钢铁工业余热能量及回收
我国工业余热回收利用技术综述
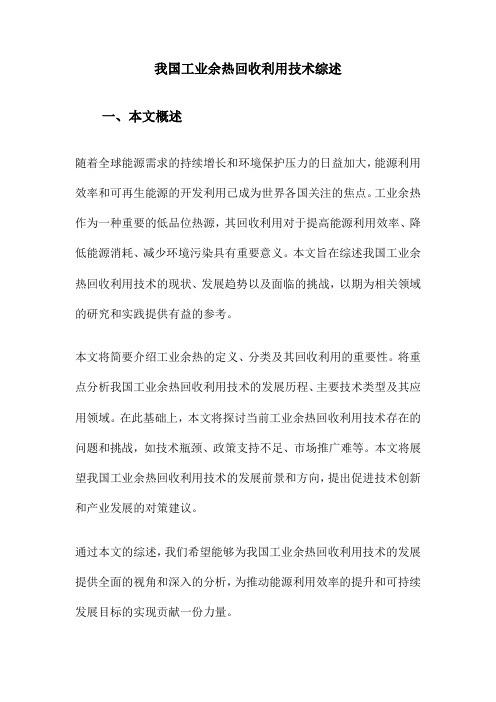
我国工业余热回收利用技术综述一、本文概述随着全球能源需求的持续增长和环境保护压力的日益加大,能源利用效率和可再生能源的开发利用已成为世界各国关注的焦点。
工业余热作为一种重要的低品位热源,其回收利用对于提高能源利用效率、降低能源消耗、减少环境污染具有重要意义。
本文旨在综述我国工业余热回收利用技术的现状、发展趋势以及面临的挑战,以期为相关领域的研究和实践提供有益的参考。
本文将简要介绍工业余热的定义、分类及其回收利用的重要性。
将重点分析我国工业余热回收利用技术的发展历程、主要技术类型及其应用领域。
在此基础上,本文将探讨当前工业余热回收利用技术存在的问题和挑战,如技术瓶颈、政策支持不足、市场推广难等。
本文将展望我国工业余热回收利用技术的发展前景和方向,提出促进技术创新和产业发展的对策建议。
通过本文的综述,我们希望能够为我国工业余热回收利用技术的发展提供全面的视角和深入的分析,为推动能源利用效率的提升和可持续发展目标的实现贡献一份力量。
二、工业余热回收利用技术分类热电联产技术:这是最常见的余热回收利用技术,主要利用工业过程中产生的废气、废水等余热,通过热力发电系统产生电能。
热电联产技术不仅可以提高能源利用效率,还可以减少环境污染。
热泵技术:热泵技术是一种利用少量电能驱动,通过热交换器将低温热源(如工业废水、废气等)中的热能转移到高温热源(如供暖系统、热水系统等)中的技术。
热泵技术具有高效、环保、节能等优点,被广泛应用于各种工业余热回收利用场景。
热管技术:热管是一种高效的传热元件,通过热管内部的工质循环,可以将热量从一个地方传递到另一个地方。
在工业余热回收利用中,热管技术常被用于将高温热源中的热量传递到低温热源中,以实现能源的梯级利用。
余热锅炉技术:余热锅炉是一种利用工业余热产生蒸汽的装置,广泛应用于钢铁、有色、造纸、化工等工业领域。
通过余热锅炉,可以将工业过程中产生的废气、废水等余热转化为蒸汽,供生产和生活使用。
余热回收系统工作原理

余热回收系统工作原理一、引言余热回收系统是一种利用工业生产过程中产生的余热进行能量回收的技术。
该系统可以有效地提高能源利用率,减少能源浪费,同时也符合环保要求。
本文将从工作原理的角度来介绍余热回收系统。
二、工作原理余热回收系统的工作原理可以分为以下几个步骤:1. 热源采集在工业生产过程中,往往会产生大量的热能。
余热回收系统首先需要识别和采集这些热源。
热源可以来自各种设备,例如锅炉、热风炉、高温烟气等。
系统需要通过传感器等装置来检测和量化这些热源的热能。
2. 热能转移一旦热源被采集到,余热回收系统需要将这些热能转移到需要热能的地方。
这一步通常通过热交换器来实现。
热交换器是一个设备,能够实现两种介质之间的热能传递,而不使它们混合在一起。
热交换器通常由一系列的传热管束组成,热能通过这些管束的壁面传递。
3. 热能利用经过热交换器传递后,热能被转移到需要热能的地方。
这个地方可以是生产过程中的其他设备,例如加热炉、干燥机等。
