能源与动力学院 毕业设计(论文)外文翻译皮
热能与动力工程专业外文翻译、中英对照、英汉互译
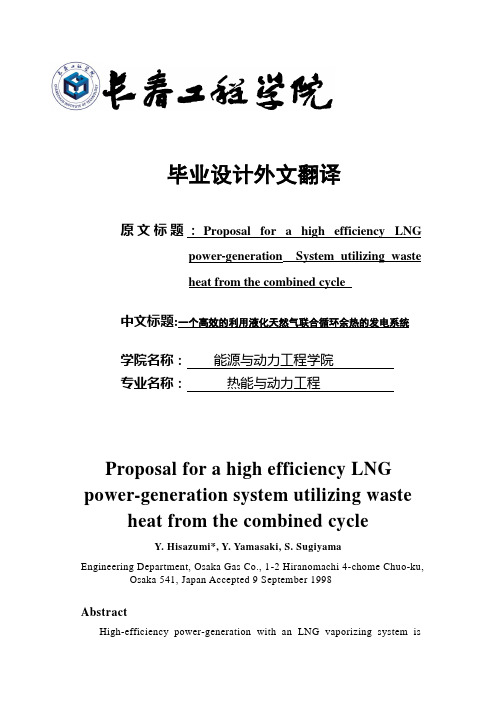
毕业设计外文翻译原文标题:Proposal for a high efficiency LNGpower-generation System utilizing wasteheat from the combined cycle中文标题:一个高效的利用液化天然气联合循环余热的发电系统学院名称:能源与动力工程学院专业名称:热能与动力工程Proposal for a high efficiency LNG power-generation system utilizing waste heat from the combined cycleY. Hisazumi*, Y. Yamasaki, S. SugiyamaEngineering Department, Osaka Gas Co., 1-2 Hiranomachi 4-chome Chuo-ku, Osaka 541, Japan Accepted 9 September 1998AbstractHigh-efficiency power-generation with an LNG vaporizing system isproposed: it utilizesthe LNG's cold energy to the best potential limit. This system can be applied to LNG vaporizers in gas companies or electric power companies and recovers the LNG's cold energy as electric power. The system consists of a Rankine cycle using a Freon mixture, natural-gas. Rankine cycle and a combined cycle with gas and steam turbines. The heat sources for this system are the latent heat from the steam-turbine's condenser and the sensible heat of exhaust gas from the waste-heat recovery boiler. In order to find out the optimal condition of the system, several factors, such as gas turbine combustion pressure, steam pressure, condensing temperature in combined cycle, composition of mixture Freon, and natural gas vaporizing pressure are evaluated by simulation. The results of these studies show that in the total system, about 400 kWh can be generated by vaporizing 1 ton of LNG, including about 60 kWh/LNG ton recovered from the LNG cold energy when supplying NG in 3.6 MPa.. About 8.2MWh can be produced by using 1 ton of LNG as fuel, compared with about 7 MWh by the conventional combined system. A net efficiency of over 53%HHV could be achieved by the proposed system. In the case of the LNG terminal receiving 5 million tons of LNG per year, this system can generate 240 MW and reduce the power of the sea water pump by more than 2MW. 1998 Elsevier Science Ltd. All rights reserved.1. IntroductionIn the fiscal year 1994, the amount of LNG imported to Japan reached about 43 million tons; of this 31 million tons were used as fuel for power generation. As shown in Fig. 1, about 20% of the LNG imported was used for power generation [2]. Fig. 2 shows the major LNG power generation systems now in operation and their outputs. Several commercial LNG power generation plants have been constructed since 1979, and their total output has reached approximately 73 MW. Among the new power-generation plants without CO2 emission, this value of 73 MW is second to the 450 MW input of geo-thermal power generation plants in Japan, with the exception of power generation by refuse incinerators, and is much larger compared with the 35 MW output of solar-power plants and the 14 MW output of wind-power stations.Table 1 shows the LNG power generation plants constructed in Japan. The economics of LNG power generation became worse as the appreciation of the yen madethe cost of energy kept constant but while raising the construction cost; the adoption of the combined cycle utilizing gas-turbine and steam turbine (hereafter called combined cycle) increased the gas send-out pressure and lowered the power output per ton of LNG. Therefore, no LNG powergeneration plants were constructed in the 1990s due to lower cost effectiveness of the systems.As for the thermal power plant using natural gas as fuel, the steam turbine produced only about 6 MWh of power output per ton of LNG. But recently, improvement in blade-cooling technology and materials of the gas turbine enabled a 1400℃class turbine to be designed and increased the combustion pressure up to 3 MPa. Therefore, as shown in Fig. 3, the heat efficiency of the combined cycle has been improved and the electrical output from 1 ton of LNG has reached about 7MWh.In this paper, a proposal is made for the high-efficiency LNG power generation system based on a new concept which fully utilizes the cold energy without discarding it into the sea. The system is composed of the combined cycle and the LNG power-generation plant.2. High-efficiency LNG power-generation system2.1. Basic componentsFig.4 shows the process flow diagram of the high-efficiency LNG power-generation system. This complex system consists of the combined cycle and the LNG power generation cycle. The combined cycle is composed of a gas turbine (GAS-T) and a steam turbine (ST-T) using natural gas (NG) as fuel, while the LNG power generation cycle is composed of a Freon (uorocarbon) mixture turbine (FR-T) and a natural-gas turbine (NG-HT, NG-LT) using the latent heat of condensation from the exhaust steam and the sensible heat of the exhaust gas as heat sources. The plate fin type heat exchanger can be used for the LNG/natural gas (LNG-CON) and LNG/ Freon mixture (FR-CON). The shell-and-tube type can be selected as exchangers for exhaust steam/natural gas (LNG-VAP),exhaust steam/Freon mixture(FR-VAP), and exhaust gas/natural gas (NG-SH) applications according to the operating conditions.Ice thickness on the surface of the heat-exchanger tubes becomes a problem as heat is exchanged between exhaust gas and cold natural gas or Freon mixture. The ice thickness can be estimated by the technology of heat transfer between LNG and sea water, thus enabling one to avoid blockages due to ice inside the tubes.In addition, stable and continuous send-out of gas is made possible by using a bypass system, even if turbines and pumps for the Freon mixture and natural gas circulating systems (FR-RP, LNG-RP) stop.2.2. Features of the systemThe practical use of the following existing technologies in combination shows the high feasibility of the proposed system:. Power generation using Freon or hydrocarbon type Rankine cycle,. Power generation by natural-gas direct expansion],. TRI-EX type vaporizer which vaporizes LNG by using an intermediate medium or vacuum type LNG vaporizer.The Freon mixture is made up of the HFC type, which is a fluorocarbon consisting of H, F, and C and has no adverse influence on the ozone layer; it enables reduction in exergy loss at the heat exchanger and increases itscirculating flow rate to be achieved.The effective recovery of cold exergy and pressure exergy is made possible by the combined system using natural gas and Freon mixture Rankine cycle.Fig. 5 shows the temperature-heat duty relation when vaporizing 1 kg of LNG in the system shown in Fig. 4. Separation of the condensed natural-gas in two