各种加工方法的经济精度和表面粗糙度解析
机械加工的经济精度及加工面加工方案

140
170
200
280
260
300
340
—
—
48
58
70
84
100
120
140
160
185
215
—
—
25
30
35
45
50
60
70
80
90
100
—
—
18
22
27
38
39
46
54
63
73
84
—
—
13
16
19
23
27
30
35
40
45
50
—
—
8
9
11
—
—
—
—
—
—
—
—
直径基本尺寸/mm
拉孔
镗孔
磨孔
研
粗拉孔后或钻孔后精拉孔
6.3~3.2
非金属
3.2~1.6
镗孔
粗镗
12.5~6.3
精车
金属
3.2~0.8
半精镗
金属
6.3~3.2
非金属
1.6~0.4
非金属
6.3~1.6
精密车(或金刚石车)
金属
0.3~0.2
精镗
金属
3.2~0.8
非金属
0.4~0.1
非金属
1.6~0.4
车削端面
粗车
12.5~6.3
精密(或
金刚石镗)
金属
0.8~0.2
280
340
——————
60
80
100
各种加工方法的经济精度和表面粗糙度

各种加工方法能够达到的尺寸的经济精度表1 孔加工的经济精度表2 圆锥形孔加工的经济精度表3 圆柱形深孔加工的经济精度表4 花键孔加工的经济精度表5 外圆柱表面加工的经济精度表6 端面加工的经济精度(mm)表7 用成形铣刀加工的经济精度(mm)注:指加工表面至基准的尺寸精度。
表8 同时加工平行表面的经刘精度(mm)注:指两平行表面距离的尺寸精度。
表9 平面加工的经济精度注:1 表内资料适用于尺寸<1m,结构刚性好的零件加工,用光洁的加工表面作为定位和测量基准。
2 端铣刀铣削的加工精度在相同的条件下大体上比圆柱铣刀铣削高一级。
3 细铣仅用于端铣刀铣削。
表10 公制螺纹加工的经济精度表11 花键加工的经济精度表12 齿形加工的经济精度各种加工方法能够达到的形状的经济精度表13 平面度和直线度的经济精度表14 圆柱形表面形状精度的经济精度注:形状精度等级的公差值见附表2、3。
表15 曲面加工的经济精度表16 在各种机床上加工时形状的平均经济精度各种加工方法所能够达到的相互位置的经济精度表17 平行度的经济精度表18 端面跳动和垂直度的经济精度表19 同轴度的经济精度表20 轴心线相互平行的孔的位置经济精度注:对于钻、卧镗及组合机床的镗孔偏差同样适用于铰孔。
表21 轴心线相互垂直的孔的位置经济精度注:在镗空间的垂直孔时,中心距误差可按上式相应的找正方法选用。
各种加工方法能够达到的零件表面粗糙度表22 各种加工方法能够达到的零件表面粗糙度各类型面的加工方案及经济精度表23 外圆表面加工方案表24 孔加工方案表25 平面加工方案——机械篇标准公差及形位公差附表1 标准公差值注:基本尺寸小于1mm时,无IT14至IT18。
13 22-4-25 10:32附表2 平面度、直线度公差值附表3 圆度、圆柱度公差值附表4 平行度、垂直度、倾斜度公差值附表5 同轴度、对称度、圆跳动、全跳动公差值参考文献1 《金属机械加工工艺人员手册》修订本上海科学技术出版社1981年2 《机械制造工艺学》顾崇衔等编著陕西科学技术出版社1982年3 《航空机械设计手册》第三机械工业部612所编1979年4 《机械制造工艺学课程设计简明手册》华中工学院机械制造工艺教研室编1981年5 《机械工程手册》第46篇机械工业出版社1981年6 《圆柱齿轮加工》上海科学技术出版社1979年切削用量切削用量的选择原则正确地选择切削用量,对提高切削效率,保证必要的刀具耐用度和经济性,保证加工质量,具有重要的作用。
