第二章 供应商与顾客关系管理
客户关系管理维护办法
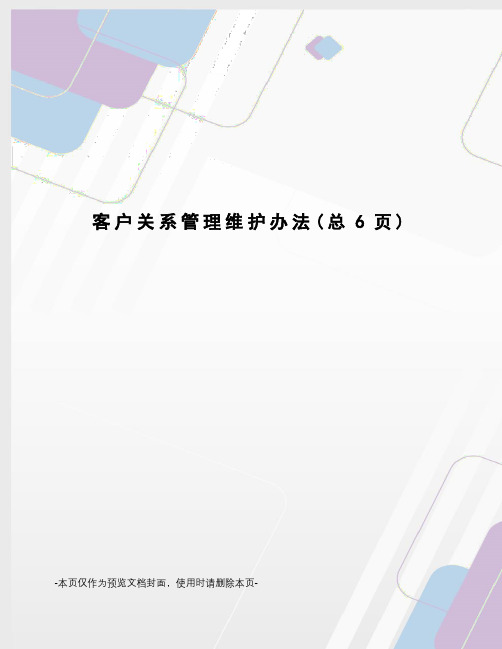
客户关系管理维护办法(总6页) -本页仅作为预览文档封面,使用时请删除本页-《客户关系管理办法》(试行)为加强公司顾客关系管理工作,提高顾客满意度,不断拓展客户群,促进公司更好更快的实现西部一流现代化企业的宏伟目标,特制定本办法。
第一章职责第一条经营部总体负责客户关系的建立、维护、投诉等管理工作。
第二条工程部牵头组织顾客关系测评工作;收集、整理顾客满意度信息,制定顾客关系测评报告;督促公司、二级单位及项目部实施顾客满意度调查、处理顾客投诉及改进顾客关系管理工作。
第三条公司、二级单位及项目部负责实施顾客满意度调查、处理顾客投诉、改进顾客关系管理工作。
第二章顾客关系的建立及维护第四条客户基础信息的建立维护:利用国土、规划等政府部门的公开信息、老客户推荐、公司员工及社会中介推荐信息,尽可能搜集更多的客户资料,建立顾客资料库,随时更新资料库,以确保资料库的精确性和完整性。
第五条建立客户群的分类与管理:按战略客户、重点客户、一般客户、潜在客户对客户群进行分类管理。
1、战略客户:合作过三次以上(含三次),有后续发展项目,客户公司基本面良好,双方有继续合作意愿的企业;或签署了战略合作协议的企业;或其他对企业阶段发展目标有重大影响的客户。
对于战略客户,重点关注合作模式、公司资源分配、质量、价格及提供服务;采取不定期高层互访、专题协商小组、座谈会、顾客满意度调查表、定期回访、客户联谊活动、节日问候等方式了解客户需求和期望,尽可能提供满足战略客户需求的服务。
2、重点客户:合作过程顺畅,有后续发展项目,客户公司基本面良好,双方有继续合作意愿的企业。
对于重点客户,重点关注合作模式、质量、价格及异议处理;采取不定期部门互访、座谈会、电话沟通、顾客满意度调查表、节日问候等方式了解客户需求和期望,尽可能提供满足重点客户需求的服务。
3、一般(普通)客户:合作双方关系良好,但客户后续项目不明的企业。
对于一般客户,重点关注价格、质量、工期及异议处理;采取不定期部门互访、电话沟通、顾客满意度调查表、节日问候等方式了解客户需求和期望,尽可能提供满足客户需求的服务。
第二章供应商与顾客关系管理练习题

第二章供应商与顾客关系管理习题及答案一、单项选择题1、供应链(Supply Chain),有时被称为价值链或需求链(Demand Chain),包括()、供应商、过程、产品以及对向最终顾客交付产品和服务有影响的各种资源。
A 生产B 顾客C 质量D 检验2、供应链管理通过计划、购买、制造、移动和销售,来产生两方面效应:降低成本和()。
A 协调关系B 减少浪费C 增加价值D 提高市场占有率3、顾客满意是顾客对其要求已被满足的程度的感受。
如果可感知效果与顾客期望相匹配,顾客就会()。
A 满意B 高度满意C 抱怨D 忠诚4、对供应商的奖惩包括两种类型。
其一是因()的划分而产生的奖惩;其二是根据业绩考核而产生的奖惩。
A 价格B 服务水平C 质量责任D 订单5、对于供应商定点个数为2的情况,如两家供应商分别为B、C类,可采取的管理对策为在督促供应商提高质量的同时,()。
A 处罚C类供应商B 处罚这这两家供应商C 寻求优秀供应商D 淘汰这两家供应商二、多项选择题6、有效控制(),有助于成功推行供应链管理。
A 关注顾客B 先进信息技术的应用C 绩效定量管理D 精简采购部门7、合作伙伴关系模式是一种互利共赢的关系,有()特征。
A 制造商同时向多家供应商购货,通过供应商之间的竞争获得价格好处;B 制造商与供应商的信息交流少;C 供应商参与制造商的早期新产品开发;D 长期的稳定的紧密合作取代短期的合同8、对供应商进行调查的内容应包括()。
A 纳税记录B 过程能力指数C 体系认证情况D 主要顾客及其反馈信息9、同一产品的供应商个数应根据()确定。
A 产品重要程度B 市场供应状况C 附近供应商的数量D 供应商的可靠程度10、同一个配套件,进厂检验时合格,出厂检查时却发现不合格。
这有可能是因为()。
A 环境或其他意外因素的影响导致了产品的不合格B 检验人员责任心差C 该配套件与其他配件之间的不协调D 产品设计有缺陷11、企业与供应商的契约可包含多个层次的内容,如()等。
供应链管理 第二章

确使用的软件工具这一点没有一个正确的认识,人们往往过分强调了 其功能。MRP被描述成了一个运行公司的完全的和独一无二的系统, 而不是整个系统的一部分。三是MRP如何与JIT相互作用。 闭环MRP 的优点: 1.主生产计划来源于企业的生产经营计划与市场需求(如合同、订单 等)。 2.主生产计划与物料需求计划的运行(或执行)伴随着能力与负荷的 运行,从而保证计划是可靠的。3.采购与生产加工的作业计划与执行 是物流的加工变化过程,同时又是控制能力的投入与产出过程。 4.能 力的执行情况最终反馈到计划制定层,整个过程是能力的不断执行与 调整的过程。
6个月~1年
1天~2周
功能性产品一般用于满足用户的基本需求,变 化很少,具有稳定的、可预测的需求和较长的 寿命周期,但它们的边际利润较低。为了避免 低边际利润,许多企业在式样或技术上革新以 寻求消费者的购买,从而获得高的边际利润, 这种革新性产品的需求一般不可预测,寿命周 期也较短。正因为这两种产品的不同,才需要 有不同类型的供应链去满足不同的管理需要。
5~10 20 1~2
40~100 10~40
20~60
产品多样性 季末降价率(%低) (每一目录0 10到20个1)0~25 高(每一目录上千)
按订单生产的提前期
6个月~1年
1天~2周
预测的平均边际错误率(%)
10
40~100
平均缺货率(%)
1~2
10~40
季末降价率(%)
