机械加工产品检验作业指导书
机加工检验作业指导书

机加工检验作业指导书[1]SL/01机加工检验作业指导书一、适用范围规定了工程机械机械加工件的技术要求,适用于各类机械加工件。
二、作业要求1、凡机械加工件必需符合产品图样、工艺规程和作业要求。
2、经加工的零件外表不允许有锈蚀和磕碰、划伤、裂纹等缺陷。
3、除有特别要求外,加工后的零件不允许留有尖棱、尖角和毛刺。
4、滚压精加工的外表,滚压后不得有剥离及脱皮现象。
5、精加工后的外表、摩擦面和定位面等工作外表不允许在其上打印标记。
6、经加工后的零件在搬运、存放时,必需防止受到损伤、腐蚀及变形。
7、成组配对加工的零件,如:齿轮箱上下盖等需有标记。
三、未注尺寸公差参阅附件:技术标准 JB/T 5936-91 四、未注外形和位置公差参阅附件:技术标准 JB/T 5936-91 五、未注公差角度的极限偏差参阅附件: 技术标准 JB/T 5936-91 六、螺纹、键和键槽参阅附件:技术标准 JB/T 5936-91七、中心孔1、图样中未注明、加工中又需要中心孔的零件,在不影响使用和外观的状况下,加工后中心孔可以保存。
2、中心孔需符合 GB 145 的规定。
八、检验规章1、凡经机械加工件,由制造厂质量检验部门按图样、有关技术文件和本要求进展检查和验收。
2、机械加工件的外观按规定要求进展检查。
3、主要机械加工件需每件检查几何外形与尺寸。
九、标志1、入库的机械加工件应有的标志2、标志的位置应不使机械加工件的质量受到损伤。
3、机械加工件入库应附有吊牌。
其中应注明:名称、零件名称、图号; 制造日期。
编制/日期: 审批:下面是赠送的团队治理名言学习,编辑删除感谢1、沟通是治理的浓缩。
2、治理被人们称之为是一门综合艺术--“综合”是由于治理涉及根本原理、自我认知、才智和领导力;“艺术”是由于治理是实践和应用。
3、治理得好的工厂,总是单调乏味,没有仸何激劢人心的大事发生。
4、治理工作中最重要的是:人正确的事,而不是正确的做事。
5、治理就是沟通、沟通再沟通。
机械加工通用作业指导书【范本模板】
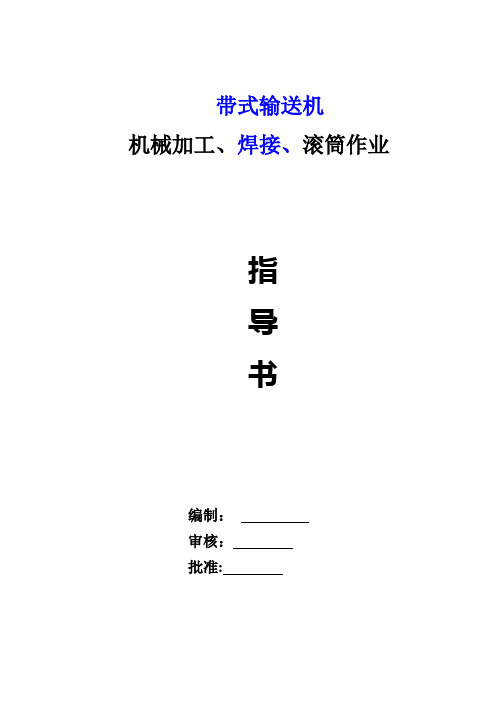
带式输送机机械加工、焊接、滚筒作业指导书编制:审核:批准:山西交城县兴星冶金设备厂机械加工通用作业指导书1、操作者应仔细看清图纸和工艺文件的各项说明,保持图纸和工艺文件的清洁与完整,并应严格按设计图纸、工艺规程和技术标准进行零部件的加工,不得随意自行更改.2、操作者按照工艺要求查看借用的工、夹、量、刀具是否符合工艺及使用要求,若有疑问,应立即与组长或车间生产管理者联系。
3、操作者应将工、夹、量、刀具分别整齐地放置在工具箱上或其它适当的地方,但不准直接放在机床上,并应妥善保管好,不得任意拆卸而改变原来尺寸或形状.4、在加工前,操作者首先应检查、抽查毛坯或经由上道工序加工并和本工序有关的尺寸,以确定余量是否符合工艺要求。