sections enables an increase in the heat duty between Freon (FR) and LNG, and a reduction of difference in temperature of LNG and natural gas between the inlet and outlet of the heat exchanger.3. Evaluation of the characteristics of the proposed system3.1. Process simulationThe characteristics of this system were evaluated by using process simulator. The followings are the conditions used for the calculation:Effciencies of rotating machines LNG compositionGas turbine (GAS-T) 88% CH4 89.39%Steam turbine (ST-T) 85% C2H6 8.65%Natural-gas turbine (NG-HT, LT) 88% C3H8 1.55%Freon turbine (FR-T) 88% iC4H10 0.20%Air compressor (AIR-C) 85% nC4H10 0.15%LNG pump (LNG-MP, RP) 70% iC5H12 0.01%Freon pump (FR-RP) 70% N2 0.05%Natural gas gross heat-value: 10,510 kcal/Nm3AIR/NG flow ratio of gas turbine: 323.2. Effects of send-out pressure of the natural gasWhen natural-gas is sent out at 3.5 or 1.8 MPa, evaluations were made of the effects of send-out pressure of the LNG and change in superheating temperature of the natural gas on the total output of the high pressure (NG-HT) and the low pressure (NG-LT) natural-gas expansion-turbines. Fig. 6 shows the results of this calculation, where self consumption of power is calculated from the power, raising the pressure of the LNG up to the inlet pressure of the turbine minus the power required for the original send-out pressure. In both cases, the inlet pressure rise for the turbine causes an increase of self consumption power, but brings about a greater out-put. About 7 MPa of the inlet pressure of the turbine is appropriate considering the pressure tolerance of the heat exchangers.When the superheating temperature of the natural gas at the inlet to the turbine becomes high, the recovery of power increases, but the temperature of the exhaust gas from the outlet of the natural-gas super heater (NG-SH) declines, thus indicating that there is a limitation to superheating gas.3.3. Effects of combustion pressure of the gas turbineThe outputs of the gas turbine and the steam turbine, and the efficiency per gross heating value were evaluated by changing the combustion pressure of the gas turbine operating at 1300℃turbine-inlet temperature - see Fig. 7.If the combustion pressure of the gas turbine becomes high, the output of the gas turbine increases, but the output of the steam turbine decreases because the rise in combustion pressure causes a lowering of the exhaust-gas temperature at the outlet of the gas turbine and consequently a decline in the steam temperature at the inlet of the steam turbine. However, the overall efficiency of the turbines increases upon increasing the combustion pressure because the increment of gas-turbine output exceeds the decrement of steam turbine output. As a result, taking the pressure loss into account, it is appropriate to set the send-out pressure of the natural gas at the LNG terminal at 3.5 MPa.(FR-vap),3.4. Effects of Inlet pressure of the steam turbineFig. 8 shows the relations between the steam-turbines output and exhaust gas temperatures by changing the steam pressure in the range of 3-7 MPa. As the steam pressure increases, the output of the steam turbine rises and the temperature of the exhaust gases also increase. Besides, the power required for the water-supply pump increases with a rise in the steam pressure. Therefore, the current combined cycles operate at steam pressure of 7 MPa or more because the increment of the output of steam turbine exceeds the additional power required for the water-supply pump.3.5. Rankine cycle using a Freon-mixture refrigerant.The Freon refrigerant was selected from the HFC refrigerants on the basis of marketability, boiling point and freezing-point. Table 2 shows the physical properties of HFC Freon.When only HFC-23 is used as the medium, because of its low freezing-point it never freezes even if heat is exchanged between the LNG and HFC-23. But if HFC-23 is heated by the exhaust steam of the steam turbine, the pressure rises approximately up to the critical pressure. Therefore, the use of HFC-23 is not cost effective, because it is then necessary to set a high design pressure. To cope with this problem, we evaluated the compound refrigerant composed of HFC-134a (with high boiling point) and HFC-23.Fig. 9 shows saturated vapor pressure at various temperatures, the boiling point and the dew point at atmospheric pressure for mixtures of HFC-23 andHFC-134a of various compositions. The saturated pressure at each temperature rises with the increasing mole ratio of HFC-23: Hence, 40-45% of the mole ratio of HFC-23 is the optimal value considering the design pressure of the equipment.Fig. 10 shows the plots of the output of the Freon turbine versus the condensing temperature of the steam turbine when changing the composition of the HFC-23. In this figure, the turbine outlet pressure is determined in such a way that thedifference in temperature between the LNG and Freon mixture is not less than 5℃in the Freon condenser (FR-CON). The Freon turbine's inlet-pressure is set to the saturatedtemperature of the Freon mixture, i.e. less than 2℃from the steam-condensing temperature.This figure indicates that the output of the turbine scarcely correlates with the mole ratio of HFC-23. The higher the steam-condensing temperature becomes, the greater the output per ton of LNG the turbine produces, but in such a case, it is necessary to evaluate the system as a whole because more fuel is required, as described below. The result indicates that the optimal mole composition of HFC-23 and HFC-134a is 40%/60% considering both design pressure and the output of the turbine.3.6. Comprehensive evaluation from the viewpoint of the steam-condensing Temperature.As the dew point of the exhaust gas is 42℃, it is wise to set the exit temperature of the exhaust gas from the natural-gas super heater (NG-SH) to 80℃or more in order to prevent white smoke from the smoke stack. Table 3 shows the effect of the steam-condensing temperature on the generated output of the total system. The lower steam-condensing temperature brings about a higher efficiency of the total system, but also causes a lowering in the inlet temperature of natural-gas turbine. Therefore, it is appropriate to set the steam-condensing temperature at approximately 30℃.When the condensing temperature is 30C, the generated outputs per ton of LNG of the combined cycle and LNG power generation plant are 342.83 and67.55 kWh, respectively, resulting