0
10~25
按订单生产的提前期
在过去的十多年里,企业面临的竞争环境发生了巨大 的变化。许多企业(特别是汽车行业企业)都应用 JIT方法进行管理,这样一种方法要求企业加快对用 户变化需求的反应速度,同时加强与合作伙伴的合作。 全球竞争中先进制造技术的发展要求企业将自身业务 与合作伙伴业务集成在一起,缩短相互之间的距离, 站在整个供应链的观点考虑增值,所以许多成功的企 业都将与合作伙伴的附属关系转向建立联盟或战略合 作关系。
刘小明-中级质量工程师课程大纲

◆熟悉和掌握统计过程控制概述、控制图的基本原理、分析用控制图与控制用控制图、常规控制图的做法及其应用、过程能力与过程能力指数、过程控制的实施六方面内容。
习题讲解
第二章常用统计技术
第一节方差分析
一、几个概念
二、单因子方差分析
三、重复数不等的情况
第二节回归分析
一、散布图
二、相关系数
三、一元线性回归方程
四、可化为一元线性回归的曲线回归
第三节试验设计
一、试验设计的基本概念与正交表
二、无交互作用的正交试验设计与数据分析
三、有交互作用的正交试验设计与数据分析
习题讲解
习题讲解
第五章计量基础
第一节基本概念
一、计量的内容、分类和特点
二、计量的法律法规
三、剂量的溯源、校准和检定
第二节计量单位
一、概述
二、法定计量单位的构成
三、法定计量单位的基本使用方法
第三节测量仪器
一、概述
二、测量仪器的计量特性
三、测量仪器的选用原则
第四节测量结果与测量准确度
一、测量结果、测量误差及测量结果的修正
六、维修性设计
第三节可靠性试验
一、环境应力筛选试验
二、可靠性增长试验
三、加速寿命试验
四、可靠性测定试验
五、可靠性鉴定试验
六、可靠性验收试验
第四节可信性管理
一、可信性管理应遵循的基本原则
二、管理的基本职能、对象和方法
三、建立故障报告、分析和纠正措施系统(FRACAS)
质量专业综合知识(中级) _第二章 第四节 顾客关系管理_2013年版
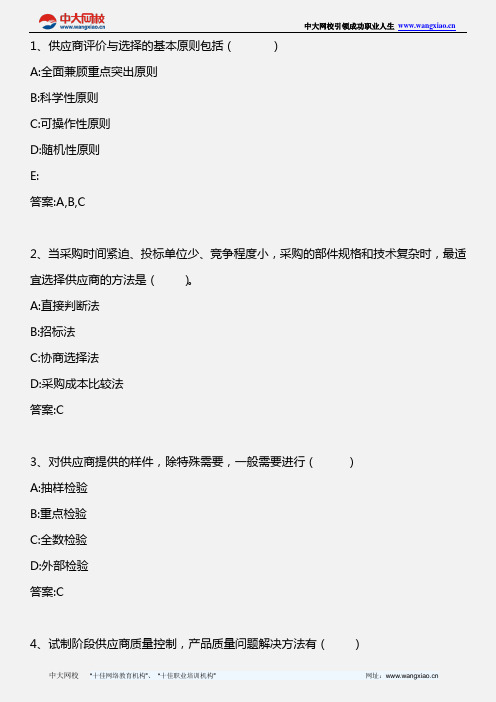
中大网校引领成功职业人生
中大网校 “十佳网络教育机构”、 “十佳职业培训机构” 网址: 1、供应商评价与选择的基本原则包括( )
A:全面兼顾重点突出原则
B:科学性原则
C:可操作性原则
D:随机性原则
E:
答案:A,B,C
2、当采购时间紧迫、投标单位少、竞争程度小,采购的部件规格和技术复杂时,最适宜选择供应商的方法是( )。
A:直接判断法
B:招标法
C:协商选择法
D:采购成本比较法
答案:C
3、对供应商提供的样件,除特殊需要,一般需要进行( )
A:抽样检验
B:重点检验
C:全数检验
D:外部检验
答案:C
4、试制阶段供应商质量控制,产品质量问题解决方法有( )。
品质专业知识及专业术语

质量(品质管理)专业综合知识第一章质量管理概论第一节质量的基本知识第二节质量管理的基本知识第三节方针目标管理第四节质量经济性分析第五节质量与标准化第六节产品质量法和职业道德规范第二章供应商与顾客关系管理第一节供应商管理第二节顾客满意第三节顾客关系管理第三章质量管理体系第一节质量管理体系的基本知识第二节质量管理体系的基本要求第三节质量管理体系的建立与实施第四节质量管理体系审核第四章质量检验第一节质量检验概述第二节质量检验机构第三节质量检验计划第四节质量特性分析和不合格品控制第五章计量基础第一节基本概念第二节计量单第三节测量仪器第四节测量结果第五节测量误差和测量不确定度第六节测量控制体系生产异常是指造成制造部门停工或生产进度延迟的情形,包括计划异常、物料异常、设备异常、品质异常、产品异常、水电异常等等。
品质异常是指在品质方面出现了不合标准或规范不能满足顾客要求的现象。
包括产品品质异常和制程异常或系统异常。
生产异常包括品质异常,生产异常的含义范围更大。
品质人员名称类QC q uality con trol 品质管理人员OQC outp ut quality control 最终出货品质管制人员IQC incomi ng quality control 进料品质管制人员QA quality a ssurance 质量保证人员OQAoutput qua lity assur ance 出货质量保证人员品质保证类FAI first article i nspection新品首件检查FAA first art icle assur ance 首件确认OOBA out o f box audi t 开箱检查FME A failuremodel effe ctivenessanalysis 失效模式分析8D 8 disciplin es 8项回复内容FQC运作类AQL Acceptabl e QualityLevel 运作类允收品质水准S/SSample siz e 抽样检验样本大小ACC Accep t 允收REE R eject 拒收C R Critical极严重的MAJMajor 主要的MIN Minor轻微的P/N Pa rt Number料号L/N Lo t Number 批号AOD Acce pt On Devi ation 允许偏差FPIR Firs t Piece In spection R eport 首件检查报告PPM Per cent Per M illion 百万分之一制程统计品管专类SPC Stat istical Pr ocess Cont rol 统计制程管制SQC Stati stical Qua lity Contr ol 统计品质管制N Number 样品数其它品质术语类QCC Quali ty Control Circle 品质圈QIT Qual ity Improv ement Team品质改善小组PD CA Plan Do Check Act