机械英语文章中英文对照
机械类文章翻译案例 中英对照

妙文翻译公司翻译样稿One concept – the whole system for all functions一个概念–具有所有功能的整体系统Power units动力单元The power unit is the heart of the turbine, supplying the power necessary to operate pitch, yaw and braking systems and providing backup in case of power failure, ensuring a safe stop with no risk of damage.Our hydraulic power units are designed with reliabilty, ease of maintenance and a wide operating temperature range in mind.动力单元是风轮机的心脏,为浆距、偏航和制动系统的运行提供必要的电力,并在断电时提供备用措施,保证安全停止,无损坏危险。
我们的液压动力单元在设计时充分考虑了可靠性、维护方便性及宽温度范围。
Added life寿命增加Parker filtration technology extends the life and increases the reliability of wind turbines by using environmental solutions.In addition to a wide range of hydraulic filters, lube filters and reservoir accessories, Parker offers you the global leader in fluid condition monitoring with the Laser CM portable particle counter.A comprehensive range of quality products to cover all your needs!通过应用环境条件解决方案,Parker过滤技术延长了风轮机的寿命并提高了可靠性。
机械类外文文献及翻译
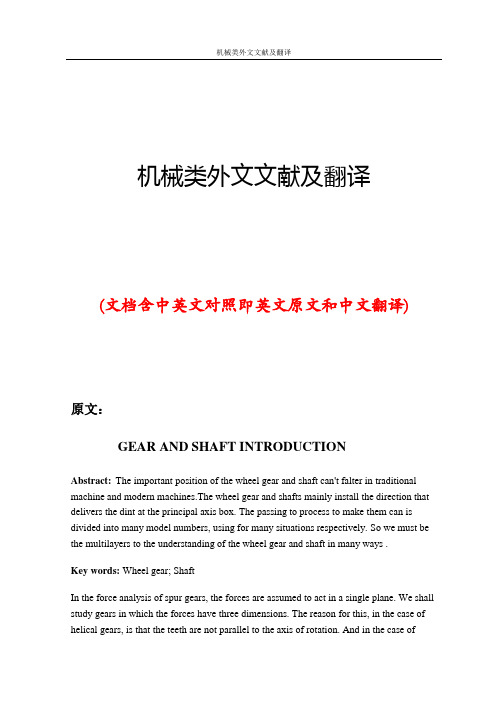
机械类外文文献及翻译(文档含中英文对照即英文原文和中文翻译)原文:GEAR AND SHAFT INTRODUCTIONAbstract:The important position of the wheel gear and shaft can't falter in traditional machine and modern machines.The wheel gear and shafts mainly install the direction that delivers the dint at the principal axis box. The passing to process to make them can is divided into many model numbers, using for many situations respectively. So we must be the multilayers to the understanding of the wheel gear and shaft in many ways .Key words: Wheel gear; ShaftIn the force analysis of spur gears, the forces are assumed to act in a single plane. We shall study gears in which the forces have three dimensions. The reason for this, in the case of helical gears, is that the teeth are not parallel to the axis of rotation. And in the case ofbevel gears, the rotational axes are not parallel to each other. There are also other reasons, as we shall learn.Helical gears are used to transmit motion between parallel shafts. The helix angle is the same on each gear, but one gear must have a right-hand helix and the other a left-hand helix. The shape of the tooth is an involute helicoid. If a piece of paper cut in the shape of a parallelogram is wrapped around a cylinder, the angular edge of the paper becomes a helix. If we unwind this paper, each point on the angular edge generates an involute curve. The surface obtained when every point on the edge generates an involute is called an involute helicoid.The initial contact of spur-gear teeth is a line extending all the way across the face of the tooth. The initial contact of helical gear teeth is a point, which changes into a line as the teeth come into more engagement. In spur gears the line of contact is parallel to the axis of the rotation; in helical gears, the line is diagonal across the face of the tooth. It is this gradual of the teeth and the smooth transfer of load from one tooth to another, which give helical gears the ability to transmit heavy loads at high speeds. Helical gears subject the shaft bearings to both radial and thrust loads. When the thrust loads become high or are objectionable for other reasons, it may be desirable to use double helical gears. A double helical gear (herringbone) is equivalent to two helical gears of opposite hand, mounted side by side on the same shaft. They develop opposite thrust reactions and thus cancel out the thrust load. When two or more single helical gears are mounted on the same shaft, the hand of the gears should be selected so as to produce the minimum thrust load.Crossed-helical, or spiral, gears are those in which the shaft centerlines are neither parallel nor intersecting. The teeth of crossed-helical fears have point contact with each other, which changes to line contact as the gears wear in. For this reason they will carry out very small loads and are mainly for instrumental applications, and are definitely not recommended for use in the transmission of power. There is on difference between a crossed heli : cal gear and a helical gear until they are mounted in mesh with each other. They are manufactured in the same way. A pair of meshed crossed helical gears usually have the same hand; that is ,a right-hand driver goes with a right-hand driven. In the design of crossed-helical gears, the minimum sliding velocity is obtained when the helix angle areequal. However, when the helix angle are not equal, the gear with the larger helix angle should be used as the driver if both gears have the same hand.Worm gears are similar to crossed helical gears. The pinion or worm has a small number of teeth, usually one to four, and since they completely wrap around the pitch cylinder they are called threads. Its mating gear is called a worm gear, which is not a true helical gear. A worm and worm gear are used to provide a high angular-velocity reduction between nonintersecting shafts which are usually at right angle. The worm gear is not a helical gear because its face is made concave to fit the curvature of the worm in order to provide line contact instead of point contact. However, a disadvantage of worm gearing is the high sliding velocities across the teeth, the same as with crossed helical gears.Worm gearing are either single or double enveloping. A single-enveloping gearing is onein which the gear wraps around or partially encloses the worm.. A gearing in which each element partially encloses the other is, of course, a double-enveloping worm gearing. The important difference between the two is that area contact exists between the teeth of double-enveloping gears while only line contact between those of single-enveloping gears. The worm and worm gear of a set have the same hand of helix as for crossed helical gears, but the helix angles are usually quite different. The helix angle on the worm is generally quite large, and that on the gear very small. Because of this, it is usual to specify the lead angle on the worm, which is the complement of the worm helix angle, and the helix angle on the gear; the two angles are equal for a 0-deg. Shaft angle.When gears are to be used to transmit motion between intersecting shaft, some of bevel gear is required. Although bevel gear are usually made for a shaft angle of 0 deg. They may be produced for almost any shaft angle. The teeth may be cast, milled, or generated. Only the generated teeth may be classed as accurate. In a typical bevel gear mounting, one of the gear is often mounted outboard of the bearing. This means that shaft deflection can be more pronounced and have a greater effect on the contact of teeth. Another difficulty, which occurs in predicting the stress in bevel-gear teeth, is the fact the teeth are tapered.Straight bevel gears are easy to design and simple to manufacture and give very good results in service if they are mounted accurately and positively. As in the case of squr gears, however, they become noisy at higher values of the pitch-line velocity. In these cases it is often go : od design practice to go to the spiral bevel gear, which is the bevel counterpart of thehelical gear. As in the case of helical gears, spiral bevel gears give a much smoother tooth action than straight bevel gears, and hence are useful where high speed are encountered.It is frequently desirable, as in the case of automotive differential applications, to have gearing similar to bevel gears but with the shaft offset. Such gears are called hypoid gears because their pitch surfaces are hyperboloids of revolution. The tooth action between such gears is a combination of rolling and sliding along a straight line and has much in common with that of worm gears.A shaft is a rotating or stationary member, usually of circular cross section, having mounted upon it such elementsas gears, pulleys, flywheels, cranks, sprockets, and other power-transmission elements. Shaft may be subjected to bending, tension, compression, or torsional loads, acting singly or in