常规型游梁抽油机传动装置设计
游梁式抽油机的设计.

绪论CYJY12-4.8-73HB型抽油机设计1 绪论1.1抽油机的应用油田开采原油的方法分为两类:一类是利用地层本身的能量来举升原油,称为自喷采油法,常见于新开发且储量大的一些油田;另一类是到了油田开发的中后期,地层本身能量不足以使原油产生自喷,必须人为地利用机械设备将原油举升到地面,称为人工举升采油法或机械采油法[1]。
上述采油方法中不利用抽油杆传递能量的抽油设备统称为无杆抽油设备,利用抽油杆上下往复进行驱动的抽油设备统称为有杆抽油设备。
利用抽油杆旋转运动驱动井下单螺旋泵装置,虽然也有抽油杆,但习惯上不列入有杆抽油设备[3]。
有杆泵采油技术是应用最早也最为广泛的一种人工举升机械采油方法。
有杆抽油系统主要有三部分组成:一是地面驱动设备即抽油机,它由电动机、减速器和四连杆机构(包括曲柄、连杆和游梁)等组成:二是井下的抽油泵(包括吸入阀、泵筒、柱塞和排出阀等),安装于油管的下端:三是抽油杆,它把地面驱动设备的运动和动力传给井下抽油泵。
抽油机是一种把原动机的连续圆周运动变成往复自线运动,通过抽油杆带动抽油泵进行抽油的机械设备。
游梁式抽油机是机械采油设备中问世最早的抽油机机种,1919年美国就开始批量生产这种抽油机。
目前我国大多数油田己相继进入了开发的中后期,油井逐渐丧失自喷能力,基本上己从自喷转入机采。
80年代初,我国拥有机采油井2万口,占总油井数的57.3%,机采原油产量占总产量的27 %,2000年我国油气田共有抽油机采油井约8万口,占油田总井数的90%。
在这些机采油井中,采用抽油机有杆式抽油的占90%,采用电潜泵、水力活塞泵、射流泵、气举等其它无杆式抽油的只占10%。
近几年,随着稳油控水和节能的要求不断提高,各种型式的节能型抽油机和长冲程抽油机的数量不断增加。
由此可见,抽油机在各油田的生产中有着举足轻重的地位,并且随着油田的进一步开发,各种新型节能抽油机将会得到广泛地推广和应用。
1.2 国内外抽油机的发展概况CYJY12-4.8-73HB型抽油机设计1.2.1国外抽油机的发展概况在国外,研究开发与应用抽油机已有100多年的历史[4]。
常规游梁式抽油机主要结构参数的优化设计

常规游梁式抽油机主要结构参数的优化设计常规游梁式抽油机是一种常用的输油装置,其主要结构参数的优化设计可以对其性能进行改进,提高其运行效率和可靠性。
本文将对常规游梁式抽油机主要结构参数进行优化设计,包括游梁长度、游梁截面形状和抽油杆直径等。
首先,游梁长度是常规游梁式抽油机中一个重要的结构参数。
游梁长度直接影响到抽油杆的行程和往复运动次数,在保证充分抽油的同时,要尽量减少杆件的磨损和能耗。
根据实际工况和抽油需求,可以通过模型计算和实验测试,得到最优的游梁长度。
一般而言,游梁长度应尽量适当,既能确保抽油杆的行程充分,又能减少抽油过程中的能耗和磨损。
其次,游梁截面形状也是常规游梁式抽油机的一个关键参数。
游梁截面形状直接影响到游梁的刚度和强度,进而影响到整个抽油机的运行性能。
对于游梁截面形状的优化设计,一方面可以通过有限元分析和疲劳试验来确定合适的截面形状,避免应力集中和疲劳破坏;另一方面,可以通过几何优化设计和材料选择,来改善结构的刚度和强度,提高抽油机的运行效率和寿命。
最后,抽油杆直径也是常规游梁式抽油机中一个重要的结构参数。
抽油杆直径直接影响到抽油杆的刚度和强度,进而影响到整个抽油机的运行效率和可靠性。
抽油杆直径的优化设计需要综合考虑抽油机的工作负荷、抽油深度和运行速度等因素。
一般而言,抽油杆直径应尽量适当,既能满足抽油机的工作需求,又能保证抽油杆的强度和刚度,避免因直径过大或过小而导致的过度磨损或破坏。
综上所述,常规游梁式抽油机的主要结构参数优化设计包括游梁长度、游梁截面形状和抽油杆直径等方面。
通过合理的优化设计,可以提高抽油机的运行效率和可靠性,减少能耗和材料磨损,延长抽油机的使用寿命。
优化设计要综合考虑抽油机的工作条件、工作负荷和运行速度等因素,采用合适的分析方法和试验手段,确保设计参数的准确性和可靠性。