各种加工方法的经济精度和表面粗糙度

各种加工方法能够达到的尺寸的经济精度表2圆锥形孔加工的经济精度表3圆柱形深孔加工的经济精度表4花键孔加工的经济精度表6端面加工的经济精度(mm)表8同时加工平行表面的经刘精度(mm)表面长度和宽(mm)W120>120〜300加工性质注:指两平行表面距离的尺寸精度。
91<lm2端铣刀铣削的加工精度在相同的条件下大体上比圆柱铣刀铣削高一级。
3细铣仅用于端铣刀铣削。
表10公制螺纹加工的经济精度表11花键加工的经济精度表12齿形加工的经济精度单头滚刀滚齿(m=1〜20mm)滚刀精度等级:AA 6〜7A8B 9C 10 圆盘形插齿刀插齿(m=1〜20mm)插齿刀精度等级:AA 6A 7B 8 磨齿:成形砂轮仿形法5〜6盘形砂轮范成法3〜6 两个盘形砂轮范成法3〜6 蜗杆砂轮范成法4〜6 用铸铁研磨轮研齿5〜6 直齿圆锥齿轮刨齿8螺旋齿圆锥齿轮刀盘铣齿8蜗轮模数滚刀滚蜗轮8 热轧齿轮(m=2〜8mm) 8〜9 热轧后冷校准齿型(m=2〜8mm)7〜8 冷轧齿轮(m W1.5mm) 7圆盘形插齿刀剃齿(m=l〜20mm)剃齿刀精度等级:ABC各种加工方法能够达到的形状的经济精度14231516牛头刨床表17平行度的经济精度表18端面跳动和垂直度的经济精度表19同轴度的经济精度表20轴心线相互平行的孔的位置经济精度最大刨削长度(mm)各种加工方法能够达到的零件表面粗糙度表22各种加工方法能够达到的零件表面粗糙度>20〜160 >20〜80>©150(mm)粗(有表皮)扩孔word格式-可编辑-感谢下载支持砂轮清理>20〜320 >3.2〜80滚压加工>0.2〜3.2钳工锉削各类型面的加工方案及经济精度表23外圆表面加工方案表24孔加工方案word格式-可编辑-感谢下载支持标准公差及形位公差附表1标准公差值1mm IT14IT18附表2平面度、直线度公差值1《金属机械加工工艺人员手册》修订本上海科学技术出版社1981年2《机械制造工艺学》顾崇衔等编著陕西科学技术出版社1982年3《航空机械设计手册》第三机械工业部612所编1979年4《机械制造工艺学课程设计简明手册》华中工学院机械制造工艺教研室编1981年5《机械工程手册》第46篇机械工业出版社1981年6《圆柱齿轮加工》上海科学技术出版社1979年切削用量切削用量的选择原则正确地选择切削用量,对提高切削效率,保证必要的刀具耐用度和经济性,保证加工质量具有重要的作用。
丝杠螺母座

丝杠螺母座夹具说明书院校: xxxxxxxx姓名:xxxxxx指导教师:xxxxxxx时间:xxxxxxxxxxxx设计说明:本夹具的二维装配图纸采用AutoCAD2000完成,夹具的相关设计参数、图样取自《机床夹具设计手册软件版》。
设计说明书由三部分组成,即工艺规程的制定、夹具设计说明和夹具使用说明工艺规程的制定1.毛坯的选择:毛坯的种类包括铸造、锻件、型材和焊接件。
选择毛坯的基本任务是选定毛坯的制造方法及其制造精度。
毛坯的选择不仅影响毛坯的制造工艺和费用,而且影响到零件机械加工工艺及其生产率和经济性。
如选择高精度的毛坯,可见小的机械加工量和材料消耗,提高了机械加工效率,降低了加工成本,但是却提高了毛坯的加工费用。
因此,选择毛坯要从机械加工和毛坯制造两方面综合考虑,以求得到最佳效果。
1)选择毛坯时应考虑的因素:(1)零件材料及机械性能的要求由于材料的工艺特性,决定了毛坯的制造方法,当零件的材料选定后,毛坯的类型就大致确定了。
