华中世纪星数控车床对刀及刀补值的设置方法(精)
华中世纪星数控车床的几种精确对刀方法

对 刀是 数 控 加 工 中的 主 要 操 作 和 重 要 外 , 把 刀具 在 使 用 过 程 中 还 会 出 现 不 同 A 点 的 X机 床 坐标 , 刀后停 车 , 量 已 切 每 退 测 技 能 。 对 刀 的准 确 性 决 定 了零 件 的 加 工精 程 度 的 磨 损 , 此 各 刀 的 刀 偏 置 和 磨 损 值 削轴 段 外径 中 D。 因 度 , 时 , 刀 效率 还 直 接 影 响数 控 加 工 效 需 要 进 行补 偿 。获 得 各 刀 刀偏 置 的 基本 原 同 对 () 准 刀按记 录值 通过 “ 3基 点动 +步 进” 率 。华 中 世纪 星 车 削 系 统是 武 汉 华 中数 控 理 是 : 刀均 对 准 工 件上 某 一 基 准 点 , 于 方 式 重 回 A 点 , 刀偏 表 的试 切 直 径 和 试 各 由 在 股 份 公 司 近 年推 出的 优 秀 国产 数 控 车 削 系
E H C N0LOGY NFORM A ION l I
工 业 技 术
华 中世 纪 星数 控 车 床 的 几种 精确 对 刀 方法
朱 海勇 申东 东 ( 壁职 业技术学院机 电工程学院 河南鹤壁 鹤
483 ) 5 0 0
摘 要: 本文 首先介 绍 了 数控 车床 常 用的 “ 试切对 刀法”的原理 以及对 刀思路 ; 着, 绍 了华中世 纪星车 削数控 系统的三种 手动试 切 接 介 对 刀方法 ; 为改进 其对 刀精度 , 据 “自动试 切- 测量_ 误 差补偿 ”的思路 , 根 + + 设计 出 了用程序控 制的 自动试切 法 , 井总结介 绍 了三种精 确 对 刀 方法 。 希 望能 对 大家 有所 帮助 。 关键词 : 数控 车床 对 刀 中图分类号 : G 9 T 5 6 文 献标识 码 : A 文章编 号 : 6 2 3 9 ( 0 8 I ( ) 0 6 — 2 1 7 - 7 12 0 ) 2b 一 0 6 0
华中世纪星数控车床中G92指令对刀方法

Z宵静 擎蕊衄
下述每种方法 的对刀 准备 工作均 相同 :在系统 M I D 功能子 菜单 下按 F 键 , 2 进入刀偏表 : ▲键移动蓝 色亮条 到各刀对应 的刀偏 号位 用 置 , F 键 ; 刀偏 号为 # 0 0 # 0 1# 0 2 # 0 3 # O 4的 x偏 按 5 将 00 、 0 、0 0 、0 0 、O O 0
如图 2 所示 ,由于各刀装夹在刀架 的 x z方 向的伸 长和位置不 、
同 .当非基准刀转位到加工位置 时.刀尖位置 B相对于 A点就有偏 置, 原来建立的工件坐标 系就不再适用了。 此外 , 刀具在使用过程 每把 中还会出现不同程度 的磨损 。 因此各刀的刀偏置和磨损值需要进行补 偿。 获得各刀刀偏置 的基本原理是 : 各刀均对准工件上某一基准点 ( 如 图 l的 A点) 由于 C T显 示的机床坐标 不同 . . R 因此将非基 准刀在该 点处的机床坐标通 过人 工计算或系统 软件 计算减去基准 刀在同样点 置 。 的机床坐标 . 就得到了各非基准刀的刀偏置。 () 5 与前述步骤( ) 5 相同。 2 多刀试切外圆轴段 . . 3 人工计算 获得刀偏置法 系统 在手动状态下对好 1 24号刀 , 、、 并切 出一个台阶轴 , 分别记 录各 刀切削终点 ( 图 3 F E D点 ) 如 中 、、 的机 床坐标 , 并测量各段 的直
