长孔、窄槽类铸件熔模铸造工艺方法
熔模铸造工艺
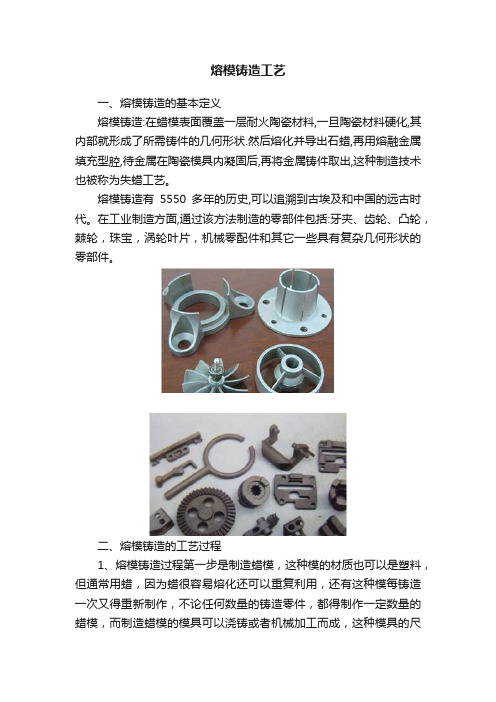
熔模铸造工艺一、熔模铸造的基本定义熔模铸造:在蜡模表面覆盖一层耐火陶瓷材料,一旦陶瓷材料硬化,其内部就形成了所需铸件的几何形状.然后熔化并导出石蜡,再用熔融金属填充型腔,待金属在陶瓷模具内凝固后,再将金属铸件取出,这种制造技术也被称为失蜡工艺。
熔模铸造有5550多年的历史,可以追溯到古埃及和中国的远古时代。
在工业制造方面,通过该方法制造的零部件包括:牙夹、齿轮、凸轮,棘轮,珠宝,涡轮叶片,机械零配件和其它一些具有复杂几何形状的零部件。
二、熔模铸造的工艺过程1、熔模铸造过程第一步是制造蜡模,这种模的材质也可以是塑料,但通常用蜡,因为蜡很容易熔化还可以重复利用,还有这种模每铸造一次又得重新制作,不论任何数量的铸造零件,都得制作一定数量的蜡模,而制造蜡模的模具可以浇铸或者机械加工而成,这种模具的尺寸精度要求比较高,需仔细计算和推敲,它必须考虑金属铸件和蜡以及蜡模表面陶瓷材料的收缩性,还需经过多次错误并不断尝试才能达到所需的尺寸范围,所以这种模具价格都比较贵。
图 (一)2、因为铸造模具属于一次性的,铸造完成后不需要开模机构,所以它可以铸造几何形状非常复杂的部件,一个铸件可以由多个蜡模结合而成,但通常情况下, 将多个蜡模连接起来,通过一次浇铸可以完成多个铸件。
其中蜡杆作为中央主浇道, 所有蜡模都与主浇道连通,蜡杆的起始端连接主浇口,这种结构被称为树形结构,主浇道好比树干而其连接的多个蜡模好比树的分枝。
3、往金属铸造模腔内灌入含有极细粒度的二氧化硅、水和粘接剂的耐火浆料,接着在蜡模与金属模腔之间的蜡模表面会形成陶瓷层,重复灌入浆料后陶瓷层的厚度也会不断增大,在某些情况下,可直接将其放入瓶子内,然后往瓶内灌入陶瓷浆料。
4、当蜡模表面耐火涂层足够厚时,将其置于空气中使它自由干燥而变硬。
5、下一步也是熔模铸造过程中关键的一步:倒置已硬化的陶瓷模具,将其加热至200F-375F(90℃-175℃)的温度,使蜡融化后流出模具,留下的空腔将用来铸造所需的金属铸件。
熔模铸造工艺(3篇)

第1篇一、熔模铸造工艺的定义熔模铸造工艺,又称精密铸造,是一种将金属熔化后注入预先制成的型腔中,冷却凝固后取出金属制品的铸造方法。
该工艺主要用于制造形状复杂、尺寸精度要求高的零件。
二、熔模铸造工艺的原理熔模铸造工艺的基本原理是将可熔化的材料(如蜡、塑料等)制成所需形状的熔模,再将熔模组装成型腔,将熔融金属注入型腔,冷却凝固后取出金属制品。
具体过程如下:1. 制作熔模:将可熔化的材料制成所需形状的熔模,通常采用手工或机械加工方法。
2. 组装型腔:将熔模组装成型腔,并固定在型腔架上。
3. 熔化金属:将金属加热至熔化状态。
4. 注入金属:将熔融金属注入型腔,使其填充熔模形成的型腔。
5. 冷却凝固:将型腔冷却至室温,使金属凝固。
6. 脱模:将型腔从金属制品中取出,得到所需的金属制品。
三、熔模铸造工艺的过程1. 熔模制作:根据零件图纸,采用手工或机械加工方法制作熔模。
熔模应保证形状、尺寸和精度符合要求。
2. 组装型腔:将熔模组装成型腔,并固定在型腔架上。
3. 熔化金属:选择合适的金属材料,将其加热至熔化状态。
