数控车床对刀的原理及方法
项目二数控车床对刀操作课件
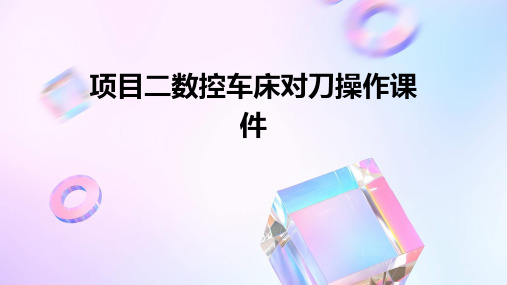
目录
• 对刀操作的基本概念 • 对刀操作的步骤 • 对刀操作的注意事项 • 对刀操作的应用实例 • 对刀操作常见问题及解决方案
01
对刀操作的基本概念
对刀操作的定义
对刀操作是指在数控车床上,通过调整刀具相对于工件的位 置,使刀具的刀位点对准工件坐标系的某一参考点,以确保 加工过程中刀具与工件正确对齐的过程。
2. 使用减震装置或工具夹具等辅助工具 ,减小振动传递;
详细描述:切削振动的原因有多种,如 工件材料硬度过高等。为了解决这一问 题,可以采取以下措施
1. 调整主轴转速和切削深度等参数,以 改变切削力的变化规律,减少振动;
加工精度问题及解决方案
总结词:加工精度问题是对刀操作中的核心问题之一, 它直接影响到工件的质量和性能。 1. 选用高精度刀具和夹具,提高对刀精度;
总结词
异形零件的形状各异,对刀操作需要根据零件的具体形状进行调整。
详细描述
在异形零件的对刀操作中,需要仔细观察工件的形状,并根据需要进行调整。对于某些具有特殊形状的零件,可 能需要采用特殊的对刀方法,以确保加工精度和表面质量。同时,还需要特别注意安全问题,以避免因操作不当 而造成意外事故。
05
对刀操作常见问题及解决 方案
刀具安装
将刀具正确安装在刀架上 ,确保刀具夹紧牢固,不 会松动。
刀具调整
调整刀具的角度、高度和 偏移量,以适应加工需求 。
刀具补偿参数设置
刀具长度补偿
根据刀具的实际长度,设 置刀具长度补偿参数,确 保加工过程中的切深与编 程深度一致。
刀具半径补偿
根据刀具的实际半径,设 置刀具半径补偿参数,确 保加工出的工件轮廓与编 程轮廓一致。
cnc数控车床坐标系机器对刀的工作原理
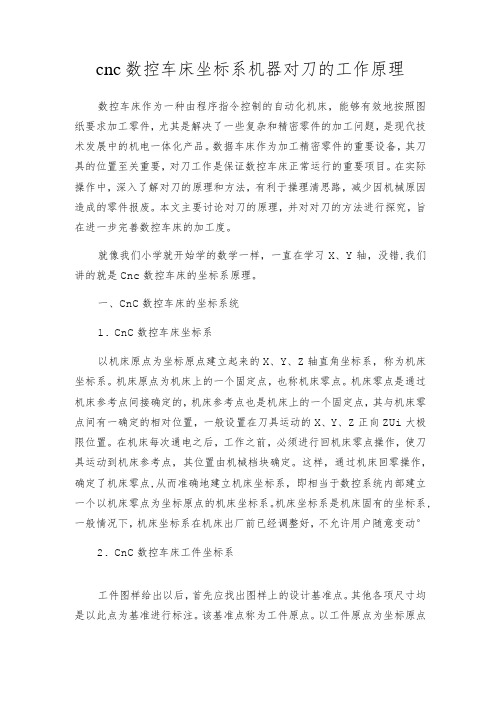
cnc数控车床坐标系机器对刀的工作原理数控车床作为一种由程序指令控制的自动化机床,能够有效地按照图纸要求加工零件,尤其是解决了一些复杂和精密零件的加工问题,是现代技术发展中的机电一体化产品。
数据车床作为加工精密零件的重要设备,其刀具的位置至关重要,对刀工作是保证数控车床正常运行的重要项目。
在实际操作中,深入了解对刀的原理和方法,有利于操理清思路,减少因机械原因造成的零件报废。
本文主要讨论对刀的原理,并对对刀的方法进行探究,旨在进一步完善数控车床的加工度。
就像我们小学就开始学的数学一样,一直在学习X、Y轴,没错,我们讲的就是Cnc数控车床的坐标系原理。
一、CnC数控车床的坐标系统C数控车床坐标系以机床原点为坐标原点建立起来的X、Y、Z轴直角坐标系,称为机床坐标系。
机床原点为机床上的一个固定点,也称机床零点。
机床零点是通过机床参考点间接确定的,机床参考点也是机床上的一个固定点,其与机床零点间有一确定的相对位置,一般设置在刀具运动的X、Y、Z正向ZUi大极限位置。
在机床每次通电之后,工作之前,必须进行回机床零点操作,使刀具运动到机床参考点,其位置由机械档块确定。
这样,通过机床回零操作,确定了机床零点,从而准确地建立机床坐标系,即相当于数控系统内部建立一个以机床零点为坐标原点的机床坐标系。
