稀土分离冶炼工艺流程图
稀土生产与分离工业工艺流程

稀土生产与分离工业工艺流程一、稀土选矿选矿是利用组成矿石的各种矿物之间的物理化学性质的差异,采用不同的选矿方法,借助不同的选矿工艺,不同的选矿设备,把矿石中的有用矿物富集起来,除去有害杂质,并使之与脉石矿物分离的机械加工过程。
当前我国和世界上其它国家开采出来的稀土矿石中,稀土氧化物含量只有百分之几,甚至有的更低,为了满足冶炼的生产要求,在冶炼前经选矿,将稀土矿物与脉石矿物和其它有用矿物分开,以提高稀土氧化物的含量,得到能满足稀土冶金要求的稀土精矿。
稀土矿的选矿一般采用浮选法,并常辅以重选、磁选组成多种组合的选矿工艺流程。
内蒙古白云鄂博矿山的稀土矿床,是铁白云石的碳酸岩型矿床,在主要成分铁矿中伴生稀土矿物(除氟碳铈矿、独居石外,还有数种含铌、稀土矿物)。
采出的矿石中含铁30%左右,稀土氧化物约5%。
在矿山先将大矿石破碎后,用火车运至包头钢铁集团公司的选矿厂。
选矿厂的任务是将Fe2O3从33%提高到55%以上,先在锥形球磨机上磨矿分级,再用圆筒磁选机选得62~65%Fe2O3的一次铁精矿。
其尾矿继续进行浮选与磁选,得到含45%Fe2O3以上的二次铁精矿。
稀土富集在浮选泡沫中,品位达到10~15%。
该富集物可用摇床选出REO 含量为30%的粗精矿,经选矿设备再处理后,可得到REO60%以上的稀土精矿。
二、稀土冶炼方法稀土冶炼方法有两种,即湿法冶金和火法冶金。
湿法冶金属化工冶金方式,全流程大多处于溶液、溶剂之中,如稀土精矿的分解、稀土氧化物、稀土化合物、单一稀土金属的分离和提取过程就是采用沉淀、结晶、氧化还原、溶剂萃取、离子交换等化学分离工艺过程。
现应用较普遍的是有机溶剂萃取法,它是工业分离高纯单一稀土元素的通用工艺。
湿法冶金流程复杂,产品纯度高,该法生产成品应用面广阔。
火法冶金工艺过程简单,生产率较高。
稀土火法冶炼主要包括硅热还原法制取稀土合金,熔盐电解法制取稀土金属或合金,金属热还原法制取稀土合金等。
稀土生产工艺流程

稀土生产工艺流程稀土是指地壳中数量非常稀少的一类金属元素,目前主要用于制造高科技产品和绿色能源设备。
由于其稀少性和广泛应用,稀土的生产工艺流程具有很大的科学性和复杂性。
下面是一种常见的稀土生产工艺流程的简要介绍。
稀土的生产过程通常可以分为开采、选矿、冶炼和纯化四个环节。
首先是开采环节。
开采是从稀土矿石中提取出有用金属元素的过程。
常见的开采方法包括露天开采和地下开采。
露天开采是指直接将矿石从地表开采出来,适用于砂矿和土矿等表层矿石;地下开采是指通过化验,挖掘机,卡车和运送设备等设备组成的整套设备,依靠方式开采矿石。
接下来是选矿环节。
选矿是指根据稀土矿石的化学成分和物理性质进行分选的过程,目的是更好地提取矿石中的稀土金属元素。
根据稀土矿石的性质,常见的选矿方法包括重选、浮选、磁选、电选和化学选矿等。
重选是根据矿石的密度差异进行分选,浮选是通过气泡吸附使稀土矿石浮起来,磁选是根据矿石的磁性差异进行分选,电选是利用数十万伏的电场对矿石进行分离,化学选矿是利用化学反应对矿石进行分选。
然后是冶炼环节。
冶炼是指将选矿得到的稀土矿石提炼成稀土金属元素的过程。
根据稀土矿石的性质和市场需求,常见的冶炼方法包括矿石熔炼法、水热法、浸出法、萃取法和电解法等。
其中,矿石熔炼法是将稀土矿石加热至高温,溶解成稀土金属,然后通过凝固和分离等操作,得到纯净的稀土金属;水热法是将稀土矿石和水进行反应,利用水热条件下稀土金属与其他杂质的不同溶解度进行分离;浸出法是通过酸性溶液将稀土金属溶解出来,再通过沉淀、过滤和烘干等过程得到纯净的稀土金属;萃取法是利用有机溶剂将稀土金属从矿石中分离出来;电解法是利用电解设备对稀土矿石进行电解,将含有稀土金属的阳离子还原成纯净的稀土金属。
最后是纯化环节。
纯化是指对冶炼得到的稀土金属元素进行纯净化处理,去除杂质,提高纯度。
常见的纯化方法包括溶液萃取、电解析、晶体生长法等。
