设备焊接和热处理方案
焊接热处理专项施工方案
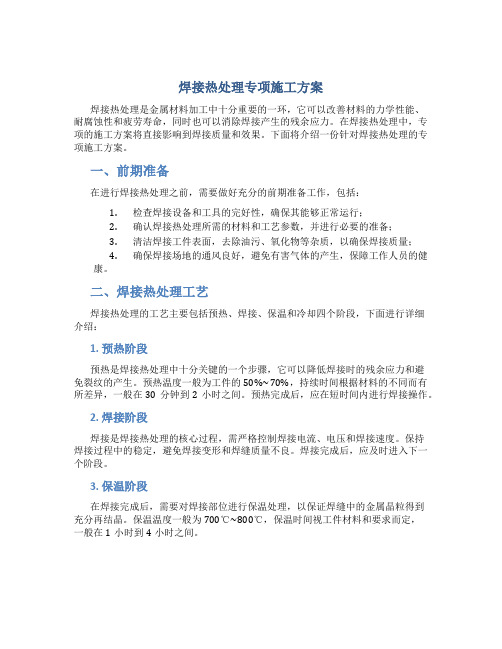
焊接热处理专项施工方案焊接热处理是金属材料加工中十分重要的一环,它可以改善材料的力学性能、耐腐蚀性和疲劳寿命,同时也可以消除焊接产生的残余应力。
在焊接热处理中,专项的施工方案将直接影响到焊接质量和效果。
下面将介绍一份针对焊接热处理的专项施工方案。
一、前期准备在进行焊接热处理之前,需要做好充分的前期准备工作,包括:1.检查焊接设备和工具的完好性,确保其能够正常运行;2.确认焊接热处理所需的材料和工艺参数,并进行必要的准备;3.清洁焊接工件表面,去除油污、氧化物等杂质,以确保焊接质量;4.确保焊接场地的通风良好,避免有害气体的产生,保障工作人员的健康。
二、焊接热处理工艺焊接热处理的工艺主要包括预热、焊接、保温和冷却四个阶段,下面进行详细介绍:1. 预热阶段预热是焊接热处理中十分关键的一个步骤,它可以降低焊接时的残余应力和避免裂纹的产生。
预热温度一般为工件的50%~70%,持续时间根据材料的不同而有所差异,一般在30分钟到2小时之间。
预热完成后,应在短时间内进行焊接操作。
2. 焊接阶段焊接是焊接热处理的核心过程,需严格控制焊接电流、电压和焊接速度。
保持焊接过程中的稳定,避免焊接变形和焊缝质量不良。
焊接完成后,应及时进入下一个阶段。
3. 保温阶段在焊接完成后,需要对焊接部位进行保温处理,以保证焊缝中的金属晶粒得到充分再结晶。
保温温度一般为700℃~800℃,保温时间视工件材料和要求而定,一般在1小时到4小时之间。
4. 冷却阶段冷却是焊接热处理完成后的最后一个阶段,要求工件在特定的温度下进行缓慢冷却。
冷却速度不宜过快,以避免引起裂纹和应力集中。
在冷却的过程中,要及时检查工件表面是否有裂纹或其他质量问题,并采取相应措施。
三、验收和保养焊接热处理完成后,需要对焊接部位进行验收,检查焊接质量和强度是否符合要求,确保焊接效果良好。
同时,还需做好保养工作,定期清洁和润滑焊接设备和工具,延长其使用寿命。
结语通过专项施工方案的制定和严格执行,可以提高焊接热处理的效率和质量,确保焊接后的金属材料具有理想的性能和寿命。
焊接预热、后热、保温最佳解决方案
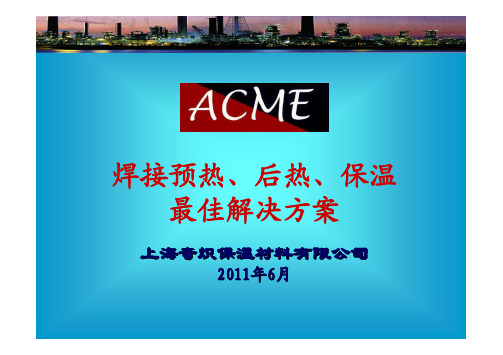
上海奇炽保温材料有限公司上海奇炽保温材料有限公司 2011 2011年 年66月 焊接预热、后热、保温最佳解决方案目 录一、背景介绍二、现状描述三、解决方案四、方案实施五、效果检测六、实际应用七、效果评估八、后热保温九、三维柔性组合焊接 工装系统十、客户群体一、背景介绍在焊接碳素钢、结构钢的工艺中,温度对焊接质量有着重大的 影响。
目前市面上的的高强结构钢基本上是低碳低合金钢或低碳低 合金调质钢。
特别是焊接强度级别≥390MPa的材料,要获得焊缝组 织优良的强韧性,防止冷裂纹,需要焊前预热,焊后低温后热处理 或消氢处理。
