汽车电子基本电气负荷试验
汽车电气实验报告总结
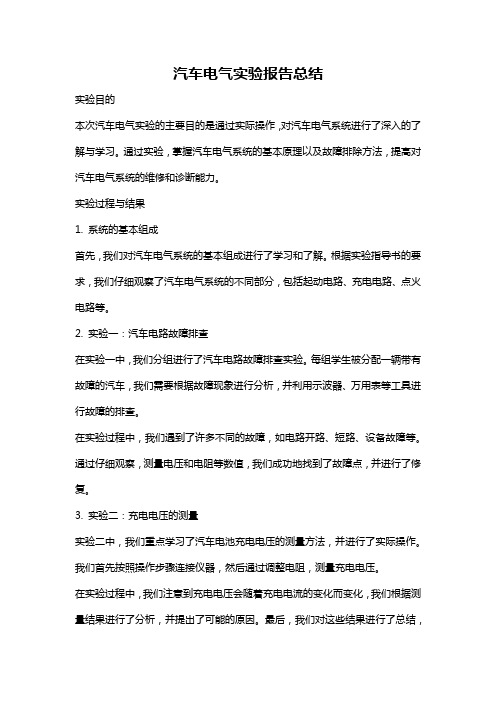
汽车电气实验报告总结实验目的本次汽车电气实验的主要目的是通过实际操作,对汽车电气系统进行了深入的了解与学习。
通过实验,掌握汽车电气系统的基本原理以及故障排除方法,提高对汽车电气系统的维修和诊断能力。
实验过程与结果1. 系统的基本组成首先,我们对汽车电气系统的基本组成进行了学习和了解。
根据实验指导书的要求,我们仔细观察了汽车电气系统的不同部分,包括起动电路、充电电路、点火电路等。
2. 实验一:汽车电路故障排查在实验一中,我们分组进行了汽车电路故障排查实验。
每组学生被分配一辆带有故障的汽车,我们需要根据故障现象进行分析,并利用示波器、万用表等工具进行故障的排查。
在实验过程中,我们遇到了许多不同的故障,如电路开路、短路、设备故障等。
通过仔细观察,测量电压和电阻等数值,我们成功地找到了故障点,并进行了修复。
3. 实验二:充电电压的测量实验二中,我们重点学习了汽车电池充电电压的测量方法,并进行了实际操作。
我们首先按照操作步骤连接仪器,然后通过调整电阻,测量充电电压。
在实验过程中,我们注意到充电电压会随着充电电流的变化而变化,我们根据测量结果进行了分析,并提出了可能的原因。
最后,我们对这些结果进行了总结,并得出了一些有关电池充电电压测量的结论。
4. 实验三:转速测量与点火系统故障诊断实验三中,我们学习了汽车发动机的转速测量方法,并探讨了点火系统故障诊断的相关知识。
我们使用了转速计进行测量,并观察了转速信号的波形图。
在实验过程中,我们发现转速信号波形图的形态可以反映点火系统的工作状态。
通过比对实际测量的转速信号和标准波形图,我们成功地诊断出了点火系统故障,并进行了相关的维修。
实验总结与收获通过本次汽车电气实验的学习,我对汽车电气系统有了更深入的了解。
通过实际操作,我不仅巩固了相关理论知识,还掌握了一些常见故障的排查与维修方法。
此外,通过与同学们的讨论和交流,我也收获了一些宝贵的经验和技巧。
我学会了如何正确使用示波器、万用表等工具,以及如何分析和解决汽车电路故障。
车载测试中的车身电气系统测试方法
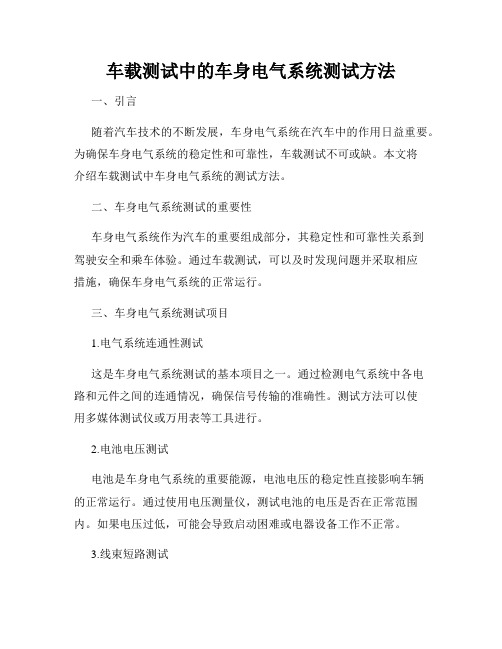
车载测试中的车身电气系统测试方法一、引言随着汽车技术的不断发展,车身电气系统在汽车中的作用日益重要。
为确保车身电气系统的稳定性和可靠性,车载测试不可或缺。
本文将介绍车载测试中车身电气系统的测试方法。
二、车身电气系统测试的重要性车身电气系统作为汽车的重要组成部分,其稳定性和可靠性关系到驾驶安全和乘车体验。
通过车载测试,可以及时发现问题并采取相应措施,确保车身电气系统的正常运行。
三、车身电气系统测试项目1.电气系统连通性测试这是车身电气系统测试的基本项目之一。
通过检测电气系统中各电路和元件之间的连通情况,确保信号传输的准确性。
测试方法可以使用多媒体测试仪或万用表等工具进行。
2.电池电压测试电池是车身电气系统的重要能源,电池电压的稳定性直接影响车辆的正常运行。
通过使用电压测量仪,测试电池的电压是否在正常范围内。
如果电压过低,可能会导致启动困难或电器设备工作不正常。
3.线束短路测试线束短路是车辆电气故障中常见的问题之一,会导致电路短路,甚至引起火灾等严重后果。
通过使用线路绝缘测试仪,可以快速检测车身电气系统中是否存在线束短路现象,并采取相应措施进行修复。
4.灯光系统测试车辆的灯光系统对于行车安全至关重要。
通过使用光照计或多媒体测试仪,测试车辆前照灯、制动灯、示宽灯等灯光是否正常。
同时,还需要测试灯光的亮度和照射范围是否符合相关标准。
5.辅助设备测试车身电气系统中包含了各种辅助设备,如空调系统、音响系统、倒车雷达等。
测试这些辅助设备是否正常工作,能够提供良好的行车环境和乘车体验。
可以使用专业测试设备进行相应的功能测试。
6.故障码检测现代汽车上的电子控制单元(ECU)会将故障信息存储在内部存储器中,通过读取故障码可以快速定位车身电气系统出现的故障。
通过连接故障诊断仪器,读取故障码并进行分析,能够更快速准确地排除故障。
四、车身电气系统测试流程1.准备工作车载测试前,需要准备相应的测试设备和工具,包括多媒体测试仪、电压测量仪、线路绝缘测试仪、光照计、故障诊断仪等。
汽车电气和电子部件 通用试验要求 04.1045-2008

1) Q/SQR汽车电气和电子部件 通用试验要求1)奇瑞汽车股份有限公司 发布Q/SQR.04.1045-2008前 言本标准规定了奇瑞汽车股份有限公司所生产汽车上的电气电子系统/部件的通用试验要求。
它作为每个电气电子系统/部件的具体技术规范或技术要求的基础,为产品的开发,认可及质量检验提供基础试验检验依据。
本标准在格式和内容的编排上均符合GB/T1.1-2000和GB/T1.2-2002的规定。
本标准由奇瑞汽车股份有限公司电器标准化技术委员会提出。
本标准由奇瑞汽车股份有限公司汽车工程研究院标准管理科归口。
本标准起草单位:试验技术中心、乘用车工程研究一院。
本标准主要起草人:王金成、陆云峰、朱礼铭、董明。
汽车电气和电子部件通用试验要求1 范围本标准规定了奇瑞汽车的电气电子系统/部件的通用试验要求。