华中数控对刀操作方法
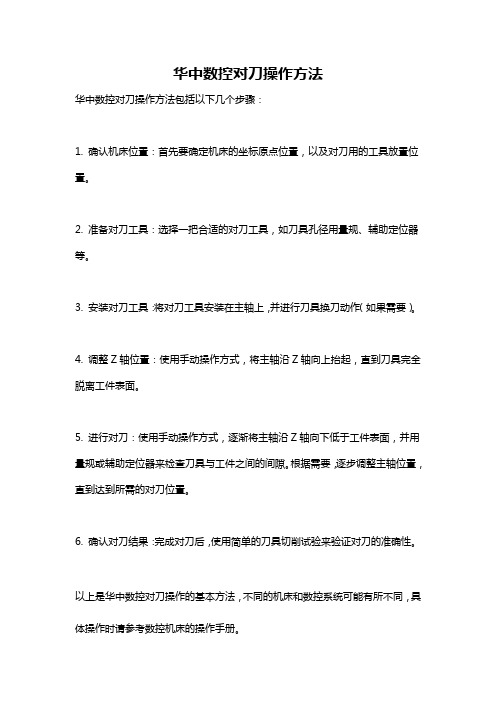
华中数控对刀操作方法
华中数控对刀操作方法包括以下几个步骤:
1. 确认机床位置:首先要确定机床的坐标原点位置,以及对刀用的工具放置位置。
2. 准备对刀工具:选择一把合适的对刀工具,如刀具孔径用量规、辅助定位器等。
3. 安装对刀工具:将对刀工具安装在主轴上,并进行刀具换刀动作(如果需要)。
4. 调整Z轴位置:使用手动操作方式,将主轴沿Z轴向上抬起,直到刀具完全脱离工件表面。
5. 进行对刀:使用手动操作方式,逐渐将主轴沿Z轴向下低于工件表面,并用量规或辅助定位器来检查刀具与工件之间的间隙。
根据需要,逐步调整主轴位置,直到达到所需的对刀位置。
6. 确认对刀结果:完成对刀后,使用简单的刀具切削试验来验证对刀的准确性。
以上是华中数控对刀操作的基本方法,不同的机床和数控系统可能有所不同,具体操作时请参考数控机床的操作手册。
数控车床上刀补用法
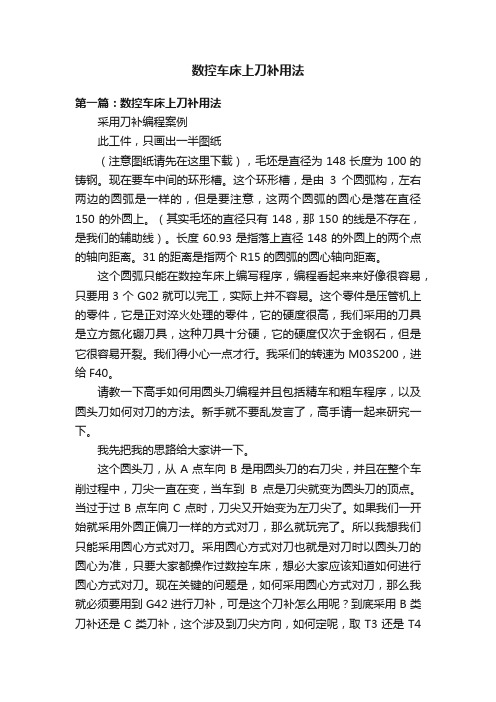
数控车床上刀补用法第一篇:数控车床上刀补用法采用刀补编程案例此工件,只画出一半图纸(注意图纸请先在这里下载),毛坯是直径为148长度为100的铸钢。
现在要车中间的环形槽。
这个环形槽,是由3个圆弧构,左右两边的圆弧是一样的,但是要注意,这两个圆弧的圆心是落在直径150的外圆上。
(其实毛坯的直径只有148,那150的线是不存在,是我们的辅助线)。
长度60.93是指落上直径148的外圆上的两个点的轴向距离。
31的距离是指两个R15的圆弧的圆心轴向距离。
这个圆弧只能在数控车床上编写程序,编程看起来来好像很容易,只要用3个G02就可以完工,实际上并不容易。
这个零件是压管机上的零件,它是正对淬火处理的零件,它的硬度很高,我们采用的刀具是立方氮化硼刀具,这种刀具十分硬,它的硬度仅次于金钢石,但是它很容易开裂。
我们得小心一点才行。
我采们的转速为M03S200,进给F40。
请教一下高手如何用圆头刀编程并且包括精车和粗车程序,以及圆头刀如何对刀的方法。
新手就不要乱发言了,高手请一起来研究一下。
我先把我的思路给大家讲一下。
这个圆头刀,从A点车向B是用圆头刀的右刀尖,并且在整个车削过程中,刀尖一直在变,当车到B点是刀尖就变为圆头刀的顶点。
当过于过B点车向C点时,刀尖又开始变为左刀尖了。
如果我们一开始就采用外圆正偏刀一样的方式对刀,那么就玩完了。
所以我想我们只能采用圆心方式对刀。
采用圆心方式对刀也就是对刀时以圆头刀的圆心为准,只要大家都操作过数控车床,想必大家应该知道如何进行圆心方式对刀。
现在关键的问题是,如何采用圆心方式对刀,那么我就必须要用到G42进行刀补,可是这个刀补怎么用呢?到底采用B类刀补还是C类刀补,这个涉及到刀尖方向,如何定呢,取T3还是T4还是T8呢?看起在每个不同时间,刀尖的方向都不同,到底应该如何取刀尖方向呢?还有刀补从哪个程序开始补呢?又在哪里结束呢?我第一次编写这个程序时,我采用圆心方式对刀,我将圆弧分成两半,我用T0101车左边圆弧,用T0102车圆弧,在中间开始换刀偏。