机床坐标系是机床固有的坐标系,一般情况下,机床坐标系在机床出厂前已经调整好,不允许用户随意变动°C数控车床工件坐标系工件图样给出以后,首先应找出图样上的设计基准点。
其他各项尺寸均是以此点为基准进行标注。
该基准点称为工件原点。
以工件原点为坐标原点建立的X、Y、Z轴直角坐标系,称为工件坐标系。
工件坐标系是用来确定工件几何形体上各要素的位置而设置的坐标系,工件原点的位置是人为设定的,它是由编程人员在编制程序时根据工件的特点选定的,所以也称编程原点。
cnc数控车床加工零件的工件原点一般选择在工件右端面、左端面或卡爪的前端面与Z轴的交点上。
数控机床的对刀原理及常用的对刀方法

万方数据万方数据2.6百分表(或千分表)对刀法(一般用于圆形工件的对刀)1)并,Y向对刀。
将百分表的安装杆装在刀柄上,或将百分表的磁性座吸在主轴套筒上,移动工作台使主轴中心线(即刀具中心)大约移到工件中心,调节磁性座上伸缩杆的长度和角度,使百分表的触头接触工件的圆周面,(指针转动约0.1mill)用手慢慢转动主轴,使百分表的触头沿着工件的圆周面转动,观察百分表指针的便移情况,慢慢移动工作台的轴和轴,多次反复后,待转动主轴时百分表的指针基本在同一位置(表头转动一周时,其指针的跳动量在允许的对刀误差内,如0.02mm),这时可认为主轴的中心就是轴和轴的原点。
2)卸下百分表装上铣刀,用其他对刀方法如试切法、塞尺法等得到z轴坐标值。
2.6专用对刀器对刀法易撞坏)占用机时多(如试切需反复切量几次),人为带来的随机性误差大等缺点,已经适应不了数控加工的节奏,更不利于发挥数控机床的功能。
用专用对刀器对刀有对刀精度高、效率高、安全性好等优点,把繁琐的靠经验保证的对刀工作简单化了,保证了数控机床的高效高精度特点的发挥,已成为数控加工机上解决刀具对刀不可或缺的一种专用工具。
参考文献:[1]陈志雄.数控机床与数控编程技术[M].北京:电子工业出版社,2007.[2]华中数才全一操作说明书[z].武汉华中数控股份有限公司.[3]任国兴主编.数控铣床华中系统编程与操作实训[M].北京:中国劳动社会保障出版社,2007.传统对刀方法有安全性差(如塞尺对刀,硬碰硬刀尖收稿日期:2009一10—14(上接第38页)通过机床附带的后处理程序后即可得到控制机床运行的代码程序。
创建刀轨选择的加工参数及其他加工信息汇总列在表l中。
表I加工参数及其他加工信息加工设备加工工具直径/mm板料毛坯尺寸/mm3切削连接方式固定好板料,对好刀具后,将加工代码程序输入机床,既可实现壁板零件的自动加工成形。
2.2.4成形零件机床加工完成后,得到的实际零件如图5所示。
数控车床对刀的原理及方法

数控车床对刀的原理及方法一、数控车床对刀的原理:对刀是数控加工中的主要操作和重要技能。
在一定条件下,对刀的精度可以决定零件的加工精度。
同时,对刀效事还直接影响数控加工效丰。
仅仅知道对刀方法是不够的。
还要知道数控系统的各种对刀设置方式,。
以及这些方式在加工程序中的调用方法,同时要知道各种对刀方式的优缺点。
使用条件等。
一股来说,数控加工零件的编程和加工是分开进行的。