毕业设计常规游梁式抽油机设计

毕业设计常规游梁式抽油机设计引言:抽油机是石油开采中不可缺少的重要设备之一、游梁式抽油机作为抽油机的一种常见设计,已经在石油开采中得到广泛应用。
本文将对游梁式抽油机进行常规设计,从结构设计、工作原理、控制系统等方面进行详细阐述。
一、结构设计:游梁式抽油机的结构主要由主骨架、曲柄杆、游梁、连杆等组成。
主骨架是整个抽油机的主要支撑结构,承受着巨大的载荷。
曲柄杆通过曲轴与发动机相连接,通过往复运动驱动游梁实现抽油机的工作。
游梁由游梁杆和游梁头组成,游梁杆可以左右滑动,提供了抽油机的往复运动。
连杆连接着游梁和曲柄杆,使得游梁能够沿着曲柄杆方向运动。
二、工作原理:游梁式抽油机的工作原理基于连杆机构,将曲柄杆的旋转运动转变为游梁的往复运动。
曲柄杆与游梁通过连杆连接,当曲柄杆旋转时,连杆将转动力转移到游梁上。
由于游梁杆可以左右滑动,游梁在连杆驱动下完成了往复运动。
当游梁向上运动时,抽油杆与井下抽油泵相连,完成抽油工作。
当游梁向下运动时,抽油杆与井下抽油泵断开,准备进行下一次往复运动。
三、控制系统:常规游梁式抽油机的控制系统主要包括位置控制系统和液压系统。
位置控制系统通过传感器、控制器等实现对游梁位置的监测和控制,保证游梁的往复运动的准确性。
液压系统通过控制液压泵和液压缸等实现对游梁的驱动,控制游梁的上下运动。
在工作过程中,位置控制系统和液压系统紧密配合,以保证抽油机的正常工作。
四、优化设计:为了提高游梁式抽油机的效率和可靠性,可以进行优化设计。
首先,可以通过材料选择和结构设计来提高主骨架的强度和刚度,以承受更大的载荷。
其次,可以优化连杆的设计,减小摩擦损失,提高能量传递效率。
此外,还可以提高液压系统的控制精度和响应速度,以提高抽油机的工作效率。
结论:本文对游梁式抽油机进行了常规设计,并对其结构、工作原理和控制系统进行了详细阐述。
通过优化设计,可以进一步提高抽油机的效率和可靠性,促进石油开采工作的顺利进行。
这对于石油工业的发展具有重要意义,也为相关领域的研究提供了一定的参考。
游梁式抽油机设计

游梁式抽油机设计
一、结构设计
其次,是驱动机构的设计。
驱动机构是游梁式抽油机的核心部件,通过动力传递和控制来驱动游梁运动。
驱动机构通常采用液压或机械传动形式,根据需要选择合适的驱动方式,并确保驱动机构的安全可靠。
最后,是泵头的设计。
泵头主要用于抽取地下的石油,所以需要选择合适的泵头型号,并考虑到泵头的工作效率和稳定性。
同时,还需要考虑到泵头与游梁之间的连接方式和安装位置,以确保泵头可以正常工作。
二、动力传递
动力传递主要是通过液压或机械传动的方式将动力传递给游梁。
在液压传动方面,需要考虑到液压泵、液压缸、油管等的选型和布置,以确保液压传动的稳定性和可靠性。
在机械传动方面,需要考虑到传动轴、联轴器、齿轮箱等的设计和安装,以确保机械传动的平稳性和高效性。
三、操作控制
游梁式抽油机的操作控制主要包括对驱动机构和泵头的控制。
驱动机构的控制可以通过液压阀、电气控制柜等实现,可以实现启停、方向控制和速度控制等功能。
泵头的控制可以通过液压阀和控制阀等实现,以保证泵头的工作效率和稳定性。
同时,还需考虑到游梁的位置检测和安全保护。
游梁的位置检测可以通过限位开关、传感器等实现,以确保游梁的正常工作范围。
安全保护方面可以采用过载保护装置、漏油报警装置等,以确保抽油机的安全运行。
总结起来,设计游梁式抽油机需要考虑到机器的结构、动力传递和操
作控制等方面。
在设计过程中,需要根据实际需求选择合适的材料和部件,并对各部件进行合理布置和安装。
同时,还需对驱动机构和泵头进行合理
选择和控制,以确保游梁式抽油机的正常运行。
常规游梁式抽油机自动平衡改造方案及节能原理分析
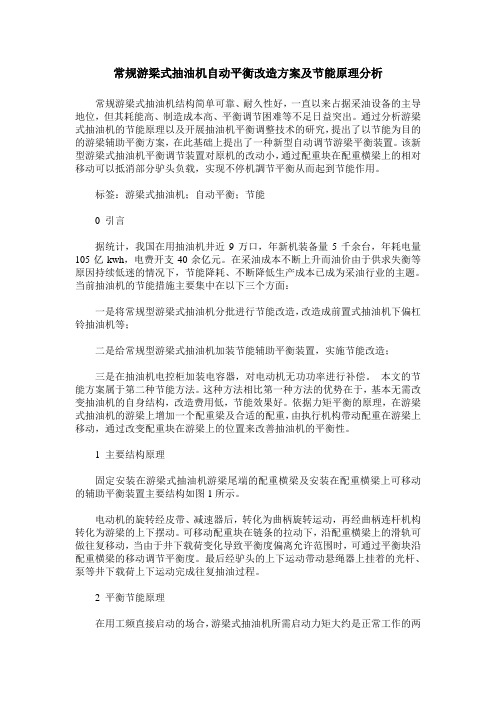
常规游梁式抽油机自动平衡改造方案及节能原理分析常规游梁式抽油机结构简单可靠、耐久性好,一直以来占据采油设备的主导地位,但其耗能高、制造成本高、平衡调节困难等不足日益突出。
