完整版钢铁行业余热回收
钢铁工业余热能量及回收

如何有效回收利用烧结矿余热,降低烧结工艺能耗, 是国内钢铁行业中普遍存在并关注的一个课题。目前,国 内钢铁企业中不少企业采用烧结矿余热回收蒸汽,如武 钢、鞍钢等,但是对于蒸汽的利用不充分,造成能源浪 费。国外先进企业生产每吨烧结矿可回收余热蒸汽80~ 100 kg/t。 另外近两年,济钢和马钢分别采用国产和日本技术把 烧结矿余热回收的蒸汽用于发电,取得了良好的利用效 果,但其技术完善和蒸汽能源的合理利用方法有待进一步
焦化
烧结
4.89 ~0.35 -
高炉
转炉炼 钢 轧钢
0.41 ~0.10 -
分析表明:
—— 无论选取何种基准温度,各工序二次能源所占钢铁制造 流程二次能源总量的比例相差不大,高炉工序二次能源产生量 最大,约占50%以上。 —— 各工序二次能源的理论产生量约为408.73 kgce/t-s(修正的 基准温度下),如果充分利用现有技术,二次能源回收利用率可 以达到约85.6%。 —— 二次能源中,副产煤气占比例最大,约74.6%,其中 COG 22.29%,BFG 43.66%,LDG 9.02%。若不含煤气和顶 压的余热资源约为104kgce/t-s。 —— 目前高炉渣、钢渣显热尚无有效回收利用技术;高炉煤 气显热、烧结和焦化烟气显热由于工艺操作原因,尚未很好地 回收利用。
12
2.2 煤调湿技术(Coal Moisture Control,CMC)
我国的煤调湿建设情况 现在我国宝钢、太钢和攀钢已建成以蒸汽为热源的 CMC装置,采用国产的回转式干燥机。 济钢于2007年10月投产了自已开发的以焦炉烟道废气 为热源、具有风选功能的流化床煤调湿装置。 首钢、昆钢、鞍钢、沙钢和安钢正在进行CMC的前期 工作。 CMC节能效果: 采用CMC技术,煤料含水量每降低1%,炼 焦耗热量就降低62.0MJ/t(干煤)。当煤料水分从11%下 降至6%时,炼焦耗热量节省310MJ/t(干煤);
钢铁工业余热回收的主要环节介绍
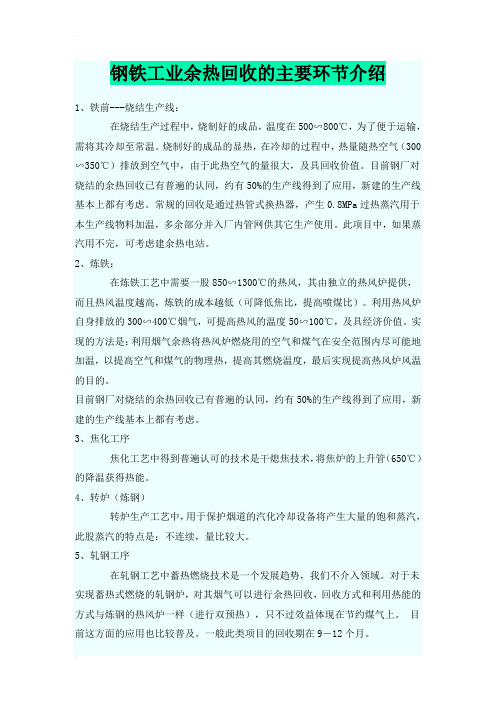
钢铁工业余热回收的主要环节介绍1、铁前---烧结生产线:在烧结生产过程中,烧制好的成品,温度在500∽800℃,为了便于运输,需将其冷却至常温。
烧制好的成品的显热,在冷却的过程中,热量随热空气(300∽350℃)排放到空气中,由于此热空气的量很大,及具回收价值。
目前钢厂对烧结的余热回收已有普遍的认同,约有50%的生产线得到了应用,新建的生产线基本上都有考虑。
常规的回收是通过热管式换热器,产生0.8MPa过热蒸汽用于本生产线物料加温,多余部分并入厂内管网供其它生产使用。
此项目中,如果蒸汽用不完,可考虑建余热电站。
2、炼铁:在炼铁工艺中需要一股850∽1300℃的热风,其由独立的热风炉提供,而且热风温度越高,炼铁的成本越低(可降低焦比,提高喷煤比)。
利用热风炉自身排放的300∽400℃烟气,可提高热风的温度50∽100℃,及具经济价值。
实现的方法是:利用烟气余热将热风炉燃烧用的空气和煤气在安全范围内尽可能地加温,以提高空气和煤气的物理热,提高其燃烧温度,最后实现提高热风炉风温的目的。
目前钢厂对烧结的余热回收已有普遍的认同,约有50%的生产线得到了应用,新建的生产线基本上都有考虑。
3、焦化工序焦化工艺中得到普遍认可的技术是干熄焦技术,将焦炉的上升管(650℃)的降温获得热能。
4、转炉(炼钢)转炉生产工艺中,用于保护烟道的汽化冷却设备将产生大量的饱和蒸汽,此股蒸汽的特点是:不连续,量比较大。
5、轧钢工序在轧钢工艺中蓄热燃烧技术是一个发展趋势,我们不介入领域。