利用热能的方式多种多样,可以是直接加热,也可以是通过蒸汽、热水等中介介质传递热能。
不同的工业生产过程有不同的热能利用方式。
4. 热能排放经过热能转移和利用后,热能的温度会降低。
如果这些低温热能不能再被利用,那么就需要将其排放。
热能排放可以通过多种方式进行,例如通过冷却器将热能转移到环境中,或者通过烟囱排放烟气。
在排放过程中,需要注意对环境的影响,确保排放符合环保要求。
5. 控制与监测为了保证余热回收系统的正常运行,需要进行系统的控制与监测。
控制可以通过自动控制系统来实现,根据实时的热能采集情况和热能需求情况进行调节。
监测则可以通过传感器等装置来实现,对热能采集、转移、利用和排放进行实时监测,以保证系统的稳定运行。
三、应用案例余热回收系统的应用案例非常广泛。
例如,在电厂中,通过余热回收系统可以将烟气中的高温热能转移到锅炉的进水中,提高发电效率。
在化工厂中,通过余热回收系统可以将炉排烟气中的热能转移到蒸发器中,提高蒸发效率。
钢铁工业余热回收的主要环节介绍
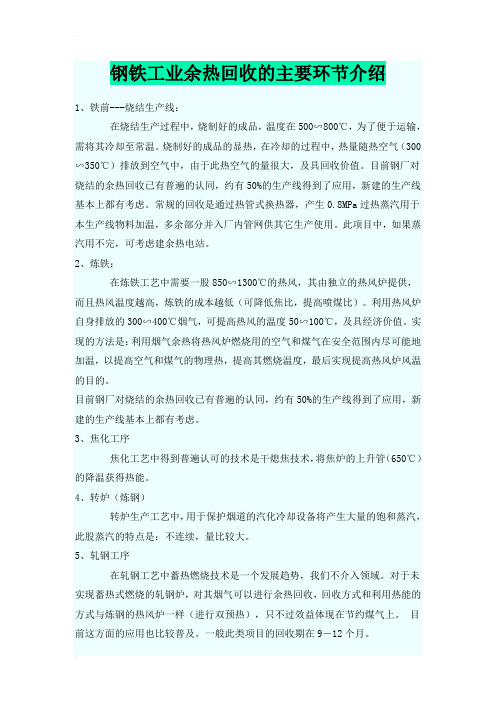
钢铁工业余热回收的主要环节介绍1、铁前---烧结生产线:在烧结生产过程中,烧制好的成品,温度在500∽800℃,为了便于运输,需将其冷却至常温。
烧制好的成品的显热,在冷却的过程中,热量随热空气(300∽350℃)排放到空气中,由于此热空气的量很大,及具回收价值。
目前钢厂对烧结的余热回收已有普遍的认同,约有50%的生产线得到了应用,新建的生产线基本上都有考虑。
常规的回收是通过热管式换热器,产生0.8MPa过热蒸汽用于本生产线物料加温,多余部分并入厂内管网供其它生产使用。
此项目中,如果蒸汽用不完,可考虑建余热电站。
2、炼铁:在炼铁工艺中需要一股850∽1300℃的热风,其由独立的热风炉提供,而且热风温度越高,炼铁的成本越低(可降低焦比,提高喷煤比)。
利用热风炉自身排放的300∽400℃烟气,可提高热风的温度50∽100℃,及具经济价值。
实现的方法是:利用烟气余热将热风炉燃烧用的空气和煤气在安全范围内尽可能地加温,以提高空气和煤气的物理热,提高其燃烧温度,最后实现提高热风炉风温的目的。
目前钢厂对烧结的余热回收已有普遍的认同,约有50%的生产线得到了应用,新建的生产线基本上都有考虑。
3、焦化工序焦化工艺中得到普遍认可的技术是干熄焦技术,将焦炉的上升管(650℃)的降温获得热能。
4、转炉(炼钢)转炉生产工艺中,用于保护烟道的汽化冷却设备将产生大量的饱和蒸汽,此股蒸汽的特点是:不连续,量比较大。
5、轧钢工序在轧钢工艺中蓄热燃烧技术是一个发展趋势,我们不介入领域。
对于未实现蓄热式燃烧的轧钢炉,对其烟气可以进行余热回收,回收方式和利用热能的方式与炼钢的热风炉一样(进行双预热),只不过效益体现在节约煤气上。
目前这方面的应用也比较普及。
一般此类项目的回收期在9-12个月。
1、铁前---烧结生产线:在烧结生产过程中,烧制好的成品,温度在500∽800℃,为了便于运输,需将其冷却至常温。
烧制好的成品的显热,在冷却的过程中,热量随热空气(300∽350℃)排放到空气中,由于此热空气的量很大,及具回收价值。
余热回收的应用案例有哪些?
