炼钢工艺设计2017
新西兰钒钛海砂磁铁矿冶炼工艺分析

第45卷第4期2017年8月现代冶金Modern M etallurgyV ol. 45 No. 4A u g. 2017新西兰钒钛海砂磁铁矿冶炼工艺分析李志强,张洋(南京钢铁股份有限公司,江苏南京210035)摘要:介绍了新西兰机钬海砂磁铁矿冶炼工艺,并与传统高炉炼铁工艺进行了比较与分析;此工艺成熟稳定、工序 少、环境友好、资源丰富、成本低,是值得推广发展的一项革命性技术。
关键词!机钬;海砂矿;煤基直接还原;回转窑;多层炉中图分类号:T F521; T F533. 2引言钢铁厂铁水的生产工艺基本可分成以下三大 类:A:气-固热交换熔化还原,如高炉、CO REX;B:预还原-电弧炉熔分,如煤基回转窑B电弧 炉、气基竖炉B电弧炉;C气-液热交换熔融还原,如H ISM ELT、AUS-IRON。
高炉流程经过上千年的发展,目前已确立霸主地 位:规模大、单座装置年产能可达300万吨以上,工艺 操作极为成熟,焦比已接近理论计算值,设备制造已 系列化,资源供应有保障;气基竖炉受天然气价格影 响竞争力下降;煤基回转窑在印度等缺少焦煤的地区仍在运行;熔融还原工艺目前尚无商业化运作。
对新西兰钢厂的海砂矿采选、冶炼生产线进行 考察,同时对海砂矿资源进行了初步调查,与高炉炼 铁工艺进行了比较与分析,新西兰钒钛海砂磁铁矿 冶炼工艺颇具特色。
1新西兰钒钛海砂磁铁矿直接还原工艺11工艺流程新西兰钢厂炼铁工艺以钒钛海砂磁铁矿和褐煤 为原燃料(指标如表1、表2所示),经多层炉干燥和 预热,回转窑预还原,矿热炉终还原、渣铁分离这三 道生产工序(如图1所示),生成铁水和炉渣,铁水送 至转炉炼钢工序进行提钒和炼钢。
表1海砂矿精矿参照指标/ "!(T Fe)!(CaO)!(SiO2)!(TiO2)!(A l2O3)!(MgO)!(P)!(V2O5)!(MnO)!(S)57 1.5 3.9 7.7 3.7 3.4 0.035 0.45 0.66 0.004多层炉回转窑储藏和混合图1工艺流程图收稿日期=2017-04-25作者简介:李志强(960—),男,高级工程师。
炼钢厂房屋面管道支架设计
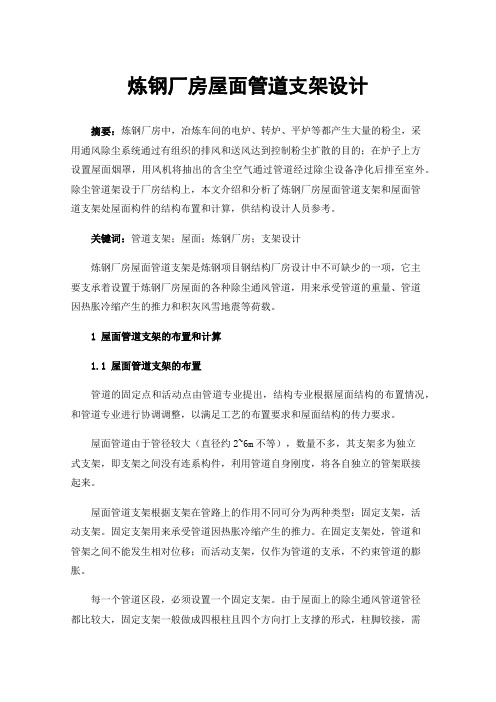
炼钢厂房屋面管道支架设计摘要:炼钢厂房中,冶炼车间的电炉、转炉、平炉等都产生大量的粉尘,采用通风除尘系统通过有组织的排风和送风达到控制粉尘扩散的目的;在炉子上方设置屋面烟罩,用风机将抽出的含尘空气通过管道经过除尘设备净化后排至室外。
除尘管道架设于厂房结构上,本文介绍和分析了炼钢厂房屋面管道支架和屋面管道支架处屋面构件的结构布置和计算,供结构设计人员参考。
关键词:管道支架;屋面;炼钢厂房;支架设计炼钢厂房屋面管道支架是炼钢项目钢结构厂房设计中不可缺少的一项,它主要支承着设置于炼钢厂房屋面的各种除尘通风管道,用来承受管道的重量、管道因热胀冷缩产生的推力和积灰风雪地震等荷载。
1 屋面管道支架的布置和计算1.1 屋面管道支架的布置管道的固定点和活动点由管道专业提出,结构专业根据屋面结构的布置情况,和管道专业进行协调调整,以满足工艺的布置要求和屋面结构的传力要求。
屋面管道由于管径较大(直径约2~6m不等),数量不多,其支架多为独立式支架,即支架之间没有连系构件,利用管道自身刚度,将各自独立的管架联接起来。
屋面管道支架根据支架在管路上的作用不同可分为两种类型:固定支架,活动支架。
固定支架用来承受管道因热胀冷缩产生的推力。
