轴承微振磨损
(完整word版)(整理)滚动轴承故障诊断分析章节

滚动轴承故障诊断滚动轴承是应用最为广泛的机械零件质疑,同时,它也是机器中最容易损坏的元件之一。
许多旋转机械的故障都与滚动轴承的状态有关。
据统计,在使用滚动轴承的旋转机械中,大约有30%的机械故障都是由于轴承而引起的。
可见,轴承的好坏对机器工作状态影响极大。
通常,由于轴承的缺陷会导致机器产生振动和噪声,甚至会引起机器的损坏。
而在精密机械中(如精密机床主轴、陀螺等),对轴承的要求就更高,哪怕是在轴承上有微米级的缺陷,都会导致整个机器系统的精度遭到破坏。
最早使用的轴承诊断方法是将听音棒接触轴承部位,依靠听觉来判断轴承有无故障。
这种方法至今仍在使用,不过已经逐步使用电子听诊器来替代听音棒以提高灵敏度。
后来逐步采用各式测振仪器、仪表并利用位移、速度或加速度的均方根值或峰峰值来判断轴承有无故障。
这可以减少对设备检修人员的经验的依赖,但仍然很难发现早期故障。
随着对滚动轴承运动学、动力学的深化研究,对轴承振动信号中频率成分和轴承零件的几何尺寸及缺陷类型的关系有了比较清楚的了解,FFT级数的发展也使得利用频率域分析和检测轴承故障成为一种有效的途径。
也是目前滚动轴承监测诊断的基础。
从发展的历程看,滚动轴承故障检测诊断技术大致经历了以下阶段:1961年,W.F.Stokey完成了轴承圈自由共振频率公式的推导,并发表;1964年,O.G.Gustafsson研究了滚动轴承振动和缺陷、尺寸不均匀及磨损之间的关系,这与目前诊断滚动轴承故障的方法是基本一致的;1969年,H.L.Balderston根据滚动轴承的运动分析得出了滚动轴承的滚动体在内外滚道上的通过频率和滚动体及保持架的旋转频率的计算公式。
至此,有关滚动轴承监测诊断的理论体系已经基本完成;1976年,日本新日铁株式会社研制了MCV-021A机器检测仪,其方法是通过检测低频、中频和高频段轴承的信号特征来判断轴承的工作状态;1976~1983年之间,日本精工公司也积极在滚动轴承检测仪器方面做工作,相继推出了NB系列轴承检测仪,利用1~15kHz范围内的轴承振动信号的有效值(rms)和峰峰值(p-p)来诊断轴承的故障;1980年代至今,以改良频率分析的方法来精密诊断滚动轴承的故障、确定故障位置,一直是精密诊断采取的必备方法,其中包括细化谱分析、倒频谱分析、共振解调技术、包络分析技术等。
滚动轴承的损伤形式

3)滚动体的圆周方向在对称位置上有剥落
4)深沟球轴承滚道的斜向表面产生剥落
5)滚子轴承的滚道和滚动体靠近端部处表面产生剥落
6)受力表面较大面积压光和微观剥落
7)滚道面和滚动体早期出现表面剥落
8)装配后轴承早期出现表面剥落
使滚动体或滚道表面产生剥落坑,并向大片剥落发展,导致轴承失效。
1)空气中水分的凝结,腐蚀ห้องสมุดไป่ตู้介质侵入
2)电流通过产生电火花融化
3)微振,装配不当
表面损伤,丧失精度而不能继续工作
破损
1)冲击载荷过大,装配不当,胶合发展
2)冲击载荷,热处理不当,装配不当,胶合发展
