合成氨工艺总流程与压缩机
合成氨生产工艺流程
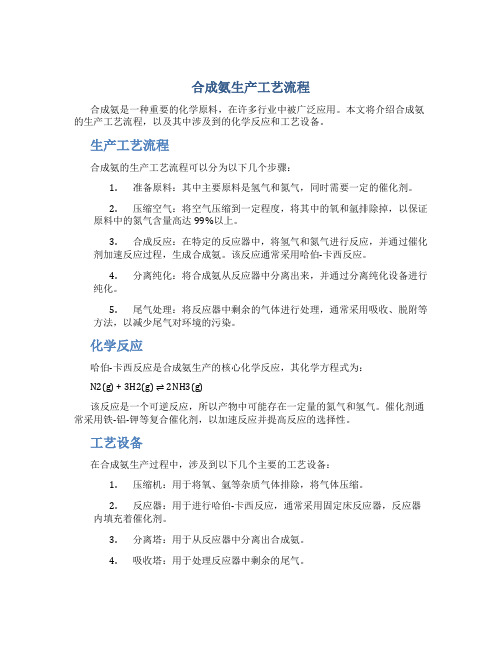
合成氨生产工艺流程合成氨是一种重要的化学原料,在许多行业中被广泛应用。
本文将介绍合成氨的生产工艺流程,以及其中涉及到的化学反应和工艺设备。
生产工艺流程合成氨的生产工艺流程可以分为以下几个步骤:1.准备原料:其中主要原料是氢气和氮气,同时需要一定的催化剂。
2.压缩空气:将空气压缩到一定程度,将其中的氧和氩排除掉,以保证原料中的氮气含量高达99%以上。
3.合成反应:在特定的反应器中,将氢气和氮气进行反应,并通过催化剂加速反应过程,生成合成氨。
该反应通常采用哈伯-卡西反应。
4.分离纯化:将合成氨从反应器中分离出来,并通过分离纯化设备进行纯化。
5.尾气处理:将反应器中剩余的气体进行处理,通常采用吸收、脱附等方法,以减少尾气对环境的污染。
化学反应哈伯-卡西反应是合成氨生产的核心化学反应,其化学方程式为:N2(g) + 3H2(g) ⇌ 2NH3(g)该反应是一个可逆反应,所以产物中可能存在一定量的氮气和氢气。
催化剂通常采用铁-铝-钾等复合催化剂,以加速反应并提高反应的选择性。
工艺设备在合成氨生产过程中,涉及到以下几个主要的工艺设备:1.压缩机:用于将氧、氩等杂质气体排除,将气体压缩。
2.反应器:用于进行哈伯-卡西反应,通常采用固定床反应器,反应器内填充着催化剂。
3.分离塔:用于从反应器中分离出合成氨。
4.吸收塔:用于处理反应器中剩余的尾气。
合成氨是一种十分重要的化学原料,其生产工艺流程麻烦且多种化学反应涉及其中,因此需要一系列的工艺设备来完成整个生产过程。
哈伯-卡西反应是该生产过程的核心反应,通过复合催化剂加速反应过程并提高反应的选择性。
通过合理的工艺流程设计和设备选型,能够实现高效、稳定的合成氨生产。
合成氨工艺

合成氨工艺陈昶君化九三20090118921.合成氨生产工艺流程图(1)煤为源头工艺路线:以无烟煤为原料生成合成氨常见过程是:造气->半水煤气脱硫->压缩机1,2工段->变换->变换气脱硫->压缩机3段->脱硫->压缩机4,5工段->铜洗->压缩机6段->氨合成->产品NH3造气过程为以煤为原料,用间歇式固定层常压气化法,反应方程为煤+氧气→二氧化碳二氧化碳+煤→一氧化碳煤+水蒸气→一氧化碳+氢气(2)天然气为源头采用天然气、焦化千气力原料的合成氨生产工艺流程包括:脱硫、转化、变换、脱碳、甲烷化、氨的合成、吸收制冷及输入氨库和氨吸收八个工序(一)脱琉原料气进入后,首先进入三段脱硫塔.第一、二段分别采用5—6%Na0H和10。
12%Na0H碱洗,第三段采用水洗。
在脱硫塔内。
气体中大部分无机硫和部分有机硫被碱液吸收,湿法脱硫后的焦化干气由压缩机道往一段转化炉对流段,加热至340—3500C后,进人干法脱硫槽。
干法脱硫剂通常采用氧化锰、氧化锌或钴—铜催化剂。
经干法脱硫后。
焦化干气中的总硫量要求低于3ppm.这里需要进行痕量硫的测定。
(二)转化经脱硫合格的焦化干气返回对流五段与来自废热锅炉的蒸汽混合,加热至500.610%后,进入一段转化炉(简称一段炉),控制共水碳比为3.5.4.0。
在催化刘作用下原料气转化为氢气、一氧化碳和二氧化碳。
反应所需的大量热能由转化炉两倜均匀分布的无焰燃烧喷嘴供给,反应温度控制在760—7的℃;出口气中残余甲烷含量要求小于10%。