5、操作者应按照工艺规定的定位基面安装零件。
工艺未规定定位基面的,允许操作者自行选择定位基面和装夹方法,但是必须保证加工出来的工件符合图纸和工艺上的尺寸和精度要求。
在装夹工具前,应将夹具和工件清理干净,在定位基面上不得有铁屑、毛刺、污物及磕碰现象。
6、预压紧工件后,应按工艺要求进行工件的校正,若工艺未作出规定时,可按下列方法校正工件:6.1、当在本工序或本工步中加工到成品尺寸,且以后该加工面不再加工,装配时也不再调整或刮研时,可以按定位基面到加工面技术要求的1/3值校正,最后加工完成后应保证图纸中的技术要求。
6.2、在本工序或本工步中加工的加工面以后尚需加工或刮研,则按该加工面下道工序余量的1/3值校正,加工后要按此检验。
6.3、在本工序或本工步中加工的加工面到成品尺寸,以后该加工面不再加工,且图纸、工艺卡片内对该加工面与定位面无任何要求时,加工后应达到通用技术标准。
7、按工艺要求进行压紧,如工艺上无要求,零件压紧时注意压紧力的位置、大小和方向,并允许自加各种辅助支承,以增强刚性。
压紧前与压紧后都要测量,防止变形和磕碰。
8、凡加工面末到成品尺寸而工艺卡片又未规定工序的粗糙度时,粗车、粗铣、粗刨、粗镗和粗插的表面粗糙度应为Ra6.3(△4),磨削前的各种表面粗糙Z应为Rd3.2(△5),粗磨时外围的表面粗糙度应为Ra0.8(△7),平面、轴、孔互为Ral.6(△6);刮研前的加工面应为Ra3.2~Ral.6(△5~△6)。
机械加工作业指导书Microsoft Word 文档
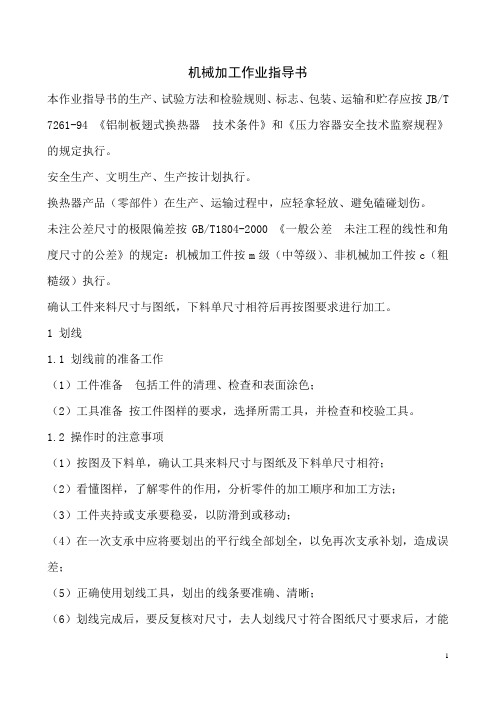
机械加工作业指导书本作业指导书的生产、试验方法和检验规则、标志、包装、运输和贮存应按JB/T 7261-94 《铝制板翅式换热器技术条件》和《压力容器安全技术监察规程》的规定执行。
安全生产、文明生产、生产按计划执行。
换热器产品(零部件)在生产、运输过程中,应轻拿轻放、避免磕碰划伤。
未注公差尺寸的极限偏差按GB/T1804-2000 《一般公差未注工程的线性和角度尺寸的公差》的规定:机械加工件按m级(中等级)、非机械加工件按c(粗糙级)执行。
确认工件来料尺寸与图纸,下料单尺寸相符后再按图要求进行加工。
1 划线1.1 划线前的准备工作(1)工件准备包括工件的清理、检查和表面涂色;(2)工具准备按工件图样的要求,选择所需工具,并检查和校验工具。
1.2 操作时的注意事项(1)按图及下料单,确认工具来料尺寸与图纸及下料单尺寸相符;(2)看懂图样,了解零件的作用,分析零件的加工顺序和加工方法;(3)工件夹持或支承要稳妥,以防滑到或移动;(4)在一次支承中应将要划出的平行线全部划全,以免再次支承补划,造成误差;(5)正确使用划线工具,划出的线条要准确、清晰;(6)划线完成后,要反复核对尺寸,去人划线尺寸符合图纸尺寸要求后,才能进行机械加工;(7)批量生产时,划线可只划1~2件,其余加工时用靠模板来定位后进行加工(视具体情况而定)。