对于未实现蓄热式燃烧的轧钢炉,对其烟气可以进行余热回收,回收方式和利用热能的方式与炼钢的热风炉一样(进行双预热),只不过效益体现在节约煤气上。
目前这方面的应用也比较普及。
一般此类项目的回收期在9-12个月。
1、铁前---烧结生产线:在烧结生产过程中,烧制好的成品,温度在500∽800℃,为了便于运输,需将其冷却至常温。
烧制好的成品的显热,在冷却的过程中,热量随热空气(300∽350℃)排放到空气中,由于此热空气的量很大,及具回收价值。
余热回收工程方案
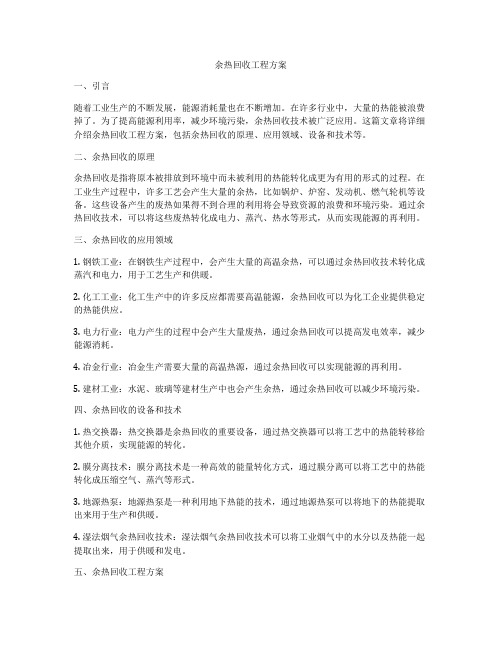
余热回收工程方案一、引言随着工业生产的不断发展,能源消耗量也在不断增加。
在许多行业中,大量的热能被浪费掉了。
为了提高能源利用率,减少环境污染,余热回收技术被广泛应用。
这篇文章将详细介绍余热回收工程方案,包括余热回收的原理、应用领域、设备和技术等。
二、余热回收的原理余热回收是指将原本被排放到环境中而未被利用的热能转化成更为有用的形式的过程。
在工业生产过程中,许多工艺会产生大量的余热,比如锅炉、炉窑、发动机、燃气轮机等设备。
这些设备产生的废热如果得不到合理的利用将会导致资源的浪费和环境污染。
通过余热回收技术,可以将这些废热转化成电力、蒸汽、热水等形式,从而实现能源的再利用。
三、余热回收的应用领域1. 钢铁工业:在钢铁生产过程中,会产生大量的高温余热,可以通过余热回收技术转化成蒸汽和电力,用于工艺生产和供暖。
2. 化工工业:化工生产中的许多反应都需要高温能源,余热回收可以为化工企业提供稳定的热能供应。
3. 电力行业:电力产生的过程中会产生大量废热,通过余热回收可以提高发电效率,减少能源消耗。
4. 冶金行业:冶金生产需要大量的高温热源,通过余热回收可以实现能源的再利用。
5. 建材工业:水泥、玻璃等建材生产中也会产生余热,通过余热回收可以减少环境污染。
四、余热回收的设备和技术1. 热交换器:热交换器是余热回收的重要设备,通过热交换器可以将工艺中的热能转移给其他介质,实现能源的转化。
2. 膜分离技术:膜分离技术是一种高效的能量转化方式,通过膜分离可以将工艺中的热能转化成压缩空气、蒸汽等形式。
3. 地源热泵:地源热泵是一种利用地下热能的技术,通过地源热泵可以将地下的热能提取出来用于生产和供暖。
4. 湿法烟气余热回收技术:湿法烟气余热回收技术可以将工业烟气中的水分以及热能一起提取出来,用于供暖和发电。
五、余热回收工程方案根据不同行业的需求和特点,余热回收工程方案也有所不同。
下面以钢铁工业为例,介绍余热回收工程方案的具体实施步骤。
钢铁生产过程余热资源回收与利用技术

就我国钢铁工业而言(以长流程为例),其比较典型的 余热资源有: 焦化工序:红焦显热、焦炉荒煤气显热; 烧结工序:烧结矿显热、烧结烟气显热; 炼铁工序:铁水显热、高炉炉顶余热、融渣显热、高炉冷却 水显热;
炼钢工序:钢水显热、转炉烟气显热、融渣显热;
轧钢工序:加热炉冷却水显热。
余热总量
2005年,我国大中型钢铁企业生产1吨钢所产生的余热资 源总量为8.44GJ/t钢,大约占吨钢可比能耗的37%。
0.21
0.08
1.65 0.95
0.29 1.24 0.02 0.02 0.02
0.19 0.17 0.69 0.77 0.36 0.21 0.72 3.11 0.95
0.29 1.24 8.44
0.02
0.11 0.08 0.25 0.46 0.02 0.02 2.17
利用分析
3.36
1.49
2.19
冷却水显 热15% 产品显热 39%
废烟气显 热37%
渣显热 9%
图5 我国钢铁工业余热资源构成*