一段沪出口气与空气压缩机送来的空气相混合,进人二段转化炉(简称二段炉)内燃烧,温度达到900一950。
C,在催化捌作用下,甲烷转化成一氧化碳和二氧化碳;二段炉出口气中残余甲烷应小于0.3%。
同时获取合成气所需的氮气,并控制氢、氮比在2.8—3.1之问。
在整个转化过程要进行原料气的总碳分析和一、二段炉出口气残余甲烷的分析。
合成氨的工艺流程

工艺流程 1.合成氨的工艺流程(1)原料气制备将煤和天然气等原料制成含氢和氮的粗原料气。
对于固体原料煤和焦炭,通常采用气化的方法制取合成气;渣油可采用非催化部分氧化的方法获得合成气;对气态烃类和石脑油,工业中利用二段蒸汽转化法制取合成气。
(2)净化对粗原料气进行净化处理,除去氢气和氮气以外的杂质,主要包括变换过程、脱硫脱碳过程以及气体精制过程。
①一氧化碳变换过程在合成氨生产中,各种方法制取的原料气都含有CO,其体积分数一般为12%~40%。
合成氨需要的两种组分是H2和N2,因此需要除去合成气中的CO。
变换反应如下:CO+H2OH→2+CO2 =-41.2kJ/mol 0298HΔ由于CO变换过程是强放热过程,必须分段进行以利于回收反应热,并控制变换段出口残余CO含量。
第一步是高温变换,使大部分CO转变为CO2和H2;第二步是低温变换,将CO 含量降至0.3%左右。
因此,CO变换反应既是原料气制造的继续,又是净化的过程,为后续脱碳过程创造条件。
②脱硫脱碳过程各种原料制取的粗原料气,都含有一些硫和碳的氧化物,为了防止合成氨生产过程催化剂的中毒,必须在氨合成工序前加以脱除,以天然气为原料的蒸汽转化法,第一道工序是脱硫,用以保护转化催化剂,以重油和煤为原料的部分氧化法,根据一氧化碳变换是否采用耐硫的催化剂而确定脱硫的位置。
工业脱硫方法种类很多,通常是采用物理或化学吸收的方法,常用的有低温甲醇洗法(Rectisol)、聚乙二醇二甲醚法(Selexol)等。
粗原料气经CO变换以后,变换气中除H2外,还有CO2、CO和CH4等组分,其中以CO2含量最多。
CO2既是氨合成催化剂的毒物,又是制造尿素、碳酸氢铵等氮肥的重要原料。
因此变换气中CO2的脱除必须兼顾这两方面的要求。
一般采用溶液吸收法脱除CO2。
根据吸收剂性能的不同,可分为两大类。
一类是物理吸收法,如低温甲醇洗法(Rectisol),聚乙二醇二甲醚法(Selexol),碳酸丙烯酯法。
合成氨各工序工艺详细流程

合成氨各工序工艺详细流程合成氨是一种重要的化工原料,广泛用于合成各类农药、肥料、化学品等。
下面将详细介绍合成氨的工序和流程。
合成氨的工艺主要分为三个步骤:气体净化、气体压缩和反应制氨。
1.气体净化:合成氨的原料气体主要有空气和甲烷。
在进入反应装置之前,需要进行气体净化处理。
空气首先经过过滤装置去除微小杂质、灰尘和固体颗粒物。
然后通过制冷装置降低气体温度,使其中的水蒸气凝结成液体,然后被排放。
甲烷通过碳分子筛吸附去除杂质。
这样可以保证反应装置中气体的纯度和稳定性。
2.气体压缩:经过气体净化后的空气和甲烷被分别压缩到一定压力,以满足反应器中的需求。
通常使用压缩机进行压缩,然后将压缩后的气体分别输送到反应器中。
3.反应制氨:反应制氨是整个过程的关键步骤。
通常采用哈柏法(Haber-Bosch)来实现反应制氨。
反应器中,高温高压的空气与甲烷的混合气体通过催化剂床进行催化反应。
常用的催化剂是铁与铁-铝的混合物,也可以加入少量的钾、镁等元素。
反应是一个放热反应,反应温度一般在380-550°C 之间,压力一般在1.7-3.5 MPa之间。
