钢板超声波手动检测方法操作细则
超声波检测工艺规程

超声波检测工艺规程1适用范围1.1 本工艺适用于板厚为6-250mm得板材、碳素钢与低合金钢锻件、母材壁厚8—400mm得全焊透熔化焊对接焊缝及壁厚大于等于4mm,管径为57—1200mm碳素钢与低合金石油天然气长输、集输与其她油气管道环向对接焊缝、钢质储罐对接焊缝得超声波检测等、1。
2 本工艺规定了使用A型脉冲反射式超声波探伤仪进行检测过程中,对受检设备做出准确判定应遵循得一般程序与要求。
1、3 引用标准JB4730/T—2005《承压设备无损检测》SY/T4109-2005《石油天然气钢质管道无损检测》GB11345-89《钢焊缝手工超声波探伤方法与探伤结果得分级》JB/T9214-1999《A型脉冲反射式超声探伤系统测试方法》JB/T10062-1999《超声探伤用探头性能测试方法》GB50128—2005《立式圆筒形钢制焊接储罐施工及验收规范》2对检测人员得要求2、1 从事超声波检测人员必须经过培训,持证上岗。
只有取得质量技术监督部门颁发得超声波检测技术等级证书得人,方可独立从事与该等级相应得超声波检测工作、2、2 检测人员应具有良好得身体素质,其校正视力不得低于 5.0,并每年检查一次。
2、3检测人员应严格执行《检测作业安全防护指导书》与其它安全防护规定,确保安全生产。
3检测程序3、1根据工程特点与本工艺编制具体得《无损检测技术方案》。
3.2受检设备经外观检查合格后,由现场监理或检验员开据《无损检测指令》或《无损检测委托单》到检测中心。
3。
3 检测人员按指令或委托单要求进行检测准备,技术人员根据实际情况编制《探伤工艺卡》、3、4 检测人员按《超声波探伤仪调试作业指导书》等工艺文件进行设备调试。
3.5 外观检查合格后,施加耦合剂,实施检测,做好《超声波检测记录》。
3。
7 根据检测结果与委托单,填写相应得回执单或合格通知单、若有返修,还应出据《返修通知单》,标明返修位置等。
将回执单与返修通知单递交监理或检验员,同时对受检设备进行检验与试验状态标识。
超声波检测工艺规程完整
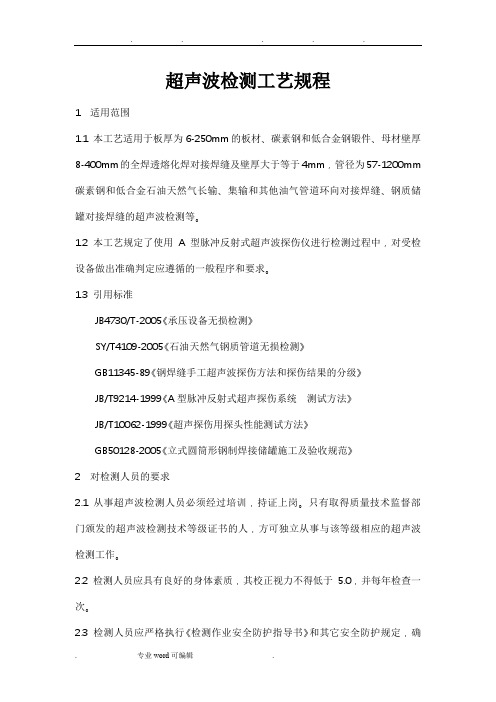
超声波检测工艺规程1适用范围1.1 本工艺适用于板厚为6-250mm的板材、碳素钢和低合金钢锻件、母材壁厚8-400mm的全焊透熔化焊对接焊缝及壁厚大于等于4mm,管径为57-1200mm 碳素钢和低合金石油天然气长输、集输和其他油气管道环向对接焊缝、钢质储罐对接焊缝的超声波检测等。
1.2 本工艺规定了使用A型脉冲反射式超声波探伤仪进行检测过程中,对受检设备做出准确判定应遵循的一般程序和要求。
1.3 引用标准JB4730/T-2005《承压设备无损检测》SY/T4109-2005《石油天然气钢质管道无损检测》GB11345-89《钢焊缝手工超声波探伤方法和探伤结果的分级》JB/T9214-1999《A型脉冲反射式超声探伤系统测试方法》JB/T10062-1999《超声探伤用探头性能测试方法》GB50128-2005《立式圆筒形钢制焊接储罐施工及验收规范》2对检测人员的要求2.1 从事超声波检测人员必须经过培训,持证上岗。
只有取得质量技术监督部门颁发的超声波检测技术等级证书的人,方可独立从事与该等级相应的超声波检测工作。
2.2 检测人员应具有良好的身体素质,其校正视力不得低于5.0,并每年检查一次。
2.3检测人员应严格执行《检测作业安全防护指导书》和其它安全防护规定,确保安全生产。