通常,焊接预热、消氢工艺是采用火焰或履带式电热器加热, 火焰加热完全靠人工掌握,加热温度极不均匀;履带式电热器与工 件的间隙不一致,导致加热不均匀;电源(220V)接头容易损坏, 有触电的危险;加热器本身生热,温度很高,容易烫伤操作工人;加热温度需要人工看护才能控制,容易过烧,导致产品报废或质量 不稳定,且加热时间长,能耗很高。
大型号焊炬火焰加热:采用气体燃烧的火焰进行加热,温度通过传导深入工件 内部,工件表面温度较高、内部温度较低,操作完全靠人工掌握,加 热温度极不均匀;二、现状描述电热器加热:采用电热丝的电阻发热,温度通过传导深入工件内部,工 件表面温度较高、内部温度较低,加热温度不均匀;虽然可以自动温控,但 是热电偶不能和电热板接触,否则会导致温度读书极大的偏差,因此加热过 程需要人工检测控制。
例如:某结构件钢管与接头的焊接预热、消氢新工艺是采用履带式电热 器加热,加热器与工件的间隙不一致,导致加热不均匀。
间隙不一致,导 致温度不均匀 工人装卸时容 易被烫伤三、解决方案应用感应加热工艺。
感应加热是利用电磁感应原理在被加热物体(工件)内部产生电流 (涡流),而使物体(工件)发热的方法。
感应加热的特点加热均匀 由于感应加热是钢材受到磁感应产生涡流而自身发热,所以加热温度很均 匀,这一特性对焊接的预热及后热消氢非常有利;生产率高 感应加热是钢材受到磁感应产生涡流而自身发热,不需热传导,设 备功率因素达到95%,加热时间短、生产效率高;控制精准 可根据各种温度曲线的需要进行编程,实现自动化精准控制;安全可靠 采用安全的航空接头,漏电保护装置,消除了安全隐患 ;设备为全空冷设计,降低了系统损耗,并彻底消除了设备来水冷却系统的故障;完善 的限制保护措施使得设备在各种工况下保持连续安全运行;使用期长 红外电热器由于是电热丝发热,所以电热丝很快会烧损;而感应线 圈本身不产生高温,不会被烧损,因此使用寿命很长。
高压蒸汽管道焊接及热处理施工方案
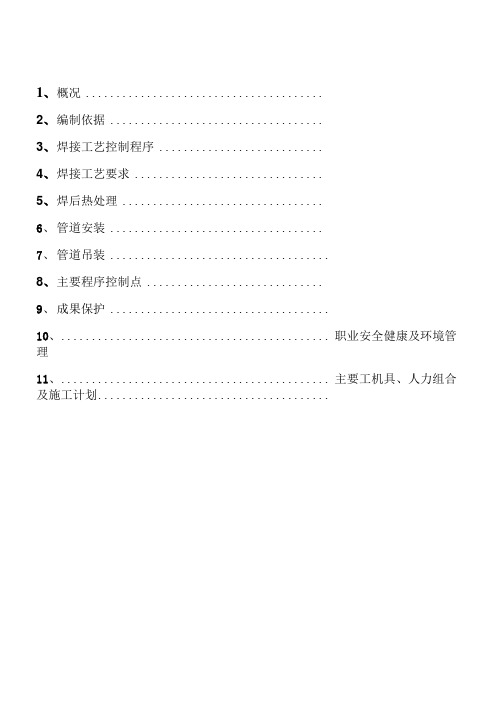
1、概况 .......................................2、编制依据 ...................................3、焊接工艺控制程序 ...........................4、焊接工艺要求 ...............................5、焊后热处理 .................................6、管道安装 ...................................7、管道吊装 ....................................8、主要程序控制点 .............................9、成果保护 ....................................10、............................................ 职业安全健康及环境管理11、............................................ 主要工机具、人力组合及施工计划......................................1、概况咸阳60万吨/年吨甲醇项目空分装置(271)及压缩机厂房(671 )区域共有高压蒸汽管线470米,管线材质均为12Cr1MoVG,管道主要尺寸主要为325*28及450*38的厚皮管道,此合金钢管道材料需要做焊前预热、焊后后热及焊后热处理,以降低焊接接头的残余应力,改善焊缝及近缝区的组织性能。