溶液萃取是利用有机溶剂对稀土金属进行分离和纯化;电解析是利用电解设备对稀土金属进行电解,将杂质还原成纯净的稀土金属;晶体生长法是通过不断蒸发溶液,使稀土金属结晶出来,从而提高纯度。
稀土生产工艺流程图资料

稀土生产工艺流程图白云鄂博矿 矿石粉碎 弱磁、强磁选矿 铁精矿强磁中矿、尾矿火法生产线汽车尾气净化器 永磁电机 节能灯风力发电机 各种发光标牌 电动汽车 电动核磁共振 自行车磁悬浮磁选机看稀土原矿生产新闻中有离子型稀土矿原矿“堆浸工艺”这个词,是怎样的工艺?怎么翻译成英文或日文?堆浸提金是指将低品位金矿石或浮选尾矿在底垫材料上筑堆,通过氰化钠溶液循环喷淋,使矿石中的金、银溶解出来。
含金贵液用活性炭吸附、锌置换沉淀或直接电解沉积等方法回收金,提金后的尾渣经消毒后排放。
堆浸法提金具有工艺简单、操作容易、设备少、动力消耗少、投资省、见效快、生产成本低等特点。
堆浸用于处理0.5-3g/t的低品位矿石,金的回收率50-80%,甚至能达到90%。
因此,堆浸法使原来认为无经济价值的许多小型金矿、低品位矿石、尾矿或废石现在都能得以经济回收。
我国在二十世纪八十年代将堆浸法广泛用于工业生产。
堆浸法适合处理以下几种矿产资源:1、规模较大,以前认为不能利用的低品位金银矿;2、矿山开采过程中剥离的低品位含金“废石”;3、地质坑探和矿山掘进中采掘出的中低品位含金矿石;4、含金品位稍高,但规模较小,不宜建机械化选厂的金银矿;5、采用常规氰化法处理经济上不利的金矿;6、含金的冶炼烧渣、高品位尾矿和含有金的大型废石场。
堆浸提金生产工艺主要由堆浸场地的修筑、矿石的预处理(破碎或制粒)、筑堆、喷淋浸出、含金贵液中金的回收以及废矿堆的消毒、卸堆等几部分组成。
堆浸的生产成本:尾矿堆浸成本度大约在30-40元/吨,原矿堆浸成本大约在40-50元/吨.我想问一下现在离子型稀土矿的开采方法是什么方法成本怎样计算需要什么试剂?????????????离子型稀土第一代提取工艺,可简述为"异地提取工艺",或归结为"池浸工艺"。
其主要工艺过程为:表土剥离→开挖含矿山体、搬运矿石→浸矿池→将按一定比例(浓度要求)配置的电解质溶液作为"洗提剂"或"浸矿剂",加入浸矿池,溶液对池中含"离子相"稀土矿石进行"渗滤洗提"或"淋洗" →溶液中活泼离子与稀土离子交换,"离子相"稀土从含矿载体矿物中交换出来,成为新状态稀土;加入"顶水",获含稀土母液;母液经管道或输液沟流入集液池或母液池,然后进入沉淀池;浸矿后废渣从浸矿池中清出,异地排放→在沉淀池中加入沉淀剂、除杂剂,使稀土母液中稀土除杂、沉淀,获混合稀土;池中上清液经处理后,返回浸矿池,作"洗提剂"循环使用→混合稀土经灼烧,获纯度≥92%的混合稀土氧化物。
稀土冶炼分离核心技术
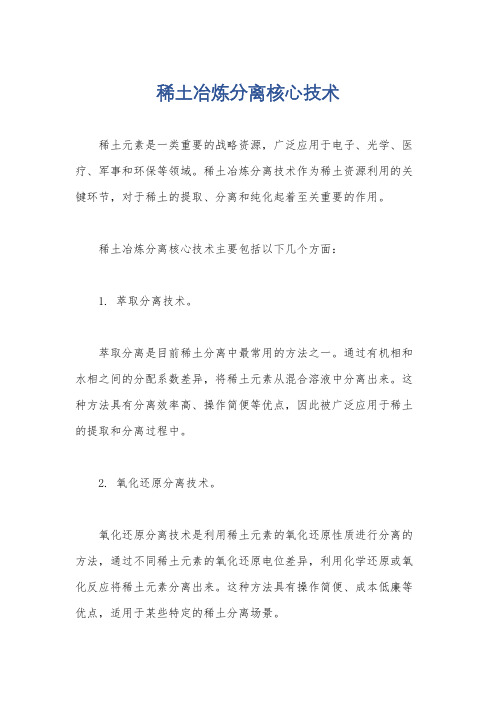
稀土冶炼分离核心技术
稀土元素是一类重要的战略资源,广泛应用于电子、光学、医疗、军事和环保等领域。
稀土冶炼分离技术作为稀土资源利用的关键环节,对于稀土的提取、分离和纯化起着至关重要的作用。
稀土冶炼分离核心技术主要包括以下几个方面:
1. 萃取分离技术。
萃取分离是目前稀土分离中最常用的方法之一。
通过有机相和水相之间的分配系数差异,将稀土元素从混合溶液中分离出来。
这种方法具有分离效率高、操作简便等优点,因此被广泛应用于稀土的提取和分离过程中。
2. 氧化还原分离技术。
氧化还原分离技术是利用稀土元素的氧化还原性质进行分离的方法,通过不同稀土元素的氧化还原电位差异,利用化学还原或氧化反应将稀土元素分离出来。
这种方法具有操作简便、成本低廉等优点,适用于某些特定的稀土分离场景。
3. 结晶分离技术。
结晶分离技术是通过溶液中不同稀土元素的溶解度差异,将其
逐步结晶分离出来的方法。
这种方法适用于某些特定的稀土元素分
离场景,具有分离效率高、产品纯度高等优点。
4. 膜分离技术。