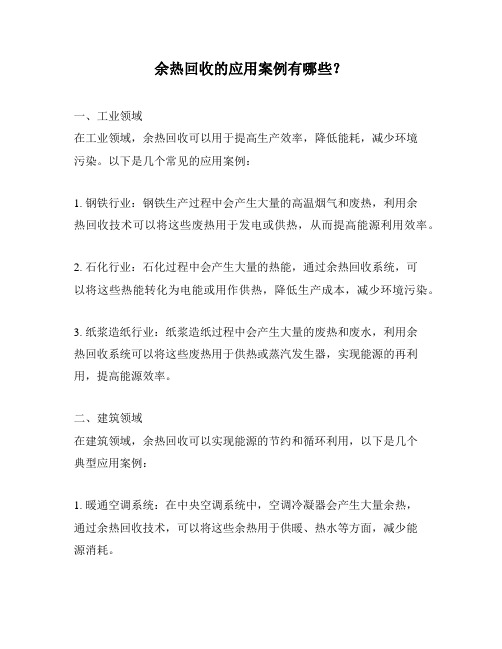
余热回收的应用案例有哪些?一、工业领域在工业领域,余热回收可以用于提高生产效率,降低能耗,减少环境污染。
以下是几个常见的应用案例:1. 钢铁行业:钢铁生产过程中会产生大量的高温烟气和废热,利用余热回收技术可以将这些废热用于发电或供热,从而提高能源利用效率。
2. 石化行业:石化过程中会产生大量的热能,通过余热回收系统,可以将这些热能转化为电能或用作供热,降低生产成本,减少环境污染。
3. 纸浆造纸行业:纸浆造纸过程中会产生大量的废热和废水,利用余热回收系统可以将这些废热用于供热或蒸汽发生器,实现能源的再利用,提高能源效率。
二、建筑领域在建筑领域,余热回收可以实现能源的节约和循环利用,以下是几个典型应用案例:1. 暖通空调系统:在中央空调系统中,空调冷凝器会产生大量余热,通过余热回收技术,可以将这些余热用于供暖、热水等方面,减少能源消耗。
2. 混凝土暖房:利用太阳能或地下热能预热混凝土墙板,在夜间或阴雨天通过余热回收技术释放热能,实现冬季保温和夏季散热的双重效果。
三、交通运输领域在交通运输领域,余热回收可以提高能源利用效率,减少尾气排放,以下是几个应用案例:1. 船舶:船舶发动机产生的废热可以利用余热回收技术,转化为动力用于推进船舶,从而减少燃油消耗和减少排放。
2. 汽车:汽车发动机也会产生大量的废热,通过余热回收技术,可以将这些废热用于发电、提供车内供暖或冷却系统,实现能源的节约和减少尾气排放。
综上所述,余热回收在工业、建筑和交通运输领域都有着广泛的应用。
通过利用余热回收技术,可以实现能源的节约、环境保护和可持续发展,对于实现绿色低碳的未来具有重要意义。
我们应该进一步推广和应用这项技术,为可持续发展作出贡献。
余热回收利用报告

余热回收利用报告第一篇:余热回收利用报告关于“第八届余热回收利用研讨会”学习报告11月1号有幸参加了“第八届余热回收利用研讨会”,通过参加此次研讨会了解了国内外在余热回收利用方面的新技术,其中一些技术已经用于实践生产,并取得了良好的经济效益,以下是本次报告主要的内容:1、介绍余热综合利用的潜力及必要性;2、介绍国内外关于钢厂余热回收利用的最新技术。
3、总结适用于我公司的余热再回收技术。
一、余热综合利用的潜力及必要性。
钢铁工业是能源消耗的大户,我国钢铁工业生产过程中的能源有效利用率仅为30%左右,能源使用效率的低下造成钢铁企业能源成本增加,产品竞争力下降。
钢铁行业在生产过程中产生大量余热能源,吨钢产生的余热总量约占吨钢能耗的37%。
我国大型钢铁联合企业余热、余能资源的回收利用率约为30%-50%,但与国际先进水平相比仍有很大的差距。
国际平均利用率达80%以上,我们的节能工作仍有很大的空间,大量的余热资源可以回收产生蒸汽,做好余热蒸汽的回收和科学利用可以使钢铁企业对一次能源的需求量减少约8%。
当前,在钢铁行业面临产能过剩、结构调整、资料能源成本和环保代价日益加大,回收余热、余能越来越受到关注,成为钢铁企业节能降耗、降低成本的重点。
二、现国内在余热回收方面的研究及应用于实际工业生产的最新技术。
研究一:提高换热器的换热效率,改善换热器的换热结构及材质,使换热器能够在更加恶劣的换热环境下使用。