数控车床的对刀与刀具补偿(附图)

数控车床的对刀与刀具补偿(附图)一、对刀对刀的目的是确定程序原点在机床坐标系中的位置,对刀点可以设在零件上、夹具上或机床上,对刀时应使对刀点与刀位点重合。
数控车床常用的对刀方法有三种:试切对刀、机械对刀仪对刀(接触式)、光学对刀仪对刀(非接触式),如图3-9 所示。
1、试切对刀1 )外径刀的对刀方法如图3-10 所示。
Z 向对刀如(a) 所示。
先用外径刀将工件端面( 基准面) 车削出来;车削端面后,刀具可以沿X 方向移动远离工件,但不可Z 方向移动。
Z 轴对刀输入:“Z0 测量”。
X 向对刀如(b) 所示。
车削任一外径后,使刀具Z 向移动远离工件,待主轴停止转动后,测量刚刚车削出来的外径尺寸。
例如,测量值为Φ50.78mm, 则X 轴对刀输入:“X50.78 测量”。
2 )内孔刀的对刀方法类似外径刀的对刀方法。
Z 向对刀内孔车刀轻微接触到己加工好的基准面(端面)后,就不可再作Z 向移动。
Z 轴对刀输入:“Z0 测量”。
X 向对刀任意车削一内孔直径后,Z 向移动刀具远离工件,停止主轴转动,然后测量已车削好的内径尺寸。
例如,测量值为Φ45.56mm, 则X 轴对刀输入:“X45.56 测量”。
3 )钻头、中心钻的对刀方法如图3-11 所示。
Z 向对刀如(a )所示。
钻头( 或中心钻) 轻微接触到基准面后,就不可再作Z 向移动。
Z 轴对刀输入:“Z0 测量”。
X 向对刀如(b )所示。
主轴不必转动,以手动方式将钻头沿X 轴移动到钻孔中心,即看屏幕显示的机械坐标到“X0.0 ”为止。
X 轴对刀输入:“X0 测量”。
2、机械对刀仪对刀将刀具的刀尖与对刀仪的百分表测头接触,得到两个方向的刀偏量。
有的机床具有刀具探测功能,即通过机床上的对刀仪测头测量刀偏量。
3、光学对刀仪对刀将刀具刀尖对准刀镜的十字线中心,以十字线中心为基准,得到各把刀的刀偏量。
二、刀具补偿值的输入和修改根据刀具的实际参数和位置,将刀尖圆弧半径补偿值和刀具几何磨损补偿值输入到与程序对应的存储位置。
华中“世纪星”铣床数控系统刀具长度补偿功能说明

华中“世纪星”铣床数控系统刀具长度补偿功能说明
刀具长度补偿功能的原理是通过在数控系统中设定一个刀具长度补偿值,然后系统会根据这个值对刀具的加工轨迹进行相应的调整。
当刀具的
实际长度与理论长度不一致时,系统会自动对加工轨迹进行补偿,以达到
预期的加工效果。
在进行刀具长度补偿时,首先需要进行刀具长度的测量。
可以使用专
用的刀具测量仪器对刀具进行测量,得到刀具的实际长度。
然后将测量得
到的刀具长度输入到数控系统中。
接下来,通过数控系统的操作界面进入刀具长度补偿功能的设置菜单。
在设置菜单中,可以设置刀具长度补偿值。
这个值是根据实际测量的刀具
长度与理论长度之间的差异来确定的,可以为正值或负值,用来调整刀具
的加工轨迹。
通过设置好刀具长度补偿值后,系统会自动对加工轨迹进行调整。
在
加工过程中,系统根据刀具长度补偿值对刀具的加工轨迹进行微调,以确
保工件的尺寸精度和表面质量。
刀具长度补偿功能的应用范围广泛。
在高精度加工中,刀具长度的微
小偏差都会对加工效果产生影响。