在固定支架处,管道和管架之间不能发生相对位移;而活动支架,仅作为管道的支承,不约束管道的膨胀。
每一个管道区段,必须设置一个固定支架。
由于屋面上的除尘通风管道管径都比较大,固定支架一般做成四根柱且四个方向打上支撑的形式,柱脚铰接,需承受管道的水平推力、风荷载、竖向恒活荷载和地震力;屋面上的活动支架一般可分为刚性活动支架和半铰接活动支架两种形式。
刚性活动支架一般也做成四根柱且四个方向打个支撑的形式,柱脚铰接,需承受管道移动时的摩擦力、风荷载、恒活荷载和地震力;半铰接活动支架一般做成两根柱且打上支撑(沿管道径向)的形式,仅承受竖向恒活荷载和风荷载,需借助管道作为轴向支点。
典型的固定支架和活动支架示意图如图1所示。
9Cr5Mo轧辊钢Ф500mm连铸坯的生产实践

2 9Cr5Mo钢试 制生产
2.1 工艺控 制难点 1)化 学 成分 。用 户技 术协 议 中对 9Cr5Mo钢化
学 成 分 的要 求及 内控 要 求见 表 1,对 有 害元 素 含量 也 提 出了要求 。由于 9Cr5Mo钢 P、S含量 要求 较低 , 电炉 出钢 时要 将 钢水 中的 P脱 到很 低 的水 平 ,同时 还要 避免 钢水 的过 氧化 ,工 艺控制 难度较 大 。
3)铸 坯低 倍 质 量 控 制 。9Cr5Mo轧辊 要 求 探 伤 交 货 ,对 圆坯 内部 质 量提 出了更 高要 求 。圆坯 的低 倍 组 织 按 YB/T4149附 录 A评 级 图评 定 ,圆 坯 横截
收 稿 日期 :2016—05—30 作者 简介 :张庆 ,男 ,1982年生 ,2004年毕业于江西 理工大学冶金工 程专 业 ;2012年毕业 于北京科技大学 冶金工程专业 ,工 学硕士 。现 为 山钢股份莱芜 分公 司特钢 事业部技术科 副科 长 ,工程 师 ,从事炼 钢 与连铸 工艺技术工作 。
常 用 的轧辊 材 料有 合金 锻 钢 、合金 铸钢 和铸 铁 等 。近 年来 ,随 着 轧 机 向高 速 化 、自动 化 方 向 的发 展 以及 轧 制工 况条 件 的苛 刻等 特 点 ,对 轧辊 的性 能
EN 10028-2 2016 承压用钢板材 高温性能的非合金钢和合金钢(中文版)

EN10025-7:2017承压用钢板第7部分:高温性能的非合金钢和合金钢(非合金和低合金热强钢)狮子十之八九译目录欧洲标准前言(略)1 范围2 引用标准(略)3 术语和定义4 尺寸公差5 质量计算6 分类和名称6.1 分类6.2 名称7 订货信息7.1 强制性信息7.2 非强制性信息7.3 订货信息示例8 要求8.1 炼钢工艺8.2 供货条件8.3 化学成分和耐化学腐蚀性8.4 力学性能8.5 表面条件8.6 内部质量8.7 抗氢致裂纹8.8 CrMo钢的脆化9 检验9.1 检验类型和检验文件9.2 试验9.3 复验、分类和再处理10 取样11 试验方法12 标记附录A (信息)热处理指南附录B(信息)临界时间温度参数Pcrit.和消应力温度以及保温时间附录C(信息)1%(塑性变形)的蠕变极限和持久强度参考数据附录D(标准)抗氢致开裂性评估附录E(标准)步冷试验附录F(信息)与EN10028-2:2009版之间的变化附录ZA(信息)本欧洲标准与2014/68/EU指令基本要求的之间的关系参考文献(略)欧洲标准前言(略)1 范围本欧洲标准给出了表1中可焊接具有高温性能的非合金以及合金承压用钢板材的要求。
EN 10028-1中的要求同样适用。