通过分析游梁式抽油机的节能原理以及开展抽油机平衡调整技术的研究,提出了以节能为目的的游梁辅助平衡方案,在此基础上提出了一种新型自动调节游梁平衡装置。
该新型游梁式抽油机平衡调节装置对原机的改动小,通过配重块在配重横梁上的相对移动可以抵消部分驴头负载,实现不停机調节平衡从而起到节能作用。
标签:游梁式抽油机;自动平衡;节能0 引言据统计,我国在用抽油机井近9万口,年新机装备量5千余台,年耗电量105亿kwh,电费开支40余亿元。
在采油成本不断上升而油价由于供求失衡等原因持续低迷的情况下,节能降耗、不断降低生产成本已成为采油行业的主题。
当前抽油机的节能措施主要集中在以下三个方面:一是将常规型游梁式抽油机分批进行节能改造,改造成前置式抽油机下偏杠铃抽油机等;二是给常规型游梁式抽油机加装节能辅助平衡装置,实施节能改造;三是在抽油机电控柜加装电容器,对电动机无功功率进行补偿。
本文的节能方案属于第二种节能方法。
这种方法相比第一种方法的优势在于,基本无需改变抽油机的自身结构,改造费用低,节能效果好。
依据力矩平衡的原理,在游梁式抽油机的游梁上增加一个配重梁及合适的配重,由执行机构带动配重在游梁上移动,通过改变配重块在游梁上的位置来改善抽油机的平衡性。
1 主要结构原理固定安装在游梁式抽油机游梁尾端的配重横梁及安装在配重横梁上可移动的辅助平衡装置主要结构如图1所示。
电动机的旋转经皮带、减速器后,转化为曲柄旋转运动,再经曲柄连杆机构转化为游梁的上下摆动。
可移动配重块在链条的拉动下,沿配重横梁上的滑轨可做往复移动,当由于井下载荷变化导致平衡度偏离允许范围时,可通过平衡块沿配重横梁的移动调节平衡度。
最后经驴头的上下运动带动悬绳器上挂着的光杆、泵等井下载荷上下运动完成往复抽油过程。
游梁式抽油机说明书
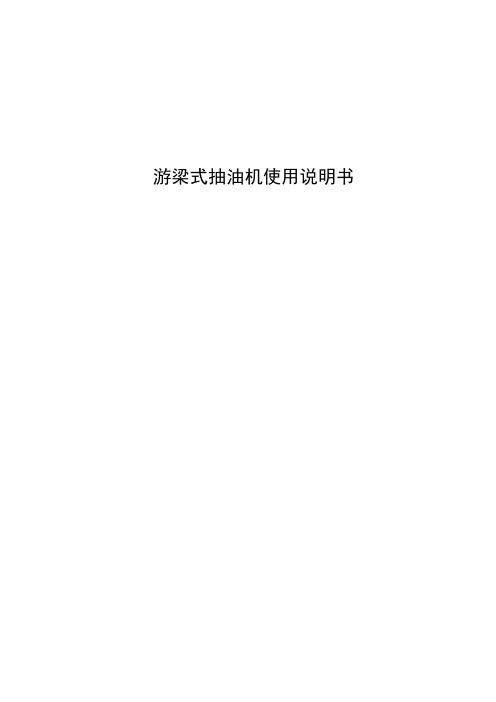
一、
抽油机用于油层能量不足以自喷的油井,作为有杆抽油的地面采油设备。
常规型游梁式抽油机具有结构简单,使用可靠,操作维护方便和能在恶劣自然条件下长期工作等特点,所以在油田开采中得到广泛的应用。
常规机型号为:CYJ×—×—×
异相型游梁式抽油机是在常规型游梁式抽油机的基础上,对四杆机构进行优化设计,使其上冲程时间长于下冲程时间,曲柄平衡重重心偏离曲柄对称中心线一个角度τ。在合适的工况下比常规型游梁式抽油机有提高机—泵效率,降低能耗的特点,异相型游梁式抽油机仍保持了常规机结构简单,使用可靠,操作维护方便等特点。
注:我厂产品在生产过程中,可能进行局部的改进,因此可能出现说明书与交付产品不尽一致之处。
四、安装与调整
(一)基础
1、基础的方位应考虑当地的主导风向,应避免井中漏气、漏液被风吹向抽油机和原动机。同时,还应考虑到井场条件,保证抽油机安装后有足够的空间,便于修井作业。
2、基础必须座落在硬土层和非冻土层以下10~20厘米处。
(三)抽油机安装时各螺栓预紧扭矩参数表
螺栓直径(mm)
M16
M20
M24
M27
M30
M36
M42
扳手扭矩(N.m)
78
156
274
405
539
950
1626
(四)空运转
除平衡块外,其余部件均安装好,检查就绪后,按润滑部位要求加注润滑油,然后进行空运转。
1、点动电机使曲柄旋转1—2周,观察运动部件有无摩擦碰撞。
2、停机后,全部螺栓再次紧固。检查减速器各密封处有无渗、漏油,检查各运动副处的发热情况。
3、上述检查合格后,即可投入正常工作。工作24小时和两周时,须各再次紧固各连接螺栓。对曲柄销螺母、平衡块连接螺栓,地脚螺栓尤应注意。
常规游梁式抽油机设计与仿真(毕业设计)

摘要现在油田的采油方式有两种:一种是利用地层本身的能量来举升原油,称作自喷采油法;另一类是人为的利用机械设备将原油举升到地面,称作机械采油法。
自喷采油法是最经济的方法,但是随着油田的开发,地层压力的降低,地层能量的消耗,油田不能再采用自喷采油法,就需要利用机械采油法。
机械采油法,有杆抽油是国内外油田最主要的,也是至今在机械采油方式中占绝对主导地位的人工举升方式。
