锅炉温度自动控制
锅炉温度PID控制系统设计
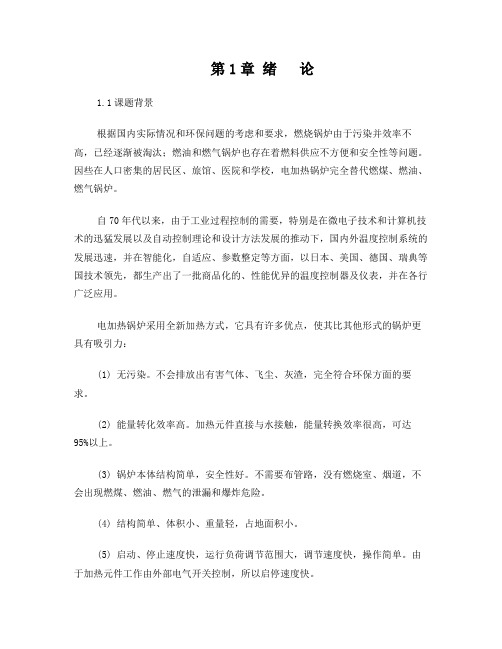
第1章绪论1.1课题背景根据国内实际情况和环保问题的考虑和要求,燃烧锅炉由于污染并效率不高,已经逐渐被淘汰;燃油和燃气锅炉也存在着燃料供应不方便和安全性等问题。
因些在人口密集的居民区、旅馆、医院和学校,电加热锅炉完全替代燃煤、燃油、燃气锅炉。
自70年代以来,由于工业过程控制的需要,特别是在微电子技术和计算机技术的迅猛发展以及自动控制理论和设计方法发展的推动下,国内外温度控制系统的发展迅速,并在智能化,自适应、参数整定等方面,以日本、美国、德国、瑞典等国技术领先,都生产出了一批商品化的、性能优异的温度控制器及仪表,并在各行广泛应用。
电加热锅炉采用全新加热方式,它具有许多优点,使其比其他形式的锅炉更具有吸引力:(1) 无污染。
不会排放出有害气体、飞尘、灰渣,完全符合环保方面的要求。
(2) 能量转化效率高。
加热元件直接与水接触,能量转换效率很高,可达95%以上。
(3) 锅炉本体结构简单,安全性好。
不需要布管路,没有燃烧室、烟道,不会出现燃煤、燃油、燃气的泄漏和爆炸危险。
(4) 结构简单、体积小、重量轻,占地面积小。
(5) 启动、停止速度快,运行负荷调节范围大,调节速度快,操作简单。
由于加热元件工作由外部电气开关控制,所以启停速度快。
(6) 可采用计算机监控,完全实现自动化。
其温度的控制都能通过微控制芯片完成,使锅炉的运行完全实现自动化,最大程度地将控制器应用于传统的锅炉行业。
本课题主要研究锅炉温度的过程控制。
新型锅炉是机电一体化的产品,可将电能直接转化成热能,具有效率高,体积小,无污染,运行安全可靠,供热稳定,自动化程度高的优点,是理想的节能环保的供暖设备。
加上目前人们的环保意识的提高,电热锅炉越来越受人们的重视,在工业生产和民用生活用水中应用越来越普及。
电热锅炉目前主要用于供暖和提供生活用水。
主要是控制水的温度,保证恒温供水。
随着计算机和信息技术的高速发展,单片机广泛的应用于工业控制中。
工业控制也越来越多的采用计算机控制,在这里我们采用51系列单片机来做控制器。
PLC在锅炉控制系统中的作用

PLC在锅炉控制系统中的作用锅炉是工业生产中常用的热力设备,它负责将水或其他流体加热到所需温度,以满足生产过程中的热能需求。
为了保证锅炉能够高效、稳定地运行,控制系统的作用至关重要。
其中,可编程逻辑控制器(PLC)在锅炉控制系统中扮演着重要的角色。