ion 计划执行检查总结MRBMaterial R eject Bill退货单QT Qu ality Targ et 品质目标7Q CTools 7 Q uality Con troll Tool s 品管七大手法通用之件类ECN E ngineering Change No tes 工程变更通知(供应商)ECOEngineerin g Change O rder 工程改动要求(客户)PCNProcess Ch ange Notic e 工序改动通知P MP Product Managemen t Plan 生产管制计划SIP Sp ecificatio n In Proce ss 制程检验规格SOP Standa rd Operati on Procedu re 制造作业规范IS Inspect ion Specif ication 成品检验规范BOM B ill Of Mat erial 物料清单PS Packag e Specific ation 包装规范SPEC Spec ification规格EVT En gineeringValidation Test 工程验证测试DVTDesign Va lidation T est 设计验证测试PV T Product ion Valida tion Test生产验证测试P/R Pil ot Run 试跑MP Mass Produ ction 大量生产QVL Quali ty VendorList 合格厂商清单WIP Wor k in proce ss 半成品(工作进行中)部类P MC Produc tion & Mat erial Cont rol 生产和物料控制PPC Prod uction Pla n Control生产计划控制MCMaterial C ontrol 物料控制ME manuf acture Eng ineering 制造工程部PE Pr oject Engi neering 产品工程部A/C Ac countant D ept 会计部P/A Personal & Adminis tration 人事行政部DC Doc ument Cent er 资料中心QE Quality E ngineering品质工程(部)Q A QualityAssurance品质保证(处)QC Quality C ontrol 品质管制(课)PD Pr oduct Depa rtment 生产部IE Indust rial Engin eering 工业工程R&D Rese arch & Des ign 设计开发部A Assembly组装P Packing 包装生产类PCS Pi eces 个(根,块等)CTN Car ton 卡通箱PA L Pallet/s kid 栈板POPurchasing Order 采购订单MO Manuf acture Ord er 生产单D/C Date Code生产日期码ID/C Identifi cation Cod e (供应商)识别码L/N Lot N umber 批号P/N Part Nu mber 料号其它OEM Origi nal Equipm ent Manufa cture 原设备制造PCE Pers onal Compu ter Enclos ure 个人电脑外设PC Person al Compute r 个人电脑CPU Central P rocessingUnit 中央处理器SECC SECC` 电解片SGCC SGCC 热浸镀锌材料NHK Nor th of Hong kong 中国香港PRC People's Republi c of China中国大陆U.S.A the Uni ted States of Americ a 美国A.S.A.P As Soon As Possib le 尽可能快的E-MAIL Elec trical-Mai l 电子邮件N/A Not Appli cable 不适用QTY Quanti ty 数量VS 以及REV Rev ision 版本J IT Just In Time 零库存I/O Input/Output 输入/输出OK Ok 好NG Not Go od 不行,不合格C=0 Critic al=0 极严重不允许ESD Elec try-static Discharge静电排放5S 希腊语整理,整顿,清扫,清洁,教养AT IN Attenti on 知会CC C arbon Copy副本复印相关人员APP Approv e 核准,认可,承认CHK Check确认AM Ant e Meridian上午PM Pos t Meridian下午CD Com pact Disk光碟CD-ROMCompact Di sk Read-On ly Memory只读光碟FDD F loppy Disk Drive 软碟机HDD HardDisk Drive碟碟机REF R eference 仅供参考CONN C onnector 连接器CAV Cav ity 模穴CAD ComputerAid Design计算机辅助设计A SS'Y Assem bly 装配,组装MAT'S Mate rial 材料IC Integrate d Circuit集成电路T/P T rue Positi on 真位度TYP Type 类型W DR WeeklyDelivery R equirement周出货需求C/T Cycle Tim e 制程周期L/T Lead Time前置时间(生产前准备时间)S/T S tandard Ti me 标准时间P/M ProductMarket 产品市场3C Compu ter, Commu nication,Consumer e