金属切屑的研究
金属切削实验技术
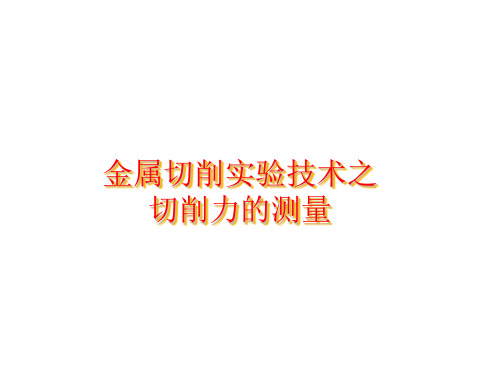
•粘贴在被测部位上的是一种特殊应变片,当温度变化时,
产生的附加应变为零或相互抵消,这种应变片称为温度
自补偿应变片。利用这种应变片来实现温度补偿的方法 称为应变片自补偿法。
3)热敏电阻补偿
R5 分流电阻
+
R1+⊿R U R3
0
T
R2 Rt
U0 URt
+
Ui
Rt
R4 U0
-
U = Ui - URt
U0
向不同,可用在多向分力的测量而避免分力的相互干 扰。压电晶体传感器的测力仪性能良好,自振频率可 达3-10kHz,适用于要求严格的科研试验。压电晶体 测力仪用于静态力的测量时,力容易产生另点漂移。
压电晶体测力仪使用性能较好,但价格昂贵,且使用
维护要求严格,因此适合在要求较高的科研试验中使 用。
电阻应变片测力传感器在测力仪中使用广泛、车、
半导体应变片受轴向力作用时, 其电阻相对变化为
d dR R (1 2 )
半导体应变片的电阻率相对变化量与所受的应变力有关:d E
式中: π——半导体材料的压阻系数;
σ——半导体材料的所受应力; E——半导体材料的弹性模量; ε——半导体材料的应变。
目前箔式应变片应用较多。
金属丝式应变片使用最早。金属丝式应变片蠕变较大,
金属丝易脱胶,有逐渐被箔式所取代的趋势。但其价格
便宜,多用于应变、应力的大批量、一次性试验。
当传感器的弹性体很薄、尺寸很小时,采用箔式应变 片会由于基底材料和粘结剂的存在而对传感器特性产生 不利影响,可采用薄膜式应变片。
测平均切削力,实际已经被淘汰。电容和电感测力仪 虽可用于测量切削力的瞬时变化值,但由于结构限制,
第二章第1节-金属切削过程及切屑类型分析

lfi
lfo
切屑与前刀面的摩擦
第一节 金属切削过程及切屑类型
积屑瘤
在切削速度不高而又能形成连续切屑的情况下,加工一般钢
料或其它塑性材料时,常常在前刀面处粘着一块剖面呈三角
状的硬块,称为积屑瘤。
它的硬度很高,通常是
工件材料的2—3倍,在
切屑
处于比较稳定的状态时,
能够代替刀刃进行切削。
积屑瘤
刀具
积屑瘤
切屑的种类
名称
带状切屑
切屑类型及形成条件
挤裂切屑
单元切屑
崩碎切屑
简图
形态 变形
形成 条件
影响
带状,底面光滑 ,背面呈毛茸状
剪切滑移尚未达 到断裂程度
加工塑性材料, 切削速度较高, 进给量较小, 刀具前角较大
切削过程平稳, 表面粗糙度小, 妨碍切削工作, 应设法断屑
节状,底面光滑有裂 纹,背面呈锯齿状
变形程度表示方法
变形系数
切削层经塑性变形后,厚度增加,长度缩小,宽度基本 不变。可用其表示切削层的变形程度。
◆ 厚度变形系数
h
hch hD
◆ 长度变形系数
L
LD Lch
Lch LD
切屑与切削层尺寸
第一节 金属切削过程及切屑类型
根据体积不变原理,则
h
lc lch
hch hDOMຫໍສະໝຸດ sin(90 OM sin
第二章 金属切削基本理论及应用
第一节 金属切削过程及切屑类型
金属切削过程是指在刀具和切削力的作用下形成切屑的过 程,在这一过程中,始终存在着刀具切削工件和工件材料抵抗切 削的矛盾,产生许多物理现象,如切削力、切削热、积屑瘤、刀 具磨损和加工硬化等。
切削铁屑形成原理

切削铁屑形成原理引言:切削铁屑形成是在金属切削过程中常见的现象,它是由切削工具与工件之间的相互作用引起的。
本文将以切削铁屑形成原理为主题,详细解析切削铁屑的形成过程以及影响因素。
一、切削铁屑的形成过程切削铁屑的形成是由于切削工具对工件进行切削时,金属材料被剪断而产生的。
具体而言,切削铁屑的形成过程可以分为以下几个阶段:1. 切削工具进入切削区域:切削工具以一定的速度和角度进入工件的切削区域,与工件表面接触。