在使用该标准时,须结合具体系统/部件的技术特征,结构,安装位置等,根据表1选取试验项目或变更试验要求,并体现在具体的技术规范或图纸中。
按照优先级顺序,从高到低依次为产品图纸、系统/部件的技术规范、本标准。
2 规范性引用文件下列文件中的条款通过本标准的引用而成为本标准的条款。
凡是注日期的引用文件,其随后所有的修改单(不包括勘误的内容)或修订版均不适用于本标准,然而,鼓励根据本标准达成协议的各方研究是否可使用这些文件的最新版本。
凡是不注日期的引用文件,其最新版本适用于本标准。
GB/T 2423.4 电工电子产品基本环境试验规程试验Db:交变湿热试验方法Q/SQR.04.030 车用低压电线束技术条件Q/SQR.04.095 塑料、织物氙弧灯连续照射试验Q/SQR.04.748 车辆电器电子零部件EMC试验方法及其要求Q/SQR.04.935 车用电线束插接器DIN 40 050-9 Road vehicles-Degrees of Protection(IP Code)-Protection against foreign objects,water and access Electrical equipment3 术语、定义和符号下列术语、定义和符号适用于本标准。
汽车电子电气部件试验 DV V验证试验

汽车电气和电子部件验证试验(DV/PV试验)汽车零部件从设计归属上分为两类:1.主机厂设计的零部件;2.供应商设计的零部件;主机厂设计的零部件通常的DFMEA设计失效模式分析和DVP设计验证计划都是有主机厂工程师来写的。
供应商设计的零部件通常也叫黑匣子件,DFMEA设计失效模式分析和DVP设计验证计划都是有供应商来写的。
主机厂的会有各种系统级和部件级的设计规范和试验方法。
试验方法里面会有具体的试验方法要求,试验设备要求和试验次数要求。
供应商的各类试验规范和试验方法要求通常不会直接发给主机厂,尤其国际供应商是DFMEA基本只能到供应商处看,比如以前我看博世的DFMEA甚至只能到德国总部才让看,不能拍照。
验证试验分为DV和PV,DV是DesignVerification设计验证,此时可以是手工件或者模具件。
PV是ProductVerification产品验证,必须是模具件,并从供应商的量产生产线上做出来的零件。
PV之后的零件再完成PPAP审核,就具备了量产供货资格了。
测试要求一般是通过对产品的需求分解而来,这个在整车和部件上都是通用的,这里的需求包含了对市场的预期、国家的法律法规,用户的需求等等。
整车方面,中国有针对乘用车的强制检验标准,大概40余项,对于可以在市场售卖的车辆而言,这些试验是必须通过的,大家也可以百度的到,这里不去多说。
个别厂商也会对产品做一些其他要求,比方说噪音,振动等,所以这些试验也不可避免。
试验根据项目阶段的不同也分为开发性试验和批量批准的试验,两者或有重叠,但是不完全相同,目的也不同。
零部件方面,根据位置的不同,所处环境的不同,功能要求的不同以及寿命要求的不同,试验的项目、方法与指标也略有不同。
针对车上的每一个零件,都会有经过需求分解,标准(国家标准、行业标准和企业标准)分析后得到的试验项目列表,下面我试着就几个方面举些例子:1、车用外饰,下面仅用保险杠作为例子来尝试分析:a、功能方面,汽车保险杠是吸收和减缓外界冲击力、防护车身前后部的安全装置。
TL80101 汽车上电子或电器一般实验条件1

2005年6月汽车上电气和电子部件一般试验条件VW80101 标准中心8M A008M A00共 49 页第1页翻译曹哲日期2005.11.20校对日期打字牛红珍日期2005.12.22 主题词:部件,电气部件,电子部件,试验条件目录1适用范围2 一般技术要求2.1 规定和测试顺序2.2 定义2.3 汽车技术要求范围和技术要求种类2.4 材料技术要求2.5 运行状况2.6 功能状态2.7 一般试验条件3 电器的技术要求3.1 工作电压3.2 工作电压扰动3.3 反馈3.4 电平:高-低状态3.5 在欠电压和过电压情况下的功能3.6 工作电流3.7 静态电流吸收和静态电荷吸收3.8 极性变换可靠性3.9 过电流强度3.10 过电压强度的长时间运用3.11 过电压的短时间运用3.12 叠加交流电压3.13 电源电压的缓慢下降和上升3.14 在电压波动情况下的变位性能3.15 防短路可靠性3.16 绝缘强度3.17 绝缘电阻3.18 中断3.19 电压降3.20 电磁兼容性4 机械性技术要求4.1 振动4.2 机械振动4.3坠地试验4.4.