循环流化床锅炉设计工艺分析
循环流化床锅炉控制系统的分析与设计

摘要:循环流化床锅炉又被称为CFB锅炉,循环流化床锅炉技术是近十几年发展迅速的燃烧技术,由于锅炉是采用燃油燃气进行燃烧,而循环流化床锅炉技术具有污染小、安全可靠、适应性广等明显优点,其作为一种高效的清洁燃煤技术,其效用受到人们广泛的关注,在燃煤技术当中占据了有力地位。
随着循环流化床锅炉商业化的快速发展,人们提出了循环流化床锅炉技术自动化运行概念。
本文通过对循环流化床锅炉控制系统的分析与研究,实现对循环流化床锅炉技术自动化的设计,有利于提高循环流化床锅炉的监控管理功能。
关键词:循环流化床锅炉自动控制技术优点1循环流化床锅炉燃烧技术的概念循环流化床锅炉技术具有污染小、安全可靠、燃烧适应性广等特点,其根据自身优势活跃在工业锅炉及废弃物处理等领域,循环流化床锅炉技术拥有很大的商业发展空间。
循环流化床燃烧技术作为一种新型的燃烧技术,其燃烧系统较为复杂,燃料燃烧形成飞灰始终流动在锅炉燃烧系统当中,流动状态的燃烧飞灰浓度较大容易影响其他控制技术的发挥,所以在循环流化床锅炉工作的过程中还需要人工进行操作调节。
如何调节各个参数之间的影响,使其控制系统操作变得稍微简单一些,对循环流化床锅炉控制系统进行研究与分析,设计合理有效的循环流化床锅炉控制系统是目前需要解决的问题。
2循环流化床锅炉控制系统的分析2.1燃烧控制系统循环流化床锅炉燃烧控制系统要保证燃烧过程中热量与负荷相适应,减少燃料不必要的损耗,从而实现锅炉燃烧控制系统的安全及高效运行。
锅炉燃烧控制系统具体可表现为对稳定的蒸汽压力及料床温度、锅炉燃烧的经济与环保、控制炉膛压力及床高范围等方面的控制。
循环流化床锅炉燃烧机理比较复杂,各参数之间耦合关系难以控制,被调参数容易同时受到多个调节参数的影响,给操控和受控变量配对造成了困难,所以循环流化床锅炉自动化控制难于一般锅炉的控制。
目前设计的燃烧控制系统比较简单,在燃烧自动控制系统运作的过程中,容易受到各个环节的影响,导致燃烧自动控制系统无法发挥出自动化控制的效用,最后还是依靠人工手动操作控制系统完成。
循环流化床烟气脱硫工艺设计 资料

1、前言循环流化床燃烧是指炉膛内高速气流与所携带的稠密悬浮颗粒充分接触,同时大量高温颗粒从烟气中分离后重新送回炉膛的燃烧过程。
循环流化床锅炉的脱硫是一种炉内燃烧脱硫工艺,以石灰石为脱硫吸收剂,与石油焦中的硫份反应生成硫酸钙,达到脱硫的目的。
较低的炉床温度(850°C〜900°C),燃料适应性强,特别适合较高含硫燃料,脱硫率可达80%〜95%,使清洁燃烧成为可能。
2、循环流化床内燃烧过程石油焦颗粒在循环流化床的燃烧是流化床锅炉内所发生的最基本而又最为重要的过程。
当焦粒进入循环流化床后,一般会发生如下过程:①颗粒在高温床料内加热并干燥;②热解及挥发份燃烧;③颗粒膨胀及一级破碎;④焦粒燃烧伴随二级破碎和磨损。