注1:一旦本欧洲标准根据指令2014/68/EU在欧盟官方公报(OJEU)上发布,则符合指令2014/68/EU 基本安全要求(ESRs)的假设仅限于本欧洲标准(本系列第1部分和本系列第7部分)中材料的技术数据,且不假设材料对特定的设备的充分性。
因此,需要根据设备具体项目的设计要求,对本材料标准中规定的技术数据进行评估,以验证是否满足指令2014/68/EU的ESRs要求。
2 引用标准(略)3 术语和定义对于此欧洲标准的使用,EN 10028-1:2017中术语和定义适用。
4 尺寸公差应根据EN 10028-1:2017。
5 质量计算应根据EN 10028-1:2017。
一、 工艺布置 - 凤宝股份

炼钢厂60tLF精炼炉初步设计方案一、概述炼钢系统现有1座600t混铁炉,两座40吨转炉(平均出钢量40吨),3座LF精炼炉(其中两座LF炉功率8MV A,一座LF炉6MV A),年平均产能120万吨。
2017年年产钢量111.4万吨。
但随着品种钢增多,精炼问题凸显,精炼能力严重不足,导致经常出现精炼周期不够,连铸空包时有发生,质量得不到有效保证。
精炼能力不足,已成为制约凤宝特钢品种结构调整的瓶颈,严重威胁到凤宝特钢的生存和发展。
为更好地适应公司品种钢开发的需求,我厂拟建一座60tLF精炼炉。
现特邀贵设计院对新建60tLF精炼炉进行设计。
二、设计原则1、尽量采用已有的成熟技术,注重技术的适用性、可靠性、经济性和先进性;设备选型尽量考虑能与现有系统设备互换;2、方案设计中尽量做到总体布局、物流和运输尽可能合理,并有利于公司今后的发展;3、尽量利用现有设施,节省工程投资;同时在制定工艺方案和技术措施时要充分考虑减少改造工程对现有生产运行的影响,尽可能缩短现有生产设施的停产时间;4、本工程中的环境保护、安全、工业卫生、消防设施严格按照有关的国家标准、规范执行,与主体工程同时设计、同时施工、同时投产。
三、设计范围(一)、工艺布置⑴新建60tLF精炼炉工艺布置60tLF精炼炉暂时考虑布置在钢水浇铸跨18~21号柱间(原2期连铸位置),双钢包车平行于转炉主厂房横向(东西方向)布置,设置单加热位(双喂丝工位)及单加料系统。
LF炉用变压器室、液压室、操作室、合金加料系统均布置在过渡跨18~21号柱间。
(2)工艺流程LF钢包精炼炉工艺流程LF钢包精炼炉工艺流程见图:LF钢包精炼炉工艺流程图(二)、主要设备选型及技术参数要求1、LF钢包精炼炉(1)60tLF炉技术参数如下:LF精炼炉公称容量:60t;LF精炼炉座数:1座;平均钢水处理量:60t/炉(远期65t/炉);最大钢水处理量:65t/炉;现钢水处理量:45 t/炉;平均冶炼周期:38min/炉;年处理钢水量:~70万t/a;(2)变压器额定功率为:12MV A(设计院核定)。
82B高碳钢的生产工艺优化

202111 前 言 82B高碳钢目前被广泛用在高强度预应力钢丝、钢绞线、帘线钢等的生产原料上,因其对炼钢、轧钢生产工艺过程要求严苛,尤其对钢水脱氧造渣、成分温度控制、夹杂物去除以及轧线加热温度、吐丝温度控制稳定性控制要求较高。
为应对82B品种市场需求和工艺控制波动,酒钢炼轧厂于近年来开始优化82B钢生产工艺,以更好的适应市场需求,目前采用铁水脱硫-转炉冶炼-LF 精炼-方坯连铸工艺-高速轧线生产路线,通过相应的工艺优化和技术攻关,实现了生产工艺路线稳定,产品性能不断提升。
2 生产工艺 82B高碳钢工艺流程:铁水脱硫→转炉炼钢→LF炉精炼→铸机全保护浇注→高速轧线。