膜分离技术是利用特定的膜材料对稀土元素进行筛选分离的方法。
这种方法具有操作简便、环保节能等优点,适用于稀土元素的
精细分离和纯化过程。
总的来说,稀土冶炼分离核心技术是稀土资源利用的关键环节,随着科技的不断进步和创新,稀土分离技术将会不断完善和发展,
为稀土资源的高效利用和保护环境做出更大的贡献。
稀有稀土金属冶炼

稀有稀土金属冶炼稀有稀土金属是指在自然界中含量极少的金属元素,具有重要的战略地位和广泛的应用价值。
由于其含量极少,因此稀有稀土金属的开采、提取和冶炼过程非常复杂,需要采用先进的技术和设备,同时还需要严格遵守环保法规。
一、稀有稀土金属概述1.1 稀有稀土金属的定义稀有稀土金属是指在自然界中含量极少的金属元素,通常包括铈、镧、钕、钐、铽、镝、铒、钆等17种元素和钼、铌等2种元素。
1.2 稀有稀土金属的应用稀有稀土金属具有广泛的应用价值,在现代工业生产中扮演着重要角色。
比如:(1)永磁材料:永磁材料是由镝、钕等元素制成,广泛应用于电机、发电机等领域。
(2)催化剂:催化剂是由钯、铑等元素制成,可用于汽车尾气处理等领域。
(3)光电材料:光电材料是由铈、钇等元素制成,可用于LED照明、太阳能电池等领域。
(4)磁记录材料:磁记录材料是由铽、钆等元素制成,可用于磁带、硬盘等领域。
1.3 稀有稀土金属的开采稀有稀土金属的开采非常困难,因为它们在自然界中的含量极少,通常只有几十个ppm(百万分之几)。
目前世界上大部分稀有稀土金属都来自中国和澳大利亚。
开采过程需要采用先进的技术和设备,同时还需要严格遵守环保法规。
二、稀有稀土金属冶炼2.1 稀有稀土金属提取方法由于稀有稀土金属在自然界中的含量非常少,因此提取方法也非常复杂。
目前主要的提取方法包括:(1)萃取法:萃取法是将含稀土金属的矿物与化学试剂混合后进行反应,使得其中的稀土金属被化学试剂吸附,并通过洗涤、沉淀等步骤将其分离出来。
(2)离子交换法:离子交换法是利用特定的树脂材料对稀土金属进行吸附和分离的方法。
(3)溶剂萃取法:溶剂萃取法是利用溶剂将稀土金属从矿物中提取出来的方法。
2.2 稀有稀土金属冶炼流程稀有稀土金属冶炼的流程非常复杂,需要经过多个步骤才能得到纯度较高的金属。
主要步骤包括:(1)矿物选别:首先需要将含有稀有稀土金属的矿物从其他杂质中分离出来。
(2)浸出:将选别后的矿物放入酸性浸出液中,使得其中的稀土金属被浸出。
稀土湿法冶炼基础知识培训教程

稀土湿法冶炼基础知识培训教程稀土湿法冶炼是指通过湿法工艺将稀土矿石中的稀土元素提取出来的一种冶炼方法。
该方法主要包括浸出、分离、纯化和萃取等步骤。
下面是一个基础知识的培训教程,详细介绍了稀土湿法冶炼的基本原理、工艺流程和常见的设备。
一、稀土湿法冶炼的基本原理二、稀土湿法冶炼的工艺流程1.矿石破碎:将稀土矿石破碎成较小的颗粒,便于后续的浸出过程。
2.浸出:将破碎后的矿石与一定比例的酸溶液进行反应,使稀土元素与酸发生化学反应,从矿石中溶出。
3.分离:通过一系列工艺步骤将稀土元素从其他杂质分离出来,包括离子交换、溶出、沉淀等。
4.纯化:将分离后的稀土元素进行纯化处理,去除杂质,提高稀土元素的纯度。
5.萃取:利用有机溶剂对稀土元素进行选择性萃取,从而实现稀土元素的富集和分离。
三、常见的稀土湿法冶炼设备1.破碎设备:包括颚式破碎机、圆锥破碎机等,用于将稀土矿石破碎成合适的颗粒大小。
2.浸出设备:主要有酸洗槽、搅拌槽、配料罐等,用于进行矿石与酸的反应。
3.分离设备:包括离子交换柱、沉淀槽、过滤机等,用于将稀土元素从其他杂质中分离出来。
4.纯化设备:主要有萃取塔、蒸发器、结晶器等,用于对稀土元素进行纯化处理。
5.萃取设备:一般采用萃取柱和混合槽,利用有机溶剂对稀土元素进行选择性萃取。
四、稀土湿法冶炼的应用领域1.光电材料:稀土湿法冶炼可以提取出高纯度的稀土元素,用于生产光电材料,如LED、LCD等。
2.钢铁冶金:稀土元素可以改善钢铁的性能,用于生产高强度和耐磨性能的钢铁产品。