因此编制此方案指导合金钢管道的施工及热处理2、编制依据2.1《现场设备、工艺管道焊接工程施工及验收规范》GB50236-982.2《工业金属管道工程施工及验收规范》GB50235-972.3报甲方批准的焊接工艺评定2.4《锅炉压力容器、压力管道焊工考试与管理规则》国家质量监督局2.5 JB/T4709钢制压力容器焊接规程2.6华陆工程科技有限责任公司的热处理技术要求及文件3、焊接工艺控制程序4、焊接工艺要求4.1焊接工艺评定和焊工资格确认。
焊接热处理专项施工方案

焊接热处理专项施工方案本工程所有管道材质多样,各种合金钢材质的管道焊接热处理方案如下:1、焊前预热使用设备为ZWK-60智能温控箱,采用局部预热时 ,应防止局部应力过大.预热的范围为焊缝两侧各不小于焊件厚度的3倍,且不小于100mm.常用钢号推荐的预热温度见表 1表1常用钢号推荐的预热温度钢号预热温度,℃09MnD≥15015CrMoG合金钢管≥150需要预热的焊件在整个焊接过程中,层间温度应不低于预热温度。
中断焊接后需要继续焊接时,应重新预热。
预热时应在坡口两侧均匀进行,内外热透并防止局部过热。
加热区以外lOOmm范围内应予以保温,保证焊件内外外表均打到规定的预热温度。
每道焊缝焊接应尽可能一次焊完。
当中断焊接时,对冷裂纹敏感的焊件应及时采取后热、缓冷等措施。
重新施焊时,仍应按规定进行预热。
2、焊后热处理管道焊接接头的热处理在焊后及时进行,用ZWK-60智能温控箱电加热块加热至650°--700°,恒温45分钟左右后断电,用保温棉保温冷却24小时。
各种钢号的管道焊接接头焊后热处理见表 2表2常用钢号焊后热处理标准焊后热处理温度,℃钢号电弧焊580~62009MnD15CrMoG 650-700热处理加热范围为焊缝两侧各不少于焊缝宽度的三倍,且不少于25mm。
加热区以外的100mm范围应予保温,管道两端的管口应封闭,以防管内气体流动。
管壁厚度小于或等于25mm的焊接接头宜用挠性指状型加热器(镍铬电阻丝)加热,热处理时的加热速度、恒温时间、冷却速度,应符合以下要求:加热速度:升温至400℃后,加热速度应按5125/δ℃/h计算,且不大于220℃/h;恒温时间:碳素钢为每毫米壁厚恒温2~,合金钢为每毫米壁厚恒温3min,且总恒温时间不得少于30min。
在恒温期间内,最高与最低温度均应在热处理要求的温度范围内,且差值不得大于50℃;冷却速度:恒温后的冷却速度应按6500/δ℃/h计算,且不大于260℃/h。
焊前预热及焊后热处理施工方案(修)
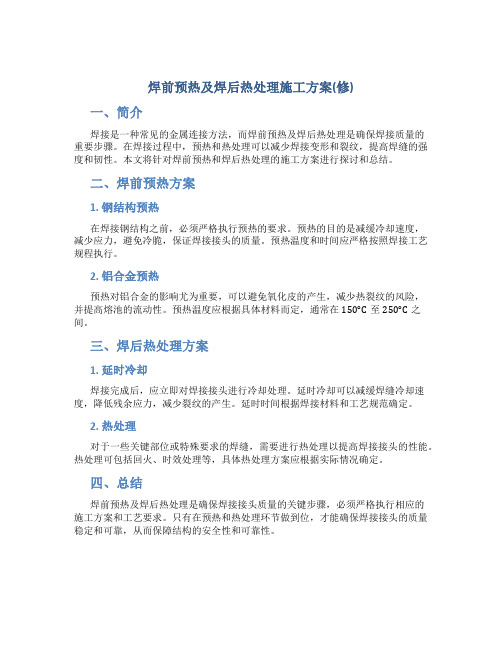