4. 注入金属:将熔融金属注入型腔,确保填充完全。
5. 冷却凝固:将型腔冷却至室温,使金属凝固。
6. 脱模:将型腔从金属制品中取出,得到所需的金属制品。
7. 后处理:对金属制品进行清理、去毛刺、抛光等后处理。
四、熔模铸造工艺的应用熔模铸造工艺广泛应用于以下领域:1. 航空航天:制造发动机叶片、涡轮盘、机匣等高精度零件。
2. 汽车:制造发动机缸体、缸盖、曲轴等关键部件。
3. 电子:制造集成电路封装、精密模具等。
4. 医疗器械:制造心脏支架、人工关节等精密医疗器械。
5. 机械制造:制造齿轮、轴承、凸轮等精密零件。
五、熔模铸造工艺的优缺点1. 优点:(1)高精度:熔模铸造工艺可以制造形状复杂、尺寸精度高的零件。
(2)高复杂度:可以制造形状复杂、尺寸精度高的零件,满足各种复杂结构的制造需求。
(3)高质量:金属熔化后注入型腔,减少了氧化、污染等不良因素的影响,保证了金属制品的质量。
熔模铸造工艺流程
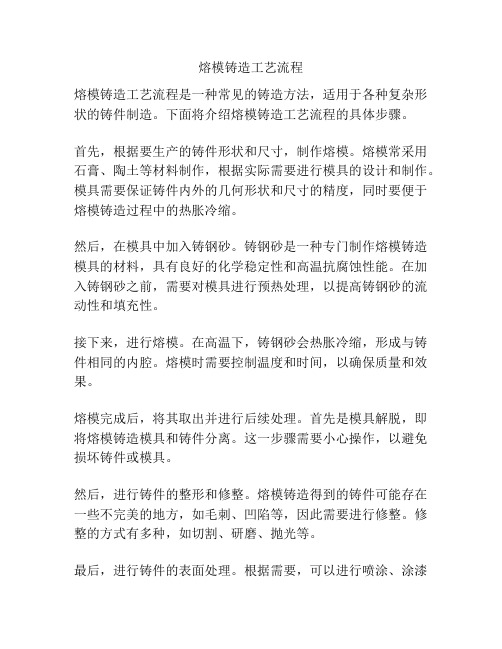
熔模铸造工艺流程
熔模铸造工艺流程是一种常见的铸造方法,适用于各种复杂形状的铸件制造。
下面将介绍熔模铸造工艺流程的具体步骤。
首先,根据要生产的铸件形状和尺寸,制作熔模。
熔模常采用石膏、陶土等材料制作,根据实际需要进行模具的设计和制作。
模具需要保证铸件内外的几何形状和尺寸的精度,同时要便于熔模铸造过程中的热胀冷缩。
然后,在模具中加入铸钢砂。
铸钢砂是一种专门制作熔模铸造模具的材料,具有良好的化学稳定性和高温抗腐蚀性能。
在加入铸钢砂之前,需要对模具进行预热处理,以提高铸钢砂的流动性和填充性。
接下来,进行熔模。
在高温下,铸钢砂会热胀冷缩,形成与铸件相同的内腔。
熔模时需要控制温度和时间,以确保质量和效果。
熔模完成后,将其取出并进行后续处理。
首先是模具解脱,即将熔模铸造模具和铸件分离。
这一步骤需要小心操作,以避免损坏铸件或模具。
然后,进行铸件的整形和修整。
熔模铸造得到的铸件可能存在一些不完美的地方,如毛刺、凹陷等,因此需要进行修整。
修整的方式有多种,如切割、研磨、抛光等。
最后,进行铸件的表面处理。
根据需要,可以进行喷涂、涂漆
等工艺,使铸件的表面光滑、均匀,增加其美观度和使用寿命。
以上就是熔模铸造工艺流程的基本步骤。
需要注意的是,该流程中的每个环节都需要仔细控制和操作,以确保铸件质量和效果。
熔模铸造是一种高难度的铸造方法,需要经验丰富的操作人员和严格的生产管理,才能保证制造出高质量的铸件。
熔模铸造工艺流程
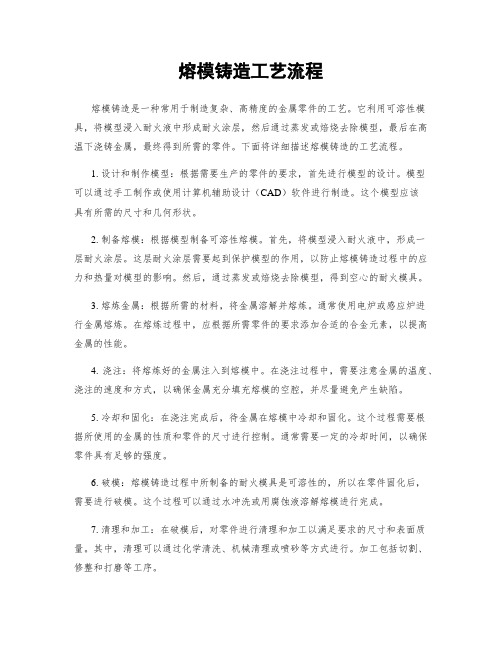
熔模铸造工艺流程熔模铸造是一种常用于制造复杂、高精度的金属零件的工艺。
它利用可溶性模具,将模型浸入耐火液中形成耐火涂层,然后通过蒸发或焙烧去除模型,最后在高温下浇铸金属,最终得到所需的零件。
下面将详细描述熔模铸造的工艺流程。
1. 设计和制作模型:根据需要生产的零件的要求,首先进行模型的设计。
模型可以通过手工制作或使用计算机辅助设计(CAD)软件进行制造。
这个模型应该具有所需的尺寸和几何形状。
2. 制备熔模:根据模型制备可溶性熔模。
首先,将模型浸入耐火液中,形成一层耐火涂层。