例如,材料为灰铸铁的零件必须铸造毛坯;对于重要的钢质零件,为获得良好的力学性能,应选用铸件,在形状简单及机械性能要求不太高时可用型材毛坯;有色金属零件常用型材或铸造毛坯。
(2)零件结构形状和尺寸大小大型且结构简单的零件毛坯多用砂型铸造或自由锻;结构复杂的毛坯多用铸造;小型零件可用模锻件或压力铸造毛坯;板状钢质零件多用锻件毛坯;轴类零件的毛坯;如直径和台阶相差不大,可用棒料,如台阶尺寸相差较大,则宜选用锻件。
(3)产纲领的大小当零件的生产纲领较大时,应选用精度和生产率较高的毛坯制造方法,如模锻、金属型机器造型铸造和精密制造等。
当单件小批生产时,则应选用木模手工造型铸造或自由锻造。
(4)现有生产条件确定毛坯时,必须结合生产厂具体的生产条件,如现场毛坯制造实际水平和能力、外协的可能性等。
(5)充分利用新工艺、新技术和新材料为节约材料和能源,提高机械加工生产率,应充分考虑精铸、精缎、冷轧、冷挤压、粉末冶金和工程塑料等在机械中的应用,这样,可大大减少机械加工量,甚至不需要机械加工,大大提高经济效益。
机械加工工艺与表面处理总结

机械加工工艺与表面处理总结部分内容来源于网络,有侵权请联系删除!部分内容来源于网络,有侵权请联系删除!部分内容来源于网络,有侵权请联系删除!部分内容来源于网络,有侵权请联系删除!部分内容来源于网络,有侵权请联系删除!部分内容来源于网络,有侵权请联系删除!部分内容来源于网络,有侵权请联系删除!部分内容来源于网络,有侵权请联系删除!部分内容来源于网络,有侵权请联系删除!.机械加工工艺与表面处理总结一、常见零件工艺1.1 加工公差等级和表面粗糙度1.外圆表面加工2.孔加工方案3.平面加工方案1.2 加工件的工艺结构1.加工时便于进刀、退刀和便于测量。
加工螺纹时,应留有退刀槽。
2.磨削时各表面间的过渡部分,应设计出越程槽,应保证砂轮自由退出和加工空间。
3.零件尽可能壁厚均匀,要考虑热处理消除应力结构。
4.零件形状尽量简单,便于加工。
便于尺寸误差测量,便于形位误差测量。
5.优先选用标准化参数,零件的孔径、锥度、螺纹孔径和螺距、齿轮模数和压力角、圆弧半径、沟槽等参数尽量选用有关标准推荐的数值,这样可使用标准的刀、夹、量具,减少专用工装的设计、制造周期和费用。
6. 尽量采用标准型材。
只要能满足使用要求,零件毛坯尽量采用标准型材,不仅可减少毛坯制造的工作量,而且由于型材的性能好,可减少切削加工的工时及节省材料。
7.加工件要便于装夹,减少装夹次数,尽可能“一刀活”。
8. 对于有外圆磨的工件,要注明是否允许中心孔;9、工艺退刀槽,砂轮越程槽、是否需要清角应注明;二、热处理、冷处理退火:将工件加热到适当温度,根据材料和工件尺寸采用不同的保温时间,然后进行缓慢冷却(冷却速度最慢),目的是使金属内部组织达到或接近平衡状态,获得良好的工艺性能和使用性能,或者进一步为淬火做准备。
正火:将工件加热到适宜温度后在空气中冷却,正火效果同退火相似,只是得到的组织更细,常用来改善材料的切削性能,也有时用于一些要求不高的零件作为最终热处理。
汽车典型零件制造技术
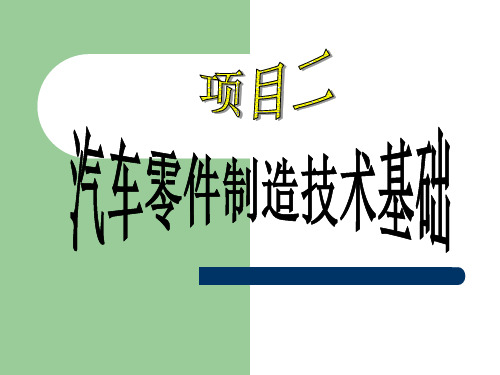
7
粗车-半精车一粗磨-精磨超精加工
IT5
0.12-0.l
主要用于 淬火钢,也 可用于未 淬火钢,但 不宜加工 有色金属
Hale Waihona Puke 主要用于8粗车-半精车-精车-精细车 (金刚石车)
IT6~7
0. 025~0.4
要求较高 的有色金
属加工
9
粗车-半精车-粗磨-精磨超精磨(或镜面磨)