符合一定粒径要求的焦粒在循环流化床锅炉内受流体动力作用,被存留在炉膛内重复循环的850C〜900C的高温床料强烈掺混和加热,然后发生燃烧。
受一次风的流化作用,炉内床料随之流化,并充斥于整个炉膛空间。
床料密度沿床高呈梯度分布,上部为稀相区,下部为密相区,中间为过渡区。
上部稀相区内的颗粒在炉膛出口,被烟气携带进入旋风分离器,较大颗粒的物料被分离下来,经回料腿及J阀重新回入炉膛继续循环燃烧,此谓外循环;细颗粒的物料随烟气离开旋风分离器,经尾部烟道换热吸受热量后,进入电除尘器除尘,然后排入烟囱,尘灰称为飞灰。
炉膛内中心区物料受一次风的流化携带,气固两相向上流动;密相区内的物料颗粒在气流作用下,沿炉膛四壁呈环形分布,并沿壁面向下流动,上升区与下降区之间存在着强烈的固体粒子横向迁移和波动卷吸,形成了循环率很高的内循环。
物料内、外循环系统增加了燃料颗粒在炉膛内的停留时间,使燃料可以反复燃烧,直至燃尽。
循环流化床锅炉内的物料参与了外循环和内循环两种循环运动,整个燃烧过程和脱硫过程就是在这两种形式的循环运动的动态过程中逐步完成的。
3、循环流化床内脱硫机理循环流化床锅炉脱硫是一种炉内燃烧脱硫工艺,以石灰石为脱硫吸收剂,石油焦和石灰石自锅炉燃烧室下部送入,一次风从布风板下部送入,二次风从燃烧室中部送入。
循环流化床锅炉的构造及工作原理

隔热层分三层砌筑: 密封层 32mm 绝热层 60mm 不大于135mm 耐火层 不大于35mm
布风板的型式
风帽
风帽的作用:是使进入流化 床的空气产生第二次分流并 具有一定的动能,以减少初 始气泡的生成和使底部粗颗 粒产生强烈的扰动,避免粗 颗粒的沉积,减少冷渣含碳 损失。风帽还有产生足够的 压降、均匀布风的作用。
正常燃烧时,在一次风机的作用下,具有一定数量和动 能的空气,经床下启动燃烧器、水冷风室、床上风帽,将床 上物料(煤+炭火+返料灰+石灰石)吹起来,较大的颗粒在 其自身重力作用下向下跌落,与吹起来的粒子发生碰撞、产 生破碎,不断更新粒子的燃烧外表面,使燃烧即快又好。在 上升的火焰和炭火流中,既有分子团的不断形成与扩散,又 有物料的强烈碰撞与返混,使燃烧的炭火流就像金色的喷泉 充满整个炉膛空间。由于流化速度比较高,离开炉膛的烟气 要带走一定数量的灰,经过旋风分离器、上料腿、回料阀、 下料腿,再一次回到床上参加流化、燃烧、传热,顾名思义 ,叫循环流化床锅炉。
回料阀的阻 力:
回料阀空床阻力4000帕-5000帕左右
回料阀的内部工作状 态:
回料器内的两个状态(松 动、流化)
CFB锅炉燃烧过程中的七个状态
• 炉膛浓相区--------紊流状态 • 炉膛稀相区--------高速流化状态 • 旋风分离器--------旋转状态 • 上料腿------------移动状态(不是流动) • 回料器------------鼓泡状态+流化状态 • 下料腿------------流动状态
罗茨风机出力可自动 调节,返料灰多风压自动 加大,返料灰少风压自动 减小。
返料风机采用的运行 方式:
循环流化床锅炉的原理与设计

循环流化床锅炉中的流化过程
循环流化床锅炉中的流化过程包括以下几个特点
• 炉膛内充满颗粒燃料,气流速度较低 • 燃料颗粒与空气充分混合,燃烧效率高 • 流化床内温度分布均匀,传热效果好
流化过程是指固体颗粒在流体中运动,形成类似流体的状态
• 当气流速度达到一定值时,固体颗粒开始悬浮并相互碰撞 • 这种状态有利于燃料的燃烧和热量的传递
循环流化床锅炉的脱硝技术
• 循环流化床锅炉的脱硝技术包括以下几个方面 • 选择性非催化还原(SNCR)技术:通过向炉内喷射氨水,实现NOx的还原 • 选择性催化还原(SCR)技术:通过设置催化剂层,对烟气进行脱硝处理
循05环流化床锅炉的运行与
维护
循环流化床锅炉的启动与停止操作
• 循环流化床锅炉的启动与停止操作需要遵循以下步骤 • 启动前进行设备检查,确保锅炉各部分正常 • 缓慢启动风机,向炉膛内加入燃料,实现燃料的流化 • 启动过程中注意观察炉膛内的温度和压力变化,确保锅炉稳定 运行 • 停止操作时,先停止燃料供应,然后降低风机转速,最后停止 风机运行
循环流化床锅炉的燃烧室设计
• 循环流化床锅炉的燃烧室设计需要考虑以下几个因素 • 燃烧室的尺寸和形状,以满足燃料燃烧和热量交换的需求 • 燃烧室的温度分布,以保证燃料的充分燃烧和热量的有效传递 • 燃烧室的气流组织,以实现燃料与空气的充分混合和燃烧产物 的排放
循环流化床锅炉的传热元件设计
• 循环流化床锅炉的传热元件设计需要考虑以下几个因素 • 传热元件的材料和结构,以满足锅炉温度和压力的要求 • 传热元件的热交换性能,以提高锅炉的热效率和适应性 • 传热元件的耐腐蚀性能,以延长锅炉的使用寿命
循环流化床锅炉的热交换原理
循环流化床锅炉的热交换原理主要依赖于传热元件
循环流化床锅炉工艺流程
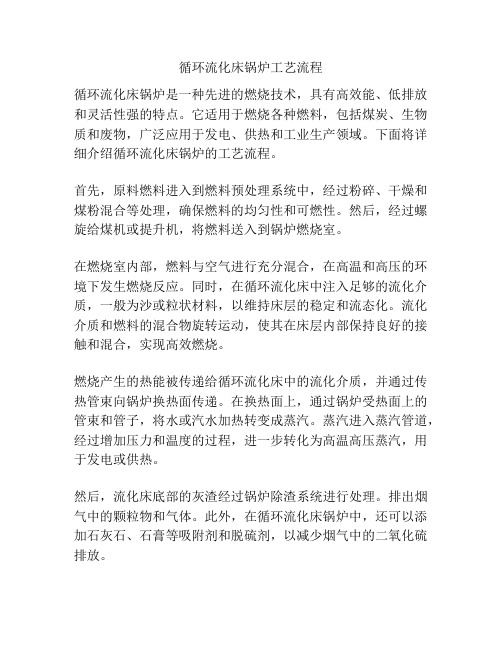
循环流化床锅炉工艺流程循环流化床锅炉是一种先进的燃烧技术,具有高效能、低排放和灵活性强的特点。
它适用于燃烧各种燃料,包括煤炭、生物质和废物,广泛应用于发电、供热和工业生产领域。
下面将详细介绍循环流化床锅炉的工艺流程。
首先,原料燃料进入到燃料预处理系统中,经过粉碎、干燥和煤粉混合等处理,确保燃料的均匀性和可燃性。
然后,经过螺旋给煤机或提升机,将燃料送入到锅炉燃烧室。
在燃烧室内部,燃料与空气进行充分混合,在高温和高压的环境下发生燃烧反应。
同时,在循环流化床中注入足够的流化介质,一般为沙或粒状材料,以维持床层的稳定和流态化。
流化介质和燃料的混合物旋转运动,使其在床层内部保持良好的接触和混合,实现高效燃烧。
燃烧产生的热能被传递给循环流化床中的流化介质,并通过传热管束向锅炉换热面传递。
在换热面上,通过锅炉受热面上的管束和管子,将水或汽水加热转变成蒸汽。
蒸汽进入蒸汽管道,经过增加压力和温度的过程,进一步转化为高温高压蒸汽,用于发电或供热。