一、PLC简介PLC是一种专门用于工业控制的计算机设备,它能够根据预先编写好的程序,对锅炉的各个部分进行自动控制。
PLC通常由CPU、输入输出模块和通信模块等组成,具备可编程、可扩展、可靠性高等特点。
二、PLC在锅炉控制系统中的应用1. 温度控制在锅炉中,温度控制是至关重要的,它直接影响锅炉的稳定性和效率。
PLC可以通过外部温度传感器获取实时温度数据,并对锅炉的加热器、循环泵等设备进行控制,以确保锅炉水温始终保持在设定范围内。
2. 压力控制锅炉的压力也是需要进行精确控制的参数之一。
过低的压力可能导致供热不足,过高的压力则可能引发爆炸等安全隐患。
PLC可以通过传感器实时监测锅炉的压力,并根据设定值自动调节燃烧器的工作状态,以保证锅炉的压力在安全范围内。
3. 水位控制锅炉的水位是影响锅炉正常运行的重要因素。
若水位过低,锅炉的加热管壁可能过热而损坏;若水位过高,又可能导致锅炉溢水。
PLC可以通过水位传感器监测锅炉的实时水位,并控制进水和排水设备的开关,以保持水位在安全范围内。
4. 烟气排放控制锅炉燃烧过程中会产生大量烟尘和有害气体,对环境造成污染。
PLC可以通过烟气传感器监测烟气的成分和排放浓度,并根据环保要求调整燃烧器的工作状态,以减少污染物的排放。
5. 故障诊断与报警锅炉系统中可能会出现各种故障,如传感器失效、设备故障等。
PLC可以通过自动检测和诊断系统中的故障,并根据设定的规则进行报警。
这样可以帮助运维人员及时发现和解决问题,保证锅炉的正常运行。
三、PLC在锅炉控制系统中的优势1. 稳定性高:PLC具备高性能的计算能力和稳定的特性,可以保证对锅炉各个参数的精确控制,提高系统的稳定性。
工业锅炉温控器的原理
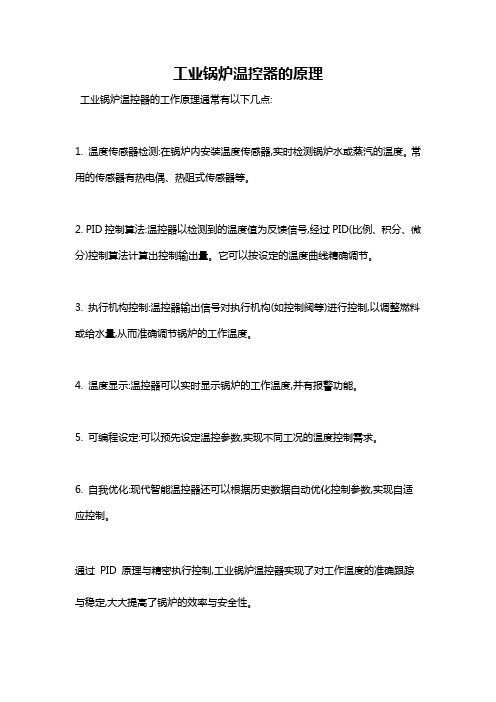
工业锅炉温控器的原理
工业锅炉温控器的工作原理通常有以下几点:
1. 温度传感器检测:在锅炉内安装温度传感器,实时检测锅炉水或蒸汽的温度。
常用的传感器有热电偶、热阻式传感器等。
2. PID控制算法:温控器以检测到的温度值为反馈信号,经过PID(比例、积分、微分)控制算法计算出控制输出量。
它可以按设定的温度曲线精确调节。
3. 执行机构控制:温控器输出信号对执行机构(如控制阀等)进行控制,以调整燃料或给水量,从而准确调节锅炉的工作温度。
4. 温度显示:温控器可以实时显示锅炉的工作温度,并有报警功能。
5. 可编程设定:可以预先设定温控参数,实现不同工况的温度控制需求。
6. 自我优化:现代智能温控器还可以根据历史数据自动优化控制参数,实现自适应控制。