combination with one another. When they are combined, one may expect to find both static and fatigue strength to be important design considerations, since a single shaft may be subjected to static stresses, completely reversed, and repeated stresses, all acting at the same time.The word “shaft” covers numerous v ariations, such as axles and spindles. Anaxle is a shaft, wither stationary or rotating, nor subjected to torsion load. A shirt rotating shaft is often called a spindle.When either the lateral or the torsional deflection of a shaft must be held to close limits, the shaft must be sized on the basis of deflection before analyzing the stresses. The reason for this is that, if the shaft is made stiff enough so that the deflection is not too large, it is probable that the resulting stresses will be safe. But by no means should the designer assume that they are safe; it is almost always necessary to calculate them so that he knows they are within acceptable limits. Whenever possible, the power-transmission elements, such as gears or pullets, should be located close to the supporting bearings, This reduces the bending moment, and hence the deflection and bending stress.Although the von Mises-Hencky-Goodman method is difficult to use in design of shaft, it probably comes closest to predicting actual failure. Thus it is a good way of checking a shaft that has already been designed or of discovering why a particular shaft has failed in service. Furthermore, there are a considerable number of shaft-design problems in which the dimension are pretty well limited by other considerations, such as rigidity, and it is only necessary for the designer to discover something about the fillet sizes, heat-treatment,and surface finish and whether or not shot peening is necessary in order to achieve the required life and reliability.Because of the similarity of their functions, clutches and brakes are treated together. In a simplified dynamic representation of a friction clutch, or brake, two in : ertias I and I traveling at the respective angular velocities W and W, one of which may be zero in the case of brake, are to be brought to the same speed by engaging the clutch or brake. Slippage occurs because the two elements are running at different speeds and energy is dissipated during actuation, resulting in a temperature rise. In analyzing the performance of these devices we shall be interested in the actuating force, the torque transmitted, the energy loss and the temperature rise. The torque transmitted is related to the actuating force, the coefficient of friction, and the geometry of the clutch or brake. This is problem in static, which will have to be studied separately for eath geometric configuration. However, temperature rise is related to energy loss and can be studied without regard to the type of brake or clutch because the geometry of interest is the heat-dissipating surfaces. The various types of clutches and brakes may be classified as fllows:. Rim type with internally expanding shoes. Rim type with externally contracting shoes. Band type. Disk or axial type. Cone type. Miscellaneous typeThe analysis of all type of friction clutches and brakes use the same general procedure. The following step are necessary:. Assume or determine the distribution of pressure on the frictional surfaces.. Find a relation between the maximum pressure and the pressure at any point. Apply the condition of statical equilibrium to find (a) the actuating force, (b) the torque, and (c) the support reactions.Miscellaneous clutches include several types, such as the positive-contact clutches, overload-release clutches, overrunning clutches, magnetic fluid clutches, and others.A positive-contact clutch consists of a shift lever and two jaws. The greatest differences between the various types of positive clutches are concerned with the design of the jaws. To provide a longer period of time for shift action during engagement, the jaws may be ratchet-shaped, or gear-tooth-shaped. Sometimes a great many teeth or jaws are used, and they may be cut either circumferentially, so that they engage by cylindrical mating, or on the faces of the mating elements.Although positive clutches are not used to the extent of the frictional-contact type, they do have important applications where synchronous operation is required.Devices such as linear drives or motor-operated screw drivers must run to definite limit and then come to a stop. An overload-release type of clutch is required for these applications. These clutches are usually spring-loaded so as to release at a predetermined toque. The clicking sound which is heard when the overload point is reached is considered to be a desirable signal.An overrunning clutch or coupling permits the driven member of a machine to “freewheel” or “overrun” bec ause the driver is stopped or because another source of power increase the speed of the driven. This : type of clutch usually uses rollers or balls mounted between an outer sleeve and an inner member having flats machined around the periphery. Driving action is obtained by wedging the rollers between the sleeve and the flats. The clutch is therefore equivalent to a pawl and ratchet with an infinite number of teeth.Magnetic fluid clutch or brake is a relatively new development which has two parallel magnetic plates. Between these plates is a lubricated magnetic powder mixture. An electromagnetic coil is inserted somewhere in the magnetic circuit. By varying the excitation to this coil, the shearing strength of the magnetic fluid mixture may be accurately controlled. Thus any condition from a full slip to a frozen lockup may be obtained.齿轮和轴的介绍摘要:在传统机械和现代机械中齿轮和轴的重要地位是不可动摇的。
机械专业英语文章中英文对照

机械专业英语文章中英文对照作为应用型人才培养的全日制机械工程专业学位研究生,除了具有扎实的理论基础以外,还需要满足机械行业的实际工作需求。
下面小编整理了中英文对照机械专业英语文章,希望大家喜欢!中英文对照机械专业英语文章品析公差系统A system of tolerances is necessary to allow for the variations in accuracy that are bound tooccur during manufacture, and still provide for interchangeability and correct function of thepart.为了允许在制造过程中必然会发生的精度变化并提供零件的互换性和正确功能一个公差系统是必需的。
A tolerance is the difference in a dimension in order to allow for unavoidable imperfections inworkmanship. The tolerance range will depend on the accuracy of the manufacturingorganisation, the machining process and the magnitude of the dimension.公差是为了允许工艺上不可避免缺陷而存在的尺寸上的不同。
公差范围取决于制造机构的精度、机加工过程和尺寸的量值。
The greater the tolerance range, the cheaper the manufacturing process. A bilateral toleranceis one where the tolerance range is disposed on both sides of the nominal dimension. Aunilateral tolerance is one where the tolerance zone is on one side only of the nominaldimension, in which case the nominal dimension may form one of the limits.公差范围越大则制造过程的成本就越低。
机械专业英语短文带翻译
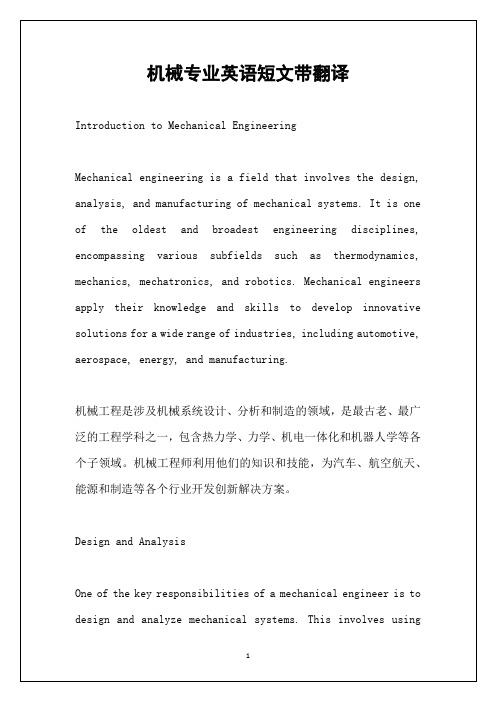
机械工程师的关键责任之一是设计与分析机械系统。这涉及使用计算机辅助设计(CAD)软件创建系统的详细三维模型,并在不同条件下模拟其性能。通过分析作用于系统组件的力、应力和振动,机械工程师可以优化设计,确保安全、可靠和高效。
Case Study: Designing an Automotive Suspension System
案例研究:汽车悬挂系统设计
例如,让我们考虑一下汽车悬挂系统的设计。悬挂系统负责在保持车辆稳定控制的同时提供平稳的行驶。机械工程师使用CAD软件设计悬挂系统的各个组件,例如弹簧、减振器和控制臂。
在完成初始设计后,工程师将使用有限元分析(FEA)软件对系统进行分析。这样可以模拟系统在不同的道路条件下(如坑洼或减速带)的行为。通过分析组件中的应力和位移,工程师可以确定潜在的设计问题,并进行必要的修改,以改善悬挂系统的性能和安全性。
For example, let's consider the design of an automotive suspension system. A suspension system is responsible for providing a smooth ride while maintaining the stability and control of the vehicle. A mechanical engineer would use CAD software to design the various components of the suspension system, such as the springs, dampers, and control arms.
After the initial design is complete, the engineer would then analyze the system using finite element analysis (FEA) software. This allows them to simulate the behavior of the system under different road conditions, such as potholes or speed bumps. By analyzing the stresses and displacements in the components, the engineer can identify potential design issues and make necessary modifications to improve the performance and safety of the suspension system.