然后,流化床底部的灰渣经过锅炉除渣系统进行处理。
排出烟气中的颗粒物和气体。
此外,在循环流化床锅炉中,还可以添加石灰石、石膏等吸附剂和脱硫剂,以减少烟气中的二氧化硫排放。
通过循环流化床的工艺流程,循环床锅炉具有以下几个优点。
首先,床层内部的混合和燃烧反应充分,可以实现高效燃烧,燃烧效率高,煤炭和其他燃料的利用率高。
其次,锅炉内部温度均匀,烟气温度低,燃烧时间长,有利于燃料彻底燃烧和污染物的降解。
此外,循环流化床锅炉灵活性强,适应多种燃料燃烧。
但是,循环流化床锅炉也存在一些局限性。
首先,床层内的颗粒流体化介质易于磨损,需要定期更换,增加了运行和维护成本。
其次,低速流化床锅炉烟气中的颗粒物排放量较高,对环境造成了一定的污染。
总之,循环流化床锅炉是一项具有很大应用潜力的燃烧技术。
通过优化工艺流程和持续创新,可以进一步提高循环流化床锅炉的经济性和环境友好性。
循环流化床锅炉简介配图讲解
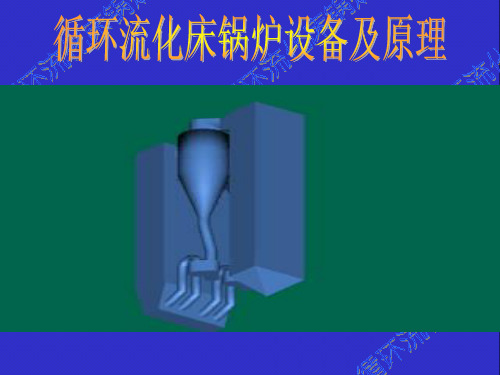
• 3.负荷调节性能好
–低负荷下仍可保持燃烧稳定; –负荷调节比达4:1,甚至可以压火备
• 流化床具有流体的某些性质
流化床类似流体的性质:
– 任一高度静压等于 此高度以上固体颗 粒重量
– 大而轻的物体浮在 床表面
– 床表面总保持水平 – 连通器作用
• “床”——反应场 所,支承物料(床
形物:机床;车床;流 化床;河床;苗床)
第一代流化床锅炉 —鼓泡床锅炉
二十世纪60年代初,出现了 “流化床锅炉”。
——循环流化床锅炉
“循环”的概念——飞 出炉膛的物料被气固分 离器收集,返回炉膛, 循环燃烧和利用。
• 循环流化床锅炉在保留 沸腾床锅炉的优点的基 础上,克服了其不足的 方面。
循环流化床锅炉的结构特点
• 1、炉膛 • 2、旋风分离器 • 3、过热器 • 4、外置式换热器 • 5、煤仓 • 6、返料装置 • 7、石灰石进料口 • 8、灰冷却器 • 9、省煤器 • 10、空气预热 • 11、除尘器 • 12、引风机 • 13、尾部烟道 • 14、汽包
• 汽冷式旋风分离器分离的床料和灰向下流经衬 有耐火材料的回料立管排出到“J”阀。 “J”阀 有两个关键功能,使再循环床料从旋风分离器 连续稳定的回送到炉膛,提供旋风分离器的负 压和下燃料室正压之间的密封。分离器的静压 非常接近大气压,而燃料回料点由于一次风和 二次风,压力非常高,故必须实现他们之间的 密封,否则,燃烧室烟气将回流到分离器。 “J”阀通过分离器底部出口的物料在立管中建 立的料位差,来实现这个目的,物料返送的动 力源于回料器上升段和下降段的不同配风,使 上升段和下降段呈现不同的流态化
循环流化床锅炉掺烧气化炉细灰渣设计与分析

循环流化床锅炉掺烧气化炉细灰渣设计与分析循环流化床锅炉掺烧气化炉细灰渣是指在循环流化床锅炉中,将不同能源的固体燃料进行气化,产生的灰渣进行细灰处理和利用的过程。