通过PID 原理与精密执行控制,工业锅炉温控器实现了对工作温度的准确跟踪与稳定,大大提高了锅炉的效率与安全性。
智能电锅炉操作方法
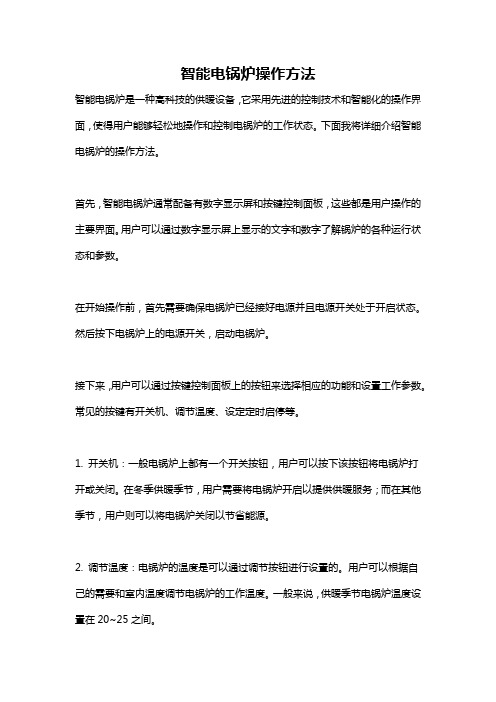
智能电锅炉操作方法智能电锅炉是一种高科技的供暖设备,它采用先进的控制技术和智能化的操作界面,使得用户能够轻松地操作和控制电锅炉的工作状态。
下面我将详细介绍智能电锅炉的操作方法。
首先,智能电锅炉通常配备有数字显示屏和按键控制面板,这些都是用户操作的主要界面。
用户可以通过数字显示屏上显示的文字和数字了解锅炉的各种运行状态和参数。
在开始操作前,首先需要确保电锅炉已经接好电源并且电源开关处于开启状态。
然后按下电锅炉上的电源开关,启动电锅炉。
接下来,用户可以通过按键控制面板上的按钮来选择相应的功能和设置工作参数。
常见的按键有开关机、调节温度、设定定时启停等。
1. 开关机:一般电锅炉上都有一个开关按钮,用户可以按下该按钮将电锅炉打开或关闭。
在冬季供暖季节,用户需要将电锅炉开启以提供供暖服务;而在其他季节,用户则可以将电锅炉关闭以节省能源。
2. 调节温度:电锅炉的温度是可以通过调节按钮进行设置的。
用户可以根据自己的需要和室内温度调节电锅炉的工作温度。
一般来说,供暖季节电锅炉温度设置在20~25之间。
3. 设定定时启停:智能电锅炉上通常还有定时启停的功能。
用户可以通过按键面板上的定时按钮来设置电锅炉的启动和停止时间。
比如,用户可以设置电锅炉在早晨6点自动启动供暖,在晚上10点自动停止供暖。
此外,智能电锅炉还具有一些智能化的功能,使得用户能够更加方便和舒适地使用电锅炉。
1. 自动调温:智能电锅炉可以根据室内温度和用户设定的温度来自动调节加热功率,以保持室内温度在设定范围内。
当室内温度过低时,电锅炉会启动加热功能;而当室内温度达到设定温度时,电锅炉会自动停止加热。
2. 温度记忆:智能电锅炉通常还具有温度记忆功能,即使在断电后重新启动,电锅炉仍能自动恢复到之前的工作状态。
这样可以避免用户重复设置温度,方便用户的使用。
3. 故障自检:当智能电锅炉出现故障时,它通常会自动进行故障自检,并通过数字显示屏上的文字和数字来显示故障代码。
家用锅炉温控器的使用方法
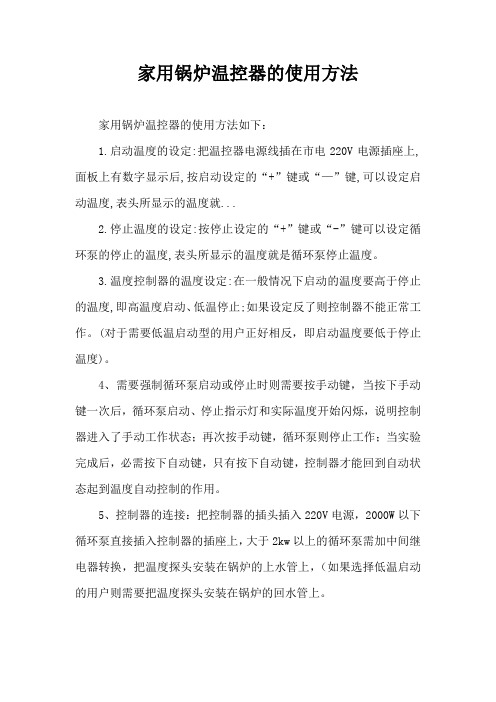
家用锅炉温控器的使用方法
家用锅炉温控器的使用方法如下:
1.启动温度的设定:把温控器电源线插在市电220V电源插座上,面板上有数字显示后,按启动设定的“+”键或“—”键,可以设定启动温度,表头所显示的温度就...