通过使用刀具长度补偿功能,可以提高
加工的精度和质量,减少误差,保证加工效果的稳定性。
在一些需要反复
换刀的加工中,使用刀具长度补偿功能可以减少调整时间,提高生产效率。
总之,华中“世纪星”铣床数控系统的刀具长度补偿功能可以通过设
定刀具长度补偿值,对刀具的加工轨迹进行自动调整,以保证加工效果的
精度和质量。
这一功能的应用范围广泛,可以在各种加工场合中发挥重要
作用。
数控机床刀补参数设置
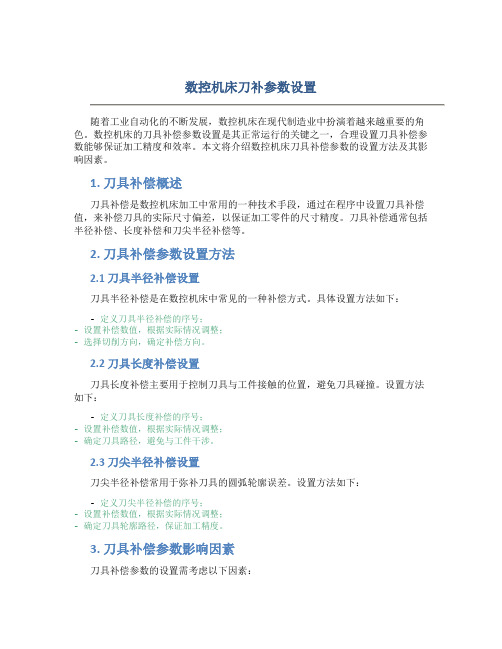
数控机床刀补参数设置随着工业自动化的不断发展,数控机床在现代制造业中扮演着越来越重要的角色。
数控机床的刀具补偿参数设置是其正常运行的关键之一,合理设置刀具补偿参数能够保证加工精度和效率。
本文将介绍数控机床刀具补偿参数的设置方法及其影响因素。
1. 刀具补偿概述刀具补偿是数控机床加工中常用的一种技术手段,通过在程序中设置刀具补偿值,来补偿刀具的实际尺寸偏差,以保证加工零件的尺寸精度。
刀具补偿通常包括半径补偿、长度补偿和刀尖半径补偿等。
2. 刀具补偿参数设置方法2.1 刀具半径补偿设置刀具半径补偿是在数控机床中常见的一种补偿方式。
具体设置方法如下:- 定义刀具半径补偿的序号;- 设置补偿数值,根据实际情况调整;- 选择切削方向,确定补偿方向。
2.2 刀具长度补偿设置刀具长度补偿主要用于控制刀具与工件接触的位置,避免刀具碰撞。
设置方法如下:- 定义刀具长度补偿的序号;- 设置补偿数值,根据实际情况调整;- 确定刀具路径,避免与工件干涉。
2.3 刀尖半径补偿设置刀尖半径补偿常用于弥补刀具的圆弧轮廓误差。
设置方法如下:- 定义刀尖半径补偿的序号;- 设置补偿数值,根据实际情况调整;- 确定刀具轮廓路径,保证加工精度。
3. 刀具补偿参数影响因素刀具补偿参数的设置需考虑以下因素:•刀具材质和尺寸;•工件材料和形状;•加工精度要求;•切削速度和进给速度。
综上所述,数控机床刀具补偿参数设置是保证加工精度和效率的重要步骤,正确设置补偿参数可以提高机床加工的稳定性和质量。
在实际操作中,操作人员需要根据具体情况灵活调整参数,不断优化加工过程,以获得更好的加工效果。
希望本文对数控机床刀具补偿参数的设置有所帮助,并能引发更多关于数控机床加工技术的讨论与思考。
华中世纪星操作简介

17、加工完毕,清扫机床。主轴停转3分钟可惯技。注意关机顺序,先按控制面板上的急停按钮 控制面板电源键 机床电源。
18、严禁在实习期间打闹、喧哗和玩游戏。
19、如违反安全操作规程,应给予严厉警告。造成严重机床故障时,根据有关规定取消实习资格、成绩或给予赔偿。望同学们严肃、认真地操作机床
10、工作台和各导轨面不得直接摆放刀具或量具。
11、手动回参考点各轴须离机械原点—30mm以上。
12、手动或手轮移动各轴时必须看清各轴正、负,先选择小进给倍率或慢转手轮观察,方向正确后再快速移动。
13、对刀时要打到步移动,防止撞刀。
14、必须在教师检查无误时方可进行加工。
15、运行程序必须由老师监督,运行须关闭防护门。
(1)
(2) +
(3)
(4)
(5)
(6)
(7)
(8)
(8)
四、刀具补偿与坐标系设置
(1)刀具补偿设置
(2)坐标系的设置
五、程序的输入与管理
一、程序的输入