3检测程序3.1 根据工程特点和本工艺编制具体的《无损检测技术方案》。
3.2 受检设备经外观检查合格后,由现场监理或检验员开据《无损检测指令》或《无损检测委托单》到检测中心。
3.3 检测人员按指令或委托单要求进行检测准备,技术人员根据实际情况编制《探伤工艺卡》。
3.4 检测人员按《超声波探伤仪调试作业指导书》等工艺文件进行设备调试。
3.5 外观检查合格后,施加耦合剂,实施检测,做好《超声波检测记录》。
3.7 根据检测结果和委托单,填写相应的回执单或合格通知单。
若有返修,还应出据《返修通知单》,标明返修位置等。
将回执单和返修通知单递交监理或检验员,同时对受检设备进行检验和试验状态标识。
超声波操作规程
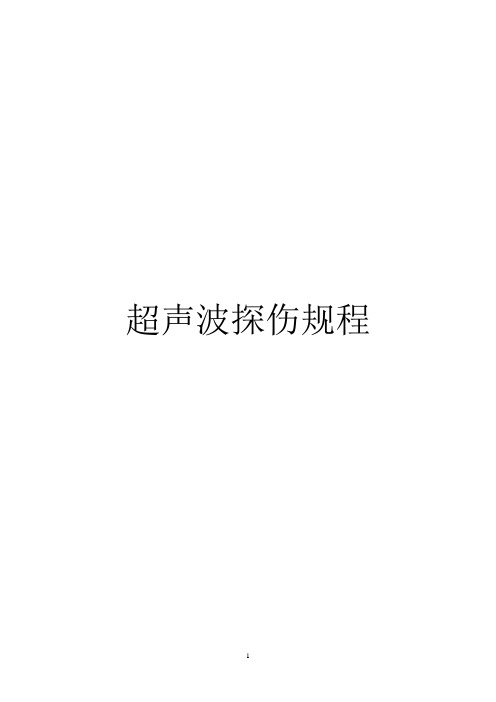
超声波探伤规程超声波探伤一、钢板(一)调试机器1、普板(1)20mm以下选用CBI试块,直探头,备耦合剂。
开机。
选参数:按<通道设置>键两次,出现参数设置菜单,将各参数修正,其中声速选距离,声速5900.测声速零点:按<调零/测试>键,选择测零点,将探头放在CBI试块上与被测工件等厚区。
定灵敏度,使B1波高50%,补偿10dB.(2)20mm以上选CB 试块开机初始化参数测声速零点定灵敏度,使5波高50%。
2、不锈钢只有灵敏度与普板不同,无试块。
在钢板完好区使B1波高80%即可。
(二)现场操作1、清理表面,无杂物、氧化皮、铁锈。
2、将耦合剂施进工件表面。
3、探头与工件在接触良好中探伤,探头沿垂直于钢板压延方向向距大于100mm 的平行线扫描。
4、定缺陷。
(1)缺陷的判定,发现下列三种情况之一即作为缺陷。
a缺陷第一次反射波(F1)波高大于或等于满刻度的50%,即大于等于50%。
b当底面第一次反射波(B1)波高未达到满刻度,此时缺陷第一次反射波(F1)波高于底面第一次反射波(B1)波高之比大于或等于50%,即B1<100%,而F1/B1≥50%.C底面第一次反射波(B1)波低于满刻度的50%,即B1<50%.(2)缺陷的边界范围或指示长度的测定a检出缺陷后,应在它的周围继续进行检测,以确定缺陷的范围。
b移动探头使缺陷第一次反射波波高于可限制基准灵敏度,条件可萤光屏满刻度的25%或使缺陷第一次反射波(F1)与底面第一次反射波高之比为50%。
此时,探头中心的移动距离即为缺陷的指示长度,探头中心点即为缺陷的边界点。
5、缺陷的评定。
(1)单个缺陷按其最大的长度为该产品的指示长度。
若单个缺陷的指示长度小于40mm时可不做记录。
Ⅰ级合格单个缺陷长度小于80mm,Ⅱ级单个缺陷小于100mm。
(2)单个缺陷指示面积,Ⅰ级小于25平方米,Ⅱ级小于50平方米。
(3)多个缺陷其间距小于100mm或间距小于相邻较小缺陷的指示长度以各缺陷面积之和作为单个缺陷指示面积。
钢结构焊缝超声检测工艺规程

1 适用范围本规程按GB/T11345编制,规定了厚度大于或等于8mm的低超声衰减(特别是散射衰减小)金属材料熔化焊焊接接头的手动超声波检测技术。
检测时焊缝及其母材温度从0~60 ℃之间。
本规程主要应用于焊缝和母体材料均为铁素体类钢的全熔透焊接接头。
本规程规定了依赖材料的超声波数值,是基于纵波速度为(5900±50)m/s,横波声速为(3255±30 ) m/s的钢材。