2.停止温度的设定:按停止设定的“+”键或“-”键可以设定循环泵的停止的温度,表头所显示的温度就是循环泵停止温度。
3.温度控制器的温度设定:在一般情况下启动的温度要高于停止的温度,即高温度启动、低温停止;如果设定反了则控制器不能正常工作。
(对于需要低温启动型的用户正好相反,即启动温度要低于停止温度)。
4、需要强制循环泵启动或停止时则需要按手动键,当按下手动键一次后,循环泵启动、停止指示灯和实际温度开始闪烁,说明控制器进入了手动工作状态;再次按手动键,循环泵则停止工作;当实验完成后,必需按下自动键,只有按下自动键,控制器才能回到自动状态起到温度自动控制的作用。
5、控制器的连接:把控制器的插头插入220V电源,2000W以下循环泵直接插入控制器的插座上,大于2kw以上的循环泵需加中间继电器转换,把温度探头安装在锅炉的上水管上,(如果选择低温启动的用户则需要把温度探头安装在锅炉的回水管上。
工业锅炉温度控制系统设计与实现

五、结论
本次演示对工业锅炉温度控制系统的设计与实现进行了详细的阐述。通过合理 地设计硬件和软件架构,以及精心的现场实施,我们成功地构建了一个高效、 稳定、安全的温度控制系统。该系统可以显著提高工业锅炉的温度控制精度和 生产效率,同时降低了能源消耗和安全隐患,为工业生产带来了积极的影响。
参考内容
5、适应性广:能够适应不同的锅炉型号和工作环境。
三、系统设计
基于以上的需求分析,我们设计出以下的温度控制系统:
1、硬件部分:采用以微处理器为核心的控制器,搭配热电偶、变送器等传感 器设备,以及电动调节阀等执行器设备。微处理器可以根据传感器采集的温度 数据,通过PID(比例-积分-微分)算法计算出调节量,控制执行器动作,以 实现对锅炉温度的精确控制。
参考内容二
摘要:
本次演示介绍了一种基于PLC(可编程逻辑控制器)的车载锅炉温度自动控制 系统,该系统的设计与实现旨在提高车载锅炉的温度控制精度和节能性能。通 过采用PLC控制器、传感器模块和显示模块等组件,实现了对车载锅炉温度的 实时监测与控制,并取得了良好的实验结果。本次演示的研究成果对于优化车 载锅炉温度控制具有一定的实用价值。
引言:
车载锅炉作为一种重要的能源设备,广泛应用于各种工业领域。然而,传统的 手动控制方式存在一定的局限性,如控制精度不高、节能性能不佳等。因此, 研究一种基于PLC的车载锅炉温度自动控制系统具有重要的现实意义。本次演 示旨在设计并实现一种具有高精度、节能性能优异的温度自动控制系统,从而 提高车载锅炉的整体运行性能。
5、通信功能:系统应具备与上位机或其它设备进行数据通信的功能,实现数 据的远程监控和管理。
四、系统实现
在系统实现阶段,我们需要完成以下几个步骤:
1、硬件选型和搭建:根据系统设计的要求,选择合适的微处理器、传感器、 执行器等硬件设备,并进行搭建。
火电厂锅炉自动化控制系统设计
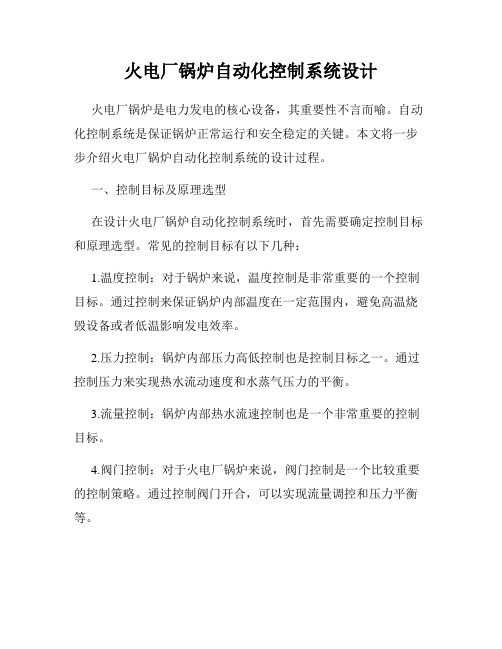
火电厂锅炉自动化控制系统设计火电厂锅炉是电力发电的核心设备,其重要性不言而喻。
自动化控制系统是保证锅炉正常运行和安全稳定的关键。
本文将一步步介绍火电厂锅炉自动化控制系统的设计过程。
一、控制目标及原理选型在设计火电厂锅炉自动化控制系统时,首先需要确定控制目标和原理选型。
常见的控制目标有以下几种:1.温度控制:对于锅炉来说,温度控制是非常重要的一个控制目标。
通过控制来保证锅炉内部温度在一定范围内,避免高温烧毁设备或者低温影响发电效率。