焊前预热及焊后热处理施工方案(修)
一、简介
焊接是一种常见的金属连接方法,而焊前预热及焊后热处理是确保焊接质量的
重要步骤。
在焊接过程中,预热和热处理可以减少焊接变形和裂纹,提高焊缝的强度和韧性。
本文将针对焊前预热和焊后热处理的施工方案进行探讨和总结。
二、焊前预热方案
1. 钢结构预热
在焊接钢结构之前,必须严格执行预热的要求。
预热的目的是减缓冷却速度,
减少应力,避免冷脆,保证焊接接头的质量。
预热温度和时间应严格按照焊接工艺规程执行。
2. 铝合金预热
预热对铝合金的影响尤为重要,可以避免氧化皮的产生,减少热裂纹的风险,
并提高熔池的流动性。
预热温度应根据具体材料而定,通常在150°C至250°C之间。
三、焊后热处理方案
1. 延时冷却
焊接完成后,应立即对焊接接头进行冷却处理。
延时冷却可以减缓焊缝冷却速度,降低残余应力,减少裂纹的产生。
延时时间根据焊接材料和工艺规范确定。
2. 热处理
对于一些关键部位或特殊要求的焊缝,需要进行热处理以提高焊接接头的性能。
热处理可包括回火、时效处理等,具体热处理方案应根据实际情况确定。
四、总结
焊前预热及焊后热处理是确保焊接接头质量的关键步骤,必须严格执行相应的
施工方案和工艺要求。
只有在预热和热处理环节做到位,才能确保焊接接头的质量稳定和可靠,从而保障结构的安全性和可靠性。
焊接热处理施工方案
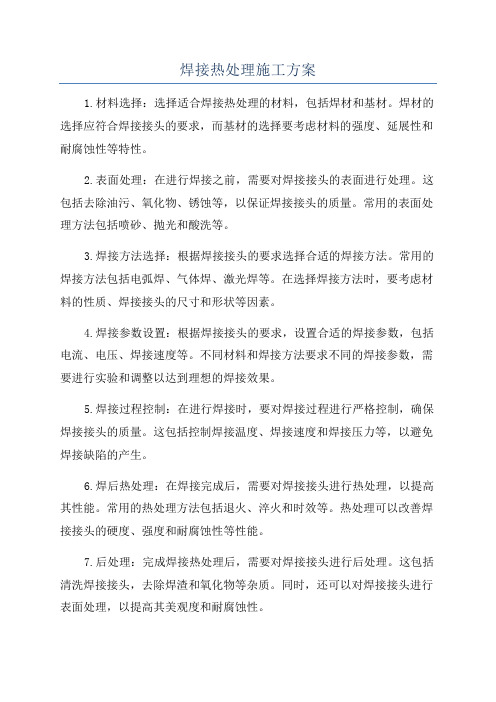
焊接热处理施工方案1.材料选择:选择适合焊接热处理的材料,包括焊材和基材。
焊材的选择应符合焊接接头的要求,而基材的选择要考虑材料的强度、延展性和耐腐蚀性等特性。
2.表面处理:在进行焊接之前,需要对焊接接头的表面进行处理。
这包括去除油污、氧化物、锈蚀等,以保证焊接接头的质量。
常用的表面处理方法包括喷砂、抛光和酸洗等。
3.焊接方法选择:根据焊接接头的要求选择合适的焊接方法。
常用的焊接方法包括电弧焊、气体焊、激光焊等。
在选择焊接方法时,要考虑材料的性质、焊接接头的尺寸和形状等因素。
4.焊接参数设置:根据焊接接头的要求,设置合适的焊接参数,包括电流、电压、焊接速度等。
不同材料和焊接方法要求不同的焊接参数,需要进行实验和调整以达到理想的焊接效果。
5.焊接过程控制:在进行焊接时,要对焊接过程进行严格控制,确保焊接接头的质量。
这包括控制焊接温度、焊接速度和焊接压力等,以避免焊接缺陷的产生。
6.焊后热处理:在焊接完成后,需要对焊接接头进行热处理,以提高其性能。
常用的热处理方法包括退火、淬火和时效等。
热处理可以改善焊接接头的硬度、强度和耐腐蚀性等性能。
7.后处理:完成焊接热处理后,需要对焊接接头进行后处理。
这包括清洗焊接接头,去除焊渣和氧化物等杂质。
同时,还可以对焊接接头进行表面处理,以提高其美观度和耐腐蚀性。
总之,焊接热处理施工需要经过材料选择、表面处理、焊接方法选择、焊接参数设置、焊接过程控制、焊后热处理和后处理等步骤。
通过严格控制每个环节,可以保证焊接接头的质量和性能。
同时,还需要根据具体的焊接要求和材料特性进行适当的调整和改进。