卷边连接和插塞连接4.5汽车上电气和电子元件的插接件4.6导线抗拉强度5 气候方面的技术要求5.1 在恒温情况下的试验5.2 温度交变试验5.3 分级温度试验5.4 抗大气腐蚀的能力5.5 环境稳定性5.6 温度突变6 化学方面的技术要求6.1 抗试剂稳定性6.2 电动机喷洗(试验IP X9K)7 疲劳试验7.1 电气和电子系统/元件的疲劳试验7.2 机电系统/元件的疲劳试验7.3 零部件特殊疲劳试验8 表9 相关参考资料修订同VW 801 01:2004-07标准比较,作了如下修改:—同以前的版本比较,在有修改的地方划出一条垂直线来表示—表1:测试顺序有修改—表2:包括了技术要求范围—假如表中的数据(数值)不够测得的量,则该技术要求应在负荷表中予以解释(补充在表中) —功能状态C做了补充— 3.2条:采纳了工作电压扰动— 3.3条:反馈做了补充— 4.6条:导线应力强度,对用途做了清楚的说明—模拟试样导线漏电时电子射出力减弱的有效性— 5.3条:采纳了级热试验— 5.6条:温度突变—凡采用的方案都在负荷表中做了说明—7条:疲劳试验款项的划分改变如下:7.1条,电气和电子系统/组件的疲劳试验7.2条,电机系统/组件的疲劳试验7.2.1疲劳试验与充做使用期限测定影响量的温度交变7.2.2疲劳试验与充做使用期限测定影响量的负荷交换7.3条,零件特殊的疲劳试验—表25;见表1,试验顺序有改变以前版本1987-06;1988-08;1992-01;1993-04;1994-05;1995-06;1998-01;1999-06;2000-09;2001-04;2003-05;2004-07抗震强度 见4.1条 疲劳试验 见7条下列各项试验可以在预处理之后预处理之后((无载地在环境中存放之后存放之后))并列进行工作电压扰动 见3.2条 反馈 见3.3条 欠电压和超电压 见3.4条 电平:HIGH-/LOW 状态配合 见3.4条 工作电流 见3.6条 静电流吸收 见3.7条 极性变换可靠性 见3.8条 过电流强度 见3.9条 长时间工作过电压强度 见3.10条 短时间工作过电压强度 见3.11条 叠加的交流电压 见3.12条 电源电压的缓慢上升和下降 见3.13条 电压扰动情况下的复位性能 见3.14条 防短路可靠性 见3.15条中断 见3.18条 电压降 见3.19条 邻近防干扰按TL 965 见3.20.2条 线路交织干扰按TL 820 66 见3.20.1条 辐射干扰按TL 821 66 见3.20.3条 传感器线路上的电磁兼容性按TL 823 66 见3.20.1.3条 对静电放电(ESD)的抗扰性,按TL 824 66 见3.20.4条 紧急关断试验 见4.3条 皱折连接和插塞连接 见4.4条 汽车上电气和电子组件的插接件 见4.5条 导线抗拉强度 见4.6条 温度突变试验 见5.2.2条 级温试验 见5.3条 耐大气腐蚀能力 见5.4条 尘埃和水密封性按DIN 40 050-9 见5.5.1条 潮湿热,周期性的 见5.5.2条 盐雾 见5.5.3条 温度突变 见5.6条 抗试剂的稳定性 见6.1条 电动机洗涤(IP X9K 试验) 见6.2条2.2 定义 2.2.1 概念 系统 功能上有逻辑联系的组件,例如ABS-系统(防抱死系统),ESP-系统(发动机次序操纵台系统)组件功能上有逻辑联系的零件,例如执行元件、传感器、控制器试样接受试验的系统或组件功能含有系统特定的功能和诊断功能2.2.2 缩略语I N额定电流T NH 对流受热温度,是一种在停车之后,在相应的技术要求范围内(见表2) 出现的最高环境温度T OL 这是一种较高的库房极限温度,是最高的环境温度,其在试样存放或传递是允许的.它含有例如漆层干燥和发动机舱的淤热.试样不得在这样温度中运转/T RT 室温(+23±5)℃.如果给出的温度没有偏差,这个温度也就是试验温度T UB,T OB 下限或上限的极限工作温度,就是最低和最高的环境温度,在此温度下, 试样可以持久运行.恒定的自加热温度略去不计T UL 下限的库房极限温度,是试样存放或传递时允许的最低温度,试样不得在这样温度中运转.U Bmax 最大的工作电压,在此电压下,试样可以持续地运作U Bmin 最小的工作电压,在此电压下,试样可以运作U N 标称电压U PA 发电机在运行情况下的试验电压U PB 蓄电池在工作状态下的试验电压U PC 人工启动时电池极性变换接口上的试验电压2.3 汽车技术要求范围和技术要求种类见图1和表2图1-技术要求范围2.4 材料技术要求全部材料,润滑剂和表面涂敷材料,都必须满足危险物质工作条列(最新资料)的要求,以及满足VW 911 00汽车环境标准和VW 50 180规定的放射性能的要求.2.5 运行状况不同的运行状况区分如下:2.5.1 运行状况1试样不是电动的—运行状况1.1 导线未接通试样—运行状况1.2 全部导线的连接都是符合汽车组装要求的,不过是无电压的2.5.2 运行状况2试样电器运行时,电源电压U PB(电池电压)与关闭着的汽车(AUS发动机)中的电器是一样的.全部系统组合(例如传感器、执行元件)和导线都是接通的—运行状况2.1 系统和组件的功能未起作用(例如休止状态)—运行状况2.2 系统功能和组件功能可以满足相应条款中的工作要求和控制要求2.5.3 运行状况3试样运行着,电源电压为U PA(发动机和发电机运行着)全部系统和组件(例如传感器、执行元件)和导线都是接通的—运行状况3.1 系统和组件的功能未起作用—运行状况3.2 系统功能和组件功能可以满足相应条款中的工作要求和控制要求2.5.4 实验室中车身运行状况如同运行状况3.2,不过试验电压和电负荷都满足当时的试验要求2.6 功能状态该条款说明了试验的当时和之后的功能状态每一次试验都是对试样功能状态的说明,追加的技术要求在负荷表中记录下来并解释清楚.2.6.1 功能状态A试样在电子碰撞之时和之后,都能满足全部规定的功能试验参数的要求,其在有诊断能力的控制器情况下不会造成误差存储器输入的结果.2.6.2 功能状态B试样在电子碰撞时,满足全部规定的功能试验参数,不过会有一个或多个功能处于规定的公差之外,而在电子碰撞结束之后,试样重又满足全部规定的试验参数,存储器功能必须维持功能状态A的水平.2.6.3 功能状态C试样在电子碰撞之时,满足一个或多个非规定的功能试验参数,不过在电子碰撞结束之后,试样重又自动地满足全部规定的功能参数.