数控车床对刀仪的用途及原理(doc 8页)
数控机床“对刀”原理解析及应用
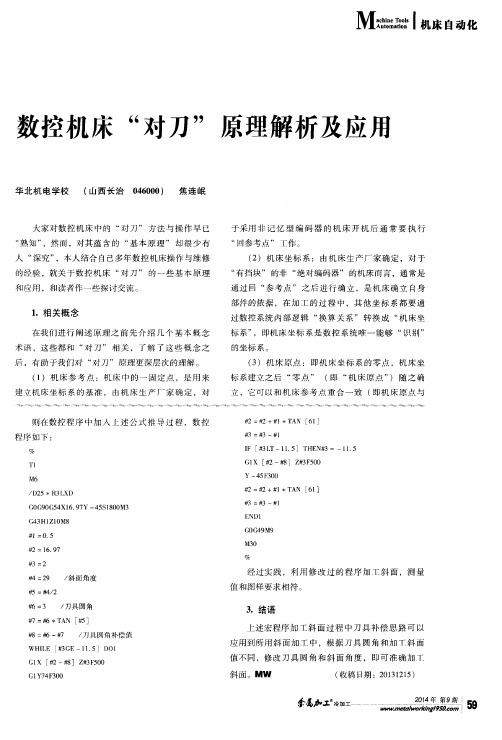
1 .相关概念
在我们 进行 阐述 原 理 之 前 先 介 绍 几 个 基 本 概 念
过数控 系 统 内部 逻 辑 “ 换 算 关 系 ”转 换 成 “ 机 床 坐 标系” ,即机床 坐 标 系 是 数控 系统 唯 一能 够 “ 识别”
的坐标 系 。
术语 ,这些 都 和 “ 对 刀 ” 相 关 ,了解 了这 些 概 念 之 后 ,有 助于 我们 对 “ 对 刀 ”原 理更 深层 次的理 解 。 ( 1 )机 床 参 考 点 :机 床 中 的一 固定 点 ,是 用 来 建立 机床 坐 标 系 的 基 准 , 由机 床 生 产 厂 家 确 定 ,对
% T I
M6
= 彝 2+ 样 I T A N[ 6 1 ] # 3 # 3 一 样 1
I F[ # 3 L T一1 1 . 5 ]T HE N # 3=一1 1 . 5 G1 X[ # 2一# 8 ]Z # 3 F 5 0 0
Y 一4 5 F 3 0 0
/ D 2 5 R 3 T X D
i n e T oo l s 上 vl A a c h
幻
I 机 床 自 动 化
数控机床 “ 对 刀" 原理解析及应用
华 北 机 电学 校 ( 山西 长 治 0 4 6 0 0 0 ) 焦 连 岷
大 家对 数控 机 床 中的 “ 对 刀 ” 方 法 与 操 作 早 已 “ 熟知” ,然 而 ,对 其蕴 含 的 “ 基 本原 理 ” 却 很 少 有 人 “ 深究” ,本人结 合 自己多 年数 控 机床 操作 与 维修 的经 验 ,就关 于 数 控机 床 “ 对 刀 ” 的一 些 基 本 原 理
联系 。
下面 以华 中世 纪 星数 控 车 床 为 例 ,通 过 不 同 的
数控车床对刀仪的用途及原理(doc 8页)

的,只是按结构的复杂程度和操作的自动化水平分为低、中、高三档型号。
第一种,HPRA (High Precision Removable Arm) 型:这是一种结构较简单、价位低的型号,其特点是对刀仪的臂和基座之间是可分离的,使用时通过插拔机构把对刀仪臂安装至对刀仪基座上(图1)图1:HPRA型对刀仪的系统构成同时电器信号亦连通并进入可工作状态;用完后可将对刀臂从基座中拔出,放到合适的地方以保护精密的对刀臂和对刀传感器部分不受灰尘、碰撞的损坏。
第二种,HPPA (High Precision Pulldown Arm) 型:这是一种较实用、中等价位的型号。
其特点是对刀仪的臂和基座之间是可旋转联接、一体化的。
使用时由操作者将对刀仪臂从保护套中摆动拉出(图2)图2:HPPA型对刀仪的系统构成不用时由操作者作把对刀仪臂再摆动推回保护套中。
这一种对刀仪与上一种型号相比的优点是不必把对刀仪臂频繁地插上、拔出,避免了频繁插拔产生的磨损对对刀精度的影响及电信号传递的可靠性。
因对刀仪摆回后传感器部分进入到保护套中,也不必担心其在工作过程中受到损坏。
第三种,HPMA (High Precision Motorised Arm) 型:这是雷尼绍公司该系列产品中的高档型。
其特点是对刀仪的臂和基座之间是通过扭矩电机来实现对刀臂的摆出和摆回(图3),除提高了自动化程度外,更重要的是可把对刀臂的摆出、摆回通过M代码编制到加工程序中,在加工循环过程中即可方便地实现刀具磨损值的自动测量、补偿和刀具破损的监测。
图3:HPMA型对刀仪的系统构成2、对刀仪都能干哪些工作?(1)、可以快速、高效、精确地在±X、±Z及Y轴五个方向上进行刀具偏置值的测量和补偿,有效消除采用人工对刀易产生的对刀误差和效率低下的问题。
因为不管是采用何种切削刀具(外圆、端面、螺纹、切槽、镗孔还是车削中心上的铣、钻削动力刀具)进行工件型面车削或铣削时,所有参与切削刀具的刀尖点或刀具轴心线,都必须通过调整或补偿使其精确地位于工件坐标系的同一理论点或轴心线上。
数控车床对刀的原理与方法

数控车床对刀的原理与方法数控车床的刀具对刀是确保机床工作精度的关键步骤之一、对刀准确度影响着工件的加工精度和质量。
数控车床的对刀一般采用刀具测量、感应式对刀、比较式对刀等方式。
下面将介绍数控车床对刀的原理和方法。
1.刀具测量:数控车床通常提供一个专门的测量装置,用来测量刀具的长度和半径。
通过刀具测量装置的读数,可以计算出刀具的几何参数,以便在数控系统中设置正确的刀具补偿值。
2.感应式对刀:数控车床使用感应式传感器,通过与刀具接触或靠近刀具来感应刀具的位置信息。
传感器可以测量到刀具的长度和半径,并将这些信息传递给数控系统。
3.比较式对刀:比较式对刀是通过测量工件上已加工的特征来确定刀具的位置。
例如,在数控车床上面加工一个规定尺寸的槽后,可以使用传感器测量槽的尺寸,然后根据预定的槽尺寸,调整刀具的位置。
根据数控车床对刀的原理,可以采用以下方法进行对刀:1.感应式对刀:数控车床上通常有一个专用的感应式对刀装置。
