外观检验标准
外观检验标准
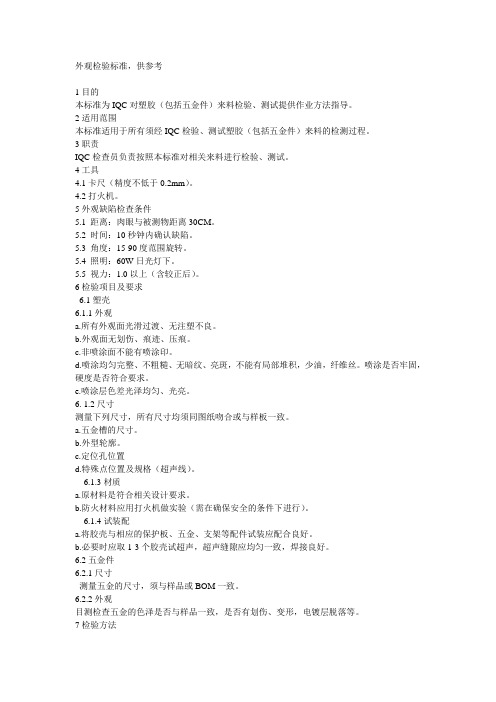
外观检验标准,供参考1目的本标准为IQC对塑胶(包括五金件)来料检验、测试提供作业方法指导。
2适用范围本标准适用于所有须经IQC检验、测试塑胶(包括五金件)来料的检测过程。
3职责IQC检查员负责按照本标准对相关来料进行检验、测试。
4工具4.1卡尺(精度不低于0.2mm)。
4.2打火机。
5外观缺陷检查条件5.1 距离:肉眼与被测物距离30CM。
5.2 时间:10秒钟内确认缺陷。
5.3 角度:15-90度范围旋转。
5.4 照明:60W日光灯下。
5.5 视力:1.0以上(含较正后)。
6检验项目及要求6.1塑壳6.1.1外观a.所有外观面光滑过渡、无注塑不良。
b.外观面无划伤、痕迹、压痕。
c.非喷涂面不能有喷涂印。
d.喷涂均匀完整、不粗糙、无暗纹、亮斑,不能有局部堆积,少油,纤维丝。
喷涂是否牢固,硬度是否符合要求。
e.喷涂层色差光泽均匀、光亮。
6. 1.2尺寸测量下列尺寸,所有尺寸均须同图纸吻合或与样板一致。
a.五金槽的尺寸。
b.外型轮廓。
c.定位孔位置d.特殊点位置及规格(超声线)。
6.1.3材质a.原材料是符合相关设计要求。
b.防火材料应用打火机做实验(需在确保安全的条件下进行)。
6.1.4试装配a.将胶壳与相应的保护板、五金、支架等配件试装应配合良好。
b.必要时应取1-3个胶壳试超声,超声缝隙应均匀一致,焊接良好。
6.2五金件6.2.1尺寸测量五金的尺寸,须与样品或BOM一致。
6.2.2外观目测检查五金的色泽是否与样品一致,是否有划伤、变形,电镀层脱落等。
7检验方法7.1外观使用目测法检查被检品的外观。
7.2尺寸使用卡尺测量被检品的尺寸。
8塑壳表面分类A面:塑壳壳面;B面:塑壳底面。
9等级分类A级:公司所生产原配、原装产品的塑壳和五金来料;B级:公司所生产自有品牌或类似产品塑壳和五金来料;C级:以客户所承认样品生产的产品的塑壳和五金来料。
10 质量评定10.1检验办法塑胶(包括五金件)来料按按GB/T 2828-87 正常检查一次抽样方案II级检查水平进行抽样检查。
外协件外观检验标准

外协件外观检验标准第一篇:外协件外观检验标准外协件验收标准外协件外观检验标准一、适用范围:外协件的尺寸和外观检验二、检验项目及验收标准:A.尺寸验收标准:外协件(锁金、机加件)尺寸按图纸要求及允许公差表执行,特殊情况以实际装配并提交研发部工程师协同解决。
B.表面处理验收标准:外观判定标准(1)表面平整,无变形,无毛刺,凸起,裂痕等。
表面各边、角、焊接部位毛刺均须去除。