2 规范性引用文件GB/T 11345 《焊缝无损检测超声检测技术、检测等级评定》3 检测前需要的信息3.1 必要的项目a) 参考等级设定方法;b) 显示评定方法;c) 验收等级;D) 检测等级;e) 检测时被检对象所处的制造和加工状态;f) 人员资格;g) 横向显示的检测范围;h) 焊前和(或)焊后的母材检测;i) 是否需要书面检测工艺规程;j) 书面检测工艺规程的要求。
3.2 测试之前所需要的具体信息焊接接头超声检测前,检测人员应获得下列必要信息:a) 母材类型和产品门类(例如:铸件、锻件、轧制件);b) 检测时被检对象所处的制造或加工状态,包括热处理状态和其他;c) 任何焊后热处理的时机和程度;d) 坡口形式和尺寸;e) 表面状态要求;f) 焊接工艺规程或相关焊接工艺参数;g) 报告要求;h) 验收等级;i) 检测范围(包括横向显示的检测要求,如相关);j) 检测等级;k) 人员资格等级;l) 发现不可验收显示后的纠正规程。
4 人员和设备4.1 人员资格实施检测的人员,应按GB/T 9445或合同各方同意的体系进行资格鉴定与认证,取得超声检测相关工业门类的资格等级证书,并由雇主或其他代理对起进行职位专业培训和操作授权。
从事焊缝检测人员应掌握焊缝超声检测通用知识,具有足够的焊缝超声检测经验,并掌握一定的材料和焊接基础知识。
4.2 设备4.2.1 宜选用按GB/T 5616或合同各方同意的体系取得认证或合格评定的超声检测仪,探头和试块。
钢板超声波检测标准

钢板超声波检测标准一、超声波探伤方法1.1 脉冲反射法脉冲反射法是一种常用的超声波探伤方法,适用于检测内部和表面缺陷。
通过在钢板上发射超声波,然后接收回波信号,分析信号的反射时间和波形变化,以确定钢板内部是否存在缺陷。
1.2 衍射时差法衍射时差法是通过测量超声波在钢板中传播的时间,结合已知的声速和钢板的厚度,计算出超声波的衍射时间,从而确定钢板内部是否存在缺陷。
二、探伤设备与器材2.1 超声波探伤仪超声波探伤仪应具有高灵敏度、高分辨率和高可靠性,能够准确测量超声波的传播时间和波形变化。
2.2 探头探头是超声波探伤的关键部件,应具有高灵敏度、高分辨率和高可靠性,能够准确测量超声波的传播时间和波形变化。
根据不同的探伤方法,需要选择不同类型的探头。
2.3 耦合剂耦合剂用于将探头与钢板表面紧密接触,以减少声波的反射和散射,提高探伤的准确性和可靠性。
三、探伤条件与环境3.1 温度与湿度超声波探伤应在适当的温度和湿度条件下进行,以避免环境因素对探伤结果产生影响。
3.2 清洁度超声波探伤前应对钢板表面进行清洁处理,以减少杂质的干扰和影响。
四、被检对象要求与制备4.1 钢板规格与材质超声波探伤适用于不同规格和材质的钢板,应根据具体的检测需求选择合适的钢板。
4.2 表面处理对于不同表面处理的钢板,如涂层、镀层等,应进行相应的处理,以避免对探头和耦合剂产生影响。
五、探伤操作要求与步骤5.1 校准仪器在进行超声波探伤前,应对探伤仪和探头进行校准,以确保测量结果的准确性和可靠性。
5.2 选择探头和耦合剂根据具体的检测需求选择合适的探头和耦合剂。
5.3 耦合与扫描将探头与钢板表面紧密耦合,并进行扫描操作。
根据信号的反射时间和波形变化确定是否存在缺陷。
对于不同的缺陷类型和位置,应进行相应的记录和分析。
钢板超声波检测作业指导书

检
尺寸
测 距 离 - 波 幅 曲 线 1、 将探头置于试块有槽的一面,使主声束对准槽的宽边,找出第一个全跨距反射
的确定
的最大波幅,调整仪器,使该反射波的最大波幅为满刻度的 80%,在显示屏上