在对刀过程中,需要选取一把已知长度的刀具,并使用感应式传感器测量其长度。
将测量到的刀具长度输入数控系统,系统会自动计算并设置刀具长度补偿值。
然后,将正确长度的刀具安装到车刀刀架上,依次对各个刀具进行对刀。
2.刀具测量:刀具测量是比较常见的对刀方式。
使用专用的刀具测量设备可以测量刀具的长度和半径。
在对刀过程中,首先选取一把已知长度和半径的刀具,将其放入测量设备中测量。
然后,将测量到的数值输入数控系统,系统会自动计算出刀具的补偿值。
最后,将已校准好的刀具安装到车刀刀架上。
3.比较式对刀:在比较式对刀中,首先需要加工一个已知尺寸的特征,例如一条槽或一组孔。
然后,使用专用的测量仪器测量加工后的特征尺寸。
将测量到的尺寸和预定的尺寸进行比较,计算出相应的补偿值。
最后,根据计算结果调整刀具的位置。
除了上述方法外,还可以使用图形化的数控系统来辅助进行对刀。
通过在数控系统中显示工件轮廓的模拟图像,可以直观地观察刀具的位置与工件轮廓之间的关系,从而调整刀具的位置。
(完整word版)对刀仪使用说明(word文档良心出品)

自动对刀仪使用说明及调试说明书一、使用自动对刀仪进行刀具长度测量本自动对刀仪可以实现自动测量刀具长度并写入到指定的补偿号中。
进行刀具长度测量使用的指令为:G910H*B*M*——G910:调用9010号宏程序——H:刀具偏置号——B:假象刀具长度(略长于实际刀具长度)——M:设定测量之前是否转动一下主轴(0:转动/不设置:不转动)如指令为G910H11B200M0,则以假象刀具长度为200定位到对刀仪上方,测量之前刀具转动一下后停止,测量出的实际刀具长度将写入11号刀具偏置中。
执行指令机床的动作过程为:1.Z轴返回机床坐标零点2.X轴Y轴移动,对刀仪移动到刀具正下方。
3.Z轴向负方向移动到接近对刀仪的一安全位置。
4.Z轴慢速向负方向移动进行长度测量。
5.完成测量,Z轴上升5毫米。
6.刀具长度写入对应偏置中。
7.Z轴返回机床坐标零点。
刀具长度测量完成。
二、工件坐标系的建立完成所有刀具的长度测量后,需执行刀具长度补偿(G43 H*)后再进行建立工件坐标系。
注意:由于刀具长度测量后,在刀具偏置中的长度偏置都为正值,故执行G43H*指令时,Z轴会向正方向移动。
三、对刀仪调试修改6050号系统参数为910。
宏程序中相关宏变量意义见下表注:需要重新进行对刀仪的调试。
四、附件宏程序:O9010(AUTOMATIC TOOL OFFSET)(S.T X500.0 Y400.0 Z330.0+150+HC)(TOOL OFFSET MACRO PROGRAM FOR OFFSET MEMORY B,C V4.0) (G910 H** B*** M0 )(CHANGE PARAMETER NO.6050 DA TA 910)(START)#30=#4001#31=#4003IF[#900GE100.0]GOTO10#3000=110(SETTING DATA ERROR #900)N10IF[#901NE#0]GOTO20#3000=110(SETTING DATA ERROR #901)N20IF[#902NE#0]GOTO30#3000=110(SETTING DATA ERROR #902)N30IF[#903NE#0]GOTO40#3000=110(SETTING DATA ERROR #903)N40IF[#11NE#0]GOTO50#3000=110(DATA ERROR "H" NOT EXIST)N50IF[#905EQ0]GOTO60IF[#905EQ#0]GOTO60#24=#905GOTO70N60#24=5.0N70IF[#906EQ480.0]GOTO80IF[#906EQ580.0]GOTO80IF[#906EQ680.0]GOTO80IF[#906EQ780.0]GOTO80#3000=110(SETTING DATA ERROR #906)N80G91G28G00Z0#22=#5043#20=#5021#21=#5022G01X[#901-#20]Y[#902-#21]F500M19N1000(AUTOMA TIC TOOL MEASURING)IF[#2EQ#0]GOTO100IF[#2GT30]GOTO110#3000=110(DATA ERROR "B")N100#2=250.0N110IF[#7EQ#0]GOTO120G00X#7N120G00Z-[#906-#900-#2-25.0](*)IF[#13EQ#0]GOTO130S50M03G04X0.1M05M00N130M21G04 X1M22G31Z-[25.0+#24]F100(*)#25=#5063#26=#903-[ABS[#22-#25]]IF[[ABS[#906-#900-#2+#24-ABS[#22-#25]]]GT0.001]GOTO160 #3000=110(DATA ERROR B TOOL SHORT)N160Z5.0G90G10L10P#11R#26G91G28Z0IF[#7EQ#0]GOTO3000G00X-#7GOTO3000N3000G#30G#31M05M99。