2.压力控制:锅炉内部压力高低控制也是控制目标之一。
通过控制压力来实现热水流动速度和水蒸气压力的平衡。
3.流量控制:锅炉内部热水流速控制也是一个非常重要的控制目标。
4.阀门控制:对于火电厂锅炉来说,阀门控制是一个比较重要的控制策略。
通过控制阀门开合,可以实现流量调控和压力平衡等。
在选择控制原理时,需要考虑控制系统的响应速度,稳态精度,以及设备成本。
常见的控制原理有PID控制器、模糊控制器、神经网络控制器等。
二、运行状态识别在设计火电厂锅炉自动化控制系统时,需要考虑锅炉的各种运行状态,对不同的运行状态进行识别和分类,以便针对不同状态采取不同的控制策略。
常见的运行状态分类有以下几种:1.启动状态:在锅炉启动阶段,需要通过控制热水流入速度和阀门开合来调节内部的压力和温度;2.稳态状态:当锅炉运行稳定时,需要通过控制温度、压力和流量等参数来保证锅炉的正常运行;3.冷却状态:当锅炉停止运行时,需要关掉热水流入阀门,开始进行冷却。
针对不同的运行状态,需要设计不同的控制模型和控制参数。
三、系统架构设计在确定好控制目标和运行状态识别后,需要进行系统架构设计,包括控制系统的硬件和软件两个方面。
1.硬件设计:硬件设计主要包括传感器、执行器、控制器等方面。
对于火电厂锅炉自动化控制系统,传感器主要用于测量锅炉内部的温度、压力、流量等参数;执行器主要用于控制阀门的开合和水泵的开关;控制器主要用于控制系统的数据传输和控制逻辑等。
锅炉自动控制系统原理

锅炉自动控制系统原理
锅炉自动控制系统原理,是指通过改变给水量、燃料量和空气量等参数,以实现锅炉运行状态的自动调节和控制。
其基本原理如下:
1. 反馈控制原理:锅炉自动控制系统通过传感器获取锅炉各种参数的实时数值,如水位、压力、温度等,并将这些数值反馈到控制器中。
控制器根据设定的目标值和实际值之间的差异,计算出调节量,并将调节量输出到执行机构,对给水量、燃料量和空气量进行调节,使得锅炉保持在预定的运行状态。
2. 控制策略原理:锅炉自动控制系统采用不同的控制策略,以满足不同的运行需求。
常见的控制策略包括比例控制、积分控制和微分控制。
比例控制是根据实际值与目标值的差异,按比例调节输出量;积分控制是根据实际值与目标值的累积差异,按比例调节输出量;微分控制是根据实际值的变化速率,按比例调节输出量。
通过合理地组合这些控制策略,可以实现锅炉自动控制系统的精确调节和稳定运行。
3. 安全保护原理:锅炉自动控制系统在设计中考虑了安全保护功能。
当锅炉出现异常情况时,如超过安全压力、水位过低等,系统会发出报警信号,并采取相应的措施进行保护。
常见的安全保护功能包括水位控制、燃料气动比控制、过热保护等。
这些保护功能可以有效地避免锅炉的过载运行和危险事故的发生。
总之,锅炉自动控制系统原理主要包括反馈控制原理、控制策
略原理和安全保护原理。
通过科学合理地运用这些原理,可以实现锅炉自动控制系统的高效运行和安全保护。
- 1、下载文档前请自行甄别文档内容的完整性,平台不提供额外的编辑、内容补充、找答案等附加服务。
- 2、"仅部分预览"的文档,不可在线预览部分如存在完整性等问题,可反馈申请退款(可完整预览的文档不适用该条件!)。
- 3、如文档侵犯您的权益,请联系客服反馈,我们会尽快为您处理(人工客服工作时间:9:00-18:30)。