催化剂的存在可以提高反应速率,但也会增加反应的等离子体强度,导致了碳催化剂和蒸汽的选择性降低,产生非氮气杂质。
反应过程中,氮气与氢气进行反应生成氨气。
原料气体经过催化剂床后,反应转化率不高,需要多次通过催化剂床进行反应。
一般采用多级反应器和中间冷却装置,提高氨气的产率和纯度。
经过多级反应后,氨气还需要进行冷却和净化处理,以达到合成氨的纯度要求。
以上是合成氨的工序和流程的详细介绍。
合成氨的过程需要进行气体净化、气体压缩和催化反应制氨。
这个过程需要确保原料气体的纯度和稳定性,通过压缩提高原料气体的压力,催化剂的存在可以提高反应速率和转化率。
经过多级反应,最终得到高纯度的合成氨。
合成氨工艺的不断优化和改进,可以提高合成氨的生产效率和氨气的纯度,降低生产成本。
合成氨工艺流程
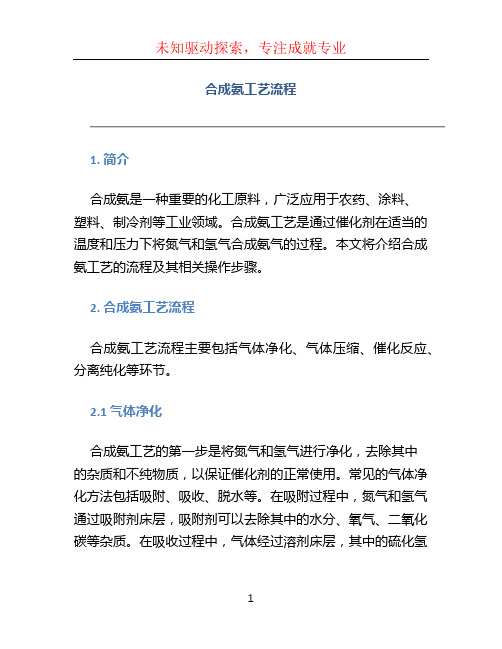
合成氨工艺流程1. 简介合成氨是一种重要的化工原料,广泛应用于农药、涂料、塑料、制冷剂等工业领域。
合成氨工艺是通过催化剂在适当的温度和压力下将氮气和氢气合成氨气的过程。
本文将介绍合成氨工艺的流程及其相关操作步骤。
2. 合成氨工艺流程合成氨工艺流程主要包括气体净化、气体压缩、催化反应、分离纯化等环节。
2.1 气体净化合成氨工艺的第一步是将氮气和氢气进行净化,去除其中的杂质和不纯物质,以保证催化剂的正常使用。
常见的气体净化方法包括吸附、吸收、脱水等。
在吸附过程中,氮气和氢气通过吸附剂床层,吸附剂可以去除其中的水分、氧气、二氧化碳等杂质。
在吸收过程中,气体经过溶剂床层,其中的硫化氢等有毒气体被吸收掉。
同时,还可以使用脱水剂去除气体中的水分。
2.2 气体压缩在气体净化后,将净化后的氮气和氢气进行压缩,提高其压力,以便后续的催化反应。
氮气和氢气分别进入压缩机进行压缩,压缩机通常采用多级压缩,保证气体压力的稳定和可控。
2.3 催化反应经过气体压缩后的氮气和氢气进入催化剂床层,进行合成氨的催化反应。
催化剂通常采用铁、钼或镍等金属催化剂,催化剂在适当的温度和压力下,使氮气和氢气发生反应,生成合成氨气。
催化反应是一个放热反应,需要控制温度以避免过高的温度导致副反应的发生。
2.4 分离纯化经过催化反应生成的合成氨气含有大量的副产物和未反应的氮气、氢气等杂质。
在分离纯化环节中,需要进行吸附、压缩、蒸馏等操作,将合成氨气中的杂质去除,提高纯度。
常见的分离纯化方法包括低温吸附法、压缩法和蒸馏法。
3. 工艺条件和参数合成氨工艺的实施需要满足一定的工艺条件和参数,以确保反应的进行和产出的质量。
常见的工艺条件和参数包括温度、压力、催化剂种类和配比、气体流速等。
3.1 温度催化反应的温度是合成氨工艺中的关键参数之一。
温度过高会导致副反应的发生,影响合成氨气的产量和纯度;温度过低则会降低反应速率。
一般情况下,催化反应的温度在300-500°C之间控制。
合成氨各工序实用工艺详细流程

一、合成氨装置工艺流程说明合成氨装置由一氧化碳变换、酸性气体脱除、硫回收、气体精制、合成气压缩、氨合成、冷冻工序共7个工序组成。
1.一氧化碳变换工序工艺流程说明来自煤气化装置的粗煤气(242.25℃ 6.25MPag)进入变换原料气分离器(S04101),分离夹带的水分,再进入煤气过滤器(S04102),除去煤气中的其他杂质。