IT5以上
0.006~0.025
极高精度
12.5~50
2 粗车一半精车
IT8~IT10
3 粗车一半精车—精车
4
粗车-半精车-精车-滚 压(或抛光)
IT7~IT8 IT7~IT8
3.2~6.3 0.8~1.6 0.025~0.2
适用于淬 火钢以外 的各种金
属
5 粗车一半精车-磨削
IT7~IT8 0.4~0.8
6 粗车一半精车-粗磨-精磨 IT6~IT7 0.1~0.4
工艺尺寸链的特征
尺寸链由一个自然形成的尺寸与若干个直接得到的尺寸所组成。 尺寸链一定是封闭的,且各尺寸按一定的顺序首尾相接。
尺寸链的组成
组成尺寸链的各个尺寸称为尺寸链的环
分为封闭环和组成环 封闭环 在加工(或测量)过程中最后自然形成的环称为封闭环 每个尺寸链必须有且仅能有一个封闭环。 组成环 在加工(或测量)过程中直接得到的环称为组成环。 按其对封闭环的影响,可分为增环和减环
大批大量生产的产品,可采用专用设各和工艺装备,如多刀、多轴机床或自动机 床等,将工序集中,也可将工序分散后组织流水线生产。但对一些结构简单 的产品,如轴承和刚性较差、精度较高的精密零件,则工序应适当分散。
设备与工装选择
机床的选择
机械制造工艺教案第七章4-6节(已排)
20
(3)时效处理 时效处理有人工时效和自然时效两 种,目的都是为了消除毛坯制造和机械加工中产 生的内应力。精度要求一般的铸件,只需进行一 次时效处理,安排在粗加工后较好,可同时消除 铸造和粗加工所产生的应力。有时为减少运输工 作量,也可放在粗加工之前进行。精度要求较高 的铸件,则应在半精加工之后安排第二次时效处 理,使精度稳定。精度要求很高的精密丝杆、主 轴等零件,则应安排多次时效处理。对于精密丝 杠、精密轴承、精密量具及油泵油嘴配件等,为 了消除残余奥氏体,稳定尺寸,还要采用冰冷处 理(冷却到-70~-80℃,保温1~2h),一般在 回火后进行。
21
(4)表面处理 某些零件为了进一步提高表面的抗蚀能力, 增加耐磨性,常采用表面处理工序,使零件表面覆盖一层 金属镀层、非金属涂层和氧化膜等。金属镀层有镀铬、镀 锌、镀镍、镀铜及镀金、银等;非金属涂层有涂油漆、磷 化等;氧化膜层有钢的发蓝、发黑、钝化,铝合金的阳极 氧化处理等。零件的表面处理工序一般都安排在工艺过程 的最后进行。表面处理对工件表面本身尺寸的改变一般可 以不考虑,但精度要求很高的表面应考虑尺寸的增大量。 当零件的某些配合表面不要求进行表面处理时,则应进行 局部保护或采用机械加工的方法予以切除。
3
(2)加工表面的技术要求是决定表面加工方法的首 要因素,此外还应包括由于基准不重合而提高对某 些表面的加工要求,以及由于被作为精基准而可能 对其提出的更高加工要求。 (3)加工方法选择的步骤总是首先确定被加工零件 主要表面的最终加工方法,然后再选择前面一系列 工序的加工方法和顺序。可提出几个方案进行比较, 选择其中一个比较合理的方案。例如加工一个直径 为φ25H7和表面粗糙度为Ra0.8μm的孔,可有四种 加工方案:①钻孔-扩孔-粗铰-精铰;②钻孔-粗镗半精镗-磨削;③钻孔-粗镗-半精镗-精镗-精细镗; ④钻-拉。应根据零件加工表面的结构特点和产量 等条件,再确定采用其中一种加工方案。主要表面 的加工方法选定以后,再选定各次要表面的加工方 法。
形位公差经济加工精度
同轴度的经济精度
平行度的经济精度
端面跳动和垂直度的经济精度
轴心线相互平行的孔的位置经济精度
注:“①距离误差”指两孔轴心线的距离误差或自孔轴心线到平面的距离误差。
轴心线相互垂直的孔的位置经济精度