3)对中不良,装配不当,润滑不良,异常载荷,转速过快,异物进入
1)外环或内环产生裂纹
2)滚动体产生裂纹
3)保持架断裂
损伤形式
损伤原因
损伤特征
损伤结果
疲劳
1)轴向载荷过大
2)轴向载荷过大,对中不良
3)保持架的圆度太大(制造原因)
4)装配不当,对中不良,轴弯曲
5)轴,保持架精度不高
6)安装时冲击载荷过大,圆柱滚子轴承的装配过盈度太大
7)间隙过小,载荷过大,润滑不良,预压过大
1)向心轴承的滚道、双列轴承的表面仅一侧表面剥落
3)异物落入,润滑不良,装配不当
1)类似静压痕
2)在配合面上出现红褐色磨损粉末的局部磨损
3)滚道面、滚到体面、凸缘面、保护架等磨损
损伤轴承,降低轴承运行精度
烧伤
装配不当,润滑不良
滚道面、滚动体面、挡边面变色、软化、熔体
表面局部软化,降低使用寿命
腐蚀
1)轴承内部配合面等锈蚀
11种轴承损伤的典型案例,原因分析及解决方案

11种轴承损伤的典型案例,原因分析及解决方案轴承在各个领域各个行业应用都非常广泛,今天为大家带来轴承损伤的经典案例,希望大家能有所收获!高质量的轴承在正确的使用下,可以使用很长一段时间,如果过早的出现损伤,很可能是因为选型错误,使用不当或润滑不良造成的。
因此,在安装轴承时,我们需要记录机器种类,安装部位,使用条件及周围配合。
通过研究总结轴承损伤的类型,发生问题时的使用环境,以避免类似情况再次发生。
轴承损伤方式按下述图片分类,我们可以图片中显示的主要特征来判断轴承损伤形式。
裂纹缺陷,部分缺口有裂纹。
原因:主机的冲击负荷过大,主轴与轴承配合过盈量大;也有较大的剥离摩擦引起裂纹;安装时精度不良;使用不当(用铜锤、卡入大异物)和摩擦裂纹。
解决措施:应检查使用条件,同时设定适当过盈及检查材质,改善安装及使用方法,检查润滑剂以防止摩擦裂纹。
滚道表面金属剥离运转面剥离。
剥离后呈明显凹凸状。
原因:轴承滚动体和内、外圈滚道面上均承受周期性脉动载荷作用,产生周期变化的接触应力。
当应力循环次数达到一定数值后,在滚动体或内、外圈滚道工作面上就产生疲劳剥离。
如果轴承的负荷过大,会使这种疲劳加剧。
另外,轴承安装不正、轴弯曲也会产生滚道剥离现象。
解决措施:应重新研究使用条件和选择轴承及游隙,并检查轴和轴承箱的加工精度、安装方法、润滑剂及润滑方法。
烧伤轴承发热变色,进而烧伤不能旋转。
原因:一般是润滑不足,润滑油质量不符合要求或变质,以及轴承装配过紧等。
另外游隙过小和负荷过大(预压大),滚子偏斜。
解决措施:选择适当的游隙(或增大游隙),要检查润滑剂的种类,确保注入量,检查使用条件,以防定位误差,改善轴承组装方法。
保持架碎裂铆钉松动或断裂,滚动体破碎。
原因:力矩负荷过大,润滑不足,转速变动频繁、振动大,轴承在倾斜状态下安装,卡入异物。
解决措施:要查找使用条件和润滑状态是否适宜,注意轴承的使用,研究保持架的选择是否合适和轴承箱的刚性是否负荷要求。
轴承损伤的16种基本原因
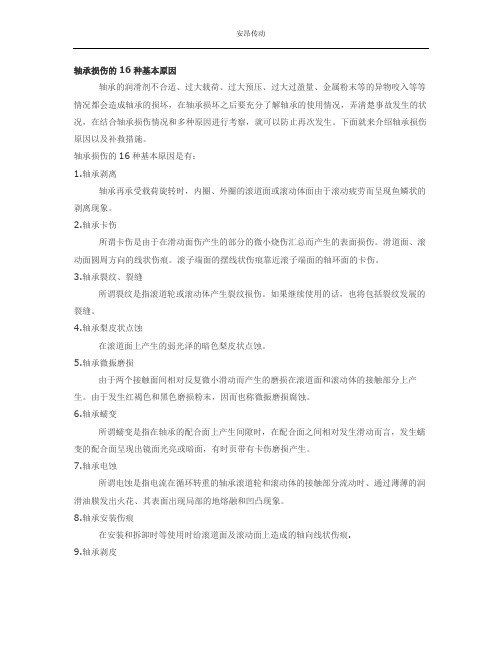