这层耐火涂层需要起到保护模型的作用,以防止熔模铸造过程中的应力和热量对模型的影响。
然后,通过蒸发或焙烧去除模型,得到空心的耐火模具。
3. 熔炼金属:根据所需的材料,将金属溶解并熔炼。
通常使用电炉或感应炉进行金属熔炼。
在熔炼过程中,应根据所需零件的要求添加合适的合金元素,以提高金属的性能。
4. 浇注:将熔炼好的金属注入到熔模中。
在浇注过程中,需要注意金属的温度、浇注的速度和方式,以确保金属充分填充熔模的空腔,并尽量避免产生缺陷。
5. 冷却和固化:在浇注完成后,待金属在熔模中冷却和固化。
这个过程需要根据所使用的金属的性质和零件的尺寸进行控制。
通常需要一定的冷却时间,以确保零件具有足够的强度。
6. 破模:熔模铸造过程中所制备的耐火模具是可溶性的,所以在零件固化后,需要进行破模。
这个过程可以通过水冲洗或用腐蚀液溶解熔模进行完成。
7. 清理和加工:在破模后,对零件进行清理和加工以满足要求的尺寸和表面质量。
其中,清理可以通过化学清洗、机械清理或喷砂等方式进行。
加工包括切割、修整和打磨等工序。
8. 检测和质量控制:最后,对熔模铸造所得到的零件进行检测和质量控制。
常用的检测方法包括X射线检测、超声波检测和尺寸测量等。
这些检测可以确保零件的尺寸和性能满足设计要求。
总结起来,熔模铸造工艺流程包括模型的设计和制作、耐火模具的制备、金属的熔炼、浇注、冷却固化、破模、清理加工以及检测和质量控制。
熔模铸造工艺流程
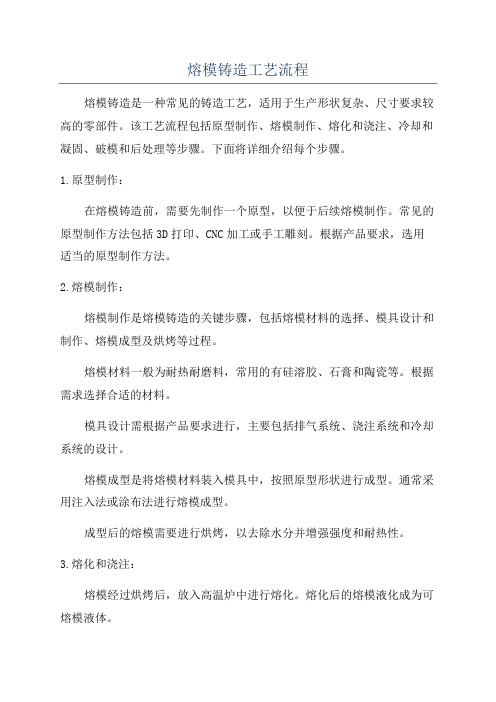
熔模铸造工艺流程熔模铸造是一种常见的铸造工艺,适用于生产形状复杂、尺寸要求较高的零部件。
该工艺流程包括原型制作、熔模制作、熔化和浇注、冷却和凝固、破模和后处理等步骤。
下面将详细介绍每个步骤。
1.原型制作:在熔模铸造前,需要先制作一个原型,以便于后续熔模制作。
常见的原型制作方法包括3D打印、CNC加工或手工雕刻。
根据产品要求,选用适当的原型制作方法。
2.熔模制作:熔模制作是熔模铸造的关键步骤,包括熔模材料的选择、模具设计和制作、熔模成型及烘烤等过程。
熔模材料一般为耐热耐磨料,常用的有硅溶胶、石膏和陶瓷等。
根据需求选择合适的材料。
模具设计需根据产品要求进行,主要包括排气系统、浇注系统和冷却系统的设计。
熔模成型是将熔模材料装入模具中,按照原型形状进行成型。
通常采用注入法或涂布法进行熔模成型。
成型后的熔模需要进行烘烤,以去除水分并增强强度和耐热性。
3.熔化和浇注:熔模经过烘烤后,放入高温炉中进行熔化。
熔化后的熔模液化成为可熔模液体。
同时,需要预热金属液体至合适温度,以便于浇注。
将熔模液体和金属液体倒入上料室,通过内部特殊结构实现金属液的浇注。
此时,金属液体填充熔模的空腔内部。
4.冷却和凝固:浇注后的熔模需要进行冷却和凝固。
冷却过程中,通过熔模材料的吸热和导热作用,将熔模液体中的热量传导到熔模表面,并通过冷却系统散热。
随着时间的推移,熔模液体开始凝固,逐渐形成固态金属零件。
5.破模和后处理:凝固完全后,需要将熔模零件与金属基体分离。
通常采用机械破模或高温烧毁破模法将熔模材料和固态金属零件分离。
破模后的固态金属零件需要进行脱蜡、除砂、清洗等后处理工艺,以去除残留物和表面杂质。
