金属切削基本理论
金属切削基本知识课件

由于切削参数不当或切削材料中含有杂质等原因,导致刀具快速磨 损或破损。
破损形式
包括崩刃、卷刃和断裂等,可能是由于刀具材料缺陷或使用不当所 致。
03
金属切削过程
切屑的形成与控制
切屑的形成
金属切削过程中,刀具对工件材料施 加压力,使材料发生剪切滑移,形成 切屑。切屑的形状和大小取决于工件 材料、刀具几何形状和切削用量。
金属切削是一种高效、高精度的加工 方式,广泛应用于机械制造、航空航 天、汽车、模具等领域。
金属切削的分类
根据切削方式
01
可分为车削、铣削、钻削、磨削等。
根据切削用量
02
可分为高速切削和低速切削。
根据切削液
03
可分为干切削和湿切削。
金属切削的原理
切削力
在切削过程中,刀具切入工件时产生的切削力, 是切削过程中的主要作用力。
切削热
由于切削过程中摩擦和变形产生的热量,会导致 刀具和工件温度升高。
切屑形成
在切削过程中,多余的金属材料形成切屑,从工 件上切除。
02
金属切削刀具
刀具的种类
车刀
主要用于车削加工,包括外圆 车刀、内圆车刀、端面车刀等
。
铣刀
用于铣削加工,包括平面铣刀 、圆柱铣刀、键槽铣刀等。
钻头
主要用于钻孔加工,包括直柄 钻头、锥柄钻头等。
磨削加工技术
定义
磨削加工是利用磨床对金属工件进行切削加工的方法。
特点
磨削加工可以获得较高的加工精度和表面质量,适用于各种硬质合 金、淬火钢等高硬度材料的加工。
应用
在机械制造中,磨削加工广泛应用于各种刀具、模具、量具等精密零 件的加工。
06
金属切削原理基本理论

当刀具作用于切屑层,切削刃由a相对运动至 O时,整个切削单元OMma就沿着OM面发生剪 切滑移;或者OM面不动,平行四边形OMma 受到剪切应力的作用,变成了平行四边形 OMm1a1 。
实际上切屑单元在刀具前面作用下还受到挤 压,因而底边膨胀为Oa2,形成近似梯形的切 屑单元OMm2a2 。
许多梯形叠加起来就迫使切屑向逆时针方 向转动而弯曲。因此也可以说,金属切削过程 是切削层受到刀具前面的挤压后,产生以剪切 滑移为主的塑性变形,而形成为切屑的过程。
一) 切屑的形成过程 我们将切屑形成过程近似地比拟为推挤一叠卡片的形象化模型。
刀具
工
件
切屑形成过程模拟
金属被切削层好比一迭卡片1´、2 ´ 、3 ´ 、4 ´…等,当刀具切入 时这迭卡片被摞到1、2、3、4….的位置。卡片之间发生滑移,这滑 移的方向就是剪切面。
当然卡片和前刀面接触这一端应 该是平整的,外侧是锯齿的、或呈不 明显的毛茸状。
金属切削的基本物理现象包括:切削变形、切削力、切削温度、 刀具磨损与刀具耐用度。本章将针对这些现象进行阐述。
§ 3-1 切削变形
切削过程中的各种物理现象,都是以切屑形成过程为基础的。 了解切屑形成过程,对理解切削规律及其本质是非常重要的,现以塑性 金属材料为例,说明切屑的形成及切削过程中的变形情况。
第Ⅰ变形区 近切削刃处切削层内产生的塑性变形区——剪切滑移变形; 第Ⅱ变形区 与前刀面接触的切屑底层内产生的变形区——挤压变形; 第Ⅲ变形区 近切削刃处已加工表层内产生的变形区——已加工表面变形。
三) 第一变形区内金属的剪切变形
追踪切削层上任一点P,可以观察切屑的变形和形成过程。
当切削层中金属某点P向切削刃逼近,到达点1时,此时其剪切应力达到材 料的屈服强度τ s,故点1在向前移动 的同时,也沿OA滑移,其合成运动 使点l流动到点2。2- 2 ´为滑移量, 当P点依次到达3、4点后,其流动方 向与前刀面平行,不再沿OM线滑移。 OA称为始剪切滑移线,OM称为终 剪切滑移线。
金属切削原理(基本理论)
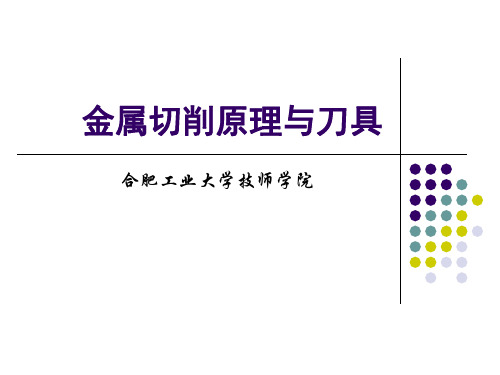
减小切屑与刀具前刀面的摩擦,并能降低切削温度,所以不易
产生积屑瘤。
积屑瘤对切削过程的影响
1. 影响刀具耐用度:
积屑瘤包围着切削刃,同时覆盖着一部分前刀面。积屑
瘤相对稳定时,可代替切削刃进行切削。切削刃和前刀面
都得到积屑瘤的保护,减少了刀具的磨损,提高刀具耐用
如铜、20钢、40Cr钢、1Crl8Ni9Ti等,随着工件材料的强
度和硬度的依次增大,摩擦系数μ略有减小;
这是由于在切削速度不变的情况下,材料的硬度、强度
大时,切削温度增高,故摩擦系数下降。
切削厚度ac增加时, μ也略为下降;如20钢的ac从0.