有杆抽油系统主要由抽油机、抽油杆、抽油泵三部分组成,抽油机是有杆抽油系统最主要的升举设备。
根据其是否有游梁,抽油机可以划分为游梁式抽油机和无游梁式抽油机。
而常规游梁抽油机自诞生以来,历经百年,经历了各种工况和各种地域油田生产的考验,经久不衰。
目前仍在国内外普通使用。
常规游梁式抽油机以其结构简单、耐用、操作简便、维护费用低等明显优势,一直占据着有杆系采油地面设备的主导地位。
所以研究有杆类采油设备是非常有意义的。
本文介绍了常规抽油机工作原理与节能原理,设计过程中对抽油机运动学和动力学分析与计算,阐述了常规游梁式抽油机运动规律。
游梁式抽油机驴头的悬点载荷标志抽油机的工作能力的重要参数之一,而看它是否节能,其技术指标是抽油机的电动机实耗功率的大小及减速器的工作状态。
本设计全面概述了常规性抽油机的发展概况,抽油机的优化设计及其节能原理,对抽油机得几何参数,运动参数,动力学参数进行了全面的分析计算,以对常规游梁式抽油机进行优化设计。
关键词:常规游梁式抽油机;结构设计计算;优化AbstractMethod of oilfield exploitation of crude oil is divided into two kinds: one kind is uses thehigh energy to lift crude oil, known as the flowing production method; another kind is the use of mechanical equipment for the crude oil onto the ground, called the mechanical recovery method. Flowing production method is the mosteconomical, but with the development of oil fields, lower formation pressure,formation energy consumption, oil field can not use the flowing production method,need to use mechanical recovery method. Machinery production equipment from the mode of production can be divided into two kinds: rod production equipment and no rod production equipment, and rod production equipment for the main part,so the energy problem rod production equipment is very meaningful.Beam pumping unit is the main equipment for the production of rod oil extraction equipment in oil field. In some oil fields in China try to use technology to replace theconventional beam pumping machine is advanced, but because the cost is too high, the cost recovery period is too long, so in the field or in the beam pumping unit.This paper introduces the conventional pumping unit working principle and theprinciple of energy saving pumping unit, the analysis