2.1 转炉工艺 结合酒钢高炉铁水条件和其他综合条件,采82B高碳钢的生产工艺优化李 洁,晁增武(酒钢集团宏兴股份公司炼轧厂,甘肃,嘉峪关, 735100) 摘 要:介绍酒钢82B高碳钢的生产工艺优化,结合生产过程存在的不稳定因素,通过优化转炉冶炼、脱氧工艺、精炼造渣、钢水钙处理等,有效控制钢水冶炼稳定性,降低钢水夹杂物,提高钢水洁净度,稳定82B轧制工艺,82B 产品质量得到了稳步提升。
关键词:夹杂物;钙处理;自开率Production Process Optimization of 82B High Carbon SteelLi Jie, Chao Zengwu(Steel-making and Rolling Plant of Hongxing Iron & Steel Co. Ltd., Jiuquan Iron andSteel (Group) Corporation, Jiayuguan, Gansu,735100) Abstract: The paper introduces the production process optimization of 82B high carbon steel in JISCO. Combined with the unstable factors in the production process, by optimizing the converter smelting, deoxidation process, refining slagging and calcium treatment of molten steel, the smelting stability of molten steel is effectively controlled, the inclusion of molten steel is reduced, the cleanliness of molten steel is improved, the 82B rolling process is stabilized and the temperature of 82B product is improved. Key words: inclusion; calcium treatment; free opening rate202112.2.2 钢水钙处理工艺优化 精炼钙处理是将高熔点的Al 2O 3夹杂变性为低熔点12CaO·7Al 2O 3,保证钢水可浇性,尽管钢水可浇性得到改善,但夹杂物变性后仍存在于钢水中,上浮去除效果差,且形成更为复杂的复合型夹杂物,尺寸进一步加大,钙处理对夹杂物控制、钢水纯净度存在不利影响[1]。
年产量100万吨棒材车间设计

(5)轧机结构形式先进合理,制造容易,操作简单,维修方便。
(6) 备品备件更换容易,并利于实现备品备件的标准化。
(7)有良好的综合技术经济指标。
而对于钢板轧机、钢管轧机、小型及线材轧机,除了要求一定的强度外,还要求有足够的刚度,以保证这些轧制产品的几何形状的正确和尺寸的精度,因此选择轧钢机时除遵循上述原则之外,要从工艺要求出发,根据不同产品的生产特点和具体要求来确定轧机的结构形式,主要的技术参数和它们的布置方式。
1.3.1
1#切头飞剪(一台)
位于粗轧与中轧之间
其主要参数有:
形式:开口曲柄式,带夹送辊装置;
剪切最大截面积:3500㎡;
剪切温度:900℃;
轧件抗拉强度:110MP~120MP;