净化后的煤气经煤气换热器(E04101)加热到280℃左右,后进第一变换炉(R04101)进行变换反应,出第一变换炉的高温变换气进煤气换热器(R04101)换热,在煤气换热器(E04101)中加热煤气化装置来的粗煤气,换热后的变换器进入中压废热锅炉(E04103)中,在此,副产 2.6MPa(G)的中压饱和蒸汽,然后在265℃左右进入第二变换炉(R04102)。
第二变换炉(R04103)出来的变换气经过中压废锅II(E04102)调温至260℃左右后进第三变换炉(R04103)继续进行反应。
出第三变换炉(R04103)的变换气进低压废热锅炉(E04105)副产0.6MPa(G)的低压饱和蒸汽,此时变换气温度降至202℃左右,进入1#变换气分离器(S04104)分离出冷凝液后,变换气继续进入锅炉给水预热器(E04113)降温,在2#变换气分离器(S04104)分离冷凝液后进入除盐水预热器II(E04107),在5#变换分离器(S04110)中分离出冷凝液后继续进入除盐水预热器(E04114)中,此时温度降至70℃,经3#变换气分离器(S04105)后分离冷凝液,而后再进入变换气水冷器(E04108),冷却至40℃后进入酸性气体脱除工序。
从1#、2#和5#分离器(S04103、S04104、S04110)出来的高温冷凝液经冷凝液闪蒸槽(S04109)汇合并闪蒸后,液相经冷凝液泵II(P04103A/B)加压后,直接送往煤气化装置。
一氧化碳变换工序的低温工艺冷凝液、低温甲醇洗来的洗氨水以及塔顶回流液进入冷凝液汽提塔上部(冷凝液汽提塔操作压力0.4MPaa),在冷凝液汽提塔中用来自管网的低压蒸汽汽提,从冷凝液汽提塔底部出来的汽提后工艺冷凝液NH3含量小于10ppm,从冷凝液汽提塔顶部出来的气体尾气在汽提气水冷器(E04109)中用循环水冷却到40℃后进尾气分离器(S04107),尾气分离器(S04107)分离出来的冷凝液一部分送到冷凝液汽提塔顶部作为回流液,约有33-55%的冷凝液送氨法脱硫装置,出汽尾气分离器(S04107)的汽提尾气送火炬焚烧处理。
合成氨工艺设计总流程及压缩机
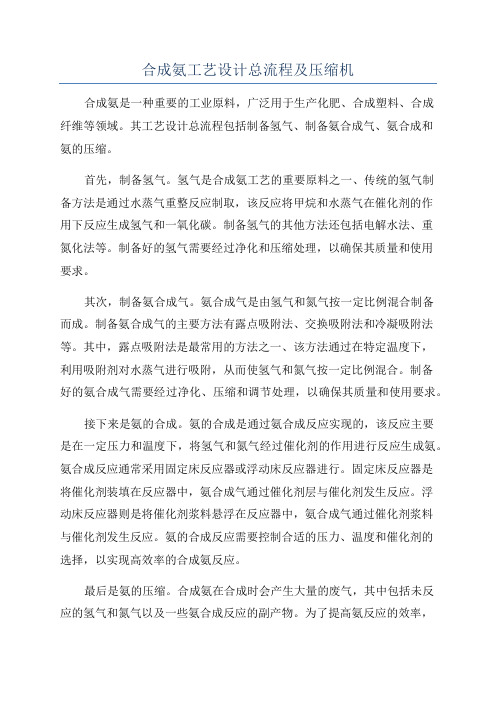
合成氨工艺设计总流程及压缩机合成氨是一种重要的工业原料,广泛用于生产化肥、合成塑料、合成纤维等领域。
其工艺设计总流程包括制备氢气、制备氨合成气、氨合成和氨的压缩。
首先,制备氢气。
氢气是合成氨工艺的重要原料之一、传统的氢气制备方法是通过水蒸气重整反应制取,该反应将甲烷和水蒸气在催化剂的作用下反应生成氢气和一氧化碳。
制备氢气的其他方法还包括电解水法、重氮化法等。
制备好的氢气需要经过净化和压缩处理,以确保其质量和使用要求。
其次,制备氨合成气。
氨合成气是由氢气和氮气按一定比例混合制备而成。
制备氨合成气的主要方法有露点吸附法、交换吸附法和冷凝吸附法等。
其中,露点吸附法是最常用的方法之一、该方法通过在特定温度下,利用吸附剂对水蒸气进行吸附,从而使氢气和氮气按一定比例混合。
制备好的氨合成气需要经过净化、压缩和调节处理,以确保其质量和使用要求。
接下来是氨的合成。
氨的合成是通过氨合成反应实现的,该反应主要是在一定压力和温度下,将氢气和氮气经过催化剂的作用进行反应生成氨。
氨合成反应通常采用固定床反应器或浮动床反应器进行。
固定床反应器是将催化剂装填在反应器中,氨合成气通过催化剂层与催化剂发生反应。
浮动床反应器则是将催化剂浆料悬浮在反应器中,氨合成气通过催化剂浆料与催化剂发生反应。