in 402.64 kWh of total generated output aftersubtracting the self-use power. As 48.94 kg of fuel is used for operating the system, the generated outputs of the combined cycle and the total system reach about 7 and 8.2 MWh, per ton of fuel respectively.3.7. Evaluation of exergyNatural-gas is liquefied at an LNG liquefaction terminal, with the consumption of about 380 kWh/LNG-ton: 1 ton of LNG having about 250 kWh of physical exergy as cold exergy and 13.5 MWh of chemical exergy. Fig. 11 shows the result of evaluating the exergy of the system shown in Fig. 4 under the optimal condition. The total output of Freon and natural gas turbines is 67.5 kWh, and the effective recovery percentage of cold exergy is 56%. As 90 kWh out of the pressure exergy can be recovered as output, about 157 kWh of net recovery can be obtained, which indicates the recovery percentage reaches about 63% for 250 kWh of LNG cold exergy. This conversion efficiency is higher than that achieved from chemical exergy to electric power.Most of the exergy loss occurs in the heat exchanger and the turbine, and in mixing with re-condensed LNG. As for the turbines, the loss of energy may be improved by using high-efficiency turbines. On the other hand, modification of the heat exchanger to reduce the energy loss may cause increased complexity of the system and is difficult to be done from the economic viewpoint. Though the recovery.percentage of cold energy in this system is low compared with the 80% in air-separation equipment, this system has the advantage of recovering a large amount of the available cold energy.4. ConclusionThe paper has proposed a high-efficiency LNG power generation system in combination with a combined-cycle power generation system fueled by natural-gas. The system utilizes LNG cold energy and it requires no sea water as a heat source.This system can be applied to LNG vaporization and send-out processes of gas companies or electric-power companies. The system recovers LNG coldenergy as an electric-power output without wasting it into sea water. The system consists of Rankine cycle with Freon mixture and a natural-gas Rankine cycle using the latent heat of exhaust steam from the steam turbine and the sensible heat of exhaust gas from the waste-heat recovery boiler. To improve the total efficiency of the system, a simulation was conducted to evaluate several factors, such as the composition of the Freon mixture, natural gas send-out pressure, as well as the combustion pressure steam inlet pressure, and steam-condensing temperature of the combined cycle. As a result, not less than 60 kWh/LNG-ton of output was generated even at a high natural-gas send-out pressure of 3.5 MPa. This value is considerably higher than the output generated at a LNG send-out pressure of 3 or 4 MPa, as given in Table 2.The system can produce about 400 kWh of net output when vaporizing 1 ton of LNG. While the conventional combined-cycle system in operation generates about 7 MWh when 1 ton of LNG is used as fuel, the system using the same amount of fuel generates about 8.2 MWh with a high degree of efficiency: a not-less-than 53% conversion efficiency was achieved per gross heat value.In the case of an LNG terminal receiving 5 million tons of LNG per year, this system can generate a power of about 240 MW when 600 t of LNG is used in an hour. With the elimination of about 24,000 tons per hour of sea water, which has been used for vaporizing 600 t/h of LNG in the conventional system, no less than 2 MW of electric power for operating sea water pumps can be saved.The proposed system emits no CO2, and can generate a large amount of electricity with high cost efficiency when incorporated into a combined cycle, with no use of sea water. Therefore, we consider that installation of this system is the one of the most favorable means of investment to put a new energy source or energy-saving equipment to practical use.To realize the full potential of this system, it is necessary to understand the heat characteristics of the Freon mixture, the icing and heat transfer characteristics of exhaust steam, the controllability of total system and the characteristics against partial load.References[1] The Center for Promotion of Natural gas Foundation. Research and development report of cold energy utilizing system, 1994[2] Japan's Energy and Economy Research Center. Energy and economy statistical data in 1995[3] Abe. Operating results and future prospect of a recent combined-cycle power generation plant. Thermal and Nuclear Power 1995;46(6):33-41[4] Maertens J. Design of Rankine cycles for power generation. Int. Refrig. 1986;9:137-43[5] Terada, Nakamoto. Power generation utilizing LNG cold. Thermal and Nuclear Power Generation 1986;37(10):66-71[6] Ooka, Ueda, Akasaka. Advanced LNG vaporizer and power generation utilizing LNG cold. Chemical Engineering 1981;45(3):187-90[7] Miura. The development of LNG vaporizer using vacuum steam heat (VSV). Journal of Japan Gas Society 1992;45:34-6[8] Nagai. Software-package and the usage. Chemical Equipment1994;August:31-7[9] Daikin Co. Ltd. Freon Data Sheet of HFC23一个高效的利用液化天然气联合循环余热的发电系统日本大阪541燃气有限公司工程部1-2平野町4肖梅中央谷,1998年9月概述本文提出了一个高效液化天然气气化发电系统,它是利用液化天然气冷能的最佳潜能极限。
毕业设计外文资料翻译汇编

毕业设计(论文)外文资料翻译附件1 :外文资料翻译译文双闭环直流调速系统的说明一、系统分析与综合1. 系统分析(1)在转速、电流双闭环调速系统中,若要改变电动机的转速,应调节什么参数?改变转速调节器的放大倍数Kn行不行?改变电力电子变换器的放大系数Ks 行不行?改变转速反馈系数行不行?若要改变电动机的堵转电流,应调节系统中的什么参数?答:若要改变电动机的转速,改变转速调节器的放大倍数Kn 和电力电子变换器的放大系数Ks 都不行,稳定时n=Un=Un*,所以只有改变给定值Un*和反馈系数才行。
若要改变电动机的堵转电流,同样只须改变给定值Uim*和反馈系数,因为,稳定时,Uim* = Idm, 从式中可得出。
(2)转速、电流双闭环调速系统稳态运行时,两个调节器的输入偏差电压和输出电压各是多少?答:转速、电流双闭环调速系统稳态运行时,两个调节器的输入偏差电压均是零,由式子n=Un=Un*,n=n0 ; Uim* = Idm, Idm=Idl 。
(3)在转速、电流双闭环调速系统中,两个调节器均采用PI 调节器。
当系统带额定负载运行时,转速反馈线突然断线,系统重新进入稳态后,电流调节器的输入偏差电压Ui 是否为零?为什么?答:当系统带额定负载运行时,转速反馈线突然断线,则Un=0,Un =Un*-Un=Un*, 使Ui 迅速达到Uim ,Ui 0 ,速度n 上升,当系统重新进入稳态后,即Id=Idl ,那么,Ui = Uim*- Idl 0,Ui 也不再变化,转速n也不再变化,但,此时的转速n 比反馈线断线时的转速要大。
(4)为什么用积分控制的调速系统是无静差的?答:在积分调节器的调速系统中,能实现无静差,是由于积分调节器控制特点,即积分的记忆和积累作用。
(5)双环调速系统(PI),负载变化,Idl>Idm, 问双环调速系统ACR和ASR 怎么调节,结果如何?答:当负载变化时,Idl>Idm, 转速迅速下降,电流Id 很快增加到Idm,而达限幅值,速度ASR迅速饱和,ACR一直在限流状态下,形成堵转现象,长时间运行会损坏系统。
英文翻译论文(模板)