数控编程员根据零件的设计图纸,速定一个方便编程的工件坐标系,工件坐标系-般与零件的工艺基准或设计基准重合。
在工件坐标系下进行零件加工程序的编制,对刀时,应使指刀位点与对刀点重合,所谓刀位点是指刀具的定位基准点,对于车刀来说,其刀位点是刀失。
对刀的目的是确定对刀点。
在机床坐标系中的绝对坐标值,测量刀具的刀位偏基值。
对刀点找正的准确度直接影响加工精度。
在实际加工工件时。
使用一把刀具一般不能满足工件的加工要求,通常要使用多把刀具进行加工。
在使用多把车刀加工时,在换刀位置不变的情况下,换刀后刀失点的几何位置将出现差异,这就要求不同的刀具在不同的起始位置开始加工时。
都能保证程序正常运行。
为了解决这个问题。
机床数控系統配备了刀具几何位置补能的功能,利用刀其几何位置补偿功能,只要事先把每把刀相对于某一预先选定的基准刀的位置偏差测量出来,输入到数控系统的刀具梦数补正栏指定组号里,在加工程序中利用T指令,即可在刀具轨述中自动补偿刀具位置偏差。
刀具位置值差的利量同样也需通过对刀操作来实现。
生产厂家在制造数控车床,必须建立位置测量,控制、显示的统基准点。
该基准点就是机床坐标系原点,也就是机床机械目零后所处的位置。
操作方法01数控车床对刀是车床加工技术中比较复杂的工艺之一,它的精度将会直接影响到所加工零部件的精度,所以不能马虎。
02数控车床对刀的基本原理就是将零件的坐标系与数控机床的坐标系整合起来,然后依据这个坐标系来确定对刀位置。
03目前数控车床大部分采用的是对刀器主动对刀,对刀器会自动向零件确定一个原点位置,这是十分方便快捷的对刀方法。
简述数控车床试切法对刀的操作步骤

简述数控车床试切法对刀的操作步骤
一、试切法对刀的原理
试切法对刀是根据数控车床的加工工艺要求,选择一种适当的切削速度和进给量,将刀具在工件上进行一次或数次试切,达到最佳的切削效果。
这种方法可以避免由于刀具磨损而引起的加工误差,同时也可以提高加工质量和效率。
二、试切法对刀的操作步骤
1. 准备工作
(1)检查机床和刀具是否处于正常状态。
(2)选择合适的试切速度和进给量。
(3)选好试切刀具,安装到刀架上。
2. 进行试切
(1)将工件放置在工作台上,固定好。
(2)打开数控设备,将试切程序输入计算机。
(3)手动调整切削位置和切削深度,使刀具与工件接触。
(4)启动数控设备,开始试切。
(5)检查试切效果,根据需要调整切削参数,再进行试切。
3. 完成试切
(1)试切结束后,停止机床运转。
(2)检查试切工件的表面质量,进行必要的调整。
(3)重复试切,直至达到最佳的加工效果。
三、小结
试切法对刀是数控车床加工的重要工艺方法,通过合理的试切参数选择和试切操作,可以提高加工效率和加工质量。
因此,在操作过程中,需要严格遵守操作规程,确保安全和加工质量。
数控机床对刀

(7)将光标移动至欲设定的偏置号处。
(8)输入Zβ(或0)。
(9)按软键[MESURE]。
(10)在手动方式中用一把实际刀具切削外圆。
(11)仅仅在Z方向上退刀,不要移动X,停止主轴。
(12)测量被车削部分的直径D。
(13)按功能键OFFSET/SETING。
(14)按软键[OFFSET]。