数控车床对刀仪的用途及原理

数控车床对刀仪的用途及原理
数控车床对刀仪是一款智能化的仪器设备,用于协助数控车床进行刀具的刀具长度和半径补偿校准,以保证机床精度和生产质量。
数控车床对刀仪的使用可以使机床开机调试更加方便快捷,并减少刀具加工过程中出现的误差,提高加工精度和效率。
数控车床对刀仪的原理是利用光电传感器捕捉机械臂差动运动时光柱划过光电头产生的信号,通过转换电路,将信号转化成电脉冲,并经由计算机处理,最终得出刀具的相对位置和偏差。
通过对刀具的长度、半径进行补偿校准,实现机床切削精度的保证。
下面对数控车床对刀仪的用途和功能进一步阐述:
1. 刀具长度校准功能:在机床加工过程中,由于刀具磨损、安装、更换等原因,刀具长度会发生变化,而数控车床对刀仪可以准确测量刀具的长度并补偿校准,确保加工精度和生产质量。
2. 刀具半径校准功能:刀具的半径也会随着使用而产生变化,如果不进行及时的补偿校准就会导致工件的尺寸和形状偏差,甚至影响到加工质量。
数控车床对刀仪可以快速测量刀具半径,进行调整和校准。
3. 刀具补偿计算:在数控加工中,刀具补偿是制造精度
的关键之一,数控车床对刀仪可以通过对刀具长度和半径的测量,计算出补偿量,以提高加工精度。
4. 制造过程中可追溯性的记录:数控车床对刀仪不仅能
够进行刀具长度和半径的检测和补偿,还能够记录下该过程的参数和数据,进行存档,以便之后进行质量追溯。
综上所述,数控车床对刀仪是一款非常重要的数控加工辅助设备,可通过快速测量刀具长度和半径进行刀具的自动补偿,从而提高加工精度,降低生产成本,达到优化生产效益的目的。
数控车床对刀的原理及方法

数控车床对刀的原理及方法数控车床对刀是指在进行数控加工前,通过调整工具与工件之间的相对位置,使其达到最佳的加工状态,从而确保加工精度和质量。
在进行数控车床对刀时,需要掌握一定的原理和方法。
一、数控车床对刀的原理:数控车床对刀是以工具为基准,通过调整工具与工件之间的相对位置,使其达到预定的加工要求。
数控车床对刀的原理包括工具长度补偿和半径补偿。
工具长度补偿:数控车床对刀时,要考虑工具长度的影响。
在机床的编程中,以工件参考点统一参考工具长度,通过编程输入工具长度补偿值,使操作者无需考虑具体工具长度,直接参照工件参考点与加工长度编程。
半径补偿:数控车床对刀时,还要考虑工具半径的影响。
在机床的编程中,通过编程输入刀具半径补偿值,使操作者无需考虑具体工具半径,直接参照工件轮廓绘制加工轮廓。
二、数控车床对刀的方法:1. 机械对刀法:数控车床对刀时,一般先采用机械对刀法进行初步调整。
具体步骤如下:(1) 选择合适的切削工具,将其装夹到主轴上;(2) 将工件装夹在工作台上,固定好;(3) 调整工具的位置,使其与工件接触;(4) 缓慢移动工具,观察工具与工件的接触情况;(5) 调整对刀量,使工具的刀尖与工件表面轻微接触;(6) 用毛刷或布将切屑清除干净;(7) 检查工具与工件的接触情况,如需调整,继续进行机械对刀。
2. 触发器对刀法:在数控车床上,一般配备有触发器对刀装置。
该装置可以根据工具与工件的相对位置变化,给出相应的触发信号。
具体步骤如下:(1) 在数控系统中,选择相应的对刀程序和参数;(2) 将工具装夹到主轴上;(3) 将工件装夹在工作台上,固定好;(4) 运行对刀程序,使切削工具逐渐接近工件;(5) 当工具与工件发生接触时,触发器将给出触发信号,停止继续靠近;(6) 根据触发信号调整工具位置,以使其与工件的接触减小到最小值;(7) 检查工具与工件的接触情况,如果需要调整,可再次进行触发器对刀。
3. 光电对刀法:光电对刀法是一种非接触式的对刀方法,通过使用光电开关检测刀具的位置与工件的位置关系,以确定最佳的对刀位置。
数控车床对刀
第二步:试切工件端面,把端面在工件坐标系中Z的坐标值,保持Z轴方向不动, 刀具退出。进入形状补偿参数设定界面,将光标移到相应的位置,输入Z0,按 [测量]软键对应的刀具偏移量自动输入 ;
第三步:按照第一、二步对刀方法,对其余2把刀具进行对刀及设置
928TC数控系统 对刀步骤:
第一步:在手动方式下移动刀具在工件上切出一个小台阶。测量所切出的 台阶的直径,按 I 键,屏幕显示 刀偏 X ,输入测量出的直径值,按 Enter 键
3.ATC对刀 它是在机床上利用对刀显微镜自动地计算出车刀长度的简称,
对刀镜与支架不用时取下,需要对刀时才装到主轴箱上。对刀时, 用手动方式将刀尖移到对刀镜的视野内,再用手动脉冲发生器微量 移动使假象刀尖点与对刀镜内的中心点重合(如图所示),再将光 标移到相应刀具补偿号,按“自动计算(对刀)”按键,这把刀具 在两个方向的长度就被自动计算出来,并自动存入它的刀具补偿号 中。
(2) 对刀原理
1
2
X
Z刀补
ZZxx xx
3
φD
X刀补
