华中世纪星数控车床对刀及刀补值的设置方法
华中世纪星数控车床的几种精确对刀方法

对 刀是 数 控 加 工 中的 主 要 操 作 和 重 要 外 , 把 刀具 在 使 用 过 程 中 还 会 出 现 不 同 A 点 的 X机 床 坐标 , 刀后停 车 , 量 已 切 每 退 测 技 能 。 对 刀 的准 确 性 决 定 了零 件 的 加 工精 程 度 的 磨 损 , 此 各 刀 的 刀 偏 置 和 磨 损 值 削轴 段 外径 中 D。 因 度 , 时 , 刀 效率 还 直 接 影 响数 控 加 工 效 需 要 进 行补 偿 。获 得 各 刀 刀偏 置 的 基本 原 同 对 () 准 刀按记 录值 通过 “ 3基 点动 +步 进” 率 。华 中 世纪 星 车 削 系 统是 武 汉 华 中数 控 理 是 : 刀均 对 准 工 件上 某 一 基 准 点 , 于 方 式 重 回 A 点 , 刀偏 表 的试 切 直 径 和 试 各 由 在 股 份 公 司 近 年推 出的 优 秀 国产 数 控 车 削 系
E H C N0LOGY NFORM A ION l I
工 业 技 术
华 中世 纪 星数 控 车 床 的 几种 精确 对 刀 方法
朱 海勇 申东 东 ( 壁职 业技术学院机 电工程学院 河南鹤壁 鹤
483 ) 5 0 0
摘 要: 本文 首先介 绍 了 数控 车床 常 用的 “ 试切对 刀法”的原理 以及对 刀思路 ; 着, 绍 了华中世 纪星车 削数控 系统的三种 手动试 切 接 介 对 刀方法 ; 为改进 其对 刀精度 , 据 “自动试 切- 测量_ 误 差补偿 ”的思路 , 根 + + 设计 出 了用程序控 制的 自动试切 法 , 井总结介 绍 了三种精 确 对 刀 方法 。 希 望能 对 大家 有所 帮助 。 关键词 : 数控 车床 对 刀 中图分类号 : G 9 T 5 6 文 献标识 码 : A 文章编 号 : 6 2 3 9 ( 0 8 I ( ) 0 6 — 2 1 7 - 7 12 0 ) 2b 一 0 6 0
华中世纪星数控车床中G92指令对刀方法

Z宵静 擎蕊衄
下述每种方法 的对刀 准备 工作均 相同 :在系统 M I D 功能子 菜单 下按 F 键 , 2 进入刀偏表 : ▲键移动蓝 色亮条 到各刀对应 的刀偏 号位 用 置 , F 键 ; 刀偏 号为 # 0 0 # 0 1# 0 2 # 0 3 # O 4的 x偏 按 5 将 00 、 0 、0 0 、0 0 、O O 0
如图 2 所示 ,由于各刀装夹在刀架 的 x z方 向的伸 长和位置不 、