功能缺陷是不允许的2.6.4 功能状态D试样在电子碰撞时,满足一个或多个非规定的功能试验参数,不过在电子碰撞结束之后, 通过重新调整或简单的修理(例如更换了损坏的保险丝),试样重又满足了全部规定的功能试验参数2.6.5 功能状态E试样在电子碰撞之间,满足一个或多个非规定的功能试验参数,但在电子碰撞之后,必须经过修理和更换才能满足试验参数2.7 一般试验一般试验条件条件待试的试件,至少要有6个,为欲增添和提高技术要求,则至少要10个试样.全部试验都要使用经过预处理的试样来完成(预处理见5.1.1条).如果温度的公差数据缺项,则给出±2℃的公差.温度测试部位按DIN 50011-11和DIN 50011 –12进行如果没有提出其他要求,实行试验所要求的温度为T RT,相对湿度为25%至75%.试验电压必须满足表3的要求,其他试验温度只有在同大众汽车康采恩主管科研单位协商妥当之后方可采用,试验电压必须在试验报告中记载清楚.表3 – 试验电压试验电压1) 12V系统(V) 24 V 系统(V)U PA14±0.1 28±0.2U PB12±0.1 24±0.2 1) 试样上保持的试验电压3 电气的技术要求3.1 工作电压工作电压见表4表4 – 电压及其使用说明额定电压U N1)(V)工作电压U Bmin U Bmax(V) (V)使用说明12 6.015在起动过程中,功能必须保持不变12 9.015在“发动机AUS”情况下,功能必须保持不变12 10.815在发动机工作过程中,功能必须保持现状24 上述数据往往要增一倍使用试样组如同额定电压12 V1) 概念按DIN 72251注释:工作电压贴近试样当试样接通网路时,网路容量要与线路负荷表中预先给定的电压值相适应3.2 工作电压扰动目的该项试验是模拟工作电压尽可能快速地扰动(工作水平平台)试验在图2中所描绘的电压曲线,是试样的电压曲线,这条曲线是在试验时从接线柱30和接线柱15上电源电压获得的在图3中所描绘的电压曲线,是试样的电压曲线,这条曲线是在试验时从接线柱75上电源电压获得的电压值,时间流程以及试验周期数,这些数据都取自表5表5中的全部电压曲线都是经过试验的图2 – 试样由接线柱30或接线柱15供电时绘成的电压曲线图3 – 试样由接线柱75供电时绘成的电压曲线表5 电压曲线上的电平/电压/持续时间技术要求见表6表6 – 功能状态3.3 反馈接线柱15上的电压反馈,最高只许达到1.0 V的电平注释:电容反馈通过保护电容器的放电电流没有反馈电流电容器如果在接线柱断电情况下出现T字形曲线≥10 ms的放电曲线,那就说明它已通过二极管与接线柱导线退耦3.4 电平:HIGH-LOW-Zustand(高-低-状态)的配合对于没有规定接口的试样,给出电平与输入状态的配合如下:≥U Bmin(最小工时)-2 VHIGH - 判读:U≤ 2 VLOW - 判读:U状态高度,即从LOW变为HIGH,或从HIGH变为LOW ,只有在超过或不超过其规定的水平线(电平)情况下才能进行对所有具备CAN-/MOST-Kommunikation(能够耦合/最大限度耦合)的仪器都适用的是:在接线柱15上终端负荷情况下的电平HIGH - 判读:U≥ 4 V≤ 2 VLOW - 判读:U3.5 在欠电压和过电压情况下的功能只要断定是过电压或欠电压,那就说明试样进入了安全运行状态,也就是表现出没有功能缺陷地运行状态.这时候,试样便是在返回工作电压区域情况履行试验任务,重又自动地恢复预先规定的全部功能.功能限制应在图纸和负荷表上说明图4 - 12 V额定电压网状连接系统的电压分辨率方块图从欠电压范围或过电压范围过渡到工作电压范围时,有≤0.5 V的滞后是允许的.各种用于发动机起动的重要控制器,如果说其在6 V和26 V之间肯定是有功能作用的, 那么:其它控制器由于没有误差存储器引入线,就未必有更多的功能作用.注释1 欠电压范围:在起动过程中应该保持不变的功能,在负荷表中必须予以说明注释2 欠电压范围:在起动过程中(例如外部起动模拟)应该保持不变的功能,在负荷表中必须予以说明注释3 “用于15.5 V ~ 17 V电压范围内 t<1 s的功能状态A”这条技术要求,不适用于直接接通电流的白炽灯工作电流3.6对于试样来说,功率消耗≥350 W时,电流变化速度应该是≤20 A/s.否则就必须有大众汽车康采恩的主管科技部门的批准.工作类别 3.23.7 静态电流吸收和静态电荷吸收静态电荷吸收,是作为稳定电流吸收的积分被计算出来的,从接线柱15 AUS的时间点开始,朝着接线柱15 AUS的方向外推到50天为止,就此而言,被采用的试样最高静态电荷吸收是从全部可想像到的汽车静态开始的.静态电流当量是这样一种电流量,它是由静态电荷吸收量除以50天得出来的.见图5图5 – 静态电荷吸收静态电流吸收期限基本上适用于所有的试样.在静止相位上的静态电流<0.1 mA 0mA当量适用于必须朝着接线柱15 AUS方向运行的试样,每个试样的静态电荷吸收持续时间不得超过50天0.12 Ah (安培小时).