dlt819火力发电厂焊接热处理规程

dlt819火力发电厂焊接热处理规程一、引言焊接热处理是dlt819火力发电厂中重要的工艺环节之一。
通过对焊接接头进行热处理,可以改善接头的力学性能和耐热性能,确保设备在高温和高压环境下的安全稳定运行。
本规程旨在规范dlt819火力发电厂焊接热处理工作,确保焊接接头的质量和可靠性。
二、焊接热处理的目的和原则1. 目的:提高焊接接头的材料性能,消除焊接应力,改善接头的力学性能和耐热性能。
2. 原则:按照工艺要求进行焊接热处理,确保焊接接头的质量和可靠性。
三、焊接热处理的工艺流程1. 准备工作:检查焊接接头的质量,确保焊接接头满足热处理要求。
2. 加热:将焊接接头放入炉内,根据工艺要求进行加热。
加热温度和时间应根据焊接接头的材料和规格确定。
3. 保温:在加热到达设定温度后,保持一定时间,使焊接接头达到均匀的温度分布。
4. 冷却:将焊接接头从炉内取出,进行自然冷却或采用其他冷却方式,确保焊接接头冷却均匀。
5. 检验:对焊接接头进行质量检验,确保焊接接头的质量符合要求。
6. 记录:对焊接热处理的工艺参数和质量检验结果进行记录,建立档案。
四、焊接热处理的工艺参数1. 加热温度:根据焊接接头的材料和规格确定加热温度,确保焊接接头达到适当的温度。
2. 保温时间:根据焊接接头的材料和厚度确定保温时间,使焊接接头达到均匀的温度分布。
3. 冷却方式:根据焊接接头的材料和要求选择合适的冷却方式,确保焊接接头冷却均匀。
五、焊接热处理的质量控制1. 焊接接头的质量检验:对焊接接头进行力学性能测试、耐热性能测试等,确保焊接接头的质量符合要求。
2. 焊接热处理过程的监控:对焊接热处理的工艺参数进行实时监控,确保焊接热处理过程的稳定性和可靠性。
3. 焊接热处理的记录和档案管理:对焊接热处理的工艺参数和质量检验结果进行记录和档案管理,以便后续跟踪和分析。
六、焊接热处理的安全措施1. 操作人员应穿戴符合要求的个人防护装备,遵守操作规程,确保人身安全。
P92焊接和热处理技术方案
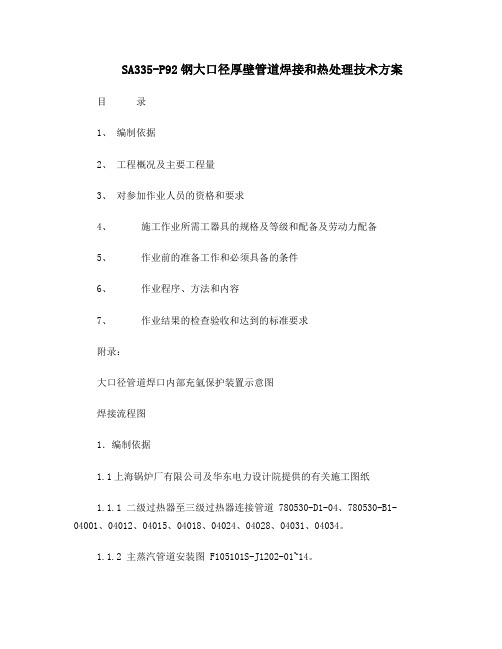
SA335-P92钢大口径厚壁管道焊接和热处理技术方案目录1、编制依据2、工程概况及主要工程量3、对参加作业人员的资格和要求4、施工作业所需工器具的规格及等级和配备及劳动力配备5、作业前的准备工作和必须具备的条件6、作业程序、方法和内容7、作业结果的检查验收和达到的标准要求附录:大口径管道焊口内部充氩保护装置示意图焊接流程图1.编制依据1.1上海锅炉厂有限公司及华东电力设计院提供的有关施工图纸1.1.1 二级过热器至三级过热器连接管道 780530-D1-04、780530-B1-04001、04012、04015、04018、04024、04028、04031、04034。
1.1.2 主蒸汽管道安装图 F105101S-J1202-01~14。
1.1.3 主蒸汽管道安装图 F105101S-J1203-01~8。
1.2技术规范、检验标准、验收依据。