(2)表面处理过程中,螺丝孔中不能被粉或者漆塞住了。
喷粉或者喷漆前要提前在螺丝孔丽塞上纸,以免粉油漆塞住。
(3)表面不得有污点,不得有任何碰伤、开裂、刮伤等严重表面缺陷。
如加工过程中有此缺陷:颗粒、气泡,允许按照以下标准进行验收检验:A面:整个表面内允许3点,每点直径Imm以下,点与点距离20mm以上。
B面:整个表面内允许5点,每点直径Imm以下,点与点距离20mm以上。
C面:整个表面内允许7点,每点直径Imm以下,点与点距离20mm以上*表面定义:A面:使用时面对使用者的表面B面:与A面相邻的4个表面,或客户不能在外部光源下直接看到的表面C面:使用时背对使用者的表面。
C.焊接(1)焊缝应牢固,均匀,不得有虚焊,裂纹,未焊透,焊穿,豁口,咬边等缺陷。
(2)焊点要求:焊点长度8-12mm,两焊点之间的距离200±20mm,V焊点位置要对称,上下位置要统一。
如加工图纸上有特殊要求,按图纸执行(3)焊接后,其他非焊接部位不允许有焊渣,电弧损伤等现象,表面焊渣,飞溅物需清洁干净。
(4)焊接后表面要磨平。
D丝印文字检验标准(1)颜色:颜色与标准色板在色差范围内,色彩印刷应该有足够的遮盖力,以反射光看,看不清下面的色彩和结构为准。
(2)缺陷:不允许有图案不清楚,字体不端正,拖墨,漏印,错位,重叠,少墨等不良。
银金件验收标准1.总则银金件是以焊接部件或单独零件的供货方式入场验收,主要技术验收项目需要我公司技术,质量人员在制造厂方进行评审检验,验收过程参照我方提供的图纸,技术协议以及制造商提供的并经我方认可的过程控制文件进行。
外观质量检查标准(通过观察检验)。

外观质量检查标准(通过观察检验)在现代社会中,产品的外观质量往往是用户选择商品的一个重要标准。
对产品的外观质量进行检查和评估显得尤为重要。
外观质量检查标准通过观察检验产品的外观特征、表面处理、外包装等内容,以确定产品是否符合质量要求。
以下将从不同角度对外观质量检查标准进行详细介绍。
一、外观特征1. 表面平整度产品的表面平整度是衡量外观质量的重要指标。
通过目视检查产品表面是否有凹凸不平、气泡、裂痕等表面缺陷,以及表面光洁度是否符合要求。
2. 颜色和色差颜色是产品外观的一个重要特征,颜色的一致性和准确性直接关系到产品的外观质量。
颜色差异过大会影响产品整体的美观性和一致性。
3. 尺寸和形状产品的尺寸和形状对外观质量也有很大影响。
通过尺寸测量仪器检查产品的尺寸和形状是否符合设计要求,确保产品外观符合标准。
二、表面处理1. 表面涂装涂装是产品表面处理的一种常见方式,目的是提高产品的外观质量和耐久性。
外观质量检查要对产品表面的涂装情况进行全面检查,包括颜色是否均匀、是否存在漏涂、结疤、起皮等情况。