这样的电荷吸收也适用于朝着接线柱15 AUS方向上必要空转的运行否则必须经过大众汽车康采恩主管科技部门的批准工作类别 2.13.8 极性变换可靠性目的在外发动情况下,试样的电阻率是模拟极性变换的电池接线电阻率,该项试验不可用于下面的零部件—发电机—没有极性变换护罩的、带固定二极管的继电器试验试样要与汽车上接通电源的转换开关和保险装置相匹配.把极性变换的试验电压加到试验工作类别实验室车身试验min负荷时间 30电流负荷电流要符合负荷表的要求技术要求全部电子输出端都必须符合负荷表中过电流强度要求功能状态C3.10 过电压强度的长时间运用目的模拟发电机上有故障的电压调节器试验工作类别实验室车身试验-20℃)温度T = (T试验电压17 V -0.2Vmin试验时间 60把试验电压加到全部电压输入端技术要求对于汽车必备的功能,全部按功能状态A所有其他功能,按最低功能状态C3.11 过电压短时间运用目的模拟用提高电压的办法进行外部起动(跳跃式起动)试验工作类别实验室车身试验试验电压26 V -0.2V试验时间60 s把试验电压加到全部电压输入端技术要求对于汽车起动的必备功能,全部按功能状态A所有其他功能,按最低功能状态C3.12 叠加交流电压目的试验工作类别实验室车身试验试验电压13 V叠加交流电压幅度(正弦) U = 1 V电压源的内电阻≤100 mΩ频率范围50 Hz至20 KHz摆动类别三角形,线性的min摆动周期 2min试验时间 10技术要求功能状态A3.13 电源电压的缓慢下降和上升目的模拟蓄电池的缓慢放电和充电试验工作类别实验室车身试验把试验电压加到所有的电压输出端电源电压从U Bmax下降到0 V电源电压从0 V上升到U Bmax电压变化(0.5±0.1) V/每分钟技术要求功能状态A,在工作电压范围之内功能状态C,在工作电压范围之外3.14 在电压波动情况下的复位性能目的在不同的电压波动下模拟试样的复位性能,该项试验通常用具有复位功能的,并可应用于实际的试样(用带有显微控制器的一般试样)来进行试验工作类别实验室车身试验试验实施对于≥10 s 调整U Bmin周期对于5 s工作电压下降情况,U Bmin约0.5 V对于≥10 s 调整U Bmin和实施功能试验每一试验周期,电压进一步下降约0.5 V(见图6).当电压达到≤0.5 V时,试验便告结束,电压改变须时100 ms功能状态A,在工作电压范围之内功能状态C,在工作电压范围之外3.15 防短路可靠性目的模拟输入和输出端上的短路输入和输出端(不包括负荷电路)必须防止U PA和短路试验全部输入和输出端都要依次防止U PA和短路试验工作要用激活的和未激活的输出端来完成工作类别 3.2试验时间60 s,每次短路3.18 中断目的模拟导线中断试验工作类别 3.2插头脚中断用于每一个插接的插头脚上,(将插头拔下又插上)中断时间10 s插头中断插头一个接一个(拔下又插上)在所有工作状态下(随便按那个顺序)进行试验中断时间10 s技术要求功能状态C3.19 电压降目的最大允许的电压降试验电子管放大系数中继电器与继电器触点相适应的试验试验工作类别实验室车身试验继电器触点电压降≤5 m V/A,但要绝对≤100 mV额定电流情况下的试验按图纸,负荷表或TL工作电流按图纸,负荷表或TL开关触点按VW 801 02电子输出端按图纸,负荷表或TL技术要求所允许的电压降在试验期间不得超过使用时间3.20 电磁兼容性(EMV)3.20.1 线路交织的干扰3.20.1.1 电源电路的干扰辐射技术要求按TL 820 66,负荷表或图纸3.20.1.2 电源电路的干扰强度技术要求按TL 820 66,负荷表或图纸3.20.1.3 传感器线路的干扰强度技术要求按TL 823 66,负荷表或图纸3.20.2 干扰辐射技术要求按TL 965,负荷表或图纸辐3.20.3 射干扰技术要求按TL821 66,负荷表或图纸3.20.4 抗静电放电[ESD]的抵抗力技术要求按TL824 66,负荷表或图纸4 机械性技术要求4.1 振动如果经过疲劳试验之后并没有提供出什么证据,则该项试验就不必再进行了.该项振动试验的目的,是要在接近于实际负荷情况下,使试样能顺利地发挥自己的功能.疲劳故障应能从振动外貌和振动时间中看出端倪.磨损试验不属振动试验范围.具有不同精度的振动试验是各种各样的,这种情况与试样的装配位置有着直接的关系.试样选好之后,将它们装到振动/滑动台相应安装位置上,连接起来的电缆、软管以及从属的配件,要满足装配的要求.电缆和软管要满足电子收集配件的条件,不影响试样进行试验.规定的数值要符合安装好的试样的具体情况.加速测量点就是试验台/试样的接口.对于庞大而笨重的试样(例如发动机、电动机或蓄电池),可以按DIN EN 60068-2-64的规定,与大众汽车康采恩主管技术科室一起商定,在试样固定点上取平均值.试样长度和试验顺序要在试验报告中叙述清楚.在汽车上,在低温或高温情况下,试验时可能出现振动疲劳应力,这时候,可以按5.2.1条提出的特定温度实现振动试验,电流供应如同5.2.1条中说的那样,要能维持持续运转.往后的全部试验都应适用于汽车上各种部件的试样,以至于3.5吨重的部件试样.