3.新能源材料:稀土湿法冶炼可以提取出稀土元素,用于生产新能源材料,如永磁材料、储能材料等。
4.化工材料:稀土湿法冶炼可以提取出稀土元素,用于生产催化剂、吸附剂等化工材料。
总之,稀土湿法冶炼是一种重要的提取和纯化稀土元素的方法,通过合理的工艺流程和设备选择,可以实现对稀土元素的高效提取和纯化,满足不同领域的应用需求。
稀土生产工艺流程图
稀土生产工艺流程图白云鄂博矿 矿石粉碎 弱磁、强磁选矿 铁精矿强磁中矿、尾矿火法生产线汽车尾气净化器 永磁电机 节能灯风力发电机 各种发光标牌 电动汽车 电动核磁共振 自行车磁悬浮磁选机看稀土原矿生产新闻中有离子型稀土矿原矿“堆浸工艺”这个词,是怎样的工艺?怎么翻译成英文或日文?堆浸提金是指将低品位金矿石或浮选尾矿在底垫材料上筑堆,通过氰化钠溶液循环喷淋,使矿石中的金、银溶解出来。
含金贵液用活性炭吸附、锌置换沉淀或直接电解沉积等方法回收金,提金后的尾渣经消毒后排放。
堆浸法提金具有工艺简单、操作容易、设备少、动力消耗少、投资省、见效快、生产成本低等特点。
堆浸用于处理0.5-3g/t的低品位矿石,金的回收率50-80%,甚至能达到90%。
因此,堆浸法使原来认为无经济价值的许多小型金矿、低品位矿石、尾矿或废石现在都能得以经济回收。
我国在二十世纪八十年代将堆浸法广泛用于工业生产。
堆浸法适合处理以下几种矿产资源:1、规模较大,以前认为不能利用的低品位金银矿;2、矿山开采过程中剥离的低品位含金“废石”;3、地质坑探和矿山掘进中采掘出的中低品位含金矿石;4、含金品位稍高,但规模较小,不宜建机械化选厂的金银矿;5、采用常规氰化法处理经济上不利的金矿;6、含金的冶炼烧渣、高品位尾矿和含有金的大型废石场。
堆浸提金生产工艺主要由堆浸场地的修筑、矿石的预处理(破碎或制粒)、筑堆、喷淋浸出、含金贵液中金的回收以及废矿堆的消毒、卸堆等几部分组成。
堆浸的生产成本:尾矿堆浸成本度大约在30-40元/吨,原矿堆浸成本大约在40-50元/吨.我想问一下现在离子型稀土矿的开采方法是什么方法成本怎样计算需要什么试剂?????????????离子型稀土第一代提取工艺,可简述为"异地提取工艺",或归结为"池浸工艺"。
其主要工艺过程为:表土剥离→开挖含矿山体、搬运矿石→浸矿池→将按一定比例(浓度要求)配置的电解质溶液作为"洗提剂"或"浸矿剂",加入浸矿池,溶液对池中含"离子相"稀土矿石进行"渗滤洗提"或"淋洗" →溶液中活泼离子与稀土离子交换,"离子相"稀土从含矿载体矿物中交换出来,成为新状态稀土;加入"顶水",获含稀土母液;母液经管道或输液沟流入集液池或母液池,然后进入沉淀池;浸矿后废渣从浸矿池中清出,异地排放→在沉淀池中加入沉淀剂、除杂剂,使稀土母液中稀土除杂、沉淀,获混合稀土;池中上清液经处理后,返回浸矿池,作"洗提剂"循环使用→混合稀土经灼烧,获纯度≥92%的混合稀土氧化物。
稀土冶炼工艺流程
稀土冶炼工艺流程稀土冶炼工艺流程1. 引言稀土元素是一种非常珍贵的资源,广泛应用于各个领域,包括磁性材料、光学材料、医药、环保和新能源等。
稀土冶炼是将稀土矿石中的稀土元素提取出来并分离纯化的过程。
本文将深入探讨稀土冶炼的工艺流程,包括主要的冶炼方法和关键步骤。
2. 稀土矿石的选择和预处理稀土矿石的选择对冶炼工艺的成功非常关键。
常见的稀土矿石包括独居石、矿石和长石矿石等。
在选择稀土矿石时,需要考虑矿石中稀土元素的含量、矿石的物理和化学性质以及开采成本等因素。
在冶炼工艺开始之前,稀土矿石需要经过预处理。
这包括矿石的粉碎、磁选和浮选等步骤,以提高稀土的提取效率和产品质量。
3. 稀土提取和分离稀土提取和分离是稀土冶炼的关键步骤。
目前常用的稀土提取方法包括酸法、碱法和溶剂萃取法。
其中,溶剂萃取法在稀土冶炼中应用最广泛。
溶剂萃取法主要包括两个步骤:提取和分离。
提取是指利用有机溶剂将稀土元素从稀土矿石中提取出来,通常使用的有机溶剂有磷酸酯和磷酸等。