轴承损伤的16种基本原因轴承的润滑剂不合适、过大载荷、过大预压、过大过盈量、金属粉末等的异物咬入等等情况都会造成轴承的损坏,在轴承损坏之后要充分了解轴承的使用情况,弄清楚事故发生的状况,在结合轴承损伤情况和多种原因进行考察,就可以防止再次发生。
下面就来介绍轴承损伤原因以及补救措施。
轴承损伤的16种基本原因是有:1.轴承剥离轴承再承受载荷旋转时,内圈、外圈的滚道面或滚动体面由于滚动疲劳而呈现鱼鳞状的剥离现象。
2.轴承卡伤所谓卡伤是由于在滑动面伤产生的部分的微小烧伤汇总而产生的表面损伤。
滑道面、滚动面圆周方向的线状伤痕。
滚子端面的摆线状伤痕靠近滚子端面的轴环面的卡伤。
3.轴承裂纹、裂缝所谓裂纹是指滚道轮或滚动体产生裂纹损伤。
如果继续使用的话,也将包括裂纹发展的裂缝。
4.轴承梨皮状点蚀在滚道面上产生的弱光泽的暗色梨皮状点蚀。
5.轴承微振磨损由于两个接触面间相对反复微小滑动而产生的磨损在滚道面和滚动体的接触部分上产生。
由于发生红褐色和黑色磨损粉末,因而也称微振磨损腐蚀。
6.轴承蠕变所谓蠕变是指在轴承的配合面上产生间隙时,在配合面之间相对发生滑动而言,发生蠕变的配合面呈现出镜面光亮或暗面,有时页带有卡伤磨损产生。
7.轴承电蚀所谓电蚀是指电流在循环转重的轴承滚道轮和滚动体的接触部分流动时、通过薄薄的润滑油膜发出火花、其表面出现局部的地熔融和凹凸现象。
8.轴承安装伤痕在安装和拆卸时等使用时给滚道面及滚动面上造成的轴向线状伤痕.9.轴承剥皮呈现出带有轻微磨损的暗面,暗面上由表面往里有多条深至5-10m的微小裂缝,并在大范围内发生微小脱落(微小剥离)10.轴承断裂所谓断裂是指由于对滚道轮的挡边或滚子角的局部部分施加乐冲击或过大载荷而一小部分断裂。
11.轴承压痕咬入了金属小粉末,异物等的时候,在滚道面或转动面上产生的凹痕。
由于安装等时受到冲击,在滚动体的间距间隔上形成了凹面(布氏硬度压痕)。
12.轴承磨损所谓磨损是由于摩擦而造成滚道面或滚动面,滚子端面,轴环面及保持架的凹面等磨损。
轴承微动磨损及其防护措施

轴承微动磨损及其防护措施
第九篇
第一章
轴承微动磨损
第一章
轴承微动磨损
第一节
微动摩擦学的基本概念和实例
一、 基本概念
为区别于传统的滑动和滚动, 微动 ( !"#$$%& ’) 指的是二个接触表面发生极小幅度的相 对运动, 它通常存在于一个振动工况 (如发动机运转、 气流波动、 热循环应力、 疲劳载荷、 电磁震动、 传动等) 下的 “近似紧固” 的机械配合件之中, 一般其位移幅度为微米量级。相 应地, 微动摩擦学是研究微动运行机理、 损伤、 测试、 监控、 预防的学科。然而, 望文生义, 微动摩擦学经常被大家误解为一门非常特殊、 狭窄的学科, 而且由于接触表面没有宏观 的相对运动, 微动现象从设计、 使用过程、 失效分析及维修几乎未被大家认识, 更谈不上 重视。因此, 在失效分析中, 一般只强调材料质量、 强度、 磨损等问题, 极少将配合面的微 动摩擦作为考虑的一个因素。