氨的合成反应需要控制合适的压力、温度和催化剂的选择,以实现高效率的合成氨反应。
最后是氨的压缩。
合成氨在合成时会产生大量的废气,其中包括未反应的氢气和氮气以及一些氨合成反应的副产物。
为了提高氨反应的效率,并方便运输和储存,需要对合成氨进行压缩处理。
氨的压缩通常采用多级压缩的方式进行,通过多级压缩机将合成氨的压力提高到所需的工艺压力。
压缩机的选型需要根据氨的流量和压力要求进行,压缩机的排气温度需要进行控制,以避免催化剂受热而失效。
总之,合成氨工艺设计总流程包括制备氢气、制备氨合成气、氨的合成和氨的压缩。
其中制备氢气和制备氨合成气是提供合成氨原料的关键步骤,氨的合成是核心反应步骤,氨的压缩则是提高效率和方便运输的必要步骤。
合成氨工艺流程

将无烟煤(或焦炭)由炉顶加入固定床层煤气发生炉中,并交替向炉内通入空气和水蒸汽,燃料气化所生成的半水煤气经燃烧室、废热锅炉回收热量后送入气柜。
? ???? 半水煤气由气柜进入电除尘器,除去固体颗粒后依次进入压缩机的Ⅰ、Ⅱ、Ⅲ段,加压到1.9~2.0Mpa,送入脱硫塔,用溶液或其他脱硫溶液洗涤,以除去硫化氢,随后,气体经饱和塔进入热交换器,加热升温后进入一氧化碳变换炉,用水蒸汽使气体中的一氧化碳变为氢。
变换后的气体,返回热交换器进行降温,并经热水塔的进一步降温后,进入变换器脱硫塔,以除去变换时产生的硫化氢。
然后,气体进入二氧化碳吸收塔,用水洗法除去大部分二氧化碳。
脱碳后的原料进入压缩机Ⅳ、Ⅴ段,升压到压缩机12.09~13.0Mpa后,依次进入铜洗塔和碱洗塔,使气体中残余的一氧化碳和二氧化碳含量进一步降至20(ppm)以下,以满足合成氨的要求。
????? 净化后的原料气进入压缩机的最后一段,升压到30.0~32.0?MPa进入滤油器,在此与循环压缩机来的循环气混合,经除油后,进入冷凝塔和氨冷器的管内,再进入冷凝塔的下部,分离出液氨。
分离出液氨后的气体进入冷凝塔上部的管间,与管内的气体换热升温后进入氨合成塔。
在高温高压并有催化剂存在的条件下,将氮氢气合成氨。
出合成塔的气体中,约含氨10~20%,经水冷器与氨冷器将氨液化并分离后,其气体进入循环压缩机循环使用。
分离出的液氨进入液氨贮槽。
?原料气的制备:制备氢氮比为3:1的半水煤气???? ?即造气。
将无烟煤(或焦炭)由炉顶加入固定床层煤气发生炉中,并交替向炉内通入空气和水蒸汽,燃料气化后生成氢氮比为3:1的半水煤气。
整个生产过程由煤气发生炉、燃烧室、废热锅炉、气柜等设备组成。
????? 固定床半水煤气制造过程由吹风、上吹制气、下吹制气、二次上吹、空气吹净等5个阶段构成,为了调节氢氮比,在吹风末端要将部分吹风气吹入煤气,这个过程通常称为吹风回收。
????? 吹风阶段:空气从煤气炉的底部吹入,使燃料燃烧,热量贮存于燃料中,为制气阶段碳与水蒸汽的反应提供热量。
- 1、下载文档前请自行甄别文档内容的完整性,平台不提供额外的编辑、内容补充、找答案等附加服务。
- 2、"仅部分预览"的文档,不可在线预览部分如存在完整性等问题,可反馈申请退款(可完整预览的文档不适用该条件!)。
- 3、如文档侵犯您的权益,请联系客服反馈,我们会尽快为您处理(人工客服工作时间:9:00-18:30)。
合成氨工艺总流程本装置以中原油田天然气为原料,采用传统流程的一二段烃类水蒸气转化,高低变,脱碳及甲烷化法。
