2014公司产能分析报告模板
xx公司产能分析报告(模板)
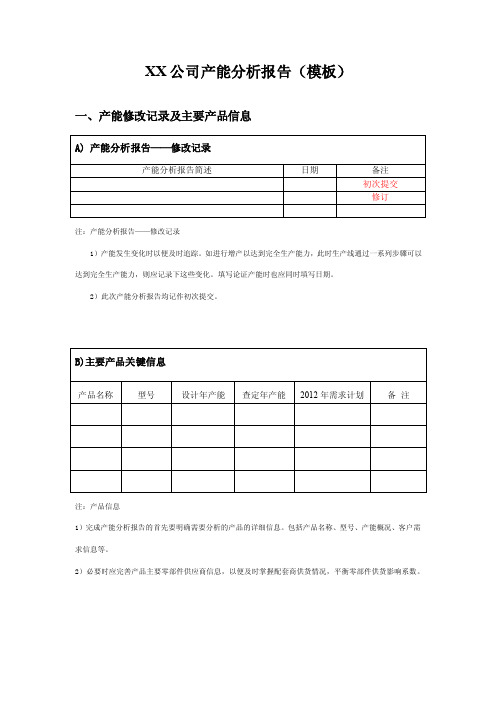
XX公司产能分析报告(模板)一、产能修改记录及主要产品信息注:产能分析报告——修改记录1)产能发生变化时以便及时追踪。
如进行增产以达到完全生产能力,此时生产线通过一系列步骤可以达到完全生产能力,则应记录下这些变化。
填写论证产能时也应同时填写日期。
2)此次产能分析报告均记作初次提交。
注:产品信息1)完成产能分析报告的首先要明确需要分析的产品的详细信息。
包括产品名称、型号、产能概况、客户需求信息等。
2)必要时应完善产品主要零部件供应商信息,以便及时掌握配套商供货情况,平衡零部件供货影响系数。
二、现有设备产能核算1、预订工作时间标准注:1)单班时间:每班总时间-每班的总计可用小时数。
2)班次:表示的是每天每个工艺操作的班次数。
3)作业率:(总工时-无效工时)/总工时。
人员休息-如果在人员休息的时候,机器也停止运转,则输入每班中机器不运转的时间长度。
计划的维修时间-这是计划的每班中机器停机用于维护的时间长度。
4)年出勤时间:年出勤天数-表示的是每年的工艺运作的天数(扣除法定节假日、双休日)。
5)计算举例:每班8小时、每天2班次、作业率80%、年出勤302天,净可用时间=8*2*80%*302=3865.6时。
2、代表产品制程/线能力计算注:1)代表产品:所谓代表产品指产品制程包含其他所有产品制造过程包含的所有工艺过程;如存在两种以上产品包含不同工艺过程、需分别取各类型产品代表产品制程并进行线能力分析。
2)评价瓶颈工序应排除可用外协、其他生产线可用设备借代等因素影响。
3)每条生产线选取一种或2种产品作为代表说明制程及瓶颈工序即可,其他产品可直接计算毛产能。
3、毛产能核算注:1)毛产能核算过程没有排除产品合格率、设备故障率、人员负荷等因素对产能的影响,不能作为需求平衡分析的依据,需进一步平衡。
2)其他产品可根据代表产品计算方法计算出出毛产能。
3、有效产能(净产能)注:1)设备生产包括机器检修、保养、待料等时间,实际的工作时间达不到计划工时,且生产的产品有不良品,因此有效产能必须是以毛产能为基础,减去因停机和良率以及人员缺口等综合因素所造成的产能损失。
公司产能分析报告

公司产能分析报告一、引言本报告旨在对公司的产能进行全面的分析,并提出合理的建议,以提高公司的产能水平,为公司的发展提供支持。
二、产能分析1.产能概况公司当前的产能为XXX,主要包括生产设备、人力资源和技术能力等。
在过去一段时间内,公司的产能基本稳定,公司的生产和经营状况良好。
2.生产设备分析公司的生产设备包括XXX,其中有部分设备已经投入使用多年,存在一定的老化情况。
这些老化设备可能导致生产效率的下降,应及时进行维护或更新。
3.人力资源分析公司的员工队伍规模适中,但是人力资源结构不够合理。
部分岗位上的员工可以通过培训或调整来提高工作效率。
同时,还需进一步完善员工的激励机制,提高员工的归属感和工作积极性。
4.技术能力分析公司的技术能力较为薄弱,导致产品的研发和创新能力不足。
应加大对技术研发的投入,提高公司的核心竞争力。
三、产能优化建议1.更新生产设备针对老化设备,应及时进行维护或更新,以提高生产效率和产品质量。
引入先进的生产设备和技术,提高生产自动化水平,降低人力成本,同时提高产品的稳定性和一致性。
2.优化人力资源通过员工的培训、激励和调动,提高员工的工作效率和工作满意度。
同时,加强对关键岗位的人才引进和培养,提高公司整体核心竞争力。
3.加强技术研发和创新加大对技术研发的投入,提高公司的技术能力和创新能力。
与科研机构合作,引入外部技术资源,提升产品的科技含量,增加产品的附加值。
4.提高生产效率通过优化生产流程、改进工艺和管理方式,提高生产效率。
合理规划和利用产能,优化生产计划,降低生产成本。