实习总结:
用试切法确定起刀点的位置对刀的步骤:
(1)在MDI或手动方式下,用基准刀切削工件端面;
(2)用点动移动X轴使刀具试切该端面,然后刀具沿X轴方向退出,停主轴。
记录该Z轴坐标值并输入系统。
(3)用基准刀切量工件外径。
(4)用点动移动Z轴使刀具切该工件的外圆表面,然后刀具沿Z方向退出,停主轴。用游表卡尺测量工件的直径,记录该X坐标值并输入系统。
(3)对刀点与对刀:对刀点是用来确定刀具与工件的相对位置关系的点,是确定工件坐标系与机床坐标系的关系的点。
对刀就是将刀具的刀位点置于对刀点上,以便建立工件坐标系。
(4)对刀基准(点):对刀时为确定对刀点的位置所依据的基准,该基可以是点、线、面,它可以设在工件上或夹具上或机床上。
(5)对刀参考点:是用来代表刀架、刀台或刀盘在机床坐标系内的位置的参考点,也称刀架中心或刀具参考点。
(5)对第二把刀,让刀架退离工件足够的地方,选择刀具号,重复(1)—(4)步骤。
法拉克车床对刀:
基准刀的对法:
(1)在手动方式中用一把实际刀具切削端面。
(2)仅仅在X轴方向上退刀,不要移动Z轴,停止主轴。
(3)测量工件坐标系的零点至端面的距离β(或0)。
(4)按功能键OFFSET/SETING。
(5)按软键[OFFSET]。
数控车床对刀的原理与方法

数控车床对刀的原理与方法数控车床的刀具对刀是确保机床工作精度的关键步骤之一、对刀准确度影响着工件的加工精度和质量。
数控车床的对刀一般采用刀具测量、感应式对刀、比较式对刀等方式。
下面将介绍数控车床对刀的原理和方法。
1.刀具测量:数控车床通常提供一个专门的测量装置,用来测量刀具的长度和半径。
通过刀具测量装置的读数,可以计算出刀具的几何参数,以便在数控系统中设置正确的刀具补偿值。
2.感应式对刀:数控车床使用感应式传感器,通过与刀具接触或靠近刀具来感应刀具的位置信息。
传感器可以测量到刀具的长度和半径,并将这些信息传递给数控系统。
3.比较式对刀:比较式对刀是通过测量工件上已加工的特征来确定刀具的位置。
例如,在数控车床上面加工一个规定尺寸的槽后,可以使用传感器测量槽的尺寸,然后根据预定的槽尺寸,调整刀具的位置。
根据数控车床对刀的原理,可以采用以下方法进行对刀:1.感应式对刀:数控车床上通常有一个专用的感应式对刀装置。
在对刀过程中,需要选取一把已知长度的刀具,并使用感应式传感器测量其长度。
将测量到的刀具长度输入数控系统,系统会自动计算并设置刀具长度补偿值。
然后,将正确长度的刀具安装到车刀刀架上,依次对各个刀具进行对刀。
2.刀具测量:刀具测量是比较常见的对刀方式。
使用专用的刀具测量设备可以测量刀具的长度和半径。
在对刀过程中,首先选取一把已知长度和半径的刀具,将其放入测量设备中测量。
然后,将测量到的数值输入数控系统,系统会自动计算出刀具的补偿值。
最后,将已校准好的刀具安装到车刀刀架上。
3.比较式对刀:在比较式对刀中,首先需要加工一个已知尺寸的特征,例如一条槽或一组孔。
然后,使用专用的测量仪器测量加工后的特征尺寸。
将测量到的尺寸和预定的尺寸进行比较,计算出相应的补偿值。
最后,根据计算结果调整刀具的位置。