1、原料气压缩和脱硫来自界区,压力2.25巴(绝)、温度30C,含总硫50p.p.m的天然气,经分离器(01-F001)分离掉所带油水后,进入原料气压缩机(01-K001), 经四段压缩至52.5巴(绝)温度114C。
出原料气压缩机的气体与来自合成压缩机(07-K001)的少量合成气相汇合,控制含2-5%H2,作为予脱硫钴-钼加氢转化用。
一二段烃类水蒸汽转化是在镍催化剂上进行,硫及其化合物对镍催化剂毒害极大,要求进入转化的原料气中含硫量在O.lp.p.m以下,因此转化前必须脱硫。
经压缩和返氢后的原料气,入对流段盘管(03-B002E04)加热至370C,于钻-钼加氢反应器(01-R001)中反应,将有机硫转化为无机硫。
然后在氧化锌脱硫槽(01-R002A/B)里硫被脱除,控制含硫小于O.lp.p.m。
2、转化经脱硫的原料气与来自工艺冷凝液汽提塔(05-C003)的水蒸汽和来自冰机的蒸汽透平(09-MT01 )或发电机蒸汽透平(85-MT01)的背压蒸汽,按比例调节进行混合,控制水碳比为 2.75左右、温度在372C o 此原料-水蒸汽混合气相继进入一段转化炉对流段盘管(O3-BOO2EO1A)和(03-B002E01B )换热,在两盘管间还设置喷雾温度调节器(03-B002E08)用它来调节出盘管(03-B002E01B)的混合气加热至580C。
此混合气从转化炉管顶部进入,在镍催化剂作用下进行转化反应。
出一段炉的转化气压力43.5巴、温度804 C,含16.3%CH4。
含CH4I6.3%的一段转化气自二段炉(03-R001)底部进入,经中心管至炉顶,与来自空压机( 02-K001 ),压缩至45 巴,途径加热盘管(03-B002E03)加热至500C的工艺空气相混合,于炉中上部空间进行燃烧反应,反应后气体温升至1250C左右。
此高温气体相继流经炉中催化剂床层,继续进行转化反应。
出二段炉的转化气(工艺气),温度983C左右,残余甲烷含量0.9% 以下。
为回收此高温工艺气的热量,入工艺气冷却器( 03E001)使之产生328C、125巴的高压蒸汽。
出(03-E001)温度588C的工艺气继续入高压蒸汽过热器( 03-E002) ,喷雾温度调节器( 03-E005) ,控制其出转化工序的工艺气温度为370 C左右。
经预热后的锅炉给水注入汽包( 03-D001) ,汽包与工艺气冷却器 ( 03-E001) 、废热锅炉( 04-E001 )和辅助锅炉相连通,设计为自然循环。
自汽包输出的高压蒸汽,依次流经高压蒸汽过热器( 03-E002) (03-B003E01)和(03-B002E02),将蒸汽过热至535C,再分别送入冰机和发电机的蒸汽透平作动力。
3、变换CO 变换采取高低变流程。
370 C的转化工艺气,自高温变换炉顶部进入,于铁-铬系催化剂条件下进行反应,温升到444C, CO含量降至3.87%。
高变气由炉底出来,入废热锅炉(04-E001),回收热量产生高压蒸汽,高变气被冷却至375C, 继入锅炉给水预热器(04-E002),降温至204C,而后入低温变换炉。
低变是在铜-锌-铝系催化剂条件下进行反应,反应后气体温升至236C, CO含量为0.36%。
低变气在锅炉给水预热器(04-E003)中换热,冷却至176C,此温度下已有水蒸汽冷凝。
为便于低变催化剂的升温还原,还专设置一套氮循环系统。
4、脱碳CO2 脱除,采用节能型的苯菲尔脱碳流程。