2. 表面镀层对于镀层产品,外观质量检查要检查镀层的均匀性、附着力、亮度和颜色等指标,以确保镀层质量符合要求。
三、外包装1. 包装完整性外包装的完整性决定了产品在运输和使用过程中是否受到保护,因此外观质量检查要对产品的外包装进行全面检查,确保包装完整无损。
2. 标识和标牌产品的外包装需要标识产品的相关信息,外观质量检查要对产品的标识和标牌进行检查,确保标识内容准确完整。
四、检验方法1. 目视检查目视检查是最直接的检验方法之一,通过肉眼观察产品的外观特征、表面处理情况和外包装完整性等内容,进行外观质量的初步评估。
2. 仪器检测对于一些尺寸、颜色和光洁度等指标,需要借助相关的仪器设备进行检测,以确保检测结果的准确性。
五、结论外观质量检查标准通过观察检验产品的外观特征、表面处理、外包装等内容,可以有效评估产品的外观质量,保证产品的外观符合质量要求。
外观检验标准
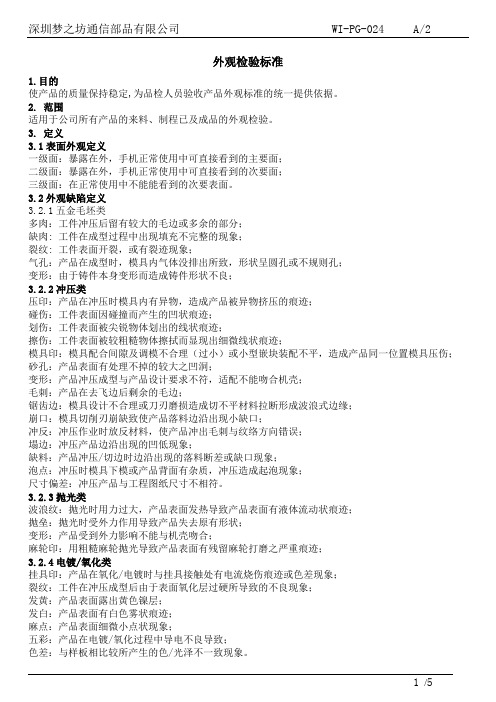
外观检验标准1.目的使产品的质量保持稳定,为品检人员验收产品外观标准的统一提供依据。
2. 范围适用于公司所有产品的来料、制程已及成品的外观检验。
3. 定义3.1表面外观定义一级面:暴露在外,手机正常使用中可直接看到的主要面;二级面:暴露在外,手机正常使用中可直接看到的次要面;三级面:在正常使用中不能能看到的次要表面。
3.2外观缺陷定义3.2.1五金毛坯类多肉:工件冲压后留有较大的毛边或多余的部分;缺肉: 工件在成型过程中出现填充不完整的现象;裂纹: 工件表面开裂,或有裂迹现象;气孔:产品在成型时,模具内气体没排出所致,形状呈圆孔或不规则孔;变形:由于铸件本身变形而造成铸件形状不良;3.2.2冲压类压印:产品在冲压时模具内有异物,造成产品被异物挤压的痕迹;碰伤:工件表面因碰撞而产生的凹状痕迹;划伤:工件表面被尖锐物体划出的线状痕迹;擦伤:工件表面被较粗糙物体擦拭而显现出细微线状痕迹;模具印:模具配合间隙及调模不合理(过小)或小型嵌块装配不平,造成产品同一位置模具压伤;砂孔:产品表面有处理不掉的较大之凹洞;变形:产品冲压成型与产品设计要求不符,适配不能吻合机壳;毛刺:产品在去飞边后剩余的毛边;锯齿边:模具设计不合理或刀刃磨损造成切不平材料拉断形成波浪式边缘;崩口:模具切削刃崩缺致使产品落料边沿出现小缺口;冲反:冲压作业时放反材料,使产品冲出毛刺与纹络方向错误;塌边:冲压产品边沿出现的凹低现象;缺料:产品冲压/切边时边沿出现的落料断差或缺口现象;泡点:冲压时模具下模或产品背面有杂质,冲压造成起泡现象;尺寸偏差:冲压产品与工程图纸尺寸不相符。