lectronics’消费性电子5W IH When, W here, Who, What, Why, How to5M Man, Mac hine, Mate rial, Meth od, Measur ement 人,机,料,法,测量S QA Strateg y QualityAssurance策略品质保证DQA Design Qu ality Assu rance 设计品质保证MQA Man ufacture Q uality Ass urance 制造品质保证SSQA S ales and s ervice Qua lity Assur ance 销售及服务品质保证LRR L ot RejectRate 批退率B S Brain st orming 脑力激荡EMI Elec tronic Mag netion Ins pect 高磁测试FMI Freque ncy Modula tim Inspec t 高频测试SPS Switching power sup ply 电源箱DT Desk Top卧式(机箱)MTMini-Tower立式(机箱)DV D Digit al Voice D isk 数位视讯影碟& 多功能数位碟片VCD VoiceCompact Di sk 影音光碟L CD LiquidCrystal Di splay 液晶显示器ABIO S Achanced Basic input/output system 先进的基本输入/输出系统CMOS Comp lemeruaryMetoll Oxi de Semicon ductor 互补金属氧化物半导体PD A Personal Digital A ssistant 个人数字助理IC I ntegratedCircuit集成电路ISA Ind ustry Stan dard Archi tecture 工业标准体制结构MCA Micro Cha nnel Archi tecture 微通道结构EISAExtended I ndustry St andard Arc hitecture扩充的工业标准结构SIMM Singl e in-linememory mod ule 单项导通汇流组件DIMM Du al in-line Memory Mo dule 双项导通汇流组件LED Li ght-Emitti ng Diode 发光二级管FMEAFailure Mo de Effecti veness 失效模式分析W/H Wi re Harness金属线绪束集组件F/C Flat C aller 排线P CB Printed Circuit B oard 印刷电路板CAR Corre ction Acti on Report改善报告NG No t Good 不良WPR Weekly DeliveryRequiremen t 周出货要求PP M Parts Pe r Million百万分之一TPMTotal Prod uction Mai ntenance 全面生产保养MRPMaterial R equirement Planning物料需计划OSOp eration Sy stem 作业系统TBA To BeDesign 待定,定缺EMI Ele ctrical-Mu sic Indust ry 电子音乐工业RFI Read F requency I nput 读频输入ECRS eliminateCombineRearrang e Simple取消合并重排简化DIR FT Doif right t he first t ime 第一次就把事情做好SWOT Stren gth weakne ss Opportu nity Threa t 优势弱势机会危机1|评论中英文对照英文缩写中文名称英文全名6 σ六个希格玛Six Sig ma8D 8D改善程序8 Disc iplinesA BC 作业制成本制度Activity-Based Cost ingANOVA变异数分析Ana lysis of V arianceA QL 允收品质成本Acceptable Quality L evelBB 黑带Black Be ltsBSC 平衡计分卡Balan ced Scoreb oardBTF计划生产Build To Foreca stBTO 订单生产Build T o OrderC a 制程准确度Pr ocess Capa bility ofAccuracy CAD 电脑辅助设计系统Compute r Aided De sign Syste mCAI 电脑辅助检验Comput er Aided I nspectionCAT 电脑辅助测试Computer Aided Tes tingCI 信赖区间Confid ence Inter valCL 中心线Center L ineCp 制程精密度Proces s Capabili ty of Prec isionCpk制程能力Proc ess Capabi lityCPM要径法Critic al Path Me thodCPM每一百万个使用者会有几次抱怨Compl aint per M illionCR M 客户关系管理C ustomer Re lationship Managemen tCRP 产能需求规划Capaci ty Require ments Plan ningCS 顾客满意度Custo mer Satisf actionCT O 客制化生产Co nfiguratio n To OrderCTQ 关键品质特性Critica l to Quali tyDFM 为制造设计Desi gn for Man ufacture DFMEA 设计失效模式分析Des ign FMEA DFSS 六个希格玛设计Desig n for