作,由此让其基本的形状符合相应的要求。
在车削加工的基本环节之中,车刀一般会反映出主偏角以及刀尖圆弧半径的基本数值,在对棒料进行适当的加工时,轴向的尺寸还是很容易产生一些误差问题,面对这样的情况应该做出合理的分析,判断这类误差和主偏角往往是呈现出一种反比的关系,当不断地增加相应的主偏角之后,相应的误差可以适当的降低,但是对比于刀尖圆弧半径来看,两者之间还是存在着正比的关联。
如果在具体加工的过程中车刀的参数发生了较为显著的变化,会使得相应的精度受到较为直接的影响。
CNC机床加工中的加工精度评估与标准
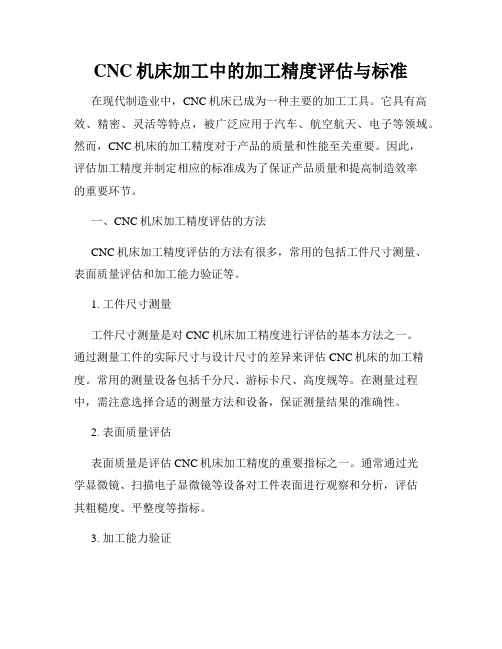
CNC机床加工中的加工精度评估与标准在现代制造业中,CNC机床已成为一种主要的加工工具。
它具有高效、精密、灵活等特点,被广泛应用于汽车、航空航天、电子等领域。
然而,CNC机床的加工精度对于产品的质量和性能至关重要。
因此,评估加工精度并制定相应的标准成为了保证产品质量和提高制造效率的重要环节。
一、CNC机床加工精度评估的方法CNC机床加工精度评估的方法有很多,常用的包括工件尺寸测量、表面质量评估和加工能力验证等。
1. 工件尺寸测量工件尺寸测量是对CNC机床加工精度进行评估的基本方法之一。
通过测量工件的实际尺寸与设计尺寸的差异来评估CNC机床的加工精度。
常用的测量设备包括千分尺、游标卡尺、高度规等。
在测量过程中,需注意选择合适的测量方法和设备,保证测量结果的准确性。
2. 表面质量评估表面质量是评估CNC机床加工精度的重要指标之一。
通常通过光学显微镜、扫描电子显微镜等设备对工件表面进行观察和分析,评估其粗糙度、平整度等指标。
3. 加工能力验证加工能力验证是评估CNC机床加工精度的定量方法之一。
通过制定一系列的加工试验,比如圆度试验、直线度试验等,得出CNC机床的实际加工能力。
加工能力验证可以帮助制定合理的加工参数和工艺流程,提高加工效率和加工精度。
二、CNC机床加工精度的评估标准为了确保CNC机床加工的稳定性和精度,制定相应的评估标准至关重要。
下面介绍几种常用的CNC机床加工精度评估标准。
1. 国家标准不同国家制定了相应的CNC机床加工精度评估标准。
例如中国的《数控机床精度检验标准》(GB/T 16672-2008)规定了CNC机床的加工精度分级与检验方法,包括几何精度、运动精度和位置精度等指标。
2. 行业标准各行业也制定了相应的CNC机床加工精度评估标准。
以航空航天行业为例,美国航空航天协会(AIA)制定了《航空航天产品精度与质量评估标准》(AIA NAS-970)。
该标准覆盖了航空航天产品的设计、制造和验收等方面,对CNC机床加工精度进行了详细的规定。
数控加工精度数控加工精度
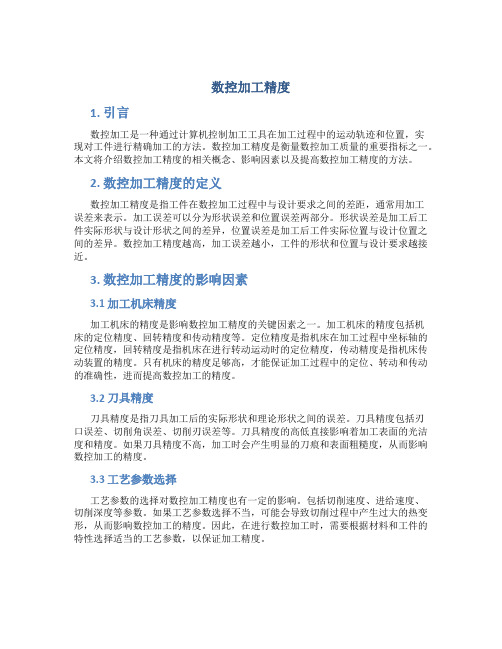
数控加工精度1. 引言数控加工是一种通过计算机控制加工工具在加工过程中的运动轨迹和位置,实现对工件进行精确加工的方法。
数控加工精度是衡量数控加工质量的重要指标之一。
本文将介绍数控加工精度的相关概念、影响因素以及提高数控加工精度的方法。
2. 数控加工精度的定义数控加工精度是指工件在数控加工过程中与设计要求之间的差距,通常用加工误差来表示。
加工误差可以分为形状误差和位置误差两部分。
形状误差是加工后工件实际形状与设计形状之间的差异,位置误差是加工后工件实际位置与设计位置之间的差异。
数控加工精度越高,加工误差越小,工件的形状和位置与设计要求越接近。
3. 数控加工精度的影响因素3.1 加工机床精度加工机床的精度是影响数控加工精度的关键因素之一。
加工机床的精度包括机床的定位精度、回转精度和传动精度等。
定位精度是指机床在加工过程中坐标轴的定位精度,回转精度是指机床在进行转动运动时的定位精度,传动精度是指机床传动装置的精度。
只有机床的精度足够高,才能保证加工过程中的定位、转动和传动的准确性,进而提高数控加工的精度。
