机电控制系统
机电控制系统
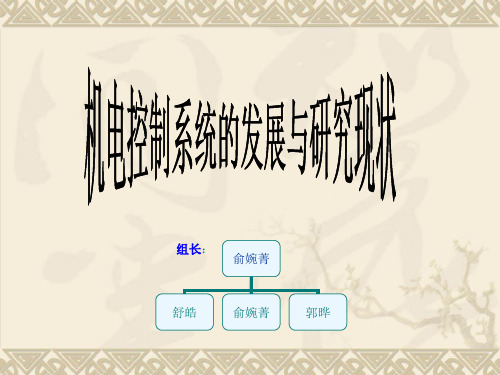
技术发展趋势
国外自上世纪60年代出现第一台工业过程控制系统以来已经过三代产 品的发展变化,随着计算机技术及产品的发展,工业控制系统亦相应地
不断发展。
➢半导体技术集成电路技术推动微处理器、微控制器的发展。 ➢分布式控制系统已推出第四代产品,如Honeywell 公司新推出的 Expersion PKS(过程知识系统),Emerson公司的A2,横河公司 的R3(PRM-工厂资源管理系统),ABB公司的Industrial IT系统。 ➢计算机技术、通信技术、控制技术的发展,使控制系统向全数 字化、全分散式、全开放可互操作和开放式互联网络的新一代现 场总线控制系统(FCS)发展。 ➢PLC技术20世纪80年代走向成熟。 ➢自动控制理论及技术的发展,先进控制、模糊控制、人工神经 网络、人工智能技术和专家系统已在工业自动化中实际应用。
❖ 富士通法纳克公司:“将 机械学和电子学有机结合 而提供的更为优越的技
术。”
工业机械手臂
机电控制技术在机械制造业中的应用,大致经历了参数数显、硬 件数控(NC控制)、计算机数控(CNC控制)、柔性生产系统 (FMS)、计算机集成制造系统(CIMS)、虚拟制造系统(VMS) 等过程,使加工制造技术与生产经营模式紧密结合,形成现代制 造技术和系统。
输入量
比较元件 串联补件
驱动元件
局部反馈
并联补偿元件
执行元件
被控对象 输出量
主反馈
测量元件
”代表比较元件,它将测量元件检测到的被控量与输入量进行比 较;“-”号表示两者符号相反,即负反馈;“+”号表示两者符号相 同,即正反馈。
二,机电控制系统的发展史
机电控制系统的发展按所用控制器件来划分,它主要经历了四个阶段:
机电控制系统自动控制技术与一体化设计

机电控制系统自动控制技术与一体化设计
机电控制系统自动控制技术与一体化设计是指将机械装置和电子控制系统相结合,实
现自动化控制的一种技术和设计方法。
这种技术和设计方法的目的是提高生产效率、降低
人力成本、优化产品品质,并保证操作的安全性。
机电控制系统自动控制技术主要包括传感器技术、信号处理技术、运动控制技术和智
能控制技术等方面。
传感器技术是机电控制系统的基础,它可以将机械装置的物理量转化
为电信号,并输入给控制系统。
信号处理技术是对传感器输出的信号进行处理和分析,以
获得有用的信号信息。
运动控制技术是实现机械装置运动控制的核心技术,它可以控制机
械装置的位置、速度和加速度等参数。
智能控制技术是利用人工智能和专家系统等方法,
对机电控制系统进行智能化控制和优化设计。
机电控制系统一体化设计是将机械装置和电子控制系统的设计过程进行整合,以实现
系统设计的整体性和协调性。
在这种设计方法中,机械装置和电子控制系统的设计可以同
步进行,并在设计过程中进行多个层面的交互。
通过一体化设计,可以提高设计效率和质量,降低系统的成本和风险。
机电控制系统自动控制技术与一体化设计在各个领域都有广泛的应用。
在工业生产中,可以利用这种技术和设计方法实现生产线的自动化控制和优化;在交通运输领域,可以利
用这种技术和设计方法实现车辆的自动驾驶和智能交通管理;在医疗领域,可以利用这种
技术和设计方法实现医疗装置的自动化控制和治疗过程的优化。
机电控制系统自动控制技术与一体化设计

机电控制系统自动控制技术与一体化设计机电控制系统是一种涵盖机械、电子、信息技术的综合性技术体系。
其主要功能是将机械、电子和信息技术有机结合,实现机械设备的高效稳定工作。