同 .当非基准刀转位到加工位置 时.刀尖位置 B相对于 A点就有偏 置, 原来建立的工件坐标 系就不再适用了。 此外 , 刀具在使用过程 每把 中还会出现不同程度 的磨损 。 因此各刀的刀偏置和磨损值需要进行补 偿。 获得各刀刀偏置 的基本原理是 : 各刀均对准工件上某一基准点 ( 如 图 l的 A点) 由于 C T显 示的机床坐标 不同 . . R 因此将非基 准刀在该 点处的机床坐标通 过人 工计算或系统 软件 计算减去基准 刀在同样点 置 。 的机床坐标 . 就得到了各非基准刀的刀偏置。 () 5 与前述步骤( ) 5 相同。 2 多刀试切外圆轴段 . . 3 人工计算 获得刀偏置法 系统 在手动状态下对好 1 24号刀 , 、、 并切 出一个台阶轴 , 分别记 录各 刀切削终点 ( 图 3 F E D点 ) 如 中 、、 的机 床坐标 , 并测量各段 的直
华中数控对刀操作方法
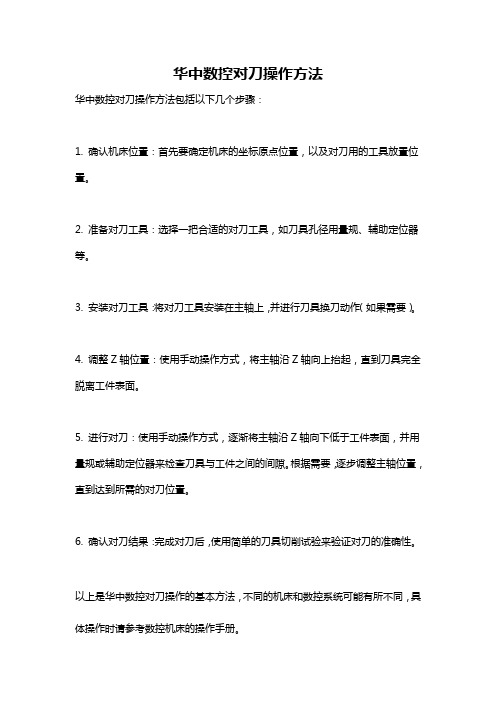
华中数控对刀操作方法
华中数控对刀操作方法包括以下几个步骤:
1. 确认机床位置:首先要确定机床的坐标原点位置,以及对刀用的工具放置位置。
2. 准备对刀工具:选择一把合适的对刀工具,如刀具孔径用量规、辅助定位器等。
3. 安装对刀工具:将对刀工具安装在主轴上,并进行刀具换刀动作(如果需要)。
4. 调整Z轴位置:使用手动操作方式,将主轴沿Z轴向上抬起,直到刀具完全脱离工件表面。
5. 进行对刀:使用手动操作方式,逐渐将主轴沿Z轴向下低于工件表面,并用量规或辅助定位器来检查刀具与工件之间的间隙。
根据需要,逐步调整主轴位置,直到达到所需的对刀位置。
6. 确认对刀结果:完成对刀后,使用简单的刀具切削试验来验证对刀的准确性。
以上是华中数控对刀操作的基本方法,不同的机床和数控系统可能有所不同,具体操作时请参考数控机床的操作手册。
华中世纪星数控车床 轴类零件程序输入、对刀及仿真操作
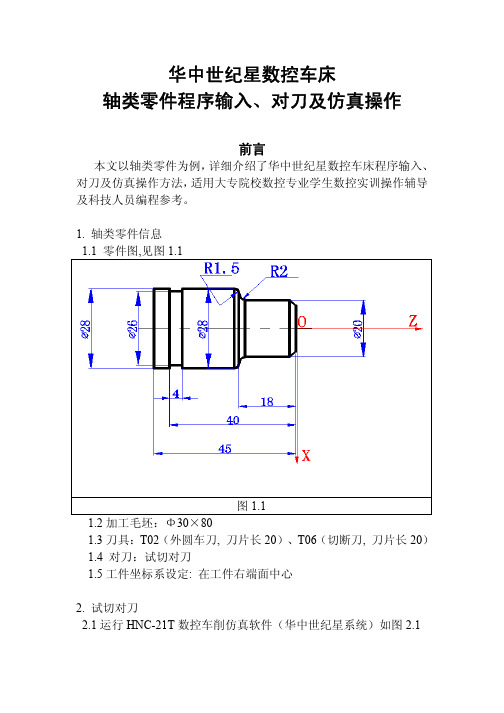
华中世纪星数控车床轴类零件程序输入、对刀及仿真操作前言本文以轴类零件为例,详细介绍了华中世纪星数控车床程序输入、对刀及仿真操作方法,适用大专院校数控专业学生数控实训操作辅导及科技人员编程参考。
1. 轴类零件信息1.1 零件图,见图1.1图1.11.2加工毛坯:Φ30×801.3刀具:T02(外圆车刀, 刀片长20)、T06(切断刀, 刀片长20)1.4 对刀:试切对刀1.5工件坐标系设定: 在工件右端面中心2. 试切对刀2.1运行HNC-21T数控车削仿真软件(华中世纪星系统)如图2.1图2.12.2输入、编辑程序2.2.1在记事本上输入程序,保存为.nc文件,如图2.2.1.1和图2.2.1.2图2.2.1.12.2.2将程序导入数控系统[程序编辑F2]Î[文件管理F1]Î[新建文件F2]Î输入新文件名(例O0100)Î[TAB]键Î[打开]按钮Î选择代码文件.nc (例O0100),如图2.2.2图2.1.2图2.2.1.22.3 机床参数设置 [参数设置]按钮Î[机床参数]:选择(后置刀架、八方刀架), 如图2.3.1和图2.3.2图2.3.1 图2.3.22.4安装刀具[刀具管理]按钮:选择有关刀具, 如图2.4图2.42.5 颜色参数设置[参数设置]按钮Î[显示颜色]:选择[刀具加工后工件显示颜色[和[刀路轨迹显示颜色],如图2.5.1和图2.5.2图2.5.1 图2.5.22.6安装工件[工件设置]按钮Î[设置毛坯]:选择工件的直径和长度,如图2.6.1和图2.6.2图2.6.1 图2.6.22.7 试切对刀,将工件坐标系设定在工件右端面的中心。