(完整版)机械类专业英语课文参考翻译

第一课Text:It is known that metals are very important in our life. Metals have the greatest importance for industry. All machines and other engineering[7endVi5niEriN] constructions have metal[5metl] parts; some of them consist only of metal parts.众所周知,金属在我们的生活中是非常重要的,金属对于工业而言是有巨大的重要性,所有机器和其他工程构造都有金属零部件,其中一些还只能由金属组成。
There are two large groups of metals:1) Simple metal- more or less pure chemical elements[5elimEnt]2) Alloys[5AlCi]- materials consisting of a simple metal combined with some other elements.有两大类金属:(1)纯金属——或多或少的金属元素(2)合金——组成纯金属的原料结合其他元素。
About two thirds of all elements found in the earth are metals, but not all metals may be used in industry. Those metals which are used in industry are called engineering metals. The most important engineering metalis iron[5aiEn], which in the form of alloys with carbon[5kB:bEn] and other elements, finds greater use than any other metal. Metals consisting of iron combined with some other elements are known as ferrous[5ferEs] metals; all the other metals are called nonferrous[5nCn5ferEs] metals. The most important nonferrous metal arecopper[5kCpE], aluminum[E5lju:minEm], lead[li:d], zinc[ziNk], tin[tin], but all these metals are used muchless than ferrous metals, because the ferrous metals are much cheaper.在地球上发现的所有元素中,大约三分之二是金属元素,但是并不是所有的金属都能够用于工业上。
机械制造专业英语文章

机械制造专业英语文章篇一:机械专业英语文章中英文对照Types of Materials材料的类型Materials may be grouped in several ways. Scientists often classify materials by their state: solid, liquid, or gas. They also separate them into organic (once living) and inorganic (never living) materials.材料可以按多种方法分类.科学家常根据状态将材料分为:固体.液体或气体.他们也把材料分为有机材料(曾经有生命的)和无机材料(从未有生命的).For industrial purposes, materials are divided into engineering materials or nonengineering materials. Engineering materials are those used in manufacture and become parts of products.就工业效用而言,材料被分为工程材料和非工程材料.那些用于加工制造并成为产品组成部分的就是工程材料.Nonengineering materials are the chemicals, fuels, lubricants, and other materials used in the manufacturing process, which do not become part of the product.非工程材料则是化学品.燃料.润滑剂以及其它用于加工制造过程但不成为产品组成部分的材料.Engineering materials may be further subdivided into: ①Metal ②Ceramics ③Composite ④Polymers, etc.工程材料还能进一步细分为:①金属材料②陶瓷材料③复合材料④聚合材料,等等.Metals and Metal Alloys金属和金属合金Metals are elements that generally have good electrical and thermal conductivity. Many metals have high strength, high stiffness, and have good ductility.金属就是通常具有良好导电性和导热性的元素.许多金属具有高强度.高硬度以及良好的延展性.Some metals, such as iron, cobalt and nickel, are magnetic. At low temperatures, some metals and intermetallic compounds become superconductors.某些金属能被磁化,例如铁.钴和镍.在极低的温度下,某些金属和金属化合物能转变成超导体.What is the difference between an alloy and a pure metal? Pure metals are elements which come from a particular area of the periodic table. E_amples of pure metals include copper in electrical wires and aluminum in cooking foil and beverage cans.合金与纯金属的区别是什么?纯金属是在元素周期表中占据特定位置的元素.例如电线中的铜和制造烹饪箔及饮料罐的铝.Alloys contain more than one metallic element. Their properties can be changed by changing the elements present in the alloy. E_amples of metal alloys include stainless steel which is an alloy of iron, nickel, and chromium; and gold jewelry which usually contains an alloy of gold and nickel.合金包含不止一种金属元素.合金的性质能通过改变其中存在的元素而改变.金属合金的例子有:不锈钢是一种铁.镍.铬的合金,以及金饰品通常含有金镍合金.Why are metals and alloys used? Many metals and alloys have high densities and are used in applications which require a high mass-to-volume ratio.为什么要使用金属和合金?许多金属和合金具有高密度,因此被用在需要较高质量体积比的场合.Some metal alloys, such as those based on aluminum, have low densities and are used in aerospace applications for fuel economy. Many alloys also have high fracture toughness, which means they can withstand impact andare durable.某些金属合金,例如铝基合金,其密度低,可用于航空航天以节约燃料.许多合金还具有高断裂韧性,这意味着它们能经得起冲击并且是耐用的What are some important properties of metals?Density is defined as a material’s mass divided by its volume. Most metals have relatively high densities, especially compared to polymers.金属有哪些重要特性?密度定义为材料的质量与其体积之比.大多数金属密度相对较高,尤其是和聚合物相比较而言.Materials with high densities often contain atoms with high atomic numbers, such as gold or lead. However, some metals such as aluminum or magnesium have low densities, and are used in applications that require other metallic properties but also require low weight.高密度材料通常由较大原子序数原子构成,例如金和铅.然而,诸如铝和镁之类的一些金属则具有低密度,并被用于既需要金属特性又要求重量轻的场合.Fracture toughness can be described as a material’s ability to avoid fracture, especially when a flaw is introduced. Metals can generally contain nicks and dents without weakening very much, and are impact resistant. A football player counts on this when he trusts that his facemask won’t shatter.断裂韧性可以描述为材料防止断裂特别是出现缺陷时不断裂的能力.金属一般能在有缺口和凹痕的情况下不显著削弱,并且能抵抗冲击.橄榄球运动员据此相信他的面罩不会裂成碎片.Plastic deformation is the ability of bend or deform before breaking. As engineers, we usually design materials so that they don’t deform under normal conditions. You don’t want your car to lean to the east after a strong west wind.塑性变形就是在断裂前弯曲或变形的能力.作为工程师,设计时通常要使材料在正常条件下不变形.没有人愿意一阵强烈的西风过后自己的汽车向东倾斜.However, sometimes we can take advantage of plastic deformation. The crumple zones in a car absorb energy by undergoing plastic deformation before they break.然而,有时我们也能利用塑性变形.汽车上压皱的区域在它们断裂前通过经历塑性变形来吸收能量.The atomic bonding of metals also affects their properties. In metals, the outer valence electrons are shared among all atoms, and are free to travel everywhere. Since electrons conduct heat and electricity, metals make good cooking pans and electrical wires.金属的原子连结对它们的特性也有影响.在金属内部,原子的外层阶电子由所有原子共享并能到处自由移动.由于电子能导热和导电,所以用金属可以制造好的烹饪锅和电线.It is impossible to see through metals, since these valence electrons absorb any photons of light which reach the metal. No photons pass through.因为这些阶电子吸收到达金属的光子,所以透过金属不可能看得见.没有光子篇二:机械专业英语作文1Mechanical engineeringEngineering Science in life are widely used, especially in mechanical engineering in the application of life is almost throughout life in all its aspects, to automobiles, aircraft, small electric fans, umbrella, all of these and related machinery. The project includes many subjects, but the mechanical engineering is one of the most important subjects, not only because of our life and it is closely related to, but with the progress of the times, people have to rely on mechanical engineering products, in automation today, machine instead of many this is the part of the human labor, improve the efficiency and save time.As a result of mechanical engineering in every aspect of life, therefore, as an engineer, be faced with a great many challenges, inaddition to a solid with knowledge, but also keep pace with the times, familiar with the machinery and related software, can be very good use of software, and as a an engineer, we should try our best to design and produce and closely related to the life of the machine, and can in life play a real role, also have only such, we address and remission now social needs, therefore, the mechanical engineering in the future social development, will play the important role, especially China s case, the industry also is not very developed, machinery can be greater development space.Before the industrial revolution, machinery is mostly wood structure, wood made by hand by. The development of social economy, the demand for mechanical products. The bulk of the production increasing and precision processing technology progress, promote the mass production method ( interchangeability of parts production, professional division of labor and cooperation, water processing lines and assembly lines ) formation. Study of mechanical products in the manufacturing process, especially when used in the pollution of the environment and natural resources e_cessive consumption problems and their treatment measures. This is a modern mechanical engineering is an especially important task to grow with each passing day, and its importance.Application of mechanical products. This includes selection, ordering, acceptance, installation, adjustment, operation, maintenance, repair and transformation of the industrial use of machinery and complete sets of machinery and equipment, to ensure that the mechanical products in the long-term use of reliability and economy. As a student, we are now the most important to learn professional knowledge, only in this way, can we later life and learning, to do its part.