记录下该信号的位置。
2、 不改变仪器的调整状态,移动探头,得到第二个全跨距信号,并找出信号最大
反射波幅,在显示屏上记录下该信号的位置。
3、 板材探头在钢板边缘或剖口预定线两侧检测区域 1 、、最大单个缺陷指示长度 Lmax>30mm 2 、最大单个缺陷指示面积 S>100mm² 3 、在任意 1m 检测长度内,单个缺陷指示长度为 15mm<L≤30mm,评定范围
内缺陷个数>3 个。
编制(资格): X X X
(UT-Ⅱ) 2016 年 12 月 21 日
合格级别 II 级
耦合剂 化学浆糊
扫描调节
声程 1:2
检测时机
下料前
纵 探头型
2.5P30Z
试块型号 2#对比试块
波号
订正:
/
订正:3#对比试块
检 基准灵 测 敏度调
深度 85mm 的Φ5 平底孔反射波调至 80%
节
订正:在 3#对比试块上绘制Φ5 平底孔的距离-波幅曲线,并以此曲线作为基准灵敏度
扫查方 式1
3、 在显示屏上将上述内容所确定的点连成一直线,此线即为距离-波幅曲线。
S 1、 白点、裂纹等危害性缺陷, 不允许缺陷 2、 板材中部检测区域
①、最大单个缺陷指示面积 S>100mm² ②、在任意 1m×1m 检测面积内,单个缺陷指示面积为 50mm²<S≤100mm², 评定范围内缺陷个数>10 个
75 75
6000
02钢板超声波检测操作指导书
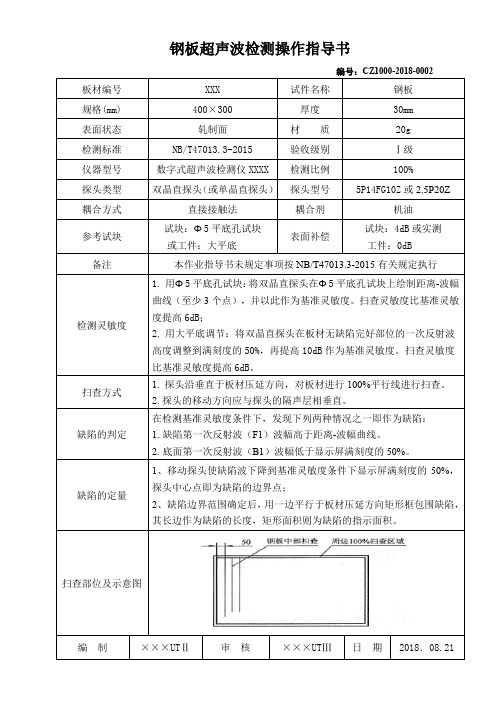
编号:CZ1000-2018-0002
板材编号
XXX
试件名称
钢板
规格(mm)
400×300
厚度
30mm
表面状态
轧制面
材质
20g
检测标准
NB/T47013.3-2015
验收级别
Ⅰ级
仪器型号
数字式超声波检测仪XXXX
检测比例
100%
探头类型
双晶直探头(或单晶直探头)
探头型号
5P14FG10Z或2.5P20Z
耦合方式
直接接触法
耦合剂
机油
参考试块
试块:Φ5平底孔试块
或工件:大平底
表面补偿
试块:4dB或实测
工件:0dB
备注
本作业指导书未规定事项按NB/T47013.3-2015有关规定执行
检测灵敏度
1.用Φ5平底孔试块:将双晶直探头在Φ5平底孔试块上绘制距离-波幅曲线(至少3个点),并以此作为基准灵敏度。扫查灵敏度比基准灵敏度提高6dB;
2.用大平底调节:将双晶直探头在板材无缺陷完好部位的一次反射波高度调整到满刻度的50%,再提高10dB作为基准灵敏度。扫查灵敏度比基准灵敏度提高6dB。
扫查方式
1.探头沿垂直于板材压延方向,对板材进行100%平行线进行扫查。
2.探头的移动方向应与探头的隔声层相垂直。
缺陷的判定
在检测基准灵敏度条件下,发现下列两种情况之一即作为缺陷:
扫查部位及示意图
编制
×××UTⅡБайду номын сангаас
审核
×××UTⅢ
日期
2018.08.21
1.缺陷第一次反射波(F1)波幅高于距离-波幅曲线。
压力容器钢板超声检测工艺守则

压力容器钢板超声检测工艺守则1、主题内容适用范围本规程规定了板厚为6~250mm的钢制压力容器用板材的超声检测和缺陷等级评定。
本规程适用于板厚为6~250mm的钢制压力容器用板材的超声检测。
2、检测人员从事超声探伤的人员由UT--Ⅱ级或Ⅱ级以上资格人员担任。
3、表面状态应消除妨碍探伤的钢板表面的氧化皮,铁锈及油污。
4、仪器和探头4.1仪器采用A型脉冲反射式超声波探伤仪。