2. 剪切力作用:切削工具施加剪切力,使工件产生塑性变形。
在这个过程中,切削工具与工件之间的摩擦力也起到了重要的作用。
3. 剪切屑的形成:在剪切力的作用下,工件的金属材料开始发生剪切断裂。
这时,金属材料从工件中剥离出来,形成切削铁屑。
4. 切削铁屑的排出:切削铁屑随着切削过程的进行,被切削液或气流带走,排出切削区域。
二、切削铁屑形态的分类切削铁屑的形态可以根据其外观和结构进行分类,常见的切削铁屑形态有以下几种:1. 连续切屑:连续切屑是切削过程中产生的一种常见切削铁屑形态。
它的形状规整,呈螺旋状或螺旋状曲线。
连续切屑的形成主要与工件材料的塑性变形特性和切削工具的几何形状有关。
2. 断续切屑:断续切屑是切削过程中产生的另一种常见切削铁屑形态。
它的形状不规则,呈不连续的碎片状。
断续切屑的形成主要与工件材料的脆性和切削工具的切削速度有关。
3. 螺旋切屑:螺旋切屑是连续切屑中的一种特殊形态,其形状呈螺旋状。
螺旋切屑的形成主要与切削工具的几何形状和切削速度有关。
4. 螺旋碎屑:螺旋碎屑是断续切屑中的一种特殊形态,其形状呈碎片状且具有螺旋结构。
螺旋碎屑的形成主要与工件材料的脆性和切削工具的切削速度有关。
三、影响切削铁屑形成的因素切削铁屑的形成受到多种因素的影响,主要包括以下几个方面:1. 切削速度:切削速度是切削铁屑形成的重要因素之一。
过高或过低的切削速度都会导致切削铁屑形态异常,影响切削质量。
2. 切削深度:切削深度对切削铁屑形态有直接影响。
切削实验报告
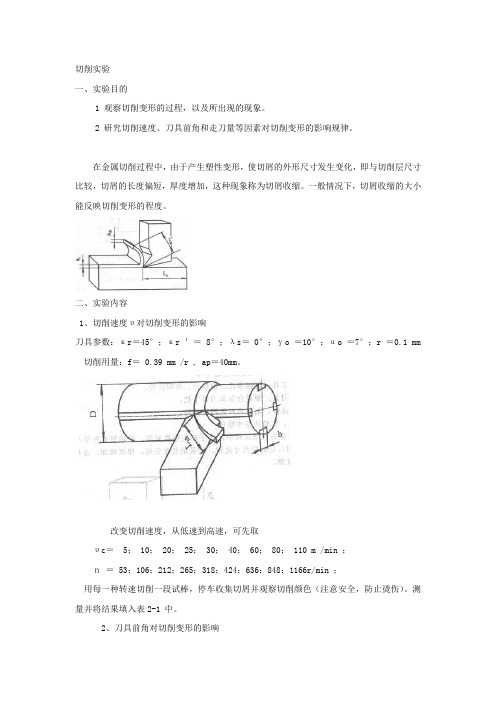
切削实验一、实验目的1 观察切削变形的过程,以及所出现的现象。
2 研究切削速度、刀具前角和走刀量等因素对切削变形的影响规律。
在金属切削过程中,由于产生塑性变形,使切屑的外形尺寸发生变化,即与切削层尺寸比较,切屑的长度偏短,厚度增加,这种现象称为切屑收缩。
一般情况下,切屑收缩的大小能反映切削变形的程度。
二、实验内容1、切削速度υ对切削变形的影响刀具参数:κr=45°;κr '= 8°;λs= 0°;γo =10°;αo =7°;r =0.1 mm 切削用量:f= 0.39 mm /r , ap=40mm。
改变切削速度,从低速到高速,可先取υc= 5; 10; 20; 25; 30; 40; 60; 80; 110 m /min ;n= 53;106;212;265;318;424;636;848;1166r/min ;用每一种转速切削一段试棒,停车收集切屑并观察切削颜色(注意安全,防止烫伤)。
测量并将结果填入表2-1 中。
2、刀具前角对切削变形的影响刀具参数:κr = 45°;κr '= 8°;λs = 0°;αo = 7°; r = 0.1 mm 。
切削用量: f= 0.39 mm /r , ap =40 mm υc= 60 m /min 。
改变车刀前角:γo = 0°; 15°; 30°。
用不同前角的车刀分别切削一段试棒,停车收集切屑并观察切削颜色(注意安全,防止烫伤)。
3、进给量 f 对切削变形的影响刀具参数:κr=45°;κr'=8°;λs=0°;γo=10°;αo=7°;r=0.1 mm 。
切削用量: ap = 40 mm υc= 60 m /min 。
改变进给量: f= 0.2 ; 0.36 ; 0.51 ; 0.66 ( mm/r )。
切屑控制-综述部分
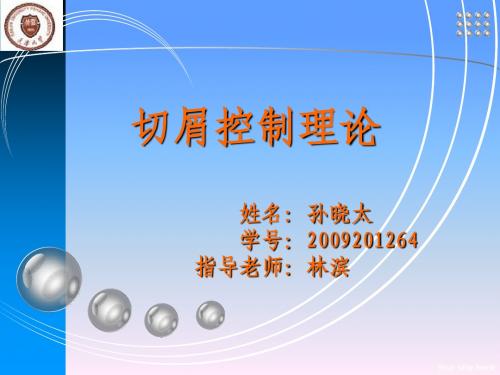
切 屑 控 制 研 究 现 状
LOGO
2.5 专家系统与切屑形成动态仿真技术
切 屑 控 制 研 究 现 状
Your site here
LOGO
2.6 激光辅助切屑控制技术