机械工程工程科学在生活中应用广泛,特别是机械工程在生活中的应用几乎就是遍布了生活中的各个方面,大到汽车.飞机,小到电风扇.雨伞,这些都和机械有关.工程包括很多科目,但是机械工程是最重要的科目之一,不仅是因为它和我们的生活关系密切,而是随着时代的进步,人们已经依赖上机械工程制造出来的产品,而在自动化的今天,机器代替了许多本该是人类该做的部分劳动,提高了效率和节约了时间.由于机械工程遍布了生活的每一个方面,因此,做为一个工程师,要面临很大且很多的挑战,除了要具备扎实的装也知识外,还要与时俱进,熟悉和机械有关的软件,并要能很好的运用软件,而作为的一个工程师,我们要尽量设计和制造出和生活密切相关的机器,并能够在生活中起到真正的作用,也只有这样,我们解决和缓解现在社会上的需要,因此,机械工程在今后的社会的发展中,还是会起这重要的作用,特别是我国的这样的情况,工业还不是很发达的情况下,机械可发展的空间更大.工业革命以前,机械大都是木结构的,由木工用手工制成.社会经济的发展,对机械产品的需求猛增.生产批量的增大和精密加工技术的进展,促进了大量生产方法(零件互换性生产.专业分工和协作.流水加工线和流水装配线等)的形成.研究机械产品在制造过程中,尤其是在使用中所产生的环境污染和自然资源过度耗费方面的问题及其处理措施.这是现代机械工程的一项特别重要的任务,而且其重要性与日俱增.机械产品的应用.这方面包括选择.订购.验收.安装.调整.操作.维护.修理和改造各产业所使用的机械和成套机械装备,以保证机械产品在长期使用中的可靠性和经济性.做为学生,我们现在最重要的学好专业知识,只有这样,我们才能以后是生活和学习中,才能尽自己的一份力量.篇三:机械类专业英语课文参考翻译_pdf第一课该○翻译整理于网络,It is known that metals are very important in our life. Metals have the greatest importance for industry. All machines and other engineering[7endVi5niEriN] constructions have metal[5metl] parts; some of them consistonly of metal parts.众所周知,金属在我们的生活中是非常重要的,金属对于工业而言是有巨大的重要性,所有机器和其他工程构造都有金属零部件,其中一些还只能由金属组成.There are two large groups of metals:1) Simple metal- more or less pure chemical elements[5elimEnt]2) Alloys[5AlCi]- materials consisting of a simple metal combined with some other elements.有两大类金属:(1)纯金属——或多或少的金属元素(2)合金——组成纯金属的原料结合其他元素.About two thirds of all elements found in the earth are metals, but not all metals may be used in industry. Those metals which are used in industry are called engineering metals. The most important engineering metal is iron[5aiEn], which in the form of alloys with carbon[5kB:bEn] and other elements, finds greater use than any other metal. Metals consisting of iron combined with some other elements are known as ferrous[5ferEs] metals; all the other metals are called nonferrous[5nCn5ferEs] metals. The most importantnonferrous metal are copper[5kCpE], aluminum[E5lju:minEm], lead[li:d], zinc[ziNk], tin[tin], but all these metals are used much less than ferrous metals, because the ferrous metals are much cheaper.第 _._._._. 在地球上发现的所有元素中,大约三分之二是金属元素,但是并不是所有的金属都能够用于工业上.那些金属—我们用于工业上的金属—被称为工程金属,最重要的工程金属那就是铁,铁跟碳和其他元素结合形成合金的那些金属比其他金属发现有更大用途.铁与别的其他某些元素相结合而组成的金属称为黑色金属,此外所有其他金属都称为有色金属,最重要的有色金属是---铜,铝.铅.锌.锡.但是使 _课的翻译暂时没有. 用这些有色金属比使用黑色金属要少的多,因为黑色金属便宜得多.Engineering metals are used in industry in the form of alloys because the properties[5prCpEti] of alloys are much better than the properties of pure[pjuE] metals. Only aluminum may be largely used in the form of simple metal. Metals have such a great importance because of their useful properties or their strength, hardness, 翻译标准.请放心使 and their plasticity[plAs5tisiti].因为合金的特性比纯金属的好,所以工程金属以合金的形式用于工业,只有铝以纯金属的形式被广泛应用.金属因为具有强度.硬度和可塑性而发挥着特别重要的作用. 用.Different metals are produced in different ways, but almost all the metal are found in the forms of metal ore[C:(r)] (iron ore, copper ore, etc[et cetra].)以不同的方法生产不同的合金但是几乎所有的金属都是以金属矿的形式(铁矿.铜矿)被发现的.The ore is a mineral[5minErEl] consistence of a metal combined with some impurities[im5pjuEriti]. Inorder to produce a metal from some metal ore, we must separate these impurities from the metal that is done by metallurgy[me5tAlEdVi].矿石是一种由金属与某些杂质相混合而组成的矿物质,为了用金属矿石来生产出一种金属,我们必须把杂质从金属矿中分离出去,那就要靠冶炼来实现. Te_t:12. Plastics and Other MaterialsTe_t:Plastics[5plAstik, plB:stik] have specific properties which may makeik] acids[5AsId], such as sulphuric[sQl5fjuErik] acid and hydrochloric[7haidrEu5klC:rik] acid. Plastics tend to be resistant to these acids, but can have dissolved or deformed by solvent[5sClvEnt], suchas carbon tetrachloride[7tetrE5klC:raid], which have the same carbon base as the plastics. Color must be applied to the surface of metals, whereas it can be mi_ed in with plastics. Metals are more rigid[5ridVid] than most plastics while plastics are very light, with a specific[spi5sifik] gravity normally between 0.9 and 1.8. Most plastics do not readily[5redili] conduct[5kCndQkt] heat or electricity[Ilek5trIsItI]. Plastics soften slowly and can easily be shaped[Feip] when they are soft.塑料具有特殊的性能.对于某种用途而言,这些性能使得塑料比传统材料更为可取.例如,跟金属相比较,塑料既有优点也有缺点.金属易受到无机酸的腐蚀,如硫酸和盐酸,塑料能抵抗这些酸的腐蚀,但可被溶剂所洛解或引起变形,例如溶剂四氯化碳与塑料具有同样的碳基.颜色必定只能涂到金属的表面.而它可以跟塑料混合为一体.金属比大多数塑料刚性要好,而塑料则非常之轻,通常塑料密度在0. 9-1. 8之间.大多数塑料不易传热导电.塑料能缓慢软化,而当其还是在软的状态时,能容易成形.It is their plasticity[plAs5tisiti] at certain temperatures[5temprItFE(r)] which gives plastics their main advantages over many other materials. It permits the large-scale production of molded[mEuld] articles, such as containers, at an economic unit cost, where other materials require laborious[lE5bC:riEs] and often costly processes involving cutting, shaping, machining, assembly[E5sembli] and decoration.在某一温度下塑料是处于塑性状态的,这就使塑料具备超过许多其他材料的主要优点.它容许大量生产单位成本低廉的模制式器件,例如,各种容器.于此,若用其他材料则需要大量劳力和往往需要很费钱的加工工艺,比如,切割.成形.加工.装配和装饰.Plastics not only replace other materials. Their properties can be e_ploited[iks5plCit] for entirely[In5taIElI] new applications. For e_ample, plastics heart valves[vAlv] and other human spare parts have make possible many recent developments in surgery[5sE:dVEri].塑料不仅可以代替其他材料,而且它的特性能被开拓应用于全新领域,比如:随着最近外科手术的发展可能做成塑料的心脏瓣膜和其他人类的器官.There is no single plastics material which is suitable for all applications. It is important that the most suitable plastics should be chosen, and if necessary adapted[E5dApt], for each particular requirement. It is also important that the properties of the plastics chosen should be e_ploited to the best advantage.没有一种纯塑料材料适用于各个领域,如果有必要改进,对于每个有特殊要求的来说选择最合适的塑料是最重要的,被选择的塑料材料的特性被开拓得到更好的应用也是很重要的.A plastics article may need to differ in design and appearance from a similar article made from another material such as metal or wood. This is due[ ] not only to the properties of plastics but also to thetechniques[tek5ni:k] employed in fabricating[5fAbrikeit] plastics. These techniques include injection[in5dVekFEn] molding[5mEuldiN], blow molding, compression molding, e_trusion[eks5tru:VEn] and vacuum[5vAkjuEm] forming.塑料器件可能需要用其他材料比如:与金属或木材制作的类似的器件从设计和外观上加以区别,这不仅是由于塑料性能不同的原因,也是由于制造塑料产品所用的技术不同所致,这些技术包括:注塑.模制.吹塑模制.压模.挤压和真空成型等.23. Casting and Die-Casting AlloysTe_t:Casting[5kB:stiN] is one of the oldest metal working techniques known to man. Our country made metal castings as early as _ B.C., and the process used then is not much different in principle[5prinsEpl] from the one used today.铸造是入类所掌握的最古老的金属加工技术之一.我国早在公元前 _年就已把金属制成铸件,而所使用的工艺从原理上和今天的工艺没有多大的区别.Foundry[5faundri]processesconsistof makingmolds,preparingandmelting[melt]themetal, pouring[pC:, pCE] the metal into the molds, and cleaning the castings. The product of the foundry is a casting, which may vary from a fraction[5frAkFEn] of a kilogram to several hundred tons. It may also vary in composition[kCmpE5ziFEn] as practically all metals and alloys can be cast.铸造工艺由制模.备料和金属熔炼,金属液浇注入模和铸件清砂等.铸造的产品是铸件,铸件可能从零点几公斤到几百吨范围变化.实际上所有金属在成分上也是变化的,而合金也可以铸造.The metals most frequently cast are iron, steel, aluminum and so on. Of these, iron, because of its low melting point, low price and ease of control, is outstanding for its suitability[9sjU:tE`bIlEtI] for casting and is used far more than all the others.最常铸造的金属是铸铁.钢.铝等等.这些金属中,铸铁,由于其低熔点,低价格和易控制,因而其铸造适应性是最突出的,而且使用也远比所有其他金属多.Castingisawidelyusedmethodofproducingmetalproducts,particularlythosew hichareintricate[5intrikit]. Since molten materials will readily take the shape of the container into which they are poured, it is nearly as easy to cast fairly comple_ shapes as to produce simple forms.由于熔融的物料能容易取得被浇注进去的容器(模型)的形状,因此,几乎像生产简单形状铸件那样颇为容易地铸造出复杂形状的铸件.The place where the metals are cast is called a foundry. The most important of cast metals is cast iron which is made from pig iron by remelting it in a special melting furnace[5fE:nis] called a cupola[5kju:pElE].铸造金属的地方叫做铸造车间.最重要的铸造金属是铸铁,铸铁是用生铁在一个特殊的熔炉—叫冲天炉的炉子中重新熔炼而制造出来的.From the cupola, the cast iron flows into ladles[5leidl] of different size, and from these ladles it is poured into the molds.从冲天炉中出来的铁水流入到不同规格的铁水包中,并从这些铁水包中被浇注到模型中.The molds may be of two kinds: sand molds and metal molds. A metal mold consists of two hollow parts which should be joined for pouring the metal into it. The inside of this mold is covered with carbon or graphite[5 Afait] so that the metal could not stick[stik] to the wall of the form. When the metal has solidlocks of steel produced by pouring the metal into these molds are called ingots and the process is called ingot casting.