综述锅炉汽包燃烧系统是工业蒸汽锅炉安全、稳定运行的重要指标,温度过高,会使蒸汽带水过多,汽水分离差,使后续的过热器管壁结垢,传热效率下降,过热蒸汽温度下降,严重时将引起蒸汽品质下降,影响生产和安全;温度过低又将破坏部分水冷壁的水循环不能满足工艺要求,严重时会发生锅炉爆炸。
尤其是大型锅炉,一旦控制不当,容易使汽包满水或汽包内的水全部汽化,造成重大事故。
因此,在锅炉运行中,保证温度在正常范围是非常重要的。
本文设计了一种数字式锅炉温度控制系统,并给出了硬件原理图。
该控制系统是用MCS-51系列单片机及其相关硬件来实现,利用传感器测量温度数据、CPU循环检测传感器输出状态,并用光柱和LED指示温度的高度。
当锅炉温度低于用户设定的值时,系统自动打开燃料通道,当温度到达设定值时,系统自动关闭燃料通道。
通过定量的计算表明该控制系统设计合理、可行。
一.系统总体设计1.1 系统总体设计方案设计框图如下所示:图1-1系统框图1.2 单元电路方案的论证与选择硬件电路的设计是整个实验的关键部分,我们在设计中主要考虑了这几个方面:电路简单易懂,较好的体现物理思想;可行性好,操作方便。
在设计过程中有的电路有多种备选方案,我们综合各种因素做出了如下选择。
1.2.1 温度信号采集电路的论证与选择采用温度传感器DS18B20美国DALLAS公司的产品可编程单总线数字式温度传感器DS18B20可实现室内温度信号的采集,有很多优点:如直接输出数字信号,故省去了后继的信号放大及模数转换部分,外围电路简单,成本低;单总线接口,只有一根信号线作为单总线与CPU连接,且每一只都有自己唯一的64位系列号存储在其内部的ROM存储器中,故在一根信号线上可以挂接多个DS18820,便于多点测量且易于扩展。
DS 18 B2 0的测温范围较大,集成度较高,但需要串口来模拟其时序才能使用,故没有选用此方案。
1.2.1输入输出通道及其接口设计1)温度检测模拟输入通道设计图1-2 输入通道原理图设V /F 变换器的额定输出频率为F ,计数器对输出脉冲的计数时间为Ts ,A /D 转换结果的分辨率为i ,则有:sis F T 2取Ts =1s ,则在V /F 的输出频率范围0~10kHz 内,可以得到13位的A /D 转换结果。
2) 晶闸管数字触发输出通道设计晶闸管的工作方式有:调压方式; 调功方式调压方式:是通过利用移相触发脉冲调节晶闸管的导通角,使输入到电加热元件的电压改变,达到调节用电器的输入功率,来实现控制目的 。
图1-3 调压方式原理图图1-4 波形图调功方式:触发电路采用的是过零触发方式,外加正弦电压过零时控制信号才使晶闸管的触发导通,则负载上得到的电压是一个正弦波。
调功方式输入电炉的平均功率为:RU N n P 2P ——输入电炉的功率;R ——负载有效电阻;U ——电网电压 ;n ——允许导通的波头数;N ——设定的波头数。
当 n =0时,电炉的输入功率为零;n =N 时,电炉的输入功率为满功率。
由以上分析可得晶闸管数字触发输出通道设计图1-4 过零检测同步脉冲电路图1-5 波形图 3) 拨码盘给定输入通道拨码盘作为数字量的输入设备,设定和修改码盘值可作为控制系统的给定值。
输入非数字信息时,需要事先将非数字信息转换为数字代码,再由拨码盘输入。
4) 数码显示输出通道 包括: 数字量输出接口电路;锁存译码驱动电路;七段数码管显示器。
5) 打印机输出通道 包括: 系统配置了通用打印机接口电路; 打印内容包括表头、制表、采样数据和采样时间。