3.2.3抛光类波浪纹:抛光时用力过大,产品表面发热导致产品表面有液体流动状痕迹;抛垒:抛光时受外力作用导致产品失去原有形状;变形:产品受到外力影响不能与机壳吻合;麻轮印:用粗糙麻轮抛光导致产品表面有残留麻轮打磨之严重痕迹;3.2.4电镀/氧化类挂具印:产品在氧化/电镀时与挂具接触处有电流烧伤痕迹或色差现象;裂纹:工件在冲压成型后由于表面氧化层过硬所导致的不良现象;发黄:产品表面露出黄色镍层;发白:产品表面有白色雾状痕迹;麻点:产品表面细微小点状现象;五彩:产品在电镀/氧化过程中导电不良导致;色差:与样板相比较所产生的色/光泽不一致现象。
外观检验标准(完整版)
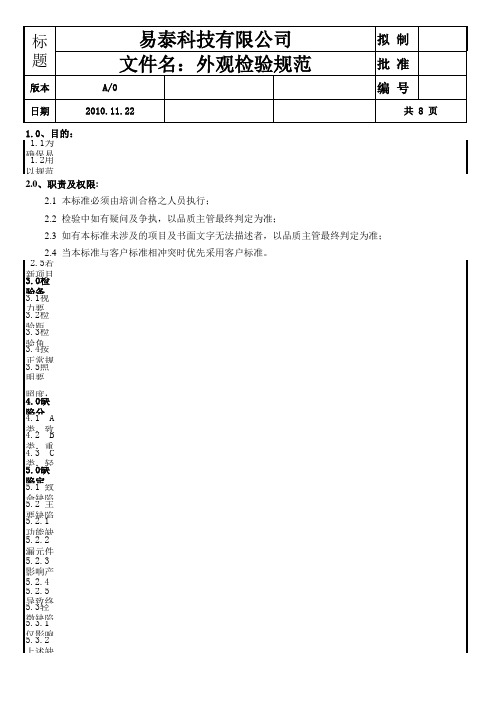
1.0、目的:1.1为确保易泰科技有限公司生产的baby monitor质量符合要求,特制定此检验标准。
1.2用以规范和统一婴儿监视器结构物料检验方案,内容及判定标准。
2.0、职责及权限:2.1 本标准必须由培训合格之人员执行;2.2 检验中如有疑问及争执,以品质主管最终判定为准;2.3 如有本标准未涉及的项目及书面文字无法描述者,以品质主管最终判定为准;2.4 当本标准与客户标准相冲突时优先采用客户标准。
2.5若新项目不断出现或本标准中有未涉及到的内容,应在本标准中加入并进行整理。
3.0检验条件:3.1视力要求:裸视或矫正视力1.0以上3.2检验距离:检验物距眼睛30-35cm3.3检验角度:水平方位45°,上下左右转动15°3.4按正常规定要求的距离和角度要求扫描整个检测面10—15秒钟为准3.5照明要求:在自然光或60W-100W的日光灯照明条件下检验,距离光源:50-55cm处;照度:500-550Lux(勒克斯(照明单位))4.0缺陷分类:4.1 A类,致命缺陷(CRI):AQL=04.2 B类,重要缺陷(MAJ):AQL=0.654.3 C类,轻微缺陷(MIN):AQL=1.05.0缺陷定义:5.1 致命缺陷(Critical Defect):产品存在对使用者的人身及财产安全构成威胁的缺陷。
5.2 主要缺陷(Major Defect)产品存在下列缺陷,为主要缺陷:5.2.1 功能缺陷影响正常使用5.2.2 漏元件·配件或主要标识,多出无关的标识及其他可能影响产品性能的物品5.2.3 影响产品形象的包装缺陷5.2.4 性能参数超出规格标准5.2.5 导致终端客户拒绝购买的结构及外观缺陷5.3轻微缺陷(Minor Defect):不影响产品使用,终端客户可能愿意让步接受的缺陷。