注:①指在100mm长度上轴心线的垂直度。
在各种机床上加工的形状、位置的平均经济精度
在各种机床上加工的形状、位置的平均经济精度
注:①指在直径上的成批工件尺寸的分散度;②指在长度上的成批工件尺寸的分散度。
在各种机床上加工的形状、位置的平均经济精度
在各种机床上加工的形状、位置的平均经济精度
1.表面加工方法的选择
选择表面加工方法是,一般先根据表面的加工精度和表面粗糙度要求并考虑生产率和经济性,考虑零件的结构形状、尺寸大小、材料和热处理要求及工厂的生产条件等因素,选定最终加工方法,然后再确定精加工前的准备工序的加工方法,即确定加工方案。
(1)经济精度与经济粗糙度
表4-5、表4-6、表4-7分别为外圆面、孔和平面等典型加工方法和加工方案能达到的经济精度和经济粗糙度。
表4-8为各种加工方法加工轴线平行的孔系时的位置精度(用距离误差表示)。
各种加工方法所能达到的经济精度和经济粗糙度等级,在机械加工的各种手册中均能查到。
各种加工方法的加工精度
各种加工方法的加工精度Revised on November 25, 2020各种加工方法的加工精度一:车削车削中工件旋转,形成主切削运动。
刀具沿平行旋转轴线运动时,就形成内、外园柱面。
刀具沿与轴线相交的斜线运动,就形成锥面。
仿形车床或数控车床上,可以控制刀具沿着一条曲线进给,则形成一特定的旋转曲面。
采用成型车刀,横向进给时,也可加工出旋转曲面来。
车削还可以加工螺纹面、端平面及偏心轴等。
车削加工精度一般为IT8—IT7,表面粗糙度为—μm。
精车时,可达IT6—IT5,粗糙度可达—μm。
车削的生产率较高,切削过程比较平稳,刀具较简单。
二:铣削主切削运动是刀具的旋转。
卧铣时,平面的形成是由铣刀的外园面上的刃形成的。
立铣时,平面是由铣刀的端面刃形成的。
提高铣刀的转速可以获得较高的切削速度,因此生产率较高。
但由于铣刀刀齿的切入、切出,形成冲击,切削过程容易产生振动,因而限制了表面质量的提高。
这种冲击,也加剧了刀具的磨损和破损,往往导致硬质合金刀片的碎裂。
在切离工件的一般时间内,可以得到一定冷却,因此散热条件较好。
按照铣削时主运动速度方向与工件进给方向的相同或相反,又分为顺铣和逆铣。
顺铣铣削力的水平分力与工件的进给方向相同,工件台进给丝杠与固定螺母之间一般有间隙存在,因此切削力容易引起工件和工作台一起向前窜动,使进给量突然增大,引起打刀。
在铣削铸件或锻件等表面有硬度的工件时,顺铣刀齿首先接触工件硬皮,加剧了铣刀的磨损。
逆铣可以避免顺铣时发生的窜动现象。
逆铣时,切削厚度从零开始逐渐增大,因而刀刃开始经历了一段在切削硬化的已加工表面上挤压滑行的阶段,加速了刀具的磨损。
同时,逆铣时,铣削力将工件上抬,易引起振动,这是逆铣的不利之处。
铣削的加工精度一般可达IT8—IT7,表面粗糙度为—μm。
普通铣削一般只能加工平面,用成形铣刀也可以加工出固定的曲面。
数控铣床可以用软件通过数控系统控制几个轴按一定关系联动,铣出复杂曲面来,这时一般采用球头铣刀。
各种加工方法的加工经济精度及粗糙度
8
刨
粗刨
11-13
5-20
半精刨
8-11
精刨
6-8
宽刀精刨
6
插
拉
粗拉
10-11
5-20
精拉
6-9
平磨
粗磨
8-10
半精磨
8-9
精磨
6-8
精密磨
6
刮
25x25
内点数
8-10
研磨
粗磨
6
精磨
5
精密磨
5
砂带磨
精磨
5-6
精密磨
5
滚压
7-10
精心搜集整理,只为你的需要
5-6
精珩
5
研磨
粗研
5-6
精研
5
精密研
5
挤