2.7.1 T02刀(外圆刀)对刀2.7.1.1 先进行手动返回参考点的操作。
2.7.1.2 手动模式→试切工件端面→Z方向不动,沿X方向退出, 如图2.7.1.2.1→→出现图2.7.1.2.2,按将光标移至“试切长度”→输入0→按→T02刀Z轴对刀完毕。
华中世纪星数控车床几种精确对刀方法

华中世纪星数控车床的几种精确对刀方法本文是一篇非常实用的文章,文中首先介绍了数控车床常用的“试切对刀法”的原理及对刀思路;接着,介绍了华中世纪星车削数控系统的四种手动试切对刀方法;为改进其对刀精度,根据“自动试切→测量→误差补偿”的思路,设计出了用程序控制的自动试切法,并总结介绍了四种精确对刀方法。
文后还给出了几种对刀的示例程序,可能会对大家有所帮助。
序,可能会对大家有所帮助。
对刀是数控加工中的主要操作和重要技能。
对刀是数控加工中的主要操作和重要技能。
对刀的准确性决定了零件的加工精度,同时,对刀效率还直接影响数控加工效率。
华中世纪星车削系统是武汉华中数控股份公司近年推出的优秀国产数控车削系统,是2004年首届全国数控技能大赛的指定数控车削系统之一。
但遗憾的是,华中公司以往多通过其技术人员口头向用户说明对刀操作,在他们编写的《操作说明书》中却没有提到对刀操作,给用户学习、使用带来不便。
笔者通过实践探索,结合教学、技能考证培训与加工实践的经验,将该系统的几种快速准确的试切对刀方法予以小结,供大家参考,结,供大家参考,希望借此对国产数控系统的推广,推动我国数控技希望借此对国产数控系统的推广,推动我国数控技能人才的培训尽一点微薄之力。
能人才的培训尽一点微薄之力。
一、数控车试切对刀法的原理及对刀思路深入理解数控车床的对刀原理,对于操作者保持清晰的对刀思路、熟练掌握对刀操作以及提出新的对刀方法都具有指导意义。
对刀的实质是确定随编程而变化的工件坐标系的程序原点在唯一的机床坐标系中的位置。
对刀的主要工作是获得基准刀程序起点的机床坐标和确定非基准刀相对于基准刀的刀偏置。
和确定非基准刀相对于基准刀的刀偏置。
本文作以下约定来说明试切法对刀的原理与思路:使用华中世纪星教学型车削系统HNC-21T HNC-21T(应用软件版本号为(应用软件版本号为5.305.30);以工件右);以工件右端面中心为程序原点,用G92指令设定工件坐标系;直径编程,程序起点H 的工件坐标为(的工件坐标为(100100100,,5050);刀架上装四把刀:);刀架上装四把刀:);刀架上装四把刀:11号刀为90°外圆粗车刀、外圆粗车刀、22号基准刀为90°外圆精车刀、90°外圆精车刀、33号刀为切断刀、号刀为切断刀、44号刀为60°三角螺纹刀(全文所举实例均与此相同)。
华中世纪星数控铣床编程与仿真操作实例02:刀具半径补偿
