质量管理的三不原则
质量管理三不原则

质量管理三不原则▌三不原则的基本做法一、不接受不合格品不接受不合格品就是指员工在生产加工之前,先对前传递的产品按规定检查其就是否合格,一旦发现问题则有权拒绝接受,并及时反馈到前工序。
前道工序人员需要马上停止加工,追查原因,采取措施,使品质问题得以及时发现纠正,并避免不合格品继续加工造成的浪费。
二、不制造不合格品不制造不合格品就是指接受前道的合格品后,在本岗位加工时严格执行作业规范,确保产品的加工质量。
对作业前的检查、确认等准备工作做得充分到位;对作业中的过程状况随野鸟留意,避免或及早发现异常的发生,减少产生不合格品的概率。
准备充分并在过程中得到确认就是不制造不合格的关键。
只有不产生不良品,才能使得不流出与不接受不良品变为可能。
三、不流出不合格品不流出不合格品就是指员工完成本工序加工,需检查确认产品质量,一旦发现不良品,必须及时停机,将不良品在本工序截下,并且在本工序内完成不良品处置并采取防止措施。
本道工序应保证传递的就是合格产品,会被下道工序或“客户”拒收。
▌三不原则的实施要点一、谁制造谁负责一旦产品设计开发结束,工艺参数流程明确,则产品的质量波动就就是制造过程的问题。
每个人的质量责任从接受上道工序合格产品开始,规范作业确保本道工序的产品质量符合要求就是员工最大的任务。
一旦在本道工序发现不良或接到后道工序反馈的不良信息后,员工必须立即停止生产,调查原因,采取对策对产品的质量负责到底。
二、谁制造谁检查产品的生产者,同时出就是产品的检查者,产品的检查只就是生产过程的一个环节。
通过检查,确认生产合格,才能确保合格产品流入下道工序。
通过自身检查,作业者对本工序加工产品的状态可以了解得更清楚,从而有利于员工不断提升加工水平,提高产品质量。
三、作业标准化产品从设计开发、设定工艺参数开始,就要对所有的作业流程中作业步骤,作业细节进行规范化、标准化,并使其不断完善。
每一个员工也必须严格执行标准化作业。
标准化就是该工序最佳的作业方法,就是保证产品质量一致性的唯一途径,否则制造一大堆不良品却找不到不良的根本原因,这个时候“三不原则”只能制造混乱,而不就是品质。
质量管理三不原则

所有产品,所有工序无论采取什么形式都必须由操作者实施全数检查。
五、工序内检查
质量是作业者制造出来的,如果安排另外的检查人员在工序外对产品进行检查或修理,即会造成浪费,也不能提高作业者的责任感,还会姑息作业者对其产品质量的漠视。
六、不良停产
在工序内一旦发现不良产品,操作者有权利也有责任停止生产,并及时采取调查对策活动。
二、谁制造谁检查
产品的生产者,同时出是产品的检查者,产品的检查只是生产过程的一个环节。通过检查,确认生产合格,才能确保合格产品流入下道工序。通过自身检查,作业者对本工序加工产品的状态可以了解得更清楚,从而有利于员工不断提升加工水平,提高产品质量。
三、作业标准化
产品从设计开发、设定工艺参数开始,就要对所有的作业流程中作业步骤,作业细节进行规范化、标准化,并使其不断完善。每一个员工也必须严格执行标准化作业。标准化是该工序最佳的作业方法,是保证产品质量一致性的唯一途径,否则制造一大堆不良品却找不到不良的根本原因,这个时候“三不原则”只能制造混乱,而不是品质。
七、现时处理
在生产过程中,产生不合格品时,作业者必须从生产状态转变到调查处理状态,马上停止作业并针对产生不良品的人、机、料、法、环等现场要素及时确认,调查造成不良的“真正元凶”并及时处理。
八、不良曝光
在生产过程中出现的任何不良,必定有其内在的原因,只有真正解决了发生不良的每个原因,才能控制制造不合格品,实现零缺点,才能让客户真正满意。因此对于发生不良,不仅作业者要知道,还必须让管理层知道,质量保证的人员知道,让设计开发的人员知道,大家一起认真分析对策,并改善作业标准,而不是简单地由作业对不合格品自行返工或报废;否则,下一次还会发生同样的问题。