程序的输入方式有三种:手动输入、磁盘输入和DNC通讯输入。
1.1手动输入程序
使用控制面板上的输入键手动输入程序。
1.2磁盘输入
先将程序存入磁盘,然后将磁盘插入到机床上,进入程序管理器,
(1)进行X轴的分中
MDI模式 M3S1000 循环启动 增量模式 手轮 ,刀具碰到工件左边 设置F5 按“X轴清零F6”键 这时相对坐标X轴显示数值0 抬起刀具(即Z向+方向移动) 把刀具碰工件右边 这时把X显示的相对坐标值除于2 得出X轴的中点 把刀具移到X轴中点位置 这时进入坐标系F1功能 在G54对应X方框内输入X轴机床坐标值(如X-200),按“Enter”确定。
- 1、下载文档前请自行甄别文档内容的完整性,平台不提供额外的编辑、内容补充、找答案等附加服务。
- 2、"仅部分预览"的文档,不可在线预览部分如存在完整性等问题,可反馈申请退款(可完整预览的文档不适用该条件!)。
- 3、如文档侵犯您的权益,请联系客服反馈,我们会尽快为您处理(人工客服工作时间:9:00-18:30)。
华中世纪星数控车床对刀及刀补值的设置方法
1. 刀具补偿值设置(F4)
在主操作界面下,按F4键进入刀具补偿功能子菜单。
命令行与菜单条的显示如图1-9所示。
图1-9 刀具补偿功能主菜单
刀具补偿分为刀具的几何补偿和刀具的半径补偿。
T代码指定刀具的几何补偿(偏置补偿与磨损补偿之和),其后的4位数字分别表示选择的刀具号(前两位数字)和刀具偏置补偿号(后两位数字)。
补偿号可以和刀具号相同,也可以不同,即一把刀具可以对应多个补偿号(值)。
刀具补偿号为00表示补偿量为0,即取消补偿功能。
G40、G41、G42指定刀具的半径补偿。
(1)刀偏数据设置(F4→F1)
刀具的几何补偿包括刀具的偏置补偿和刀具的磨损补偿,刀具的偏置补偿有绝对刀具偏置补偿和相对刀具偏置补偿两种形式。
我们推荐采用绝对刀具偏置补偿。
在主操作界面下,按F4→F1进入刀具偏置编辑画面如图1-10所示。
图1-10 刀具偏置编辑
车床编程轨迹实际上是刀尖的运动轨迹,但实际中不同的刀具的几何尺寸、安装位置各不相同,其刀尖点相对于刀架中心的位置也就不同。
因此需要将各刀具刀尖点的位置值进行测量设定,以便系统在加工时对刀具偏置值进行补偿。
我们采用试切法来设置绝对刀具偏置补偿值。
图1-11 绝对刀偏法刀具偏置补偿值
如图1-11所示,刀具偏置值即机床回到机床零点时,刀架工作位上各刀刀尖位置相对工件零点的有向距离。
当执行刀具偏置补偿时,各刀以此值设定各自的工件坐标系。
机床到达机床零点时,机床坐标值显示均为零,整个刀架上的点可考虑为一理想点,故当各刀对刀时,机床零点可视为在各刀刀位点上。
我们通过输入试切直径、长度值,自动计算工件零点相对与各刀刀位点的距离。
其步骤如下:
①用光标键将蓝色亮条移动到要设置刀具偏置值的行。
②用刀具试切工件的外径,然后沿Z轴方向退刀,在此过程中不要移动X轴。
③测量试切后的工件外径,如为ф25.26 ,然后将此值输入到刀偏表中“#××01”一行中“试切直径”一栏中并确认,设置好X偏置。
④用刀具试切工件的右端面,然后沿X轴方向退刀,在此过程中不要移动Z轴。
⑤计算试切工件端面到该刀具要建立的工件坐标系的零点位置的有向距离,如为“3mm”,然后将“3”输入到刀偏表中“#××01”一行中“试切长度”一栏中并确认,设置好Z偏置。