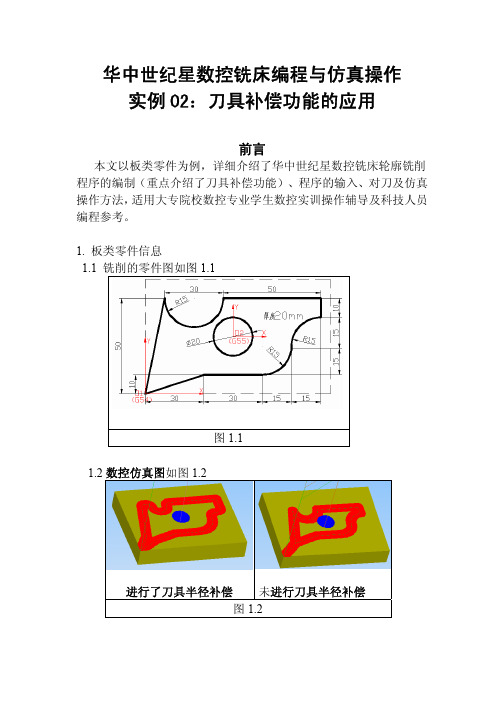
华中世纪星数控铣床编程与仿真操作 实例02:刀具补偿功能的应用前言本文以板类零件为例,详细介绍了华中世纪星数控铣床轮廓铣削程序的编制(重点介绍了刀具补偿功能)、程序的输入、对刀及仿真操作方法,适用大专院校数控专业学生数控实训操作辅导及科技人员编程参考。
1. 板类零件信息1.1 铣削的零件图如图1.1图1.11.2数控仿真图如图1.2进行了刀具半径补偿未进行刀具半径补偿图1.21.3 零件基本信息1.3.1 加工毛坯:130×100×201.3.2刀具:001φ12×120端铣刀、003φ20×100圆角刀1.3.3对刀:自动对刀1.3.4工件坐标系设定: 在工件上端面左下角2. 刀具半径补偿和刀具长度补偿功能2.1 刀具半径补偿功能2.1.1 刀具半径补偿原理2.1.1.1轮廓铣削编程加工过程中,系统程序控制的总是让刀具刀位点行走在程序轨迹上。
铣刀的刀位点通常是定在刀具中心上,若编程时直接按图纸上的零件轮廓线进行,又不考虑刀具半径补偿,则将是刀具中心(刀位点)行走轨迹和图纸上的零件轮廓轨迹重合,这样由刀具圆周刃口所切削出来的实际轮廓尺寸,就必然大于或小于图纸上的零件轮廓尺寸一个刀具半径值,因而造成过切或少切现象。
为了确保铣削加工出的轮廓符合要求,就必须在图纸要求轮廓的基础上,整个周边向外或向内预先偏离一个刀具半径值,作出一个刀具刀位点的行走轨迹,求出新的节点坐标,然后按这个新的轨迹进行编程(如图2.1.1.1所示),这就是人工预刀补编程。
人工预刀补编程图2.1.1.12.1.1.2现在很多数控机床的控制系统自身都提供自动进行刀具半径补偿的功能,只需要直接按零件图纸上的轮廓轨迹进行编程,在整个程序中只在少量的地方加上几个刀补开始及刀补解除的代码指令。
这样无论刀具半径大小如何变换,无论刀位点定在何处,加工时都只需要使用同一个程序或稍作修改,你只需按照实际刀具使用情况将当前刀具半径值输入到刀具数据库中即可。
华中世纪星数控车床的操作面板简介

华中世纪星数控车床的操作面板简介华中世纪星车削数控装置的操作面板如图1-1所示。
图1-1 华中世纪星操作面板1. 软件操作面板华中世纪星HNC-21T的软件操作界面如图1-3所示。
其界面由如下几个部分组成:①图形显示窗口。
可以根据需要,用功能键F9设置窗口的显示内容。
②菜单命令条。
通过菜单命令条中的功能键F1~F10来完成系统功能的操作。
③运行程序索引。
自动加工中的程序名和当前程序段行号。
④选定坐标系下的坐标值。
坐标系可在机床坐标系/工件坐标系/相对坐标系之间切换;显示值可在指令位置/实际位置/剩余进给/跟踪误差/负载电流/补偿值之间切换。
⑤工件坐标零点。
工件坐标系零点在机床坐标系下的坐标。
⑥辅助功能。
自动加工中的M、S、T代码。
⑦当前加工程序行。
当前正在或将要加工的程序段。
⑧当前加工方式、系统运行状态及当前时间。