这种技术可以有效提高锅炉的热效率,减少污染物的排放,并且可以实现废弃物的资源化利用。
本文将对循环流化床锅炉掺烧气化炉细灰渣的设计与分析进行详细介绍。
循环流化床锅炉掺烧气化炉细灰渣的设计需要考虑以下几个方面:气化温度、氧化剂与燃料的比例、氧化剂的类型和粒径、废气处理等。
合理设置气化温度可以提高气化效果,增加燃烧反应速率,同时降低气化过程中的污染物排放。
通过调节氧化剂与燃料的比例可以调整气化过程中产生的燃料气化效率和产物分布。
选择适当的氧化剂类型和粒径可以改善气化炉的反应动力学和传热特性。
废气处理是循环流化床锅炉掺烧气化炉细灰渣设计的重要环节,可以通过喷射吸附剂、湿式废气处理装置和高温脱硝等方式实现。
对于循环流化床锅炉掺烧气化炉细灰渣的设计,还需要进行细灰渣的分析。
细灰渣是气化过程中产生的固体残渣,其中含有大量的未完全气化物质和重金属元素。
通过对细灰渣的成分分析和物理特性测试,可以确定其适用的综合利用方式。
对于未完全气化物质的成分分析,可以进一步优化气化过程的参数设置,提高气化效率。
对于重金属元素的分析,可以评估细灰渣对环境的影响,并制定相应的治理措施。
除了细灰渣的分析,循环流化床锅炉掺烧气化炉还需要进行能耗分析和经济性评价。
通过能耗分析可以评估气化过程中的能量损失和能源利用效率,进而优化工艺设计,提高能量利用效率。
经济性评价则可以评估该技术在工程应用中的经济效益和可行性,包括投资、运行成本和收益等方面的考虑。
循环流化床锅炉掺烧气化炉细灰渣的设计与分析需要综合考虑气化温度、氧化剂与燃料的比例、氧化剂的类型和粒径、废气处理等方面的因素;对细灰渣进行成分分析和物理特性测试,制定适用的综合利用方式;进行能耗分析和经济性评价,提高能量利用效率和经济效益。
循环流化床锅炉设计与计算研究
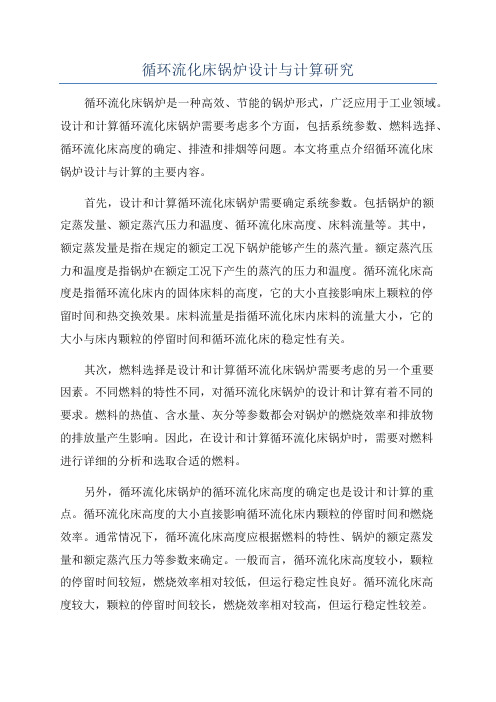
循环流化床锅炉设计与计算研究循环流化床锅炉是一种高效、节能的锅炉形式,广泛应用于工业领域。
设计和计算循环流化床锅炉需要考虑多个方面,包括系统参数、燃料选择、循环流化床高度的确定、排渣和排烟等问题。
本文将重点介绍循环流化床锅炉设计与计算的主要内容。
首先,设计和计算循环流化床锅炉需要确定系统参数。
包括锅炉的额定蒸发量、额定蒸汽压力和温度、循环流化床高度、床料流量等。
其中,额定蒸发量是指在规定的额定工况下锅炉能够产生的蒸汽量。
额定蒸汽压力和温度是指锅炉在额定工况下产生的蒸汽的压力和温度。
循环流化床高度是指循环流化床内的固体床料的高度,它的大小直接影响床上颗粒的停留时间和热交换效果。
床料流量是指循环流化床内床料的流量大小,它的大小与床内颗粒的停留时间和循环流化床的稳定性有关。
其次,燃料选择是设计和计算循环流化床锅炉需要考虑的另一个重要因素。
不同燃料的特性不同,对循环流化床锅炉的设计和计算有着不同的要求。
燃料的热值、含水量、灰分等参数都会对锅炉的燃烧效率和排放物的排放量产生影响。