此外,还需要进行修整、加工等工艺,使得零件达到设计要求。
总结:熔模铸造是一种适用于生产形状复杂、尺寸要求较高的零部件的铸造工艺。
其工艺流程包括原型制作、熔模制作、熔化和浇注、冷却和凝固、破模和后处理等步骤。
每个步骤都有着特定的过程和要求,需要严格按照规范操作。
长孔、窄槽类铸件熔模铸造工艺方法

熔模铸造型壳是“上涂料——撒砂——干燥”这一过程的重复。
但对于具有长孔、窄槽这样结构的铸件而言,由于长孔、窄槽内部不易上涂料、撒砂,当通孔的孔深和孔径之比H /d>5【1】,窄槽的槽深或长与宽之比大于一定比例时很难铸出,往往采用机械加工的方法实现。
对于直径略大的长孔,虽然型壳可以做出,但已被浆料、型砂填满,增加了缩孔、缩松缺陷发生的几率。
本文即讨论该类铸件熔模铸造的几种方法。
1.浸浆法1.1浸浆法:在制壳二层或三层后,将型壳浸入到浆料中,使浆料充满长孔或窄槽中型壳余下的空间,待其中的浆料干透后,再进行下一层型壳的制作。
目的是增加孔内型壳的强度,防止出现跑火现象。
1.2实例:接头A接头A结构见图1。
其上有一个Φ4×25细长孔,呈135°相交,孔壁厚1mm,头部0. 7mm,件小而轻,质量为9.5g。
资料【1】介绍:当孔径Φ3~Φ5时,最大可铸出孔深为5 ~10mm,即孔深与孔径之比为1.4~3.3,而该件孔深与孔径之比为6.25,可见Φ4孔制壳是该件的难点。
图1该件一、二层型壳均采用锆英材料,一层型壳厚约0.5mm,二层型壳厚约0.75mm。
制壳两层后,Φ4孔口只有约Φ1.5mm。
三层正常制壳时,撒30~60目莫来砂,粒径为0.2 ~0.6mm。
且长孔呈135°相交,孔内正常上涂料撒砂已无法实现。
但两层锆英材料型壳强度较小,无法抵抗1600℃以上高温钢水冲刷,会产生跑火现象形成废品。
在制壳二层后采用了“浸浆法”,增加了型壳的强度,满足批量生产要求。
1.3工艺要点1.3.1 浸浆浆料:硅溶胶+莫来粉(200目),粘度20±2S。
粘度大,浸浆时流动不好,不易充满;粘度小,浸浆时看起来已满,但干透后由于水分蒸发会留下较多的空洞,影响强度。
1.3.2 浸浆前吹净长孔内的浮砂。
1.3.3 浸浆后型壳一定要干透,以保证强度。
接头A三层浸浆后干燥时间为24小时,干燥条件:温度24±2℃,湿度40~60%,吹风。
熔模铸造工艺流程

熔模铸造工艺流程
《熔模铸造工艺流程》
熔模铸造是一种精密铸造工艺,常用于生产要求高精度、表面光洁度和复杂结构的零部件。
其工艺流程主要包括模具制作、熔模成型、熔炼浇注、冷却固化和后处理等环节。
首先,熔模铸造的工艺流程始于模具制作。
通常情况下,模具是由耐火材料如硅砂等制成,以保证能承受高温熔化金属的作用。
模具的制作需要考虑到最终零件的形状和尺寸精度,因此需要进行精密的设计和加工。
其次,熔模成型是熔模铸造的关键步骤。
在这一过程中,模具中填入熔化的金属,使之在模具中充分填充并冷却凝固成型。
这一步骤要求操作人员具备较高的技能和经验,以确保成型零件的质量和准确度。
接着,熔炼浇注是将金属熔炼后浇入模具中的步骤。
熔化金属需要在一定的温度和时间下完成,以确保金属能够充分填充模具并达到所需的形状和性能。
冷却固化是指模具中的熔化金属冷却后凝固成型。