2 金加工2.1 车加工(1)接头;①按图要求,取工件将其夹上车床三(四)爪卡盘,调整同轴度,车出或用沙皮纸打光外圆;②按图要求,钻孔并镗孔,保证孔位、孔径、孔深及孔的粗糙度符合图纸要求;③按图要求,车出端面,保证平面与孔的垂直度及平面的粗糙度符合图纸要求;④按图要求,孔口倒角,保证各倒角的尺寸,跳动度、粗糙度符合图纸要求;⑤顶上尾架攻丝3-5牙,其余牙纹手工攻丝;⑥按图要求,定尺车肩,倒除全部锐角后定尺车割下;⑦取工件夹上三(四)爪卡盘,手工攻丝至有效深度,用塞规检验。
(2)法兰:①按图要求,取工件将其夹上车床三(四)爪卡盘,调整同轴度;②按图要求,钻孔,保证孔位、孔深符合图纸要求,镗孔,保证孔径及粗糙度符合图纸要求;③按图要求,车出端面,保证平面与孔的垂直度及平面的粗糙度符合图纸要求;④按图要求,将工件调头,车出另一端面,保证厚度尺寸、保证平面与孔的垂直度、与另一平面的平行度及平面的粗糙度符合图纸要求。
机械加工作业指导书范例
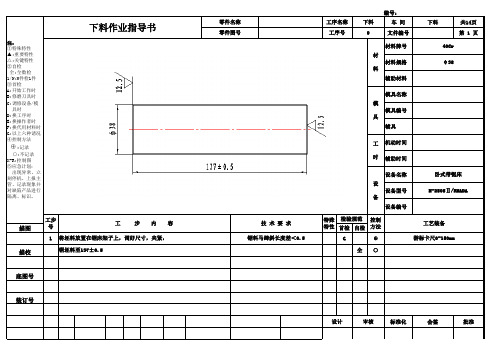
工 机动时间 时 辅助时间
设备名称
设 设备型号
备
设备编号
卧式带锯床 H-2505Ⅱ/RMADA
特殊 检验规范 控制 特性 首检 自检 方法
G
⊕
工艺装备 游标卡尺0-150mm
全○
设计
审核
标准化
会签
批准
标记 处数 更改文件号 签字 日期 标记 处数
更改文件号
签字
日期
注: ①特殊特性 ▲:重要特性 △:关键特性 ②自检
下料作业指导书
描图 描校
工步 号
工
步内容
1 将坯料放置在锯床架子上,调好尺寸,夹紧,
锯坯料至137±0.5
底图号
装订号
零件名称 零件图号
技术要求 锯料马蹄斜长度差<0.5
工序名称 工序号
下料 0
编号: 车间
文件编号
材料牌号
材 材料规格
料
辅助材料
下料
共14页 第1页
40Cr
φ38
模具名称
模 模具编号
具
全:全数检 1/N:N件检1件 ③首检 A:开始工作时 B:修磨刀具时 C:调修设备/工
装时 D:换工序时 E:换操作者时 F:换代用材料时 G:以上六种请况 ④控制方法
⊕:记录
○:不记录 X-R:控制图 ⑤应急计划:
出现异常,立 刻停机、上报主 管、记录现象并 对缺陷产品进行 隔离、标识。
机械加工作业指导书
更改文件号
签字
零件名称 零件图号
日期
工序名称 工序号
钻两孔 15
编号: 车间
文件编号
毛坯种类 材
毛坯尺寸 料
材料牌号
共14页 第4页
机械加工作业指导书
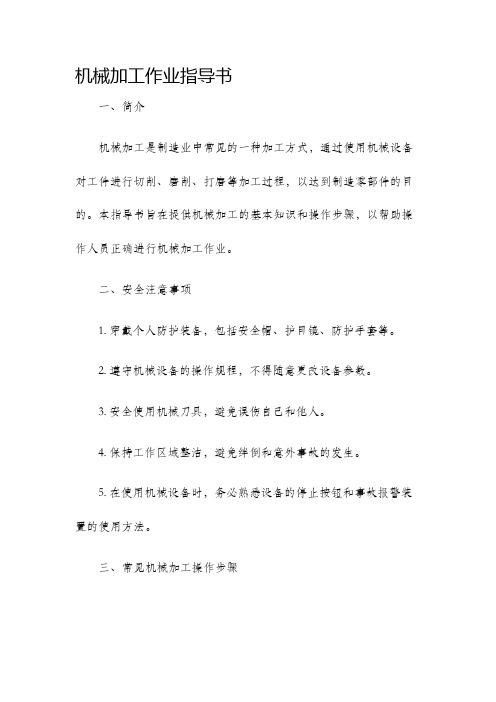
机械加工作业指导书一、简介机械加工是制造业中常见的一种加工方式,通过使用机械设备对工件进行切削、磨削、打磨等加工过程,以达到制造零部件的目的。