5.3.1 仅影响产品美观感,不影响产品的正常功能使用5.3.2 上述缺陷以外的其它不影响产品使用的缺陷6.0表面定义:6.1 A面:正常使用中,直接观察到的主要外漏表面(正常观察产品的正面)6.2 B面:正常使用中,不直接观察到但外漏次要表面(正常观察产品的上下·左右侧面和背面)6.3 C面:正常使用中,很少见或看不见的面(电池仓·充电器和配件等其它表面)7.0缺陷概念:7.1通常缺陷:1)脏污(Contamination):外来物所致的变色或吸附在零件表面上的异物。
外观检验标准
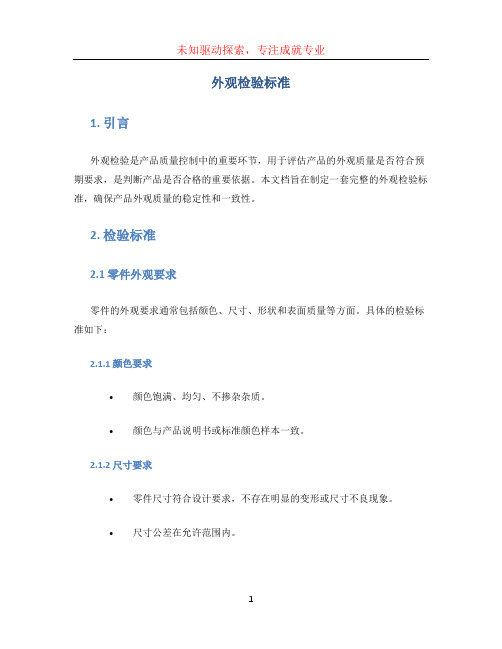
外观检验标准1. 引言外观检验是产品质量控制中的重要环节,用于评估产品的外观质量是否符合预期要求,是判断产品是否合格的重要依据。
本文档旨在制定一套完整的外观检验标准,确保产品外观质量的稳定性和一致性。
2. 检验标准2.1 零件外观要求零件的外观要求通常包括颜色、尺寸、形状和表面质量等方面。
具体的检验标准如下:2.1.1 颜色要求•颜色饱满、均匀、不掺杂杂质。
•颜色与产品说明书或标准颜色样本一致。
2.1.2 尺寸要求•零件尺寸符合设计要求,不存在明显的变形或尺寸不良现象。
•尺寸公差在允许范围内。
2.1.3 形状要求•零件形状无明显破损、变形、断裂等缺陷。
•检查零件边缘的锐利度和倒角是否符合要求。
2.1.4 表面质量要求•表面光滑、平整,无划痕和明显的凹凸。
•无明显的气泡、白点、斑点等缺陷。
2.2 成品外观要求成品外观的检验标准通常依据产品的用途和市场需求来确定。
2.2.1 外观一致性•各组件之间的外观一致性良好,形成整体感。
•产品不应有明显的色差或瑕疵。
2.2.2 标志和标识•产品的标志和标识清晰、完整可辨认。
•标志和标识的位置与规定一致。
2.2.3 表面处理和涂装•表面处理和涂装均匀、平整,无色差和脱落现象。
•涂层的厚度和粘附力符合要求。
3. 检验方法3.1 目视检查目视检查是最常用的检验方法之一,通过肉眼观察来评估产品的外观质量。
目视检查应该在光线充足的环境下进行,避免视觉误差。
3.2 触觉检查触觉检查可以用于评估产品的表面质量。
通过手感来判断产品的光滑度、凹凸等情况。
触觉检查需要注意产品不得有锋利和刺激性的边缘。
3.3 仪器检测仪器检测可以使用一些专业设备和工具,如显微镜、光谱仪、涂层测厚仪等,来进一步评估产品的外观质量。
仪器检测结果更加客观和精确。
4. 结论本文档制定了一套完整的外观检验标准,确保产品外观质量的稳定性和一致性。
在执行外观检验时,应根据具体产品的特点和市场需求,综合运用目视检查、触觉检查和仪器检测等方法,确保产品的外观质量符合要求。
汽车外观检验标准
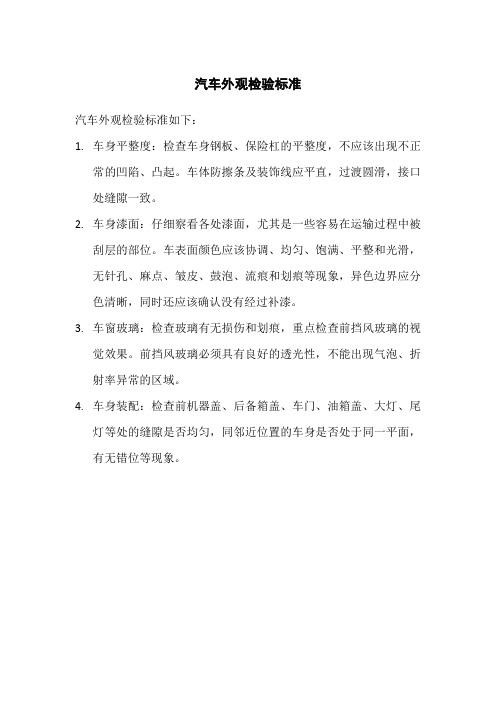
汽车外观检验标准
汽车外观检验标准如下:
1.车身平整度:检查车身钢板、保险杠的平整度,不应该出现不正
常的凹陷、凸起。
车体防擦条及装饰线应平直,过渡圆滑,接口处缝隙一致。
2.车身漆面:仔细察看各处漆面,尤其是一些容易在运输过程中被
刮层的部位。
车表面颜色应该协调、均匀、饱满、平整和光滑,无针孔、麻点、皱皮、鼓泡、流痕和划痕等现象,异色边界应分色清晰,同时还应该确认没有经过补漆。
3.车窗玻璃:检查玻璃有无损伤和划痕,重点检查前挡风玻璃的视
觉效果。
前挡风玻璃必须具有良好的透光性,不能出现气泡、折射率异常的区域。
4.车身装配:检查前机器盖、后备箱盖、车门、油箱盖、大灯、尾
灯等处的缝隙是否均匀,同邻近位置的车身是否处于同一平面,有无错位等现象。
汽车零部件外观检验质量标准和规范标准

汽车零部件外观检验质量标准和规范标准
简介
本文档旨在提供汽车零部件外观检验的质量标准和规范标准,
以确保汽车零部件的质量和外观符合相关要求。
检验对象
所有进入生产线的汽车零部件都应进行外观检验,包括但不限
于以下方面:
- 表面平整度
- 颜色均匀度
- 尺寸和形状的准确性
- 表面缺陷和瑕疵
质量标准
为确保零部件的质量和外观符合要求,以下质量标准应被遵守:
1. 表面平整度:零部件表面应平整,不得有凹凸不平、麻点等
缺陷。
2. 颜色均匀度:零部件的颜色应均匀,不得有明显的色差。
3. 尺寸和形状的准确性:零部件的尺寸和形状应符合设计要求,不得有偏差超过规定范围。
4. 表面缺陷和瑕疵:零部件表面不得有划痕、气泡、氧化等缺陷,不得有明显的色差。
规范标准
为确保检验的一致性和可靠性,以下规范标准应被遵守:
1. 检验员资质:负责进行外观检验的检验员应具备相关的知识
和技能,并经过培训和认证。
2. 检验环境:外观检验应在干燥、清洁、光线充足的环境中进行,以确保有效的观察和判断。
3. 检验工具:使用适当的检验工具,如测量仪器、放大镜等,
以帮助进行准确的外观检验。
4. 检验记录:对每个零部件的外观检验结果进行记录,包括通
过与不通过的判定,并进行必要的数据分析。
总结
本文档提供了汽车零部件外观检验的质量标准和规范标准,以
确保零部件的质量和外观符合要求。
通过严格遵守这些标准,可以
提高汽车零部件的可靠性和合格率,以保障汽车的质量和安全。
- 1、下载文档前请自行甄别文档内容的完整性,平台不提供额外的编辑、内容补充、找答案等附加服务。
- 2、"仅部分预览"的文档,不可在线预览部分如存在完整性等问题,可反馈申请退款(可完整预览的文档不适用该条件!)。
- 3、如文档侵犯您的权益,请联系客服反馈,我们会尽快为您处理(人工客服工作时间:9:00-18:30)。
3.组件板上侧立的片式元件小于或等于2个.