1.2.1火力发电厂焊接技术规程 DL/T869-20041.2.2火力发电厂金属技术监督规程 DL438-20001.2.3火电施工质量检验及评定标准(焊接篇)1.2.4钢制承压管道对接焊接接头射线检验技术规程 DL/T 821-20021.2.5管道焊接接头超声波检验技术规程 DL/T 820-20021.2.6焊接工艺评定规程 DL/T868-20041.2.7蒸汽锅炉安全技术监察规程劳部发【1996】276号1.2.8压力容器安全技术监察规程劳锅字【1990】8号1.2.9电力锅炉压力容器安全监督管理工作规定国电总【2002】465号1.2.10电力工业锅炉压力容器监察规程 DL/T612-19961.2.11电站锅炉压力容器检验规程 DL/T647-20041.2.12压力容器安全质量检验规则劳锅字【1990】10号1.2.13 SA335-P92钢大口径厚壁管道焊接及热处理工艺研究报告上海电力建设有限责任公司2.工程概况及主要工程量。
外高桥第三发电厂2×1000MW机组中SA335-P92管道有三路,一为主蒸汽管道,由华东电力设计院设计,其规格为ф546*92,焊口数量约为52只;二为热再热蒸汽管道,由华东电力设计院设计,其规格为ф747*40,焊口数量约为61只;二为锅炉岛部分的二级过热器至三级过热器连接管道由锅炉厂供货其规格为ф457*65、ф457*70,焊口数量为28只。
- 1、下载文档前请自行甄别文档内容的完整性,平台不提供额外的编辑、内容补充、找答案等附加服务。
- 2、"仅部分预览"的文档,不可在线预览部分如存在完整性等问题,可反馈申请退款(可完整预览的文档不适用该条件!)。
- 3、如文档侵犯您的权益,请联系客服反馈,我们会尽快为您处理(人工客服工作时间:9:00-18:30)。
4.5.7.焊接返修 1 缺陷返修前应采用无损检测方法进行缺陷准确定位。缺陷消除采 用砂轮打磨方法,磨槽需修整成适合补焊的形状,并经检查或无 损检测确认缺陷已被清除后方可补焊。 2 返修补焊应严格执行焊接工艺指导书,对特殊情况下的返修应根 据要求编制返修方案(含焊补工艺)。 3 补焊方法采用钨极氩弧焊或手工电弧焊,且与正式焊接相同的焊 接工艺。 4 对有焊后热处理要求的焊缝,返修工作应在热处理前完成,否则 返修后应重新进行热处理。 5 返修部位应按原探伤方法进行检验。同一部位的返修次数不宜超 过两次。若超次返修应分析原因、制定超次返修措施,并经项目 技术负责人批准后方可实施。 6 应在设备焊缝布置图上和返修记录中标注焊缝返修位置、返修次 数和返修结果。
目
录
一、概述 二、编制依据 三、施工程序 四、施工方法、技术措施、 4.1.施工准备 4.2.分段设备组对检验 4.3. 焊接坡口制备 4.4设备组对要求 4.5.设备组对焊接 4.6.焊接检验 4.7.焊缝热处理加固 4.8.焊缝热处理 五、工程质量目标及质保措施、质量控制点 六、劳动力需用计划及技术能要求 七、主要机具、计量工具一览表 八、雨季、暑季施工技术措施 九、职业安全卫生与环境管理
坡口尺寸符合图样要求,坡口面上不得有裂纹、分层、夹渣等缺 陷.