Xxx
试切一段外圆
Z
FANUC数控系统 对刀步骤:
第一步:用所选刀具试切工件外圆,测量试切后的工件直径,比如记为α,
保持X轴方向不动,刀具退出。点击MDI键盘上
的键,进入形状补偿参
数设定界面,将光标移到与刀位号相对应的位置,输入Xα,按菜单软键[测 量],对应的刀具偏移量自动输入 ;
谢谢观看/欢迎下载
BY FAITH I MEAN A VISION OF GOOD ONE CHERISHES AND THE ENTHUSIASM THAT PUSHES ONE TO SEEK ITS FULFILLMENT REGARDLESS OF OBSTACLES. BY FAITH I BY FAITH
数控机床对刀的原理分析以及常用对刀方法
数控机床对刀的原理分析以及常用对刀方法进行数控加工时,数控程序所走的路径均是主轴上刀具的刀尖的运动轨迹。
刀具刀位点的运动轨迹自始至终需要在机床坐标系下进行精确控制,这是因为机床坐标系是机床唯一的基准。
编程人员在进行程序编制时不可能知道各种规格刀具的具体尺寸,为了简化编程,这就需要在进行程序编制时采用统一的基准,然后在使用刀具进行加工时,将刀具准确的长度和半径尺寸相对于该基准进行相应的偏置,从而得到刀具刀尖的准确位置。
所以对刀的目的就是确定刀具长度和半径值,从而在加工时确定刀尖在工件坐标系中的准确位置。
对刀仪演示视频(时长1分10秒,建议wifi下观看)一、对刀的原理和对刀中出现的问题1、刀位点刀位点是刀具上的一个基准点,刀位点相对运动的轨迹即加工路线,也称编程轨迹。
2、对刀和对刀点对刀是指操作员在启动数控程序之前,通过一定的测量手段,使刀位点与对刀点重合。
可以用对刀仪对刀,其操作比较简单,测量数据也比较准确。
还可以在数控机床上定位好夹具和安装好零件之后,使用量块、塞尺、千分表等,利用数控机床上的坐标对刀。
对于操作者来说,确定对刀点将是非常重要的,会直接影响零件的加工精度和程序控制的准确性。
在批生产过程中,更要考虑到对刀点的重复精度,操作者有必要加深对数控设备的了解,掌握更多的对刀技巧。
(1)对刀点的选择原则在机床上容易找正,在加工中便于检查,编程时便于计算,而且对刀误差小。
对刀点可以选择零件上的某个点(如零件的定位孔中心),也可以选择零件外的某一点(如夹具或机床上的某一点),但必须与零件的定位基准有一定的坐标关系。
提高对刀的准确性和精度,即便零件要求精度不高或者程序要求不严格,所选对刀部位的加工精度也应高于其他位置的加工精度。
选择接触面大、容易监测、加工过程稳定的部位作为对刀点。
对刀点尽可能与设计基准或工艺基准统一,避免由于尺寸换算导致对刀精度甚至加工精度降低,增加数控程序或零件数控加工的难度。
数控车床对刀的原理及方法
一【2 】.数控车床对刀的道理:对刀是数控加工中的重要操作和重要技巧.在必定前提下,对刀的精度可以决议零件的加工精度,同时,对刀效力还直接影响数控加工效力.仅仅知道对刀办法是不够的,还要知道数控体系的各类对刀设置方法,以及这些方法在加工程序中的挪用办法,同时要知道各类对刀方法的优缺陷.应用前提等.一般来说,数控加工零件的编程和加工是离开进行的.数控编程员依据零件的设计图纸,选定一个便利编程的工件坐标系,工件坐标系一般与零件的工艺基准或设计基准重合,在工件坐标系下进行零件加工程序的编制.对刀时,应使指刀位点与对刀点重合,所谓刀位点是指刀具的定位基准点,对于车刀来说,其刀位点是刀尖.对刀的目标是肯定对刀点, 在机床坐标系中的绝对坐标值,测量刀具的刀位误差值.对刀点找正的精确度直接影响加工精度.在现实加工工件时,应用一把刀具一般不能知足工件的加工请求,平日要应用多把刀具进行加工.在应用多把车刀加工时,在换刀地位不变的情形下,换刀后刀尖点的几何地位将消失差异,这就请求不同的刀具在不同的肇端地位开端加工时,都能保证程序正常运行.为懂得决这个问题,机床数控体系配备了刀具几何地位补偿的功效,应用刀具几何地位补偿功效,只要事先把每把刀相对于某一预先选定的基准刀的地位误差测量出来,输入到数控体系的刀具参数补正栏指定组号里,在加工程序中应用T 指令,即可在刀具轨迹中主动补偿刀具地位误差.刀具地位误差的测量同样也需经由过程对刀操作来实现.临盆厂家在制作数控车床,必须树立地位测量.掌握.显示的同一基准点,该基准点就是机床坐标系原点,也就是机床机械回零后所处的地位.数控机床所设置装备摆设的伺服电机有绝对编码器和相对编码器两种,绝对编码器的开机不用回零,体系断电跋文忆机床地位,机床零点由参数设定.相对编码器的开机必须回零,机床零点由机床地位传感器肯定.编程员按工件坐标系中的坐标数据编制的刀具运行轨迹程序,必须在机床坐标系中加工,因为机床原点与工件原点消失X向偏移距离和Z向偏移距离,使得现实的刀尖地位与程序指令的地位有同样的偏移距离,是以,须将该距离测量出来并设置进数控体系,使体系据此调剂刀具的活动轨迹,才能加工出相符零件图纸的工件.这个进程就是对刀,所谓对刀其本质就是测量工件原点与机床原点之间的偏移距离,设置工件原点在以刀尖为参照的机床坐标系里的坐标.