*2005年,我国20余家大中型钢铁企业统计数据
1.2 余热资源的回收利用水平
以1吨钢为基准,统计各种余热的回收与利用数据。
表 我国大中型钢铁企业余热资源回收利用的情况
高温 中温 低温
GJ/t-s
合计
排的方向、途径及潜力所在。
企Байду номын сангаас能耗
∑(能源 j 实物耗量)×(能源 j 折标系数)—(能源回收利用量) 工序能耗 =
j
统计期内工序的实物产量
降低工序能耗必须从两方面入手: (1)降低各工序生产单位产品所直接消耗的燃料量和 各种动力;
(2)高效回收各工序产生的各种余热和余能。
中国钢铁行业余热余压回收利用途径分析1

中国钢铁行业余热余压回收利用途径分析北极星节能环保网2014/5/30 11:51:22 我要投稿关键词:余热回收设备烟气余热余热余压北极星节能环保网讯:现阶段,钢铁工业各生产工序已回收余热余压资源情况及利用途径分析如下:焦化工序。
焦化工序现阶段已回收利用的余热余压资源包括焦炭显热、焦炉煤气潜热、烟道气显热和初冷水显热。
焦炭显热主要是采用干熄焦技术回收利用产生蒸汽用于发电,目前干熄焦发电技术在国内钢铁联合企业的应用普及率已很高。
焦炉煤气热值高,是一种优质燃料,目前已得到充分利用,放散率很低,主要利用途径是供各生产用户使用,富余资源用于驱动锅炉发电。
同时,由于焦炉煤气富含氢气和甲烷,提升利用品位,将其作为化工原料生产甲醇、合成氨等化工产品和天然气资源的利用方式近年来得到了更多的关注。
烟道气显热的温度一般是250 C ~300 C,目前主要采用余热回收设备回收蒸汽供生产、生活用户或作为煤调湿热源。
焦化初冷水显热温度一般是60 C ~70 C,主要采用换热器回收热量用于北方地区冬季采暖。
烧结工序。
烧结工序现阶段已回收利用的余热余压资源包括烧结矿显热和烧结烟气显热。
烧结矿显热的回收主要在环冷机部分,按烟气温度分高、中、低三部分,目前高温段烟气余热回收利用较为充分,主要采用余热锅炉产生蒸汽用于发电或者供生产用户;中、低温烟气余热一般采用直接利用方式,用于预热混料或热风烧结等。
对于烧结烟气显热的回收利用近几年开始起步,在部分企业已有应用,主要集中在烧结大烟道高温区(300 C ~400 C )的回收,采用余热锅炉或热管换热器回收产生蒸汽。
球团工序。
球团工序现阶段已回收利用的余热余压资源包括球团矿显热、烟气显热和冷却水显热。
球团矿显热主要通过获取热风回用于生产,作为烘干、预热等热源。
烟气显热温度较低(约120 C ),少数企业采用热管换热器回收热量用于职工洗浴等生活用户。
竖炉大水梁冷却水显热通常采用汽化冷却方式替代水冷方式,避免循环冷却水消耗,并回收产生蒸汽。
钢铁厂余热利用政策

钢铁厂余热利用政策
钢铁厂余热利用政策是指政府制定的鼓励和促进钢铁厂余热利用的相关政策措施。
钢铁厂是能源消耗较大的行业,会产生大量的余热。
充分利用和回收这些余热,不仅可以减少资源浪费,还可以提高能源利用效率,降低环境污染。
因此,很多国家和地区都制定了相关的政策来推动钢铁厂余热利用。
具体的政策措施包括:
1. 减税优惠:政府可以对进行余热利用的钢铁企业给予减免税收的优惠政策,以提高企业的利润和盈利能力。
2. 资金支持:政府可以设立专项资金,用于扶持和支持余热利用项目的建设和运营。
同时,可为企业提供贷款和融资支持,降低企业投资余热利用项目的成本。
3. 技术支持:政府可以建立技术研发中心,支持钢铁企业的余热利用技术研究和开发。
提供技术指导、培训和咨询服务,加强技术交流与合作。
4. 奖励机制:政府可以设立奖励机制,对那些在余热利用方面取得显著效果的钢铁企业进行奖励和表彰,激励企业加大投入和创新。