滚珠、滚柱扩孔器,挤压头
6-8
平面中各种加工方法的加工经济精度及表面粗糙度
加工方法
加工情况
加工经济精度(IT)
表面粗糙度Ra(um)
周铣
粗铣
11-13
5-20
半精铣
8-11
精铣
6-8
端铣
粗铣
11-13
5-20
半精铣
8-11
精铣
6-8
车
粗车
8-11
半精车
6-8扩Biblioteka 粗扩12-135-20
一次扩孔
11-13
10-40
精扩
9-11
铰
半精铰
8-9
精铰
6-7
手铰
5
拉
粗拉
9-10
一次拉孔
10-11
精拉
7-9
推
半精推
- 1、下载文档前请自行甄别文档内容的完整性,平台不提供额外的编辑、内容补充、找答案等附加服务。
- 2、"仅部分预览"的文档,不可在线预览部分如存在完整性等问题,可反馈申请退款(可完整预览的文档不适用该条件!)。
- 3、如文档侵犯您的权益,请联系客服反馈,我们会尽快为您处理(人工客服工作时间:9:00-18:30)。
各种加工方法能够达到的尺寸的经济精度
表1 孔加工的经济精度
表2 圆锥形孔加工的经济精度
表3 圆柱形深孔加工的经济精度
表4 花键孔加工的经济精度
表5 外圆柱表面加工的经济精度
表6 端面加工的经济精度(mm)
表7 用成形铣刀加工的经济精度(mm)
注:指加工表面至基准的尺寸精度。
表8 同时加工平行表面的经刘精度(mm)
注:指两平行表面距离的尺寸精度。
表9 平面加工的经济精度
注:1 表内资料适用于尺寸<1m,结构刚性好的零件加工,用光洁的加工表面作为定位和测量基准。
2 端铣刀铣削的加工精度在相同的条件下大体上比圆柱铣刀铣削高一级。
3 细铣仅用于端铣刀铣削。
表10 公制螺纹加工的经济精度
表11 花键加工的经济精度
表12 齿形加工的经济精度
各种加工方法能够达到的形状的经济精度
表13 平面度和直线度的经济精度
表14 圆柱形表面形状精度的经济精度
注:形状精度等级的公差值见附表2、3。
表15 曲面加工的经济精度
表16 在各种机床上加工时形状的平均经济精度
各种加工方法所能够达到的相互位置的经济精度
表17 平行度的经济精度
表18 端面跳动和垂直度的经济精度
表19 同轴度的经济精度
表20 轴心线相互平行的孔的位置经济精度
注:对于钻、卧镗及组合机床的镗孔偏差同样适用于铰孔。
表21 轴心线相互垂直的孔的位置经济精度
注:在镗空间的垂直孔时,中心距误差可按上式相应的找正方法选用。
各种加工方法能够达到的零件表面粗糙度
表22 各种加工方法能够达到的零件表面粗糙度
各类型面的加工方案及经济精度
表23 外圆表面加工方案
表24 孔加工方案
表25 平面加工方案
——机械篇
标准公差及形位公差
附表1 标准公差值
注:基本尺寸小于1mm时,无IT14至IT18。
1 20-10-2
2 14:35
附表2 平面度、直线度公差值
附表3 圆度、圆柱度公差值
附表4 平行度、垂直度、倾斜度公差值
附表5 同轴度、对称度、圆跳动、全跳动公差值
参考文献
1 《金属机械加工工艺人员手册》修订本上海科学技术出版社1981年
2 《机械制造工艺学》顾崇衔等编著陕西科学技术出版社1982年
3 《航空机械设计手册》第三机械工业部612所编1979年
4 《机械制造工艺学课程设计简明手册》华中工学院机械制造工艺教研室编1981年
5 《机械工程手册》第46篇机械工业出版社1981年
6 《圆柱齿轮加工》上海科学技术出版社1979年
切削用量
切削用量的选择原则
正确地选择切削用量,对提高切削效率,保证必要的刀具耐用度和经济性,保证加工质量,具有重要的作用。