因此,在设计和计算循环流化床锅炉时,需要对燃料进行详细的分析和选取合适的燃料。
另外,循环流化床锅炉的循环流化床高度的确定也是设计和计算的重点。
循环流化床高度的大小直接影响循环流化床内颗粒的停留时间和燃烧效率。
通常情况下,循环流化床高度应根据燃料的特性、锅炉的额定蒸发量和额定蒸汽压力等参数来确定。
一般而言,循环流化床高度较小,颗粒的停留时间较短,燃烧效率相对较低,但运行稳定性良好。
循环流化床高度较大,颗粒的停留时间较长,燃烧效率相对较高,但运行稳定性较差。
因此,在设计和计算循环流化床锅炉时,需要综合考虑这些因素,确定合适的循环流化床高度。
最后,设计和计算循环流化床锅炉还需要考虑排渣和排烟等问题。
循环流化床锅炉的特点是床内颗粒可以循环使用,但床表面会聚集一定的灰积,需要及时清除。
因此,设计和计算循环流化床锅炉时,需要考虑灰积的处理和排渣系统的设计。
- 1、下载文档前请自行甄别文档内容的完整性,平台不提供额外的编辑、内容补充、找答案等附加服务。
- 2、"仅部分预览"的文档,不可在线预览部分如存在完整性等问题,可反馈申请退款(可完整预览的文档不适用该条件!)。
- 3、如文档侵犯您的权益,请联系客服反馈,我们会尽快为您处理(人工客服工作时间:9:00-18:30)。
循环流化床锅炉设计工艺分析
发表时间:2019-07-05T11:57:11.573Z 来源:《电力设备》2019年第4期作者:黄凯[导读] 摘要:循环流化床锅炉应用的是工业化程度较高的洁净煤燃烧技术,在我国对工业生产环保要求越来越严的背景下,循环流化床锅炉做出了巨大的贡献。
(武汉锅炉股份有限公司湖北武汉 430205)摘要:循环流化床锅炉应用的是工业化程度较高的洁净煤燃烧技术,在我国对工业生产环保要求越来越严的背景下,循环流化床锅炉做出了巨大的贡献。
对于煤矸石、油页岩、城市垃圾以及废弃物等难燃的固体燃料,都可以作为循环流化床锅炉的燃料,不仅具有较高的燃烧效率,而且污染较小。
因为循环流化床锅炉采用流态化燃烧,在设计运行中会存在磨损、结焦、物料循环不畅等问题,经过技术的不
断改进,这些问题都得到了很好的解决,下面对此进行阐述。
关键词:循环流化床;锅炉;工艺循环流化床锅炉控制系统是一类新型的锅炉控制系统,在实际的应用中发挥重要作用。
在生产环节中,为了可以提升循环流化床锅炉系统的性能,应该完善控制系统的分析,提升循环流化床锅炉设计方案。
1循环流化床锅炉设计运行中的常见问题 1.1磨损问题
循环流化床锅炉是把固态的燃料进行流体化处理,让燃料具有液体的流动性质,在其中可以加入煤矸石以及石灰等物质,可以达到除硫的效果。
因为燃料是以液态化的方式流动的固体,所以这些颗粒在流动的过程中,会与接触到的设备发生碰撞,从而造成一定的磨损。
循环流化床锅炉在运行的过程中,床料流动的速度越快、浓度越大,对锅炉受热面和耐火材料的表面所造成的冲击就越加强烈,从而导致这些部件的磨损。