二.系统框图2.1系统原理图T12.2系统框图由系统原理图可画出系统的结构框图为z)闭环控制系统是指控制器与被控对象之间既有顺向控制又有反向联系的控制系统。
闭环控制系统优点----不管任何扰动引起被控变量偏离设定值,都会产生控制作用去克服被控变量与设定值的偏差。
因此闭环控制系统有较高的控制精度和较好的适应能力,其应用范围非常广泛。
缺点---闭环控制系统的控制作用只有在偏差出现后才产生,当系统的惯性滞后和纯滞后较大时,控制作用对扰动的克服不及时,从而使其控制质量大大降低。
在闭环控制系统中,根据设定值的不同形式,又可分为定值控制系统,随动控制系统和程序控制系统3.温度系统控制器的设计由以上分析可知,锅炉的温度控制系统可以近似为二阶系统,可表示为)1(1)(+=s s s G o ,以大林算法设计数字控制器D (z)。
设采样周期T=0.5s 。
3.1计算广义对象的脉冲传递函数)1)(1(])1()1[()1)(1()1)(1()1(1111)1(1111)1()1(1)1()1(11)(11111121111112112121)1()1(11z e z z e e ez z e zz ze zze zz e z z z zs z s z e T T T T TTTT Ts T T TT s s Z s Z s s s Z z G -----------------------------+-+=--+----=⎥⎥⎦⎤⎢⎢⎣⎡-+--∙-=⎥⎥⎦⎤⎢⎢⎣⎡++-∙-=⎥⎥⎦⎤⎢⎢⎣⎡+∙-=⎥⎥⎦⎤⎢⎢⎣⎡+∙-=----把T=0.5s 、 607.05.0==--e e T 代入得)607.01)(1()832.01(107.0)(1111z z z z z G ------+=3.2 )(z Φ的计算由于 )1()1()(1//1z e e zT T N z -------=Φττ此处N=0、T=0.5s ,τ是整个系统(包括数字控制器和被控对象)的时间常数,代入上式得)1()1()(1//1z e e zT T z ------=Φττ由于 )(1)(z z G e Φ-=所以 )1()(1)(1/11z e z G T e z z ----=Φ-=-τ3.3数字控制器的设计由数字控制器的公式)()()()(Z z G z z D G e Φ=把式(3)中的)()(z z G e 和Φ代入式(4)得数字控制器z z e T z D 11/832.01)607.01)1(934.0)(---+--=(τ3.4消除振铃现象由于直接用大林算法构成的闭环控制系统时,数字控制器的输出U (z )会以1/2的采样频率大幅度上下摆动,我们把这种现象叫做振铃现象。
振铃现象与被空对象的特性、闭环时间常数、采样周期、纯滞后时间的大小等有关,振铃现象中的震荡是衰减的,并且由于被控对象中惯性环节的低通特性,使得这种震荡对系统输出几乎无任何影响,但是振铃现象却会增加执行机构的磨损。
所以要想尽办法消除振铃现象。
由于令z=-1附近的极点会引起振铃现象,为消除振铃令现象,令z=-1附近的极点的z=1,代入上式得)607.01)1(510.0)(1/z e T z D ----=(τ4.硬件设计本控制系统原理框图如图1所示,它由以下几个模块构成:信号转换及调理电路、数据采集模块、数据显示模块、脉宽调制控制及驱动电路和执行机构。
图4-1系统硬件电路4. 1.信号转换及调理电路信号转换调理就是将温度信号转化为电信号,然后调理为可采集的电压信号。
具体电路参见图。