除了上述方法外,还可以使用图形化的数控系统来辅助进行对刀。
通过在数控系统中显示工件轮廓的模拟图像,可以直观地观察刀具的位置与工件轮廓之间的关系,从而调整刀具的位置。
数控车床试切法对刀

外圆刀 螺纹刀 切断刀 Z
X
3)加工之前要检查对刀数据
试切法对刀小结:
1. 完成对刀操作,是正确执行零件加工程序的前提。 2.试切法对刀不需要任何辅助设备,操作简单方便。 3.试切法对刀要较多地占用机床时间。 4.其他对刀方法。
② 通过手轮移动刀具切外圆。
X
③ 沿+Z方向退刀,X方向不移动。
2)数控车床试切法X向对刀数据输入 车削外圆后Z向退刀停车测量外圆直径在左上角输入测量值
3)数控车床试切法对刀数据调用
调用T指令后系统可识别工件坐标系的位置
G00 Z40 ;
O、 z、
X、
40
六、注意事项
1)刀补调用指令(T指令)在程序中的正确使用 2)加工中用到的每把刀具均需进行对刀
1)数控车床试切法Z向对刀步骤
O
Z
① 在MDI(录入)状态下旋转工件 。
② 通过手轮移动刀具平端面。
X
③ 沿 +X 方向退出刀具, Z方向不移动。
2)数控车床试切法Z向对刀数据输入 车削端面后在左上角Z的位置输入0或者点清零
2. X向对刀 1)数控车床试切法X向对刀步骤
O
Z
① 在MDI状态下旋转工件。
数控车床试切法对刀
一、机床坐标系和工件坐标系 (1)数控车床机床坐标系
O
机床坐标系中,坐标 值描述红色点位置 (靠近工件为负)
Z
200
X
一、机床坐标系和工件坐标系 (2)数控车床工件坐标系
工件坐标系中,坐标 值描述刀尖点位置
O、 z、
X、
LOGO
三 工件坐标系位置的影响因素
1)工件坐标系原点Z坐标位置随着毛坯伸出卡盘长度而变化
- 1、下载文档前请自行甄别文档内容的完整性,平台不提供额外的编辑、内容补充、找答案等附加服务。
- 2、"仅部分预览"的文档,不可在线预览部分如存在完整性等问题,可反馈申请退款(可完整预览的文档不适用该条件!)。
- 3、如文档侵犯您的权益,请联系客服反馈,我们会尽快为您处理(人工客服工作时间:9:00-18:30)。
一、数控车床对刀的原理:对刀是数控加工中的主要操作和重要技能.在一定条件下,对刀的精度可以决定零件的加工精度,同时,对刀效率还直接影响数控加工效率.仅仅知道对刀方法是不够的,还要知道数控系统的各种对刀设置方式,以及这些方式在加工程序中的调用方法,同时要知道各种对刀方式的优缺点、使用条件等。
一般来说,数控加工零件的编程和加工是分开进行的。
数控编程员根据零件的设计图纸,选定一个方便编程的工件坐标系,工件坐标系一般与零件的工艺基准或设计基准重合,在工件坐标系下进行零件加工程序的编制。
对刀时,应使指刀位点与对刀点重合,所谓刀位点是指刀具的定位基准点,对于车刀来说,其刀位点是刀尖.对刀的目的是确定对刀点,在机床坐标系中的绝对坐标值,测量刀具的刀位偏差值.对刀点找正的准确度直接影响加工精度。
在实际加工工件时,使用一把刀具一般不能满足工件的加工要求,通常要使用多把刀具进行加工.在使用多把车刀加工时,在换刀位置不变的情况下,换刀后刀尖点的几何位置将出现差异,这就要求不同的刀具在不同的起始位置开始加工时,都能保证程序正常运行。