5.增加产能储备鉴于市场需求的波动性,建议增加产能储备,预留一定的生产能力,以应对突发市场需求波动或扩大市场规模的机会。
四、风险与挑战1.激烈的市场竞争可能导致产能利用率降低。
2.新的技术创新和产品设计可能对现有的产能构成威胁。
3.原材料价格波动可能对公司的产能造成不利影响。
五、总结公司的产能是公司发展的基础和保障,通过对产能进行全面的分析和优化,可以提高公司的生产效率和竞争力,为公司的长远发展打下良好的基础。
产能分析报告范文(两篇)

引言概述产能分析是企业生产经营过程中的重要环节,通过对企业现有产能的评估和分析,可以帮助企业优化生产管理,提高产能利用率,实现经济效益的最大化。
本文将以产能分析为主题,对企业的产能现状进行深入研究和分析。
正文内容1.大点一:产能概述1.1将产能定义为企业在一定时间、一定条件下能够达到的最大产量。
1.2产能包括实际生产能力和潜在生产能力两个方面。
1.3产能分析的目标是确定企业产能的合理水平,以满足市场需求,同时确保资源利用的高效性。
2.大点二:产能利用率分析2.1分析企业实际生产能力和实际产量的关系,计算产能利用率。
2.2产能利用率是评估企业生产效率的重要指标。
2.3通过对产能利用率的分析,可以发现生产过程中的瓶颈和障碍,以便采取相应的措施加以改善。
3.大点三:产能瓶颈分析3.1分析企业生产过程中的瓶颈环节,确定产能的瓶颈因素。
3.2产能瓶颈可能来自人力、设备、原材料等方面。
3.3通过产能瓶颈分析,可以找到优化产能的关键点,并提出解决方案以提高产能。
4.大点四:产能扩容方案4.1当企业的产能无法满足市场需求时,需要通过扩大产能来增加产量。
4.2产能扩容方案需要综合考虑市场需求、投资成本、技术条件等因素。
4.3可以通过增加设备、拓展生产线、优化生产流程等方式实现产能的扩容。
5.大点五:产能优化措施5.1产能优化是提高产能利用率和产能水平的重要手段。
5.2通过优化生产计划、提升设备效率、改善管理等方面,可以实现产能的优化。
5.3同时,还可以通过技术创新、流程改进等手段提高企业的核心竞争力和产能水平。
总结产能分析是企业管理中不可或缺的环节,通过对产能的评估和分析,可以为企业提供合理的产能水平和扩容方案。
通过优化产能利用率和实施产能优化措施,可以提升企业的生产效率和竞争力,实现经济效益的最大化。
在现代经济竞争激烈的环境下,不断优化产能是企业持续发展的关键因素。
因此,企业应高度重视产能管理,并不断提升自身的产能水平。
产能分析报告模板

一、封面报告名称:XX公司产能分析报告报告日期:____年__月__日编制部门:XX部门编制人:____二、目录1. 摘要2. 前言3. 产能分析基础数据4. 现有设备产能核算4.1 预订工作时间标准4.2 代表产品制程/线能力计算5. 产能瓶颈分析6. 产能提升策略7. 风险评估与应对措施8. 结论9. 附件三、摘要简要概述本次产能分析的目的、方法、主要发现和结论。
四、前言介绍公司背景、报告目的、分析范围和报告结构。
五、产能分析基础数据1. 公司概况2. 产品线信息3. 市场需求分析4. 竞争对手分析六、现有设备产能核算1. 预订工作时间标准- 单班时间/时- 班次/班- 作业率(%)- 年出勤天数/天- 净可用时间/时- 计算公式:净可用时间 = 单班时间× 班次× 作业率× 年出勤天数2. 代表产品制程/线能力计算- 产品年产能净可用时间(年)- 瓶颈工序总加工时间- 计算公式:年产能 = 产品年产能净可用时间÷ 瓶颈工序总加工时间七、产能瓶颈分析1. 瓶颈工序识别2. 瓶颈原因分析3. 瓶颈影响评估八、产能提升策略1. 提高设备利用率2. 优化生产流程3. 增加设备投入4. 人员培训与优化5. 技术创新与应用九、风险评估与应对措施1. 设备故障风险2. 人员流失风险3. 市场需求波动风险4. 应对措施十、结论总结本次产能分析的主要发现和结论,并提出改进建议。