3.2 刀具精度刀具精度是指刀具加工后的实际形状和理论形状之间的误差。
刀具精度包括刃口误差、切削角误差、切削刃误差等。
刀具精度的高低直接影响着加工表面的光洁度和精度。
如果刀具精度不高,加工时会产生明显的刀痕和表面粗糙度,从而影响数控加工的精度。
3.3 工艺参数选择工艺参数的选择对数控加工精度也有一定的影响。
包括切削速度、进给速度、切削深度等参数。
如果工艺参数选择不当,可能会导致切削过程中产生过大的热变形,从而影响数控加工的精度。
因此,在进行数控加工时,需要根据材料和工件的特性选择适当的工艺参数,以保证加工精度。
3.4 材料特性不同材料的特性也会对数控加工精度产生影响。
有些材料容易产生切削刃磨损,有些材料容易产生热变形,还有些材料容易产生划伤等问题。
在进行数控加工时,需要根据不同材料的特性选择合适的刀具和工艺参数,以提高数控加工的精度。
- 1、下载文档前请自行甄别文档内容的完整性,平台不提供额外的编辑、内容补充、找答案等附加服务。
- 2、"仅部分预览"的文档,不可在线预览部分如存在完整性等问题,可反馈申请退款(可完整预览的文档不适用该条件!)。
- 3、如文档侵犯您的权益,请联系客服反馈,我们会尽快为您处理(人工客服工作时间:9:00-18:30)。
数控机床加工精度分析与应用王美姣(河南职业技术学院机电系,河南郑州450046摘要:数控机床是一种高精度、高效率、高柔性、高技术的现代化机电设备,其应用越来越普及。
提高机床效率、保证加工精度、确保产品品质是生产所必需。
关键词:数控机床;加工精度;应用中图分类号:TG659文献标识码:B文章编号:167125276(20040320025204Application and analysis of manufacturing precision of NC machinesWAN G Mei2jiao(Henan Vocational&Technical College,Zhengzhou Henan450046,ChinaAbstract:A NC machine tool is a modern mechatronic equipment which has advantage of high precision,high efficiency,high flexibility and advanced technologies.NC machines are being used in more and more fields.It is needed in production to improve efficiency,ensure precision and quality of products.K ey w ords:NC machine tool;manufacturing precision;application数控机床是按照加工程序自动加工零件,它具有加工精度高、生产效率高、产品品质稳定、加工过程柔性好、加工功能强等特点。
加工过程中,只要改变加工程序就能达到加工不同形状、不同精度零件的目的。
但并不是每个数控操作人员都能在规定的时间内保证工件的加工精度,提高机床效率,确保产品合格。
本文总结长期以来的实践经验,结合理论分析,从以下几方面提出几点粗浅看法。
1工件坐标系设定对加工精度的影响工件坐标系是编程人员在编写程序时,在工件上建立的坐标系,其原点即为工件原点(也称工件零点或编程原点。
理论上是由编程人员任意设定的,但实际上,它是编程人员根据零件特点为了编程方便以及尺寸的直观性而设定的。