在这一过程中,需要控制冷却速度和方法,以避免发生裂缝和变形,确保最终零件的质量。
最后,后处理是指在熔模铸造完成后对零件进行清理和表面处理的环节。
包括去除模具残渣、切割和修整不规则部分、打磨
和抛光等工序,最终得到符合要求的成品。
总的来说,熔模铸造工艺流程是一个综合性的工艺,涉及到材料、成型、熔化、冷却、工艺控制和最终零件的质量检验等方面。
在实际应用中,需要严格遵循每一步骤的操作规程,以确保最终生产出质量优良的零部件。
熔模铸造的工艺过程
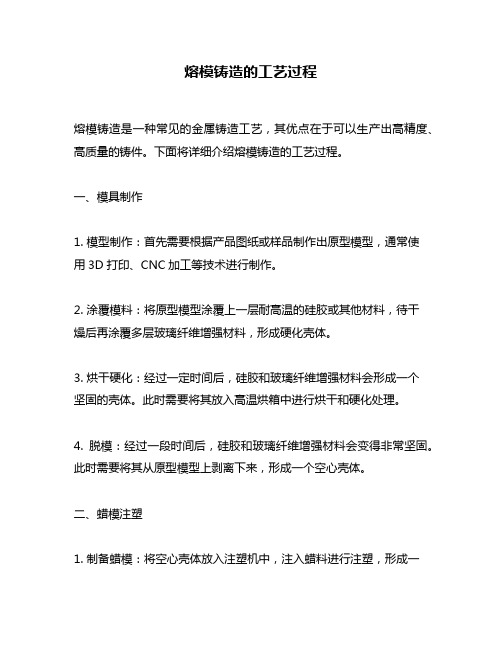
熔模铸造的工艺过程熔模铸造是一种常见的金属铸造工艺,其优点在于可以生产出高精度、高质量的铸件。
下面将详细介绍熔模铸造的工艺过程。
一、模具制作1. 模型制作:首先需要根据产品图纸或样品制作出原型模型,通常使用3D打印、CNC加工等技术进行制作。
2. 涂覆模料:将原型模型涂覆上一层耐高温的硅胶或其他材料,待干燥后再涂覆多层玻璃纤维增强材料,形成硬化壳体。
3. 烘干硬化:经过一定时间后,硅胶和玻璃纤维增强材料会形成一个坚固的壳体。
此时需要将其放入高温烘箱中进行烘干和硬化处理。
4. 脱模:经过一段时间后,硅胶和玻璃纤维增强材料会变得非常坚固。
此时需要将其从原型模型上剥离下来,形成一个空心壳体。
二、蜡模注塑1. 制备蜡模:将空心壳体放入注塑机中,注入蜡料进行注塑,形成一个与空心壳体相同的蜡模。
2. 脱模:经过一定时间后,蜡模会变得非常坚固。
此时需要将其从空心壳体上剥离下来。
三、组装1. 浇口和排气道:在空心壳体上开凿出浇口和排气道,以便于金属液进入和气体排出。
2. 组装:将蜡模放入空心壳体中,并进行粘接和定位,形成一个完整的铸造型。
四、烧结1. 烘干:将铸造型放入高温烤箱中进行烘干处理,以去除其中的水分和残留物质。
2. 烧结:经过一段时间后,铸造型会变得非常坚固。
此时需要将其放入高温熔炉中进行烧结处理,以使其更加坚硬。
五、浇注1. 准备金属液:根据产品要求选择合适的金属材料,并在高温熔炉中加热,使其变成液态状态。
2. 浇注:将金属液倒入铸造型中,在浇注过程中需要控制好流量和速度,以确保铸件质量。
六、冷却1. 冷却:经过一定时间后,金属液会逐渐凝固成铸件。
此时需要将其从铸造型中取出,并放置在冷却室中进行冷却处理。
2. 去除浇口和排气道:待铸件完全冷却后,需要去除其中的浇口和排气道,并进行表面处理和清洗。
七、检验1. 外观检验:对铸件进行外观检验,检查其表面是否有缺陷、裂纹等问题。
2. 尺寸检验:对铸件进行尺寸检验,确保其符合产品要求的精度和尺寸。
- 1、下载文档前请自行甄别文档内容的完整性,平台不提供额外的编辑、内容补充、找答案等附加服务。
- 2、"仅部分预览"的文档,不可在线预览部分如存在完整性等问题,可反馈申请退款(可完整预览的文档不适用该条件!)。
- 3、如文档侵犯您的权益,请联系客服反馈,我们会尽快为您处理(人工客服工作时间:9:00-18:30)。
熔模铸造型壳是“上涂料——撒砂——干燥”这一过程的重复。
但对于具有长孔、窄槽这样结构的铸件而言,由于长孔、窄槽部不易上涂料、撒砂,当通孔的孔深和孔径之比H/d> 5【1】,窄槽的槽深或长与宽之比大于一定比例时很难铸出,往往采用机械加工的方法实现。