在节能减排的新形势下天津大学朱教授发明了新一代高效节能平行流管壳式换热器,实现了换热器管/壳程空间可控的纯逆流,提高了总传热效率30%-60%,降低运行阻力20%-70%,大大降低了动力设备的能耗,节能15%-40%、节材20%-40%、节地30%-70%,此项研究成果已获得国家相关部门认可并已应用于实际生产当中。
设计原理:传统管壳式换热器由折流板改变流体方向,通过冷热介质在管内外的换热,使工质达到冷却或加热的目的,而朱教授摒弃了这种以碰撞形式进行换热的方式,改变管子表面形状,优化换热器结构,使管内外流体形成纯逆流流动,这样大大降低了运行工质的阻力,使阻力仅为原来运行的40%-50%,达到节能的效果。
余热回收工程方案
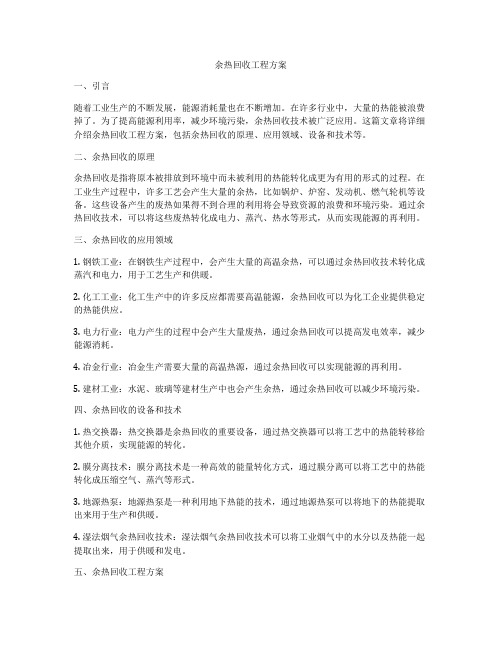
余热回收工程方案一、引言随着工业生产的不断发展,能源消耗量也在不断增加。
在许多行业中,大量的热能被浪费掉了。
为了提高能源利用率,减少环境污染,余热回收技术被广泛应用。
这篇文章将详细介绍余热回收工程方案,包括余热回收的原理、应用领域、设备和技术等。
二、余热回收的原理余热回收是指将原本被排放到环境中而未被利用的热能转化成更为有用的形式的过程。
在工业生产过程中,许多工艺会产生大量的余热,比如锅炉、炉窑、发动机、燃气轮机等设备。
这些设备产生的废热如果得不到合理的利用将会导致资源的浪费和环境污染。
通过余热回收技术,可以将这些废热转化成电力、蒸汽、热水等形式,从而实现能源的再利用。
三、余热回收的应用领域1. 钢铁工业:在钢铁生产过程中,会产生大量的高温余热,可以通过余热回收技术转化成蒸汽和电力,用于工艺生产和供暖。
2. 化工工业:化工生产中的许多反应都需要高温能源,余热回收可以为化工企业提供稳定的热能供应。
3. 电力行业:电力产生的过程中会产生大量废热,通过余热回收可以提高发电效率,减少能源消耗。
4. 冶金行业:冶金生产需要大量的高温热源,通过余热回收可以实现能源的再利用。
5. 建材工业:水泥、玻璃等建材生产中也会产生余热,通过余热回收可以减少环境污染。
四、余热回收的设备和技术1. 热交换器:热交换器是余热回收的重要设备,通过热交换器可以将工艺中的热能转移给其他介质,实现能源的转化。
2. 膜分离技术:膜分离技术是一种高效的能量转化方式,通过膜分离可以将工艺中的热能转化成压缩空气、蒸汽等形式。
3. 地源热泵:地源热泵是一种利用地下热能的技术,通过地源热泵可以将地下的热能提取出来用于生产和供暖。
4. 湿法烟气余热回收技术:湿法烟气余热回收技术可以将工业烟气中的水分以及热能一起提取出来,用于供暖和发电。
五、余热回收工程方案根据不同行业的需求和特点,余热回收工程方案也有所不同。
下面以钢铁工业为例,介绍余热回收工程方案的具体实施步骤。
钢铁制造全流程余热余能资源的回收利用现状

文章编号 : 1 0 0 2 — 1 7 7 9 ( 2 0 1 7 ) 0 2 — 0 0 5 2 — 0 5
钢铁制造全流程余热余能资源的回收利冶金行业余热余能资源 的定义 、 分类 和利用 方式 , 分析 了钢铁制造全流程 的余热余能利用 概况 , 各工序余 热余能利 用技术 和研 究趋势 , 以及先 进钢铁企业 的余热余 能利用状况 , 介绍 和分析
终轧制成材或成材前铁水 、 钢水、 坯料具有的显热 ; 烧结 矿、 球团矿具有的显热 ; 高炉渣和钢渣等熔渣显热 ; 生产
中 各种冷却水及产生的 蒸汽携带的 热能; 高炉炉顶煤气 的余压 , 少许带有压力的冷却水; 等等。