lmm增大到0. 18mm, μ从0 .74降至0 .72。因为ac增加
最后长成积屑瘤。
影响积屑瘤产生的因素:
①工件材料的影响:塑性高的材料,由于切削时塑性
变形较大,加工硬化趋势较强,积屑瘤容易形成;而
脆性材料一般没有塑性变形,并且切屑不在前刀面流
过,因此无积屑瘤产生。
②切削速度主要通过切削温度影响积屑瘤。
低速(Vc<3~5m/min)时,切削温度较低(低于
300℃),切屑流动速度较慢,摩擦力未超过切屑分子的结
工件母体分离,一部分变成切屑,很小一部分留在已加
工表面上。
第Ⅰ变形区
近切削刃处切削层内产生的塑性变形区——剪切滑移变形;
第Ⅱ变形区
与前刀面接触的切屑底层内产生的变形区——挤压变形;
第Ⅲ变形区
近切削刃处已加工表层内产生的变形区——已加工表面变形。
三) 第一变形区内金属的剪切变形
追踪切削层上任一点P,可以观察切屑的变形和形
系数ξ可直观反映切屑的变形程度,并且容易测量。
第一章金属切削基本原理
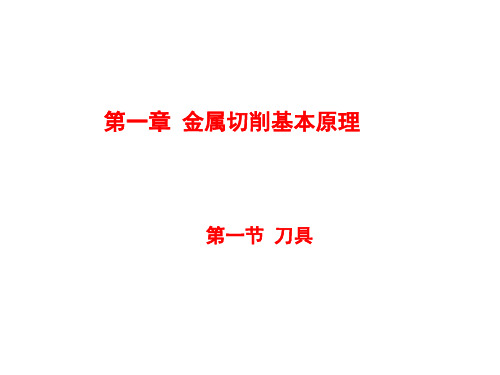
图1-5 车刀标注角度旳参照系
(四)刀具旳标注角度 1、在正交平面参照系中旳标注角度
(1)主偏角r (2)刃倾角s (3)前角o (4)后角o
“一刃四角”
切削刃旳选定点、刃倾角 和主偏角这三个参数,拟 定了主切削刃在参照系中 旳位置。
(5)副偏角 r ˊ (6)副后角oˊ
派生角度:
楔角bo、刀尖角er、余偏角r
(2)切削平面Ps 经过切削刃选定点,与切削刃相切,并垂直于基面旳平面。
(3)正交平面Po 经过切削刃选定点,同步垂直于基面和切 削平面旳平面。正交平面垂直于切削刃在 基面上旳投影。 由基准平面Pr — 切削平面Ps — 正交平 面Po构成旳静止参Pn 经过切削刃选定点并垂直于切削刃旳平面。
(二)刀具角度旳参照系
刀具标注角度旳参照系
刀具工作角度旳参照系
设计、制造、测量角度时旳基准 实际切削中拟定角度旳基准
• 静止参照系
主运动方向 进给运动方向 刀具安装位置
静态角度
• 工作参照系
实际合成切削运动方向 进给运动方向 刀具实际安装位置
工作角度
刀具静止参照系是在下列假定条件下建立旳:
1)刀刃上旳选定点位于假定工件旳轴平面内,是刀具静止 参照系旳原点;
第一章 金属切削基本原理
第一节 刀具
三、切削用量
切削用量三要素
1. 切削速度 v (m/s或m/min) 主运动为旋转运动:v =πd n/1000 往复运动:v = 2Lnr /1000
2. 进给量 f (mm/r 或mm/双行程) 进给速度:vf =n f = n fz z (mm/s 或mm/min)
(二)常用刀具材料旳种类及特征
工具钢(碳素工具钢、合金工具钢、高速钢)、硬质合金、陶瓷、金刚石 (天然、人工)、立方氮化硼等。
8、金属切削加工基本理论
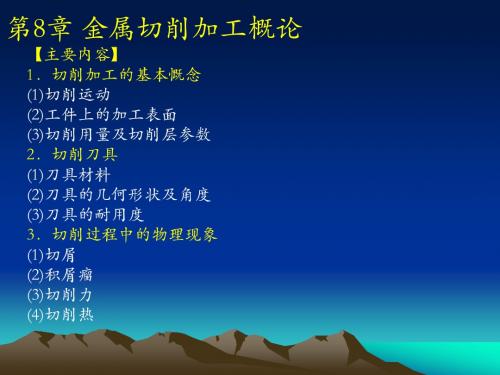
合成方法,也是利用高温高压加催化剂的方法将六方 氮化硼转变成立方氮化硼。 • 立方氮化硼是六方氮化硼的同素异形体,硬度达 8000~9000HV,是人类已知的硬度仅次于金刚石的材
料,其热稳定性和化学惰性大大优于金刚石,可耐1
300~1500°C的高温,在1200~1300°也不易 与铁系材料发生化学反应,其导热率也大大高于高速
• 2、常用刀具材料