二.对刀办法对刀的办法有许多种,按对刀的精度可分为粗略对刀和精确对刀;按是否采用对刀仪可分为手动对刀和主动对刀;按是否采用基准刀,又可分为绝对对刀和相对对刀等.但无论采用哪种对刀方法,都离不开试切对刀,试切对刀是最根本的对刀办法.1.数控车床试车对刀办法图1(1)如图1,夹持工件,换须要对的刀具到刀架当前位..图2(2)如图2,在手动操作方法下,启动主轴,用当前刀具在加工余量规模内试切工件外圆,车的长度必须可以或许便利测量,X轴不要移动,沿Z的正偏向退出来,停主轴,测量所车的外圆尺寸Xa,如图3.图3(3)按“OFS/SET”键如图4,按刀偏如图5,将光标移到与刀具号相对应的地位后,输入“Xa”,如图6,按操作面板上的“刀具测量”,再按显示器下面的软键“测量”,在对应的刀补位上生成对应刀补值.图4留意:刀具补偿包括“磨损”和“外形”补偿两部分,刀偏分外形和磨损,刀尖的地位放在外形里,尺寸的调剂和刀具的磨耗放在磨损里.两者之和组成车刀偏移量补偿参数.如图5显示.图5图6(4)如图7在手动方法下,再用该把刀去平工件端面,平完端面后,沿X正偏向退出来,Z偏向不动,停主轴,测量工件原点到工件端面的距离Lz.图7(5)同(3)一样.按“OFS/SET”键,进入“外形”补偿设定界面,将光标移到与刀位号相对应的地位后,输入“Lz”,按操作面板上的“刀具测量”,再按显示器下面的软键“测量”,在对应的刀补位上生成精确的刀补值.(6)当前刀具对刀完毕好,换程序中须要用到的其他刀具,反复(1)到(5)进程,生成响应的刀补.加工中间对刀对刀的本质是肯定程序原点在机床坐标系中的地位.对刀消失误差,对刀误差在某种程度内是许可产生的,也是不可避免的,但却可以尽量削减.对刀的精确程度直接影响加工精度,是以,对刀办法必定要与零件加工精度请求相顺应.当零件加工精度请求过高时可采用千分表.对刀时一般以机床主轴轴线与断面的交点为刀位点,即假设基准刀的刀长为0,其他刀的长度就是其刀补值,故无论采用哪种刀具对刀,成果都是机床主轴轴线与端面的交点与对刀点重合,应用机床的坐标显示肯定对刀点在机床坐标系中的地位,从而肯定工件坐标系在机床坐标系内的地位.再应用对刀仪肯定其他刀的长度,就解决了工件坐标系肯定问题和多刀加工时的刀补肯定问题.2 .对刀办法在数控加工中,对刀的根本办法有试切法.对刀仪对刀和主动对刀等.本文以数控铣床为例,介绍几种常用的对刀办法.2. 1 试切对刀法这种办法简略便利,但会在工件表面留下切削陈迹,且对刀精度较低.如图1 所示,以对刀点在工件表面中间地位为例采用双边对刀方法.图11) 将工件经由过程夹具装在工作台上,装夹时,工件的四个侧面都应留出对刀的地位.2) 启动主轴中速扭转,快速移动工作台和主轴,让刀具快速移动到接近工件左侧有必定安全距离的地位,然后下降速度移动至接近工件左侧.3) 接近工件时改用微调操作( 一般用0. 01 mm) 来接近,让刀具慢慢接近工件左侧,使刀具正好接触到工件左侧表面( 不雅察,听切削声音.看切痕.看切屑,只要消失一种情形即表示刀具接触到工件) ,再回退0. 01 mm.或者显示页面切换到相对坐标显示页面,将X坐标值清零.4) 沿z 正偏向退刀,至工件表面以上,用同样办法接近工件右侧,记下此时相对坐标系中显示的坐标值,如- 340. 500.5) 据此可得工件坐标系原点在机床坐标系中坐标值为-340.5/2 = -170.25.然后向左移念头床到相对坐标显示为-170.25,此时主轴中间在工件坐标系X0的地位.6)在OFFSET页面,在响应的工件坐标页面G54-G59中输入X0,按软键测量,即可生成X的工件原点坐标值,此值与此时的机械坐标值一样. 7)同理可测得Y工件坐标系原点在机床坐标系中的坐标值.Z向对刀.1) 将刀具快速移至工件上方.2) 启动主轴中速扭转,快速移动工作台和主轴,让刀具快速移动到接近工件上表面有必定安全距离的地位,然后下降速度移动让刀具端面接近工件上表面.3) 接近工件时改用微调操作( 一般用0. 01 mm) 来接近,让刀具端面慢慢接近工件表面( 留意刀具特殊是立铣刀时最好在工件边缘下刀,刀的端面接触工件表面的面积小于半圆,尽量不要使立铣刀的中间孔在工件表面下刀) ,使刀具端面正好碰着工件上表面,再将轴再举高,记下此机会床坐标系中的z 值, - 140. 400,则工件坐标系原点W 在机床坐标系中的坐标值为- 140. 400.c) 将测得的x,y,z 值输入到机床工件坐标系存储地址G5* 中( 一般应用G54 ~ G59 代码存储对刀参数) .d) 进入面板输入模式( MDI) ,输入“G5* ”,按启动键( 在主动模式下) ,运行G5* 使其生效.e) 磨练对刀是否精确.2. 2 塞尺.标准芯棒.块规对刀法此法与试切对刀法类似,只是对刀时主轴不迁移转变,在刀具和工件之间加人塞尺( 或标准芯棒.块规) ,以塞尺正好不能自由抽动为准,留意盘算坐标时如许应将塞尺的厚度减去.