5. 示范工程:政府可以选择一些具有示范和推广价值的余热利用项目进行资助和扶持,以提供技术和经验参考给其他企业。
通过上述政策措施的推动和支持,可以有效促进钢铁厂余热的利用,推动钢铁产业的可持续发展。
钢铁厂余热利用政策
钢铁厂余热利用政策
钢铁厂余热利用政策是指政府对钢铁厂利用余热进行能源节约和环境保护的政策措施。
钢铁行业是能源消耗较大的行业之一,大量的余热没有得到有效利用,不仅浪费了资源,还导致了环境污染。
因此,各国政府都纷纷出台了相关政策,鼓励和支持钢铁厂进行余热利用。
在中国,钢铁厂余热利用政策主要体现在以下几个方面:
1. 能源节约减排政策:中国政府鼓励钢铁企业进行余热利用,减少能源消耗和二氧化碳排放。
钢铁企业通过利用余热发电或供热,可以减少煤炭等能源的消耗,降低生产成本,提高企业的竞争力。
2. 资金支持政策:政府为钢铁企业的余热利用项目提供一定的资金支持,包括贷款优惠、补贴资金等,降低企业投资成本,增加项目的可行性。
3. 技术支持政策:政府鼓励钢铁企业引进先进的余热利用技术,提高能源利用效率,降低环境污染。
政府可以通过技术培训、技术指导等方式,帮助企业提升技术水平。
4. 税收政策:政府可以对实施余热利用的钢铁企业给予税收优惠,减少企业税负,提高企业盈利能力,促进企业积极开展余热利用。
5. 监管政策:政府加强对钢铁企业余热利用项目的监管,确保项目合法合规运行,保障环境和能源的可持续利用,推动钢铁行业的绿色发展。
总的来说,钢铁厂余热利用政策是为了促进钢铁行业的绿色发展,实现资源的高效利用和环境的保护。
政府的政策支持和资金扶持可以帮助钢铁企业更好地开展余热利用,提高企业的经济效益和社会效益,推动钢铁行业向绿色、可持续的方向发展。
企业也应积极响应政策,加大投入,加强管理,提高技术水平,共同推动钢铁行业的绿色转型,为可持续发展做出贡献。
(完整版)钢铁行业余热回收
烧结线余热烧结生产线有两部分余热,一是冷却机产生的热风,二是烧结机尾的高温烟气。
用余热锅炉将这两部分余热来产生蒸汽,再通过汽轮机发电。
据经验数据,每10m2的烧结面积可产生1.5t/h的蒸汽,可发电300kW,折合标煤120kg/h。
转炉余热转炉汽化冷却烟道间歇产生的蒸汽,通过蓄能器变为连续的饱和蒸汽,采用我公司的专利——机内除湿再热的多级冲动式汽轮机发电。
每炼1t钢,可产生80kg 饱和蒸汽,每吨饱和蒸汽大约可发电150kWh,折合标煤60kg。
转炉煤气经过汽化冷却烟道冷却后温度仍高达800~900℃,采用我公司的干法煤气显热回收技术,通过下降管烟道、急冷换热器回收显热生产蒸汽,经蓄能器调节后发电。
电炉余热电炉冶炼过程中产生200~1000℃的高温含尘废气,采用余热锅炉将其回收,电炉烟气属于周期波动热源,因此余热锅炉产生的蒸汽需要经过蓄能器调节后方可进入汽轮机发电。
加热炉余热加热炉有两处余热可以利用:一处是炉内支撑梁的汽化冷却系统,另一处是烟道高温烟气。
根据炉型不同,加热炉的烟气量在7000~300000Nm3/h,若用来发电,以烟气量10万Nm3,烟气温度400℃计算,发电量约2000kWh,折合标煤0.8t;汽化冷却系统可生产0.4~1.0Mpa的饱和蒸汽,每吨蒸汽(0.5Mpa)可发电120kWh,折合标煤48kg。
高炉冲渣水用高速水流冲击炉渣使之充分急冷、粒化的过程中,会产生大量的冲渣热水。
每吨铁排出约0.3t渣,每吨渣可产生80~95℃,5~10t的冲渣水,将这部分热水减压产生低压蒸汽,再进入饱和蒸汽凝汽式汽轮机发电。
每吨90℃热水可发电1.5kWh,折标煤0.6kg,80℃热水可发电1kWh,折标煤0.4kg。