刀具材料类型: 工具钢(高速钢) 硬质合金 陶瓷 超硬材料 最常用
工具钢耐热性差,但抗弯强度高,价格便宜,焊接与 刃磨性能好,故广泛用于中、低切削的成形刀具,不 宜高速切削。
• 3)高速钢 • 高速钢是加入了钨(W)、钼(Mo)、铬(Cr)、钒(V) 等合金元素的高合金工具钢。它们都是强烈的 碳化物形成元素,在熔炼与热处理过程中与碳 形成了高硬度的碳化物,从而提高了钢的耐磨 性。 • 高速钢的强度(抗弯强度为硬质合金的2~3倍 ,为陶瓷的5~6倍)、硬度(62~70HRC)、耐 热性(600~700°C)、韧性、耐磨性和工艺性 均较好,刃磨锋利,故又称“锋钢”,适合于 大部分常用材料的切削加工。
6)超硬刀具材料
• 超硬刀具材料有金刚石和立方氮化硼。金刚石可分天然和人造两 种,其代号分别用JT和JR表示,都是碳的同素异形体。
• 天然金刚石大多属于单晶金刚石,单晶天然金刚石具 有各向异性(即不同晶面上强度、硬度和耐磨性差异很 大,可在100~500倍范围内变化,故制造时应考虑刃磨 方向),选择正确的刃磨方向,可使刀的刃口圆角半 径磨到最小,刀具极为锋利,可用于有色金属及非金 属的超精密加工。 • 天然金刚石价格十分昂贵,使用较少。
第8章 金属切削加工概论
【主要内容】 1.切削加工的基本慨念 (1)切削运动 (2)工件上的加工表面 (3)切削用量及切削层参数 2.切削刀具 (1)刀具材料 (2)刀具的几何形状及角度 (3)刀具的耐用度 3.切削过程中的物理现象 (1)切屑 (2)积屑瘤 (3)切削力 (4)切削热
金属切削的基本理论
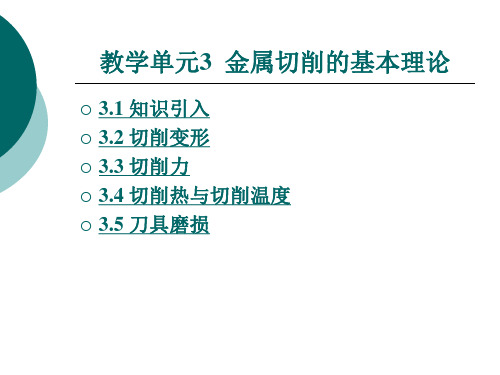
上一页 下一页 返回
3.2 切削变形
相应的轮廓算术平均偏差Rα为
Ra 1 Rz mm
用圆头刀加工时,残留层4的最大高度Rz为:
2.实际粗糙度
Rz f 2 mm
8
实际粗糙度是在理论粗糙度上叠加着非正常因素,例如:积屑 瘤、鳞刺、刀具磨痕和切削振纹等附着物和痕迹,因此,增 大了残留面积的高度值。
刀具几何形状和切削运动对表面粗糙度的影响主要是通过刀 具的主偏角、副偏角、刀尖圆弧半径厂以及进给量对切削后 工件上的残留层高度来体现的。主偏角、副偏角、进给量越 小表面粗糙度越小;刀尖圆弧半径厂越大,表面粗糙度越小。
如图3-8所示,用尖头刀加工时,残留层的最大高度Rz为
Rz
f
mm
cot cot '
教学单元3 金属切削的基本理论
3.1 知识引入 3.2 切削变形 3.3 切削力 3.4 切削热与切削温度 3.5 刀具磨损
教学单元3 金属切削的基本理论
金属切削的基本理论是关于金属切削过程中基本物理现象变 化规律的理论。金属切削过程就是刀具从工件表面上切除多 余的金属,形成切屑和已加工表面的过程。伴随这一过程将 产生一系列物理现象,包括切削变形、切削力、切削温度和 刀具磨损等,而这些现象均以切削过程中金属的弹性、塑性 变形为基础,将直接或间接地影响工件的加工质量和生产率 等。生产实践中出现的积屑瘤、鳞刺、振动等问题,又都同 切削过程中的变形规律有关。因此,了解并掌握这些变化规 律,对分析解决切削加工中出现的问题有着十分重要的意义。
(1)积屑瘤和鳞刺影响钻附在刀刃上的积屑瘤顶端切入加工表 面后使已加工表面粗糙不平。在已加工表面上垂直于切削速 度方向会产生突出的鳞片状毛刺,通常称作鳞刺(如图3-9所 示)。