二、不制造不合格品
质量管理的三检和三不原则
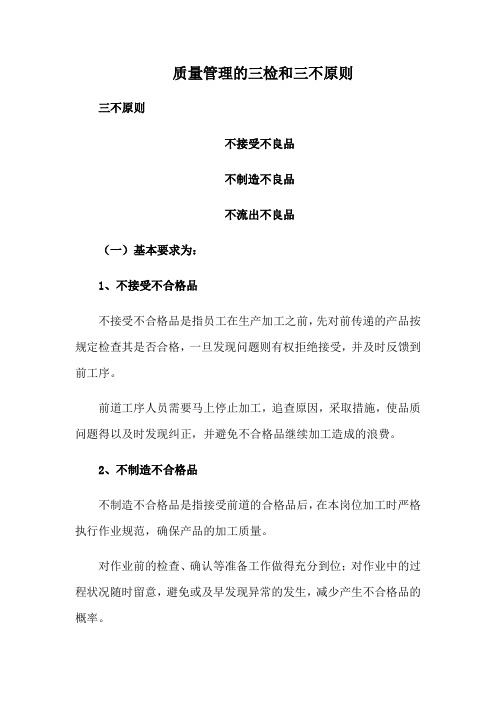
质量管理的三检和三不原则三不原则不接受不良品不制造不良品不流出不良品(一)基本要求为:1、不接受不合格品不接受不合格品是指员工在生产加工之前,先对前传递的产品按规定检查其是否合格,一旦发现问题则有权拒绝接受,并及时反馈到前工序。
前道工序人员需要马上停止加工,追查原因,采取措施,使品质问题得以及时发现纠正,并避免不合格品继续加工造成的浪费。
2、不制造不合格品不制造不合格品是指接受前道的合格品后,在本岗位加工时严格执行作业规范,确保产品的加工质量。
对作业前的检查、确认等准备工作做得充分到位;对作业中的过程状况随时留意,避免或及早发现异常的发生,减少产生不合格品的概率。
准备充分并在过程中得到确认是不制造不合格的关键。
只有不产生不良品,才能使得不流出和不接受不良品变为可能。
3、不流出不合格品不流出不合格品是指员工完成本工序加工,需检查确认产品质量,一旦发现不良品,必须及时停机,将不良品在本工序截下,并且在本工序内完成不良品处置并采取防止措施。
本道工序应保证传递的是合格产品,不会被下道工序或“客户”拒收。
(二)三不原则的实施要点1、谁制造谁负责一旦产品设计开发结束,工艺参数流程明确,则产品的质量波动就是制造过程的问题。
每个人的质量责任从接受上道工序合格产品开始,规范作业确保本道工序的产品质量符合要求是员工最大的任务。
一旦在本道工序发现不良或接到后道工序反馈的不良信息后,员工必须立即停止生产,调查原因,采取对策对产品的质量负责到底。
2、谁制造谁检查产品的生产者,同时是产品的检查者,产品的检查只是生产过程的一个环节。
通过检查,确认生产合格,才能确保合格产品流入下道工序。
通过自身检查,作业者对本工序加工产品的状态可以了解得更清楚,从而有利于员工不断提升加工水平,提高产品质量。
3、作业标准化产品从设计开发、设定工艺参数开始,就要对所有的作业流程中作业步骤,作业细节进行规范化、标准化,并使其不断完善。
每一个员工也必须严格执行标准化作业。
质量管理三不原则

质量管理三不原则▌三不原则的基本做法一、不接受不合格品不接受不合格品是指员工在生产加工之前,先对前传递的产品按规定检查其是否合格,一旦发现问题则有权拒绝接受,并及时反馈到前工序。
前道工序人员需要马上停止加工,追查原因,采取措施,使品质问题得以及时发现纠正,并避免不合格品继续加工造成的浪费。
二、不制造不合格品不制造不合格品是指接受前道的合格品后,在本岗位加工时严格执行作业规范,确保产品的加工质量。
对作业前的检查、确认等准备工作做得充分到位;对作业中的过程状况随野鸟留意,避免或及早发现异常的发生,减少产生不合格品的概率。
准备充分并在过程中得到确认是不制造不合格的关键。
只有不产生不良品,才能使得不流出和不接受不良品变为可能。
三、不流出不合格品不流出不合格品是指员工完成本工序加工,需检查确认产品质量,一旦发现不良品,必须及时停机,将不良品在本工序截下,并且在本工序内完成不良品处置并采取防止措施。
本道工序应保证传递的是合格产品,会被下道工序或“客户”拒收。
▌三不原则的实施要点一、谁制造谁负责一旦产品设计开发结束,工艺参数流程明确,则产品的质量波动就是制造过程的问题。
每个人的质量责任从接受上道工序合格产品开始,规范作业确保本道工序的产品质量符合要求是员工最大的任务。
一旦在本道工序发现不良或接到后道工序反馈的不良信息后,员工必须立即停止生产,调查原因,采取对策对产品的质量负责到底。
二、谁制造谁检查产品的生产者,同时出是产品的检查者,产品的检查只是生产过程的一个环节。
通过检查,确认生产合格,才能确保合格产品流入下道工序。
通过自身检查,作业者对本工序加工产品的状态可以了解得更清楚,从而有利于员工不断提升加工水平,提高产品质量。