sixsigmaDMA IC 定义衡量分析改善管制Define Mea sure Analy ze Improve Control DOE 实验设计Design of Experimen tDPM 每百万单位的缺点数D efects per million DPMO 每百万个机会的缺点数De fects permillion op portunitie s DPU 单位缺点数Defec ts per uni tDR 设计审查DesignReviewDS S 决策支援系统DecisionSupport Sy stemDVT设计验证Des ign Verifi cation Tes tingEC 设计变更/工程变更Engineeri ng ChangeEDI 电子资料交换Electr onic DateInterchang eEMC 电磁相容Electr ic Magneti c Capabili tyEOQ 基本经济订购量Ec onomic Ord er Quantit yEPC 工程制程控制Engi neering Pr ocess Cont rolERP 企业资源规划En terprise R esource Pl anningES工程规格En gineeringSpecificat ionEV 仪器系统变异Equ ipment Var iationFM EA 故障模式效应分析Failur e Mode and Effect An alysisFM ECA 故障模式.效应与关键性分析Failure Mo de, Effect, andCrit icality An alysisFM S 弹性制造系统FlexibleManufactur e System FQC 成品品质管制Finishor Final Q uality Con trolFTA缺陷树分析Fa ult Tree A nalysisF TY 初检通过率First Tim e YieldG B 绿带Gre en Belts GR&R 仪器再现性及再生性Gau ge Repeata bility & R eproducibi lity IPQC制程品质管制In-Process Quality C ontrolIQ C 进料品质管制IncomingQuality Co ntrolISA R 首批样品认可Initial S ample Appr oval Reque stISO 国际标准组织Int ernational Organizat ion for St andardizat ion JIT 即时管理Just In Time KM 知识管理KnowledgeManagementKPIV 关键输入变数KeyProcess In put Variab lesKPOV关键输出变数K ey Process Output Va riablesK URT 峰度K urtosisL CL 管制下限Lower Cont rol LimitLPCL 前置管制下限Lower Per-contr ol Limit LSL 规格下限Lower Spe cification LimitLT PD 不良率L ot Toleran ce Percent DefectiveMES 制造执行系统Manuf acturing E xecution S ystemMIL STD 美军标准Military StandardMO 制令M anufacture OrderMP S 主生产排程Master Pro duction Sc heduleMR O 请修(购)单Maintenan ce RepairOperationMRP 物料需求规划Materi al require planningMRP 物料需求规划Materi al Require ment Plann ingMRPII制造资源计划Manufactur ing Resour ce Plannin gMSA 量测系统分析Meas urement Sy stems Anal ysisNFCF更改预估量的通知Notice f or Changin g Forecastnp 不良数管制图Number of Defect ivesODM委托设计与制造Original D esign & Ma nufactureOEM 委托代工Original Equipment Manufactu reOPT 最佳生产技术Opt imized Pro duction Te chnology OQC 出货品质管制Outgoin g QualityControlP CL 前置管制中心限Per-con trol Centr al Limit PDCA PDCA管理循环Plan-Do-Check-ActionPF MEA 制程失效模式分析Proce ss FMEAP O 订单Pur chase Orde rPp 制程绩效指数Proce ss Perform ance IndexPPAP 生产零件承认程序Pr oduction P art Approv al ProcessPpk 制程绩效指数PPM每百万不良率P areto Anal ysisQA 品质保证Qual ity Assura nceQC 品质管制Quali ty ControlQC PlanQC工程表Qua lity Contr ol PlanQ CC 品管圈Q uality Con trol Circl eQE 品质工程Quality Engineeri ngQFD 品质机能展开Qua lity Funct ion Deploy mentQLF品质损失函数Q uality Los s FunctionQMA 品质成熟度分析Qual ity Maturi ty Analysi sRMA 