2 . 冶金行业余热资源的分类
流程的能源利用率仅为2 7 %, 其余7 3 % 主要以 余能余热 的形式存在。因 此, 提高钢铁生产流程各工序的 余热回
收利用率 , 分析与优化能耗 , 利用先进的节能技术提高资 源利用率 , 降低生产成本 , 是实现生产流程的高能效 、 高 品质、 低排放甚至零排放的根本途径。
一
( 1 ) 按品种分类
若按照余热资源的品种分类, 可将余热资源分为产 品显热 、 废气显热 、 冷却水显热和熔渣显热。其中, 产品
品显热直接输送到下道T序, 如高温铁水供转炉炼钢 ( 一
罐到底 ) 、 热钢坯送进加热炉 ( 热送热装 ) ; 烟气显热预热
二、钢铁制造全流程的余热余能利用概况
我同钢铁企业9 0 % 是以高炉一转炉为主的长流程企
业。完整的制造流程包括焦化、 烧结或球团、 高炉炼铁 、 转炉炼钢 、 轧制。陶l 是一个典型钢铁企业的制造全流程
显热占3 9 %, 废气显热  ̄ i 3 7 %, 冷却水显热 占1 5 %, 熔渣 显热 占9 %。可见 , 产品显热和废烟气显热 占总余热资
钢铁工业余热回收技术现状研究
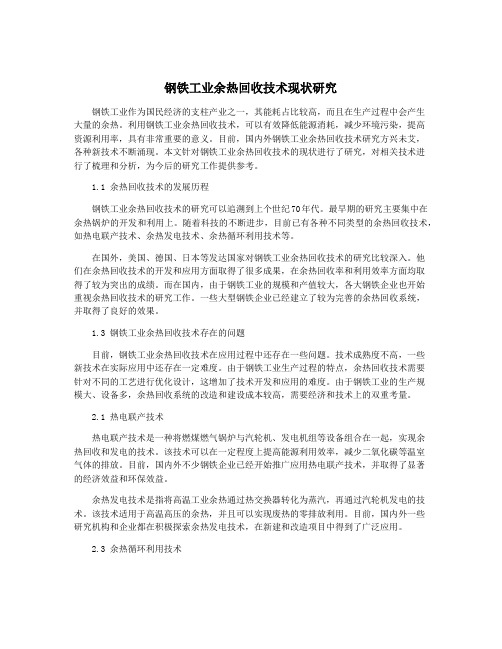
钢铁工业余热回收技术现状研究钢铁工业作为国民经济的支柱产业之一,其能耗占比较高,而且在生产过程中会产生大量的余热。
利用钢铁工业余热回收技术,可以有效降低能源消耗,减少环境污染,提高资源利用率,具有非常重要的意义。
目前,国内外钢铁工业余热回收技术研究方兴未艾,各种新技术不断涌现。
本文针对钢铁工业余热回收技术的现状进行了研究,对相关技术进行了梳理和分析,为今后的研究工作提供参考。
1.1 余热回收技术的发展历程钢铁工业余热回收技术的研究可以追溯到上个世纪70年代。
最早期的研究主要集中在余热锅炉的开发和利用上。
随着科技的不断进步,目前已有各种不同类型的余热回收技术,如热电联产技术、余热发电技术、余热循环利用技术等。
在国外,美国、德国、日本等发达国家对钢铁工业余热回收技术的研究比较深入。
他们在余热回收技术的开发和应用方面取得了很多成果,在余热回收率和利用效率方面均取得了较为突出的成绩。
而在国内,由于钢铁工业的规模和产值较大,各大钢铁企业也开始重视余热回收技术的研究工作。
一些大型钢铁企业已经建立了较为完善的余热回收系统,并取得了良好的效果。
1.3 钢铁工业余热回收技术存在的问题目前,钢铁工业余热回收技术在应用过程中还存在一些问题。
技术成熟度不高,一些新技术在实际应用中还存在一定难度。
由于钢铁工业生产过程的特点,余热回收技术需要针对不同的工艺进行优化设计,这增加了技术开发和应用的难度。
由于钢铁工业的生产规模大、设备多,余热回收系统的改造和建设成本较高,需要经济和技术上的双重考量。
2.1 热电联产技术热电联产技术是一种将燃煤燃气锅炉与汽轮机、发电机组等设备组合在一起,实现余热回收和发电的技术。
该技术可以在一定程度上提高能源利用效率,减少二氧化碳等温室气体的排放。
目前,国内外不少钢铁企业已经开始推广应用热电联产技术,并取得了显著的经济效益和环保效益。
余热发电技术是指将高温工业余热通过热交换器转化为蒸汽,再通过汽轮机发电的技术。
- 1、下载文档前请自行甄别文档内容的完整性,平台不提供额外的编辑、内容补充、找答案等附加服务。