分离是指将提取的稀土元素进行分离,通常采用萃取剂的选择性萃取特定的稀土元素。
4. 稀土纯化和精炼提取和分离后的稀土元素通常需要进行纯化和精炼,以获得高纯度的稀土产品。
常用的纯化方法包括晶体生长、离子交换和萃取等。
晶体生长是指通过溶液中的结晶过程获得高纯度的稀土产品。
离子交换是利用吸附树脂将杂质离子与稀土离子交换,从而实现纯化的方法。
萃取是在溶液中加入适当的萃取剂,分离出稀土元素。
5. 客户定制和加工经过纯化和精炼的稀土产品可以根据客户的要求进行定制和加工。
客户可能需要不同纯度和不同形状的稀土产品。
根据客户的需求,冶炼厂家可以调整工艺流程和生产参数,以达到最终产品的要求。
6. 结论稀土冶炼是一项复杂而精细的工艺,涉及到多个步骤和方法。
在冶炼过程中,选择适宜的稀土矿石、合理的提取和分离方法,以及精细的纯化和精炼技术是取得高质量稀土产品的关键。
通过本文对稀土冶炼工艺流程的介绍,我们可以深入了解稀土的提取和分离过程,以及后续的纯化和精炼步骤。
稀土生产工艺流程图
稀土生产工艺流程图白云鄂博矿矿石粉碎弱磁、强磁选矿铁精矿强磁中矿、尾矿稀土精矿稀土选矿碱法生产线酸法生产线火法生产线核磁共振自行车磁悬浮磁选机看稀土原矿生产新闻中有离子型稀土矿原矿“堆浸工艺”这个词,是怎样的工艺?怎么翻译成英文或日文?堆浸提金是指将低品位金矿石或浮选尾矿在底垫材料上筑堆,通过氰化钠溶液循环喷淋,使矿石中的金、银溶解出来。
含金贵液用活性炭吸附、锌置换沉淀或直接电解沉积等方法回收金,提金后的尾渣经消毒后排放。
堆浸法提金具有工艺简单、操作容易、设备少、动力消耗少、投资省、见效快、生产成本低等特点。
堆浸用于处理0.5-3g/t的低品位矿石,金的回收率50-80%,甚至能达到90%。
因此,堆浸法使原来认为无经济价值的许多小型金矿、低品位矿石、尾矿或废石现在都能得以经济回收。
我国在二十世纪八十年代将堆浸法广泛用于工业生产。
堆浸法适合处理以下几种矿产资源:1、规模较大,以前认为不能利用的低品位金银矿;2、矿山开采过程中剥离的低品位含金“废石”;3、地质坑探和矿山掘进中采掘出的中低品位含金矿石;4、含金品位稍高,但规模较小,不宜建机械化选厂的金银矿;5、采用常规氰化法处理经济上不利的金矿;6、含金的冶炼烧渣、高品位尾矿和含有金的大型废石场。
堆浸提金生产工艺主要由堆浸场地的修筑、矿石的预处理(破碎或制粒)、筑堆、喷淋浸出、含金贵液中金的回收以及废矿堆的消毒、卸堆等几部分组成。
堆浸的生产成本:尾矿堆浸成本度大约在30-40元/吨,原矿堆浸成本大约在40-50元/吨. 我想问一下现在离子型稀土矿的开采方法是什么方法成本怎样计算需要什么试剂?????????????离子型稀土第一代提取工艺,可简述为"异地提取工艺",或归结为"池浸工艺"。
其主要工艺过程为:表土剥离→开挖含矿山体、搬运矿石→浸矿池→将按一定比例(浓度要求)配置的电解质溶液作为"洗提剂"或"浸矿剂",加入浸矿池,溶液对池中含"离子相"稀土矿石进行"渗滤洗提"或"淋洗" →溶液中活泼离子与稀土离子交换,"离子相"稀土从含矿载体矿物中交换出来,成为新状态稀土;加入"顶水",获含稀土母液;母液经管道或输液沟流入集液池或母液池,然后进入沉淀池;浸矿后废渣从浸矿池中清出,异地排放→在沉淀池中加入沉淀剂、除杂剂,使稀土母液中稀土除杂、沉淀,获混合稀土;池中上清液经处理后,返回浸矿池,作"洗提剂"循环使用→混合稀土经灼烧,获纯度≥92%的混合稀土氧化物。
稀土生产工艺流程图-+矿的开采技术
稀土生产工艺流程图白云鄂博矿 矿石粉碎 弱磁、强磁选矿 铁精矿强磁中矿、尾矿火法生产线汽车尾气净化器 永磁电机 节能灯风力发电机 各种发光标牌 电动汽车 电动核磁共振 自行车磁悬浮磁选机独居石又名磷铈镧矿.化学成分及性质:(Ce,La,Y,Th)[PO4]。
成分变化很大。
矿物成分中稀土氧化物含量可达50~68%。