立碑
不可接收图样
立碑----不可接受
错件
不可接收图样
错件----不可接受
多件:
不可接收图样
多件----不可接受
少件:
不可接收图样
少件----不可接受
反白:
1.单片组件板允许有3个晶片电阻或电容反白,但必须同时满足以下2项
a.组件长L≦3mm,宽W≦1.5mm
不可接收图样:
不可接受标准:
末端焊接宽度(C)小于元件直径(W)的50%,小于焊盘宽度(P)的50%。
底部少锡:
D.侧面焊点长度
T.元件可焊端长度
S.焊盘长度
可接受标准:
D≥50% T或D≥50% S
不良图片(暂无)
不可接收标准:
侧面焊点长度(D)小于元件可焊端长度(T)的50%,或小于焊盘宽度(S)的50%。
17
移位
MP (Moving Position)
零件贴片时离幵规定位置
18
连焊
SS (Solder short)
管脚与管脚之间连接在一起,或PCB板上两个pad上的锡连在一起
19
锡尖
ST (Solder Tip)(TombstonePart)
零件一边贴在焊盘上另一边没有焊接形成立起的形状
C.扁平”L”型脚零件
侧面偏移
A:侧面偏移长度
W:零件脚宽
可接受标准:
A≤25% W
理想图样
可接收图样
不可接收图样(A﹥25% W)
趾部偏移:
B.趾部最大偏移
可接受标准:
趾部最大偏移(B)顶端与PCB线路距离等于或大于0.13mm,同时焊锡量达到标准要求
不良图片(暂无)
不可接收标准:
1.趾部最大偏移(B)顶端与PCB线路距离小于0.13mm。
3.任何电阻质的缺口
不可接收图样
F.PCB
平整度:
可接受标准:
1.已贴组件的光板,弓曲和弯曲不应超过长边的0.75%.
2.已完成焊接的板,弓曲和弯曲不应超过长边的1.5%.
3.不影响正常的装配功能
整洁度:
可接收标准:
1.表面干净,清洁(必须采用客户指定的清洗笔进行清洗动作)
2.表面无灰尘、脏污、手指印、锡渣等异物。
E.J型引脚
侧面偏移:
W:引脚宽度
A:侧面偏移宽度
可接收标准:
最大侧面偏移宽度小于或等于50%的引脚宽度
A≤50% W
可接收图样
不可接收图样
底部少锡:
D:侧面焊点长度
可接收标准:
侧面焊点长度大于150%的引脚长度
理想图样
不可接收图样
根部少锡
F:根部焊点高度
T:引脚厚度
G:焊锡高度
可接受标准:
根部焊点高度至少为50%引脚厚度加焊锡厚度
21
侧立
SU (Stand-Up)
零件与实际贴片翻转90度
22
虚焊
US (Unsolder)
零件与焊盘有焊接,但没有焊接牢固
23
错件
WP (Wrong Part)
板子上零件与样品规定不符
24
PAD脱落
PE (PCB Error)
PCB铜泊脱落
25
PCB断裂
PB (PCB Break)
PCB物理断开并露出底材
不可接受标准:
根部焊点高度小于50%引脚厚度加焊锡厚度
多锡:
E:焊锡面
可接受标准:
焊锡面不可接触元件体
不可接受标准:
焊锡面已经接触到元件体
F.I型引脚:
偏移:
A:偏移宽度
W:引脚宽度
可接受标准:
A≤25% W
B:趾部偏移:
不可接收标准:
不允许任何的趾部偏移
焊锡高度:
F:最小焊锡高度
可接收标准:
最小焊锡高度大于等于0.5mm.
不可接收图样
多锡:
E:最高焊点高度
可接受标准:
最高焊点高度E可以超出焊盘或爬升至金属镀层端冒可焊端的顶部,但不可接触元件体。
未接触元件体
可接收图样
已经接触到元件体
不可接收图样
B.柱状元件:
侧面偏移:
A:侧面偏移长度
W:元件端帽的宽度长度
P:PAD的宽度
可接受标准:
A≤25% W或A≤25% P
侧面偏移:
6.1.检验条件
6.1.2.检验工具:光学放大镜(特殊情况下采用显微镜)、Sample、Location、赛规等
6.1.3.检验条件:
A.室内照明600lux以上
B.检验人员必须穿戴好防静电衣/帽/鞋,佩戴测试为好的静电手环。
C.检验工作台面保持干净整洁,静电防护措施检验OK。
6.1.4.检验方法:
不可接收图样:
不可接收标准:
侧面偏移长度﹥25%元件可焊端直径
或﹥25%焊盘宽度
末端偏移:
B:末端偏移长度
可接受标准:
末端偏移(B)未偏移出焊盘
不可接收图样:
不可接收标准:
任何末端偏移(B)偏移出焊盘
末端少锡:
C.末端焊接宽度
W.元件直径
P.焊盘宽度
可接受标准:
C≥50% W或C≥50% P
末端少锡:
零件没有平贴在板子表面
6
外来异物
FM (Foreign Material)
零件底部或PCB上有不明物
7
反白
FP (Flip Part)
零件与实际贴片翻转180度背面朝上
8
金手指沾锡
GF (Gold Finger)
板子上金手指部位有锡膏
9
少锡
IS (Insufficient Solder)
焊点上的焊料量低于最少需求量,会造成焊点虚焊
B.严重缺陷(MAJ):指不能达成制品使用目的或显着降低其实用性的不合格点,以及客户要求的其它非性能不良的不合格点。
C.次要缺陷(MIN):指生产之制品在使用或操作上并无明显影响,不至于引起客户投诉的缺陷。
6.2.SMT外观检验标准
6.2.1.SMT常见外观缺陷名词解释
见下表
序号
缺陷中文名称
缺陷英文缩写
26
PCB烘焦
PO(PCB Overheated)
表面严重受热而引起的PCB烧焦
27
线路短路
PCS (PCB Circuit Short)
PCB内部线路短路
28
管脚弯曲
BP (BendPin)
零件管角表面不平整,导致不良
29
组件功能失效
CD (Component defect)
材料失效,外观正常
30
不可接触到元件体
D:最小侧面焊锡长度
可接收标准:
最小侧面焊锡长度不做尺寸要求
不可接触到元件体
但必须考虑到元器件的功能和实用性
G.其它缺陷
浮高
晶片状零件不允许浮高
可接收标准:
1.最大浮起高度是引线厚度﹝T﹞的两倍.
2.本体浮高需符合以下条件:
a.引线基本平贴(≦1.5T)
b.本体焊接面积≧1/3 PAD
A.检验人员需坐姿端正,确保与检查的零件保持20cm-30cm的距离。
B.从PCBA表面450角开始检验,左右移动PCBA,目光顺着移动的方向逐步检验,若遇到IC类或其它具有多方位焊脚的元器件,则转动PCBA从各角度进行检验。
6.1.4.缺陷等级
A.致命缺陷(CR):是指缺陷影响程度足以造成人体或机器产生伤害或危及生命财产安全。
侧面少锡:
F:焊点高度
G:焊锡高度
W:元件端冒直径
可接受标准:
最小焊点高度(F)正常润湿。
不可接收图样
不可接受标准:
最小焊点高度(F)未正常润湿。
多锡
E:焊锡的最大高度
可接受标准:
最高焊点高度(E)可以超出焊盘或爬升至金属镀层端冒可焊端的顶部,但不可接触元件体。
不可接收图样:
不可接收标准:
最高焊点高度(E)接触到元件本体。
组件损坏
DP (Damaged Part)
零件本体某一部位缺损
31
误测
NTF (No Test Fail)
未经过任何动作,重测该站PASS
32
待分析
TBA (To BE Analysis)
未分析
6.2.2.图示范例
TOP面
BOTTOM面
6.2.3.外观检验项目及判定标准
A.片状零件
侧面偏移:
A:侧面偏移长度
c.不影响结构和功能
锡珠
不可接收图样
不可接收标准:
1.锡珠/飞溅分布在焊盘或印制线条周围0.10mm范围内
2.锡珠直径大于0.13mm.
3.每片PWB板超过2个锡珠
4.任何造成短路的锡珠.
5.三倍以内放大镜与目视可见之锡渣,不可接受.
侧立
不可接收图样
可接受标准:
需同时满足以下3项:
1.侧立元件长L<=3mm,宽W<=1.5mm.
3.不允许有助焊剂和清洗液擦拭后的残留物。
不可接收图样(锡渣)
不可接收图样(清洗液残留物)
不可接收图样(灰尘/脏污)
PCB其它项
序号
缺陷描述
ACC
MIN
MAJ
CR
1
PCB表面刮伤深至露铜。
●
2
PCB表面划伤只涉及到表面绿油,但有明显的痕迹,深度小于或等于0.25mm,且长度不超过2-3cm。
●
3
PCB表面只是轻微刮花,不具备深度,透过灯光反照才能看到。