- 2、"仅部分预览"的文档,不可在线预览部分如存在完整性等问题,可反馈申请退款(可完整预览的文档不适用该条件!)。
- 3、如文档侵犯您的权益,请联系客服反馈,我们会尽快为您处理(人工客服工作时间:9:00-18:30)。
转炉煤气干法净化系统与湿法煤气净化系统的效益比较
120t转炉干法除尘 序号 项目 吨钢耗量 1 备件(折旧费4%计) 2 水耗(m ) 3 电耗(kWh) 4 回收煤气(m )8360 kJ/m3 5 环保效益 效益合计 1440.504 380.16 1060.34
International Energy Efficiency EM&V Seminar
钢铁工业余热余能量及回收 技术
钢铁研究总院 北京, 2010
1
内容提纲
1、钢铁生产流程余热余能发生源及其产生量 2、钢铁工业余热余能回收技术及其节能 效果 3、粗钢主要生产工序能耗限额标准
2
1、钢铁生产流程余热余能发生源及其产生量
焦化
烧结
4.89 ~0.35 -
高炉
转炉炼 钢 轧钢
0.41 ~0.10 -
分析表明:
—— 无论选取何种基准温度,各工序二次能源所占钢铁制造 流程二次能源总量的比例相差不大,高炉工序二次能源产生量 最大,约占50%以上。 —— 各工序二次能源的理论产生量约为408.73 kgce/t-s(修正的 基准温度下),如果充分利用现有技术,二次能源回收利用率可 以达到约85.6%。 —— 二次能源中,副产煤气占比例最大,约74.6%,其中 COG 22.29%,BFG 43.66%,LDG 9.02%。若不含煤气和顶 压的余热资源约为104kgce/t-s。 —— 目前高炉渣、钢渣显热尚无有效回收利用技术;高炉煤 气显热、烧结和焦化烟气显热由于工艺操作原因,尚未很好地 回收利用。
5.74 17.78 8.22
1.53 11.32 --
1.73 2.01 9.46
13
0.78
9
日本钢铁企业的节能技术如CDQ、TRT、烧结 余热回收等技术的普及率都非常高
10
2.1 干熄焦技术现状 上个世纪我国没有自已的干熄焦技术,不能制造干熄 焦设备,只能花费大量资金从国外引进,。 世纪之交,我国开始了干熄焦技术与设备的国产化研 发创新工作。 2004年采用我国干熄焦技术与设备的马钢和通钢干 熄焦示范装置顺利投产,标志着我国实现了干熄焦技术 与设备的国产化,以后又实现了大型化和系列化。现在 我国可以设计建设50t/h~200t/h各种规模的干熄焦装置 。最近几年,大中型钢铁企业从节能、环保、改善焦炭 质量和多用弱粘结性煤的角度出发,纷纷兴建干熄焦装 置。一些大型独立焦化厂从节能环保、减排二氧化碳的 角度出发,也在认可和采用干熄焦技术。
B
35.83 105.52 31.05 77.23 104.49 2.54
干熄焦蒸汽回收 kg/t 572.53 , kg/t 烧结蒸汽回收, kgce/t 转炉蒸汽回收, kgce/t 转炉煤气回收, % 高炉煤气放散率, 20.73 3.9 27.05 0.74
0.228GJ 225.86
6.03 11.59 12.90
16
2.4 高炉炉顶煤气余压发电(Top Pressure Recovery Turbine,简称TRT)