随着科技的不断进步,机电控制系统自动化技术不断更新,而一体化设计成为其中的重要组成部分。
一体化设计指的是在机电控制系统设计中同时考虑机械、电气和信息技术三个方面,使其成为一个统一的系统。
一体化设计可以提高机电控制系统的安全性、可靠性、稳定性和维护性。
因此,在机电控制系统的设计中,一体化设计已成为不可或缺的一环。
一体化设计的实现需要涉及到多个方面,例如在机械设计中考虑机电一体化的要求,制定机电一体化的设计方案,把机械、电气、信息模块优化整合,最终完成整体的机电控制系统设计。
在实际应用中,一体化设计需要在各个方面进行统筹考虑,在满足机械性能的前提下,设计出电气和信息方面的配套控制系统。
机电控制系统的自动控制技术是实现一体化设计的重要手段之一。
自动化技术的应用可以提高机电控制系统的工作效率,减少人为干预,从而提高机械设备的稳定性和可靠性。
机电自动控制技术可以实现多个设备之间的协同工作,使整个机电控制系统具有高度自动化、高效性和稳定性。
在机电自动控制技术应用中,需采用各种传感器、执行器等,将物理量通过电气信号进行传输,再进行处理和控制,从而实现机械设备的自动化控制。
例如,在机械运动控制中,可以通过使用步进电机控制器实现精确控制线性和旋转运动;在流程控制中,可通过采用PLC程序控制器等设备实现系统流程的自动控制和管理。
机电控制系统自动控制技术和一体化设计的结合可以极大地提高机械设备的生产效率和稳定性,实现设备的高效运行和维护。
此外,机电一体化设计同时还能降低机械设备的生产成本和维护成本,提高企业的经济效益,具有非常重要的应用前景。
总之,机电控制系统自动控制技术和一体化设计是目前机械设备制造行业发展的重要趋势,这种技术在机械设备控制系统中的应用已经越来越广泛,是机械设备制造企业不可或缺的重要手段。
机电控制系统课程设计

设计任务书的内容与要求
设计任务:完成机电控制系统的设计,包括硬件和软件部分 设计要求:满足功能需求,保证稳定性和可靠性,易于维护和升级 设计内容:包括系统架构、硬件选型、软件设计、测试和调试等 设计时间:根据课程安排,制定合理的设计周期,确保按时完成设计任务
设计报告的撰写要求
语言要求:使用专业术语, 语言简洁明了,逻辑清晰
机电控制系统的分类
按照控制方式分类:开环控制、闭环控制、半闭环控制
按照控制对象分类:机械系统、电气系统、液压系统、气动系统
按照控制功能分类:速度控制、位置控制、力控制、压力控制、流量控制
按照控制结构分类:单回路控制、多回路控制、串级控制、比值控制、前馈控制、 自适应控制、模糊控制、神经网络控制、专家系统控制等。
格式要求:采用统一的格式, 如Word、PDF等
报告内容:包括设计目的、设 计思路、设计方案、设计结果、 设计总结等
字数要求:根据课程要求, 一般在3000字左右
图表要求:适当使用图表, 使报告更加直观易懂
参考文献:列出参考文献, 注明出处,尊重知识产权
感谢您的观看
汇报人:
机电控制系统设 计的基本原则与 步骤
设计的基本原则
安全性原则:确保系统安全可靠,避免 故障和事故
经济性原则:考虑成本效益,降低系统 成本
可靠性原则:保证系统稳定运行,减少 故障和维修
灵活性原则:适应不同环境和需求,易 于扩展和升级
环保性原则:减少能源消耗和污染排放, 保护环境
美观性原则:注重外观设计,提高用户 体验和满意度
智能家居控制系统
智能照明系统:根据环境光线 自动调节亮度
智能安防系统:实时监控家庭 安全,报警提醒
智能家电控制系统:远程控制 家电,节能环保
机电控制系统
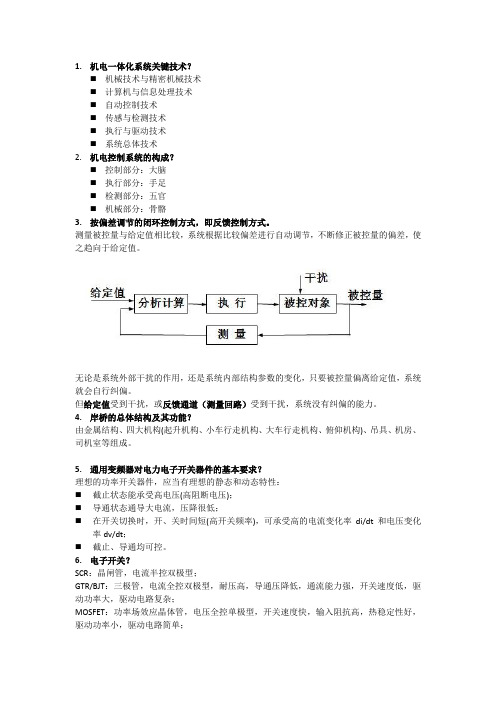