and calculation of the kinematics and dynamics of machine design process, the conventional beampumping oil machine movement law. One of the important parameters of the beampumping unit horsehead of the pumping unit horsehead load mark working ability,and to see whether it is energy saving, the technical indicators are motor pumping unit of the actual power consumption and the size of the reducer working state. The design of a comprehensive overview of the development of the conventionalpumping unit, optimizing design and energy-saving principle of oil drawing machine,the geometrical parameters, pumping motion parameters, the kinetic parameterswere analyzed to calculate.目录常规游梁式抽油机设计与仿真第一章绪论1.1游梁式抽油机技术发展抽油机产生和使用由来已久,已有百年的历史。
(完整word版)游梁式抽油机系统机械部分分析

常规游梁式抽油机系统机械部分分析2009年8月6日目录游梁式抽油机概述 (3)一、游梁式抽油机基本种类 (3)二、游梁式抽油机的工作原理 (4)三、常规游梁式抽油机 (7)常规游梁式抽油机的运动分析(下图为ppt演示文稿,请双击打开相关内容) (9)常规游梁式抽油机的悬点载荷计算 (9)一、抽油机悬点载荷简介 (9)二、悬点载荷计算 (11)常规游梁式抽油机减速器扭矩计算 (14)一、抽油机减速器扭矩计算 (14)二、抽油机扭矩特性参数 (17)常规游梁式抽油机性能分析 (19)负载特性对电机的影响 (20)抽油机电机的启动问题 (21)游梁式抽油机概述随着原油和油气的产出,贮存压力减小。
最终在某一点,贮存压力达到小的必需用人工举升的方式才可以产油。
游梁式抽油机,是一个借鉴了水井工业的理想应用。
自从1925年Trout 设计的油泵演变到现今的具有统治地位游梁是人工举升设备。
历经多年的发展和完善,主要是提高其可靠性和零件的设计方法上。
比如抽油杆材料从木头改变成玻璃钢和塑料加强型。
一、游梁式抽油机基本种类(1)传统型传统的曲柄配重型被广泛的接受和认可,是久经考验的油田“战士”。
支点前面是负载,后面是配重。
(2)前置配重型由于其独特的几何结构和配重特征,低转矩峰值和低动力需求。
运行特点是是快速的下冲程,慢速的上冲程。
减小重型负载上冲程的加速载荷。
降低峰值转矩延长油杆寿命。
(3)结构紧凑型紧凑结构的设计防便用于经常移动的工作方式或者城区的应用,很多部件在工厂已经完成安装。
(4)气压配重型应用压缩气体替代沉重的铸铁配重块并且可以更精确得控制配重。
大大的减轻了系统地重量,运输和安装费用明显降低。
气压配重独特的优点在于更大的增大冲程,而对于铸铁配重结构来说将是非常庞大难于实现。
(5)游梁配重型配重块安装在游梁的另一端,是一种适合浅井应用的经济型。
游梁式抽油机彩图(从左到右依次为(1)~(5))二、游梁式抽油机的工作原理游梁式抽油机是有杆抽油系统的地面驱动装置,它由动力机、减速器、机架和连杆机构等部分组成。
- 1、下载文档前请自行甄别文档内容的完整性,平台不提供额外的编辑、内容补充、找答案等附加服务。