4.2探头选用应按NB/T47013-2015表3的规定进行。
板厚6~20mm,采用双晶探头,频率4~5 MHZ;板厚>20~250mm,采用单直探头,频率2~5 MHZ。
5、耦合剂应采用透声性好,且不损伤检测面的耦合剂,如机油、浆糊、甘油和水等。
6、试块6.1用双晶直探头检测壁厚≤20mm的钢板时,采用NB/T47013.3-2015标准规定的图1所示的CBⅠ标准试块。
用单直探头检测板厚>20mm 的钢板时,采用NB/T47013.3-2015标准规定的图2和表4试块。
6.2试块用钢板,试块厚度应与被检钢板厚度相近。
试块不得有Φ2当量以上缺陷。
7、探伤面、探头移动区和探头移动速度7.1探伤面为单侧单面检测。
若认为需要或设计上有要求时,也可对钢板的上下面分别检测。
7.2探头移动区为沿垂直于钢板压延方向,间距100mm的平行线扫查。
在钢板剖口予定线两侧各50mm(当板厚超过100mm时,以板厚的一半为准)内应作100%扫查。
7.3探头移动速度不得大于150mm/s.8、检测灵敏度8.1板厚≤20mm时,用NB/T47013.3-2015标准中图1所示的CBⅠ标准试块将工件等厚部位第一次底波高度调整到满刻度的50%,再提高10dB作为基准灵敏度。
8.2板厚>20mm时,用NB/T47013.3-2015标准中的CBⅡ试块平底孔第一次反射波高调整到满刻度的50%作为基准灵敏度。
8.3板厚不小于探头3倍近场区时,也可取钢板无缺陷完好部位的第一次底波来校准灵敏度。
- 1、下载文档前请自行甄别文档内容的完整性,平台不提供额外的编辑、内容补充、找答案等附加服务。
- 2、"仅部分预览"的文档,不可在线预览部分如存在完整性等问题,可反馈申请退款(可完整预览的文档不适用该条件!)。
- 3、如文档侵犯您的权益,请联系客服反馈,我们会尽快为您处理(人工客服工作时间:9:00-18:30)。
钢板超声波手动检测方法操作细则
1.范围
本操作细则规定了厚钢板超声波检验对比试样、检验仪器和设备、检验条件与方法、缺陷的测定与评定、钢板的质量分级、检验报告等内容。
本操作细则适用于厚度不小于6m m的锅炉、压力容器、桥梁、建筑、造船、钢结构、管线、模具等用途钢板的超声波检验。
奥氏体不锈钢板也可参照本标准。
2.引用文件
GB/T 2970-2004
GB/T 8651
JB/T 10061
/
3. 一般要求
3.1 被检板材表面应平整、光滑、厚度均匀,不应有液滴、油污、腐蚀和其他污物。
被检板材的金相组织不应在检验时产生影响检验的干扰回波。
检验场地应避开强光、强磁场、强振动、腐蚀性气体、严重粉尘等影响超声波探伤仪稳定性或检验人员可靠观察的因素。
从事钢板超声波检验人员应经过培训,并取得权威部门认可的超声探伤专业1级及其以上资格证书。
签发探伤报告者应获得权威部门认可的超声探伤专业I级及其以上资格证书。
检验方式可采用手工的接触法、液浸法(包括局部液浸和压电探头或电磁超声探头的自动检验法)。
所采用的超声波波型可为纵波和横波。
4.对比试样
—
4. 1 对比试样材质、声学性能应与被检验钢板相同或相似,并应保证内部不存在影响检验的缺陷。
用双晶片直探头检验厚度不大于60 mm的钢板时,所用对比试样如图1所示。
用单晶片直探头检验钢板时,对比试样应符合图2、表1和表2的规定。
5. 检验仪器和设备
探伤仪
—
所用探伤仪的性能应符合GB/T 8651或JB/T 10061的有关规定。