干法熄焦采用惰性气体来冷却红焦,加热后的气体在余热锅炉中产生蒸汽,蒸汽可发电或并入蒸汽管网。
吨焦可生产3.9Mpa、300℃的蒸汽0.45t~0.6t,可发电85~115kWh,折合标煤35~46kg。
炼钢余热深度余热回收技术
炼钢余热深度回收技术的研究与应用
引言:
随着工业化进程的加速,能源消耗问题日益凸显。
尤其是在炼钢行业,大量的余热资源未得到充分利用,不仅造成了能源浪费,也对环境产生了负面影响。
因此,如何有效回收并利用炼钢过程中的余热资源成为了当前亟待解决的问题。
一、炼钢余热的产生及特性
炼钢过程中产生的余热主要包括炉渣余热、废气余热和冷却水余热等。
这些余热具有温度高、数量大、持续性强等特点,具备很高的回收价值。
二、炼钢余热深度回收技术
1. 炉渣余热回收技术:主要采用换热器进行余热回收,通过将出炉的高温炉渣与换热介质(如水或蒸汽)进行热交换,将热量传递给换热介质,再进一步转化为电能或热能。
2. 废气余热回收技术:主要采用热管换热器或陶瓷换热器进行余热回收,将废气中的热量传递给换热介质,再进一步转化为电能或热能。
3. 冷却水余热回收技术:主要采用热泵技术进行余热回收,通过将冷却水中的热量提取出来,再进一步转化为电能或热能。
三、炼钢余热深度回收技术的应用
目前,上述余热回收技术已在许多炼钢厂得到了广泛应用,并取得了显著的经济效益和社会效益。
例如,某炼钢厂通过应用余热回收技术,每年可节省标准煤约万吨,减排二氧化碳近万吨,同时还能提高生产效率,降低生产成本。
四、结论
综上所述,炼钢余热深度回收技术是一种有效的节能降耗措施,不仅可以实现能源的高效利用,还可以减少环境污染,具有广阔的推广应用前景。
未来,我们应继续加大技术研发力度,推动炼钢余热深度回收技术的进一步发展和完善。
钢铁行业余热回收 相关的政策
钢铁行业余热回收相关的政策一、背景钢铁行业作为国民经济重要的基础产业,其产能和产量均居全球第一位。
然而,钢铁生产过程中会产生大量的余热,不仅资源浪费严重,还会对环境造成污染。
因此,钢铁行业余热回收已成为当前能源节约和环境保护的紧迫任务。
二、意义1. 能源节约:钢铁行业的余热回收可有效利用高温烟气中的余热,提高能源利用效率,保护有限的能源资源。
2. 减少排放:余热回收可以减少炼钢企业排放的废热和废气,降低环境污染,改善空气质量。
3. 降低成本:通过合理利用余热,可以减少对外购能量的依赖,降低生产成本,提高企业竞争力。
三、政策措施1. 奖励制度:政府可以出台奖励措施,对使用余热回收技术并取得一定效果的钢铁企业给予一定的财政奖励。
2. 政策引导:政府可以加大对余热回收技术的扶持力度,通过贷款贴息、税收减免等方式鼓励企业投资并采用余热回收设备。
3. 技术支持:政府可以加大对余热回收技术的研发投入,鼓励企业开展科技创新,提高余热回收技术的先进性和可靠性。
4. 限制排放:政府可以制定环保政策,限制钢铁企业的废热和废气排放量,强制企业加强余热回收设备的安装和使用。
5. 行业标准:政府可以牵头组织制定行业标准,要求钢铁企业在余热回收方面达到一定的技术和效果标准。
四、预期效果1. 能源节约:通过余热回收,预计可以减少钢铁行业的能源消耗,提高能源利用效率,减少资源浪费。
2. 环境改善:余热回收可以大幅度减少钢铁行业的废热和废气排放,降低环境污染,改善周边环境质量。
3. 产业升级:通过余热回收技术的推广应用,将促进我国钢铁行业的技术升级和发展,提高产业的可持续竞争力。
五、总结钢铁行业余热回收是国家能源节约和环境保护的紧迫任务,只有整合政府和企业的力量,出台相关政策措施,推动钢铁行业余热回收技术的应用,才能实现能源效益和环境效益的双赢。