1.机电一体化系统关键技术?⏹机械技术与精密机械技术⏹计算机与信息处理技术⏹自动控制技术⏹传感与检测技术⏹执行与驱动技术⏹系统总体技术2.机电控制系统的构成?⏹控制部分:大脑⏹执行部分:手足⏹检测部分:五官⏹机械部分:骨骼3.按偏差调节的闭环控制方式,即反馈控制方式。
测量被控量与给定值相比较,系统根据比较偏差进行自动调节,不断修正被控量的偏差,使之趋向于给定值。
无论是系统外部干扰的作用,还是系统内部结构参数的变化,只要被控量偏离给定值,系统就会自行纠偏。
但给定值受到干扰,或反馈通道(测量回路)受到干扰,系统没有纠偏的能力。
4.岸桥的总体结构及其功能?由金属结构、四大机构(起升机构、小车行走机构、大车行走机构、俯仰机构)、吊具、机房、司机室等组成。
5.通用变频器对电力电子开关器件的基本要求?理想的功率开关器件,应当有理想的静态和动态特性:⏹截止状态能承受高电压(高阻断电压);⏹导通状态通导大电流,压降很低;⏹在开关切换时,开、关时间短(高开关频率),可承受高的电流变化率di/dt和电压变化率dv/dt;⏹截止、导通均可控。
6.电子开关?SCR:晶闸管,电流半控双极型;GTR/BJT:三极管,电流全控双极型,耐压高,导通压降低,通流能力强,开关速度低,驱动功率大,驱动电路复杂;MOSFET:功率场效应晶体管,电压全控单极型,开关速度快,输入阻抗高,热稳定性好,驱动功率小,驱动电路简单;IGBT:绝缘栅晶体管,电压全控复合型,耐压高,导通压降低,开关速度快,大功率,低驱动,高频化。
7.电压全控混合型器件—智能功率模块IPMIPM(Intelligent Power Module)是将主开关器件、续流二极管、驱动电路、电流、电压、温度检测组件及保护电路、接口电路等集成在同一封装体内,形成的功率集成电路。
控制功能,保护功能,接口功能8.电力二极管,IGBT动态特性图P25 P379.电力电子器件的开关频率越低,其开通时间或关断时间越短。
机电控制系统实验报告

一、实验目的1. 理解机电控制系统的基本原理和组成;2. 掌握机电控制系统的调试方法;3. 熟悉常用控制元件的性能和特点;4. 提高动手能力和分析问题、解决问题的能力。
二、实验原理机电控制系统是指由电动机、执行机构、控制器、传感器等组成的,用于实现特定运动或控制功能的系统。
本实验主要研究步进电机驱动系统,通过控制步进电机的旋转角度和速度,实现机械装置的运动控制。
三、实验内容1. 步进电机驱动系统原理研究2. 步进电机驱动电路设计3. 步进电机驱动系统调试四、实验步骤1. 步进电机驱动系统原理研究(1)了解步进电机的工作原理和驱动方式;(2)分析步进电机驱动电路的基本组成和功能;(3)掌握步进电机驱动电路的调试方法。
2. 步进电机驱动电路设计(1)根据步进电机的参数(如相数、步距角等)选择合适的驱动电路;(2)设计步进电机驱动电路的硬件电路,包括驱动芯片、驱动模块、电源电路等;(3)绘制电路原理图和PCB布线图。
3. 步进电机驱动系统调试(1)搭建实验平台,包括步进电机、驱动电路、控制器、传感器等;(2)编写控制程序,实现步进电机的正转、反转、定位等功能;(3)调试系统,观察步进电机的运行状态,调整参数,使系统达到预期效果。
五、实验结果与分析1. 步进电机驱动系统原理研究通过学习,掌握了步进电机的工作原理和驱动方式,了解了步进电机驱动电路的基本组成和功能。
2. 步进电机驱动电路设计根据步进电机的参数,选择了合适的驱动电路,并完成了电路原理图和PCB布线图的绘制。
3. 步进电机驱动系统调试搭建了实验平台,编写了控制程序,实现了步进电机的正转、反转、定位等功能。