类质同象混入物有Y、Th、Ca、[SiO4]和[SO4].独居石溶于H3PO4、HClO4、H2SO4中。
晶体结构及形态:单斜晶系,斜方柱晶类.晶体成板状,晶面常有条纹,有时为柱、锥、粒状.物理性质:呈黄褐色、棕色、红色,间或有绿色.半透明至透明。
条痕白色或浅红黄色。
具有强玻璃光泽.硬度5.0~5。
5。
性脆。
比重4。
9~5.5。
电磁性中弱.在X射线下发绿光。
在阴极射线下不发光.生成状态:产在花岗岩及花岗伟晶岩中;稀有金属碳酸岩中;云英岩与石英岩中;云霞正长岩、长霓岩与碱性正长伟晶岩中;阿尔卑斯型脉中;混合岩中;及风化壳与砂矿中。
用途:主要用来提取稀土元素.中国稀土矿床在地域分布上具有面广而又相对集中的特点。
截止目前为止,地质工作者已在全国三分之二以上的省(区)发现上千处矿床、矿点和矿化产地,除内蒙古的白云鄂博、江西赣南、广东粤北、四川凉山为稀土资源集中分布区外,山东、湖南、广西、云南、贵州、福建、浙江、湖北、河南、山西、辽宁、陕西、新疆等省区亦有稀土矿床发现,但是资源量要比矿化集中富集区少得多。
全国稀土资源总量的98%分布在内蒙、江西、广东、四川、山东等地区,形成北、南、东、西的分布格局,并具有北轻南重的分布特点.但是因为中国稀土占据着几个世界第一:储量占世界总储量的第一,尤其是在军事领域拥有重要意义且相对短缺的中重稀土;生产规模第一,2005年中国稀土产量占全世界的96%;出口量世界第一,中国产量的60%用于出口,出口量占国际贸易的63%以上,而且中国是世界上惟一大量供应不同等级、不同品种稀土产品的国家。
- 1、下载文档前请自行甄别文档内容的完整性,平台不提供额外的编辑、内容补充、找答案等附加服务。
- 2、"仅部分预览"的文档,不可在线预览部分如存在完整性等问题,可反馈申请退款(可完整预览的文档不适用该条件!)。
- 3、如文档侵犯您的权益,请联系客服反馈,我们会尽快为您处理(人工客服工作时间:9:00-18:30)。
白云鄂博矿床的物质成分白云鄂博矿床物质成分极为复杂,已查明有73种元素,170多种矿物。
其中,铌、稀土、钛、锆、钍及铁的矿物共近60种,约占总数的35%。
主要矿石类型有块状铌稀土铁矿石、条带状铌稀土铁矿石、霓石型铌稀土铁矿石、钠闪石型铌稀土铁矿石、白云石型铌稀土铁矿石、黑云母型铌稀土铁矿石、霓石型铌稀土矿石、白云石型铌稀土矿石和透辉石型铌矿石。
稀土生产工艺流程图白云鄂博矿矿石粉碎弱磁、强磁选矿铁精矿强磁中矿、尾矿稀土精矿稀土选矿风力发电机各种发光标牌电动汽车电动核磁共振自行车磁悬浮磁选机稀土精矿硫酸法分解(decomposition of rare earth concentrate by suIphuric acid method)稀土精矿用硫酸处理、生产氯化稀土或其他稀土化合物的稀土精矿分解方法。
本法具有对原料适应性强、生产成本低等优点,是稀土精矿工业上常用的分解方法,广泛用于氟碳铈矿精矿、独居石精矿和白云鄂博混合型稀土矿精矿的分解。
主要有硫酸化焙烧一溶剂萃取法、硫酸分解一复盐沉淀法、氧化焙烧一硫酸浸出法三种工艺。
硫酸化焙烧-溶剂萃取?? 主要用于分解白云鄂博混合型稀土矿精矿生产氯化稀土。
白云鄂博混合型稀土矿精矿成分复杂,属于难处理矿,其典型的主要成分(%)为:RE2O350~55,P2.5~3.5,F7~9,Ca7~8,Ba1~4,Fe3~4,ThO2约0.2。
精矿中放射性元素钍和铀含量低,冶炼的防护要求不高,适于用硫酸化焙烧法分解。
原理?? 经瘩细的稀土精矿与浓硫酸混合后加热焙烧到423~673K温度时,稀土和钍均生成水溶性的硫酸盐。
氟碳铈矿与硫酸的主要反应为:2REFCO3+3H2SO4=RE2(SO4)3+3HF↑+2CO2+2H2O独居石与硫酸的主要反应是:2REPO4+3H2SO4=RE2(SO4)3+2H3PO4Th3(PO4)4+6H2SO4=3Th(SO4)2+4H3PO4铁、钙等杂质也生成相应的硫酸盐。