轧件运行速度:0.5m/s~2.5m/s
剪切头尾公差:±20mm
碎断长度:600mm
夹送辊装置为焊接钢结构,并带有悬臂辊,辊子直径为330mm,宽度为100mm,由马达通过齿轮传动下辊,上辊为气动压下。
金属收得率可提高6-12%; 2、 每吨钢大约节约热能14万大卡;
1.1.2 炉型选择
炉型的选择取决于坯料的断面大小,钢材品种和加热质量等要求。线棒材轧机加热炉大都采用步进梁式加热炉。梁底组合式步进加热炉比推钢式加热炉有较多的优点,也优于步进底式加热炉,它能使钢坯的加热温度均匀,没有或很少有水管墨印,坯料不与滑轨摩擦,不会划伤坯料,加热质量好。
小结:
炉宽: B=10.6m
有效炉长:L=18m
有效炉底面积:S=190.8㎡
炉底过钢面积:S`=180㎡
四、其它参数
空气预热温度:450℃-550℃
转炉溅渣护炉技术
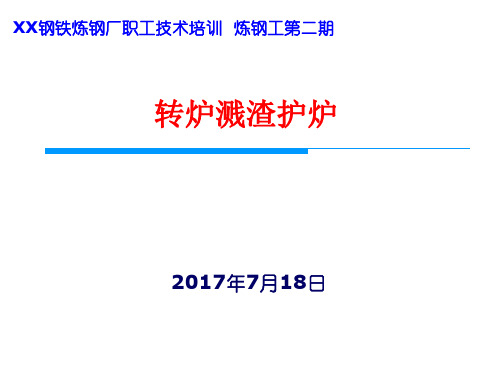
工艺措施
打击方式 抽真空 真空油浸 原料纯度 颗粒配比 树脂质量 抗氧化剂数量 模具质量
碳含量
如何延长转炉炉衬的使用寿命
4 转炉砌筑
减少衬砖损坏 背紧靠实,砖缝0.5mm-1mm 合缝位置在耳轴 避免倒插门 砌后细料扫填 开炉前减少摇炉
如何延长转炉炉衬的使用寿命
刚吹炼时,石灰难熔化,是因为石灰的熔化靠吹氧使铁水氧化形成的FeO 很少,这一段时间渣的碱度上不来,故炉衬的受浸蚀量大。上述两个原因导致吹炼 前期炉衬浸蚀是最严重的。
一、刚开吹时投入含FeO材料使炉渣中的氧化铁含量迅速增加,从而促 进石灰迅速熔化,提高炉渣碱度,降低渣中MgO的饱和熔解度。
二、刚开始吹炼时加入轻烧白云石或轻烧镁球,从渣中本身就会有 8%~9%的MgO,以减少炉渣为保持自己的饱和熔解度而对炉衬的浸蚀。
MgO含量在炉衬与炉渣中的平衡 氧化镁在炼钢渣中的饱和溶解度,渣中FeO含量越高,炉渣碱度
越小,炉渣的温度越高,MgO在渣在溶解度越大。
炉渣中的MgO在没有达到饱和时,就要从炉衬中浸取MgO,努力达到饱和 浓度,这也叫平衡,而MgO在炉渣中的含量和溶解度随炉渣的碱度R(CaO/SiO2) 的减小而迅速增大。当R=3.5时,其饱和熔解度为8%~9%,可是刚刚开吹时,石 灰没全熔化而铁水中Si氧化成二氧化硅(SiO2)量又很大,所以CaO/SiO2值很小 只有1%左右,这时MgO在渣中的熔解度远远大于8%~9%,有时达到30%,必然 要大量从炉衬中浸取熔解MgO使炉衬受到大量熔损。
9 转炉的维护 维护方式 1、喷补; 2、换出钢口管,及内出钢口修补; 3、垫补前大面。
转炉炉衬的垫补、喷补方式
1、湿法喷补 料与水先混合; 2、半干法喷补 料水在喷枪出口处混合; 3、火焰喷补 料经出口火熘部分熔化。
- 1、下载文档前请自行甄别文档内容的完整性,平台不提供额外的编辑、内容补充、找答案等附加服务。
- 2、"仅部分预览"的文档,不可在线预览部分如存在完整性等问题,可反馈申请退款(可完整预览的文档不适用该条件!)。
- 3、如文档侵犯您的权益,请联系客服反馈,我们会尽快为您处理(人工客服工作时间:9:00-18:30)。
炼钢工艺流程设计概述
氧气转炉炼钢在钢铁企业中处于整个钢铁生产流程的中间环节,起到 承上启下的作用,炼钢是决定钢材产量、质量、品种的关键所在。炼钢环 节的任何延误或产量、质量变化都会影响前后生产工序的协调运转。这都 与转炉炼钢的设备、工艺、组织管理等因素有关。所以在设计转炉炼钢车 间时,应当处理好各种设计问题,为正常生产,保持良好的生产秩序打下 基础。