因为主轴不须要迁移转变切削,这种办法不会在工件表面留下陈迹,但对刀精度也不够高. 2. 3 采用寻边器.偏幸棒和轴设定器等具对刀法操作步骤与采用试切对刀法类似,只是将刀具换成寻边器或偏幸棒. 这是最常用的办法.效力高,能保证对刀精度.应用寻边器时必须当心,让其钢球部位与工件稍微接触,同时被加工工件必须是良导体,定位基准面有较好的表面光滑度.z 轴设定器一般用于转移( 间接) 对刀法.2. 4 转移( 间接) 对刀法加工一个工件常常须要用到不止一把刀,第二把刀的长度与第一把刀的装刀长度不一样,须要从新对零,但有时零点被加工失落,无法直接找回零点,或不许可损坏已加工好的表面,还有某些刀具或场合不好直接对刀,这时刻可采用间接找零的办法.a) 对第一把刀.1) 对第一把刀的时仍然先用试切法.塞尺法等.记下此时工件原点的机床坐标z1.第一把刀加工完后,停转主轴.2) 把对刀器放在机床工作台平整台面上( 如虎钳大表面) .3) 在手轮模式下,应用手摇移动工作台至合适位置,向下移动主轴,用刀的底端压对刀器的顶部,表盘指针迁移转变,最好在一圈以内,记下此时轴设定器的示数并将相对坐标轴清零.4) 确举高主轴,取下第一把刀.b) 对第二把刀.1) 装上第二把刀.2) 在手轮模式下,向下移动主轴,用刀的底端压对刀器的顶部,表盘指针迁移转变,指针指向与第一把刀雷同的示数A 地位.3) 记载此时轴相对坐标对应的数值z0( 带正负号) .4) 举高主轴,移走对刀器.5) 将本来第一把刀的G5* 里的z1坐标数据加上z0( 带正负号) ,得到一个新的坐标.6) 这个新的坐标就是要找的第二把刀对应的工件原点的机床现实坐标,将它输人到第二把刀的G5* 工作坐标中,如许,就设定好第二把刀的零点.其余刀与第二把刀的对刀办法雷同.注: 假如几把刀应用同一G5* ,则步骤5) ,6) 改为把z0存进二号刀的长度参数里,应用第二把刀加工时挪用刀长补正G43H02 即可.2. 5 顶尖对刀法a) x,y 向对刀.1) 将工件经由过程夹具装在机床工作台上,换上顶尖.2) 快速移动工作台和主轴,让顶尖移动到近工件的上方,查找工件画线的中间点,下降速度移动让顶尖接近它.3) 改用微调操作,让顶尖慢慢接近工件画线的中间点,直到顶尖尖点瞄准工件画线的中间点,记下此机会床坐标系中的x,y 坐标值.b) 卸下顶尖,装上铣刀,用其他对刀办法如试切法.塞尺法等得到z 轴坐标值.6 百分表( 或千分表) 对刀法( 一般用于圆形工件的对刀)1) x,y 向对刀.将百分表的安装杆装在刀柄上,或将百分表的磁性座吸在主轴套筒上,移动工作台使主轴中间线( 即刀具中间) 大约移到工件中间,调节磁性座上伸缩杆的长度和角度,使百分表的触头接触工件的圆周面,( 指针迁移转变约0. 1 mm) 用手慢慢迁移转变主轴,使百分表的触头沿着工件的圆周面迁移转变,不雅察百分表指针的便移情形,慢慢移动工作台的轴和轴,多次反复后,待迁移转变主轴时百分表的指针根本在同一地位( 表头迁移转变一周时,其指针的跳动量在许可的对刀误差内,如0. 02 mm) ,这时可以为主轴的中间就是轴和轴的原点.2) 卸下百分表装上铣刀,用其他对刀办法如试切法.塞尺法等得到z 轴坐标值.2. 6 专用对刀器对刀法传统对刀办法有安全性差( 如塞尺对刀,硬碰硬刀尖易撞坏) 占用机时多( 如试切需反复切量几回) ,工资带来的随机性误差大等缺陷,已经顺应不了数控加工的节拍,更不利于施展数控机床的功效.用专用对刀器对刀有对刀精度高.效力高.安全性好等长处,把繁琐的靠经验保证的对刀工作简略化了,保证了数控机床的高效高精度特色的施展,已成为数控加工机上解决刀具对刀不可或缺的一种专用对象.。
数控机床对刀仪的使用说明
数控机床对刀仪的使用说明为了有效提高数控机床的使用效率和精度,对刀仪作为重要的辅助工具被广泛应用。
数控机床对刀仪能够实现精确定位和调整刀具位置,本文将对其使用进行详细说明。
一、对刀仪的定义和分类数控机床对刀仪是一种可测量刀具长度、直径以及中心线位置的装置。
根据其结构和功能,对刀仪可分为机械对刀仪和光电对刀仪两种类型。
1. 机械对刀仪机械对刀仪采用机械测量原理,通过测量机械感应器的位移或/和力值来确定刀具位置。
常见的机械对刀仪有机械触针式对刀仪、机械共振对刀仪等。
2. 光电对刀仪光电对刀仪利用光电测量原理,通过光电传感器探测刀具的位置信息,并将其转化为电信号进行处理。
光电对刀仪具有无接触、高精度等优点,广泛应用于数控机床中。
二、对刀仪的操作流程使用数控机床对刀仪需要按照以下步骤进行操作:1. 准备工作首先,确保对刀仪与数控机床正确连接,并确认连接稳固可靠。
其次,检查刀具是否安装正确,刀具应牢固固定在刀柄上,无松动现象。
2. 设置测量模式根据实际需要,选择对刀仪的测量模式。
常见的测量模式有刀长度测量、刀具半径测量和刀具边角测量等,根据不同的模式选择相应功能。
3. 启动机床和对刀仪打开数控机床和对刀仪的电源开关,并等待系统启动完成。
确保数控机床和对刀仪的通信正常。