现代高炉炉顶压力高达0.15~0.25MPa,炉顶煤气中 存在大量势能。炉顶余压发电技术,就是利用炉顶煤气剩 余压力使气体在透平内膨胀做功,推动透平转动,带动发 电机发电。根据炉顶压力不同,每吨铁可发电约20~ 40kWh。如果高炉煤气采用干法除尘,发电量还可增加 30%左右。 该技术可回收高炉鼓风机所需能量的30%左右,实际 上回收了原来在减压阀中白白丧失的能量。这种发电方式 既不消耗任何燃料,也不产生环境污染,发电成本又低, 是高炉冶炼工序的重大节能项目,经济效益十分显著。此 项技术在国外已非常普及,国内也在逐步推广。
17
TRT发电不消耗任何燃料就可回收大量电力,据统计,在运行 良好的情况下,吨铁回收电力约20~40kWh,可满足高炉鼓风耗电 的30%。目前,国内大多采用的是湿式除尘装置与TRT相配,未来 的发展趋势是干式除尘配TRT。TRT装置如果配有干式除尘,则吨 铁回收电力将比湿法多30%~40%,最高可回收电力约54 kWh/t。 2008年重点大中型企业约有高炉513座,其中高炉1000m3以上 高炉154座都配备TRT,TRT普及率达到100%,其中干式除尘比例 达到30%左右。我国1000m3以下高炉只有约20多座高炉配备TRT, 几乎全部为干式除尘。
8
——我国重点企业二次能源利用与国际先进 水平的比较
指标名称 TRT回收,kWh/t 国际先进水平
A
34.77 675
B
18.94 66.06 9.73 20.12 5.67
C
4.72 0
D
0
E
F
0.67 20.89 -
G
31 0 0 40 90 3.5
H
A
22.10 227.65 19.31 — 91.83
2、钢铁工业余热余能回收技术及其节能 效果
我国钢铁工业经过八、九十年代的努力,基本完成了生 产工艺结构的调整,初步实现了钢铁生产流程现代化。但由 于工艺、技术、装备的多层次性以及一些企业的结构不合 理,我国钢铁工业在余热余能回收上与国内外先进水平相比 还有一定差距,一些先进的节能工艺装备技术(如CDQ、 TRT、负能炼钢等)尚未得到普遍的推广应用,而且节能效 果也尚有差异。
转炉钢产量占中国粗钢产量的85%以上。
1.1 二次能源产生环节与品质
LDG
合成
CDQ回收红焦 显热 干式TRT 板坯热送热装
烧结矿显热回收 废烟气余热回收
烟气余热回 收 热风炉烟 气
典型钢铁制造流程二次能源产生 和回收利用情况
4
二次能源的种类与品质
工序 二次能源的种类 焦炉煤气 焦化工序 焦炭显热 废烟气显热 烧结矿显热 烧结工序 烧结烟气显热 球团矿显热 竖炉烟气 高炉煤气 高炉工序 高炉炉渣显热 高炉炉顶余压 热风炉烟气显热 转炉工序 轧钢工序 转炉煤气 炉渣显热 加热炉烟气显热 品质 高热值、显热较高 高温余热 低温余热 高温余热 中低温余热 高温余热 低温余热 热值高、显热较低 高温余热 高品质 中低温余热 高热值、显热较高 高温余热 高温余热 国内钢铁工业利用现状 仅回收潜热 多数钢厂已回收,CDQ技术 未回收 一些钢厂回收,余热蒸汽或发电 一些钢厂有回收,热风烧结 未回收 未回收 仅回收潜热 冲渣水采暖 全部1000m3以上高炉及部分小高炉 煤气、空气双预热 回收潜热、显热 未回收 回收显热
5
球团工序
1. 2 二次能源产生量与回收水平