切 屑 控 制 研 究 现 状
切屑会挂在主轴、刀片、夹具和测量装置上,使自 动测量和装卸设备无法正常使用 缠绕在刀具和工件上的长切屑会在工件上形成擦伤 ,并会缩短刀具寿命 长切屑不能像细小切屑那样有制 研 究 现 状
Your site here
LOGO
2.2 关于切屑卷曲的研究
切屑的上向卷曲
切 屑 控 制 研 究 现 状
切屑的三维卷曲 切屑产生二维卷曲(即上向卷曲和侧向卷曲)的同时 。还常常会产生第三个方向的卷曲。即产生三维卷 曲.第三向卷曲的转动速度同量,分别与上向卷曲 和侧向卷曲的转动角速度向量互相垂直。切屑的三 维卷曲的概念的提出是目前关于切屑卷曲研究的最 新成果。
切 屑 控 制 的 研 究 理 论 及 历 史
切屑的折断力学主要研究经过变形、卷曲和 空间运动的切屑是如何折断的。它包括切屑 碰到障碍物而被折断的机理和切屑被甩断的 机理。
Your site here
LOGO
1.5 切屑研究历史成果
------障碍型断屑器 ------障碍型断屑器
切 屑 控 制 的 研 究 理 论 及 历 史
名称 带状切屑 挤裂切屑 单元切屑 崩碎切屑
控 制 的
简图
研 究
形态
理 论
变形
带状,底面光滑, 节状,底面光滑有裂 背面呈毛茸状 纹,背面呈锯齿状 剪切滑移尚未达 到断裂程度 加工塑性材料, 切削速度较高, 进给量较小, 刀具前角较大 切削过程平稳, 表面粗糙度小, 妨碍切削工作, 应设法断屑
金属切削中的切屑处理与管理方案

金属切削中的切屑处理与管理方案在机械加工过程中,金属切削是一种常见且重要的加工方法。
然而,金属切削过程中产生的切屑处理与管理成为了一个值得重视的问题。
合理的切屑处理与管理方案可以提高生产效率,减少能源浪费,且对环境保护也具有重要意义。
金属切削过程中产生的切屑主要包括连续切屑、螺旋切屑和碎裂切屑。
这些切屑的特性和数量与切削过程中的材料、切削速度、刀具状况等因素密切相关。
因此,切削过程中的切屑处理与管理需要根据不同的情况制定合适的方案。
首先,切削过程中的切屑处理应该进行及时清理。
及时清理切削产生的切屑可以保持工作环境的清洁与卫生,避免切削刀具因为积屑而损坏。
对于连续切屑和螺旋切屑,可以设置专门的切屑槽或切屑收集装置,在切削过程中将切屑直接引导至切屑槽中进行集中管理。
对于碎裂切屑和小颗粒切屑,可以采用切削油膜、水冷却等辅助手段,将切屑固定在切削液或切削液中形成悬浮液,然后通过切削液循环系统进行处理与过滤。
其次,切屑处理与管理方案还应注重资源利用。
金属切屑中含有大量的金属资源,如果直接丢弃,不仅造成了资源的浪费,还给环境带来了污染。
因此,切削中的切屑可以通过回收、再利用等方式得到合理利用。
例如,可以对切屑进行磁选、洗涤等处理,分离出切屑中的金属物质,然后通过回收再加工,利用于其他生产过程中。
这种方式不仅可以减少资源消耗和环境污染,还可以实现资源的循环利用。
同时,切屑处理与管理方案还需要考虑安全因素。
金属切削过程中产生的切屑往往具有高速旋转的趋势,并且会与刀具生产的高温碰撞,因此切屑会产生较高的温度和动能,并且可能对人员和设备造成伤害。
因此,在制定切屑处理与管理方案时,应考虑安全防护措施,如设置切屑防护罩、切屑收集装置等。
同时,也应加强对切屑清理与管理操作的培训,提高员工的安全意识和操作能力。
最后,切屑处理与管理方案还应考虑环境保护的因素。
金属切削过程中产生的切屑中可能含有有害物质,如重金属元素等,如果不妥善处理,可能会对环境造成污染。
金属切削加工中刀—屑紧密型接触长度的研究