系统工作方式根据机床控制面板上相应按键的状态可在自动运行、单段运行、手动、增量、回零、急停、复位等之间切换;系统工作状态在“运行正常”和“出错”之间切换;系统时钟显示当前系统时间。
⑨机床坐标、剩余进给。
机床坐标显示刀具当前位置在机床坐标系下的坐标;剩余进给指当前程序段的终点与实际位置之差。
⑩直径/半径编程、公制/英制编程、每分进给/每转进给、快速修调、进给修调、主轴修调。
图1-3 华中世纪星HNC-21T软件操作界面操作界面中最重要的一块是菜单命令条。
系统功能的操作主要通过菜单命令条中的功能键F1~F10来完成。
由于每个功能包括不同的操作,菜单采用层次结构,即在主菜单下选择一个菜单项后,数控装置会显示该功能下的子菜单,用户可根据该子菜单的内容选择所需的操作,如图1-4所示。
当要返回主菜单时,按子菜单下的F10键即可。
图1-4 菜单层次2. 机床控制面板机床手动操作主要由机床控制面板完成,机床控制面板如图1-5所示。
①②按下“手动”按键(指示灯亮),系统处于手动运行方式,可点动移动机床坐标轴。
数控车床上刀补用法
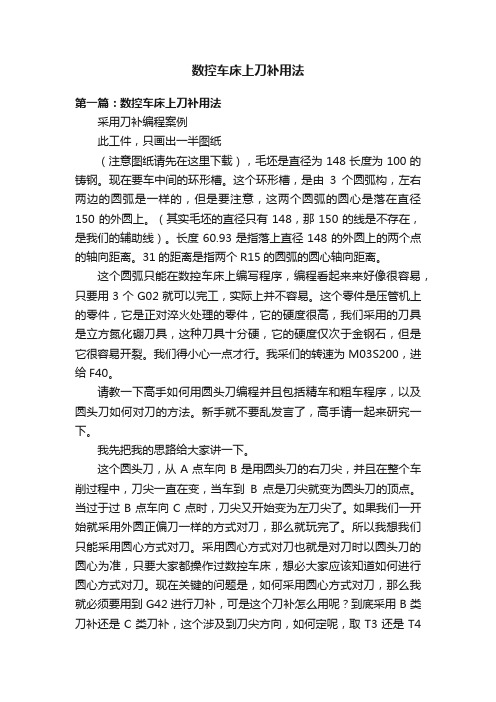
数控车床上刀补用法第一篇:数控车床上刀补用法采用刀补编程案例此工件,只画出一半图纸(注意图纸请先在这里下载),毛坯是直径为148长度为100的铸钢。
现在要车中间的环形槽。
这个环形槽,是由3个圆弧构,左右两边的圆弧是一样的,但是要注意,这两个圆弧的圆心是落在直径150的外圆上。
(其实毛坯的直径只有148,那150的线是不存在,是我们的辅助线)。
长度60.93是指落上直径148的外圆上的两个点的轴向距离。
31的距离是指两个R15的圆弧的圆心轴向距离。
这个圆弧只能在数控车床上编写程序,编程看起来来好像很容易,只要用3个G02就可以完工,实际上并不容易。
这个零件是压管机上的零件,它是正对淬火处理的零件,它的硬度很高,我们采用的刀具是立方氮化硼刀具,这种刀具十分硬,它的硬度仅次于金钢石,但是它很容易开裂。
我们得小心一点才行。
我采们的转速为M03S200,进给F40。
请教一下高手如何用圆头刀编程并且包括精车和粗车程序,以及圆头刀如何对刀的方法。
新手就不要乱发言了,高手请一起来研究一下。
我先把我的思路给大家讲一下。
这个圆头刀,从A点车向B是用圆头刀的右刀尖,并且在整个车削过程中,刀尖一直在变,当车到B点是刀尖就变为圆头刀的顶点。
当过于过B点车向C点时,刀尖又开始变为左刀尖了。
如果我们一开始就采用外圆正偏刀一样的方式对刀,那么就玩完了。
所以我想我们只能采用圆心方式对刀。
采用圆心方式对刀也就是对刀时以圆头刀的圆心为准,只要大家都操作过数控车床,想必大家应该知道如何进行圆心方式对刀。
现在关键的问题是,如何采用圆心方式对刀,那么我就必须要用到G42进行刀补,可是这个刀补怎么用呢?到底采用B类刀补还是C类刀补,这个涉及到刀尖方向,如何定呢,取T3还是T4还是T8呢?看起在每个不同时间,刀尖的方向都不同,到底应该如何取刀尖方向呢?还有刀补从哪个程序开始补呢?又在哪里结束呢?我第一次编写这个程序时,我采用圆心方式对刀,我将圆弧分成两半,我用T0101车左边圆弧,用T0102车圆弧,在中间开始换刀偏。