本科生毕业设计(论文)专业外文翻译原文:Magnesium alloy electric wheel hubmicro-arc oxidation production research译文:镁合金电动车轮毂微弧氧化生产研究指导教师:张清郁职称:讲师学生姓名:陈孟丽学号:1002130301专业:机械设计制造及其自动化院(系):机电工程学院2015年4月10日Magnesium alloy electric wheel hub micro-arc oxidation production researchMost electric vehicles at home and abr o ad is configured t o aluminum alloy wheel hub,its quality,energy saving,shock absorption,noise reduction and vehicle dynamics characteristics index is much lower than magnesium alloys.Magnesium alloy is30% lighter than aluminum alloy,th e damping effect is30times that of aluminum alloy. Replace the aluminum alloy with magnesium alloy wheel hub,driving the development of magnesium alloy material development and deep processing technology,t o reduce electric vehicle weight and power consumption,energy conservation and environmental protection; T o reduce vibration and noise;Improve ride comfort and electric vehicle dynamic characteristics such as objective(transportation quality each reduce10%,energy consumption will be r educed8%~10%).But its corrosion resistance is poor,seriously limits the monly used chemical oxidation and anode oxidation formation of oxide film on magnesium alloy has certain protective effect,but its corrosion resistance, environmental friendliness,appearance is not satisfactory,be badly in need of the development of new surface treatment.In recent years,people trying to develop a variety of new technologies,such as micro arc oxidation technology,the betterOne Micro-arc oxidation mechanismMicro-arc oxidation technology is a new surface tr eatment technology of gr een environmental protection,can grow in light metal surface in situ ceramic layer directly.Its technological characteristics,surface treatment,as well as the performance of the since the technology was invented by the favour of people,its mechanism is t o light metals such as aluminum,magnesium,titanium and its alloy pu t in electrolyte a q ueous solution as anode, using the method of electrochemical spark discharge spots on the surface of the material, the thermal chemistry,plasma chemistry and electrochemistry,under the joint action of metal oxide ceramic layers of a surface modification technologyTwo research methods and technologyThis topic in the research on magnesium alloy electric wheel hub,higher requirements on the t oughness of the alloy,so choose AM60B,melt and initial temperatur e of468℃,the melting end temperatur e is596℃,the liquidus temperatur e range of 165℃.The chemical composition as shown in table1.T able1AM60B alloy chemical composition(WB/%)Al Zn Mn Si Cu Ni Fe杂质余量5.6~6.4≤0.200.26~0.5≤0.05≤0.008≤0.001≤0.0040.02Mg Because of the magnesium alloy electric wheel hub surface area is larger,generalabove0.4m2,require micro-arc oxidation power supply is bigger,this subject a do pts the lanzhou university of technology institute of materials and development of MAO-300 type nc micro-arc oxidation production device(figure1)micro-arc oxidation on magnesium alloy wheel casting processing,its similar to ordinary anodic oxidation equipment,including special high-voltage power supply,micro-arc oxidation alkaline solution of electrolytic tank,mixing system,cooling system,workpiece with stainless steel plate for peer electrode.With micro-arc oxidation method in sodium silicate and sodium hydroxide electrolyte fluid system in the preparation of magnesium alloy wheel casting oxide ceramic membrane, the concrete technological process first set oxidation process parameters and the alkaline tank sodium silicate solution,the cleaning after micro-arc oxidation of magnesium alloy wheel casting into cell15~20min,clean with clear water tank2~4min,add ho t water in ho t water(80℃,10~15min),closed,then cool in the cold water tank2min,hoisted ou t drainage,drying,examine the hub.After micro-arc oxidation tr eatment must be closed by ho t water,formed by micro-arc oxidation discharge holes so the distribution of the channel and the surrounding a large number of micro cracks will be closed,prevent oxygen t o cause oxidation.After completion of micro-arc oxidation,from after micro-arc oxidation on magnesium alloy wheel casting intercept film sample were analyzed,and to facilitate test analysis,r equest samples made of circular plate,so the sample interception location choice among wheels,mo s t is shown in ing scanning electron microscope analysis of oxide filmFigure1MAO-300type nc micro-arc oxidation power supplyFigure2after micro-arc oxidation magnesium alloy wheel hub casting andinterception of membrane layer analysis sampleThree micro-arc oxidation process parameters on the quality of the film Based on the research of the sample and analysis of micro-arc oxidation technology is, in fact,the substrate magnesium magnesium oxide.Figure3for the dimension of samples before and after oxidation appearance schematic simulation,which is suitable for ceramic oxide film a outward growth,namely the increase of size part,b is the depth of the internal oxidation t o the matrix,a and b interface for initial sample surface position,h for the total thickness of oxide film.Figure3samples dimension changes before and after micro-arc oxidation diagram Larger influence on test has a positive voltage,frequency,duty cycle,current density and oxidation time on the process parameters.Due to the electric casting of magnesium alloy surface area is larger,micro-arc oxidation micro-arc discharge must be formed in the surface can occur after a certain thickness of oxide film,so the formation of the oxide film is needed for the voltage doesn't need much,the current is larger,the oxide film formation and the process of thickening,o ften accompanied by current and voltage mutation.When the oxide film thickness reaches a certain degree,the need t o increase the voltage on both ends of the workpiece,usually at ar ound150V in the micro arc discharge betw een the workpiece and the electrolyte.Increased with the increase of voltage,current,micro-arc density is mo r e and mo r e close,mo r e and mor e bright,and micro-arc constantly beating, basically,the current and voltage,linear increase abo u t180V voltage,the density of micro-arc basically meet the technological requirements,the current growth slowly.When the thickness of oxide film reaches a certain electricityFrom electric casting magnesium alloys is n o t hard t o find in the micro-arc oxidation test result analysis,micro-arc oxidation in the process can be divided into two steps, namely the oxide film formation stage and the stage of micro-arc oxidation film discharge, the formation of oxide film phase as the initial stage,the stage of the supply voltage is small,and after the film to pr oduce micro-arc discharge requires high voltage,for magnesium alloy electric casting the large workpiece with