调试过程中,观察了步进电机的运行状态,调整了参数,使系统达到预期效果。
六、实验总结1. 通过本次实验,加深了对机电控制系统原理的理解,掌握了步进电机驱动系统的设计方法;2. 提高了动手能力和分析问题、解决问题的能力;3. 了解了常用控制元件的性能和特点,为今后从事相关领域工作奠定了基础。
机电控制工程基础课件:机电控制系统应用举例
机电控制系统应用举例
图 9-7 水位自动控制的自动调节过程
机电控制系统应用举例
9. 3 发动机离心调速系统
9. 3. 1 液压阀控液压缸和液压阻尼器 1. 液压阀控液压缸 液压阀控油缸(又称液压伺服阀)是液压伺服系统中常用
的一种执行元件。其结构原理图如图 9-8 所示。它实际上 是一个控制滑阀和一个动力液压缸的组合。
机电控制系统应用举例
1. 系统组成 1 )交流伺服电机 图中的被控对象是交流伺服电动机 SM , A 为励磁绕组, 为使励磁电流与控制电流互差 90° 电角,励磁回路中串接了 电容 C1 ,它通过变压器 T 1 产生的交流电源供电。 B 为控制 绕组,它通过变压器 T 2 经交流调压电路接于同一交流电源。 供电的电源为 115V 、 400Hz交流电源。系统的被控量为角 位移 θ 0 。
机电控制系统应用举例 2. 系统方块图 综上所述,可得如图 9-2 所示的位置随动系统的方框图。
图 9-2 位置随动系统方框图
机电控制系统应用举例
3. 工作原理 在稳态时, θo = θ i , Δ U =0 , U k 1 = U k 2 =0 , VT 正 与 VT 反 均关断, U s =0 ,电机停转。当位置给定信号 θi 改变,设 θ i 增大,则 U θ i = kθ i ,偏差电压 Δ U ( = U θ i - Ufθ) >0 ,此信号电 压经 PID 调节器 A 1 和放大器 A 2 后产生的 U k 1 >0 ,使正组 触发电路发出触发脉冲,双向晶闸管 VT 正 导通,使电动机正 转, θ o 增大。这个调节过程一直继续到 θ o = θi ,到达新的稳 态,此时 Ufθ= U θ i , Δ U =0 , U k 1 =0 , VT 正 关断,电机停转。 如图 9-3 ( a )所示。
机电一体控制系统设计及控制技术
5.3.1 PLC特点与应用
1.PLC控制特点 ① 可靠性高,抗干扰能力强。 ② 功能强,配置灵活。 ③ 编程简单,易学易用。 ④ 系统设计与维护方便。 ⑤ 体积小、重量轻、能耗低。
24
5.3.1 PLC特点与应用
2.PLC应用
①开关量控制:开关量控制是PLC控制器最基本、最广泛的应用,它取 代传统的继电器电路,实现逻辑控制、顺序控制。 ②模拟量控制:为了使PLC处理模拟量,必须要进行模拟量和数字量之 间的A/D转换及D/A转换。 ③运动控制:PLC可以用于旋转运动或直线运动控制。 ④过程控制:过程控制是指对温度、压力、流量等模拟量的闭环控制。
25
5.3.2 典型PLC介绍
1.三菱PLC
(1)三菱PLC概述 三菱PLC分为F系列、Q系列、IQ-F系列,IQ-R系列、L系列、
QS/WS系列等,不同系列PLC在CPU运算速度、输入/输出类型与规模 、控制功能、通讯功能、安全功能等方面配置不同,适用于不同的控制 需求。
26
5.3.2 典型PLC介绍
9
运行员 操作站
管理 计算机
运行员 操作站
管理 计算机
运行员 操作站
工程师 操作站
商用网络
计算 工作站
系统网络
经营 管理级
过程 管理级
通讯 接口
过程控制站
通讯
接口
过程控制站
基 本基 本 控制单元 控制单元