三、作业标准化产品从设计开发、设定工艺参数开始,就要对所有的作业流程中作业步骤,作业细节进行规范化、标准化,并使其不断完善。
每一个员工也必须严格执行标准化作业。
标准化是该工序最佳的作业方法,是保证产品质量一致性的唯一途径,否则制造一大堆不良品却找不到不良的根本原因,这个时候“三不原则”只能制造混乱,而不是品质。
质量管理三不原则

质量管理三不原则▌三不原则的基本做法一、不接受不合格品不接受不合格品是指员工在生产加工之前,先对前传递的产品按规定检查其是否合格,一旦发现问题则有权拒绝接受,并及时反馈到前工序。
前道工序人员需要马上停止加工,追查原因,采取措施,使品质问题得以及时发现纠正,并避免不合格品继续加工造成的浪费。
二、不制造不合格品不制造不合格品是指接受前道的合格品后,在本岗位加工时严格执行作业规范,确保产品的加工质量。
对作业前的检查、确认等准备工作做得充分到位;对作业中的过程状况随野鸟留意,避免或及早发现异常的发生,减少产生不合格品的概率。
准备充分并在过程中得到确认是不制造不合格的关键。
只有不产生不良品,才能使得不流出和不接受不良品变为可能。
三、不流出不合格品不流出不合格品是指员工完成本工序加工,需检查确认产品质量,一旦发现不良品,必须及时停机,将不良品在本工序截下,并且在本工序内完成不良品处置并采取防止措施。
本道工序应保证传递的是合格产品,会被下道工序或“客户”拒收。
▌三不原则的实施要点一、谁制造谁负责一旦产品设计开发结束,工艺参数流程明确,则产品的质量波动就是制造过程的问题。
每个人的质量责任从接受上道工序合格产品开始,规范作业确保本道工序的产品质量符合要求是员工最大的任务。
一旦在本道工序发现不良或接到后道工序反馈的不良信息后,员工必须立即停止生产,调查原因,采取对策对产品的质量负责到底。
二、谁制造谁检查产品的生产者,同时出是产品的检查者,产品的检查只是生产过程的一个环节。
通过检查,确认生产合格,才能确保合格产品流入下道工序。
通过自身检查,作业者对本工序加工产品的状态可以了解得更清楚,从而有利于员工不断提升加工水平,提高产品质量。
三、作业标准化产品从设计开发、设定工艺参数开始,就要对所有的作业流程中作业步骤,作业细节进行规范化、标准化,并使其不断完善。
每一个员工也必须严格执行标准化作业。
标准化是该工序最佳的作业方法,是保证产品质量一致性的唯一途径,否则制造一大堆不良品却找不到不良的根本原因,这个时候“三不原则”只能制造混乱,而不是品质。
质量管理三不原则及实施要点

质量办理三不原则及实施要点之五兆芳芳创作▌什么是三不原则?1. 不接受不及格品不接受不及格品是指员工在生产加工之前,先对前传递的产品按规则查抄其是否及格,一旦发明问题则有权拒绝接受,并实时反应到前工序.前道工序人员需要马上停止加工,追查原因,采纳措施,使品质问题得以实时发明纠正,并避免不及格品持续加工造成的浪费.2. 不制造不及格品不制造不及格品是指接受前道的及格品后,在本岗亭加工时严格执行作业标准,确保产品的加工质量.对作业前的查抄、确认等准备任务做得充分到位;对作业中的进程状况随野鸟留意,避免或尽早发明异常的产生,削减产生不及格品的几率.准备充分并在进程中得到确认是不制造不及格的关头.只有不产生不良品,才干使得不流出和不接受不良品变成可能.3. 不流出不及格品不流出不及格品是指员工完成本工序加工,需查抄确认产品质量,一旦发明不良品,必须实时停机,将不良品在本工序截下,并且在本工序内完成不良品处置并采纳避免措施.本道工序应包管传递的是及格产品,会被下道工序或“客户”拒收.▌三不原则的实施要点1. 谁制造谁担任一旦产品设计开发结束,工艺参数流程明确,则产品的质量动摇就是制造进程的问题.每团体的质量责任从接受上道工序及格产品开始,标准作业确保本道工序的产品质量合适要求是员工最大的任务.