分解产物用精矿质量12倍的水浸出,获得含稀土、铁、磷和钍的硫酸盐溶液。
控制不同的焙烧温度、硫酸用量和水浸出的液固比,即可改变分解效果。
当硫酸与稀土精矿的量比为1.5~2.5、分解温度503~523K、水浸出液含RE2O350~70g/L时,钍、稀土、磷、铁等同时进入溶液。
上述焙烧和浸出条件主要用于独居石精矿和白云鄂博混合型稀土矿精矿的分解。
当硫酸与稀土精矿的量比为1.2~1.4、分解温度413~433K、水浸出溶液含游离硫酸50%时,主要是钍进入溶液,大部分稀土则留在渣中。
当硫酸与稀土精矿的量比为1.2~1.4、分解温度573~623K、水浸出液含RE2O350g/L时,则稀土进入溶液,钍和铁等留在渣中。
通过控制焙烧和浸出条件,就可使稀土与主要伴生元素得以初步分离。
工艺过程?? 从稀土精矿到获得氯化稀土,主要经过硫酸化焙烧、浸出除杂质和溶剂萃取转型等过程。
(1)硫酸化焙烧。
白云鄂博混合型稀土矿精矿粉与浓硫酸在螺旋混料机内混合后,送入回转窑进行硫酸化焙烧分解。
控制进料端(窑尾)炉气温度493~,523K,焙烧分解过程中炉料慢慢移向窑前高温带,氟碳铈矿和独居石与硫酸作用生成可溶性的硫酸稀土。
铁、磷、钍等则形成难溶于水的磷酸盐。
炉料随着向高温带移动温度不断升高,过量的硫酸逐渐被蒸发掉。
当炉料运行到炉气温度为11’73K左右的窑前出料端时,炉料温度达到623K左右,并形成5~10mm的小粒炉料,称为焙烧料,从燃烧室侧端排出。
(2)浸出除杂质。
焙烧料含硫酸3%~7%,直接落入水浸槽中溶出稀土,而杂质几乎全部留在渣中与稀土分离。
制得纯净的硫酸稀土溶液含RE2O340g/L、Fe0.03~0.05g/L、P约0.005g/L、Th<0.001g/L,酸0.1~0.15mol/L。
用此溶液生产氯化稀土。
(3)溶剂萃取转型。
用溶剂萃取法使硫酸稀土转变成为氯化稀土的过程。
这种工艺已用于取代传统的硫酸复盐沉淀、碱转化等繁琐转型工艺。
这是中国在20世纪80年代稀土提取流程的一次重大革新。
溶剂萃取转型采用羧酸类(环烷酸、脂肪酸)萃取剂,预先用氨皂化,然后直接从硫酸稀土溶液中萃取稀土离子,稀土负载有机相用含HCl6mol/L溶液反萃稀土,制得氯化稀土溶液。
萃取和反萃取过程采用共流萃取(见溶剂革取)方式。
萃余液pH为7.5~8.0,含RE2O310mg/L 左右,稀土萃取率超过99%。
盐酸反萃液含RE2O3250~270g/L,含游离酸0.1~0.3mol/L。
采用减压浓缩方式将反萃液浓缩制成氯化稀土。
氯化稀土的主要成分(质量分数ω/%)为:RE2O3约46,Fe0.01,P0.003,Th0.0002,SO42-<0.01,Ca1.25,NH4+1~2。
1982年中国用上述流程在甘肃稀土公司建成一条年产氯化稀土约6000t的生产线,经过近十年的生产实践证明,工艺流程稳定、操作简单、经济效益好。
中国研究成功从硫酸化焙烧分解白云鄂博混合型稀土矿精矿产出的硫酸稀土溶液中直接用P204萃取剂萃取分离稀土的新工艺,具有将稀土精矿分解作业和单一稀土萃取分离过程结合起来的特点,即同在硫酸介质中分离钐、铕、钆和钕以及制取稀土氯化物,省去了萃取转型和一些化学分离工序,从而减少了试剂消耗,降低了生产成本。
1986年中国的四家工厂用此工艺改造原有流程,共建立了年处理10000t混合矿的生产线,其简化流程如图1。
钕一钐萃取分组产出的钐铕钆富集物含:Eu2O311%、Sm2O350%。
萃取法生产Na2O3的产品纯度达到99%。
萃取法回收稀土所得氯化稀土溶液含RE2O3250g/1,,残液含RE2O30.2~0.4g/L。
硫酸分解-复盐沉淀?? 主要用于处理独居石精矿。
独居石为磷酸盐矿物,是生产稀土和钍的重要原料,通常含RE2O355%,6、ThO23%~10%、U3O8约0.3%、P2O5约25%,另外还含少量钛、铁、锆、硅等杂质。