金属切削的基本理论
此外,切屑的形状还与刀具切削角度及切削用量有关,当切 削条件改变时,切屑形状会随之作相应地改变,例如在车削 钢类工件时,如果我们逐渐增加车刀的锋利程度(如加大前角 等措施),提高切削速度,减小走刀量,切屑将会由粒状逐渐 变为节状,甚至变为带状。同样,采用大前角车刀车削铸铁 工件时,如果切削深度较大,切削速度较高,也可以使切屑 由通常的崩碎状转化为节状,但这种切屑用手一捏即碎。在 上述几种切屑中,带状切屑的变形程度较小,而且切削时的 振动较小,有利于保证加工精度与粗糙度,所以这种切屑是 我们在加工时所希望得到的,但应着重注意它的断屑问题。
2.切屑的形成和种类 切削塑性金属材料(如钢等)时,被切层一般经过弹性变形、
塑性变形(滑移)、挤裂和切离四个阶段形成切屑。切削脆性 材料(如铸铁等)时,被切层一般经过弹性变形、挤裂和切离 三个阶段形成切屑。图3-3、图3-4分别表示在刨床上加工这 两种不同材料时的切削过程。
上一页 下一页 返回
3.2 切削变形
上一页 下一页 返回
3.2 切削变形
二、积屑瘤
在用中等或较低的切削速度切削一般钢料或其他塑性金属材 料时,常在前刀面接近刀刃处,钻结硬度很高(为工件材料硬 度的2~3.5倍)的楔形金属块,这种楔形金属块称为积屑瘤, 如图3-1所示。
积屑瘤的形成 (1 )形成条件简单地概括为3句话:中等切削速度,切削塑性材
下一页 返回
3.1 知识引入
车削
63
0 0.05
短轴外圆时,在CKS6116车床(7.5kW)上加工,
进给量为0.3 mm/ r ,背吃刀量为1.5mm,转速为800 r/min,设机
金属切削的基础知识
金属切削的基础知识金属切削是一种通过切削工具在金属工件上施加力量,使其产生剪切应力,从而剥离所需形状的金属层的加工方法。
它是目前最常用和广泛应用的金属加工方式之一。
以下是金属切削的基础知识:1. 切削工具:切削工具通常由硬质材料制成,如高速钢、硬质合金等。
常见的切削工具包括刀片、钻头、铣刀等。
刀具的选择根据加工材料、加工形状和加工质量要求等因素进行。
2. 切削速度:切削速度是指在单位时间内切削刀具工作部分对工件的相对运动速度。
它是影响切削加工效果和刀具寿命的重要因素。
通常以米每分钟(m/min)作为单位。
3. 进给速度:进给速度是指切削刀具沿工件表面移动的速度。
它决定了每分钟进给长度。
进给速度的选择需要考虑切削深度、加工精度和刀具强度等因素。
4. 切削深度:切削深度是指切削刀具在每次切削中从工件表面剥离金属的厚度。
切削深度越大,切削力也会增加,刀具磨损加剧。
因此,切削深度的选择要根据材料性质、刀具强度和加工要求等综合考虑。
5. 切削力:切削力是指在切削过程中作用在切削刀具上的力。
它是切削加工过程中的重要力学参数,会影响刀具的磨损和加工精度。
切削力的大小与切削厚度、切削速度、切削角度和材料硬度等因素密切相关。
6. 刀具磨损:切削刀具在切削过程中会不可避免地发生磨损。
刀具磨损会使切削力增加、切削质量下降,并且降低了刀具的寿命。
因此,定期更换和修磨切削刀具是保证加工质量和生产效率的重要措施。
7. 切削液:切削液是指在金属切削过程中加入的一种液体。
它主要用于降低切削温度、润滑切削表面、冲洗切削区域,以减少金属切削时产生的摩擦和热量。