技术要求在工作类别3.2情况下,取功能状态A在所有工作类别情况下,都不得有噪音.4.1.1 发动机附件的试验目的内燃机的振动是由两部分部件共同产生的:—正弦形的振荡激励,是由活塞运动的合力造成的—由所有其余部件运动合成的宽频带噪声激励起来的振动.试验两方面振动试验可以先后依次进行,也可以同时进行正弦形的振荡激励方法和实施按DIN EN 60068-2-6每一空间轴线的试验时间22 h频率变动时间1倍频程/min,对数的曲线1所表达的试样,说明在发动机内安装的汽缸在5个以内曲线2所表达的试样,说明在发动机内安装的汽缸在6个以内对于在发动机内安装≤5个汽缸和>5个汽缸的那些组件,可以使用双曲线来表达(见图4)振荡波形及其相应的值见图7,图8,表7和表8图7. – 发动机配件正弦曲线的振荡波形表7 – 发动机配件正弦曲线的振荡波形线数值振荡激励的宽带噪音按DIN EN 60068-2-64进行试验 每空间轴线的试验时间 22 h加速度有效值 181 m/s 2图8 - 发动机配件宽带噪音振荡波形表8 – 发动机配件宽带噪音振荡波形线数值频率 (Hz) 功率密度谱 [(m/s 2)2/Hz]10 10 100 10 300 0.51 500 20 2000 204.1.2 联动装置配件的试验 目的 联动装置振荡可分为两个部分: — 正弦曲线振荡激励,由活塞运动合力造成的 — 宽带噪音振荡激励,由齿轮摩擦和其他运动形成的合力造成的 — 注释:对于试样来说,联动装置内部产生的振荡可能会出现较高的值 试验 两次振荡试验可以先后依次进行,也可以同时完成 正弦曲线振荡激励 方法与实施按DIN EN 60068-2-6每空间轴线试验时间 22 h 频率变动时间 1倍频程/min,对数的 振荡波形及其相应的值见图9和表9图9.- 联动装置配件正弦曲线的振荡波形图表9 – 联动装置配件正弦曲线的振荡波形图值频率 (Hz) 加速度振幅 (m/s 2)100 30 200 60 440 60宽带噪音振荡激励实施按DIN EN 60068-2-64每空间轴线的试验时间 22 h 加速度有效值 96.6 m/s 2 振荡波形及其相应值见图10和表10图10.- 联动装置配件宽带噪音振荡波形图 表10.- 联动装置配件宽带噪音振荡波形频率 (Hz) 功率密度谱 [(m/s 2)2/Hz]10 10 100 10 300 0.51 500 5 2000 54.1.3 退耦吸气总管中零部件的试验 目的 该项试验专用于处在进气行程中的试样,这些试样不是固定地安装着的 在该试验区域的振荡是正弦曲线形的,是由于流进的空气的脉动而产生的 试验 振荡激励是正弦形的 方法和实施按DIN EN 60068-2-6每空间轴线的试验时间 22 h 频率变动时间 1倍频程/min,对数的 振荡波形及其相应值见图11和表11图11.- 退耦吸气总管中零部件正弦曲线振荡波形图表11.- 关于退耦吸气总管中零部件正弦曲线振荡波形的数值频率(Hz) 加速度振幅(m/s2)100 90200 180325 180500 801500 804.1.4车身配件试验目的该项试验专用于安装在弹簧承载的车身上的试样在这方面的振荡是宽带噪音,是由不良路段引起的试验振荡激励宽带噪音实施按DIN EN 60068-2-64每空间轴线上的试验时间8 h加速度有效值锐度1: 27.8 m/s2锐度2: 19.7 m/s2锐度3: 13.9 m/s2缺少锐度数据时,则使用锐度1,至于锐度3,只有同大众汽车康采恩主管科技部门商妥之后才能使用.降低或提高试验精度,对于一件特殊的试样来说,一定要与大众汽车康采恩相关的专业科室协商解决,并且详细记载下来.振荡波形及其相关值见图12和表12图12.- 车身配件宽带噪声振荡波形图表12.- 车身配件宽带噪声振荡波形值频率(Hz)功率密度谱锐度1[(m/s2)2/Hz]功率密度谱锐度2[(m/s2)2/Hz]功率密度谱锐度3[(m/s2)2/Hz]10 20 10 555 6.5 3.25 1.625180 0.25 0.125 0.0625300 0.25 0.125 0.0625360 0.14 0.07 0.0351000 0.14 0.07 0.0354.1.5行走机构零部件试验目的该项试验专用于非弹性体的试样(例如行走机构和齿轮的试样)在该试验范围内,振荡是宽带噪音,是由不良路段引起的.试验振荡激励宽带噪音实施按DIN EN 60068-2-64每空间轴线上的试验时间8 h加速度有效值 107.3m/s2振荡波形及其相应值见图13和表13图13.- 行走部分零部件宽带噪音振荡波形图表13.- 行走机构零部件振荡波形宽带噪音值频率(Hz) 功率密度谱[(m/s2)2/Hz]20 200 40 200 300 0.5 800 0.5 1000 3 2000 34.2 机械震动4.2.1 门和盖操纵系统/组件的连续冲击试验 目的 模拟门和盖使劲砰然关上 试验 试验实施按DIN EN 60068-2-29,冲击次数见表14 工作类别 1.2 冲击形式 半正弦的 标准技术要求 300 m/s 2, 6 ms 提出的较高技术要求 500 m/s 2, 11 ms 冲击方向 如果试样是固定在汽车上的,则与试样的方向相同. 