d r e h o c l A e nl gt h omua t se a i ee h t h o lc i e v dt e  ̄a a y c o :n ot efr l .i i o s rdt a t et - hpdoe o na t i h 讲 p ers l 。 te i l l ad o s  ̄ tc kn 出 st ec n 0 ut f h e
o u ̄ g e p r ns I c io , te rl nly ad ap fetn x ei t. n al6 n h a o a t n p  ̄ me d i i
c ∞ I I lt g
c 1 a e ltd rs l wi h x ea e ml e u s 8 Iu a e u ̄ t t ee 0 r n  ̄ s l . c e h r t
紧密型接触长度是切 削第一 、 第二变形 区综台作用 的结果 ; 过切 削试验 , 通 讨论 了切削参数 对刀一 屑紧密型接触长 度的影响 ; 将计算结果与试验结果相 比较 , 分折了该理论公式 的合 理性及适用 范围。 关键词 : 刀一屑紧密型接触长度 . 摩 擦角 , 剪切角 S u y 加 Too- h p Cl s n a tLe g h n m ea ut g td lc i o e Co t c n t i t lc en
i t a e fs m d8 r
d e
肚iIne .T eit e e 。 ut gp r ees3 eto- ̄pcoec na telL r ie ̄e yrB 0l 【a h n u n  ̄ f tn am ̄ tr 1t l l e l 11h o e ls o tc r haedsu db l g n it fte te ̄6 a a uaig fr l r a ly o h h a el eI lt omua ae n i e n
金属切削原理实验报告

时针两个方向各 100°的刻度。其上的工作台 5
可以绕小轴 7 转动,转动的角度,由固连于工作
台 5 上的工作台,指针 6 指示出来。工作台 5 上
的定位块 4 和导条 3 因定在一起,能在工作台 5
的滑槽内平行滑动。
立柱 20 固定安装在底盘 2 上,它是一根矩
形螺纹丝杠,旋转丝杆上的大螺帽 19,可以使
(2)实验仪器
1) 设备: CA6140 普通车床。 2) 刀具:YT15 硬质合金车刀。 3) 试件:45# 钢。
(3)实验原理
切削层变形就是指被切屑层在刀具的切削刃与前刀面的影响作用下,经受挤压而产生的 剪切滑移变形。
(4)实验方法步骤
1) 将车床的参数调至如下结果::n=80rpm;ap=0.5~1mm; =30°;f=0.2mm/r 时,观察 切屑形状。
偏角 的数值。
2
图 1-4 用车刀量角台测量车刀刃倾角
图 1-5 用车刀量角台测量车刀副偏角
5) 前角 的测量
前角 的测量,必须在测量完主偏角 kr 的数值之后才能进行。
从图 1-2 所示的原始位置起,按逆时针方向转动工作台,使工作台指针指到底
盘上Ψ =90°—Kr 的刻度数值处(或者从图 1-3 所示测完主偏角 kr 的位置起,按逆时
针方向使工作台转动 90°),这时,主刀刃在基面上的投影恰好垂直于大指针前面
a(相当于 P0),然后让大指针底面 c 落在通过主刀刃上选定点的前刀面上(紧密贴
合),如图 1-6 所示,则大指针在大刻度盘上所指示的刻度数值,就是正交平面前角
的数值。指针在 0°右边时为+ ,指针在 0°左边时为– 。
6) 后角 的测量
1
平行于工作台 5 的平面。测量车刀角度时,就是根据被测角度的需要,转动工作台 5, 同时调整放在工作台 5 上的车刀位置,再旋转大螺帽 19,使滑体 13 带动大指 针 9 上升或下降而处于适当的位置,然向用大指针 9 的前面 a (或侧面 b、或底面 c),与构成被测角度的面或线紧密贴合,从大刻度盘 12 上读出大指针 9 指示的被 测角度数值。