良好的切削液选择能够有效地提高加工质量和刀具寿命。
金属切削是工业生产中广泛应用的加工方式之一,掌握金属切削的基础知识对于提高加工质量、降低生产成本具有重要意义。
因此,对于从事金属加工的工作者来说,了解切削工具、切削速度、进给速度、切削深度、切削力、刀具磨损以及切削液等基础知识是十分必要的。
机械制造技术PPT课件第二章金属切削基本原理
合理副偏角值的选择
添加标题
一般较小
添加标题
—5°~10°
添加标题
精加工
添加标题
—小,0°
添加标题
加工高强高硬材料或断续切削
添加标题
—小,4°~6°
添加标题
切断刀、锯片、槽铣刀
添加标题
—小,1°~2°
过渡刃的型式
①直线刃
—粗车、强力车 κrε=κr/2
②圆弧刃
—粗糙度值小
冷却作用 清洗与防锈作用
常用切削液及其选用 =乳化油+水 切削油 = 矿物油、+动植物油 极压切削油 =切削油+硫、氯和磷极压添加剂 难加工材料的精加工
=水+防锈剂、清洗剂、油性添加剂 磨削、粗加工
①水溶液
01
车削、钻削、攻螺纹 滚齿、插齿、车螺纹、一般精加工
②乳化液
02
刀具磨损与刀具耐用度
4
磨屑形态
带状切屑
直线刃、折线刃、圆弧刃、波形刃
刀具合理几何参数选择应考虑的因素
—化学成分、制造方法、热处理状态 性能,表层情况等
①工件材料
壹
—化学成分、性能,刀具结构形式
②刀具材料及结构
—机床、夹具,系统刚性,功率 切削用量和切削液
③加工条件
叁
贰
各参数间的联系 —综合考虑相互作用与影响
刀具角度的选择
大后角→减小摩擦、提高寿命、改善表面质量 强度降低、散热差、磨损加快
后角的选择原则
工艺系统刚性 刚性差—振动 → 小后角 精度要求高 —重磨 → 小后角
切削层厚度hD小 → 大后角 切削层厚度hD大 → 小后角
强度、硬度高 → 小后角 塑性大 → 大后角
金属切削基础ppt课件
基面
基面Pr: “通过主切削刃上选定 点垂直于主运动方向的 平面”
22
切削平面
2.切削平面Ps: 3.通过主切削刃上选定 点,与切削刃相切并垂 直于基面的平面
23
主剖面
主剖面Po: 通过主切削刃上选定点,并 同时垂直于基面和切削平面 的平面
24
法平面
法平面Pn: 通过主切削刃上选定点,并垂直 于切削刃的平面。
热塑性差,不宜制造成大截面刀具。
B、钨钼钢(将一部分钨用钼代替所制成 的钢 )典型牌号:W 6 Mo 5 Cr 4 V 2
优点:减小了碳化物数量及分布的不均匀性 。 缺点:高温切削性能和W18相比稍差。
66
高性能高速钢
在通用型高速钢的基础上,通过调整基本 化学成分并添加其他合金元素,使其常温 与高温力学性能得到显著提高
45
刀具的工作角度
•刀杆轴线安装的偏 斜的影响: •改变了主偏角和副 偏角 •(也就是说:实际的 主偏角和标注时的 主偏角不同)
46
刀具的工作角度
进给运动的 影响
进给量改变了 合成运动的方 向
(从而改变了基 面的位置以及 其他面的位置, 影响所有的角 度)
47
刀具的工作角度
刀尖的安装位 置的影响
63
高速钢
概念:
高速钢是一种含有钨、钼、铬、钒等合金元 素较多的工具钢
性质:
①、具有良好的热稳定性 ②、具有较高强度和韧性 ③、具有一定的硬度(63~70HRC)和耐磨性
64
高速钢的分类
普通高速钢 钨系高速钢 钨钼钢
高性能高速钢