对于直径略大的长孔,虽然型壳可以做出,但已被浆料、型砂填满,增加了缩孔、缩松缺陷发生的几率。
本文即讨论该类铸件熔模铸造的几种方法。
1. 浸浆法1.1浸浆法:在制壳二层或三层后,将型壳浸入到浆料中,使浆料充满长孔或窄槽中型壳余下的空间,待其中的浆料干透后,再进行下一层型壳的制作。
目的是增加孔型壳的强度,防止出现跑火现象。
1.2实例:接头A接头A结构见图1。
其上有一个Φ4×25细长孔,呈135°相交,孔壁厚1mm,头部0. 7mm,件小而轻,质量为9.5g。
资料【1】介绍:当孔径Φ3~Φ5时,最大可铸出孔深为5~ 10mm,即孔深与孔径之比为1.4~3.3,而该件孔深与孔径之比为6.25,可见Φ4孔制壳是该件的难点。
图1该件一、二层型壳均采用锆英材料,一层型壳厚约0.5mm,二层型壳厚约0.75mm。
制壳两层后,Φ4孔口只有约Φ1.5mm。
三层正常制壳时,撒30~60目莫来砂,粒径为0.2 ~0.6mm。
且长孔呈135°相交,孔正常上涂料撒砂已无法实现。
但两层锆英材料型壳强度较小,无法抵抗1600℃以上高温钢水冲刷,会产生跑火现象形成废品。
在制壳二层后采用了“浸浆法”,增加了型壳的强度,满足批量生产要求。
1.3工艺要点1.3.1 浸浆浆料:硅溶胶+莫来粉(200目),粘度20±2S。
粘度大,浸浆时流动不好,不易充满;粘度小,浸浆时看起来已满,但干透后由于水分蒸发会留下较多的空洞,影响强度。
1.3.2 浸浆前吹净长孔的浮砂。
1.3.3 浸浆后型壳一定要干透,以保证强度。
接头A三层浸浆后干燥时间为24小时,干燥条件:温度24±2℃,湿度40~60%,吹风。
2. 长孔插木条法2.1 长孔插木条法:在制壳三层或四层后,在长孔余下的空间插入木条,随后进行正常制壳、封浆、脱蜡等操作。
型壳焙烧时,插入的木条烧掉形成空洞,从而改善型壳浇注后的散热条件,消除缩孔、缩松缺陷的方法。
2.2实例接头B接头B的结构见图2,虚线为浇口,其上均布Φ7.8×23的长孔六个。
工艺设计采用一字型横模头组树,正常制壳四层半后浇注,并采用“型壳局部淬水”【2】工艺,即在型壳浇注前,将型壳下部淬入水中2~3秒,形成自上而下的温度梯度和凝固顺序。
但在浇口下部的两个孔出现大比例的缩松现象,严重的已缩透。
分析认为:这两个孔位于浇口下部,浇注时钢水经此处流入型腔,有过热倾向,而Φ7.8mm孔正常制壳四层半后已被浆料和型砂填满,恶化了此处散热和冷却条件,加剧了缩松产生倾向。
在制壳三层后,采用插入木条法,消除了孔的缩松缺陷。
图22.3 工艺要点:2.3.1 插入木条可根据孔大小在制壳三层后或者四层后进行,此时应保证型壳有一定强度抵抗钢水冲击。
2.3.2 插入木条直径应与余下型壳孔洞接近,这样既方便操作,又保证能插住。
2.3.3 插入木条应在制壳2~3小时后进行。
过早,型壳强度低,易损坏;过晚,型壳有一定强度,凹凸不平的撒砂平面,阻碍了木条的插入。
2.3.4 木条长度足够,以保证插透。
2.3.5 为便于操作,组树时蜡模六孔中心与模头夹角大于60°。
3. 型壳局部保温法3.1 型壳局部保温法:焙烧前,在型壳的局部敷贴保温材料,延缓此处的冷却、凝固时间,打开钢水的补缩通道,以达到消除缩孔、缩松缺陷的目的。