换能器
. 1 压电直探头的选用如表3,
不管选用哪种探头,都要保证有效探测区。
板厚大于60 mm时,若双晶片直探头性能指标能达到单晶片直探头,也可选用双晶片直探头。
当采用横波探伤时,可参照.1B 4730-1994的附录H。
6. 检验条件和方法
6. 1 检验时间
)
原则上在钢板加工完毕后进行,也可在轧制后进行。
检验面
可以从钢板任一轧制面进行检验,被检验钢板的表面应平整,应清除影响检验的氧化皮、腐蚀、油污等。
检验灵敏度
. 1 用压电探头时,检验灵敏度应计人对比试样与被检验钢板之间的表面祸合声能损失(dB) 。
用双晶片直探头检验时,用图7试样或在同厚度钢板上将第一次底波高度调整到满刻度的50% ,再提高灵敏度10 dB作为检验灵敏度。
用单晶片直探头检验时,灵敏度按图2试样平底孔的第一次反射波高等于满刻度的50% 来校准。
板厚大于探头3倍近场区时,检验灵敏度用计算法、通过第一次底面回波高度来确定。
^
在动态状况下,也可利用中所述的动态试样中相应的缺陷,在无杂波的情况下,使人工缺陷反射波高不低于仪器荧光屏满刻度的50% ,再提高10 dB作为检验灵敏度。
探头扫查形式
. 1 用压电探头时,探头沿垂直于钢板压延方向、间距不大于100 mm的平行线进行扫查;在钢板周围50 mm(板厚大于100 mm时,取板厚的一半)及坡口预定线(由供需双方在合同或技术协议中确定具体位置)两侧各25 mm内沿周边进行扫查。
用双晶片探头时,探头隔声层应与压延方向平行(垂直于压延方向扫查)
根据合同或技术协议或图纸要求,也可进行其他形式的扫查或100%扫查。
检验速度
检验速度应不影响探伤,但在使用不带自动报警功能的探伤装置进行扫查时,检验速度应不大于200 mm /s。
7. 缺陷的测定与评定
>
7. 1 在检验过程中,发现下列情况应记录
缺陷第一次反射波(F,)波高大于或等于满刻度的50%。
当底面第一次反射波(B,)波高未达到满刻度时,缺陷第一次反射波(F,)波高与底面第一次反射波(B,)波高之比大于或等于50%。
7. 当底面(或板端部)第一次反射波(B)波高低于满刻度的50%
缺陷的边界或指示长度的测定方法
. 1 检验出缺陷后,在周围进行检验,以确定缺陷的延伸。
用双晶片探头确定缺陷的边界或指示长度时,探头移动方向应与探头的隔声层相垂直。
利用半波高度法确定缺陷的边界或指示长度。
(
确定中缺陷的边界或指示长度时,移动探头,将板底面(或端部)第一次反射波升高到检验灵敏度条件下荧光屏满刻度的50% 此时,探头中心点即为缺陷的边界点。
采用自动超声方法检验时,发现可疑缺陷后,缺陷的定量定位可用手工方法进行。
缺陷的指示
长度及边界的精确测定亦用人工方法。
缺陷指示长度的评定规则
单个缺陷按其表现的最大长度作为该缺陷的指示长度,若指示长度小于40m m时,则其长度可不作记录。
单个缺陷指示面积的评定规则
. 1 单个缺陷按其表现的面积作为该缺陷的单个指示面积。
当多个缺陷的相邻间距小于100 mm或间距小于相邻缺陷(以指示长度来比较)的指示长度(取其较大值)时,其各块缺陷面积之和也作为单个缺陷指示面积。
缺陷密集度的评定规则
在任一1m xlm 检验面积内,按缺陷面积占的百分比来确定。
8.钢板的质t分级
钢板质量分级见表4.
在钢板周边50 mm(板厚大于100 mm时,取板厚的一半)可检验区域内及坡口预定线两侧各25 mm内,单个缺陷的指示长度不得大于或等于50 mm。