独居石主要含轻稀土元素,中稀土、重稀土只占稀土总量的8%~10%,产于澳大利亚、印度、巴西。
中国每年生产独居石约2200t。
硫酸分解一复盐沉淀是从独居石提取稀土的传统工艺,独居石精矿和浓硫酸在铸铁搅拌槽中加热到473K温度后分鳃2~4h,大部分稀土促转化成可溶性的硫酸盐。
用水浸出分解产物所得的硫酸稀土溶液的主要成分为:??????????主要成分?????????????????????????????????? ?RE2O3????????????? ThO2?????????????? U3O8含量(质量浓度p)/g?L-1?????????????????????? 约50????????????????? 6~7??????????????? 0.4????????? 主要成分?????????????????????????????????? P2O5????????????????? Fe2O3??????????????H+含量(质量浓度p)/g?L-1????????????????????? 25??????????????????????? 2~3??????????????? 2.5mol/L从这种浸出溶液中提取稀土、钍和铀最常用的是硫酸钠复盐沉淀法。
硫酸钠复盐沉淀法是用硫酸钠或氯化钠沉淀剂使稀土和钍以3Na2SO4?RE2(SO4)3?4H2O?0.09Th(SO4)2复盐沉淀析出。
接着用NaOH将稀土和钍转化成氢氧化物,然后用盐酸优先溶出稀土。
所得氯化稀土溶液经减压浓缩、冷却结晶产出氯化稀土(图2)。
钍富集物送提钍处理。
硫酸分解一复盐沉淀工艺可以处理品位较低的独居石精矿,具有对原料适应性强、生产成本低等优点,但放射性元素钍、铀在流程中分散,较难回收。
近来有人用伯胺从硫酸稀土溶液中首先萃取钍,然后再用硫酸复盐沉淀法回收纯净的稀土,这种方法更有利于稀土和钍的提取。
氧化焙烧硫酸浸出?? 主要用于从氟碳铈矿精矿中提取稀土。
中国山东微山湖畔和四川冕宁蕴藏着丰富的氟碳铈矿,与美国芒廷帕斯(Mountain?Pass)盛产的氟碳铈矿相似,矿物粒度粗,易选别,精矿中的RE2O3?达60%左右,含磷低,容易提取。
美国钼矿公司(Molycorp Inc.)采用氧化焙烧一盐酸浸出分解氟碳铈矿,生产氯化稀土和铈富集物已有30多年历史,稀土产量占世界稀土总产量的30%以上。
氟碳铈矿(REFCO3)在773~873K温度的氧化焙烧过程中,即分解放出CO2,生成稀土氧化物和氟氧化物,三价铈被氧化为四价,难溶的氟碳铈矿转变成可溶性产物。
盐酸浸出过程中可以利用三价稀土和四价铈的性质差别而将铈作为氟化物和氧化物富集于渣中,富铈渣中的CeO2/RE2O3?可达到85%~90%。
但富铈渣还含有重晶石、萤石和独居石等杂质,用此渣生产铈产品时,因需要除去这些杂质而致使流程复杂化。
美国钼矿公司的产品主要是氧化铕、氧化钐和富镧氢氧化甲物,因此要先除去大量铈,以利于单一稀土的萃取分离。
20世纪60年代中国开发的氧化焙烧一硫酸浸出氟碳铈矿精矿分解工艺(图3),能使稀土全部进入酸浸出液。
在773~873K温度下焙烧氟碳铈矿时,Ce3+被氧化为ce4+。
用含硫酸1.25~1.5mol/L溶液浸出焙烧矿时,焙烧矿中Ce4+与F-形成稳定的配位离子CeF62-进入溶液,Ce4+与F-的结合不但防止了氟化稀土生成沉淀物,还促进了焙烧矿中氟化稀土的溶解。
当溶液中存在CeF62-时,氟起着加速难溶二氧化铈溶解的作用。
以上两种作用互相促进,使焙烧矿中的二氧化钍、重稀土草酸盐送回收钾稀xi铈、氟化稀土、氟氧化稀土和氧化稀土等能很快被稀硫酸全部溶解。
稀土浸出率可达96%~97%。
此法制得的硫酸稀土溶液含RE2O380g/L左右、F8~9g/L酸约1.5mol/L、Fe1g/L以下,铈的氧化率达98%~99%。
所得溶液比较纯净,可以直接用P204萃取法、碳酸钠法或硫酸复盐法生产纯度99%~99.9%的二氧化铈。
→。