本指导书旨在提供机械加工的基本知识和操作步骤,以帮助操作人员正确进行机械加工作业。
二、安全注意事项1. 穿戴个人防护装备,包括安全帽、护目镜、防护手套等。
2. 遵守机械设备的操作规程,不得随意更改设备参数。
3. 安全使用机械刀具,避免误伤自己和他人。
4. 保持工作区域整洁,避免绊倒和意外事故的发生。
5. 在使用机械设备时,务必熟悉设备的停止按钮和事故报警装置的使用方法。
三、常见机械加工操作步骤1. 初步设计:首先,根据工件的要求,确定加工工艺和加工方法。
包括选择合适的机床和刀具,并进行初步计算。
2. 安装工件:根据机床的类型和工件的特点,正确安装工件。
确保工件固定稳定,避免在加工过程中产生位移或松动。
3. 调整刀具:根据工件要求,选择合适的刀具,并进行装夹和调整。
确保刀具与工件的相对位置和角度正确。
4. 加工参数设置:根据工件材料和加工要求,设置合适的加工参数,包括切削速度、进给速度和切削深度等。
5. 检查设备状态:在加工过程前,检查设备的运行状态,包括润滑系统、冷却系统等是否正常运行,避免设备故障导致加工质量下降。
6. 开始加工:按照设定的加工程序和顺序,启动机床,开始加工工件。
过程中,密切关注加工状态,确保加工质量。
7. 完成加工:当工件加工完毕后,及时关闭机床,并进行工件的检查和测量。
确保加工工件符合要求。
四、常见问题及解决方法1. 加工过程中出现加工质量下降的情况:可能是刀具磨损严重,需要更换刀具;或者加工参数设置不当,需要调整加工参数。
2. 工件加工后出现尺寸偏差的问题:可能是机床定位不准确,需要重新调整机床;或者是工件固定不稳,需要重新安装工件。
3. 加工过程中发生设备故障:应及时关闭机床,并联系维修人员进行修理。
五、总结机械加工作业是制造业中常见的一种操作,正确的机械加工操作步骤能够保证加工质量和工作安全。
机加工作业指导书模板

机加工作业指导书模板摘要:一、引言二、机加工作业概述1.加工范围2.加工方法3.加工材料三、机加工工艺流程1.工艺流程步骤2.工艺参数设置3.加工注意事项四、机加工安全操作规程1.操作规程要点2.安全防护措施3.异常情况处理五、机加质量控制与检验1.质量控制要求2.检验方法与标准3.质量改进措施六、设备维护与保养1.设备维护内容2.设备保养周期3.设备故障排除七、环境保护与职业健康1.环保措施2.职业健康要求3.培训与教育八、总结与展望正文:一、引言随着现代制造业的快速发展,机加工作业在各类工厂中得到了广泛应用。
为了规范机加工作业流程,提高工作效率,保证加工质量,特制定本指导书。
本指导书旨在为从事机加工作的人员提供一套完整的作业规范,内容包括机加工作概述、工艺流程、安全操作规程、质量控制与检验、设备维护与保养、环境保护与职业健康等方面。
二、机加工作业概述1.加工范围机加工作业主要包括金属切削、钻孔、磨削、镗孔、铣面、刨削、拉削等加工过程。