一旦在本道工序发明不良或接到后道工序反应的不良信息后,员工必须立即停止生产,调查原因,采纳对策对产品的质量担任到底.2. 谁制造谁查抄产品的生产者,同时出是产品的查抄者,产品的查抄只是生产进程的一个环节.通过查抄,确认生产及格,才干确保及格产品流入下道工序.通过自身查抄,作业者对本工序加工产品的状态可以了解得更清楚,从而有利于员工不竭提升加工水平,提高产品质量.3. 作业尺度化产品从设计开发、设定工艺参数开始,就要对所有的作业流程中作业步调,作业细节进行标准化、尺度化,并使其不竭完善.每一个员工也必须严格执行尺度化作业.尺度化是该工序最佳的作业办法,是包管产品质量一致性的唯一途径,不然制造一大堆不良品却找不到不良的根来源根底因,这个时候“三不原则”只能制造凌乱,而不是品质. 4. 全数查抄所有产品,所有工序无论采纳什么形式都必须由操纵者实施全数查抄.5. 工序内查抄质量是作业者制造出来的,如果安插另外的查抄人员在工序外对产品进行查抄或修理,即会造成浪费,也不克不及提高着业者的责任感,还会迁就作业者对其产品质量的漠视.6. 不良停产在工序内一旦发明不良产品,操纵者有权利也有责任停止生产,并实时采纳调查对策勾当.7. 现时处理在生产进程中,产生不及格品时,作业者必须从生产状态转变到调查处理状态,马上停止作业并针对产生不良品的人、机、料、法环等现场要素实时确认,调查造成不良的“真正元凶”并实时处理.8. 不良曝光在生产进程中出现的任何不良,肯定有其内在的原因,只有真正解决了产生不良的每个原因,才干控制制造不及格品,实现零缺点,才干让客户真正满意.因此对于产生不良,不但作业者要知道,还必须让办理层知道,质量包管的人员知道,让设计开发的人员知道,大家一起认真阐发对策,并改良作业尺度,而不是复杂地由作业对不及格品自行返工或报废;不然,下一次还会产生同样的问题.9. 防错产品的品质不克不及够完全依赖操纵业者者的责任心来包管,任何人都会有情绪,会有惰性,会有侥幸心理,会受一些意外因素搅扰,从而使产品质量出现动摇.因此,必须尽可能科学公道地设计使用防错装置来避免疏忽.同时在现场办理中,认真进行细节办理,尽量把任务做在前面,周全的筹划,充分的准备,事先的预防,削减各类差别变动,把品质控制在要求的规模内.10. 办理支持作业者承坦产品的品质责任,但产品出现不良,办理层应该承坦更多的责任,因为现场办理者的职责就是帮忙员工解决问题.当员工发明问题并陈述时,作为现场办理者应第一时间出现在现场,一起调查并处理问题.对于不良品若只是轻率地推卸责任给作业者,不但不克不及完全解决不及格品的产生,并且易造成办理层与员工之间的对立.所以,若要对员工进行指导,事先预防问题的产生,和员工配合阐发问题、调查解决问题,就必须配备员工所需的资源设施,必须帮忙员工解除生活、任务上的后顾之忧.总之,办理者只有成为员工的刚强后台,“三不原则”才干真正在生产中落实.。
质量“三不”原则

质量管理质量管理(quality management)是指确定质量方针、目标和职责,并通过质量体系中的质量策划、质量控制、质量保证和质量改进来使其实现的所有管理职能的全部活动。
三不原则不接受不合格品是指员工在生产加工之前,先对前传递的产品按规定检查其是否合格,一旦发现问题则有权拒绝接受,并及时反馈到前工序。
前道工序人员需要马上停止加工,追查原因,采取措施,使品质问题得以及时发现纠正,并避免不合格品继续加工造成的浪费。
一不接受不合格品不制造不合格品是指接受前道的合格品后,在本岗位加工时严格执行作业规范,确保产品的加工质量。
对作业前的检查、确认等准备工作做得充分到位;对作业中的过程状况随野鸟留意,避免或及早发现异常的发生,减少产生不合格品的概率。
准备充分并在过程中得到确认是不制造不合格的关键。
只有不产生不良品,才能使得不流出和不接受不良品变为可能。