工序 种类 焦炭显热 COG潜热 COG显热 废烟气显热 小计 烧结矿显热 废气显热 小计 BFG潜热 BFG显热 炉顶余压 炉渣显热 热风炉烟气显热 小计 LDG潜热 LDG显热 炉渣显热 小计 加热炉废气显热 总计 产生量/GJ 吨产品 折吨钢 1.78 0.59 7.66 2.55 0.50 0.17 0.57 0.19 10.51 3.50 0.62 0.94 0.45 0.69 1.07 1.62 5.29 5.02 0.81 0.77 0.47 0.45 0.62 0.59 0.38 0.36 7.58 7.20 0.90 0.90 0.21 0.21 0.15 0.15 1.26 1.26 0.72 0.70 14.28 回收量/GJ 吨产品 折吨钢 1.42 0.59 7.59 2.52 0.11 0.04 9.45 0.22 0.22 5.16 0.47 0.21 5.83 0.77 0.18 0.95 0.41 3.14 0.33 0.33 4.90 0.45 0.19 5.54 0.77 0.18 0.95 0.40 10.37 回收比例 /% 80.0 99.0 21.1 89.90 35.6 0.0 20.59 97.5 100.0 53.8 77.02 85.0 86.9 75.32 57.1 72.6 国内回收 水平/GJ ~1.47 ~7.50 0.11 ~0.15 所占比例/% 工序 吨钢 16.91 4.14 72.89 17.84 4.77 1.17 5.43 1.33 100 24.48 2.657 6.57 42.22 4.80 100 11.37 69.80 35.18 10.73 5.41 6.25 3.15 8.19 4.14 5.03 2.52 100 50.40 71.58 6.33 16.66 1.47 11.76 1.04 100 8.85 100 4.91 100 6
11
截至2008年5月底,我国投产运行的干熄焦装置共57套 ,有4880万吨年焦炭生产能力配置了干熄焦装置,占我 国机焦产能3.6亿吨的13.5%,占我国2007年钢铁工业耗 焦总量28822万吨的16.9%。 我国在建和已投产的干熄焦装置共119套,已经和正在 为11448万吨年焦炭生产能力配置干熄焦装置,占我国机 焦产能的31.8%,相当于我国2007年钢铁工业耗焦总量 的39.7%。按干熄焦能力计,位居世界第一位。 当前世界各国已投产、正在施工和设计的干熄焦装置约 300套。
13
2.3 烧结余热回收技术
在钢铁企业中,烧结工序的总能耗仅次于炼铁,居第 二位,一般为钢铁企业总能耗的10%~20%。我国烧结工 序的能耗指标和先进国家相比差距较大,每吨烧结矿的平 均能耗要高20 kgce。因此,我国烧结节能的潜力很大。 国内外对烧结余热的回收利用进行了大量的研究,据 日本某钢铁厂热平衡测试数据表明,烧结机的热收入中烧 结矿显热占28.2%、废气显热占31.8%。由此可见,烧结 厂余热回收的重点应为烧结废(烟)气余热和烧结矿(产 品)显热回收。
14
烧结矿余热回收(Sinter Plant Heat Recovery)是提 高烧结能源利用效率、降低烧结工序能耗的途径之一。 烧结系统的显热回收有两部分:一是烧结矿的显 热,二是烧结机尾部烟气的显热。目前,烧结废气余热回 收利用的方式主要有以下四种: 利用余热锅炉产生蒸汽或提供热水,直接利用; 用冷却器的排气代替烧结机点火器的助燃空气或用于 预热助燃空气; 将余热锅炉产生的蒸汽,通过透平及其它装置转换成 电力; 将排气直接用于预热烧结机的混合料。