在床料流动的过程中,也会伴随温度的循环流动,在耐火构件热膨胀系数不同的情况下,受到机械应力的影响会对炉内耐火构件造成磨损。
1.2结焦问题
循环流化床锅炉结焦是设计运行中的常见问题,结焦不仅降低锅炉的运行效率,同时还威胁到锅炉运行的安全性。
形成结焦的原因主要是旋风分离器超温、床料结块、返料器堵塞等,如果燃烧室温度超过灰的变形温度,会导致炉内未燃碳重新燃烧,在床温上涨的情况下形成结焦。
如果物料循环系统漏风,热床料中的可燃物与氧气接触重新燃烧,但由于热量不足就会形成局部超温结焦。
如果在启动期间煤油混烧时间较长,在风量与燃煤颗粒匹配不佳等情况下,燃烧速度过慢就会导致未完全燃烧的油渣与床料板结成块,在流化不良的情况下,形成松散的渣块。
在返料器运行过程中如果因为堵塞而突然停止工作,由于炉内循环物料不足就会导致温度升高,从而导致高温结焦。
1.3旋风分离器的问题旋风分离器的主要功能就是进行气固分离,保证循环流化床锅炉的正常运行。
旋风分离器结构比较简单,其运行效率主要与形状、结构、进口气体温度、入口烟温、入口颗粒等因素有关。
如果分离器的运行效率达不到设计值,就会出现未完全燃烧现象,直接影响到锅炉的燃烧效率。
在飞灰量较大的情况下,就会对尾部受热面造成严重的磨损,增加除灰设备的能耗。
如果进入循环回路中的灰量较少,就无法达到设计的循环量,无法有效控制床温,对锅炉满负荷运行以及炉膛传热产生一定的影响。
2循环流化床锅炉设计工艺分析
2.1循环床气固两相流动在循环床内,颗粒会聚集在一起,这些粒子团聚在一起,导致颗粒的体积和重量增大,产生非常大的自由沉降终端速度,在一定的气流速度下,粒子会顺着锅炉墙向下运动。
在粒子流动的环节中,气体和固体之间会产生非常大的相对速度,粒子会在锅炉壁上沉积。
在粒子团不断的聚集、下沉和上升的环节中,会形成内循环,导致锅炉内发生热量的交换。
粒子团会沿着锅炉壁下沉,锅炉内的内循环非常剧烈,导致锅炉的传热效果非常好,锅炉内的热量分布也非常均匀。
在850摄氏度的锅炉温度下,燃料和脱硫剂在短时间内会被加热到850摄氏度,燃烧效率非常高,而且在石灰石的作用下会产生脱硫反应,在合适的反应温度下实现燃料的二次循环。
在循环床内的任何位置,都可以实现良好的传热效果。
在循环过程中固体颗粒是向下运动的,但是颗粒的粒径比较大,可以降低颗粒的流动速度,防止炉壁发生严重的磨损情况。
在循环流化床锅炉悬浮段运行环节中,固体颗粒的流动不会呈现出快速流态化,此时的颗粒具有一定的浓度,并且会出现成团的现象。
循环流化床悬浮段中的燃料的分布不均匀,应该在采用热态测试的基础上,确保燃料的均匀分布。
2.2物料平衡理论及其应用固体骨料在循环系统中呈现出对传热的流动特征,这对燃料的燃烧和脱硫过程都会产生一定的干扰,对整个锅炉的使用也会产生影响。
采用物料平衡理论可以对固体燃料在燃烧系统内的分布规律进行合理的分析,在循环流化床的锅炉的设计中起到很好的效果。