为回收低变气中的热能,含CO217%左右的低变气依次流经气体冷却器(05-E001),再沸器(05-E002)及脱盐水预热器(05-E009)而得以产生低压蒸汽,发生汽提蒸汽和加热了脱盐水。
低变气冷却至95C左右,自吸收塔(05-C001 )下部进入,与塔顶喷淋下来的吸收液(贫液)逆流接触。
经下塔吸收后的气体中CO2 含量降至0.4%,再经上塔吸收,从塔顶逸出的脱碳气,温度70C,CO2含量却为0.1%。
而后经分离器(05-F002)回收随气体带出的溶液。
吸收塔底流出的富液,经水力透平(05-MT01 )送至解吸塔(05-C002)顶部,溶液减压闪蒸出部分水蒸气和二氧化碳,然后向下流经解吸塔填料,此时溶液与再沸器(05-E002)及闪蒸槽(05-D002)返回的蒸汽逆流接触,实现汽提,达到再生目的。
解吸塔顶部压力控制为1.52巴(绝)时,塔底溶液温度为118C左解吸塔底流出的溶液,入闪蒸槽(05-D002),经五级闪蒸压力降至0.89巴(绝),此时溶液温度为100C左右。
闪蒸释放出的蒸汽由蒸汽喷射器(05-A001,05-A002,05-A003,05-A004)和蒸汽压缩机(05-K001 )注回解吸塔。
为节省蒸汽压缩机功耗,在最后一级闪蒸溶液用锅炉给水做适当加热。
再生好的溶液,经贫液泵(05-P001A/B)送出,分两路送入吸收塔:一路为大致25%的溶液量,经热水加热器(05E010A/B),将溶液冷却至70C入上塔;另一路则将其与75%的溶液量,不经冷却器直接送入下塔。
且溶液泵(05-P001A/B)与水力透平(05-MT01 )是在同一轴上,由此水力透平所回收的能量可以补偿溶液泵轴功率的40%。
脱碳系统中,自分离器(05-F001 )分离出来的工艺冷凝液,经冷凝液预热器(05-E008),被冷却至98C。
由冷凝液泵(05-P006A/B)送经冷凝液预热器(05-E011A/B)被加热后入汽提塔(05-C003),与来自冰机蒸汽透平( 09-MT01 )或发电机蒸汽透平 (85-MT01 )的背压蒸汽与塔中逆流接触,进行汽提。
使用水蒸汽量每小时15吨。
塔顶逸出的汽提蒸汽(其中包括转化、变换的付产物甲醇、乙醇、氨等)送往转化工序。
从解吸塔顶(1.52巴、94C)排出的CO2气,入脱盐水预热器(05-E004A/B)、水冷却器(05-E007A/B)换热,冷却至40C。
此CO2 气冷凝液于(05-F003)和(05-F005)分离器中将冷凝液分离下来,用泵(05-P002A/B)将少量冷凝液分别送入解吸塔顶的洗涤塔板、闪蒸槽的洗涤料盘作洗涤水和溶液泵、水力透平的清洗液。
而其余冷凝液经(05-E008)预热至120C,送回(05-E001 )作为锅炉给水用。
分离器分离出的CO2气,送尿素装置CO2气压缩机的吸入端。
5、甲烷化脱碳气中含0.1%CO2、0.44%CO,是远远超过对合成气中(C0+CO2)vlOp.p.m的要求,为此采用甲烷化法除去少量的CO和CO2。
70C的脱碳气,在换热器(06-E001)中被加热至300C,入甲烷化炉(06-R001),反应放热,温升至336 C左右。
此热气在换热器(06-E001)中被冷却至100C。
继入水冷器(06-E003)中,冷却至40C,气中含(CO+ CO2)<10p.p.m,成为合格的N2.战混合气,即新鲜气。
6、合成气的压缩及氨合成氮与氢在铁催化剂条件下合成氨,当压力98.24巴、440C时,平衡氨含量为17.92%。
因此,大量未参与合成的N2.H2 应循环使用。