3.2 实例DN15法兰阀盖法兰阀盖结构见图3,虚线为浇口。
该件结构特点:上下两个较厚法兰盘间有较长的流量口,孔径Φ15mm,长51.4mm,壁厚3mm。
铸造工艺设计:上法兰盘一个浇口,一字横模头组树,四层半型壳,浇注时下法兰盘处采用“型壳局部淬水”工艺,浇注温度为160 0~1610℃。
但在浇注后,有部分铸件在流量孔中部产生缩松现象。
分析认为:该件流量孔长且壁薄,铸件浇注后的凝固补缩状态见图4。
下法兰盘及附近的Ⅲ区,因型壳淬水的激冷作用,最先凝固而得到致密的组织;靠近浇口Ⅰ区,钢水的收缩有来自浇口的热钢水补充,也得到致密的组织;处在中间的Ⅱ区,上部的钢水补充及下部的激冷作用都无法到达该处,而在制壳完成后,流量孔基本上已被浆料和型砂填满,散热及冷却条件极差,于是在流量孔的中部产生了缩松缺陷。
在流量孔的外部型壳处涂敷保温材料后,延缓了Ⅰ区的凝固时间,打开了自上而下的补缩通道,使来自浇口的热钢水通过Ⅰ区补充到了Ⅱ区,解决了孔的缩松问题。
图3 图43.3 工艺要点3.3.1 保温材料可以使用保温石棉、石棉布、耐火泥或其它的耐火材料。
3.3.2 对两法兰盘间有筋的阀盖,保温材料应让出筋部,以防止筋部产生缩松缺陷。
4. 瓷型芯法4.1 瓷型芯法:即将预制的具有一定常温和高温强度、线膨胀系数小、高温下具有化学稳定性的型芯放在压型中压制蜡模,然后正常制壳做出带有型芯的型壳,经浇注后再去除型芯,从而得到复杂腔铸件的方法。
4.2 实例连接器连接器结构见图5。
其上有约4×12.5×32.5的腰圆形窄槽,并与Φ8孔相交,在铸件部形成一个垂直的流道。
该流道窄而长,正常制壳已不可能,故采用瓷型芯方法。
瓷型芯外购,压制出蜡模见图6。
图5 图6为保证瓷型芯定位准确,设计了长10mm的两个芯头,即伸出蜡模之外不与金属接触部分,见图6的A、B部位。
为防止芯与型壳材料热膨胀系数不同,导致在型壳焙烧或浇注过程中,二者因长度变化不一,引起型芯变形甚至断裂,修蜡模时将其中一个芯头端部涂上一薄层修补蜡,这样在型壳脱蜡后,型壳与芯头之间有一定间隙,防止型芯受力损坏。
正常制壳四层半,浇注温度1600~1610℃。
芯去除采用碱煮或碱爆的方法。
4.3 工艺要点4.3.1 芯芯头与模具间留有0.2~0.8间隙,方便芯安放。
4.3.2 当芯偏长或下芯受阻时,可用细砂纸打磨芯头或受阻部位,保证芯平稳安放在模具中。
当芯偏短或定位不是很牢时,可在芯头端部涂抹修补蜡,增加芯与模具间的粘结力。
4.3.3 当芯较大时,组树后蜡模的清洗改在组树前。
可用软布沾有清洗剂的清洗液擦拭蜡模,防止树组清洗时芯头吸潮,影响型壳干燥。
4.3.4 去除芯有个别残留时,可采用机械法或手喷砂辅助去除。
5.自硬型芯法5.1 自硬型芯法制壳2~3层后,在窄槽口部尚未被涂料和型砂填满之前,灌注配制好的以水溶性磷酸盐为粘结剂的专利制芯材料J×R-2浆料。
浆料灌入后自硬成型,形成含水磷酸盐结晶体,随后正常制壳浇注,再除去型芯得到窄槽的方法【3】5.2 实例阀体塞头阀体塞头结构见图7。
其上有Φ165×11的窄槽,上表面为曲面,槽深处为54mm,该槽能否顺利铸出是该件的关键。
工艺试制中,曾先后采用正常制壳五层半,制壳三层后填30~60目莫来砂的方法,但均因槽严重跑火失败,采用“自硬型芯法”后,窄槽顺利铸出。