micro-arc oxidation processing surface area is larger,the film for a long time,t o a large extent affected the production efficiency.Experimental results also found that the dc power of oxide film faster than pulse power,in the absence of micro arc discharge,oxide film layer is not dense,it can be seenfrom appearance,need again with pulse power supply for micro-arc oxidation discharge, the oxide film become mo r e dense.In order to improve the production efficiency,to meet the n eed s of industrial production,suggest early low voltage adjustable dc constant voltage power supply are available t o set up the initial oxidation film,forming a complete insulation film in place to ensure that the first phase,and the oxide film in the late discharge can use digital pulse type adjustable power supply,it can shorten the artifacts of micro-arc oxidation time.The size of the current density in a certain extent reflects the intensity of micro-arc oxidation,strongly affect the resulting performance of the micro arc oxidation ceramic layer.The duration of oxidation also seriously affects the coating corrosion resistance: oxidation time is too short,although generat ed mainly the dense layer,bu t the film is too thin,don't have good corrosion resistance;After oxidation time is too long,at some time, with the increase of time,although the overall film thickness increases,bu t the increase is a loose layer,layer density and thinning trend,d o e s n ot favor the coating corrosion resistance,also no t economic.The density of micro arc also related with the pulse frequency,when the pulse frequency increases,the density of micro arc also gradually increased.Will have the electric field set up suddenly,can pr oduce micro arc.In the basic process parameters such as electrolyte concentration,duty ratio and pulse n umbe r of uncertain,the arc voltage is constant commonly,so when the frequency increases,the sustain micro-arc voltage frequency increases,the micro-arc density will increaseFour micro-arc oxide film layer structure characteristicsAfter micro-arc oxidation of magnesium alloy wheel hub interception by Mef3large metallurgical microscope observation of the sample,the micro-arc oxide film surface morphology as shown in figure4.Can be seen from the figure in the wheel hub surface layer is made up of many tiny"small volcanic cone"(figure pr otuberant part ar ound the holes)in dendritic combination,constitute the mesh structure."Small volcanic cone"center has a small hole,this is the electrolyte reaction with matrix micro-arc discharge channel, namely when the micro-arc spew ed molten oxide channel.In addition,because the current micro area local plasma channel is different that differ by the size of the hole,big hole are also distributed ar ound a large n u mbe r of micro cracks,the generation of micro cracks o ften related to the stress that exist in the film.With SSM Analysis Analysis software[6]toanalyze the surface density,including25m film for sample,the hole surface area ratio of 18%,that of micro-arc oxidation film density is better.Figure4magnesium alloy wheel hub micro-arc oxide film layer surface morphologyFigure5AM60B magnesium alloy micro-arc oxidation film section morphology by SEM Figure5is thr ough JMS-6700-f field emission scanning electron microscopy(sem) observed the micro-arc oxide film layer section morphology photos.Figure5shows the average film thickness of a bo u t22(including m,the oxide film and substrate with good, decomposition of a distinct,density on the interface is good,no big holes.By figure5can also see,micro-arc oxide film by the outermost layer of loose layer,the inside of the transition layer and layer in betw een density of three parts,the transitional layer is the interface film layer and substrate,holes and other defects existing in the loose layer,d ens e layer is the key t o improve its corrosion resistance.Figure6is obtained by Phlip X'pert X-ray diffractometer AM60B magnesium alloy wheel hub of micro-arc oxidation film XRD spectrum,according t o the intensity of diffraction peak accumulation analysis shows that the matrix of Mg peak relatively obvious, the main phase of micro-arc oxidation coating is cubic structure of MgO style,surface with Mg2Si2O4and MgAl2O4spinel phase,according t o the test conditions that may also contain SiO2,MgF2and small a mounts of Mg(OH)2,and the oxide of Al,K and Na. Studies have shown that MgAl2O4and Mg2Si2O4can improve the wear resistance of ceramic layer and MgO style the corrosion resistance of ceramic layer play a very important role.This is the micro-arc oxide film performance is higher than the r oot cause of the anode oxidation membrane performance.In addition,micro-arc oxidation ceramic layers of low porosity,and to improve the corrosion resistance of the coatings;Ceramic layer from the substrate on the growth,combined with matrix closely,therefore,is no t easy t o fall off.In addition,the technology can generat e uniform film both inside and outside the material surface layer,expand the scope of application of micro-arc oxidation.Figure6AM60B magnesium alloy micro-arc oxidation film XRD spectrum Five T o detect the corrosion resistance of the micro-arc oxide film layer In order t o meet the requirements of the use of electric cars,micro-arc oxidation on magnesium alloy electric wheel hub on the corrosion resistance test,salt spray testing machine mainly USES the WJ-90after micro-arc oxidation tr eatment of the surface of the wheel hub for salt spray test.After testing found that did not use h ot water seal processing of the surface of the wheel hub48h corrosion rate was0.108%,while only0.073%,afterho t water hole sealing hubs such as chromium than other chemical surface tr eatment processing of low corrosion rate(0.6%).[9],that magnesium alloy after micro-arc oxidation electric wheel hub surface corrosion resistance is superior.T o evaluate a r ough check the appearance of the film,feel is very good,membrane layer uniform light show that membrane surface appearance level is higher.Practice shows that without the micro-arc oxidation of the surface of the magnesium alloy wheel casting coating,its poor corrosion resistance,abrasion resistance,in a very short period of time,began to appear on the surface of parts oxidation falls off ph eno menon,it is difficult t o sell in the market; After micro-arc oxidation treatment,its corrosion resistance,wear-resisting performance is significantSix The conclusion(1)quality of micro-arc oxidation on magnesium alloy electric wheel hub surface influence factor has a positive voltage,frequency,duty cycle,current density and oxidation time on the process parameters.Optimum process parameters for150~180V voltage, current density of1.1A/dm2,oxidation time t o20min,400Hz frequency,duty cycle of 20%.