同时,行业主管部门应加大监督检查力度,确保政策的有效实施,为钢铁行业的可持续发展提供有力的支持。
- 1、下载文档前请自行甄别文档内容的完整性,平台不提供额外的编辑、内容补充、找答案等附加服务。
- 2、"仅部分预览"的文档,不可在线预览部分如存在完整性等问题,可反馈申请退款(可完整预览的文档不适用该条件!)。
- 3、如文档侵犯您的权益,请联系客服反馈,我们会尽快为您处理(人工客服工作时间:9:00-18:30)。
烧结线余热烧结生产线有两部分余热,一是冷却机产生的热风,二是烧结机尾的高温烟气。
用余热锅炉将这两部分余热来产生蒸汽,再通过汽轮机发电。
据经验数据,每10m2的烧结面积可产生 1.5t/h 的蒸汽,可发电300kW,折合标煤120kg/h 。
转炉余热转炉汽化冷却烟道间歇产生的蒸汽,通过蓄能器变为连续的饱和蒸汽,采用我公司的专利——机内除湿再热的多级冲动式汽轮机发电。
每炼1t 钢,可产生80kg 饱和蒸汽,每吨饱和蒸汽大约可发电150kWh,折合标煤60kg。
转炉煤气经过汽化冷却烟道冷却后温度仍高达800〜900 C,采用我公司的干法煤气显热回收技术,通过下降管烟道、急冷换热器回收显热生产蒸汽,经蓄能器调节后发电。
电炉余热电炉冶炼过程中产生200〜1000 C的高温含尘废气,采用余热锅炉将其回收,电炉烟气属于周期波动热源,因此余热锅炉产生的蒸汽需要经过蓄能器调节后方可进入汽轮机发电。
加热炉余热加热炉有两处余热可以利用:一处是炉内支撑梁的汽化冷却系统,另一处是烟道高温烟气。
根据炉型不同,加热炉的烟气量在7000〜300000Nm3/h,若用来发电,以烟气量10万Nm3烟气温度400 C计算,发电量约2000kWh,折合标煤0.8t ; 汽化冷却系统可生产0.4~1.0Mpa的饱和蒸汽,每吨蒸汽(0.5Mpa)可发电120kWh,折合标煤48kg。
高炉冲渣水用高速水流冲击炉渣使之充分急冷、粒化的过程中,会产生大量的冲渣热水。
每吨铁排出约0.3t渣,每吨渣可产生80〜95 °C,5〜10t的冲渣水,将这部分热水减压产生低压蒸汽,再进入饱和蒸汽凝汽式汽轮机发电。
每吨90 C热水可发电1.5kWh,折标煤0.6kg,80 C热水可发电1kWh,折标煤0.4kg 。
干法熄焦采用惰性气体来冷却红焦,加热后的气体在余热锅炉中产生蒸汽,蒸汽可发电或并入蒸汽管网。
吨焦可生产 3.9Mpa、300 C的蒸汽0.45t〜0.6t ,可发电85〜115kWh,折合标煤35〜46kg。
高炉煤气余压利用高炉炉顶煤气的压力能和热能,通过透平膨胀机做功发电,但不影响煤气后续利用。
高炉炉顶压力达0.15〜0.25Mpa,平均每吨铁可发电20〜50kWh,折标煤8〜20kg,单位投资费用约4500元/kW,根据压力及除尘方式不同,投资回收期在2〜6年。
煤气一一蒸汽联合循环发电利用高炉煤气和焦炉煤气作为能源发电,煤气先在燃气透平中燃烧发电,燃气透平排出的高温烟气再在余热锅炉生产蒸汽,通过蒸汽轮机发电,总发电效率可达40〜46% 1万m3的煤气(热值3000kJ/m3 ),约发电4000kWh左右,折合标煤 1.6t,单位投资费用4500〜6500元/kW左右,投资回收期为3〜5年。
注:电力折标系数为0.404kg标煤/kWh。
(经验计算总量煤气90000m3/h- 3.6=25000kw/h发电机功率)(1kw/h "热值3.6~4 MJ/m3)(经验计算发电总功率25MW 3.6~4.4〜90~110t高温高压煤气锅炉)(经验换算发一度电(1KW)大概用热值3.6-4 MJ/m3高炉煤气)。