- 1、下载文档前请自行甄别文档内容的完整性,平台不提供额外的编辑、内容补充、找答案等附加服务。
- 2、"仅部分预览"的文档,不可在线预览部分如存在完整性等问题,可反馈申请退款(可完整预览的文档不适用该条件!)。
- 3、如文档侵犯您的权益,请联系客服反馈,我们会尽快为您处理(人工客服工作时间:9:00-18:30)。
金属变形过程
刀具的磨损
金属切削原理及刀具设计
(Principles of machining by cutting and design of cutter)
基本技能 高级要求
刀具材料选择 刀具几何形状设计 合理切削用量拟订 专用刀具设计
切削过程的模型及理论分析 计算机控制仿真切削过程 新型刀具材料的开发与应用 难加工材料的切削实践
金属切削原理及刀具设计
(Principles of machining by cutting and design of cutter)
前言(Preliminary information)
课程性质
研究金属切削过程与设备的技术科学
专业基础课
主要教学内容
第一章 金属切削过程的基本概念 第二章 金属切削刀具材料及选用 第三章 金属切削变形过程分析 第四章 切削力与切削热 第五章 刀具磨损破损与刀具耐用度 第六章 刀具合理几何参数的选择
主要教学内容
第七章 切削用量的选择 第八章 车削及车刀设计 第九章 磨削及砂轮选择 第十章 钻削及孔加工刀具设计 第十一章 铣削及铣刀设计 第十二章 拉削及拉刀设计 第十三章 齿形加工及刀具简介
金属切削原理及刀具设计
(Principles of machining by cutting and design of cutter)
刀具的起源
牙齿、指甲 旧石器 新石器 陶器 青铜器 铁器
金属切削原理及刀具设计
(Principles of machining by cutting and design of cutter)
近代
优质碳素钢 碳素工具钢 合金工具钢 硬质合金 陶瓷 金刚石、CNC
金属切削原理及刀具设计
(Principles of machining by cutting and design of cutter)
刀具的作用
毛坯ቤተ መጻሕፍቲ ባይዱ
机加工
60%以上为切削加工
地位暂无可替代
新材料、新技术、新工艺
重要领域
成品
金属切削原理及刀具设计
(Principles of machining by cutting and design of cutter)
金属切削原理及刀具设计
(Principles of machining by cutting and design of cutter)
刀具基本概述
刀具的起源
刀具的作用
刀具的发展
金属切削原理及刀具设计
(Principles of machining by cutting and design of cutter)
2. Principles of machining by cutting,abrasion and erosion
3. 陈日嚁. 金属切削原理. 机械工业出版社. 第二版,2012, 02.
4. 乐兑谦. 金属切削刀具. 机械工业出版社.第二版, 2012, 02.
5. 周泽华. 金属切削原理. 上海科学技术出版社. 第二版,
刀具的发展
新材料
新理 论
新工 艺
新运 用
金属切削原理及刀具设计
(Principles of machining by cutting and design of cutter)
学习要求
活学活用
Bi-language
参考书目
1. handbook of high-speed machining technology