十一、附件1. 产能分析数据表格2. 相关图表3. 产能提升方案请注意,以上模板仅供参考,具体内容需根据实际情况进行调整和完善。
产能分析报告模板及指标明细

产能分析报告模板及指标明细一、产能修改记录及主要产品信息注:产能分析报告——修改记录1)产能发生变化时以便及时追踪。
如进行增产以达到完全生产能力,此时生产线通过一系列步骤可以达到完全生产能力,则应记录下这些变化。
填写论证产能时也应同时填写日期。
2)此次产能分析报告均记作初次提交。
注:产品信息1)完成产能分析报告的首先要明确需要分析的产品的详细信息。
包括产品名称、型号、产能概况、客户需求信息等。
2)必要时应完善产品主要零部件供应商信息,以便及时掌握配套商供货情况,平衡零部件供货影响系数。
二、现有设备产能核算1、预订工作时间标准注:1)单班时间:每班总时间-每班的总计可用小时数。
2)班次:表示的是每天每个工艺操作的班次数。
3)作业率:(总工时-无效工时)/总工时。
人员休息-如果在人员休息的时候,机器也停止运转,则输入每班中机器不运转的时间长度。
计划的维修时间-这是计划的每班中机器停机用于维护的时间长度。
4)年出勤时间:年出勤天数-表示的是每年的工艺运作的天数(扣除法定节假日、双休日)。
5)计算举例:每班8小时、每天2班次、作业率80%、年出勤302天,净可用时间=8*2*80%*302=3865.6时。
2、代表产品制程/线能力计算注:1)代表产品:所谓代表产品指产品制程包含其他所有产品制造过程包含的所有工艺过程;如存在两种以上产品包含不同工艺过程、需分别取各类型产品代表产品制程并进行线能力分析。
2)评价瓶颈工序应排除可用外协、其他生产线可用设备借代等因素影响。
3)每条生产线选取一种或2种产品作为代表说明制程及瓶颈工序即可,其他产品可直接计算毛产能。
3、毛产能核算注:1)毛产能核算过程没有排除产品合格率、设备故障率、人员负荷等因素对产能的影响,不能作为需求平衡分析的依据,需进一步平衡。
2)其他产品可根据代表产品计算方法计算出出毛产能。
3、有效产能(净产能)注:1)设备生产包括机器检修、保养、待料等时间,实际的工作时间达不到计划工时,且生产的产品有不良品,因此有效产能必须是以毛产能为基础,减去因停机和良率以及人员缺口等综合因素所造成的产能损失。
产能分析报告模板与指标明细.doc

产能分析报告模板与指标明细.doc产能分析报告模板及指标明细一、产能修改记录及主要产品信息A)产能分析报告——修改记录产能分析报告简述日期备注初次提交修订注:产能分析报告——修改记录1)产能发生变化时以便及时追踪。
如进行增产以达到完全生产能力,此时生产线通过一系列步骤可以达到完全生产能力,则应记录下这些变化。
填写论证产能时也应同时填写日期。
2)此次产能分析报告均记作初次提交。
B)主要产品关键信息产品名称型号设计年产能查定年产能2012 年需求计划备注注:产品信息1)完成产能分析报告的首先要明确需要分析的产品的详细信息。
包括产品名称、型号、产能概况、客户需求信息等。
2)必要时应完善产品主要零部件供应商信息,以便及时掌握配套商供货情况,平衡零部件供货影响系数。
二、现有设备产能核算1、预订工作时间标准A)计划工时计算公式:净可用工时e=a*b*c*d说明a单班时间 / 时8根据自身工时计划安排填写b班次 /班2根据自身工时计划安排填写c作业率( % )80根据自身工时计划安排填写d年出勤天数/ 天302根据自身工时计划安排填写e净可用时间/ 时注:1)单班时间:每班总时间- 每班的总计可用小时数。
2)班次:表示的是每天每个工艺操作的班次数。
3)作业率:(总工时- 无效工时)/ 总工时。
人员休息- 如果在人员休息的时候,机器也停止运转,则输入每班中机器不运转的时间长度。