选择工件坐标系时一般应遵循如下原则:a尽可能将工件原点选择在工艺定位基准上,这样有利于加工精度的提高;b尽量将工件原点选择在零件的尺寸基准上,这样便于坐标值的计算,减少错误率(当尺寸基准与工艺基准不重合时,则要考虑由基准不重合产生的误差;c尽量选在精度较高的工件表面上,以提高被加工零件的加工精度;d对于对称零件,应设在对称中心上,一般零件应设在工件轮廓某一角上,且Z轴方向上原点一般设在工件表面;e对于卧式加工中心最好把工件原点设在回转中心上,即设置在工作台回转中心与Z轴连线的适当位置上;f应将刀具起点和编程原点设在同一处,这样可以简化程序,便于计算,提高加工精度;对一般零件,仅按上述原则确定工件坐标系,即能保证其加工精度。
但对于复杂、特殊零件,就要综合考虑各种因素对加工精度的影响。
111在立式加工中心上加工畸形工件根据畸形工件的结构特点,往往在一个零件上要选择两个或两个以上的坐标系,这时就要根据零件的形状特征、夹紧方式及各加工部位的精度高低等因素综合考虑:a建立几个坐标系;b先加工哪个坐标系的哪个表面才能提高整个零件的加工精度;c坐标系间定位尺寸的精度对各部位加工精度的影响(某些定位基准可能不在工件上。
112在卧式加工中心上加工箱体类零件根据箱体类零件的结构特点,不仅除上下底面之外的四个侧面需要分别建立四个定位坐标系,而且每一侧面上有时还需建立几个坐标系,这时就必须考虑各加工精度如何保证。
如:a机床回转中心坐标精度对零件相对两侧面坐标系的建立来说,它直接影响两相对侧面通孔的同轴度;b每一侧面上几个坐标系建立时,加工工序的设计对加工精度的影响;c以底面为基准的的装夹精度,直接影响孔轴线相对端面的垂直度;d基准底面精度对孔的中心高精度的影响。
当然,零件结构不同,精度要求不同,坐标系的建立也不一样,不管何种情况都应详细分析优先选用哪一原则或同时兼顾哪几项原则,才能有利于保证零件加工精度、提高工作效率,降低加工成本。
2指令选择对加工精度的影响以下分析皆以加工中心为例aG92指令与G54~G59的选择。
G92指令设定工件坐标系是在程序中,用程序段直接给出,指令中的坐标值,并不使机床产生运动,仅代表当前刀具的刀位点在工件坐标系中的坐标值。
因此,操作者在使用写有坐标系设定指令的程序时,必须在工件安装后检查或调整刀具的刀位点与工件坐标系之间的关系,保证机床处于加工起始点(对刀点,以确保在机床上设定的工件坐标系,与编程时在零件上规定的工件坐标系在位置上重合一致,否则将降低零件加工精度。
并且G92X Y Z各坐标轴不可省略,否则未被设定的坐标轴将按以前的记忆执行,这样刀具在运动时,可能到达不了预期的位置,甚至造成事故。
G54~G59指令设置工件坐标系时,首先必须通过偏置页面,预先将G54~G59设置在寄存器中,编程中再用程序选择,操作者安装工件后,通过测量来确定工件原点与机床原点偏移量。
目前的CNC系统一般都配有测量头,手动操作能准确测量该偏移量,其测量误差对工件的加工精度影响很小,可以忽略不计,用MDI方式存入到G54~G59的原点寄存器中,其后系统在执行程序中,就可以按照工件坐标系中的坐标值来运动了。
并且同一工件上能同时设定六个坐标系,特别是加工复杂零件更显示其优越性,事实证明,实际加工中不管何种零件,选用G54~G59指令省时准确又方便,且出错率极低。
bG40、G41、G42的选择。
G40、G41、G42为刀具半径补偿指令,G40是刀具半径补偿功能撤消指令、G41、G42分别是左偏、右偏指令。
如果机床没有刀具半径补偿功能,那么当刀具因更换、磨损或重磨而改变半径,或因粗加工时的余量不同等原因,而改变了刀具中心偏移量时,都要按刀具中心轨迹重新编制加工程序,这将是极其繁琐,并且影响生产的正常进行。
为解决此问题,数控系统一般都具有半径自动补偿功能。
在编程时不需要计算刀具中心运动轨迹,而可按工件的轮廓直接编程,刀具半径改变时在控制面板上用手工输入方式改变刀具半径补偿值即可,而不必修改程序,极大的方便了编程和加工。
据此该指令的应用将会大大提高加工效率,但在工厂的应用并非如此,如若选择使用不当,不仅会降低工件的加工精度,严重还会使工件报废,并且在某些情况下根据零件的具体结构并不总是按照零件轮廓进行编程。
举例如下:如图1为毛胚工件,D30孔已加工,现需加工长方孔。