二不制造不合格品不流出不合格品是指员工完成本工序加工,需检查确认产品质量,一旦发现不良品,必须及时停机,将不良品在本工序截下,并且在本工序内完成不良品处置并采取防止措施。
本道工序应保证传递的是合格产品,会被下道工序或“客户”拒收。
三不传递不合格品三不原则实施要点一旦产品设计开发结束,工艺参数流程明确,则产品的质量波动就是制造过程的问题。
每个人的质量责任从接受上道工序合格产品开始,规范作业确保本道工序的产品质量符合要求是员工最大的任务。
一旦在本道工序发现不良或接到后道工序反馈的不良信息后,员工必须立即停止生产,调查原因,采取对策对产品的质量负责到底。
一谁制造谁负责产品的生产者,同时出是产品的检查者,产品的检查只是生产过程的一个环节。
通过检查,确认生产合格,才能确保合格产品流入下道工序。
通过自身检查,作业者对本工序加工产品的状态可以了解得更清楚,从而有利于员工不断提升加工水平,提高产品质量。
二谁制造谁检查产品从设计开发、设定工艺参数开始,就要对所有的作业流程中作业步骤,作业细节进行规范化、标准化,并使其不断完善。
质量管理的“三不原则”

质量管理的“三不原则”前言“不接受不合格品、不制造不合格品、不流出不合格品”的“三不原则”的实施,导入了“供应商一客户”的市场关系,每个人既是供应商,又是客户,既是产品的使用者,也是制造者、供应者。
现场管理的6个观念就是:以现场为中心,全员参与管理4M1E和QCDMSS,以下道工序为客户,待续改善达到零缺点。
从现场质量管理的角度,“三不原则”(不接受、不制造、不流出)其实就是对这些观念的阐释和实施。
质量是从组织内的每一个人,承诺绝不将不合格品或不完整的信息,送至下一流程开始。
因为下一流程就是客户,绝不应把不合格品送至下一流程的客户,以免造成他们的不便。
当每一个人都能认同、实现这个理念时,一个良好质量保证体系就能存在了。
“不接受不合格品、不制造不合格品、不流出不合格品”的“三不原则”是许多公司的质量方针、质量目标、或者宣传口号,常在公司的墙壁或柱子上高高悬挂。
随着社会大生产的分工合作,任何产品都不太可能由一个人独立全部完成,产品总是分工序、分流程,包括职能部门间的工作协助,这些过程都是环环相扣,紧密相连。
只要其中的某一环节出问题都将影响整个产品质量或工作质量。
“三不原则”就是每个环节的质量保证原则。
“三不原则”的实施,意味着人人都要参与,人人都是主角,是全面质量管理(TQM)认真贯彻的要求和结果。
“三不原则”的实施,导入了“供应商一客户”的市场关系,每个人既是供应商,又是客户,既是产品的使用者,也是制造者、供应者,因此每个人都要牢固树立“下道工序是客户”的观念。
要实现“三不原则”,要做到“不制造不合格品”,这就要求我们第一次就把事情做对,要求我们以“零缺点”的观念和方式工作。
因此,要实施“三不原则”,使“三不原则”不仅仅是顺溜的口号,现场管理还有很多工作要去做。
一、三不原则的基本做法1、不接受不合格品不接受不合格品是指员工在生产加工之前,先对前传递的产品按规定检查其是否合格,一旦发现问题则有权拒绝接受,并及时反馈到前工序。
- 1、下载文档前请自行甄别文档内容的完整性,平台不提供额外的编辑、内容补充、找答案等附加服务。
- 2、"仅部分预览"的文档,不可在线预览部分如存在完整性等问题,可反馈申请退款(可完整预览的文档不适用该条件!)。
- 3、如文档侵犯您的权益,请联系客服反馈,我们会尽快为您处理(人工客服工作时间:9:00-18:30)。
质量管理的三不原则
▌三不原则的基本做法
一、不接受不合格品
不接受不合格品是指员工在生产加工之前,先对前传递的产品按规定检查其是否合格,一旦发现问题则有权拒绝接受,并及时反馈到前工序。
前道工序人员需要马上停止加工,追查原因,采取措施,使品质
问题得以及时发现纠正,并避免不合格品继续加工造成的浪费。
二、不制造不合格品