为了解决这个问题,机床数控系统配备了刀具几何位置补偿的功能,利用刀具几何位置补偿功能,只要事先把每把刀相对于某一预先选定的基准刀的位置偏差测量出来,输入到数控系统的刀具参数补正栏指定组号里,在加工程序中利用T 指令,即可在刀具轨迹中自动补偿刀具位置偏差.刀具位置偏差的测量同样也需通过对刀操作来实现。
生产厂家在制造数控车床,必须建立位置测量、控制、显示的统一基准点,该基准点就是机床坐标系原点,也就是机床机械回零后所处的位置。
数控机床所配置的伺服电机有绝对编码器和相对编码器两种,绝对编码器的开机不用回零,系统断电后记忆机床位置,机床零点由参数设定。
相对编码器的开机必须回零,机床零点由机床位置传感器确定.编程员按工件坐标系中的坐标数据编制的刀具运行轨迹程序,必须在机床坐标系中加工,由于机床原点与工件原点存在X向偏移距离和Z向偏移距离,使得实际的刀尖位置与程序指令的位置有同样的偏移距离,因此,须将该距离测量出来并设置进数控系统,使系统据此调整刀具的运动轨迹,才能加工出符合零件图纸的工件。
这个过程就是对刀,所谓对刀其实质就是测量工件原点与机床原点之间的偏移距离,设置工件原点在以刀尖为参照的机床坐标系里的坐标。
二、对刀方法对刀的方法有很多种,按对刀的精度可分为粗略对刀和精确对刀;按是否采用对刀仪可分为手动对刀和自动对刀;按是否采用基准刀,又可分为绝对对刀和相对对刀等。
但无论采用哪种对刀方式,都离不开试切对刀,试切对刀是最根本的对刀方法。
1.数控车床试车对刀方法图1(1)如图1,夹持工件,换需要对的刀具到刀架当前位.。
图2(2)如图2,在手动操作方式下,启动主轴,用当前刀具在加工余量范围内试切工件外圆,车的长度必须能够方便测量,X轴不要移动,沿Z 的正方向退出来,停主轴,测量所车的外圆尺寸Xa,如图3。
图3(3)按“OFS/SET”键如图4,按刀偏如图5,将光标移到与刀具号相对应的位置后,输入“Xa”,如图6,按操作面板上的“刀具测量”,再按显示器下面的软键“测量”,在对应的刀补位上生成对应刀补值.图4注意:刀具补偿包括“磨损”和“形状”补偿两部分,刀偏分形状和磨损,刀尖的位置放在形状里,尺寸的调整和刀具的磨耗放在磨损里。
两者之和构成车刀偏移量补偿参数。
如图5显示。
图5图6(4)如图7在手动方式下,再用该把刀去平工件端面,平完端面后,沿X正方向退出来,Z方向不动,停主轴,测量工件原点到工件端面的距离Lz。
图7(5)同(3)一样。
按“OFS/SET”键,进入“形状”补偿设定界面,将光标移到与刀位号相对应的位置后,输入“Lz”,按操作面板上的“刀具测量”,再按显示器下面的软键“测量”,在对应的刀补位上生成准确的刀补值。
(6)当前刀具对刀完毕好,换程序中需要用到的其他刀具,重复(1)到(5)过程,生成相应的刀补。
加工中心对刀对刀的实质是确定程序原点在机床坐标系中的位置。
对刀存在误差,对刀误差在某种程度内是允许产生的,也是不可避免的,但却可以尽量减少。
对刀的准确程度直接影响加工精度,因此,对刀方法一定要与零件加工精度要求相适应.当零件加工精度要求过高时可采用千分表。