图75.2.1 浆料配制工艺a. 浆料配制比例:100g芯料+25ml硅溶胶,粉液比:4b. 浆料搅拌时间:人工搅拌1~2分钟5.2.2 制壳工艺:一、二层型壳采用锆英材料,三层采用莫来砂粉料。
此时11mm宽的窄槽约有5~6mm的窄缝,三层干燥后,灌注已调配好的J×R-2浆料,10分钟后,浆料自硬成型,1小时后浆料强度已较高,再制四层后的型壳,并正常脱蜡。
型壳焙烧30分钟后浇注,在铸件表面形成气孔,延长焙烧时间到60分钟以上,气孔基本消除。
浇注后的J×R-2自硬型芯,呈浅绿色,溃散性良好,正常喷砂基本去除,边角残余部分,可人工清理。
5.3 工艺要点5.3.1 资料【3】介绍:浆料配比100g芯料加硅溶胶19~24ml,粉液比约为4.2~5. 2。
随粉液比降低,浆料流动性变好,但固化时间加长。
根据该件结构,兼顾两个方面因素,我们选择粉液比4。
5.3.2 浆料调配好后,要尽快灌注。
时间长时,由于固化原因,流动性会急剧下降,影响操作。
5.3.3 灌注浆料前,吹净槽浮砂,减少浆料流动阻力,同时有利于提高自硬型芯的密度和强度。
5.3.4 灌浆料时宜倾斜型壳,避免卷入气体。
5.3.5 该件因窄槽深浅不一,采用两次灌浆,尽可能使槽灌满浆,以减少制壳难度,避免跑火缺陷产生。
5.3.6 严格控制浆料灌注后的固化时间。
因浆料固化过程伴有体积膨胀,时间长会胀裂型壳,导致型壳报废。
6.讨论与分析6.1 有资料介绍,对于碳钢材质,熔模铸件外形尺寸为10~50时,可铸出壁厚一般是2.0~2.5,最小1.5【4】,不锈钢材质由于含Cr量高,钢液易氧化,流动性变差,但适当提高浇注温度,增加钢水的过热度,延长液态金属的流动时间,可以铸出壁厚0.7~1mm铸件。
6.2 接头A上细长孔Φ4×25,呈135°相交,一般情况下应采用瓷型芯,采用“浸浆法”后,在保证铸件质量前提下,降低了使用瓷型芯的成本,又避免了清壳困难,是一种经济实用的工艺方法。
6.3 对孔径约Φ6~Φ15的铸件长孔,正常制壳可以实现,但涂料和型砂填满了长孔的所有空间,变成了不透气的死孔,形成新的热节,具有热节效应,容易形成开放式的缩孔缺陷【5】。
长孔插入木条,型壳焙烧时,木条烧掉留下空间,消除了热节,改善了钢水浇注后的冷却和散热条件。
“型壳局部保温法”延缓了钢水的冷却时间,打开了钢水的补缩通道,同时采用“型壳局部淬水”工艺,形成了自上而下的顺序凝固条件,可以消除长孔的缩孔缩松缺陷。
6.4 阀体塞头窄槽长宽之比47,深与宽之比约为5,已超出了表1所列黑色金属熔模铸件铸槽尺寸【6】。
如果应用瓷型芯,会存在下列三个问题:①型芯为Φ165×11圆环状,上表面呈曲面,尺寸大,分量重,成本高。
②型芯尺寸大容易变形,受结构及工艺限制不好定位,这样使槽尺寸难以符合铸件图要求。
③瓷型芯去除一般采用化学方法:氢氟酸腐蚀法、碱煮或碱爆,污染环境,有一定危险。
采用自硬型芯后,克服上述问题,生产出铸件尺寸精确,清壳容易,成本低廉。
7.结语长孔、窄槽类铸件是熔模精密铸造常见结构之一,生产中经常因为孔槽跑火、缩松等缺陷造成返修,甚至报废。
本文所述几种工艺方法,在某种程度上可解决这些问题,生产出符合要求的铸件。