65
普通高速钢
A、钨系高速钢(简称 W18) 典型牌号:W18Cr4V 优点:钢磨削性能和综合性能好,通用性强。 缺点:碳化物分布常不均匀,强度与韧性不够强,
- 1、下载文档前请自行甄别文档内容的完整性,平台不提供额外的编辑、内容补充、找答案等附加服务。
- 2、"仅部分预览"的文档,不可在线预览部分如存在完整性等问题,可反馈申请退款(可完整预览的文档不适用该条件!)。
- 3、如文档侵犯您的权益,请联系客服反馈,我们会尽快为您处理(人工客服工作时间:9:00-18:30)。
➢崩碎切屑: 在切削铸铁和
黄铜等脆性材料时,切削层 金属发生弹性变形以后,一 般不经过塑性变形就突然崩 落,形成不规则的碎块状屑 片,即为崩碎切屑。
➢当刀具前角小、进给量大时易产生这种切屑,
➢产生崩碎切屑时,切削热和切削力都集中在主切
削刃和刀尖附近,刀具易崩刃、刀尖易磨损,并容 易产生振动,影响表面质量。
(2)切削力的分解
通常将合力F分解为 相互垂直的三个分力: 切削力 Fc 、进给力 Ff 、 背向力 Fp 。
主切削力Fz(Fc) 背向力 Fy(Fp)
总切削力在主运动方向的分力,大小 约占总切削力的80%~90Байду номын сангаас 。Fc消耗 的功率最多,约占总功率的90%左右, 是计算机床切削功率、选配机床电机、
形;
➢ 适当的热处理来提高工件材料的硬度、降低塑
性、减小加工硬化倾向。
(二)切削力
切削过程中,刀具 施加于工件使工件材料产生 变形,并使多余材料变为切 屑所需的力,称为切削力。
1.切削力的来源、切削合力及分力、切削功率
(1) 切削力的来源
切削力来自于金属切削过程 中克服被加工材料的弹、塑 性变形抗力和刀具与工件及 刀具与切屑之间摩擦阻力。
面上,增大表面粗糙度和导致刀具磨损。
在精加工时应尽可能避免积屑瘤的产生。
(4)抑制或消除积屑瘤的措施
➢ 采用低速或高速切削,由于切削速度是通过切
削温度影响积屑瘤的,以切削45钢为例,在低
速vc<3m/min和较高速度vc≥60m/min范围内,
摩擦系数都较小,故不易形成积屑瘤;
➢ 采用高润滑性的切削液,使摩擦和粘结减少; ➢ 适当减少进给量、增大刀具前角、减小切削变
材料受到刀具的作用以后,开始产生弹性变形;虽着 刀具继续切入,金属内部的应力、应变继续加大,当 达到材料的屈服点时,开始产生塑性变形,并使金属 晶格产生滑移;刀具再继续前进,应力进而达到材料 的断裂强度,便会产生挤裂。
(2)变形区的划分
大量的实验和理论分析证明,塑性金属切削过程中切屑 的形成过程就是切削层金属的变形过程。切削层的金属变形 大致划分为三个变形区:第一变形区(剪切滑移)、第二变 形区(纤维化)、第三变形区(纤维化与加工硬化)。
第Ⅰ变形区 近切削刃处切削 层内产生的塑性变形区;
第Ⅱ变形区 与前刀面接 触的切屑层内产生的变形区;
第Ⅲ变形区 近切削刃处已 加工表层内产生的变形区。
2.切屑的形成过程及切屑类型
(1)切屑的形成过程
1)切削变形的力学本质
切削金属形 成切屑的过程是一个 类似于金属材料受挤 压作用,产生塑性变 形进而产生剪切滑移 的变形过程 。
形成条件:用大前角的刀具、较高的切削速 度和较小的进给量切削塑性材料
优 点:切削过程平稳,切削力波动较小,已加工表面粗糙度较 小。 缺点:切屑连续不断,不太安全或可能擦伤已加工表面,因此 要采取断屑措施。