对刀时一般以机床主轴轴线与断面的交点为刀位点,即假设基准刀的刀长为0,其他刀的长度就是其刀补值,故无论采用哪种刀具对刀,结果都是机床主轴轴线与端面的交点与对刀点重合,利用机床的坐标显示确定对刀点在机床坐标系中的位置,从而确定工件坐标系在机床坐标系内的位置.再利用对刀仪确定其他刀的长度,就解决了工件坐标系确定问题和多刀加工时的刀补确定问题。
2 。
对刀方法在数控加工中,对刀的基本方法有试切法、对刀仪对刀和自动对刀等.本文以数控铣床为例,介绍几种常用的对刀方法。
2.1试切对刀法这种方法简单方便,但会在工件表面留下切削痕迹,且对刀精度较低.如图1 所示,以对刀点在工件表面中心位置为例采用双边对刀方式。
图11)将工件通过夹具装在工作台上,装夹时,工件的四个侧面都应留出对刀的位置。
2)启动主轴中速旋转,快速移动工作台和主轴,让刀具快速移动到靠近工件左侧有一定安全距离的位置,然后降低速度移动至接近工件左侧。
3)靠近工件时改用微调操作( 一般用0。
01 mm) 来靠近,让刀具慢慢接近工件左侧,使刀具恰好接触到工件左侧表面( 观察,听切削声音、看切痕、看切屑,只要出现一种情况即表示刀具接触到工件),再回退0。
01 mm。
或者显示页面切换到相对坐标显示页面,将X坐标值清零.4) 沿z 正方向退刀,至工件表面以上,用同样方法接近工件右侧,记下此时相对坐标系中显示的坐标值,如- 340. 500。
5)据此可得工件坐标系原点在机床坐标系中坐标值为-340。
5/2 = —170。
25.然后向左移动机床到相对坐标显示为-170.25,此时主轴中心在工件坐标系X0的位置.6)在OFFSET页面,在相应的工件坐标页面G54—G59中输入X0,按软键测量,即可生成X的工件原点坐标值,此值与此时的机械坐标值一样。
7)同理可测得Y工件坐标系原点在机床坐标系中的坐标值。
Z向对刀.1)将刀具快速移至工件上方。
2) 启动主轴中速旋转,快速移动工作台和主轴,让刀具快速移动到靠近工件上表面有一定安全距离的位置,然后降低速度移动让刀具端面接近工件上表面。
3) 靠近工件时改用微调操作( 一般用0. 01 mm) 来靠近,让刀具端面慢慢接近工件表面( 注意刀具特别是立铣刀时最好在工件边缘下刀,刀的端面接触工件表面的面积小于半圆,尽量不要使立铣刀的中心孔在工件表面下刀) ,使刀具端面恰好碰到工件上表面,再将轴再抬高,记下此时机床坐标系中的z 值, - 140.400,则工件坐标系原点W 在机床坐标系中的坐标值为- 140.400。
c)将测得的x,y,z值输入到机床工件坐标系存储地址G5* 中(一般使用G54 ~ G59 代码存储对刀参数) .d) 进入面板输入模式( MDI) ,输入“G5* ",按启动键(在自动模式下),运行G5*使其生效。
e)检验对刀是否正确。
2. 2 塞尺、标准芯棒、块规对刀法此法与试切对刀法相似,只是对刀时主轴不转动,在刀具和工件之间加人塞尺(或标准芯棒、块规) ,以塞尺恰好不能自由抽动为准,注意计算坐标时这样应将塞尺的厚度减去。
因为主轴不需要转动切削,这种方法不会在工件表面留下痕迹,但对刀精度也不够高。
2。
3 采用寻边器、偏心棒和轴设定器等具对刀法操作步骤与采用试切对刀法相似,只是将刀具换成寻边器或偏心棒。