计划的维修时间- 这是计划的每班中机器停机用于维护的时间长度。
4)年出勤时间:年出勤天数- 表示的是每年的工艺运作的天数(扣除法定节假日、双休日)。
5)计算举例:每班8 小时、每天 2 班次、作业率80% 、年出勤302 天,净可用时间=8*2*80%*302=3865.6 时。
产能分析统计报告模板
产能分析统计报告模板产能分析统计报告模板1. 介绍在本报告中,我们对公司的产能进行了统计和分析。
产能是指企业在一定的资源投入和工作时间下,能够生产的最大产品数量或提供的最大服务规模。
产能分析可以帮助企业了解其目前的产能情况,找出潜在的瓶颈,并制定相应的解决方案,以提高产能和效益。
2. 数据统计我们对公司过去一年的产能进行了详细的统计和分析。
根据统计数据,公司的总产能为X个产品/服务每年。
其中,产品/服务A的产能为X个/年,占总产能的XX%;产品/服务B的产能为X个/年,占总产能的XX%;产品/服务C的产能为X个/年,占总产能的XX%;其他产品/服务的产能为X个/年,占总产能的XX%。
3. 产能利用率分析在进行产能分析时,我们还对公司的产能利用率进行了评估。
产能利用率是指实际产出与产能之间的比率,即企业利用自身产能生产产品或提供服务的效率。
根据统计数据,公司的产能利用率为XX%。
其中,产品/服务A的产能利用率为XX%;产品/服务B的产能利用率为XX%;产品/服务C的产能利用率为XX%;其他产品/服务的产能利用率为XX%。
4. 瓶颈分析通过对产能数据的统计和分析,我们发现了一些潜在的瓶颈问题。
首先,产品/服务A的产能利用率较低,说明存在生产能力不足的情况。
其次,产品/服务B的产能利用率也较低,可能是由于生产流程不够高效或人力资源不足。
此外,产品/服务C的产能利用率较高,但存在质量问题,需要加强品质管理。
5. 解决方案针对上述瓶颈问题,我们提出以下解决方案。
对于产品/服务A,公司可以增加设备和人力资源,以提高生产能力。
对于产品/服务B,公司应优化生产流程,提高生产效率,并适当增加人力资源。
对于产品/服务C,公司应加强品质管理,确保产品/服务的质量稳定和提高客户满意度。
6. 结论综上所述,通过对公司产能的统计和分析,我们发现了一些潜在的瓶颈问题,并提出了相应的解决方案。
希望这些分析和建议可以帮助公司提高产能和效益,实现可持续发展。
产能分析报告范文(一)
产能分析报告范文(一)引言概述:本文将对公司X的产能情况进行分析,以评估公司的生产能力及潜在的扩张空间。
通过对公司当前的产能状况、产能利用率、产能瓶颈等方面进行详细分析,旨在为公司提供有关产能优化和扩大生产规模的建议。
正文内容:一、当前产能状况1. 公司X目前的年产量2. 厂房和设备的利用率3. 人力资源的配置和使用情况4. 产能规模与市场需求的匹配程度5. 公司X在产能方面面临的挑战和机遇二、产能利用率分析1. 产能利用率的计算方法和指标2. 公司X的产能利用率情况3. 产能利用率低的原因分析4. 产能利用率提升的潜在措施5. 高产能利用率对公司X的益处和影响三、产能瓶颈分析1. 产能瓶颈的定义和常见类型2. 公司X是否存在产能瓶颈3. 产能瓶颈对公司生产效率和成本的影响4. 产能瓶颈的解决策略和实施方案5. 解决瓶颈问题对公司X的长期发展意义四、产能优化建议1. 优化生产流程和工艺2. 产品标准化和模块化设计3. 引入新技术和设备4. 供应链管理和协调5. 人力资源调整和培训计划五、扩大生产规模的可行性分析1. 市场需求预测和行业趋势分析2. 竞争对手的产能情况与扩张计划3. 扩大生产规模的投资成本和回报分析4. 可行性研究和风险评估5. 扩大生产规模的建议和预期效果总结:通过对公司X的产能进行分析,我们得出了以下结论:公司当前的产能利用率较低,存在一定程度的产能瓶颈。
为了提高产能利用率和解决瓶颈问题,我们建议公司采取一系列的措施,如优化生产流程、引入新技术和设备、进行供应链管理和人力资源调整等。