不制造不合格品是指接受前道的合格品后,在本岗位加工时严格执行作业规范,确保产品的加工质量。
对作业前的检查、确认等准备工作做得充分到位;对作业中的过程状况随野鸟留意,避免或及早发现异常的发生,减少产生不合格品的概率。
准备充分并在过程中得到确认是不制造不合格的关键。
只有不产
生不良品,才能使得不流出和不接受不良品变为可能。
三、不流出不合格品
不流出不合格品是指员工完成本工序加工,需检查确认产品质量,一旦发现不良品,必须及时停机,将不良品在本工序截下,并且在本工序内完成不良品处置并采取防止措施。
本道工序应保证传递的是合格产品,会被下道工序或“客户”拒收。
▌三不原则的实施要点
一、谁制造谁负责
一旦产品设计开发结束,工艺参数流程明确,则产品的质量波动就是制造过程的问题。
每个人的质量责任从接受上道工序合格产品开始,规范作业确保本道工序的产品质量符合要求是员工最大的任务。
一旦在本道工序发现不良或接到后道工序反馈的不良信息后,员工必须立即停止生产,调查原因,采取对策
对产品的质量负责到底。
二、谁制造谁检查
产品的生产者,同时出是产品的检查者,产品的检查只是生产过程的一个环节。
通过检查,确认生产合格,才能确保合格产品流入下道工序。
通过自身检查,作业者对本工序加工产品的状态可以了解得更清
楚,从而有利于员工不断提升加工水平,提高产品质量。
三、作业标准化
产品从设计开发、设定工艺参数开始,就要对所有的作业流程中作业步骤,作业细节进行规范化、标准化,并使其不断完善。
每一个员工也必须严格执行标准化作业。
标准化是该工序最佳的作业方法,是保证产品质量一致性的唯一途径,否则制造一大堆不良品却找不到不良的根本原因,这个时候“三不原则”
只能制造混乱,而不是品质。
四、全数检查
所有产品,所有工序无论采取什么形式都必须由操作者实施全数检查。
五、工序内检查
质量是作业者制造出来的,如果安排另外的检查人员在工序外对产品进行检查或修理,即会造成浪费,也不能提高作业者的责任感,还会姑息作业者对其产品质量的漠视。
六、不良停产
在工序内一旦发现不良产品,操作者有权利也有责任停止生产,并及时采取调查对策活动。
七、现时处理
在生产过程中,产生不合格品时,作业者必须从生产状态转变到调查处理状态,马上停止作业并针对产生不良品的人、机、料、法环等现场要素及时确认,调查造成不良的“真正元凶”并及时处理。
八、不良曝光
在生产过程中出现的任何不良,必定有其内在的原因,只有真正解决了发生不良的每个原因,才能控制制造不合格品,实现零缺点,才能让客户真正满意。
因此对于发生不良,不仅作业者要知道,还必须让管理层知道,质量保证的人员知道,让设计开发的人员知道,大家一起认真分析对策,并改善作业标准,
而不是简单地由作业对不合格品自行返工或报废;否则,下一次还会发生同样的问题。
九、防呆防错
产品的品质不能够完全依赖操作业者者的责任心来保证,任何人都会有情绪,会有惰性,会有侥幸心理,会受一些意外因素干扰,从而使产品质量出现波动。
因此,必须尽可能科学合理地设计使用防呆防错装置来防止疏忽。
同时在现场管理中,认真进行细节管理,尽量把工作做在前面,周全的计划,充分的准
备,事先的预防,减少各种差异变动,把品质控制在要求的范围内。
十、管理支持
作业者承坦产品的品质责任,但产品出现不良,管理层应该承坦更多的责任,因为现场管理者的职责就是帮助员工解决问题。
当员工发现问题并报告时,作为现场管理者应第一时间出现在现场,一起调查并处理问题。
对于不良品若只是轻率地推卸责任给作业者,不仅不能彻底解决不合格品的产生,而且易造成管理层与员工之间的对立。
所以,若要对员工进行指导,事先预防问题的产生,和员工共同分析问题、调查解决问题,就必须配备员工所需的资源设施,必须帮助员工解除生活、工作上的后顾之忧。
总之,管理者只有成为员工的坚强后盾,“三不原则”才能真正在生产中落实。