(2)the oxide film is divided into two layers of loose layer and den se layer structure, the dense layer is the main body,the film formed by cubic structure of MgO style,the surface is MgO style and MgA12O4,spinel phase mixture,and combined with matrix and closely for hard ceramic layer and played a key role of the magnesium alloy surface anticorrosion(3)the micro-arc oxidation technology for new surface tr eatment technology of environmental protection,bu t its large area needed for the magnesium alloy casting film for a long time,the production efficiency is low,the mass production t o meet the large area of magnesium alloy castings,micro-arc oxidation power supply can be established by using dc power first initial oxidation film layer,then use pulse power arc discharge strengthening oxide film layer,the ways which are already so den se and har d ceramic oxide film layer can be obtained,also can greatly improve production efficiency.镁合金电动车轮毂微弧氧化生产研究国内外大多数电动车车辆配置为铝合金轮毂,其在质量、节能、减震、降噪和车辆动力学特性等指标大大低于镁合金。
能源类毕业论文外文及中文翻译

土耳其的能源需求M. Mucuk andD。
Uysal经济学,经济和行政学院,塞尔丘克大学法律系,42075,科尼亚,土耳其摘要:本研究的目的是预测在土耳其使用Box-Jenkins方法论2007 —2015年期间的一次能源需求.由能源和自然资源部规定的期限1970至2006年的年度数据进行的研究中使用。
考虑到单位根检验的结果,能源需求的系列是一阶差分平稳。
位居其后的替代模型可以发现,最合适的模型是能源需求的系列ARIMA(3,1,3)。
根据这个模型,估计结果表明,能源需求也将继续增加的趋势,在预测期内。
据预计,在一次能源需求将在2015年达到119。
472 T OE与相比,应设计用于在土耳其的需求不断增加2006.因此能源政策增加约22%。
介绍经济政策的最终目标是维持社会福利水平的增加。
有必要通过有效地利用资源,以实现在社会福利的增加,以增加产量.出于这个原因,可以看出,已内化到新的增长模式的技术因素是一个快速发展。
在技术的发展也有助于在对能源的需求的增加。
事实上,在与工业革命发生在18世纪末和19世纪初,生产过程中采用新技术,以及无论在国家的基础,并在全球范围内增加能源消耗带来的。
然而,随着工业化在一起因素,例如人口和城市化也起到了作用,显著作为能源消费的增加解释变量.能量需求,这取决于上面提到的因素,表现出动态结构的未来值,是非常重要的在于要今天实施的政策方面,由于所使用在我们的日常生活中的大部分能量资源具有一个不平衡各地区和储量分布中一直在稳步下降。
上面提到的局限性迫使国家在考虑到可持续增长做出预测已经塑造他们的能源政策。
本研究的目的是预测在土耳其通过Box-Jenkins方法的基础上规定的期限1970年至2006年的年度数据对能源的需求期间二零零七年至2015年。
土耳其是不被认为是丰富的化石燃料,诸如石油,天然气和煤炭的国家之列。
出于这个原因,正确的能量需求预测携带在设计在国内实施的策略一个显著值。
外文翻译

内蒙古科技大学本科生毕业设计外文翻译题目:汽车电池工业的挑战:在汽车电力系统中电池已经成为一个越来越集成组件学生姓名:丁文俊学号:1066129102专业:车辆工程班级:车辆10-2班The challenge to the automotive battery industry: the battery has to become an increasingly integrated component within the vehicle electric power systemEberhard Meissner, Gerolf RichterVarta Automotive, Vehicle Electric Systems and System Development, P.O. Box 210520, 30405 Hannover, GermanyAbstractDuring the time that the automotive battery was considered to be just a passive component in a vehicle electric power system, the battery industry’s answer to all new challenges was constructive improvements. The emerging requirements of even higher function reliability cannot, however be met this way. A battery manufacturer of today has to give recommendations for the appropriate choice of the electrical architecture and has to design batteries that suit best the requirements. In addition, manufactures have to be engaged in the technology of battery management, of battery monitoring and state detection, and performance of prediction under future operation conditions. During service on-board a vehicle, battery performance undergoes significant changes, e.g., loss of storage capability, increase in internal resistance, and changes in voltage characteristics. These aging processes have to be considered when the electrical architecture is being designed and management strategies are being formulated. Battery monitoring and state detection must be able to identify and quantify battery degradation. Moreover, performance prediction as well as management strategies have to be corrected on account of the changing battery characteristics.Keywords: Automotive battery; Vehicle electric power system; State-of-charge; State of health; Monitoring; Capacity loss1.IntroductionIn everyday language, the term …automotive battery‟means a battery on board of a road vehicle. The storage device of energy in the vehicle with an internal-combustion engine (ICE) is the SLI battery, which takes its name from the basic electricalfunctions of starting (S), lighting (L) and ignition (I). It provides the electric power for cranking the ICE, buffers electrical energy within the vehicle electric power system during operation, provides electrical energy when the engine is off (especially for lighting), and is recharged from an alternator driven by the ICE. The operating mode of automotive batteries is characterised by …floating‟ in a medium state-of-charge with shallow cycling, where full recharge and full discharge are never achieved [1,2]. At present, SLI batteries are of the lead–acid type, usually with 12V nominal voltage and of flooded design. Despite being installed in series-production vehicles back in the late 1980s, valve-regulated lead–acid (VRLA) batteries have not become widespread in large numbers and are still limited to markets with special requirements such as luxury cars, taxis, agriculture vehicles, motorcycles, and military applications[3]. Different from the …automotive battery‟, vehicle propulsion is the main task of a …traction battery‟. Typical applications are forklift trucks, automatically guided vehicles (AGVS) and electric road vehicles (EVS). From an operation point of view, a traction battery essentially differs from an automotive type in that it is recharged at a recharge station,or is exchanged by another recharged battery. For example,the electric energy for vehicle propulsion is not generated on board of the vehicle, but comes from a (immobile) recharge station. In most cases, the operating mode is characterized by deep cycles, starting from a full state-of-charge, and complete recharge (at least from time to time) afterwards.2. Functions and situation of automotive batteryToday’s vehicle electric power systems with the battery as an essential component are characterized by the increasing number and associated power demand of electrical consumers, by packaging issues, and by the limitation of the operational voltage of electronic components.With the old d.c. generators, the SLI battery had to act as a charge buffer element when the ICE was idling due to their low power output at low revolutions. After introduction of ac alternators of increasing power and efficiency, this was not an issue for many