此外,公司应该进行可行性分析,评估扩大生产规模的可行性,并考虑投资成本和回报情况。
通过实施这些措施,公司X将能够提高产能和生产效率,为未来的扩张奠定基础。
产能分析报告模板及指标明细
产能分析报告模板及指标明细一、产能修改记录及主要产品信息注:产能分析报告--- 修改记录1)产能发生变化时以便及时追踪。
如进行增产以达到完全生产能力,此时生产线通过一系列步骤可以达到完全生产能力,则应记录下这些变化。
填写论证产能时也应同时填写日期。
2)此次产能分析报告均记作初次提交。
注:产品信息1)完成产能分析报告的首先要明确需要分析的产品的详细信息。
包括产品名称、型号、产能概况、客户需求信息等。
2)必要时应完善产品主要零部件供应商信息,以便及时掌握配套商供货情况,平衡零部件供货影响系数。
二、现有设备产能核算1、预订工作时间标准注:1)单班时间:每班总时间-每班的总计可用小时数。
2)班次:表示的是每天每个工艺操作的班次数。
3)作业率:(总工时-无效工时)/总工时。
人员休息-如果在人员休息的时候,机器也停止运转,则输入每班中机器不运转的时间长度。
计划的维修时间-这是计划的每班中机器停机用于维护的时间长度。
4)年岀勤时间:年岀勤天数-表示的是每年的工艺运作的天数(扣除法定节假日、双休日)。
5)计算举例:每班8小时、每天2班次、作业率80% 年出勤302天,净可用时间=8*2*80%*302=3865.6时。
2、代表产品制程/线能力计算生产线瓶颈工序设备产能描述:1 )瓶颈工序、设备产能2)其他注:1)代表产品:所谓代表产品指产品制程包含其他所有产品制造过程包含的所有工艺过程;如存在两种以上产品包含不同工艺过程、需分别取各类型产品代表产品制程并进行线能力分析。
2)评价瓶颈工序应排除可用外协、其他生产线可用设备借代等因素影响。
3)每条生产线选取一种或2种产品作为代表说明制程及瓶颈工序即可,其他产品可直接计算毛产能。
3、毛产能核算1)毛产能核算过程没有排除产品合格率、设备故障率、人员负荷等因素对产能的影响,不能作为需求平衡分析的依据,需进一步平衡。
2)其他产品可根据代表产品计算方法计算岀岀毛产能。
3、有效产能(净产能)1)设备生产包括机器检修、保养、待料等时间,实际的工作时间达不到计划工时,且生产的产品有不良品,因此有效产能必须是以毛产能为基础,减去因停机和良率以及人员缺口等综合因素所造成的产能损失。
公司产能分析报告模板
告报析分踪跟能产.一、现有设备产能核算1、预订工作时间标准注:)单班时间:1)计划工时A-每班总时间每班的总计可 e=a*b*c*d说明计算公式:净可用工时用小时数。
表示)班次:2根据自身工时计划安排填写8 a 单班时间/时的是每天每个工艺操作的b根据自身工时计划安排填2班次次数根据自身工时计划安排填c80作业率)(总)作业率:3无效工工时根据自身工时计划安排填d302年出勤天/ /总工时。
时如人员休息净可用时e果在人员休息的时候,机器也停止运转,则输入每班中机器不运转的时间长度。
这是计划的每班中机器停机用于维护的时间长度。
-计划的维修时间表示的是每年的工艺运作的天数(扣除法定节假日、双休日)。
4)年出勤时间:年出勤天数- 时。
净可用时间=8*2*80%*302=3865.62班次、作业率80%、年出勤302天,5)计算举例:每班8小时、每天线能力计算2、代表产品制程/注:=产品年产能瓶颈工序总加工时间净可用时间(年)/)代表产1品:所谓代人员日加工总加工辅助工时加工工时设备工序设备设备表产品指产备注配置min/ 名称名称编号台数件 min/件时间能力品制程包含其他所有产品制造过程包含的所有工艺过程;如存在两种以上产品包生产线瓶颈工序设备产能描述:含不同工艺)其他1)瓶颈工序、设备产能,2过程、需分别取各类型产品代表产品制程并进行线能力分析。