炼钢厂设计的目的和基本内容
目的:是要建设新的生产厂,扩建或改建旧有企业使之更 适合国民经济发展的需要,提高产量和质量,改善生产环境。 任务:是要对建设单位作出技术与经济的详细规划,确定 企业的生产经济状况、技术经济指标,以及可能的工程建设进 度计划。设计中所拟定的劳动人员编制和建设投资估算与概算, 是企业招工定额、建立人员编制和申请拨付投资或贷款的依据。 基本内容: (1)车间工艺设计(与钢铁冶金专业直接相关); (2)车间机械设备设计; (3)供电设施设计,通讯系统设计,照明设计; (4)给水、排水(包括污水处理)设计; (5)厂房通风与局部的采暖、通风设计; 、 (6)厂房与设备基础及其他构筑物设计; (7)环境保护与安全卫生设计。
宝钢一炼钢于1985年 9月投产,设计年产量 648.5万t,目前产能可 以达到850万t。在后 来的生产过程中,根据 市场需要和产品开发 的需要,还逐步新增和 改造了一些工艺设备 装置,它是宝钢目前产 量最高、品种最多的 炼钢生产线。主要品 种有汽车板用钢、管 线钢、船板钢、塑模 钢、耐候钢、钢帘线 钢和高压锅炉管钢等。
炼钢车间工艺设计的任务
车间工艺设计的任务是以设计任务书为依据,对下列各项 内容完成较详细的设计与计算,编制设计说明书,绘制相应的 图纸。 (1)制订详细的产品方案(产品大纲); (2)根据不同钢种,制订生产工艺大纲; (3)主体设备的选型、设计,确定设备数量、型号等; (4)选择各种辅助设备,提出非标准设备的设计工艺要求; (5)设计并绘制车间的工艺布置平面图与剖面图; (6)提供水、电、热力、土建、通风、照明、设备制造及总 图运输等各专业设计所需要的资料; (7)计算各项原材料的消耗量,计算炼钢到浇注生产过程的 各项技术经济指标; (8)编制劳动定员计划; (9)钢坯生产成本计算或提出成本计算的技术资料,提出进 行技术经济分析所需要的资料。
设计前期工作
设计工作
项目实施
冶金工程项目基本建设工作流程图
政府部门
①项目 申报
设计部门
项目 申请 设计项目建议书 修改意见
用户
项目 批复 修改意见
施工方案施工图
建设部门
②项 目设 计
设计方案设计图
③项 目施 工
投产、生产、管 理
一个建设项目的设计,需要各种专业设计人员共同协作完成。 如在转炉炼钢车间的设计中,作为主体专业的钢铁冶金专业设计 人员所负责完成的任务是根据设计任务书,进行转炉炼钢厂的工 艺设计,它主要包括制定产品大纲;对生产的钢种,制定生产工 艺路线;炼钢主体设备的设计与选择;设计并绘制炼钢车间的工 艺布置平面图和剖面图;提出其他辅助专业设计所需要的设计工 艺要求和资料等。
出铁倒渣
铁水兑入 同一转炉
脱碳 吹炼 出钢不倒渣
脱碳炉渣热回收 转炉A 转炉B
装入铁 水废钢
脱磷 吹炼 出铁倒渣
铁水兑入 另一转炉
脱碳 吹炼 出钢倒渣
所以在进行转炉炼钢厂的设计中,应充分考虑转炉炼钢工 艺流程的上述的这些炼钢工艺流程的科技进步,使转炉炼钢车 间在设备、工艺方面处于先进的水平,以适应产品需求。目前, 随着环境保护意识的增强,考虑到钢铁企业的可持续发展,在 设计中,要注意转炉炼钢的烟气净化与回收,目前新设计的转 炉都采用干法技术。炉渣处理回收等技术的应用,减少排放物, 甚至实现零排放的目标。 转炉双联法脱磷是在转炉内对不脱硅的铁水进行同时脱硅 脱磷预处理,脱磷结束后,将脱磷渣与脱磷后的铁水分离,然 后在同一座转炉或另一座转炉进行脱碳。在转炉内进行脱磷预 处理的优点是转炉的容积大、可以采用比铁水包或鱼雷罐预处 理脱磷工艺大的供氧强度,反应速度快,脱磷效率高,可节省 造渣剂的用量,吹氧量较大时也不易发生严重的喷溅现象,有 利于生产超低磷钢。但这一工艺由于中途要进行脱磷渣和预处 理后的铁水分离,总的炼钢周期长,热损失大,终点钢水的残 锰量低,铁损高。