4. 定位刀具和刀柄使用机械手或手动操作,将刀具和刀柄准确安装到数控机床的刀库中。
确保刀具和刀柄的编号与程序中一致。
5. 进行对刀操作按照数控机床的操作界面提示,选择对刀功能,并按要求操作。
对刀过程中,对刀仪将会自动测量刀具的位置信息,并将测量结果传输给数控机床进行相应调整。
6. 验证刀具位置对刀完成后,使用测量工具(如游标卡尺或三坐标测量机)验证刀具位置的准确性。
如果发现误差较大,应重新进行对刀操作。
三、对刀仪的注意事项在使用数控机床对刀仪时,需要注意以下事项,以确保操作的准确性和安全性:1. 定期校准对刀仪作为精密测量设备,需要定期进行校准,以保证测量的准确性。
- 1、下载文档前请自行甄别文档内容的完整性,平台不提供额外的编辑、内容补充、找答案等附加服务。
- 2、"仅部分预览"的文档,不可在线预览部分如存在完整性等问题,可反馈申请退款(可完整预览的文档不适用该条件!)。
- 3、如文档侵犯您的权益,请联系客服反馈,我们会尽快为您处理(人工客服工作时间:9:00-18:30)。
数控车床对刀仪的用途及原理(doc 8页)
英国“雷尼绍”(RENISHAW)车床对刀仪的用途及原理
济南一机床集团有限公司李军
摘要:文中着重介绍了英国“雷尼绍”公司数控车床用对刀仪的种类、用途以及简要的工作原理,同时也简要介绍了在数控车床上采用对刀仪对提高加工精度及加工效率的意义。
关键词:对刀仪种类及用途工作原理
作为机械加工业中用量最大的数控车床,近些年来随国内经济的高速发展已迅速得到普及。
今天,一个企业内拥有几十台甚至上百台数控车床早已不是什么稀罕事了。
但众所周知,使用数控车床的目地是提高工件的加工质量和效率。
可是使用过数控车床的人都知道,在一个工件的加工过程中,工件的装卸、刀具的调整等辅助时间占用了加工周期中相当大的比例,其中的刀具调整更是既麻烦、又费力。
统计资料证明,实现一个工件的加工,纯机动时间大约要占总时间的55%,装、夹和对刀等辅助时间却占到45%,这实在不是一个小数。
老话讲磨刀不误砍柴工,但在现代社会中,时间就是金钱,效率就是生命。
要多砍柴就必须向磨刀要效益,对时间进行分秒必争。
那么,在提高对刀效率方面我们还有什么好办法吗?实践证明,通过在数控车床上增设对刀仪装置即是一种向“磨刀”要时间的好方法。
以下,结合英国雷尼绍公司的对刀仪装置,谈谈它在构成、用途及简要工作原理等方面的知识:
1、雷尼绍公司有哪几种对刀仪装置?
目前在雷尼绍车床对刀仪系列产品中共有三种型号,其对刀的原理是一样
图2:HPPA型对刀仪的系统构成
不用时由操作者作把对刀仪臂再摆动推回保护套中。
这一种对刀仪与上一种型号相比的优点是不必把对刀仪臂频繁地插上、拔出,避免了频繁插拔产生的磨损对对刀精度的影响及电信号传递的可靠性。
因对刀仪摆回后传感器部分进入到保护套中,也不必担心其在工作过程中受到损坏。
第三种,HPMA (High Precision Motorised Arm) 型:
这是雷尼绍公司该系列产品中的高档型。
其特点是对刀仪的臂和基座之间是通过扭矩电机来实现对刀臂的摆出和摆回(图3),除提高了自动化程度外,更重要的是可把对刀臂的摆出、摆回通过M代码编制到加工程序中,在加工循环过程中即可方便地实现刀具磨损值的自动测量、补偿和刀具破损的监测。
图3:HPMA型对刀仪
的系统构成
2、对刀仪都能干哪些工作?
(1)、可以快速、高效、精确地在±X、±Z及Y轴五个方向上进行刀具偏置值的测量和补偿,有效消除采用人工对刀易产生的对刀误差和效率低下的问题。
因为不管是采用何种切削刀具(外圆、端面、螺纹、切槽、镗孔还是车削中心上的铣、钻削动力刀具)进行工件型面车削或铣削时,所有参与切削刀具的刀尖点或刀具轴心线,都必须通过调整或补偿使其精确地位于工件坐标系的同一理论点或轴心线上。
对动力型回转刀具,除要测量并补偿刀具长度方向上的偏置值外,同时还要测量和补偿刀具直径方向上的偏置值(刀具以轴心线分界的两个半径的偏置值)。
否则机床也无法加工出尺寸正确的工件来。
安装、调整、或更换新刀具后,要使刀架上每把刀具的刀尖点或刀具的轴心线都准确地与机床坐标系零点(对数控车床而言,X轴机床坐标系的零点与主轴中心线重合;Z轴在主轴头前端发蓝的立面上)保持一个精准的固定值是不可能的,这是因刀具安装、调整、磨损后必然会产生的误差造成,或是更换刀具后新刀具与旧刀具位置之间所产生的安装偏差值造成。
所谓刀具偏置值就是指的这种误差值(图4)。
图4:四个坐标方向上的刀具的偏置值
在没有安装对刀仪的机床上,每把刀具的偏置值是通过对每把刀具都进行仔细的试切削,然后通过对试切削后的工件尺寸进行测量、计算、补偿(手工对刀)才可完成,肯定费时费力,稍不小心还会报废工件。
当更换刀具后,这
项工作还要重新进行。
因而对刀实际上是占用机床辅助时间最长的工作内容之一。
在使用了对刀仪的机床上,因对刀后能够自动设置好刀具对工件坐标系的偏置值,从而自动建立起工件坐标系,在这种情况下加工程序中就无需再用“G50指令”来建立工件坐标系了。