建立坐标系如图,刀具为D16立铣刀;方法一:选用G40、G42指令程序如下:N10G90G00G54X0Y0;N20Z10.S300M03;N30G01Z-5.F1000;N40G42X-23.D31F100;N50Y17.5;N60X23.;N70Y-17.5;N80X-23.;N90Y17,5;N100G0Z50.;N110G40G91G28Z0Y0M05; N120M30;图1零件工序图方法二:选用G40、G41指令只对部分程序加以修改,其余相同N40G41X-23.D31F100;N50Y-17.5;N60X23.;N70Y17.5;N80X -23.N90Y0;方法一运行结果:1最后铣刀停留在B 点,虽说是按零件轮廓编程,但很明显多铣一个刀具半径,工件报废。
2加工表面粗糙度不理想。
3两尺寸精度通过半径补偿完全保证。
方法二运行结果:尺寸精度及表面粗糙度都完全保证。
分析:两种方法的差异就在于分别采用了G42(刀径右补、G41(刀径左补,从而决定了顺铣、逆铣的选择。
逆铣时(如图2(a ,切削厚度从零开始逐渐增大,当实际前角出现负值时,刀齿在加工表面上挤压、滑行,不能切除切屑,既增大了后刀面的磨损,又使工件表面产生较严重的冷硬层。
当下一个刀齿切入时,又在冷硬层表面上挤压、滑行,更加剧了铣刀的磨损,使工件加工后的表面粗糙度值也较大。
从力学角度分析,铣刀作用于工件上的纵向分力(图2(a 中F e ,总是与工作台的进给方向相反,即使机床进给机构有间隙,也始终能保持良好的接触,从而使进给运动平稳;但垂直分力(图2(a 中F v 的大小和方向是变化的,并且当刀齿切离工件时,F v 向上,有挑起工件的趋势,引起工作台的振动,从而影响工件表面的粗糙度。
所以当工件表面有硬皮,机床的进给机构有间隙时应选用逆铣。
图2顺铣与逆铣的受力分析顺铣时(如图2(b ,刀齿的切削厚度从最大开始,避免了挤压、滑行现象;并且垂直分力F u 始终压向工作台,从而使切削平稳,提高铣刀耐用度和加工表面质量;但纵向分力F e 与进给运动方向相同,如果进给机构有间隙,会造成工作台窜动,使铣削进给量不均匀,严重时会打刀,但一般数控机床,特别是加工中心,进给机构间隙很小,造成的影响可以忽略不计。
因此,当工件表面无硬皮时,应选用顺铣,特别是精铣,当工件材料为铝镁合金、钛合金或耐热合金时更应尽量采用顺铣。
由上述分析可知,选择刀径补G41和G42时应注意:1结合零件材料、机床特点及加工精度,适当选择G41和G42。
2使用G41和G42指令时,应仔细分析刀具运动轨迹,以免多切(长方形孔或少切(通槽。
3需要改变刀径补偿数值大小时,切忌改错方向,造成废品。
3气温及工艺系统热变形对加工精度的影响311气温分析物体,特别是金属材料具有热胀冷缩性质,温度的变化会引起零件尺寸的改变。
虽然零件的尺寸变化微小,但对于数控机床(很多数控车间并不能保证标准室温条件加工的高精度零件却不容忽视,否则会出现在某一温度条件下加工的零件合格,而在另一温度条件下测量就不合格。
如一精度要求较高的尺寸,在夏季加工与冬季加工就不一样,夏季因温度较高,机床工艺系统、刀具、工件变形较大,为保证零件在其他温度条件下也合格,加工好测量时就应使实际偏差靠近上偏差,这样即使在冬季测量时,就不会因温度较低尺寸变小而超差。
同理,冬季加工零件时,就应使实际偏差靠近下偏差,春秋季节应使实际偏差靠近上下偏差的中间位置,孔或轴类零件高精度尺寸皆应如此。
312工艺系统热变形分析在机械加工过程中,由于切削热、摩擦热等影响,使工艺系统各部分的温度升高不等,产生复杂的变形,从而改变了工件、刀具及机床之间的相互位置,破坏了工件和刀具之间相对运动的准确性,改变了已调整好的加工尺寸,严重影响了零件的加工精度。
据此,数控机床在设计制造时已考虑了这些因素的影响,使数控设备的传动系统和机床结构都具有很高的刚度和热稳定性,并对反向间隙与丝杠螺距误差等由计算机软件实现自动补偿,大大提高了加工精度。