)评价瓶颈工序应排除可用外协、其他生产线可用设备借代等因素影响。
2 种产品作为代表说明制程及瓶颈工序即可,其他产品可直接计算毛产能。
)每条生产线选取一种或23 3、毛产能核算产品年度毛产能= 产品定额系数代表产品/产品系产品名工时定产品定额系注备实际产能所占比例线产能数额称列.注毛产能核)1算过程没有排除产品格率、设备故障率、人员负荷等因素对产能的影响,不能作为需求平衡分析的依据,需进一步平衡。
)其他产品可根据代表产品计算方法计算出出毛产能。
2、有注:)设备生产包括机器检修、保养、待料等时间,实际的工作时间达不到计划工时,且生产的产品有不良品,因此有效产1 能必须是以毛产能为基础,减去因停机和良率以及人员缺口等综合因素所造成的产能损失。
- 1、下载文档前请自行甄别文档内容的完整性,平台不提供额外的编辑、内容补充、找答案等附加服务。
- 2、"仅部分预览"的文档,不可在线预览部分如存在完整性等问题,可反馈申请退款(可完整预览的文档不适用该条件!)。
- 3、如文档侵犯您的权益,请联系客服反馈,我们会尽快为您处理(人工客服工作时间:9:00-18:30)。
2014公司产能分析报告模板一、产能修改记录及主要产品信息注:产能分析报告——修改记录1)产能发生变化时以便及时追踪。
如进行增产以达到完全生产能力,此时生产线通过一系列步骤可以达到完全生产能力,则应记录下这些变化。
填写论证产能时也应同时填写日期。
2)此次产能分析报告均记作初次提交。
注:产品信息1)完成产能分析报告的首先要明确需要分析的产品的详细信息。
包括产品名称、型号、产能概况、客户需求信息等。
2)必要时应完善产品主要零部件供应商信息,以便及时掌握配套商供货情况,平衡零部件供货影响系数。
二、现有设备产能核算1、预订工作时间标准注:1)单班时间:每班总时间-每班的总计可用小时数。
2)班次:表示的是每天每个工艺操作的班次数。
3)作业率:(总工时-无效工时)/总工时。
人员休息-如果在人员休息的时候,机器也停止运转,则输入每班中机器不运转的时间长度。
计划的维修时间-这是计划的每班中机器停机用于维护的时间长度。
4)年出勤时间:年出勤天数-表示的是每年的工艺运作的天数(扣除法定节假日、双休日)。
5)计算举例:每班8小时、每天2班次、作业率80%、年出勤302天,净可用时间=8*2*80%*302=3865.6时。
2、代表产品制程/线能力计算注:1)代表产品:所谓代表产品指产品制程包含其他所有产品制造过程包含的所有工艺过程;如存在两种以上产品包含不同工艺过程、需分别取各类型产品代表产品制程并进行线能力分析。
2)评价瓶颈工序应排除可用外协、其他生产线可用设备借代等因素影响。
3)每条生产线选取一种或2种产品作为代表说明制程及瓶颈工序即可,其他产品可直接计算毛产能。
3、毛产能核算注:1)毛产能核算过程没有排除产品合格率、设备故障率、人员负荷等因素对产能的影响,不能作为需求平衡分析的依据,需进一步平衡。
2)其他产品可根据代表产品计算方法计算出出毛产能。
3、有效产能(净产能)注:1)设备生产包括机器检修、保养、待料等时间,实际的工作时间达不到计划工时,且生产的产品有不良品,因此有效产能必须是以毛产能为基础,减去因停机和良率以及人员缺口等综合因素所造成的产能损失。
2)总体设备利用率计算公式:OEE=设备可用性*性能效率*产品合格率。
根据来自生产验证运转的历史数据来计算总体设备利用率的(OEE)。
性能效率的计算是通过计划的所需周期时间来的。
如果计算单元显示的是100%或者更高,则该单元用红色进行强调。
3)人员负荷率=(现有生产人员/人员配置)*100%反映了以设备为依据的人员配备情况,这一指标在短期内直接对净产能产生影响。
注释OEE=可用率X 表现性 X质量指数。
其中:可用率=操作时间 / 计划工作时间它是用来考虑停工所带来的损失,包括引起计划生产发生停工的任何事件,例如设备故障,原料短缺以及生产方法的改变等。