years. Nowadays, however, electronic ICE controllers allow reduced idlingrpm to lower emissions, while many comfort components and mechanical devices that are driven electrically require electrical power. Under poor weather conditions in a hot climate, with airconditioning, headlights and wipers on and the electrical cooling fan of the ICE in operation periodically, the alternator cannot supply sufficient current for a modern highly equipped A-size car. While the alternator provides about 70 A, the overall current load fluctuates between 80 and 100 A, and the battery has to provide the difference.When (electrical power assisted) steering is activated, battery discharge peaks reach −60 A. More current (up to 120 A) is generated when idling is over and the ICE rpm increase. But with increasing alternator voltage, the load current increases as well as many loads have a ohmic-like behaviour. For battery recharge, there is not more than +40A left in best case and +20A on average. In this case of load-levelling, charge balance under stop-and-go conditions will be negative, whichmay compromise cranking capability at the long term. Negative charge balance, compromising cranking capability, may have other reasons as well, e.g., extended use of comfort components when the engine is off. In all these cases, an intelligent energy management, which uses information from battery state detection, may switch off non-essential consumers, provide appropriate control to the alternator, or even the idle speed and the automatic gearbox, [2]3. New functions of automotive batteryNew vehicle electric designs are driven by fuel economy and reduced emissions, as well as by new functions for improvement of safety and comfort, reliability, and the availability of the vehicle, i.e., cranking and energy supply to essential functions under all (standard or misuse) conditions. While some of these functions are already established, such as electrically controlled and powered systems for braking, steering and stabilization, others are just being introduced. The stop–start operation mode of the ICE will require even more battery cycling when the electrical system has to be bridged while the ICE is at standstill. The same is true for the torque assist/acceleration assist (boost) mode. Planned generation of electrical energy (onlywhen it is economically meaningful), including electrical brake energy recovery (recuperation), requires knowledge about the capability of the battery to accept charge.4. Battery state detection—foundation of vehicle electrical power managementThe necessary steps to analyze battery status, and to make use of this information, are discussed here in more detail, as the terms used in the field of battery monitoring and energy management are often used in different manner. Especially, there is no unequivocal meaning for the term ‘battery management system’(BMS). In most cases, any feedback to the battery is missing, i.e., the battery is only (passively) monitored and information is generated, rather than it is (actively) Managed. Any analysis of an arbitrary system requires information,i.e., input data. In case of the battery, voltage U, temperature T and current i can be measured directly (observable values). Measurements of a sub-set of such data are ‘battery monitoring’,as battery operation is only (passively) observed These data are input information that are being processed during ‘battery state detection’(BSD). This term comprises analysis of the state vector P of the battery, i.e., values of internal parameters or properties that may not be accessible for direct measurement (non-observable values), but that determine battery state, property, performance and capability.Examples for such internal battery parameters are acid gravity, active material utilization, and any inhomogeneity of these.4.1 Determination of loss of capacit yFollowing the introduction of antimony-free grid alloys, grid corrosion has become a common failure mode that limits battery use in hot environments. In moderate environments,the ohmic part of a value is only then a helpful indication for battery degradation if electrolyte resistance is a relevant failure mode, e.g., with AGM batteries that suffer of dry-out. On the other hand, reduced grid corrosion together with increased cycling duty have resulted in loss of capacity (i.e., charge storage capability measured at the standard low rate) due to active-material degradation beingvery often a prominent failure mode. In many cases, the limiting process of active-material degradation from cycling is softening of the positive active material. This soft material is still in place but is so poorly connected to the grid that discharge is significantly impeded at technically relevant rates. There is, however, some electrical connection of this soft active material to the grid and this is why it is charged to PbO2. This view is supported by the fact that even shed material has been found to be charged PbO2 rather than discharged PbSO4 [5]. If there is no significant sulfation at the negative electrode, then electrolyte is not involved in this type of storage capability loss, i.e., the electrolyte specific gravity would be the original value for a (hypothetical) full recharge. The amount of liquid that can bestored in the tank (its charge storage capability CSC) is represented by the height times the width of this 2-dimensional representation. Change in the height of the liquid level represents the change in actual pressure (i.e., the equilibrium voltage U OO), and the width the amount of liquid (i.e., charge throughput Q) that is drawn from the tank when the height is changed by a certain amount. and is an approximation of the lead–acid battery characteristic . From the considerations given above, the capacity loss due to active-material degradation does not use up electrolyte, i.e., the electrolyte relative density in the fully charged state is the same as that for a fresh battery. If the battery is discharged at a low rate, negligible changes are observed until the available portion of the active material is consumed. This situation is illustrated with a set of ‘stones’on the bottom of the storage tank. The storage capability above these ‘stones’is unchanged, and the existence of the ‘stones’is scarcely obvious before the level of the liquid falls to their level. Then, the pressure in the tank decreases suddenly.4.2 Quantification of acid stratificationAcid