如果要设置其余的刀具,就重复以上步骤。
需要注意,对刀前,机床必须先回机床零点。
(2)刀具磨损量补偿参数设置(F4→F1)
刀具使用一段时间后磨损,也会使产品尺寸产生误差,因此需要对其进行补偿,该补偿值与刀具偏置补偿存放在同一个寄存器的地址号中如图1-10所示。
例如在粗加工时,将“X磨损”输入“0.5”(0.5mm作为精加工的余量),工件粗加工后,实测工件值大于图样尺寸0.48mm,则相应刀具磨损量为“0.5-0.48=0.02”,在图1-10刀偏表中,“X磨损”输入“0.02”,自动加工后即可保证工件尺寸。
若长度出现偏差也可以用刀具磨损量补偿,在图1-10刀偏表中“Z磨损”输入相应值即可。
(3)刀具半径补偿数据设置(F4→F2)
刀尖圆弧半径补偿是通过G41、G42、G40代码及T代码指定的刀尖圆弧半径补偿号来加入或取消半径补偿值。
车刀刀尖的方向号定义了刀具刀位点与刀尖圆弧中心的位置关系,其从0~9有十个方向,如图1-12所示。
图1-12 车刀刀尖方位定义
在主操作界面下,按F4→F2进入刀补数据设置画面,如图1-13所示。
图1-13 刀补数据设置
输入刀补数据的操作步骤如下:
①用光标键移动蓝色亮条到要编辑的选项。
②按Enter键,蓝色亮条所指刀具数据的颜色和背景都发生变化,同时有一光标在闪烁。
③进行编辑修改。
④修改完毕,按Enter键确认。
⑤若输入正确,图形显示窗口相应位置将显示修改过的值,否则原值不变。
2. 坐标系的设置(F5→F1)
用绝对刀具偏置补偿值的方法可直接设定工件坐标系,当执行刀具偏置补偿时,各刀以此值设定各自的工件坐标系,在编程时不用G92或G54~G59。
如使用G54~G59设定工件坐标系,应将T0101写成T0100 , T0202写成T0200以后的刀具以次类推。
也就是系统在执行T0100程序段时只做调刀动作,并不建立工件坐标系。
在主操作界面下,按F5→F1键进入G54、G55等坐标系数据显示窗口,如图1-14所示。
以程序段“G54 X80 Z100”为例,其设置操作步骤如下:
①选择要输入的数据类型G54坐标系。
②选用使用的刀具T01并在手动方式下切削工件外圆一刀,沿Z轴的正方向退刀,用千分尺测量工件直径为“ф45.420”,同时记录下CRT显示“机床实际坐标”一栏“X”值,如为“-41.124”,得X=(-41.124)+( -45.420)= -86.544。
在工件右端面试切一刀,沿X轴的正方向退刀,并记录下CRT显示“机床实际坐标”一栏“Z”值,如“-315.225”,即Z=-315.225。
③输入零点偏置值。
在图1-14显示方式下输入“X-86.544”、“Z-315.225”,确认并退出界面,此时系统便将一号刀零点偏置数据X、Z(即工件零点在机床坐标系下的坐标值)自动记忆到系统中。
此时无论刀具T01当前点处于何位置,当调出程序段“G54 X80 Z100”执行时,刀具总能找到在工件坐标系下X 80、Z100的点,即数控系统用新的工件坐标系取代了回参考点时所建立的机床坐标系。
图1-14 坐标系设置
使用多把刀具时,每把刀对刀的方法相同,可在G54/G55/G56/G57/G58/G59之中任意选择,但坐标系一定要与所使用的刀具的刀位号对应。