➢挤裂(节状)切屑
外形特征:刀屑接触面有裂纹,外 表面是锯齿形。
形成条件:采用较低的切削速度和 较大的进给量,刀具前 角较小,粗加工中等硬 度的钢材料
校核机床主轴、设计机床部件及计算 刀具强度等必不可少的参数。
总切削力在垂直于工作平面方向的分力,Fp不消耗功率。但容易使 工件变形,甚至可能产生振动,影响工件的加工精度。是进行加工 精度分析、计算工艺系统刚度以及分析工艺系统振动时,所必须的 参数。
进给力Fx (Ff)
总切削力在进给方向的分力,进给力也作功,但只 占总功的1%~5%。是设计、校核机床进给机构, 计算机床进给功率不可缺少的参数
实验表明,切屑的形成过程是被切削层金 属受到刀具前面的挤压作用,迫使其产生弹性 变形,当剪切应力达到金属材料屈服强度时, 产生塑性变形。随着刀具前刀面相对工件的继 续推挤,与切削刃接触的材料发生断裂而使切 削层材料变为切屑。
切屑的变形和形成过程实际上经历了弹性 变形、塑性变形、挤裂、切离四个阶段。
2) 变形系数ξ
➢切屑厚度hch与切削层的厚度hD之比称为厚度
变形系数,用ξh 表示,ξh = ach/ac ;
➢而切削层长度Lc与切屑长度Lch之比称为长度
变形系数,用ξl表示,ξl=Lc/Lch 。
➢变形系数越大,切屑越厚越短,切削变形越大。
(2)切屑的类型
➢带状切屑
外形特征:它的内表面是光滑的,外表面是 毛茸茸的。
3.积屑瘤的形成及其对切削过程的影响
(1)什么是积屑瘤
在一定速度范围下, 切削塑性金属材料形成 带状切屑时, 常在刀具 前刀面靠近切削刃的部 位粘结一些工件材料, 形成一块硬度很高的楔 块,称之为积屑瘤。
(2)积屑瘤的形成原因
当切屑沿刀具的前刀面流出时,在一定的温度与压力作 用下,与前刀面接触的切屑底层受到很大的摩擦阻力,致使 这一层金属的流出速度减慢,形成一层很薄的“滞流层”。 当前刀面对滞流层的摩擦阻力超过切屑材料的内部结合力时, 就会有一部分金属粘结或冷焊在切削刃附近,形成积屑瘤。
模块一 金属切削原理
课题二 金属切削过程的物理现象的认识
知识点
切削层的变形 切削力 切削热和切削温度
技能点 认识切屑的形成及其分类 认识切削力的来源及分解 认识切削热和切削温度形成及加工的影响
一.课题分析
在金属切削过程(cutting process)中,始终存在着 刀具切削工件和工件材料抵抗切削的矛盾,从而产生 一系列物理现象,如切削变形、切削力、切削热与切 削温度以及有关刀具的磨损与刀具寿命、卷屑与断屑 等。
研究、掌握并能灵活应用金属切削基本理论, 对有 效控制切削过程、保证加工精度和表面质量,提高切 削效率、降低生产成本,合理改进、设计刀具几何参 数,减轻工人的劳动强度等有重要的指导意义。
二.相关知识
(一) 金属切削过程的物理现象
1.切削层的变形
(1)概述 金属的切削过程与金属的挤压过程很相似。金属
(3)积屑瘤对起削过程的影响
❖积屑瘤的硬度比工件材料的硬度高,能代替切
削刃进行切削,起到保护切削刃的作用。
❖使实际前角增大,切削轻快。
因此,粗加工时可利用积屑瘤。
❖积屑瘤的顶端伸出切削刃之外,而且在不断
地产生和脱落,使切削层公称厚度不断变化, 影响尺寸精度。
❖此外,还会导致切削力的变化,引起振动, ❖并会有一些积屑瘤碎片粘附在工件已加工表