stratification is a consequence of the participation of sulfuric acid from the electrolyte in the electrochemical reactions. Convection of the free electrolyte is generated by differences in local concentration, i.e., specific gravity of the electrolyte, and results in electrolyte concentration being higher in the lower part of the cells than in the upper part. Suppression of this electrolyte convection is one of the majorbenefits of electrolyte immobilization in VRLA batteries. To date, acid stratification has received little attention in the case of SLI batteries. Due to the usual rather shallow cycling operation, generation of stratification is limited, and mechanical movement of the battery in the vehicle, as well as some gas evolution during charge at elevated temperature (when the battery is located under the hood), supports equilibration. Cycling operation is more harsh today and generates more stratification, while there is less electrolyte mixing due to the use of battery designs with low-gassing grid and closer plate packaging, and to better vehicle suspension. The reduction in the storage capability of a SLI battery (12 V/110 Ah) when cycled between 80 and 20% SOC at the C20 rate is shown. Already after six cycles, the charged battery (14.7V for 24 h) provides less than 70% of its nominal capacity (Note, when the battery was turned upside down several times and recharged at 16V, stratification was overcome the and capacity was fully recovered). This demonstrates the relevance of acid stratification for battery state detection5. SummaryNowadays, vehicle electric systems are driven by fuel economy, ecology, and by new functions for improvement of safety, comfort, and reliability. Electrically driven components that require electrical power of high reliability are penetrating the mass market, and the emerging start–stop systems will bring new challenges. Overall the requisite electrical performance is increasing with much higher fluctuations of the load demand. This cannot be accommodated simply by scaling up today’s components. All of the above also applies to the battery, especially as packaging of the rather bulky battery within the vehicle is becoming more and more of an issue for designers. Consultation with the battery manufacturer for packaging and possibly partitioning into two batteries may be helpful in many cases. While there is still potential for the further technical improvement of automotive batteries, procedures are needed for optimum use of the battery resource, i.e., knowledge of actual SOC, power capability, and quantification of the degradation of the battery performance as an input for energy management. Early detection of possible restrictions of reliability by battery state detection allows for actions by the energy management system well inadvance. The expertise of the battery manufacturer is challenged by this task.References[1] E. Meissner, G. Richter, J. Power Sources 95 (2001) 13–23.[2] E. Meissner, G. Richter, J. Power Sources 116 (2003) 79–98.[3] J.R. Pierson, R.T. Johnson, J. Power Sources 42 (1993) 237–246.[4] D. Berndt, J. Power Sources 100 (2001) 29–46.[5] D. Berndt, Maintenance-free Batteries, second ed., John Wiley &Sons, New York, 1997.汽车电池工业的挑战:在汽车电力系统中电池已经成为一个越来越集成组件埃伯哈德迈斯纳,高尔夫级瓦尔塔汽车、车辆电气系统和系统开发,邮政信箱210520,30405汉诺威,德国文摘在起初期间,汽车电池被认为只是一个无源元件。
毕业设计论文 外文文献翻译 光伏电力系统 中英文对照
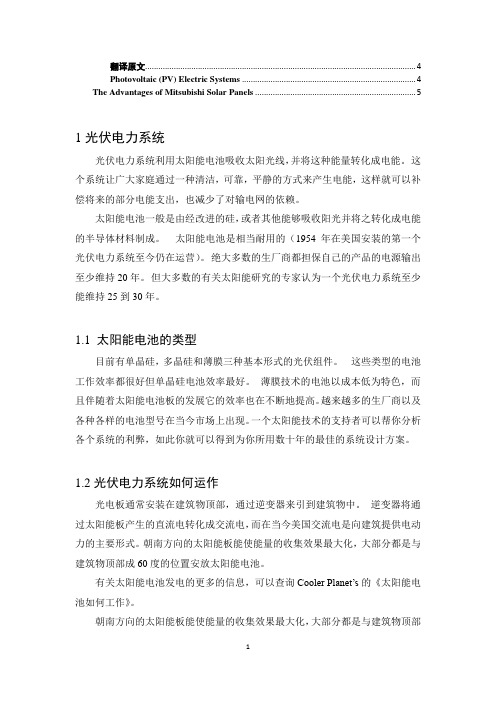
翻译原文 (4)Photovoltaic (PV) Electric Systems (4)The Advantages of Mitsubishi Solar Panels (5)1光伏电力系统光伏电力系统利用太阳能电池吸收太阳光线,并将这种能量转化成电能。
这个系统让广大家庭通过一种清洁,可靠,平静的方式来产生电能,这样就可以补偿将来的部分电能支出,也减少了对输电网的依赖。
太阳能电池一般是由经改进的硅,或者其他能够吸收阳光并将之转化成电能的半导体材料制成。
太阳能电池是相当耐用的(1954年在美国安装的第一个光伏电力系统至今仍在运营)。
绝大多数的生厂商都担保自己的产品的电源输出至少维持20年。
但大多数的有关太阳能研究的专家认为一个光伏电力系统至少能维持25到30年。
1.1 太阳能电池的类型目前有单晶硅,多晶硅和薄膜三种基本形式的光伏组件。
这些类型的电池工作效率都很好但单晶硅电池效率最好。
薄膜技术的电池以成本低为特色,而且伴随着太阳能电池板的发展它的效率也在不断地提高。
越来越多的生厂商以及各种各样的电池型号在当今市场上出现。
一个太阳能技术的支持者可以帮你分析各个系统的利弊,如此你就可以得到为你所用数十年的最佳的系统设计方案。
1.2光伏电力系统如何运作光电板通常安装在建筑物顶部,通过逆变器来引到建筑物中。
逆变器将通过太阳能板产生的直流电转化成交流电,而在当今美国交流电是向建筑提供电动力的主要形式。
朝南方向的太阳能板能使能量的收集效果最大化,大部分都是与建筑物顶部成60度的位置安放太阳能电池。
有关太阳能电池发电的更多的信息,可以查询Cooler Planet’s的《太阳能电池如何工作》。
朝南方向的太阳能板能使能量的收集效果最大化,大部分都是与建筑物顶部成60度的位置安放太阳能电池。
1.3 太阳能电池板与光伏建筑一体化太阳能电池板是用于捕获太阳光的平面板,他们以阵列的形式安装在建筑物顶部或者柱子上。
他们是传统的用于获得太阳能的阵列形式。
机电学院毕业设计外文翻译

景德镇陶瓷学院毕业设计(论文)有关外文翻译院系:机械电子工程学院专业:机械设计制造及其自动化姓名:李东波学号:200610310131指导教师:吕冬青(老师)完成时间:2011年4月20日说明1、将与课题有关的专业外文翻译成中文是毕业设计(论文)中的一个不可缺少的环节。
此环节是培养学生阅读专业外文和检验学生专业外文阅读能力的一个重要环节。
通过此环节进一步提高学生阅读专业外文的能力以及使用外文资料为毕业设计服务,并为今后科研工作打下扎实的基础。
2、要求学生查阅与课题相关的外文文献3篇以上作为课题参考文献,并将其中1篇(不少于3000字)的外文翻译成中文。
中文的排版按后面格式进行填写。
外文内容是否与课题有关由指导教师把关,外文原文附在后面。
3、指导教师应将此外文翻译格式文件电子版拷给所指导的学生,统一按照此排版格式进行填写,完成后打印出来。
4、请将封面、译文与外文原文装订成册。
5、此环节在开题后毕业设计完成前完成。
6、指导教师应从查阅的外文文献与课题紧密相关性、翻译的准确性、是否通顺以及格式是否规范等方面去进行评价。
指导教师评语:签名:年月日计算机辅助夹具设计 - 回顾与未来趋势J.塞西尔虚拟企业工程实验室(VEEL),工业工程处,新墨西哥州立大学,拉斯克鲁塞斯,美国夹具设计是一个重要的工艺设计活动,因为它的自动化对计算机辅助设计和计算机辅助制造(CAM)的一体化是至关重要的。
在本文提供了夹具设计最先进的国家的审查办法。
夹具设计现有目前的缺点方法和研究领域集中在不久的将来的发展也已确定。
关键词:计算机辅助设计,计算机辅助制造;夹具设计1.导言夹具是是用来固定某个工件的位置的机构,利用机械工具来准确的固定工件和在加工过程中支撑着工件。
通常情况下,夹具设计包括压板,定位装置和支撑装置,以及相应的夹具元件来实现各自的职能。
在制造业中,夹具设计的自动化是一个重要的研究领域,必须让设计和制造实现一体化。
夹具的设计是一项复杂的任务,作为一个关键的是设计制造环节,特别是在现代计算机集成制造(CIM)环境[1,2]。
热能与动力工程毕业设计文献翻译

热能与动力工程毕业设计文献翻译文献翻译题目生水源热泵空调系统学生姓名专业班级热能与动力工程08-1 学号院(系)机电工程学院指导教师(职称)完成时间生水源热泵空调系统Yong Cho , Rin YunA K-Water Institute, Korea Water Resources Corporation, 462-1, Jeonmin-dong, Daejeon305-730, Republic of KoreaB Department of Mechanical Eng., Hanbat National Univ., Duckmyung-dong, San 16-1, Daejeon 305-719, Republic of Korea摘要生水源是很有发展前景的新热源之一,研究人员正在将生水源和其他水源(如地面水、湖泊水、河流水和污水)一起作为研究对象。
一般来说,取于环境再供给水质处理设备的水就叫做生水。
在这个课题中,利用供给水质处理设备的生水热能来工作的热泵机组的制冷和制热性能还有待研究。
每两个被测的热泵的热容量为65.2KW,并且通常安置在加热或制冷的控制中心房间。
可以运用焊接的金属板接收来自于生水源的热能。
除了春季,与周围的空气源相比,生水源能够提供良好的热源。
在春秋季节,加热和制冷的负荷极低,因此,生水源热泵系统在这些季节表现不佳。
关键词生水源/热泵/加热和制冷/部分负荷性能1.引言水源有很多种,像地面水,湖泊水,河水,污水和生水。
生水是这些很有发展前景的热源之一。
一般来说,这种水取于环境再通过大型的管道进入水质处理设备来进行后续处理或净化。
像那种没有经过处理的水源就叫做生水。
被调往多个区域供水系统的生水通过各种渠道的运输流动是产生巨大温差的来源。
在这个研究项目中,生水被当作热泵系统的热源来完成水质处理设备整合操作中心的加热和冷却过程。
在实际生活中我们很难找到可以把生水当作热源的相似或相近的操作系统。
- 1、下载文档前请自行甄别文档内容的完整性,平台不提供额外的编辑、内容补充、找答案等附加服务。
- 2、"仅部分预览"的文档,不可在线预览部分如存在完整性等问题,可反馈申请退款(可完整预览的文档不适用该条件!)。
- 3、如文档侵犯您的权益,请联系客服反馈,我们会尽快为您处理(人工客服工作时间:9:00-18:30)。
外文文献翻译
能源与动力学院School of Energy and Power
专业班级:
学生姓名:
学生学号:
指导教师:
年月日
一、目的:
1.了解国外相关知识的发展;
2.熟悉外文科技文献的写作格式及特点;
3.熟悉和巩固所学专业外语的有关知识;
4.学会中英(外)文文献的检索方法。
二、选题要求:
1.学生自主选题,经指导教师审查合格。
2.篇幅在3000汉字以上,较完整的一篇外文论文
3.内容与所学专业相关,并注明来源。
三、译文要求:
1.译文正确,内容完整,图可以复印后贴于适当位置。
2.译文打印在A4纸上,原稿复印后附在译文后。
四、时间安排:
在毕业设计开题3周内完成。
外文文献资料简表。