其实, 微动在工程实际中普遍存在, 涉及到学科如机械、 材 料、 力学、 物理、 化学甚至生物医学、 电工等也相当广泛。因此, 其普遍性、 复杂性和研究 难度都远远超过常见的滑动和滚动摩擦。 微动可以造成接触表面摩擦磨损, 引起构件咬合、 松动、 功率损失、 噪声增加或污染 源形成等; 微动也可以加速疲劳裂纹的萌生和扩展, 使构件的疲劳寿命大大降低。 按不同的相对运动方向, 实际的微动现象十分复杂, 根据简单化的球( 平面接触模型, 微动可分为四类基本运行模式 (如图 ) * + * + 所不) : 或称平移式微动, 这 ! 切向式微动, 是最普遍的微动方式; "径向式微动; #滚动式微动; $ 扭动式微动。后面三种微动形式 ・ /.-, ・
图!"#")
轴承失效的九个阶段
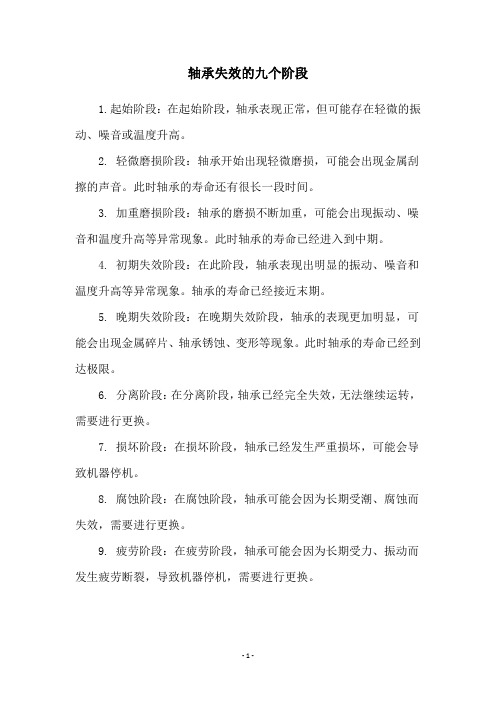
轴承失效的九个阶段
1.起始阶段:在起始阶段,轴承表现正常,但可能存在轻微的振动、噪音或温度升高。
2. 轻微磨损阶段:轴承开始出现轻微磨损,可能会出现金属刮擦的声音。
此时轴承的寿命还有很长一段时间。
3. 加重磨损阶段:轴承的磨损不断加重,可能会出现振动、噪音和温度升高等异常现象。
此时轴承的寿命已经进入到中期。
4. 初期失效阶段:在此阶段,轴承表现出明显的振动、噪音和温度升高等异常现象。
轴承的寿命已经接近末期。
5. 晚期失效阶段:在晚期失效阶段,轴承的表现更加明显,可能会出现金属碎片、轴承锈蚀、变形等现象。
此时轴承的寿命已经到达极限。
6. 分离阶段:在分离阶段,轴承已经完全失效,无法继续运转,需要进行更换。
7. 损坏阶段:在损坏阶段,轴承已经发生严重损坏,可能会导致机器停机。
8. 腐蚀阶段:在腐蚀阶段,轴承可能会因为长期受潮、腐蚀而失效,需要进行更换。
9. 疲劳阶段:在疲劳阶段,轴承可能会因为长期受力、振动而发生疲劳断裂,导致机器停机,需要进行更换。
- 1 -。
滚动轴承常见的失效形式
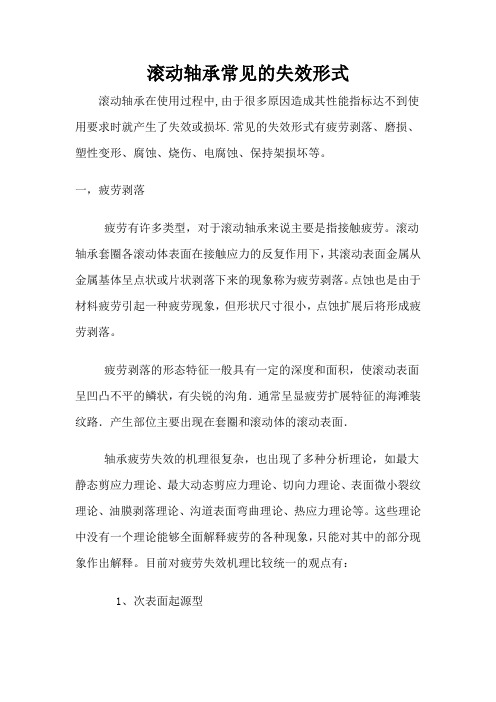
滚动轴承常见的失效形式滚动轴承在使用过程中,由于很多原因造成其性能指标达不到使用要求时就产生了失效或损坏.常见的失效形式有疲劳剥落、磨损、塑性变形、腐蚀、烧伤、电腐蚀、保持架损坏等。
一,疲劳剥落疲劳有许多类型,对于滚动轴承来说主要是指接触疲劳。
滚动轴承套圈各滚动体表面在接触应力的反复作用下,其滚动表面金属从金属基体呈点状或片状剥落下来的现象称为疲劳剥落。
点蚀也是由于材料疲劳引起一种疲劳现象,但形状尺寸很小,点蚀扩展后将形成疲劳剥落。
疲劳剥落的形态特征一般具有一定的深度和面积,使滚动表面呈凹凸不平的鳞状,有尖锐的沟角.通常呈显疲劳扩展特征的海滩装纹路.产生部位主要出现在套圈和滚动体的滚动表面.轴承疲劳失效的机理很复杂,也出现了多种分析理论,如最大静态剪应力理论、最大动态剪应力理论、切向力理论、表面微小裂纹理论、油膜剥落理论、沟道表面弯曲理论、热应力理论等。
这些理论中没有一个理论能够全面解释疲劳的各种现象,只能对其中的部分现象作出解释。