物料平衡理论主要是指燃料、焦炭等在回料装置等可以保持平衡,物料平衡建立的效果直接会影响到循环流化床锅炉的运行效果。
(1)循环量的确定在循环流化床设计环节中,要确保一台锅炉可以正常的运行,在设计中应该确保热量分配的平衡。
循环流化床中物料的浓度与受热面传导系数具有直接的关系,所以,要确保锅炉内具有充足的物料循环。
在循环流化床物料循环中,结合不同燃料的特性,确定循环量。
在具体的设计环节中,如果循环量低于设计的循环量,就会导致锅炉内的燃料过分燃烧,热量被受热面过度吸收。
如果燃料的浓度过低,就会导致锅炉出力不足。
(2)分离器效率的要求循环流化床锅炉在运行环节中,要确保充足的循环量,所以要合理的设计分离器。
在分离器设计中,要提升分离效率。
一定速度下,在确定的粒度分布中,应该确保某个粒径的分离效率非常高,粒径的范围是循环灰中的主体,其在锅炉的物料中成分非常多。
如果分离器的分离效率对任意粒径的颗粒都不能达到100%,那么在循环流化床锅炉使用的环节中,分离器就不能实现物料的循环,锅炉的运行效果就不能得到保障。
(3)床压降的要求
床压降对锅炉内物料量是整体反映,在一定的物料下,物料的力度也与循环量的大小具有密切的关系。
循环流化床锅炉的正常运行离不开床压降,如果床压降过低,说明循环量需要提升。
循环量的过低直接会导致吸热量过小,不能保障锅炉的正常运转。
如果床压降过大,就会导致机械的能耗过大,降低了锅炉运行的经济性。
过大的循环量会产生锅炉磨损,降低锅炉的使用年限。
所以,合理的选择床压降非常重要,床压降一般控制在8000-1000Pa。
2.3优化配煤
一般来说,灰分越大的煤种,其燃烧产物中灰分含量也越大,易使炉内床压持续升高,更快地达到排渣所需要的参数;而增大排渣频次,容易将大颗粒度的床料排走,同样达到改善炉内颗粒度的效果,有利于降低床压。
为此,云浮C厂根据煤种的不同,通过将灰分较大的烟煤(20%以上)与灰分较小的印尼煤(5%左右)以1:1、1:2等比例进行动态配比,使混合后配煤灰分保持在10%左右,使其燃烧产物颗粒度保持在合理的范围内。
结束语
循环流化床锅炉由于燃烧效率和环保性能都较强,所以在我国电站生产广泛应用。
在以往的设计运行过程中,由于种种原因而导致磨损、结焦、分离效率下降以及回料故障等问题,但是随着设计水平的提升,这些问题都得到了有效的改善。
随着科学技术的发展,在循环硫化床锅炉设计运行中,应该善于使用新工艺、新技术和新材料,不断提升循环流化床锅炉的运行效率,为促进电站生产的可持续发展奠定坚实的基础。
参考文献
[1]程乐鸣,许霖杰,夏云飞,王勤辉,骆仲泱.600MW超临界循环流化床锅炉关键问题研究[J].中国电机工程学报,2015-11-05.
[2]姬鹏,任与非,黄振祥,刘建国.燃用煤泥的20t/h循环流化床锅炉系统设计与运行[J].热能动力工程,2018-01-20.
[3]蔡润夏,吕俊复,凌文,杨海瑞,张缦.超(超)临界循环流化床锅炉技术的发展[J].中国电力,2016-11-09.。