钢铁行业余热回收钢铁工业是我国重点的耗能大户,总能耗约占全国总能耗量的15%左右,钢铁生产工艺流程长,工序多,且主要以高温冶炼、加工为主,生产过程中产生大量余热能源,主要来自烧结机烟气显热、红焦显热、转炉烟气及加热炉炉底的余热回收装置等,各种余热资源约占全部生产能耗的68%说明在目前钢铁生产过程中2/3以上的能量是以废气、废渣和产品余热形式消耗。
在余热发电技术的研发应用方面,与日本、德国等发达国家钢铁工业相比,我国钢铁行业的余热发电技术起步较晚。
目前,钢铁工业余热发电主要有以下三种方式,一是利用焦化、烧结工序烟气余热换热产生过热蒸汽发电;二是利用炼钢、轧钢工序烟气余热换热产生饱和蒸汽发电;第三种是利用高炉的冲渣热水发电。
A. 过热蒸汽发电a.干熄焦余热发电炼焦生产中,高温红焦冷却有两种熄焦工艺:一种是传统的采用水熄灭炽热红焦的工艺,简称湿熄焦,另一种是采用循环惰性气体与红焦进行热交换冷却焦炭,简称干熄焦。
干熄焦余热发电技术是指利用与红焦热交换产生的高温烟气驱动汽轮发电机组进行发电,其主要工艺流程为:焦炉生产出来的约1000 摄氏度赤热焦炭运送入干熄炉,在冷却室内与循环风机鼓入的冷惰性气体进行热交换。
惰性气体吸收红焦的显热,温度上升至800 摄氏度左右,经余热锅炉生产中高压过热蒸汽,驱动汽轮发电机组发电,同时汽轮机还可产生低压蒸汽用于供热。
随着干熄焦技术所产生的社会和节能环保效益得到普遍认可,干熄焦余热发电技术也得到了国内钢铁企业越来越广泛的应用。
该项发电技术已十分成熟,目前的发展趋势集中在进一步提高余热的回收利用效率上,正逐步由传统的小型中压参数系统向系列化、大型化、高参数发展。
典型用户及投资效益:马钢煤焦化公司,投资约 2 亿元,安装了中温中压强制循环干熄焦余热锅炉及汽轮发电机组,干熄焦能力为125t/h,日发电量30万kwh,年回收热能折标煤52020t,投资回收期 4 年。
沙钢集团,投资约2亿元,安装了中温高压强制循环干熄焦余热锅炉及汽轮发电机组,年发电1.5亿kWh,取得经济效益8000万元,投资回收期2.5年。
技术的利用现状和市场潜力:目前中国的干熄焦技术普及率较低,且大部分为中低压干熄焦,高压干熄焦的推广潜力很大。
“十一五”期间该技术在行业能推广到的比例为20%,总投资约为60亿元,年可发电量45亿kWh。
b. 烧结余热发电具有较好回报价值的烧结余热是指从烧结机尾部风箱排出的废气及热烧结矿在冷却机前段受空气冷却后产生的热废气,温度一般可达到300-400 摄氏度,这两部分热废气所含热量占整个烧结矿热能消耗的23%-28%左右,具有温度高、数量大、运行稳定的特点,是烧结工序节能和回收利用的重点。
国内钢铁企业大多将烧结余热用于助燃空气、预热混合料或利用余热回收装置产生蒸汽,回收利用效率不高。
特别是现阶段伴随着烧结机的大型化,传统的余热利用途径已无法充分利用余热资源,达到效益的最大化。
因此,从实现能源梯级利用的高效性和经济性角度分析,利用余热发电是现今最为有效的余热利用途径。
烧结余热发电是指将烧结机生产过程中产生的高温废烟气,经余热锅炉产生中低压过热蒸汽,驱动汽轮发电机组发电。
技术原理:在烧结工序总能耗中,有近50%的热能以烧结烟气和冷却机废气的显热形式排入大气。
由于烧结冷却机废气的温度不高,仅150〜450°C,加上以前余热回收技术的局限,余热回收项目往往被忽略。
烧结冷却机余热的回收,是通过回收烧结机尾落矿风箱及烧结冷却机密闭段的烟气加热余热锅炉来回收低品味余热能源,结合低温余热发电技术,用余热锅炉的过热蒸气来推动低参数的汽轮发电机组做功发电的成套技术。
具体流程是:给水经给水泵进入余热锅炉,经废气加热后,一部分变为过热蒸汽,进入汽轮机作功发电。