目前对疲劳失效机理比较统一的观点有:1、次表面起源型次表面起源型认为轴承在滚动接触部位形成油膜的条件下运转时,滚动表面是以内部(次表面)为起源产生的疲劳剥落。
2、表面起源型表面起源型认为轴承在滚动接触部位未形成油膜或在边界润滑状态下运转时,滚动表面是以表面为起源产生的疲劳剥落。
3、工程模型工程模型认为在一般工作条件下,轴承的疲劳是次表面起源型和表面起源型共同作用的结果。
疲劳产生的原因错综复杂,影响因素也很多,有与轴承制造有关的因素,如产品设计、材料选用、制造工艺和制造质量等;也有与轴承使用有关的因素,如轴承选型、安装、配合、润滑、密封、维护等。
具体因素如下:A、制造因素1、产品结构设计的影响产品的结构设计是根据使用性能目标值来确定的,这些目标值如载荷容量、寿命、精度、可靠性、振动、磨损、摩擦力矩等。
在设计时,由于各种原因,会造成产品设计与使用的不适用或脱节,甚至偏离了目标值,这种情况很容易造成产品的早期失效。
轴承故障图

轴承的损伤:梨皮状点蚀损伤状态原因措施在滚道面上产生的弱光泽的暗色梨皮状点蚀。
润滑过程中出现的异物咬入由于空气中的水分而结露。
润滑不良。
改善密封装置。
充分过滤润滑油。
使用合适的润滑剂。
照片 9-1●回转支撑轴承的外圈●滚道面上产生的梨皮状点蚀●凹处底部受到腐蚀照片 9-2●照片 9-1的球●转动面上产生的梨皮状点蚀轴承的损伤:微振磨损损伤状态原因措施由于两个接触面间相对反复微小滑动而产生的磨损。
在滚道面和滚动体的接触部分上产生。
由于发生红褐色或黑色磨损粉未,因而也称微振磨损腐蚀。
润滑不良。
小振幅的摇摆运动。
过盈量不足。
使用适当的润滑剂。
加预压。
检查过盈量。
向配合面上涂润滑剂。
照片 11-1●深沟球轴承的内圈●内径面上产生的微振磨损 ●由于振动造成的损伤照片 11-2●向心推力球轴承的内圈●整个径道面上产生的显著的微振磨损●过盈量不足造成的损伤照片 11-3●双列圆柱滚子轴承的外圈●滚道面上在滚子间距中产生的微振磨损轴承的损伤:卡伤损伤状态原因措施所谓卡伤是由于在滑动面上产生的部分的微小烧伤汇总而产生的表面损伤。
滑道面、滚动面圆周方向的线状伤痕。
滚子端面的摆线状伤痕。
靠近滚子端面过大载荷、过大预压。
润滑不良。
异物咬入。
内圈外圈的倾斜、轴的挠度。
轴、轴承箱的精度不良。
检查载荷的大小。
预压要适当。
改善润滑剂和润滑方法。
检查轴、轴承箱的精度。
照片3-1●自动调心滚子轴承的内圈 ●内圈大挡边面上产生的卡伤 ●原因是急加减速造成的滚子打滑照片 3-2●照片 3-1的球面滚子 ●滚子端面上产生的卡伤●原因是急加减速造成的滚子打滑照片 3-3●推力圆锥滚子轴承的内圈 ●内圈挡边面上产生的挡边●原因是磨损粉末混入,过大载荷造成油膜热裂轴承的损伤:擦伤照片 3-4●向心球轴承的内圈●滚道面上产生的球距的剥离 ●由停转时冲击载荷造成的压痕发展面成损伤状态原因措施所谓擦伤,是在滚道面或滚动面上,由随着滚动的打滑和油膜热裂产生的微小烧伤的汇总而发生的表面损伤。