模型有两种类型:砂模和金属模.金属模是由两个中空的部件组成,它们应被联结在一起以便将金属液浇入模箱中.这模腔的内侧是要涂以碳粉或石墨,因此金属不玫于粘贴到型腔壁上口当金属液凝固后,这中空的型箱部件被打开并取出铸件.也有一种特殊模型,在该模型中可以铸造大型钢块.这些模型通常用铸铁米制造,并被称为锭模.而浇注金属液到这些模子中生产出的钢块被称为钢锭.该工艺过程叫锭铸.A relatively[5relEtIvlI] wide range of nonferrous alloys can be die-cast. The principal base metals used, in order to commercial importance, are zinc, aluminum, copper, magnesium[mA ni:zjEm], lead, and tin. The alloys may be further classified as low-temperature alloys and high-temperature alloys; those having a casting 3temperature below 538C, such as zinc, tin, and lead, are in the low-temperature class. The low-temperature alloys have the advantages of lower cost of production and lower die-maintenance[5meintinEns] costs. As the casting temperature increases, alloy and other special steels in the best treated condition are required to resist the erosion[i5rEuVEn] and heat checking[5tFekiN] of die surface. The destructive[dis5trQktiv] effect of high temperaturesonthedies hasbeentheprincipalfactorinretarding[ri5tB:d] thedevelopmentof high-temperature die castings.相当大量的有色金属合金可以进行模铸}h 用的主要而基本的金属,按其在工业上应用的重要性的顺序是锌.铝.铜.锰.铅和锡.这些合金可以进一步进行分类为低温类合金和高温类合金.铸造温度低于538℃的那些合金,就像锌.锡和铅,是属于低温类合金.低温类合金具有低生产成本和低的模具维修费用等优点.当铸造温度上升时,需要最佳条件下处理过的合金钢和其他特种钢来抵抗腐蚀及防止模具表面的热裂纹.高温在模具上的损坏作用已经成为阻碍.延缓高温模铸发展的主is more pronounced[pr5naunst] with some alloys than with others. Aluminum, in particular, has a destructive action on ferrous metals and, for this reason, is seldom melted in the machine, whereas the copper-basealloys are never melted in the machine.控制选择合金的另外一个因素就是熔融的金属在相关的机器零件上和模具上的腐蚀或溶解作用.这种作用随着温度的升高而增加,甚至某些合金比另一些合金更为明显.特别是 .铝对黑色金属有一种破坏作用,为此.铝几乎不熔混于机器零件中,而铜基合金是决不能熔混于机器构件中的.44. ForgingTe_t:Press forging[5fC:dViN] employs a slow squeezing[skwi:z] action in deforming[di:5fC:m] the plastic metal, as contrasted with the rapid-impact[5impAkt] blows of a hammer. The squeezing action is carried completely to the center of the part being pressed, thoroughly working the entire section[5sekFEn]. These presses are the vertical[5vE:tikEl] type and may be either mechanically[mi5kAnikEli] or hydraulically[hai5drC:lik] operated. The mechanical presses, which are faster operating and most commonly used, range in capacity[kE5pAsiti] from 5_ to 1_0 tons.与锤锻的快速冲击不同,压力机锻造是用缓慢的挤压作用使塑性金属变形.这挤压作用完全被施加到正在被压锻的零件中心位置上,直至彻底使整个工件得到加工.这些压力机都是立式的,可能是机械操作也可能是液压操作的.机械操作压力机,操作速度比较快,使用最普遍,锻造能力从 5_吨到1__吨范围.For small press forgings, closed impression dies are used and only one stoke of the ram[rAm] is normally required to perform[pE5fC:m] the forging operation. The ma_imum[5mAksimEm] pressure is built up at the endof the stroke which forces the metal into shape. Dies may be mounted[maunt] as separate units, or all the cavities may be put into single block. Forsmall forgings, individual[7indi5vidjuEl] die unites are more convenient. There is some difference in the design of dies for different metals; copper-alloy forgings can be made withless draft[drB:ft] than steel,consequently more complicated[5kCmplikeitid]shapes can be produced. These alloys flow well in the die and are rapidly e_truded 对于小型压力锻使用闭式锻模.通常要求锻锤仅一个冲程就完成锻造工艺.在冲程终端产生最大压力,该冲击压力迫使金属成形.模具可由各白独立的单元装配而成,即把所有个别模腔都放到一起,组成整体.对于小型锻件使用分模装置更为方便.对于不同的金属在模具设计上有些区别 .铜合金锻件比钢件用较小的拔模斜度,因此可生产更加复杂形状的锻件.这些合金在该种模具中流动性好,而且能快速挤压成形.In the forging press, a greater proportion of the total work put into the machine is transmitted[trAnz5mit] to the metal than in a drop hammer press. Much of the impact of the drop hammer is absorbed by the machine and foundation. Press reduction of the metal is faster, and the cost of operation is consequently lower. Most press forgings are symmetrical[si5metrikEl] in shape, having surfaces which are quite smooth, and provide a closer tolerance[5tClErEns] than is obtained by a drop hammer. However, many parts of irregular[i5re…ulE] and complicated shapes can be forged more economically by drop forging. Forging press is often used for sizing operations on parts made by other forging processes.锻压机比落锤锻,输入到机器里的总能量中有更大部分的能量被传输到金属坯料上.落锤锻的冲击能量被机器和基础吸收得较多(比起压力机来〕.金属上的压力衰减较快,因此生产成本比较低.大多数压力锻锻件形状.产生的表面都是对称的,而且表面非常光滑,并比落锤锻件的公差尺寸更加精确.然而落锤锻造可以锻制形状复杂而不规则的锻件,因而较为经济.锻压机常常用来为其他锻造工艺所生产的锻件进行整形和校正加工用.In drop forging, a piece of metal, roughly[5rQflI] or appro_imately of the desired[di5zaiE] shape, is placed between die faces having the e_act form of the finished piece, and forced to take thin form by drawing the dies together. Large ingots are now almost always forged with hydraulic presses instead of with steam hammers, sinc。
机械外文翻译中英文

附录英文原文N/C Machine Tool ElementN/C machine tool elements consist of dimensioning systems, controlsystems,servomechanisms and open-orclosed-loop systems. It is important to understand each elementprior to actual programming of a numerically controlled port.The term measuring system in N/C refers to the method a machine tool uses to move a partfrom a reference point to a target point. A target point may be a certain locating for drilling a hole,milling a slot, or other machine operation. The two measuring systems used on N/C machines arethe absolute and incremental. The absolute measuring system uses a fixed reference point. It ison this point that all positional information is based. In other words, all the locations to which apart will be moved must be given dimensions relating to that original fixed reference point.Figure shows an absolute measuring system with X and Y dimensions, each based on the origin.The incremental measuring system has a floating coordinating system. With the incrementalsystem, the time the part is moved. Figure 16.2 show X and Y values using an incrementalmeasuring system. Notice that with this system, each new location bases its values in X and Yfrom the preceding location. One disadvantage to this system is that any errors made will berepeated throughout the entire program, if not detected and corrected.There are two types of control systems commonly used on N/C equipment: point-to-point andcontinuous path. A point-to-point controlled N/C machine tool, sometimes referred to as apositioning control type, has the capability of moving only along a straight line. However, whentwo axes are programmed simultaneously with equal values a 45 angle will be generated.Point-to-point systems are generally found on drilling and simple milling machine where holelocation and straight milling jobs are performed. Point-to-point systems can be utilized togenetate arcs and angles by programming the machine to move in a series of small steps. Usingthis technique, however, the actual path machined is slightly different from the cutting pathspecified.Machine tools that have the capability of moving simultaneously in two or more axes areclassified as continuous-path or contouring. These machines are used for machining arcs, radii,circles, and angles of any size in two or there dimensions. Continuous-path machines aremoreexpensive than point-to-point systems and generally require a computer to aid programming when machining complex contours.N/C servomechanisms are devices used for producing accurate movement of a table or slid along an axis. Two types of servos are commonly used on N/C equipment: electric stepping motors and hydraulic motors. Stepping motor servos are frequently used on less expensive N/C equipment. These motors are generally high-torque power servos and mounted directly to a lead screw of a table or tool slide. Most stepping motors are actuated by magnetic pulses from the stator and rotor assemblies. The net result of this action is that one rotation of the motor shaft produces 200 steps. Connection the motor shaft to a 10-pitch lead screw allows 0.0005-in. movements to be made. Hydraulic servos produce a fluid pressure that flows through gears or pistons to effect shaft rotation. Mechanical motion of lead screws and slides is accomplished through various values and controls from these hydraulic motors. However, they are more expensive and noisy. Most larger N/C machines use hydraulic servos.N/C machines that use an open-loop system contain no-feedback signal to ensure that a machine axis has traveled the required distance. That is, if the input received was to move a particular table axis 1.000 in, the servo unit