2.加工方法加工方法主要包括普通加工和数控加工。
普通加工包括手动加工和自动加工,数控加工采用数控机床、加工中心等设备进行高精度加工。
3.加工材料加工材料主要包括金属材料、非金属材料和复合材料。
金属材料包括铁、钢、铝、铜等,非金属材料包括塑料、橡胶、陶瓷等,复合材料包括碳纤维、玻璃纤维等。
三、机加工工艺流程1.工艺流程步骤(1)工艺分析与方案制定(2)设备选用与安装(3)刀具准备(4)工件装夹与定位(5)加工操作(6)加工质量检验(7)成品验收与包装2.工艺参数设置根据加工材料、刀具、设备等因素,合理设置切削速度、进给速度、切削深度等工艺参数。
3.加工注意事项(1)遵守操作规程,防止误操作(2)注意加工过程中刀具的磨损与更换(3)保持设备清洁,防止故障发生(4)定期检查加工质量,确保加工精度四、机加工安全操作规程1.操作规程要点(1)认真阅读操作手册,掌握设备性能(2)严格遵守操作规程,不得擅自变更(3)开机前检查设备完好,确认无异常(4)穿戴劳动保护用品,严禁酒后操作2.安全防护措施(1)设置安全防护装置,如防护罩、限位器等(2)定期检查电气线路,防止短路、漏电等事故(3)使用安全可靠的电源,避免触电事故3.异常情况处理遇到异常情况,如设备故障、加工质量问题等,应立即停机检查,找出原因并进行处理。
机械制造作业指导书精选

机械制造作业指导书精选在机械制造领域,作业指导书是确保生产过程高效、质量稳定的重要工具。
它为操作人员提供了详细的操作步骤、技术要求和注意事项,使生产能够标准化、规范化地进行。
以下为您精选了几种常见机械制造作业的指导书示例。
一、车床加工作业指导书1、加工前的准备操作人员应熟悉加工图纸和工艺要求,明确加工零件的尺寸、形状、精度等技术指标。
检查车床的各部分是否正常,包括润滑系统、电气系统、刀具夹紧装置等。
安装好所需的刀具,并调整刀具的位置和角度,确保刀具锋利且安装牢固。
准备好所需的量具,如卡尺、千分尺等,并确保量具经过校准且在有效期内。
2、工件的装夹根据工件的形状和尺寸,选择合适的夹具,如三爪卡盘、四爪卡盘或顶尖等。
装夹工件时,要确保工件的中心与车床主轴的中心重合,并且夹紧力度适中,避免工件变形或松动。
对于细长轴类工件,应使用跟刀架或中心架来增加工件的刚性,防止加工时产生振动。
3、切削参数的选择根据工件的材料、硬度、加工精度和表面粗糙度要求,合理选择切削速度、进给量和切削深度。
一般来说,对于硬度较高的材料,应选择较低的切削速度和较小的进给量;对于要求表面粗糙度较低的工件,应选择较小的切削深度和较高的切削速度。
4、加工过程启动车床,使主轴旋转,然后手动移动刀架,接近工件进行试切削,检查切削深度和表面质量是否符合要求。
调整好切削参数后,进行正式切削。
在切削过程中,要密切观察刀具的磨损情况、工件的表面质量和尺寸精度,如有异常应及时停机处理。