(2)、可以对加工过程中的刀具磨损、破损进行自动监测、补偿和报警。
刀具在切削过程中会产生磨损,当这种磨损值达到一定程度后就应及时补偿,否则会影响工件尺寸的加工稳定性。
在没有安装对刀仪的机床上完成磨损值的补偿是很麻烦的,需要频频的停下机床对工件的尺寸进行手工测量、还要将得到的磨损值人工敲到系统中去修改刀补参数。
而当安装了对刀仪后,解决这个问题就方便简单的多了,特别是机床安装的是HPPA型或HPMA型后则更为方便。
前者,只要根据刀具的磨损规律,干完一定数量的工件后停下机床,用对刀仪再进行一遍对刀的过程即可;后者,只要在程序中人为设定完成多少个加工循环后执行一次自动对刀,既可完成刀具的偏置补偿工作。
对于刀具破损报警或对刀具磨损到一定程度后进行强制更换,其原理也是一样,根据刀具允许的磨损量,人为设定一个“门槛值”,一旦对刀仪监测到的误差超过门槛值,即可认为刀具已破损或超过了允许的磨损值,则机床自动报警停机,然后强制进行刀具的更换。
(3)、当机床因热变型造成滚珠丝杠伸长后,也可对由此而引起的刀具偏置值变动量进行补偿,以确保工件尺寸的稳定。
机床在工作循环过程中,由于机床直线运动产生的摩擦是以热量的形式体现出来,另还有一个不可忽视的热源是切削下来的铁屑向机床的热传导。
这些因素的客观存在都会导致机床的变形特别是丝杠的热伸长,反映出来的现象是刀尖的位置要发生变化,其结果是工件的尺寸精度一定会随这种热变形同步变化。
如果在机床上安装了对刀仪装置,上述问题也可迎刃而解,无非是把这种由热变形产生的刀尖位置变化视为刀具的磨损值罢了,通过用对刀仪来测量及补偿这种新产生的刀具偏置值即可解决。
3、对刀仪的简要工作原理
雷尼绍对刀仪的核心构件是由一个高精度的开关(传感器)、一个高硬度高耐磨性的硬质合金四面体(对刀探针)和一个信号传输接口器组成(其它构件
略)。
四面体探针是用于与刀具进行接触并通过安装在其下的绕性支撑杆把力向高精度开关传递;开关所发出的通、断信号通过信号传输接口器传输到数控系统中去进行刀具方向识别、运算、补偿、存取等。
不管是刀具偏置值还是磨损值还是热变形引起的刀尖位置变动值,实质上都可归结为刀具初始偏置值与刀具经工作一段时间后的实际偏置值之间的变动量。
数控机床的工作原理决定,当机床返回各自运动轴的机械参考点后,建立起来的是机床坐标系。
该参考点一旦建立,相对机床零点而言,在机床坐标系数轴上的各运动方向就有了数值上的实际意义。
一般情况下此时只要在机床坐标系的基础上通过编程,建立起G50工件坐标系就可以进行实际加工了(仅使用机床坐标系十分不便于加工程序的编制)。
但仅此对于安装了对刀仪的机床还不行,还必须要通过参数设定的方法来精确确定对刀仪传感器距机床坐标系零点的各方向实际坐标固定值才能满足使用(图5),否则数控系统将无法在机床坐标系和对刀仪固定坐标之间进行相互位置的数据换算。
图5:对刀仪的坐标系
当我们在机床上建立起来了“机床坐标系”和“对刀仪固定坐标”后(不同规格的对刀仪应设置不同的固定坐标值),有以下对刀仪的简要工作原理描
述:
(1)、机床各直线运动轴返回各自的机械参考点之后,机床坐标系和对刀仪固定坐标之间的相对位置关系就建立起了具体的数值。
(2)不论是使用自动编程控制还是手动控制方式操作多刀仪,当移动所选定的某个轴的刀具并使刀尖(或动力回转刀具的外径)触动、靠向对刀仪上四面探针的对应平面并探针通过绕性支撑杆摆动触发了高精度开关传感器后,开关会立即通知系统锁定该进给轴的运动。
因为数控系统是把这一信号作为高级信号来处理,所以动作的控制会极为迅速、准确。
(3)由于数控机床直线进给轴上均安装有进行位置环反馈的脉冲编码器,数控系统中也有记忆该进给轴实际位置的计数器,此时系统只要读出该轴停止的准确位置,通过机床、对刀仪两者之间相对关系的自动换算,即可确定该轴刀具刀尖(或直径)的初始刀具偏置值了。
换一个角度说,如把它放到机床坐标系中来衡量,即相当于确定了机床参考点距机床坐标系零点的距离与该刀具测量点距机床坐标系零点的距离及两者之间的实际偏差值。
(4)不论是工件切削后产生的刀具磨损、还是滚珠丝杠热伸长后出现的刀尖变动量,只要再进行一次对刀的作业,数控系统就会自动把测得的该把刀具的新刀具偏置量与该把刀具的初始刀具偏置量进行比较计算,并将需要进行补偿的δ误差值自动补偿进刀补存储区中去。
当然,如果换了新的一把刀具,再对其重新进行对刀,所获得的偏置值就应该是该刀具新的初始刀具偏置值了。
附:雷尼绍对刀仪能达到怎样的对刀精度?
根据实际应用情况及有关资料证明,雷尼绍对刀仪能达到以下精度:
15"以下卡盘(含15")的中小规格数控车床,使用雷尼绍对刀仪能达到的对刀重复精度为:±5um 。
18"以上卡盘(含18")的大规格数控车床,使用雷尼绍对刀仪能达到的对刀重复精度为:±8um 。
在以上篇幅中,只是将雷尼绍对刀仪装置的构成、用途及简单的工作原理进行了简要介绍。
受篇幅所限,有关对刀仪安装后的调试、参数设置及使用方法、注意事项等,不在此赘述。
(完)。