表14 – 连续冲击试验的冲击次数安装处所 冲击次数驾驶员车门100 000 副驾驶员和客座车门50 000 后盖/门30 000 发动机舱盖3 000 技术要求 功能状态C4.2.2 车厢上操纵系统/组件的机械冲击试验 目的 模拟快速驶过马路牙子、石块和路边的深坑洼 试验 试验实施按DIN EN 60068-2-27 工作类别 3.2 冲击形式 半正弦的 技术要求 500 m/s 2, 6 ms 冲击方向 如果试样是固定在汽车上的,则与试样的方向相同 如果方向非已知的,则在该处空间的六个方向都要进行试验 冲击次数 空间的每个方向上冲击10次 技术要求 功能状态A4.3 坠地坠地试验试验 目的模拟坠地,如果是坠在混凝土地面上,势必损坏试样(例如前灯),所以不可这样坠地.试验试验实施按DIN EN 60068-2-32工作类别 1.1零部件数量 3每见试样坠地次数 2坠地高度 1 m接受坠物的地面混凝土地面坠地方向每个试样都有若干空间轴线每次坠地沿着一条空间轴线方向(即用壳体的一侧照准地面)每次坠地后都进行外观检查技术要求经过合格的外观检查,功能状态C4.4 卷边连接和插塞连接按VW 751 73-1和VW 603 304.5 汽车上电气和电子元件的插接件按VW 801 064.6 导线抗拉强度目的试样导线输出端上减轻拉力有效性的模拟试验工作类别 1.2在T RT的情况下加载按图纸在T OB的情况下加载按图纸s加载时间 30技术要求功能状态C5 气候方面的技术要求5.1 在恒温情况下的试验5.1.1预处理(环境空气中的无载存放)目的该项试验专用于正式试验开始前试样的预处理.。
QBYDQ-AF01.707.4-2010汽车电气、电子组件系统可靠性试验方法及要求 第4部分 气候负荷

4.3 温度变化 4.3.1 目的
试样在温度变化情况下工作状况的模拟。 4.3.2 试验
工作类别:工作模式 1.2 和 3.2。 a)试验时间:30 个周期; b)试验条件:见图 3 和表 2;
Q/BYDQ-AF01.707.4—2010
c)关于 Top•max 选用等级为 E 或 C 的样品,试验过程和试验温度均按图 4 和表 3 进行处理。
对于工作类别为 1.2 的样品,试验后应达到功能等级 C 的要求;对于工作类别为 3.2 的样品,试验后
应达到功能等级 A 的要求。
4.4 冷热冲击
4.4.1 目的
对由各部件和电路板之间热膨胀系数失谐引起的机构故障进行加速试验。
4.4.2 试验
5
Q/BYDQ-AF01.707.4—2010 工作类别:工作模式 1.1 或 1.2。 a) 试验温度:Tmax, Tmin; b) 试验时间:见总体要求表 7。 在每个温度点保存的时间需要测量。在高温段或低温段保存的时间可为 30min(样品重量小于 0.68kg)、 60min(样品重量在 0.68kg~4.53kg 之间)90min(样品重量大于 4.53kg)。这个时间应该从样品内部温度达 到比最高温度低 3°或比最低温度高 3°的时候开始计算。 4.4.3 要求 试验后,常温放置 2h 后功能应达到等级 D 的要求。 4.5 凝露(DEW)试验 4.5.1 目的 这项试验主要是要测试安装在有湿度的区域的电子元器件暴露在极限湿度下能否满足功能要求。 4.5.2 试验 工作类型:工作模式 1.1 或 3.2,见表 4。
表 4 凝露试验条件
工作类型
时间
试验条件
1.1
2h
放在(0/+2)℃的环境中,湿度不受控制
德国大众 吨以下汽车电气和电子部件试验标准

共 94 页第1页LV 1243.5吨以下汽车电气和电子部件试验项目、试验条件和试验要求目录页适用范围第一部分:电气要求1 参考标准2 通用部分2.1 概念和定义2.2 扫描率和测量值分辨率2.3 工作电压范围2.4 功能状态2.5 工作方式2.6 参数试验2.7 用漂移分析法不间断监控参数2.8 物理分析2.9 接口说明2.10 实施的限制条件3 试验选择3.1 试验选择表4 电气试验和要求4.1 E-01 长时间过电压4.2 E-02 瞬态过电压4.3 E-03 瞬态欠电压4.4 E-04 Jumpstart(跃变启动)4.5 E-05 Load Dump(甩负荷)4.6 E-06 叠加的交流电压4.7 E-07 供电电压缓慢下降和缓慢提升4.8 E-08 供电电压缓慢下降快速提升4.9 E-09 复位特性4.10 E-10 短时中断4.11 E-11 启动脉冲4.12 E-12 具有智能发电机调整装置的电压波动波形4.13 E-13 插脚中断4.14 E-14 插头中断4.15 E-15 极性变换4.16 E-16 接地偏移4.17 E-17 信号线路和负荷电路短路4.18 E-18 绝缘电阻4.19 E-19 静止电流4.20 E-20 击穿强度4.21 E-21 反馈4.22 E-22 过电流第二部分:环境要求5 通用部分5.1 参考标准5.2 概念和定义5.3 工作方式5.4 渗透温度5.5 参数试验5.6 用漂移分析法不间断监控参数5.7 物理分析6 使用特性曲线6.1 寿命设计6.2 温度集中试验7 试验选择7.1 试验选择表7.2 试验流程图8 机械试验和要求8.1 M-01 自由落体试验8.2 M-02 碎石冲击试验8.3 M-03 防灰尘试验8.4 M-04 振动试验8.5 M-05 机械冲击试验8.6 M-06 机械持续冲击试验9 气候试验和要求9.1 K-01 高温 / 