表现性=(总产量/操作时间)/理想周期时间=(总产量 / 操作时间)*生产速率表现性考虑生产速度上的损失。
包括任何导致生产不能以最大速度运行的因素,例如设备的磨损,材料的不合格以及操作人员的失误等。
质量指数=良品/总产量质量指数考虑质量的损失,它用来反映没有满足质量要求的产品(包括返工的产品)。
利用OEE的一个最重要目的就是减少一般制造业所存在的六大损失:停机损失、换装调试损失、暂停机损失、减速损失、启动过程次品损失和生产正常运行时产生的次品损失。
下面表格是六大损失的说明及其与OEE 的关系:六大损失类别 OEE损失类别事件原因注释停机损失有效率刀具损坏设备突发故障原料短缺等表示设备因为一些大的故障,或者突发事件所引起的停工。
换装调试损失有效率改变工具设备预热等因改换工具,生产线调试等准备工作而造成的损失,一般位于工位安排,生产布置这一阶段暂停机损失表现性不通畅的生产流导轨阻塞清洁,检查一般指停工5分钟以下,并不需要维护人员介入的停工减速损失表现性低于设计产能运行设备磨损员工技术因素等任何阻止设备达到设计产能的因素启动过程次品损失质量指数报废、重工等设备预热,调节等生产正式运行之前产生的次品生产过程次品损失质量指数报废、重工等生产稳定进行时产生的次品表一六大损失与OEE的关系编辑本段OEE计算实例我们举一个例子来说明OEE的计算方法:设某设备某天工作时间为8h, 班前计划停机15min, 故障停机30min,设备调整25min, 产品的理论加工周期为0.6 min/件, 一天共加工产品450件, 有20件废品, 求这台设备的OEE。
根据上面可知:计划运行时间=8x60-15=465 (min)实际运行时间=465-30-25=410 (min)有效率=410/465=0.881(88.1%)生产总量=450(件)理想速度x实际运行时间=1/0.6 x 410=683表现性=450/683=0.658(65.8%)(另外解法:表现性=理想加工周期*生产数量/实际运行时间=0.6*450/410=0.658(65.8%))质量指数=(450—20)/450=0.955(95.5%)OEE=有效率x表现性x质量指数=55.4%另一种OEE算法:OEE=符合质量要求的产品/最大理论产量此例中最大理论产量=(8*60-15)/0.6件=775件符合质量要求产品=450-20=430件OEE=430/775*100%=55.4%OEE的作用实践证明OEE是一个极好的基准工具,通过OEE模型的各子项分析,它准确清楚地告诉你设备效率如何,在生产的哪个环节有多少损失,以及你可以进行那些改善工作。
长期的使用OEE工具,企业可以轻松的找到影响生产效率的瓶颈,并进行改进和跟踪。
达到提高生产效率的目的,同时使公司避免不必要的耗费。
编辑本段OEE数据采集方法OEE的计算虽然简单,但是,在实际的应用中,当与班次,员工,设备,产品等生产要素联系在一起时,便变得十分复杂,利用人工采集数据计算OEE显得麻烦费事,为了更有效的利用OEE这个工具,OEE数据采集信息化越来越成为人们关心的话题,OEE Toolkit 是世界上最优秀的OEE系统,它具有自动化数据采集模块,可以轻松地获取有关设备的生产信息,为OEE 提供最有价值的数据,同时,该系统也可以生成实时的生产信息报告,包括故障停工,在制品信息和OEE等。
通过这些有价值的数据,企业的管理工作无疑会变得轻松而简单。
该系统已在世界上许多著名公司得到广泛的应用,例如波音飞机,通用电气,阿斯利康,道达尔石油等。
编辑本段OEE计算实例设某设备某天工作时间为8H,班前计划停机10MIN,故障停机30MIN,设备调整35MIN,产品的理论加工周期为1min/件,一天共加工产品400件,有20件废品,求这台设备的OEE。