退货验收Return ed Materia l ApprovalROP 再订购点Re-Orde r PointR TY 直通率R olled Thro ughout Yie ldSCM 供应链管理Supp ly Chain M anagementSFC 现场监控Shop Flo or ControlSL 规格界线Specific ation Limi tsSO 订单Sales Ord erSOP 标准作业程序Sta ndard Oper ation Proc edureSOR特殊订单需求Special Or der Reques tSPC 统计制程管制Stat istical Pr ocess Cont rolSQC 统计品质管制St atisticalQuality Co ntrolSTD EV 标准差St andard Dev iationTO C 限制理论T heory of C onstraintsTPM 全面生产管理Total Productio n Manageme ntTQC 全面品质管制Tot al Quality Control TQM 全面品质管理Total Q uality Man agementU CL 管制上限Upper Cont rol LimitUPCL 前置管制上限Upper Per-contr ol Limit USL 规格上限Upper Spe cification LimitVA R 变异数Va rianceWI P 在制品Wo rk In Proc essXbar-R 平均数- 全距管制图Avera ge-Range C ontrol Cha rtXbar-s平均数- 标准差管制图Avera ge-Standar d Deviatio n ControlChart ZD零缺点Zero Defectσ, s 标准差Standard d eviation σ2, S2 变异数Varianc e。
第二章 供应商与顾客关系管理

第二章供应商与顾客关系管理第二章供应商与顾客关系管理第一节供应商管理一、供应链管理概述(一)供应商与供应链gb/t19000―2000标准中表述的供应链为“供方→组织→顾客”,其中供方是指,“提供产品的组织或个人”。
本章中将供方称为供应商。
他们可以是制造商、批发商、产品的零售商或商贩,也可以是服务或信息的提供者。
在传统的管理模式中,组织在提供原材料、半成品、零部件或服务时,总是采用投资、自建、投资控股或合并的方式。
在稳定的市场环境下,组织以“大而全”和“小而全”的形式发展,真正掌握主动权,增加利润,控制每个业务阶段的全过程。
然而,在当今高科技发展的今天,客户的需求正在发生变化,市场竞争也越来越激烈。
传统的管理模式已经显示出越来越多的弱点,为了避免投资负担过大、建设周期长的风险,以及来自不同领域的竞争,可能会遭受损失。
在外部资源即供应商资源的帮助下,组织将遵循优势互补的原则,集中不同的核心竞争力,以达到快速响应市场需求的目的。
因此,越来越多的组织放弃了传统的管理模式,形成了共同利益联盟,从而形成了从供应商到组织、分销商、零售商和最终客户的全过程“链条”。
由于“链”中相邻节点的不同组织通过供需关系依次相连,形成了供应链。
供应链(supplychain),有时被称为价值链或需求链(demandchain),包括顾客、供应商、过程、产品以及对向最终顾客交付产品和服务有影响的各种资源。
供应链强调的是公司之间的过程与关系。
供应链管理(supplychainmanagement)就是指从原材料采购到成品分销给顾客的整个过程中对产品和服务的管理,它是通过前馈的信息流和反馈的物料流和信息流,将供应商、制造商、分销商、零售商、直到最终顾客连成一个整体的管理模式,强调的是协调公司间、甚至大的集团公司之间的活动以求产生双赢效果。
供应链管理产生两种效果:通过计划、采购、制造、移动和销售活动降低成本和增加价值。
具体而言,有效的供应链管理可以为企业带来以下好处:(1)改善供应链内的战略、运营和财务绩效。
中级质量工程师 质量专业综合知识与质量专业理论与实务 知识要点

第一章质量管理理论1质量:一组固有特性满足要求的程度;要求“明示的、通常隐含的、必须履行的(法律法规或强制性标准要求的)、要求可以由相关方提出”;2质量的内涵:经济性、广义性(产品、过程、体系)、时效性、相对性3产品的四种类别:服务、软件、硬件、流程性材料;4质量特性指产品、过程或体系与要求有关的固有特性。
包括“性能、适用性(使用要求与满足程度)、可信性(可靠性、维修性、维修保障性)”、安全性、环保、经济、美学。
服务特性“可靠性、相应性、保证性、移情性、有形性”;软件质量特性“功能性、可靠性、易适用性、效率、可维护性、可移植性”。
质量的适用性是建立在质量特性基础上5质量概念的发展:符合性质量、适用性质量、广义性质量6管理职能:计划、组织、领导、控制;计划是前提/组织是保证/领导是关键/控制是手段. 7管理技能:技术技能/人际技能/概念技能;作业/战术/战略-基层(技术、人际)、中层(人际、概念)、高层(概念)8质量管理:质量策划、质量控制、质量保证、质量改进。
质量目标:组织在质量方面追求的目的9质量方针:最高管理者发布的质量宗旨和方向;包括“供方的组织目标和顾客的期望需求”控制图-休哈顿;PDCA-戴明环;因果图-石川馨;10戴明观点:1.效率低下的主因是公司的管理系统而非员工;2.停止依靠检验来保证质量;3.结束依靠价格选供应商;4.消除不同部门之间的壁垒/5.持续改进/6建立改进的长期目标11朱兰三部曲:质量策划、质量控制、质量改进12石川馨:认为日本的TQC包括“1.所有部门参与质量管理;2.全员参加质量管理;3.以质量为中心,同时推进成本管理”。