基本 控制单元
基 本基 本 控制单元 控制单元
基本 控制单元
数据输入 输出单元
通讯 接口
数据采集站
11
操作站
操作站
电源
耦合器
耦合器
电源
商用网络
机电控制系统的基本组成结构
机电控制系统的基本组成结构
*机电掌握是讨论如何设计掌握器并合理选择或设计放大元件、执行元件、检测与转换元件、导向与支承元件和传动机构等,并由此组成机电掌握系统使机电设备达到所要求的性能的一门科学,在机电一体化技术中占有特别重要的地位。
机电掌握系统是机电一体化产品及系统中担当着掌握对象输出,并根据指令规定的规律变化的功能单元,是机电一体化产品及系统的重要组成部分。
机电掌握系统是一种自动掌握系统。
*机电掌握系统一般由指令元件,比较、综合与放大元件,转换与功率放大元件、执行元件、工作机构、检测与转换元件等6部分组成。
机电掌握系统的工作原理是:有指令元件发出指令,通过比较、综合与放大元件将此信号与输出反馈信号比较,再将差值进行处理和放大、掌握及转换,将此处理后的信号加到功率放大元件并施加到执行元件的输入信号,使得执行元件按指令的要求运动;而执行元件往往和机电装备的工作机构相连接,从而使机电装备的被控量(如位移、速度、力、转矩等)符合所要求的规律。
1。
机电一体化控制系统组成及作用
控制系统
控制系统由数字控制装置、输入输出装置,输入输出接口及功率放大电路、变频等部件组成其作用为:
(1)数字控制装置
作用:程序译码执行;状态信号输入采集处理,产生输出控制信号和状态显示信息。
(2)输入装置
作用:接受现场状态信息和操作命令,(专为可识别的信息格式)
(3)输出装置(输出设备)
作用:接受来自数字控制装置的控制命令,转化并执行相应命令信息,产生调解、改变系统工作状态的操作和动作。
(4)输入输出接口
作用:连接数字控制装置和输入输出设备的信息桥梁,完成I/O信号的电平转换,隔离,信号方式转换,滤波,锁存和缓冲等功能
(5)功率放大电路。
作用:将输出接口的输出控制信号进行功率放大,以足够的功率驱动输出执行设备(输出装置),完成系统的运行。
- 1、下载文档前请自行甄别文档内容的完整性,平台不提供额外的编辑、内容补充、找答案等附加服务。
- 2、"仅部分预览"的文档,不可在线预览部分如存在完整性等问题,可反馈申请退款(可完整预览的文档不适用该条件!)。
- 3、如文档侵犯您的权益,请联系客服反馈,我们会尽快为您处理(人工客服工作时间:9:00-18:30)。
1.铣床主要结构及运动情况
1)主要结构
铣床主要由底座、床身、悬梁、刀杆支架、升降台、工作台和溜板等部分组成,如图所示。
2)运动情况
主运动:主轴带动铣刀的旋转。
主运动分顺铣和逆铣两种形式
进给运动:是工件在工作台上实现三个相互垂直方向的进给,即工作台沿溜板上部回转台的导轨在垂直于主轴轴线方向的纵向进给,溜板沿升降台上的水平导轨在平行于主轴轴线方向的横向进给,以及升降台沿床身的垂直导轨作上下垂直进给。
辅助运动:可转动部分对溜板可绕垂直轴线转动一个角度(一般为45o),因此工作台除能实现平行或垂直于主轴方向的横向或纵向进给外,还能在倾斜方向上进给,从而可进行螺纹的加工。
铣床一般还配有圆工作台,以扩大其加工范围。
辅助运动有工作台在纵向、横向、垂直方向上的快速移动。
2.铣床对电力拖动与控制的要求
1)铣床要求主轴能够调速,且在各种铣削速度下保持恒功率。
因此,主轴电动机采用笼形异步电动机,经齿轮变速箱拖动主轴。
2)为实现顺铣和逆铣加工,要求主轴正反转,但在铣削加工过程中旋转方向不需变换,而是加工前预选主轴转动的方向。