根据上面可知:计划运行时间=8*60-10=470(min)实际运行时间=470-30-35=405(min)有效率=405/470=0.86(86%)表现性=400/405=0.98(98%) 质量指数=(400-20)/400=0.95(95%) OEE=有效率*表现性*质量指数=80% 在上表中,我们只列举了一些事件原因,在实际应用中它可能包括与生产有关的任何原因。
OEE能准确地告诉你设备效率如何,在生产的哪个环节有多少损失,以及你可以进行哪些改善工作。
长期的使用OEE工具,企业可以轻松的找到影响生产效率的瓶颈,并进行改进和跟踪,以达到提高生产效率的目的。
编辑本段设备综合效率(OEE)* 什么是OEE* 认识OEE的三个构成因素:可用水平,运行水平,质量水平* OEE计算要素与实例:根据设备维护的历史数据,选定单元,计算OEE* OEE 的计算与意义的解释* 如何改善OEE:评价目前的OEE水平,提出改进目标* 如何建立基于OEE的设备管理监控编辑本段OEE的实质如果追究OEE的本质内涵,其实就是计算周期内用于加工的理论时间和负荷时间的百分比。
请注意,当展开OEE公式,有OEE = 时间开动率×性能开动率×合格品率=(开动时间/负荷时间)×[加工数量/(开动时间/理论加工周期)]×(合格产量/加工数量)=(开动时间×加工数量×理论加工周期×合格产量) /(负荷时间×开动时间×加工数量)约去分子、分母的公因子,OEE = (理论加工周期×合格产量)/负荷时间 = 合格产品的理论加工总时间/负荷时间这也就是实际产量与负荷时间内理论产量的比值。
三个环节的管理重点:时间开动率:重点管理设备故障时间和调整时间,即减少设备故障时间、产品切换时间。
性能开动率:重点管理单件生产时间,即,减少单件生产时间。
合格频率:重点管理成品率,提高制程控制能力,减少不良品的发生。
三、产能需求平衡/预警机制1、产能负荷率计算注:1)产能负荷率反映了企业中长期、短期需求计划对目前净产能比值的柔性指标,其作为产能预警的基础数据,对产能提升计划起指导性作用。
2)当负荷率反映3个月以内需求产能状态时,初步方案采取短期产能提升计划; 3-6月以上,采取中长期产能提升计划;超过6个月以上,采取长期产能提升计划。
2)预警设置采取红黄蓝三色,具体设置见(三、2)产能预警。
2、产能预警注:产能负荷率:产品/生产线净产能 需求计划产能负荷率预警设置 初步方案 >1 红 中长期扩能>1黄短期扩能 =1 蓝短期扩能/不需扩能<1 蓝 不需扩能净产能需求计划产能负荷率1)坐标轴纵轴表示产能,横轴为时间进度,两条黑色虚线分别表示长期扩能预警、短期扩能预警,红色实线为需求线(变化情况可参照历史数据)。
2)当需求线在短期扩能预警线以下时显示为蓝色椭圆。
不设预警,不需扩能;当需求线在短期扩能预警线与长期扩能预警线之间时,设置黄色预警,采取短期产能提升计划;当红色需求线超过长期扩能预警线,并长时间处于短期最大可获得差能之上,采取红色预警,并策划中长期扩能计划。
四、需求平衡/产能提升策略1、约束产能的解决对策通过设置产能预警线,提前对可能产生约束的时间点提出产能扩充的对策建议,并针对各类扩充对策预留实施提前期。
2、超过短期预警线的解决对策:可以在标准产能的基础上快速扩充,并在1个月内投入使用,内容概括为(括号内为准备周期):1)人力资源:A)增加班次,采取两班制或三班制(1小时-1星期)B)加班,适当延长工作时间(1小时-1星期)C)内部支援,其他线暂时借调(1小时-1星期)D)借用外协员工(培训期在1个月内);2)增大外协量、外包量(增大现有的计划外协比例,1星期-2星期);3)设备资源:内部调配或快速购买(<1个月);机器增加开机的台数、开机时间(<1个月)。
4)场地资源:内部调配(<1个月)等.3、超过长期产能预警线的解决对策:无法在现有资源基础上扩充达到,需要新增设备、人员,通常这种产能扩充需要一个月或更长的准备周期。