对于坡口形式,若设计文件有规定时,可按设计文件执行,若设 计文件无规定时如下图所示: Δ=16 对接坡口型式为V型单面坡口,坡口各部分尺寸
α C P T
Δ=38、50 对接坡口型式为U型单面坡口,坡口各部分尺寸如下图所 示:R=6mm
α
4.6.焊接检验 4.6.1. 设备组焊完毕后,应对其外观检查,表面不得有裂纹、气孔、弧
坑、和夹渣等缺陷,熔渣、飞溅应及时清干净。焊接接头咬边的连 续长度不得大于100mm,焊接接头两侧咬边的总长不得超过该焊接接 头总长的10%。咬边深度不得大于0.5mm。焊缝高度:单面坡口时 e1=0-10%δ且≤3mm、e2≤1.5mm 4.6.2.设备焊接后应及时进行焊缝的射线照相检验,焊缝检测比例按图 纸要求。 4.6.3.所有焊缝随时接受甲方代表的检查。 4.6.4.当抽样检验未发现需要返修的焊缝缺陷时,则该次抽样代表的一 批焊缝应认为全部合格;当抽样检验发现需要返修的焊缝缺陷时, 除返修该焊缝外,还应采取原规定方法按下列规定进一步检验: A、每出现一道不合格焊缝应再检验两道该焊工所焊的同一批焊
设备 位号
筒体同 一断面 处的不 圆度
外圆周长
筒体 高度
任意3m长 筒体直线 度mm/总 直线度mm
塔体垂 直度
2201 ≤25 ≤±15 ±40 ≤3/29.8 ≤30
2202 ≤25 2204 ≤25 2205 ≤25
≤±18 ≤±15 ≤±15
±60 ±60 ±40
≤3/36.8 ≤30 ≤3/40 ≤30 ≤3/31 ≤30
艺。手工电孤焊时注意层间清渣,以防止产生气孔、夹渣等缺陷,如有 缺陷应立即铲除重焊。
f、焊接环境出现下列任一情况,需要采取措施,否则停止焊接 工作。
手工焊时风速大于10m/s;相对湿度大于90%;雨、雪环境。 g、塔组装时的点固焊,应符合下列规定: 点固焊应在基层坡口内进行; 点固焊的焊接工艺应与正式焊接的要求相同; 点固焊的焊道长度应为30-50 mm,焊道应有足够的强度,点固焊焊 接宜采用回焊法,使引弧和熄弧点均在焊道内 组对卡具及吊耳的焊接工艺应与正式焊接要求相同,卡具及吊耳拆 除后,应对其焊缝的残留痕迹进行打磨修整。
十、文明施工措施
设备组对焊接与热处理方案
一、概述 1.1中国石化股份公司安庆分公司化肥原料结构调整及炼油化工资源 优化工程,
按照大件设备吊装组对方案分段数据统计如下表所示:
设备 位号
设备名称
第 一 段
H2S 第 C2201 吸收 二
塔段
第 三 段
第 一 段
CO2 第 C2202 吸收 二
塔段
第 三 段
δ=16/12
29658
09MnNiDR
65000
第 一 φ3700 δ=16 18550 20R 段
65000
第
热再 C2205 吸收
二
φ3700
δ=16
17000
20R
塔段
55000
第 三 φ3700 δ=16/22 18860 20R 段
65000
1.2.根据设计图纸要求现场组对焊缝焊后需进行消除应力热处理。 二、编制依据
a、筒体不直度检查,通过中心线的铅直度即沿周围00 900 1800 2700四个部位拉φ0.5mm细钢丝进行测量,测量的位置离纵缝的距离不 小于100mm;当筒体厚度不同时,计算不直度应减去厚度差。允许偏差 见上表
b、筒体不圆度允许偏差见上表。
4.5.设备组对焊接 4.5.1焊接采用氩电联焊。 4.5.2焊条选用见附表。
4.3. 焊接坡口制备 3.3 坡口宜采用机械方法加工; 当采用火焰切割时,应采用机械方 法清除热影响区和谵硬层,并将表面打磨光滑,火焰切割时的环境 温度不得低于0℃。 3.4 坡口表面应按JB4730-1994《压力容器无损检测》进行100%磁 粉检测,Ι级合格。 3.5 容器施焊前应按JB4708-2000《钢制压力容器焊接工艺评定》进 行焊接工艺评定试验。焊接工艺评定包括焊缝和热影响区的低温夏 比(V型缺口)冲击试验,试验温度为-70℃;当板厚≤40mm时,焊 缝和热影响区各一组,每组三个冲击试样;当板厚>40mm时,冲击 试样的数量和位置按JB4744-2000《钢制压力容量产品焊接试板的力 学性能检验》中表1及图8和图9的规定,即焊缝两组,热影响区一 组,每组三个试样;冲击试验时,每组三个试样(试样尺寸为 10*10*55)的冲击功平均值必须≥24 J,其中只允许有一个试样的冲 击功低于规定值,但不得低于规定值的70%。 3.9 引弧须采用引弧板或在坡口内引弧,不得在非焊接部位引弧。 因引弧或电弧擦伤所产生的弧坑和疤痕要打磨平滑,并用磁粉检 测。 3.13 焊接接头厚度大于16mm的容器或部件,应进行焊后消除应力热 处理,所有预焊件均应在热处理前焊于容器上,热处理后不得再进 行施焊。 3.14 每台低温容器都应制备产品焊接试板,试板的尺寸、试样截