- 1、下载文档前请自行甄别文档内容的完整性,平台不提供额外的编辑、内容补充、找答案等附加服务。
- 2、"仅部分预览"的文档,不可在线预览部分如存在完整性等问题,可反馈申请退款(可完整预览的文档不适用该条件!)。
- 3、如文档侵犯您的权益,请联系客服反馈,我们会尽快为您处理(人工客服工作时间:9:00-18:30)。
华中世纪星数控车床对刀及刀补值的设置方法
1. 刀具补偿值设置(F4)
在主操作界面下,按F4键进入刀具补偿功能子菜单。
命令行与菜单条的显示如图1-9所示。
图1-9 刀具补偿功能主菜单
刀具补偿分为刀具的几何补偿和刀具的半径补偿。
T代码指定刀具的几何补偿(偏置补偿与磨损补偿之和),其后的4位数字分别表示选择的刀具号(前两位数字)和刀具偏置补偿号(后两位数字)。
补偿号可以和刀具号相同,也可以不同,即一把刀具可以对应多个补偿号(值)。
刀具补偿号为00表示补偿量为0,即取消补偿功能。
G40、G41、G42指定刀具的半径补偿。
(1)刀偏数据设置(F4→F1)
刀具的几何补偿包括刀具的偏置补偿和刀具的磨损补偿,刀具的偏置补偿有绝对刀具偏置补偿和相对刀具偏置补偿两种形式。
我们推荐采用绝对刀具偏置补偿。
在主操作界面下,按F4→F1进入刀具偏置编辑画面如图1-10所示。
图1-10 刀具偏置编辑
车床编程轨迹实际上是刀尖的运动轨迹,但实际中不同的刀具的几何尺寸、安装位置各不相同,其刀尖点相对于刀架中心的位置也就不同。
因此需要将各刀具刀尖点的位置值进行测量设定,以便系统在加工时对刀具偏置值进行补偿。
我们采用试切法来设置绝对刀具偏置补偿值。
图1-11 绝对刀偏法刀具偏置补偿值
如图1-11所示,刀具偏置值即机床回到机床零点时,刀架工作位上各刀刀尖位置相对工件零点的有向距离。
当执行刀具偏置补偿时,各刀以此值设定各自的工件坐标系。
机床到达机床零点时,机床坐标值显示均为零,整个刀架上的点可考虑为一理想点,故当各刀对刀时,机床零点可视为在各刀刀位点上。
我们通过输入试切直径、长度值,自动计算工件零点相对与各刀刀位点的距离。
其步骤如下:
①用光标键将蓝色亮条移动到要设置刀具偏置值的行。
②用刀具试切工件的外径,然后沿Z轴方向退刀,在此过程中不要移动X轴。
③测量试切后的工件外径,如为ф25.26 ,然后将此值输入到刀偏表中“#××01”一行中“试切直径”一栏中并确认,设置好X偏置。
④用刀具试切工件的右端面,然后沿X轴方向退刀,在此过程中不要移动Z轴。
⑤计算试切工件端面到该刀具要建立的工件坐标系的零点位置的有向距离,如为“3mm”,然后将“3”输入到刀偏表中“#××01”一行中“试切长度”一栏中并确认,设置好Z偏置。
如果要设置其余的刀具,就重复以上步骤。
需要注意,对刀前,机床必须先回机床零点。
(2)刀具磨损量补偿参数设置(F4→F1)