generally moves the table 1.000 in. There is no means for comparing the actual table movement with the input signal, howeve r, The only assurance that the table has actually moved 1.000 in. is the reliability of the servo system used.Open-loop systems are, of course, less expensive than closed-loop systems. A closed-loop system compares the actual output with the input signal and compensates for any errors. A feedback unit actually compares the amount the table has been moved with the input signal. Some feedback units used on closed-loop systems are transducers, electrical or magnetic scales, and synchros. Closed-loop systems greatly increase the reliability of N/C machines. Machining Centers Many of today’s more sophisticated lathes are called machining centers since they are capable of performing, in addition to the normal turning operations, certain milling and drilling operations. Basically, a machining center can be thought of as being a combination turret lathe and milling machine. Additional features are sometimes included by manufacturers to increase the versatility of their machines.Numerical ControlOne of the most fundamental concepts in the area of advanced manufacturing technologies is numerical control (NC). Prior to the advent of NC, all machine tools were manually operated and controlled .Among the many limitations associated with manual control machine tools, perhaps none is more prominent than the limitation of operator skills. With manual control, the quality of the product is directly related to and limited to the skills of the operator. Numerical control represents the first major step away from human control of machine tools.Numerical control means the control of machine tools and other manufacturing systems through the use of prerecorded, written symbolic instructions. Rather than operating a machine tool, an NC technician writes a program that issues operational instructions to the machine tool. For a machine tool to be numerically controlled, it must be interfaced with a device for accepting and decoding the programmed instructions, known as a reader.Numerical control was developed to overcome the limitation of human operators, and it has done so. Numerical control machines are more accurate than manually operated machines, they can produce parts more uniformly, they are faster, and the long-run tooling costs are lower. The development of NC led to the development of several other innovations in manufacturing technology:1. Electrical discharge machining.2. Laser cutting.3. Electron beam welding.Numerical control has also made machine tools more versatile than their manually operated predecessors. An NC machine tool can automatically produce a wide variety of parts, each involving an assortment of widely varied and complex machining processes. Numerical control has allowed manufacturers to undertake the production of products that would not have been feasible from an economic perspective using manually controlled machine tools and processes. Like so many advanced technologies, NC was born in the laboratories of the Massachusetts Institute of Technology. The concept of NC was developed in the early 1950s with funding provided by the U. S. Air force. In its earliest stages, NC machines were able to make straight cuts efficiently and effectively.However, curved paths were a problem because the machine tool had to be programmed to undertake a series of horizontal and vertical steps to produce a curve. The shorter is the straight lines making up the steps, the smoother is the curve. Each line segment in the steps had to be calculated.This problem led to the development in 1959 of the Automatically Programmed Too ls (APT) language. This is a special programming language for NC that uses statements similar to English language to define the part geometry, describe the cutting tool configuration, and specify the necessary motions. The development of the APT language was a major step forward in the further development of NC technology. The original NC systems were vastly different from those used today. The machines had hardwired logic circuits. The instructional programs were written on punched paper, which was later to be replaced by magnetic plastic tape. A tape reader was used to interpret the instructions written on the tape for the machine. Together, all of this represented a giant step forward in the control of machine tools. However, there were a numberof problems with NC at this point in its development.A major problem was the fragility of the punched paper tape medium. It was common for the paper tape containing the programmed instructions to break or tear during a machining process. This problem was exacerbated by the fact that each successive time a part was produced on a machine tool, the paper tape carrying the programmed instructions had to be rerun through the reader. If it was necessary to produce 100 copies of a given part, it was also necessary to run the paper tape through the reader 100 separate times. Fragile paper tapes simply could not withstand the rigors of a shop floor environment and this kind of repeated use.This led to the development of a special magnetic plastic tape. Whereas the paper tape carried the programmed instructions as a series of holes punched in the tape, the plastic tape carried the instructions as a series of holes punched in the tape, the plastic tape carried the instructions as a series of magnetic dots. The plastic tape was much stronger than the paper taps, which solved the problem of frequent tearing and breakage. However, it still left two other problems.The most important of these was that it was difficult or impossible to change the instructions entered on the tape. To make even the most minor adjustments in a program of instructions, it was necessary to interrupt machining operations and make a new tape .It was also still necessary to run the tape through the reader as many times as there were parts to be produced. Fortunately, computer technology became a reality and soon solved the problems of NC associated with punched paper and plastic tape.The development of a concept known as direct numerical control (DNC) solved the paper and plastic tape problems associated with numerical control by simply eliminating tape as the medium for carrying the programmed instructions. In direct numerical control .machine tools are tied, via a data transmission link, to a host computer. Programs for operating the machine tools are stored in the host computer and fed to the machine tool as needed via the data transmission linkage. Direct numerical control represented a major step forward over punched tape and plastic tape. However, it is subject to the same limitations as all technologies that depend on a host computer. When the lost computer goes down, the machine tools also experience downtime. This problem led to the development of computer numerical control.The development of the microprocessor allowed for the development of programmable logic controllers (PLCs) and microcomputers. These two technologies allowed for the development of computer numerical control (CNC).With CNC, each machine tool has a PLC or a microcomputer that serves the same purpose. This allows programs to be input and stored at each individual machine tool. It also allows programs to be developed off-line and downloaded at the individual machine tool. CNC solved the problems associated with downtime of the hostcomputer, but it introduced another known as data management. The same program might be loaded on ten different microcomputers with no communication among them. This problem is in the process of being solved by local area networks that connect microcomputers for better data management. Cutting Tool GeometryShape of cutting tools, particularly the angles, and tool material are very important factors. Angles determine greatly not only tool life but finish quality as well. General principles upon which cutting tool angles are based do not depend on the particular tool, Basically, the same considerations hold true whether a lathe tool, a milling cutter, a drill, or even a grinding wheel are being designed. Since, however the lathe tool, depicted in Fig. 18.1, might be easiest to visualize, its