现代转炉炼钢工艺流程及车间构成
CAS RH
铁水预处理 复吹转炉炼钢 连铸 LF 炉外精炼
铁水预处 理间
加料跨
转炉跨
精炼跨(钢水接受跨)
浇铸跨
切割跨
AS
RH
预处理 脱硫 连铸 预处理脱磷 脱碳 炉外精炼 LF
装料
废钢
脱硅脱磷
熔剂
倒渣
脱碳
出钢
熔渣回收
转炉A 脱碳炉渣热回收
装入铁 水废钢
脱磷 吹炼
90
比 例
40000 85 80
转 炉钢产量/万t
30000
产量
75 20000 70 10000 65 0 60
2000
2001
2002
2003
2004
2005
2006
2007
年份
转 炉钢比 例/%
转炉炼钢生产流程及车间的发展
传统转炉炼钢工艺流程及车间
宝钢一期炼钢车间平面布置示意图
10—430吨/80吨桥式起重机, 21—440吨/80吨桥式起重机,22—3吨悬臂吊车;
炼钢原材料质量要求和供应 铁水成分 C Si Mn >0.3 4.0~4.3 0.4~0.6 (%) P <0.10 S ≤0.06
入炉铁水温度>1250℃,年需铁水XXX万吨。 废钢形状及单重表
来源 厂内回收废 钢 种类 炼钢废钢 连铸废钢 成品废钢 形状尺寸(mm) 厚度 <250 <250 <300 宽度 <500 <500 <500 长度 <1000 <1000 <1000 单重(t) <1.0 <1.0 <1.0
宝钢二炼钢于1998年4月 投产 , 属于宝钢三期建设 项目 , 设计年产量 288 万 t 。 2006 年通过挖潜改造 , 新 增 1 座转炉、 1 台 RH 、 1 座 LF 、 1 座 IR-UT (Injection Refining-Up Temperature) 和1台连铸机,目前产能已 达到680万t。主要品种有 电工钢、镀锡板、汽车 用钢、高强度钢等。
宝钢湛江项目金属料平衡图
高炉炼铁 2×5050m3
823
转炉炼钢
509.74
3×300t
892.8
383.06
2150mm板坯连铸x2
499.51
1650mm板坯连铸x2
315.4
60
2250mm热轧
550
1780mm热轧
310
平整横 切机组
2030mm 冷轧
酸洗
热轧商品 材(供南 沙冷轧)
平整分 卷机组
普碳钢 优质碳素结构钢 低合金钢 冷镦钢
Q235B 20、45、65、70、82B HRB335、HRB400 ML08Al、SWRCH22A、 SWRCH35
外购废钢
打包废钢
<300
<500
<1000
<0.8
年需废钢XXX万吨。
(4)氧气转炉的容量和座数(委托单项转炉设计时要说明,做全 车间设计时可作指定或根据年钢产量确定;如果转炉是在现有 厂房内的改造项目,则尚需提供转炉周围的厂房尺寸和图纸 )。 (5) 连铸机浇铸的各种连铸坯断面尺寸、单机的生产能力、要 求的连铸机流数和台数、要求的连铸机类型 (如弧形多点矫直、 立弯弧形多点矫直等 )和基本半径。如果连铸机是在现有厂房 内增建或改建项目,则需提供连铸机周围的厂房尺寸和图纸。 (6) 对于转炉全连铸炼钢厂整体设计,需提供到达车间的基本 原料(石灰、铁矿、氧化铁皮等)的成分和粒度,废钢(尤其是外 供废钢) 的类型和品质,可供应的各种能源的状况,可供耐火 材料(主要是炉衬材料)的类型和品质等,并且提出这些物品的 运输方式。 (7) 对于转炉全连铸炼钢厂整体设计,用户的有关具体要求, 如采用新技术的水平,已有配套辅助设备的利用,投资的使用 和限定,要求选用的有关配套设备如混铁车容量和炉外精炼的 类型等。