刀具使用一段时间后磨损,也会使产品尺寸产生误差,因此需要对其进行补偿,该补偿值与刀具偏置补偿存放在同一个寄存器的地址号中如图1-10所示。
例如在粗加工时,将“X磨损”输入“0.5”(0.5mm作为精加工的余量),工件粗加工后,实测工件值大于图样尺寸0.48mm,则相应刀具磨损量为“0.5-0.48=0.02”,在图1-10刀偏表中,“X磨损”输入“0.02”,自动加工后即可保证工件尺寸。
若长度出现偏差也可以用刀具磨损量补偿,在图1-10刀偏表中“Z磨损”输入相应值即可。
(3)刀具半径补偿数据设置(F4→F2)
刀尖圆弧半径补偿是通过G41、G42、G40代码及T代码指定的刀尖圆弧半径补偿号来加入或取消半径补偿值。
车刀刀尖的方向号定义了刀具刀位点与刀尖圆弧中心的位置关系,其从0~9有十个方向,如图1-12所示。
图1-12 车刀刀尖方位定义
在主操作界面下,按F4→F2进入刀补数据设置画面,如图1-13所示。
图1-13 刀补数据设置
输入刀补数据的操作步骤如下:
①用光标键移动蓝色亮条到要编辑的选项。
②按Enter键,蓝色亮条所指刀具数据的颜色和背景都发生变化,同时有一光标在闪烁。
③进行编辑修改。
④修改完毕,按Enter键确认。
⑤若输入正确,图形显示窗口相应位置将显示修改过的值,否则原值不变。
2. 坐标系的设置(F5→F1)
用绝对刀具偏置补偿值的方法可直接设定工件坐标系,当执行刀具偏置补偿时,各刀以此值设定各自的工件坐标系,在编程时不用G92或G54~G59。
如使用G54~G59设定工件坐标系,应将T0101写成T0100 , T0202写成T0200以后的刀具以次类推。
也就是系统在执行T0100程序段时只做调刀动作,并不建立工件坐标系。
在主操作界面下,按F5→F1键进入G54、G55等坐标系数据显示窗口,如图1-14所示。
以程序段“G54 X80 Z100”为例,其设置操作步骤如下:
①选择要输入的数据类型G54坐标系。
②选用使用的刀具T01并在手动方式下切削工件外圆一刀,沿Z轴的正方向退刀,用千分尺测量工件直径为“ф45.420”,同时记录下CRT显示“机床实际坐标”一栏“X”值,如为“-41.124”,得X=(-41.124)+( -45.420)= -86.544。
在工件右端面试切一刀,沿X轴的正方向退刀,并记录下CRT显示“机床实际坐标”一栏“Z”值,如“-315.225”,即Z=-315.225。
③输入零点偏置值。
在图1-14显示方式下输入“X-86.544”、“Z-315.225”,确认并退出界面,此时系统便将一号刀零点偏置数据X、Z(即工件零点在机床坐标系下的坐标值)自动记忆到系统中。
此时无论刀具T01当前点处于何位置,当调出程序段“G54 X80 Z100”执行时,刀具总能找到在工件坐标系下X 80、Z100的点,即数控系统用新的工件坐标系取代了回参考点时所建立的机床坐标系。
图1-14 坐标系设置
使用多把刀具时,每把刀对刀的方法相同,可在G54/G55/G56/G57/G58/G59之中任意选择,但坐标系一定要与所使用的刀具的刀位号对应。