定期测量工件的尺寸,确保加工尺寸在公差范围内。
对于精度要求较高的尺寸,应采用多次测量取平均值的方法,以提高测量精度。
5、加工结束加工完成后,先停止车床主轴的旋转,然后将刀架移动到安全位置。
卸下工件,清理车床和工作区域,将刀具和量具妥善存放。
二、铣床加工作业指导书1、加工前的准备熟悉加工图纸和工艺要求,了解加工零件的形状、尺寸、精度等技术要求。
检查铣床的各部分是否正常,包括主轴、工作台、进给机构、润滑系统等。
机加工作业指导书

机加⼯作业指导书机加⼯作业指导书⼀、⽬的与适⽤范围本作业指导书旨在规范机械加⼯过程中的操作步骤、技术要求及安全注意事项,确保机械加⼯产品的质量和⽣产效率,同时保障操作⼈员的安全。
本指导书适⽤于公司内所有涉及机加⼯岗位的⽣产活动,包括但不限于铣削、⻋削、磨削、钻削等加⼯⽅式。
⼆、作业前准备1.设备检查:开机前,操作⼈员应对机床进⾏全⾯检查,确认机床各部位(如主轴、导轨、传动系统等)⽆异常,润滑油量充⾜且清洁,安全防护装置完好。
2.⼯具与量具准备:根据加⼯图纸要求,准备相应的⼑具、夹具、量具等辅助⼯具,并检查其是否完好⽆损,规格型号是否匹配。
3.⼯件准备:确保待加⼯⼯件清洁⽆异物,根据⼯艺要求正确安装⾄夹具上,并紧固牢靠。
4.程序编制与加载:对于数控机床,需根据加⼯图纸编制加⼯程序,并进⾏模拟验证⽆误后,⽅可加载⾄机床控制系统中。
5.个⼈防护:操作⼈员应穿戴好劳动防护⽤品,如安全帽、防护眼镜、防护服、防护鞋及防尘⼝罩等。
三、作业流程1.开机与对⼑:按照机床操作规程启动机床,进⾏机床回零操作。
对于需要对⼑的机床,准确进⾏⼑具与⼯件的对⼑操作,并记录相关数据。
2.参数设置:根据加⼯要求,设置机床的加⼯参数,包括主轴转速、进给速度、切削深度等,确保参数设置合理,避免超负荷运⾏。
3.加⼯操作:开始加⼯前,再次确认所有设置⽆误,启动加⼯程序。
加⼯过程中,操作⼈员应密切关注机床运⾏状态及加⼯质量,及时发现并处理异常情况。
4.质量监控:加⼯过程中,适时使⽤量具对⼯件进⾏尺⼨检查,确保加⼯精度符合要求。
对于不合格品,应及时分析原因并采取纠正措施。
5.换⼑与调整:根据加⼯需要,适时更换⼑具或调整切削参数,以保证加⼯效率和加⼯质量。
四、作业结束与清理1.停机与清理:加⼯完成后,按照机床操作规程停机,并清理机床及周围环境,保持⼯作区域整洁。
2.⼯件与⼯具整理:将加⼯完成的⼯件分类摆放,并做好标识;整理好⼑具、夹具、量具等辅助⼯具,归位存放。
- 1、下载文档前请自行甄别文档内容的完整性,平台不提供额外的编辑、内容补充、找答案等附加服务。
- 2、"仅部分预览"的文档,不可在线预览部分如存在完整性等问题,可反馈申请退款(可完整预览的文档不适用该条件!)。
- 3、如文档侵犯您的权益,请联系客服反馈,我们会尽快为您处理(人工客服工作时间:9:00-18:30)。
一汽解放青岛汽车厂质量保证部技术文件