3)铣刀是一种多刃刀具,其切削过程是断续的,为了减小负载波动的影响,往往在主轴上装有飞轮增加惯性,这样主轴电动机由于惯性大使停车时间变长。
为了能快速停车,提高生产效率,主轴采用制动停车方式。
铣床中常用反接制动或电磁离合器制动。
4)为使主轴变速箱内齿轮易于啮合,要求主轴电动在主轴变速时能产生变速冲动。
5)工作台的进给运动、快速移动以及圆工作台工作由同一台进给电动机拖动。
由于进给运
动和快速移动在三个方向上都是往复式的,因此要求进给电动机正反转。
进给运动和快速移动是通过牵引电磁铁来换接传动链得以实现。
6)工作台进给运动与圆工作台旋转运动不能同时进行。
工作台左、右、上、下、前、后六个方向的进给运动在同一时刻只允许一个方向进行
7)工作台的进给运动需要变速,进给变速也是由机械齿轮变速箱来实现,变速时为了便于齿轮啮合,也要有变速冲动环节。
8)应保证主轴起动后,工作台方可进给;主轴停止,工作台也要停止进给,以免造成刀具和工件损坏。
但主轴不转时,允许工件快速移动到加工位置。
9)为了实现工件和刀具的冷却,需要一台冷却泵电动机。
10)应具有必要的保护、联锁及照明电路。
3.X62W卧式升降台铣床控制线路分析
图中M1为主轴电动机、M2为进给电动机、M3为冷却泵电动机
1)主轴的控制
主轴电动机起动与停止
主轴电动机M1由接触器KM1控制,其旋转方向(顺铣或逆铣)由转换开关SA5预先选择。
KM2为反接制动用接触器,R为反接制动电阻。
起动主轴时,先将电源开关Q合上,再将转换开关SA5转到主轴所需的旋转方向,然后按下起动按钮SB1或SB2(两地控制),KM1得电并自锁,主轴电动机M1起动。
当M1转速大于速度继电器KS的吸合值时,KS常开触点闭合,为接通反接制动回路作准备。
停止主轴时,按停止按钮SB3或SB4,使KM1线圈断电,切断主轴电动机M1的三相电源,由于此时KS常开触点是闭合的,所以KM得电,实现反接制动。
当M1的转速下降到KS的释放值(接近于0)时,KS常开触点断开,制动结束。
由于没有自锁回路,在制动过程中SB3或SB4要一直按住。
1)主轴的控制
主轴变速冲动
主轴变速机构如图所示
2)工作台的控制
进给运动的控制
工作台的纵向、横向及垂直方向进给由两个操纵手柄来控制,一个是纵向操纵手柄,一个是横向及垂直方向操纵手柄。
纵向操纵手柄通过联动机构控制行程开关SQ1和SQ2,分别控制工作台向右和向左进给运动;横向及垂直方向操纵手柄通过联动机构控制行程开关SQ3和SQ4,SQ3控制工作台向前或向下运动,SQ4控制工作台向后或向上运动。
要进行工作台纵向、横向及垂直方向的进给,SA1应选择在触点SA1-1通、SA1-2断、SA1-3通的位置,同时KM1应得电,触点KM1(11-12)接通
进给运动的控制(工作台纵向进给运动)
例:当纵向操纵手柄扳到“右”位置时,挂上纵向传动链,同时SQ1被压合,其常开触点(18—19)接通、常闭触点(25—17)断开,此时控制回路3—5—10—11—12—15—16—17—18—19—20—21—14—9—PE接通,接触器KM3得电,进给电动机M2的正转,通过纵向传动链拖动工作台向右进给运动。
若将操纵手柄扳到“中间”位置,SQ1、SQ2复位,KM3、KM4都不得电,工作台停止右或左方向的进给运动。
应注意,当纵向操纵手柄扳到“右”或“左”时,横向及垂直方向操纵手柄应处于“中间”位置(即SQ3、SQ4复位)。
2)工作台的控制
工作台快速移动的控制
铣床工作台除能实现进给运动外,还可以实现六个方向上的快速移动。
工作台的快速移动是
通过进给操纵手柄配合快速移动按钮SB5或SB6进行操作。