低温存放9.2 K-02 梯度温度试验9.3 K-03 低温工作9.4 K-04 再次油漆温度9.5 K-05 温度冲击试验(部件)9.6 K-06 盐雾喷射试验,在舱外工作情况下9.7 K-07 盐雾喷射试验,在舱内工作情况下9.8 K-08 湿热循环试验9.9 K-09 湿热循环试验(附霜冻)9.10 K-10 防水保护— IPX0至IPX6X9.11 K-11 高压射流清洗 / 蒸汽射流清洗9.12 K-12 有浪涌水的温度冲击试验9.13 K-13 浸入式温度冲击试验9.14 K-14 恒定湿热试验9.15 K-15 与部件组一起的凝露试验9.16 K-16 温度冲击试验(无外壳)9.17 K-17 阳光辐射试验9.18 K-18 有害气体试验10 化学试验和要求11 寿命试验11.1 L-01 机械 / 液压耐久寿命试验11.2 L-02 高温耐久寿命试验11.3 L-03 温度交变耐久寿命试验12 附录12.1 试验流程图12.2 各种安装范围的典型温度集中试验12.3 高温耐久寿命试验计算模型12.4 温度交变耐久寿命试验计算模型12.5 恒定湿热试验计算模型—锐度212.6 凝露试验、试验箱程序设计和曲线12.7 汇总适用范围本标准是对3.5吨以下汽车使用的电气、电子、机械电子部件和系统试验项目、试验条件和试验要求的规定。
车辆电气测试方案

车辆电气测试方案一、前言随着车辆电子化的不断升级,车辆电气测试已经成为了新车开发过程中的一个重要环节。
而且,随着新能源汽车的不断发展,对车辆电气测试的要求也越来越高。
因此,本文将介绍一套适用于新车开发过程中的车辆电气测试方案,希望能够对开发人员提供帮助。
二、测试环境首先,需要构建适合的测试环境。
在这个测试环境中,需要有一个以太网交换机、多个基准机、车载协议转换器、电动车号制动踏板踏板测试架等硬件设备,并且需要在计算机上配置相应的测试软件来控制这些硬件设备。
需要注意的是,不同车型的测试环境是由不同的硬件设备组成的,因此在选择测试环境时需要考虑到开发过程中所需测试的车型,从而选择相应的测试设备。
三、测试内容在测试过程中,需要对车辆电气系统进行以下测试:1. 动力系统测试包括电机控制器、发电机、电动机等。
测试项目:•启动性能测试•性能参数测试•故障检测测试2. 刹车系统测试包括制动踏板、真空助力器、刹车泵、制动盘等。
测试项目:•制动灵敏度测试•停车性能测试•故障检测测试3. 灯光系统测试包括前照灯、后照灯、示宽灯、刹车灯等。
测试项目:•光强测试•光束方向测试•故障检测测试4. 仪表板测试包括中央控制台、显示器等。
测试项目:•功能测试•界面测试•故障检测测试5. 无线电系统测试包括收音机、导航仪、蓝牙电话等。
测试项目:•接收性能测试•传输性能测试•故障检测测试除了上述测试内容外,还需要对车辆的整车功能进行测试,如起步加速、行驶过程中加速、转向、停车、倒车等,以验证车辆的实际性能。
四、测试数据管理在测试过程中,需要对测试数据进行收集和管理。
对于每一项测试,都需要记录下测试结果,以便后续数据分析和维护。
需要建立数据库来储存测试数据,并且需要制定相应的数据格式和数据存储方式。
五、测试报告在测试完成后,需要对测试结果进行分析和总结,生成测试报告。
测试报告需要包含以下内容:•测试概述•测试环境•测试进程•测试数据•测试结果•结论和建议六、总结车辆电气测试是新车开发过程中不可或缺的环节。
- 1、下载文档前请自行甄别文档内容的完整性,平台不提供额外的编辑、内容补充、找答案等附加服务。
- 2、"仅部分预览"的文档,不可在线预览部分如存在完整性等问题,可反馈申请退款(可完整预览的文档不适用该条件!)。
- 3、如文档侵犯您的权益,请联系客服反馈,我们会尽快为您处理(人工客服工作时间:9:00-18:30)。
汽车电子基本电气负荷试验
通过以下的电气负荷可了解汽车电子面临的电子环境(12V 系统的)。
过电压实验
18V 实验:模拟发电机调节器失效,引起发电机输出电压上升,高于正
常电压的情况。
我们在实验中模块温度比模块最高温度小20 度,施加电压
18V,持续时间为60 分钟。
24V 实验:模拟辅助起动的情况。
我们在实验中模块温度在室温下,施
加电压24V,持续时间为60 秒。
叠加交流电压实验
模拟直流供电(配电系统)中残留的交流电。
实验条件:Upp = 1 V ,4V 两种等级;电源内阻为50 mΩ~100 mΩ;波形频率范围为50 Hz ~ 20 KHz;扫频波形类型为三角形或对数;扫频持续时间为120 s;扫频次数为5 次。
供电电压缓降和缓升
模拟蓄电池的逐渐放电和充电情况。
给模块的施加电压,0.5 ±
0.1 V/min 速率,将供电电压由USmax 降到0 V ,然后从0 V 升到USmax 。
供电电压中断
供电电压瞬间下降:模拟其他电路内的典型熔丝熔断时造成的影响。
注
意试验脉冲的上升和下降时间≤10 ms。
电压骤降复位性能:检验电压骤降的情况下,模块的复位性能,适用于
具有复位功能的设备。
供电电压以5 %速率从USmin 降到0.95 USmin,保持5 s,再上升到USmin ,至少保持10 s 并进行功能试验。
然后将电压降至0.9 USmin 等,以USmin 的5%梯度继续进行直到降到0V,然后再将电压升到。