图4-2信号转换及调理电路4.2 数据采集模块通过A/D转换器将输入的模拟电压量转换为数字量,并通过并行接口芯片将数字量送给计算机。
本控制系统A/D转换器采用高精度的MC14433,图为MC14433的典型电路图。
MC14433是三位半十进制(即11位二进制数)的双积分式模数转换器,转换速率为4-10Hz,它无控制启停信号,一旦上电,就不断地转换。
转换结果采用BCD码动态扫描输出,它的千位、百位、十位、个位的BCD码输出为分别与DS1、DS2、DS3、DS4输出高电平是相对应,由于它们无三态特性,不可与PC机直接相连,因此要通过并行接口芯片相连接。
又因为MC14433无内部参考电压源,因此利用低温漂的集成化的精密电源MC1403来产生稳定的参考电压。
图4-3数据采集电路4.3数据显示模块PC机将采集到的温度值经处理后送往LED数码管上显示,并在屏幕上打印出控制曲线。
这部分可利用PC微机总线接口实验装置上的现有资源,在实验装置上本模块提供了六个LED数码管,CPU通过两个端口来驱动LED数码管,分别为段输出选通端和位选通端。
数据的输出显示采用动态扫描方式,利用眼睛的视觉惯性来实现稳定的数字显示。
4. 4.脉宽调制控制及驱动电路脉宽调制控制及驱动部分的原理图(图中包括执行机构部分)如下:图 4-4 脉宽调制控制及驱动电路本电路用于完成反馈控制的功能,利用PC机输出的经PID控制算法处理后的误差信号去控制产生具有一定占空比的脉冲,并送往驱动电路进行脉冲放大。
改变占空比的调节方法有脉宽调制(PWM)和脉频调制(PFM)。
由原理图可知本系统采用PWM方式,即工作频率不变,通过改变后级电路的导通与截止比来改变占空比。
图上所示各点的波形具体体现了本电路的工作过程。
4.5.执行机构这部分电路比较简单,由双向可控硅(晶闸管)及电路组成,见图所示。
晶闸管一旦触发,管子就导通,把控制信号减少甚至完全去掉,它仍然导通,只有当阳极电流减少到维持电流以下,管子才会截止。
不过双向可控硅则无所谓阴、阳极。
本电路可控硅采用BT138 600E,见图,其中T1:主端子 T2:主端子 G:门极5软件设计系统控制程序的任务:a)系统初始化。
b)多路模拟转换开关的切换控制。
c)温度反馈信号采样和数字滤波、线性化处理。
d)读给定输入值,且将BCD码转换为二进制码。
e)完成系统的控制算法和控制输出。
f)定点或巡回显示温度值和网带速度值。
g)定时打印时间、温度和网带运行速度。
按控制功能将程序分成三个程序模块:5.1系统初始化程序模块系统初始化包括:a)设置堆栈;b)清除动态数据缓冲区;c)初始化打印缓冲区;d)设置计数器的控制字和计数初始值;e)设置时钟系统的初始值;f)设置控制算法程序的初始值;g)系统中断控制初始化等。
5.2外部中断服务程序模块中断服务程序的任务:1)读取A/D转换结果,以BCD码的形式送到数码管中显示。
2)读取温度给定值并将BCD码转换为二进制码。
3)外部中断产生ls钟内,将多路模拟转换开关切换到下一个通道。
5.3定时打印程序模块实现任务:1)实时时钟程序2)根据设定时间完成打印控制图5-2 定时打印程序模块流程图6.系统仿真分别进行给定值变化和干扰变化仿真,并与PID控制的变化加以比较,整理得下图6-1 燃烧系统的内模控制与PID控制的阶跃响应曲线由图6-1可以看出,内模控制比普通PID控制更能获得良好的动态效应,稳定速度快,超调量减小,抗干扰能力强。
系统投入运行之后,满足了系统的控制要求。