这是最常用的方法.效率高,能保证对刀精度。
使用寻边器时必须小心,让其钢球部位与工件轻微接触,同时被加工工件必须是良导体,定位基准面有较好的表面粗糙度.z 轴设定器一般用于转移(间接) 对刀法。
2. 4 转移( 间接)对刀法加工一个工件常常需要用到不止一把刀,第二把刀的长度与第一把刀的装刀长度不一样,需要重新对零,但有时零点被加工掉,无法直接找回零点,或不容许破坏已加工好的表面,还有某些刀具或场合不好直接对刀,这时候可采用间接找零的方法.a)对第一把刀.1)对第一把刀的时仍然先用试切法、塞尺法等。
记下此时工件原点的机床坐标z1。
第一把刀加工完后,停转主轴。
2)把对刀器放在机床工作台平整台面上( 如虎钳大表面) 。
3)在手轮模式下,利用手摇移动工作台至适合位置,向下移动主轴,用刀的底端压对刀器的顶部,表盘指针转动,最好在一圈以内,记下此时轴设定器的示数并将相对坐标轴清零。
4) 确抬高主轴,取下第一把刀。
b) 对第二把刀。
1)装上第二把刀。
2) 在手轮模式下,向下移动主轴,用刀的底端压对刀器的顶部,表盘指针转动,指针指向与第一把刀相同的示数A 位置。
3)记录此时轴相对坐标对应的数值z0(带正负号) .4) 抬高主轴,移走对刀器.5) 将原来第一把刀的G5* 里的z1坐标数据加上z0(带正负号),得到一个新的坐标。
6) 这个新的坐标就是要找的第二把刀对应的工件原点的机床实际坐标,将它输人到第二把刀的G5*工作坐标中,这样,就设定好第二把刀的零点。
其余刀与第二把刀的对刀方法相同.注:如果几把刀使用同一G5* ,则步骤5) ,6)改为把z0存进二号刀的长度参数里,使用第二把刀加工时调用刀长补正G43H02 即可。
2. 5 顶尖对刀法a) x,y 向对刀。
1)将工件通过夹具装在机床工作台上,换上顶尖。
2)快速移动工作台和主轴,让顶尖移动到近工件的上方,寻找工件画线的中心点,降低速度移动让顶尖接近它。
3)改用微调操作,让顶尖慢慢接近工件画线的中心点,直到顶尖尖点对准工件画线的中心点,记下此时机床坐标系中的x,y 坐标值。
b)卸下顶尖,装上铣刀,用其他对刀方法如试切法、塞尺法等得到z 轴坐标值.6 百分表(或千分表) 对刀法( 一般用于圆形工件的对刀)1)x,y 向对刀。
将百分表的安装杆装在刀柄上,或将百分表的磁性座吸在主轴套筒上,移动工作台使主轴中心线(即刀具中心) 大约移到工件中心,调节磁性座上伸缩杆的长度和角度,使百分表的触头接触工件的圆周面,(指针转动约0. 1 mm)用手慢慢转动主轴,使百分表的触头沿着工件的圆周面转动,观察百分表指针的便移情况,慢慢移动工作台的轴和轴,多次反复后,待转动主轴时百分表的指针基本在同一位置(表头转动一周时,其指针的跳动量在允许的对刀误差内,如0。
02 mm) ,这时可认为主轴的中心就是轴和轴的原点.2) 卸下百分表装上铣刀,用其他对刀方法如试切法、塞尺法等得到z 轴坐标值。
2.6专用对刀器对刀法传统对刀方法有安全性差(如塞尺对刀,硬碰硬刀尖易撞坏) 占用机时多(如试切需反复切量几次) ,人为带来的随机性误差大等缺点,已经适应不了数控加工的节奏,更不利于发挥数控机床的功能。