编号:IPQC-JYZD-7-2009 批准:宋宗强
机械加工产品
检验作业指导书
2008年12月31日发布2009年1月1日实施
一汽解放青岛汽车厂质量保证部发布
前言
本检验作业指导书依据有关汽车标准及一汽解放青岛汽车厂技术文件制定。
是一汽解放青岛汽车厂质量保证部技术文件之一。
本检验作业指导书与国家标准、企业标准及相关技术文件相一致。
从实施之日起,原《IPQC-JYZD-7-2008机械加工产品验作业指导书》同时废止。
各相关部门检验机械加工产品质量时,都需要按本检验作业指导书的规定执行。
本标准由一汽解放青岛汽车厂质量保证部起草。
本检验作业指导书起草人:林桂升
本检验作业指导书审核人:石建通
1 主要内容与适用范围
本检验作业指导书规定了机械加工产品的检验方式及质量记录。
本检验作业指导书主要适用于机加工车间。
2 引用标准
下列标准包括的条文,通过在本检验作业指导书中的引用而构成本标准的条文。
在本检验作业指导书发布时,所示版本均为有效。
所有标准都会被修订,使用本标准的各方应探讨使用下列标准最新版本的可能性。
CA/CBG-1-82 切削零件未注公差尺寸的公差
CA/CBG-9-91 未注公差角度的极限偏差
3 检验及质量记录规定
3.1所有机加工产品必须按产品标准、技术要求等进行自检控制。
3.2检验零件时,按控制计划合理选用量检具,并正确操作。
3.3未注公差尺寸的极限偏差
3.3.2 两孔的中心距和孔与零件边缘距离的未注公差尺寸的公差按下表执行。
(以孔径为基本尺寸查选。
当两孔径不相等时,其轴心距的公差按两孔直径的算术平均值确定。
)如
3.3.4 L查选。
3.3.5 螺纹长度尺寸L未注公差的极限偏差:对非全螺纹,长度L偏差为0~+1.5P;对全螺纹,长度L偏差为-1.5P~0。
(P:螺纹的螺距)
3.4 正常路线件
3.4.1 对有明确公差要求的尺寸,检查员按不低于1/30的频次抽检并形成质量记录。
每日记录5——7种,在此类制件中,其它无明确公差要求的尺寸可按不低于1/50的频次检验并记录。
3.4.2 对无明确公差要求的产品,其质量由生产操作者负全责,检查员对此类产品按不低于1/50的频次进行抽检,每天对5——7种件记录。
3.4.3 机械加工件应无铁屑、尖锐毛刺、锈蚀等。
3.5 迂回工艺路线件
3.5.1 用钻孔胎生产的钻孔件,检查员对每天每种生产件的首件、末件进行检验并记录,并且中间抽检一次,形成记录。
3.5.2 用其它方法生产的钻孔件(包括划线钻孔、模板打点钻孔等),检查员应对每种每批次的零件按不低于1/50的频次抽样检验并记录。
3.5.3 钻孔孔边毛刺不应大于0.5mm高度。
3.6 检查员应做到随机抽样,并尽可能做到及时、准确。
3.7 检验、记录数
按3.4、3.5规定抽检频次检验、记录时,每批制件3件以下(包括3件)需全检,3件以上检验记录数不应少于3件。