geometry is discussed.Tool features have been identified by many names. The technical literature is full of confusing terminology. Thus in the attempt to cleat up existing disorganized conceptions and nomenclature, this American Society of Mechanical Engineers published AS A Standard B5-22-1950. What follows is based on it.A single-point tool is a cutting tool having one face and one continuous cutting edge, Tool angles identified in Fig. 18.2 are as follows:Tool angle 1, on front view, is the back-rank angle. It is the angle between the tool face and a line parallel to the tool base of the shank in a longitudinal plane perpendicular to the tool base. When this angle is downward from front to rear of the cutting edge, the rake is positive; when upward from front to black, the rake is negative. This angle is most significant in the machining process, because it directly affects the cutting force, finish, and tool life.The side-rake angle, numbered 2, measures the slope of the face on a cross plane perpendicular to the tool base. It, also, is an important angle, because it directs chip flow to the side of the tool post and permits the tool to feed more easily into the work.The end-relief angle is measured between a line perpendicular to the base and the end flank immediately below the end cutting edge; it is numbered 3 in the figure. It provides clearance between work and tool so that its cut surface can flow by with minimum rubbing against the tool. To save time, a portion of the end flank of the tool may sometimes be lest unground, having been previously forged to size. In such case, this end-clearance angle, numbered 4, measured to the end flank surface below the ground portion, would be larger than the relief angle.Often the end cutting edge is oblique to the flank. The relief angle is then best measured in a plane normal to the end cutting edge angle. Relief is also expressed as viewed from side and end of the tool.The side-relief angle, indicated as 5, is measured between the side flank, just below thecutting edge, and a line through the cutting edge perpendicular to the base of the tool. This clearance permits the tool to advance more smoothly into the work.Angle 6 is the end-cutting-edge angle measured between the end cutting edge and a line perpendicular to the side of the tool shank. This angle prevents rubbing of the cut surface and permits longer tool file.The side-cutting-edge angle, numbered 7, is the angle between the side cutting edge and the side of the tool shank. The true length of cut is along this edge. Thus the angel determines the distribution of the cutting forces. The greater the angle, the longer the tool life; but the possibility of charter increases. A compromise must, as usual, be reached.The nose angle, number 8, is the angle between the two component cutting edges. If the corner is rounded off, the arc size is defined by the nose radius 9. The radius size influences finish and chatter.Sand CastingThe first stage in the production of sand castings must be the design and manufacture of a suitable pattern. Casting patterns are generally made from hard word and the pattern has to be made larger than the finished casting size to allow for the shrinkage that takes place during solidification and cooling. The extent of this shrinkage varies with the type of metal or alloy to be cast. For all but the simplest shapes the pattern will be made in two or more pieces to facilitate moulding. If a hollow casting is to be made the pattern design will include extension pieces so that spaces to accept the sand core are moulded into sand. These additional spaces in the mould are termed core prints.Sand moulds for the production of small and medium-sized castings are made in a moulding box. The mould is made in two or more parts in order that the pattern may be removed.The drag half of the mould box is placed on a flat firm board and the drag half of the pattern placed in position. Facing sand is sprinkled over the pattern and then the mould box is filled with moulding sand. The sand is rammed firmly around the pattern. This process of filling and ramming may be done by hand but mould production is automated in a large foundry with the mould boxes moving along a conveyor, firstly to be filled with sand from hoppers and then to pass under mechanical hammers for ramming. When ramming of the sand is complete, excess sand is removed to leave a smooth surface flush with the edges of the moulding box.The completed drag is now turned over and the upper, or cope, portion of the moulding box positioned over it. The cope half of the pattern is placed in position, correct alignment being ensured by means of small dowel pins. Patterns for the necessary feeder, runner and risers are also placed so as to give an even distribution of metal into the mould cavity. The rise rs should coincide with the highest readily escape from the mould. The sizes of risers should be such thatthe metal in them does not freeze too rapidly. An important function of a riser is to act as reservoir of liquid metal to feed solidification within the mould. A thin coating of dry parting sand is sprinkled into mould at this stage. This is to prevent the cope and drag sticking together when the cope half is moulded. The cope is now filled with moulding sand and this is rammed firmly into shape in the same manner as in the making of the drag.After the ramming of sand in the cope is completed the two halves of the moulding box are carefully separated. At this stage venting of the moulding box are carefully separated. At this stage venting of the mould can be done, if necessary, to increase the permeability of the mould. After venting the patterns are carefully removed from both cope and drag, and a gate or gates are carefully cut to connect the runner channel with the main cavity. Gates should be sited to allow or entry into mould with a minimum of turbulence. Any loose sand is gently blown away and if a core is to be used it the cope upon the drag and it is then ready for use. Liquid metal is poured smoothly into the mould via the feeder. Pouring ceases when liquid metal appears at the top of the risers and the feeder channel is also full.When the metal that has been poured into a sand mould has fully solidified the mould is broken and casting is removed. The casting still has the runner and risers attached to it and there will be sand adhering to portions of the surface. Runners and risers are cut off and returned to the melting furnace. Sand cores are broken and adherent sand is cleaned from the surface by vibration or by sand blasting with dry sand. Any fins or metal flash formed at mould parting lines are removed by grinding and the castings are then ready for inspection.The main Elements of Horizontal Milling MachinesColumn and base The column and base form the foundation of the complete machine. Both are made from cast iron, designed with thick sections to ensure complete rigidity and freedom form vibration. The base, upon which the column is mounted, is also the cutting-fluid reservoir and contains the pump to circulate the fluid to cutting area.The column contains the spindle, accurately located in precision bearings. The spindle id driven through a gearbox from a vee-belt drive from the electric motor housed at the base of column. The gearbox enables a range of spindle speeds to be selected. In the model shown, twelve spindle speeds from 32 to 1400rev/min are available. The front of column carries the guideways upon which the knee is located and guided in a vertical direction.KneeThe knee, mounted on the column guideways, provides the vertical movement of the table. Power feed is available, through a gearbox mounted on the side, from a separate built-in motor, providing a range of twelve feed rates from 6 to 250mm/min. Drive is through a leadscrew, whose bottom end is fixed to machine base. Provision is made to raise and lower the knee byhand through a leadscrew and nut operates by a handwheel at the front. The knee has guideways on its top surface giving full-width support to the saddle and guiding it in a transverse direction. lock is provided to clamp the knee in any vertical position on the column.SaddleThe saddle, mounted on the knee guideways, providers