另一部分经余热锅炉低温段加热后,产生过热或饱和蒸汽进入汽轮机相应低压进汽口作功发电。
冷凝水经低压省煤器后由中压锅炉给水泵供给低压汽包,低压汽包具有自除氧功能,实现一个完整的热力循环。
烧结冷却机烟气具有如下特点:1)烧结余热热源品质整体较低,低温部分占比例大;2)烧结过程中,随着烧结矿在烧结机上的烧成情况不同,其烟气温度也不同;3)在烧结生产中由于设备的运行的不确定性,短时间停机不可避免,造成烧结烟气不连续性。
因此,要求发电系统:1)汽轮机必须带有前压调节装置,当机组在正常运行时,以汽轮机的进口压力作为主要控制参数,来调节机组输出功率以保证压力基本稳定,这种方式可适应废气余热参数的变化,使整个系统有较高的适应性和可靠性;2)用于余热利用的汽轮发电机的特点是以汽定电,所以要求带负荷的能力可在较大范围内波动,尤其是发电机的选型要考虑能超过设计发电量的15%左右。
经济社会效益:从能源利用角度原来生产线24%左右的热能随废气排放到大气中,不仅造成能源的浪费,同时产生温室效应。
建设余热发电项目后,不仅节约能源而且减少排放。
以360m2烧结机余热电站为例,总投资为1.7亿元,每年可发电1.4亿kWh产生净经济效益7000万元,投资回收期为 2.5 年。
近几年,随着双压、闪蒸发电和补汽蒸汽式汽轮机在技术上获得突破,烧结余热发电技术已逐渐进入成熟阶段,同时其在节能环保、减少污染排放、经济效益等方面的显著优势使得其发展迅速。
2005年9月,马钢引进日本川崎技术在2台300M2烧结机上建成了国内第一套17.5MW余热发电机组,截至到2009年底,国内钢铁企业共有19台烧结机配套建设了余热发电机组,配备余热发电机组10套,总装机容量136.7M W此外,安钢等一些企业正在施工建设烧结余热发电站。
烧结余热发电技术推广比例不及4%。
烧结余热发电技术在国内应用已经成熟,全套设备可以国产化,已具备全面推广的条件。
B. 饱和蒸汽发电除上述余热资源外,钢铁企业生产过程中炼钢、轧钢等工序尚产生大量低压饱和蒸汽,按产生制度分为间断蒸汽及相对连续蒸汽,其相比焦化、烧结工序余热资源,利用价值相对较低。
间断蒸汽,这部分主要是指炼钢工序产生的余热蒸汽。
转炉在吹炼过程中,产生大量1200摄氏度以上高温烟气,为降低烟气温度、回收高温烟气中的余热同时为转炉烟气除尘机煤气回收创造条件。
目前大多数转炉均配套设置了烟道式汽化冷却装置,电炉炼钢烟道也在向汽化冷却的方向发展,但由于炼钢生产的间断性,决定由该装置产生的蒸汽具有饱和不连续性。
钢铁企业饱和蒸汽产生量大,但利用效率低,特别是在南方大部分冬季不采暖地区的钢铁厂。
采用饱和蒸汽发电,既可以充分利用饱和蒸汽,避免蒸汽放散造成的浪费,同时能提供电能,产生新的效益。
因此,可以预计该项发电技术未来的发展潜力将很大。
C. 热水发电高炉炼铁过程中,产生的炉渣温度大约为1000摄氏度,炉渣在冲渣箱内由冲渣泵提供的高速水流急冷冲成水渣并粒化,这一过程中能够产生大量温度在80-95 摄氏度的低温热水,热水量达到几千吨/ 小时,长期排放既浪费了能源,又造成环境污染和水资源流失。
由于高炉冲渣水具有温度低、流量大的特点,应用较为困难,现阶段除北方少数钢铁企业用于冬季采暖外,大部分企业均未利用。
针对这种情况,目前认为比较可行的应用措施是利用有机工质形成双循环,吸收排放的废热水的热能,将有机工质加热成汽液两相,直接进入螺杆膨胀动力机或汽轮机,驱动发电机进行发电。
从技术角度分析,高炉冲渣水发电已完全可行,国内也有多家钢铁企业对此项目进行了前期论证,目前尚未有实际应用实例,但随着企业对节能减排工作的日益重视以及该项技术相关细节的进一步完善,它的发展应用将只是一个时间的问题。