2.1《石油化工钢制塔、容器现场组焊施工工艺标准》SH3524-1999
2.2《钢制压力容器》GB150-1998
2.3《钢制塔式容器》JB4710-92
2.4《钢制压力容器焊接工艺评定》JB4708-2000
2.5《钢制压力容器焊接工艺规程》JB/T4709-2000
2.6《压力容器安全技术监察规程》
在有效期之内。 b. 坡口及其内外侧表面不小于100mm范围内的氧化铁、水、锈、
油等杂质清理干净,且不得有裂纹、夹层等缺陷,且将影响焊接质量的 凹凸不平处打磨平整。
c. 焊条、焊丝包装完好,产品说明书、合格证明书和质量保证 书齐全。
d、焊工领用焊条要使用焊条保温筒。 e、筒体对接焊缝的焊接方法采用手工电弧焊,焊接过程中应保 证起弧和收弧 的质量,收弧是应将弧坑填满。多层焊的层间接头应错开。在保证焊透 和熔合的良好条件下,采用小电流、短电弧、快焊速和多层多道焊工
处理焊缝上段 → 稳固检查 → 焊缝热处理 → 焊缝硬度检测
四、施工方法、技术措施、
4.1.施工准备
4.1.1焊接工艺评定
焊接工艺评定试验在于测定焊件具有要求的使用性能。本工程
中设备材质:20R
、09MnNiDR按《钢制压力容器焊接工艺评定》
JB4708-2000进行评定。
4.1.2.焊工技能评定
焊工技能评定在于测定焊工具有熔敷优质焊缝金属的能力。
δ=55 18831 09MnNiDR 150000
δ=55 21628 09MnNiDR 155000
一 φ3900 δ=24/20 25010 09MnNiDR 90000 段
C2204
再吸 收塔
第 二
φ3900 δ=20/16 20513 09MnNiDR
70000
段
第 三 段
φ3900/ φ2600
2.7《压力容器无损检测》JB4730-94
2.8设计提供的设备图纸及技术资料
三、施工程序
制作安装临时平台→按照大件设备吊装方案将分段设备在空中就位→
组对卡具制作安装 → 对口方位调整 → 用经纬仪(或细钢丝)检查铅
直度并调整 → 用组对卡具调整对口间隙及错边 →组对固定后检查 →
点焊 → 正式焊接 → 焊缝外观检查 →无损检验 → 750T吊车稳固热
设备位号 设备材质
2201/2/3 2204
09MnNiDR 20R
选用焊材
焊丝
焊条
W807Ni
J427
备注
4.5.3.焊接时应按焊接工艺规程(WPS)规定的焊接参数焊接。焊接工 艺规程依据相应的焊接工艺评定报告(PQR)进行的焊接工艺试验。 4.5.4焊接基本要求: a. 所有焊工必须持证作业,合格证项目能满足于本工程使用且
C P T
α
R
设备壁厚 T
9~26 38~50ቤተ መጻሕፍቲ ባይዱ
坡口尺
间 隙 C(mm) 钝 边 P(mm)
0~3
0~3
2~3
1.5~2
寸 坡口角度α(°)
55~65 10~15
4.4设备组对要求 4.4.1设备组对时,其环焊缝的对口错边量应≤1/8δ。 4.4.2.圆筒对接环向焊缝接头形成的棱角E,用长度不小于300mm钢直 尺检查,其E值不得大于5mm。 4.4.3.组对后的检查 设备组对完毕后,应进行筒体不直度、不圆度检查:
4.5.5焊接顺序
焊工A从1#向4#施焊;焊工B从下1#向2#方向施焊; 焊工C从4#向3#施焊。焊工D从2#向3#施焊。
4.5.6.低温钢的焊接要点 焊条使用前于350~400℃保温2h烘干,焊丝去除油污。 制造过程中,还应从其他各方面尽量防止接头中的过热组织和工件 上的应力集中。 返修工艺的制定及实施应特别严格;不得在非焊接部位任意打弧; 可在焊缝或坡口内引弧,但引弧处应受到重熔,弧坑应填满;焊缝 应成形良好,避免咬边; 应注意避免焊接缺陷(如弧坑、未焊透、咬边和焊缝成形不良等) 产生应力集中源,并应及时修补缺陷,以防止在长期低温操作条件 下产生裂纹倾向。焊缝表面应打磨圆滑过渡,不能留有尖角。