- 2、"仅部分预览"的文档,不可在线预览部分如存在完整性等问题,可反馈申请退款(可完整预览的文档不适用该条件!)。
- 3、如文档侵犯您的权益,请联系客服反馈,我们会尽快为您处理(人工客服工作时间:9:00-18:30)。
常规型游梁抽油机传动装置设计
打开文本图片集
一、传动装置总体设计方案
1.传动方案
传动方案已给定,前置外传动为普通V带传动,减速器为展开式二级圆柱齿轮减速器。
2.该方案的优缺点
由于V带有缓冲吸振能力,采用V带传动能减小振动带来的影响,并且该工作机属于小功率、载荷变化不大,可以采用V 带这种简单的结构,并且价格便宜,标准化程度高,大幅降低了成本。
展开式二级圆柱齿轮减速器由于齿轮相对轴承为不对称布置,因而沿齿向载荷分布不均,要求轴有较大刚度。
二、动力学参数计算
1.电动机输出参数
2.高速轴的参数
3.中间轴的参数
4.低速轴的参数
5.工作机轴的参数
各轴转速、功率和转矩列于下表
三、减速器的密封與润滑
1.减速器的密封
为防止箱体内润滑剂外泄和外部杂质进入箱体内部影响箱体工作,在构成箱体的各零件间,如箱盖与箱座间、及外伸轴的输出、输入轴与轴承盖间,需设置不同形式的密封装置。
对于无相对运动的结合面,常用密封胶、耐油橡胶垫圈等;对于旋转零件如外伸轴的密封,则需根据其不同的运动速度和密封要求考虑不同的密封件和结构。
本设计中由于密封界面的相对速度较小,故采用接触式密封。
输入轴与
轴承盖间V 3m/s,输出轴与轴承盖间也为V 3m/s,故均采用半粗羊毛毡封油圈。
2.齿轮的润滑
通用的闭式齿轮传动,其润滑方式根据齿轮的圆周速度大小决定。
由于低速级大齿轮的圆周速度v≤12m/s,将大齿轮的轮齿浸入油池进行浸油润滑。
这样,齿轮在传动时,就把润滑油带到啮合的齿面上,同时也将油甩到箱壁上,借以散热
齿轮浸入油中的深度通常不宜超过一个齿高,但一般亦不应小于10mm。
为了避免齿轮转动时将沉积在油池底部的污物搅起,造成齿面磨损,大齿轮齿顶距离油池地面距离不小于30mm,取齿顶距箱体内底面距离为30mm。
由于低速级大齿轮全齿高h=6.75mm≤10mm,取浸油深度为10mm。
则油的深度H为
H=30+10=40mm
根据齿轮圆周速度查表选用负荷工业齿轮油(GB 5903-2011),牌号为320润滑油,黏度推荐值为266cSt。
3.轴承的润滑
滚动轴承的润滑剂可以是脂润滑、润滑油或固体润滑剂。
选择何种润滑方式可以根据齿轮圆周速度判断。
由于V齿≤2m/s,所以均选择脂润滑。
采用脂润滑轴承的时候,为避免稀油稀释油脂,需用挡油环将轴承与箱体内部隔开,且轴承与箱体内壁需保持一定的距离。
在本箱体设计中滚动轴承距箱体内壁距离10mm,故选用通用锂基润滑脂(GB/T 7324-1987),它适用于宽温度范围内各种机械设备的润滑,选用牌号为ZL-1的润滑脂。
四、设计小结
之前我对《机械设计基础》这门课的认识是很肤浅的,实际动手设计的时候才发现自己学得知识太少,而且就算上课的时候再认真听课,光靠课堂上学习的知识根本就无法解决实际问题,必须要靠自己学习。
我的设计中存在很多不完美、缺憾甚至是错误的地方,但由于时间的原因,是不可能一一纠正过来的了。
尽管设计中存在这样或那
样的问题,我还是从中学到很多东西。
首先,我体会到参考资料的重要性,利用一切可以利用的资源对设计来说是至关重要的。
往往很多数据在教材上是没有的,我们找到的参考资料也不齐全,这时参考资料的价值就立时体现出来了。
其次,从设计过程中,我复习了以前学过的机械制图知识,*****的画图水平有所提高,Word输入、排版的技巧也有所掌握,这些应该是我最大的收获。
再次,严谨理性的态度在设计中是非常重要的,采用每一个数据都要有根据,设计是一环扣一环的,前面做错了,后面就要全改,工作量差不多等于重做。
通过这次的课程设计,极大的提高了我们对机械设计这门课程的掌握和运用,让我们熟悉了手册和国家标准的使用,并把我们所学的知识和将来的生产实际相结合,提高了我们分析问题并自己去解决问题的能力,也提高了我们各个方面的素质,有利于我们今后更顺利地走上工作岗位。