内容“1.质量第一2.面向消费者3.下道工序是顾客4.用数据说话5.尊重人的经营6.技能管理”13全面质量管理:1.以全面质量为中心2.建立质量体系是质量管理的主要任务3.将质量概念扩充为全部管理目标。
方针目标由总方针、目标、措施构成14方针目标管理:1.强调系统管理2.强调重点管理3.注重措施管理4.注重自我管理。
- 1、下载文档前请自行甄别文档内容的完整性,平台不提供额外的编辑、内容补充、找答案等附加服务。
- 2、"仅部分预览"的文档,不可在线预览部分如存在完整性等问题,可反馈申请退款(可完整预览的文档不适用该条件!)。
- 3、如文档侵犯您的权益,请联系客服反馈,我们会尽快为您处理(人工客服工作时间:9:00-18:30)。
第二章供应商与顾客关系管理第一节供应商管理一、供应链管理概述(一)供应商与供应链GB/T 19000—2000标准中表述的供应链为“供方→组织→顾客”,其中供方是指,“提供产品的组织或个人”。
本章中将供方称为供应商。
他们可以是制造商、批发商、产品的零售商或商贩,也可以是服务或信息的提供者。
在传统的管理模式中,组织对为其提供原材料、半成品、零部件或劳务等环节,一直采取投资自建、投资控股或兼并的方式。
在市场环境稳定的条件下,组织以“大而全”、“小而全”的形式发展,确实可在各业务阶段掌握主动、增加利润并控制全过程。
但是,在高科技发展的今天,顾客的需求不断变化,市场竞争日益激烈。
传统的管理模式已经显示出越来越多的薄弱之处,为避免承受过重的投资负担和过长的建设周期带来的风险以及来自不同领域的竞争而可能受到损失。
组织将借助于外界的资源,即供应商的资源,遵循优势互补的原则,集中不同的核心能力,达到快速响应市场需求的目的。
为此,越来越多的组织放弃了传统的管理模式,结成利益共同联盟,从而形成了一条从供应商到组织再到分销商、零售商直至最终顾客,贯穿于全过程的“链”。
由于“链”上相邻节点的不同组织以供需关系,依次连接起来,便形成了供应链。
供应链(Supply Chain),有时被称为价值链或需求链(Demand Chain),包括顾客、供应商、过程、产品以及对向最终顾客交付产品和服务有影响的各种资源。
供应链强调的是公司之间的过程与关系。
供应链管理(supply Chain Management)就是指从原材料采购到成品分销给顾客的整个过程中对产品和服务的管理,它是通过前馈的信息流和反馈的物料流和信息流,将供应商、制造商、分销商、零售商、直到最终顾客连成一个整体的管理模式,强调的是协调公司间、甚至大的集团公司之间的活动以求产生双赢效果。
供应链管理通过计划、购买、制造、移动和销售等活动,来产生两方面效应:降低成本和增加价值。
具体来说,有效的供应链管理可为企业带来以下利益:(1)在供应链范围内改进战略、作业及财务绩效。
(2)降低成本,有效管理周转资本(Working capital)。
(3)原材料、在制品和制成品库存的有效管理。
(4)降低交易成本,提高供应链成员间的交易效率。
(5)创造顾客化产品和服务,提供一揽子解决方案,为顾客创造价值。
(6)增强平衡供需的能力。
当前,供应链管理的成功案例难以计数,其中较为著名的供应链管理优秀企业有宝洁、沃尔玛、克莱斯勒、戴尔、IBM、3M、施乐、以及我国的海尔、小天鹅等等。
成功企业的示范作用和企业自身生存的需要,促使企业越来越重视供应链管理,并根据顾客需求、全球化、竞争、信息与通讯、政策和环境的不断变化,积极寻求供应链变革与再造,以提高企业的竞争能力。
(二)供应链管理的发展阶段近几十年来,供应链管理得到了前所未有的重视,发展十分迅速。
根据供应链管理覆盖的范围可将其分为三个阶段。
(1)传统物流管理阶段(Physical distribution Management):集合了运输和仓储两大职能。
(2)现代物流阶段(Logistics):增加了制造、采购和订货管理职能,辅以EDI、世界范围的通信和高性能计算机的应用。
(3)同步一体化供应链阶段(Synchro Integrated Supply Chain):在原有供应链的两端分别增加了供应商和顾客,供应链成为七项功能的集合体,一体化意味着在整个过程中整合许多职能以实现共同目标,其复杂性大大增加,对此,必须依赖于电子数据、电子资金支付、宽频通信和计算机决策支持系统来规划和执行。
一体化供应链管理涵盖了信息流、物流和资金流的管理,需要更多职能间的协作,如产品开发、营销和顾客服务。
产品设计者作为供应链团队的一部分,依据顾客要求设计出易于制造、安装和服务的产品;预测和订货信息将被送往供应链的所有成员以期快速准确的反应;制造人员将成为安装团队的一部分以缩短安装时间;物流接受触发无发票付款;信息传递由原来的逐级传递变为同步传递,减少了信息扭曲和传递时间,从而可以大大缩短交付提前期。
如德国大众向其供应商发出电子订单,其内部供应厂家和合同供应商同样根据日生产计划向他们的供应商发出订单,要求准时到达。
大众公司将交付周期从几个周减至几天。
(三)供应链管理的成功因素要成功推行供应链管理,仅仅依靠大量投资是不够的,重要的是有效控制以下关键因素。
(1)关注顾客。
始终把最终顾客的需要和期望视为最重要的,并尽力识别和理解最终顾客的需要和期望,作为决策的主要依据。
如一家医药公司,改变了以往根据销售量和利润向销售代表发放奖金的办法,而是评价其顾客是否达到了目标。
这样销售代表致力于帮助顾客实现其战略目标,而不像以前那样不管顾客是否需要而一味推销产品。
(2)先进信息技术的应用。
开发先进的信息管理系统,保证数据与信息在整个供应链内各方之间交流通畅;计算机辅助决策支持系统利用供应链中复杂的信息帮助管理者更好地进行决策并将之在供应链伙伴之间迅速传递。
(3)绩效定量管理。