1 粗加工切削用量的选择原则:
粗加工时加工精度与表面求不高,毛坯余量较大。
因此,选择粗加工的切削用量时,要尽可能保证较高的单位时间金属切除量(金属切除率)和必要的刀具耐用度,以提高生产效率和降低加工成本。
金属切除率可以用下式计算:
1000⨯≈p w vfa Z
式中 Zw ——单位时间内的金属切除量(mm 3/s); v ———切削速度(m/s); f ———进给量(mm/r); a p ——切削深度(mm)。
提高切削速度、增大进给量和切削深度,都能提高金属切除率。
但是,在这三个因素中,影响刀具耐用度最大的是切削速度,其次是进给量,影响最小的是切削深度。
所以粗加工切削用量的选择原则是:首先考虑选择一个尽可能大的吃刀深度a p ,其次选择一个较大的进给量f ,最后确定一个合适的切削速度v 。
选用较大的a p 和f 以后,刀具耐用度t 显然也会下降,但要比v 对t 的影响小得多,只要稍微降低一下v 便可以使t 回升到规定的合理数值。
因此,能使v 、f 、a p 的乘积较大,从而保证较高的金属切除率。
此外,增大a p 可使走刀次数减少,增大f 又有利于断屑。
因此,根据以上原则选择粗加工切削用量对于提高生产效率,减少刀具消耗,降低加工成本是比较有利的。
切削深度的选择:
粗加工时切削深度应根据工件的加工余量和由机床、夹具、刀具、工件组成的工艺系统的刚性来确定。
在保留半精加工、精加工必要余量的前提下,应当尽量将粗加工余量一次切掉。
只有当总加工余量太大,一次切不完时,才考虑分几次走刀。
进给量的选择:
粗加工时限制进给量提高的因素主要是切削力。
因此,进给量应根据机床—夹具—刀具—工件系统的刚性和强度来确定。
选择进给量时应考虑到机床进给机构的强度、刀杆尺寸、刀片鹌鹑、工件的直径和长度等。
在工艺系统的刚性和强度好的情况下,可选用大一些的进给量;在刚性和强度较差的情况下,应适当减小进给量。
表13所示为粗车外圆和端面时的进给量,可供选用时参考。
切削速度v的选择:
粗加工时,切削速度v主要受刀具耐用度和机床功率的限制。
合理的切削速度一般不需要经过精确计算,而是根据生产实践经验和有关资料确定。
切削深度、进给量和切削速度三者决定了切削功率,在确定切削速度时必须考虑到机床的许用功率。
如超过了机床的许用功率,则应适当降低切削速度。
2 精加工时切削用量的选择原则:
精加工时加工精度和表面粗糙度要求较高,加工余量要小且较均匀。
因此,选择精加工的切削用量时应着重考虑如何保证加工质量,并在此基础上尽量提高生产效率。
切削深度的选择:
精加工时的切削深度应根据粗加工留下的余量确定。
通常希望精加工余量不要留得太大,否则,当吃刀深度a p较大时,切削力增加较显著,影响加工质量。
进给量的选择:
精加工时限制进给量提高的主要因素是表面粗糙度。
进给量f增大时,虽有利于断屑,但残留面积高度增大,切削力上升,表面质量下降。
表14所示为半精车和精车时的进给量,可供选用时参考。
切削速度v的选择:
切削速度v提高时,切削变形减小,切削力有所下降,而且不会产生积屑瘤和鳞刺。
一般选用切削性能好的刀具材料和合理的几何参数,以尽可能提高切削速度v。
只有当切削速度受到工艺条件限制而不能提高时,才选用低速,以避开积屑瘤产生范围。
由此可见,精加工时应选用较小的吃刀深度a p和进给量f,并在保证合理刀具耐用度的前提下,选取尽可能高的切削速度v,以保证加工精度和表面质量,同时满足生产率的要求。
一、车削
1 车削切削力的计算:
1) 用实验公式计算车削切削力。