同时,为降低合成氨能耗,采用了径向合成塔和两级氨冷。
甲烷后的工艺气(新鲜气),在38.3巴、40 C下,经分离器(07-F001)分离水份,入离心式合成气压缩机(07-K001 ),经一段压缩至65.4 巴、112C,此时少量气体送脱硫,用于钻-钼加氢,大量气体经中间冷却器(07-E002)和分离器(07-F002)冷却分离后,入合成气压缩机高压缸,压缩至101.95巴、100C。
为保证催化剂不受毒害,出高压缸的新鲜气进入第一氨冷器(08-E005),冷却器至5C此时新鲜气的水蒸汽和CO2 气被冷凝,于分离器(07-F003)中分离掉。
自(07-F003)逸出的新鲜气与(08-E005)出口的回路气在管路中汇合,由于回路气中部分液氨的汽化,使汇合后的循环气降温至0.9C,继入第二氨冷器(08-E006),降温至-10 C,在该温度下大部分气氨冷凝。
随之物流入氨分离器(08-F001),分离下来的液氨入氨闪蒸槽(08-D001),闪蒸后的液氨,用泵(08-P001A/B)送往尿素装置或球罐储存,从(08-F001)分理出的冷气,经冷热交换器(08-E004)回收冷量,而后入(07-K001)循环段进行压缩,以补充回路压降的损失。
出循环段的气体(105.8巴、32C), 经热交换器(08-E002),温升至239 C左右,入合成塔(08-R001)。
105巴、239C、含4.12%NH3的循环气,流经三床层的径向合成塔,在铁催化剂上进行合成反应。
出塔气压力为101巴、414 C、含16.36%NH3,入废热锅炉(08-E001 )回收热量,产生127巴、329C的高压蒸汽。
合成气被冷却至275C,继入(08-E002)、(08-E003)、(08-E004)换热器换热,合成气温度分别降至53C、38C、23C,而后入第一氨冷器(08-E005)。
出第一氨冷器的回路气与新鲜气相汇合为循环气。
这样形成的一个循环过程,称之“合成回路” 。
因新鲜气中含惰气(CH4+Ar) 1.86%,在不断循环过程中惰气的含量会积累增多,影响氨的生成。
为此,出(07-K001)循环段的气体需要放空一部分,以控制循环气中惰气含量。
此放空气送往氨回收装置。
7、冷冻来自第二氨冷器(08-E006)的气氨(-15C、2.36巴)来自第一氨冷器(08-E005)及气体冷却器(10-E004)的气氨(05C、4.38巴),分别进入氨压缩机又称冰机(09-K001 )一段的吸入侧,经一段压缩的出口气氨(86C、9.34巴),入中间冷却器(09-E005)冷却后与从氨闪蒸槽(09-D001)来的气氨相汇合,于42C、9.08巴压力下进入(09-K001)的二段吸入侧,压缩至16.6巴、100C,经水冷器(09-E002A/B)冷却冷凝,气氨液化为液氨,入氨受槽(09-D002)。
冰机由蒸汽透平(09-MT01)驱动。
氨受槽(09-D002)中的液氨,温度较高,可称为热氨。
此热氨流经换热器(09-E003A/B)、氨闪蒸槽(09-D001)及产品氨加热器(09-E004)与来自闪蒸槽(08-D001、的冷氨进行热交换,使之冷却、减压降温,重新作为冷冻剂送往氨冷器(08-E005)、(08-E006)和气冷器(10-E004)使用。
冷氨用泵(08-P001A/B、提压至22.6巴、20C送往尿素装置。
8、氨回收氨合成回路的放空气及氨闪蒸槽(08-D001、的闪蒸汽(驰放气)中氨需要回收。