the transverse movement of the table. Power feed is provided through the gearbox on the knee. A range of twelve feeds is available, from 12 to 500mm/min. Alternative hand movement is provided through a leadscrew and nut by a hand heel at the front of the knee.Camping of saddle to the knee is achieved by two clamps on the side of the saddle.The saddle has dovetail gun its upper surface, at right angles to the knee guideways, to provide a guide to the table in a longitudinal direction.TableThe table provides the surface upon which all workpieces and workholding equipment are located and clamped. A series of tee slots is provided for this purpose. The dovetail guides on undersurface locate in the guideways on the saddle, giving straight-line movement to the table in longitudinal direction at right angles to the saddle movement.Power feed is provided from the knee gearbox, through the saddle, to the table leadscrew. Alternative hand feed is provided by a handwheel at each end of the table. Stops at the front of the table can be set to disengage the longitudinal feed automatically in each direction. Spindle The spindle, accurately mounted in precision bearings, provides the drive for the milling cutters. Cutters can be mounted straight on the spindle nose or in curter-holding devices which in turn are mounted in the spindle, held in position by a drawbolt passing the hold spindle. Spindles of milling machines have a standard spindle nose to allow for easy interchange of cutters and cutter-holding devices. The bore of the nose is tapered to provide accurate location, the angle of taper being 1. The diameter of the taper depends on the size of the machine and may be 30,40,or 50 IST. Due to their steepness of angle, there tapers –known as non-stick or self-releasing- cannot be relied upon to transmit the drive to the cutter or cutter-holding device. Two driving keys are provided to transmit the drive.Overarm and arbor supportDue to the length of arbors used, support is required at the outer end to prevent deflection when cutting takes place. Support is provided by an arbor-support bracket, clamped to an overarm which is mounted on top of the column in a dovetail slide. The overarm is adjustable in or out for different lengths of arbor, or can be fully pushed in when arbor support is not required. Two clamping bolts are support is located in the overarm dovetail and is locked by which the arbor runs during splindle rotation.中文译文数控机床的组成部分数控机床的组成部分包括测量系统、控制系统、伺服系统及开环或闭环系统,在对数控零件进行实际程序设计之前,了解各组成部分是重要的。
机械类英语论文翻译.doc

机械类英语论文翻译.doc轴承内径 bearing bore diameter轴承寿命 bearing life轴承套圈 bearing ring轴承外径 bearing outside diameter轴颈 journal轴瓦、轴承衬 bearing bush轴端挡圈 shaft end ring轴环 shaft collar轴肩 shaft shoulder轴角 shaft angle轴向 axial direction轴向齿廓 axial tooth profile轴向当量动载荷 dynamic equivalent axial load轴向当量静载荷 static equivalent axial load轴向基本额定动载荷 basic dynamic axial load rating轴向基本额定静载荷 basic static axial load rating 轴向接触轴承 axial contact bearing轴向平面 axial plane轴向游隙 axial internal clearance轴向载荷 axial load轴向载荷系数 axial load factor轴向分力 axial thrust load主动件 driving link主动齿轮 driving gear主动带轮 driving pulley转动导杆机构 whitworth mechanism转动副 revolute (turning) pair转速 swiveling speed rotating speed转动关节 revolute joint转轴 revolving shaft转子 rotor转子平衡 balance of rotor装配条件 assembly condition锥齿轮 bevel gear锥顶 common apex of cone锥距 cone distance锥轮 bevel pulley; bevel wheel锥齿轮的当量直齿轮 equivalent spur gear of the bevel gear 锥面包络圆柱蜗杆 milled helicoids worm准双曲面齿轮 hypoid gear子程序 subroutine子机构 sub-mechanism自动化 automation自锁 self-locking自锁条件 condition of self-locking自由度 degree of freedom, mobility。
- 1、下载文档前请自行甄别文档内容的完整性,平台不提供额外的编辑、内容补充、找答案等附加服务。
- 2、"仅部分预览"的文档,不可在线预览部分如存在完整性等问题,可反馈申请退款(可完整预览的文档不适用该条件!)。
- 3、如文档侵犯您的权益,请联系客服反馈,我们会尽快为您处理(人工客服工作时间:9:00-18:30)。
Ceramics and Glasses陶瓷和玻璃A ceramic is often broadly defined as any inorganic nonmetallic material. By this definition, ceramic materials would also include glasses; however, many materials scientists add the stipulation that “ceramic” must also be crystalline.陶瓷通常被概括地定义为无机的非金属材料。
照此定义,陶瓷材料也应包括玻璃;然而许多材料科学家添加了“陶瓷”必须同时是晶体物组成的约定。
A glass is an inorganic nonmetallic material that does not have a crystalline structure. Such materials are said to be amorphous.玻璃是没有晶体状结构的无机非金属材料。
这种材料被称为非结晶质材料。
Properties of Ceramics and GlassesSome of the useful properties of ceramics and glasses include high melting temperature, low density, high strength, stiffness, hardness, wear resistance, and corrosion resistance.陶瓷和玻璃的特性高熔点、低密度、高强度、高刚度、高硬度、高耐磨性和抗腐蚀性是陶瓷和玻璃的一些有用特性。
Many ceramics are good electrical and thermal insulators. Some ceramics have special properties: some ceramics are magnetic materials; some are piezoelectric materials; and a few special ceramics are superconductors at very low temperatures. Ceramics and glasses have one major drawback: they are brittle.许多陶瓷都是电和热的良绝缘体。
某些陶瓷还具有一些特殊性能:有些是磁性材料,有些是压电材料,还有些特殊陶瓷在极低温度下是超导体。
陶瓷和玻璃都有一个主要的缺点:它们容易破碎。
Ceramics are not typically formed from the melt. This is because most ceramics will crack extensively (i.e. form a powder) upon cooling from the liquid state.陶瓷一般不是由熔化形成的。
因为大多数陶瓷在从液态冷却时将会完全破碎(即形成粉末)。
Hence, all the simple and efficient manufacturing techniques used for glass production such as casting and blowing, which involve the molten state, cannot be used for the production of crystalline ceramics. Instead, “sintering” or “firing” is the process typically used.因此,所有用于玻璃生产的简单有效的—诸如浇铸和吹制这些涉及熔化的技术都不能用于由晶体物组成的陶瓷的生产。
作为替代,一般采用“烧结”或“焙烧”工艺。
In sintering, ceramic powders are processed into compacted shapes and then heated to temperatures just below the melting point. At such temperatures, the powders react internally to remove porosity and fully dense articles can be obtained.在烧结过程中,陶瓷粉末先挤压成型然后加热到略低于熔点温度。
在这样的温度下,粉末内部起反应去除孔隙并得到十分致密的物品。
An optical fiber contains three layers: a core made of highly pure glass with a high refractive index for the light to travel, a middle layer of glass with a lower refractive index known as the cladding which protects the core glass from scratches and other surface imperfections, and an out polymer jacket to protect the fiber fromdamage.光导纤维有三层:核心由高折射指数高纯光传输玻璃制成,中间层为低折射指数玻璃,是保护核心玻璃表面不被擦伤和完整性不被破坏的所谓覆层,外层是聚合物护套,用于保护光导纤维不受损。
In order for the core glass to have a higher refractive index than the cladding, the core glass is doped with a small, controlled amount of an impurity, or dopant, which causes light to travel slower, but does not absorb the light.为了使核心玻璃有比覆层大的折射指数,在其中掺入微小的、可控数量的能减缓光速而不会吸收光线的杂质或搀杂剂。
Because the refractive index of the core glass is greater than that of the cladding, light traveling in the core glass will remain in the core glass due to total internal reflection as long as the light strikes the core/cladding interface at an angle greater than the critical angle.由于核心玻璃的折射指数比覆层大,只要在全内反射过程中光线照射核心/覆层分界面的角度比临界角大,在核心玻璃中传送的光线将仍保留在核心玻璃中。
The total internal reflection phenomenon, as well as the high purity of the core glass, enables light to travel long distances with little loss of intensity.全内反射现象与核心玻璃的高纯度一样,使光线几乎无强度损耗传递长距离成为可能。
•Composites 复合材料Composites are formed from two or more types of materials. Examples include polymer/ceramic and metal/ceramic composites. Composites are used because overall properties of the composites are superior to those of the individual components.复合材料由两种或更多材料构成。
例子有聚合物/陶瓷和金属/陶瓷复合材料。
之所以使用复合材料是因为其全面性能优于组成部分单独的性能。
For example: polymer/ceramic composites have a greater modulus than the polymer component, but aren’t as brittle as ceramics.Two types of composites are: fiber-reinforced composites and particle-reinforced composites.例如:聚合物/陶瓷复合材料具有比聚合物成分更大的模量,但又不像陶瓷那样易碎。
复合材料有两种:纤维加强型复合材料和微粒加强型复合材料。
Fiber-reinforced CompositesReinforcing fibers can be made of metals, ceramics, glasses, or polymers that have been turned into graphite and known as carbon fibers. Fibers increase the modulus of the matrix material.纤维加强型复合材料加强纤维可以是金属、陶瓷、玻璃或是已变成石墨的被称为碳纤维的聚合物。
纤维能加强基材的模量。
The strong covalent bonds along the fiber’s length give them a ve ry high modulus in this direction because to break or extend the fiber the bonds must also be broken or moved.沿着纤维长度有很强结合力的共价结合在这个方向上给予复合材料很高的模量,因为要损坏或拉伸纤维就必须破坏或移除这种结合。
Fibers are difficult to process into composites, making fiber-reinforced composites relatively expensive.把纤维放入复合材料较困难,这使得制造纤维加强型复合材料相对昂贵。