将进给操纵手柄扳到需要快速移动方向对应的进给位置上,工作台开始进给,然后按下快速移动按钮SB5或SB6,KM5得电,接通快速铁磁铁YA,工作台按选定的方向作快速移动。
放开SB5(SB6)时,快速移动停止,工作台仍在选定的方向上进给。
2)工作台的控制
圆工作台的控制
圆工作台是铣床的一个附件。
它可以手动回转,也可通过工作台的光杆由进给电动机M2经传动机构驱动。
使用时先将圆工作台转换开关SA1扳到接通位置(即SA1-1断、SA1-2通、SA1-3断),然后按下起动按钮SB1(SB2),KM1、KM3得电,接通主轴和进给电动,圆工作台开始工作。
KM3线圈得电的工作电路是:由控制电源经3—5—10—11—12—15—16—17—25—22—19—20—21—14—9—PE。
在使用圆工作台时,不能进行其它进给运动
2)工作台的控制
进给变速冲动
需要改变进给速度,先将蘑菇形进给变速手柄拉出并转动变速盘至需要的速度档,在推回变速手柄时,先将手柄向后拉一下,使行程开关SQ6瞬时压合,接通KM3,则进给电动机作瞬时转动(即变速冲动),便于齿轮啮合。
KM3得电的工作电路是:由控制电源经3—5—10—11—12—22—25—17—16—15—19—20—21—14—9—PE。
进给变速时不允许工作台作任何方向的进给。
3)冷却泵的控制及照明电路
冷却泵电动机M3由转换开关SA3控制。
当转换开关SA3扳到“接通”位置时,SA3(3—4)通,KM6得电,M3起动旋转,拖动冷却泵开始工作。
机床照明由变压器T2供电,电压为24V。
由开关SA4控制照明灯EL的通断。
4)电路的联锁与保护
联锁环节
主运动与进给运动的顺序联锁
进给运动的电气控制线路接在主轴电动机起动接触器KM1触点(11—12)之后。
这就保证了在主轴电动机起动后,方可进行进给运动,主轴电动机停止,进给运动立即停止。
工作台六个方向进给的互锁
工作台左、右、前、后、上、下六个方向进给运动由两套操纵手柄控制,使左和右不能同时进给,前、后、上、下也不能同进给,但纵向(左、右)和横向及垂直方向(前、后、上、下)还可能同时操作。
为保证加工时只允许一个方向的进给,因此又在电路上采用了互锁,即工作台实现左或右进给的工作电路经过控制前、后、上、下进给的行程开关SQ3、SQ4的常闭触点;而工作台实现前、后、上、下方向进给的工作电路经过控制右、左的行程开关SQ1、SQ2的常闭触点
4)电路的联锁与保护
联锁环节
圆工作台与六个方向进给的互锁
圆工作台工作时,不允许作六个中的任一方向进给。
电路中除了SA1开关联锁外,还使圆工作台的工作电路经过SQ1、SQ2、SQ3、SQ4的常闭触点来实现互锁。
进给变速与工作台工作的互锁
进给变速冲动的工作电路经过SA1-3(12—22)触点(即圆工作台不工作)和SQ1、SQ2、SQ3、SQ4四个常闭触点(即工作台六个方向均无进给),从而保证了进给变速时不允许工作台作任一方向进给,也不允许圆工作台工作
4)电路的联锁与保护
保护环节
短路保护
主电路、控制电路、照明电路都有熔断器起短路保护。
过载保护
主轴电动机、进给电动机、冷却泵电动机分别由热继电器FR1、FR2、FR3实现过载保护。
为了确保刀具与工件的安全,要求主轴电动机、冷却泵电动机过载时,除本电动机停止外进给电动机也应停止,因此FR1、FR3的触点串在PE—14之间;当进给电动机过载时,只要进给电动机停止,因此FR2的触点(14—21)只串接在进给支路中。
限位保护
工作台六个方向进给运动的终端限位保护是由各自的限位挡铁来碰撞对应的操纵手柄,使手柄返回中间位置,以停止进给运动。