运用时间和成本等关键衡量指标,在定量的基础上进行绩效评价。
(4)跨职能团队,来自相关职能部门的团队成员紧密协作可以消除往常的组织界限并发现有益于整个供应链的改进。
(5)关注人力资源和动态组织,消除人与人、部门与部门的框限,实现整个供应链的协作。
如雷德公司和施乐公司的密切合作。
雷德公司不仅为施乐公司运送复印机,雷德的司机还负责安装设备并培训顾客。
(6)对变化的环境做出快速反应,设计柔性供应链。
(四)提高供应链管理绩效的途径尽管有许多公司投入大量时间与资金以期提高供应链能力,但只有少部分公司认为其供应链业绩好于行业平均水平。
据估计美国食品工业由于供应链伙伴间协作不佳每年带来损失300亿美元。
这是因为:许多公司没有正式的供应链开发战略;缺乏支持供应链一体化的管理环境;缺乏信任,功能导向而不是过程导向;缺乏有效管理供应链中物流、信息流和资金流的工具。
战略规划和财务分析是当前供应链管理中最缺乏的技巧。
这样,公司采取了孤立的增值改进措施,但无法取得突破性的效果。
许多公司提高供应链绩效聚焦于成本降低上而非增加价值。
提高供应链绩效一是进一步降低成本,二是创造更多的价值。
为达此目的,有以下途径:(1)减少供应商数量。
企业以往的做法是对同一零部件采用多家供应商,以便对供应商施加压力,获得较低的进价。
企业的收益是以其供应商的损失为代价的。
目前,这一情形已开始改变。
企业通过减少供应商数量,扩大供应商的供货量,从而使供应商获得规模效益,企业和供应商都可以从低成本中受益。
如英国石油开发公司已将供应商数量从20000个减至3600个。
(2)精简顾客。
与选定的顾客建立伙伴关系。
爱考恩斯公司是一家家具制造公司,在3年内将在法国的销售量增加2倍,同时将零售商的数量减少1/3。
爱考恩斯在每个地区选择其所需的客户。
通过制订合作协议,爱考恩斯和其零售商共同开展培训和提供特定服务,其经营哲学是共同设计和管理零售商店面里的最赚钱的20平方米。
为了更加了解顾客的需要,纽约按钮有限公司将顾客减少到2400个,减少了31%,根据顾客的需要来调整业务。
例如顾客不仅被问及他们希望发运什么,而且包括如何发运。
有时,纽约按钮公司管理顾客的库存,用可回收的包装箱发运,尽快地变革来适应顾客。
(3)在客户办公室派驻代表,以全面了解客户的运作体系,驻厂代表向自己的公司发出订单,并为客户计划所需供应的材料。
美国一家著名音响制造公司——伯勒公司和他的供应商已采用这种方法。
(4)与供应商和顾客共享详细的信息。
如售货点信息可电子传输到制造商订单处理系统并与运输公司共享。
这使交叉码头成为可能,而货物无须进入仓库。
再如EDI为顾客、供应商和第三方物流公司(3PLs)节约了大量费用。
在3PLs的控制下,通过EDI交易系统自动启动付款,这样付款部门和收款部门就没有存在的必要了。
(5)供应商的早期参与,在新产品开发阶段,供应商的参与可显著缩短开发时间,节省资源和费用。
在日本,供应商在汽车设计中早期参与,取得了很好的效果,其工程改动费用比美国同行要低2/3。
(6)选择一个供应商负责协调。
当需要多个供应商提供同一项服务时,选择一个牵头的供应商来协调整个物流。
当埃克森化学公司将其在意大利互麦工厂的周期时间由天减少到小时,取消制成品库存时,卡车的准时到达成为必不可少的。
在这个行业中,半数可控制的费用是配送。
埃克森选择了单一的供应商——耐德劳德公司,由其协调一个供应商小组,这个小组成员由耐德劳德公司和其他四家运输服务公司组成。
显然,在调度卡车到达方面耐德劳德公司要比埃克森强得多,由此节省了129%的配送费用。
(7)制订利益共享计划。
利益共享对供应链各方来讲都是很重要的,只有充分调动供应链各方的积极性才有可能产生协同效应。
如英国石油开发公司,在美国北海岸的一个大型项目中,节省预算30%。
在这个项目中,英国石油开发公司和其主要供应商组成了一个委员会,节省的费用将在英国石油开发公司和其主要供应商之间分摊,总费用越少,大家分摊的收益就越大。
有趣的是,供应商们建议给一个很小的工程公司以较大的节省份额,因为这家小公司出色的设计是该项目远低于预算的关键,这家小公司当年赢利因此增加了好几倍。
(8)通过客户和供应商进行竞争。
创新性公司组建包括其顾客和供应商的团队一同开发独特的竞争优势。
勇于创新的管理者正试图将原来松散的买卖关系转变为紧密协作的关系,甚至一些供应商及其顾客结成组织,以提供单个公司无法提供的产品和服务。
例如:一家汽车分装商是某汽车制造商的某个车型的某分系统的惟一供应商,双方之间的业务量在这家分装商的销售额中占相当重要份额。
在此,这家供应商的经济业绩不单单依靠自身的表现,还依靠其顾客的成功,具体来说,依赖于顾客产品的成功。
反之亦然,汽车制造商的成功同样依赖于供应商的设计与开发工作。
这种供应链上各公司间的高度依赖要求必须从战略的角度选择供应链。
设计供应链组合的一个关键因素是要考虑各公司的独特竞争优势。
如品牌,特殊的制造能力或高超的组织能力等。
(9)竞争对手合作。
如美国两大汽车公司福特公司和克莱斯勒公司在产品的交付运输方面进行了合作。
在美国的几个地区,由克莱斯勒公司的车队负责运输交付两家公司的产品,提高了卡车的满载率,缩短了产品交付周期,而且降低了成本,可以说双方都从中受益。
目前这两家公司正准备扩大合作的范围。
二、供应商选择在经济全球化不断深化的今天,企业越来越注重于发现和发挥自身的核心能力,对于非核心业务大多采用采购和外包的方式,由供应商提供核心业务以外的作业。
以汽车制造业为例,近20年来世界汽车业巨头基本上剥离了其大部分次要零部件的生产,如表 2.1-1所示。
由此可见,供应商提供零部件的质量在很大程度上直接决定着企业产品的质量和成本,对供应商的选择已经成为企业质量管理的重要部分。