热轧商品材
总能力:铁水823、钢坯874.9、热轧860、冷轧320(含酸洗)万吨
宝钢湛江项目总图及物流 二、总平面布置图
原料
预留二期用地
混匀 烧结
预留二期用地
2030冷轧 原料 球团
辅料
预留二期用地
2250热轧 炼钢连铸 1780热轧 1550冷轧
化产
预留二期用地
焦化
炼铁
预留二期用地
设计工作程序
冶金工厂设计基础 (钢铁冶金工厂设计)
钢铁生产工艺流程 1 长流程钢铁生产
2 短流程炼钢
钢铁厂实际设计中出现的问题
1、设备安全生产
设计的设备如果不能保证安全生产,投 产后将容易造成事故。 2、前后工序的产量匹配
(1)厂际之间:炼铁-炼钢之间产量匹配
(2)厂内工序之间:转炉-精炼-连铸匹配
电炉-精炼-连铸匹配
氧气转炉炼钢自1952年在奥地利诞生以来,因其生产率高、 建设费用低、节省劳动力、不需外加能源、生产成本低、钢质 量好、耐材消耗少、易与连铸配合等优点而得到迅速发展。
世界转炉钢产量占总的钢产量的百分比从 1961 年的 6% 上 升到 1970 年的 43.0% ,到 1996 年,转炉钢产量的比例达到 60.2% 。 2007 年中国的钢产量为 4.9 亿 t ,转炉钢产量达到 4.4 亿t,转炉钢产量占总钢产量的 90%。2010年,我国粗钢产量 6.27亿吨,其中转炉钢产量约为 5.6亿吨,约占粗钢总产量的 89.4%。2016年全国钢产量8.0837亿t。
为解决总体方案和建设总体部署等重大问题,需进行总体规划或总体设计。 一般建设项目的设计分为初步设计和施工图设计两个阶段。技术复杂而又缺乏设 计经验的专业工程,可以在施工图设计前增加技术设计,然后在此基础上编制施工 图设计。 (1)制订方案设计文件,它的目的是满足编制初步设计文件和控制概算的需要。 大中型建设工程的方案设计是在核准的立项文件的基础上,对建设项目进行总体 部署和安排,使设计意图具体化,细化总平面布局、功能分区、总体布置、空间组 合、交通组织等;细化总建筑面积等各项技术经济指标。 (2)初步设计的目的是为了满足编制施工招标文件、主要设备材料订货和编制施工 图设计文件等的需要。要做到六定:定规模、定设备、定方案、定总体、定定员和 定投资。对于建设一个炼钢厂,在做出的初步设计报告中,首先应阐述设计依据, 然后介绍钢厂的规模和产品的方案,生产的工艺流程,生产设备容量及其基本参数, 车间厂房的组成和基本尺寸,各项生产和原材料及能源的消耗指标,设计成本和投 资总概算,人员配备,各项工艺设备的性能和所需数量及其重量,车间平面图,车 间纵横剖面图,车间内各层平台平面图,炼钢炉炉型及连铸机辊列图等。此外,还 包括有关辅助专业的介绍,如燃气、氧气、热力、供排水、仪表、电力、通风、机 械化、技术经济和土建等。 (3)施工设计的目的应当满足设备材料采购、非标准设备制作和施工需要,并注明 建设工程合理使用年限。设计出进行施工所需的各种工艺施工图纸,如车间平面与 剖面总图、炉型及砌砖图、吹氧喷头图和中间包砌砖图等,主要是为有关专业的施 工图提供工艺条件和要求。