超高温(UHT)灭菌.
UHT灭菌机操作规程
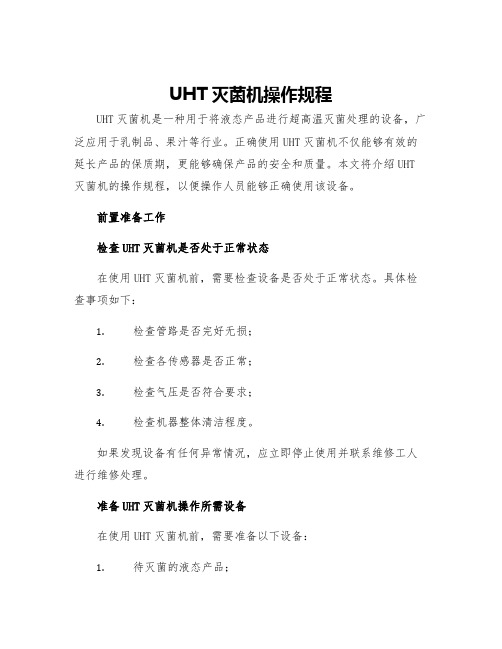
UHT灭菌机操作规程UHT灭菌机是一种用于将液态产品进行超高温灭菌处理的设备,广泛应用于乳制品、果汁等行业。
正确使用UHT灭菌机不仅能够有效的延长产品的保质期,更能够确保产品的安全和质量。
本文将介绍UHT 灭菌机的操作规程,以便操作人员能够正确使用该设备。
前置准备工作检查UHT灭菌机是否处于正常状态在使用UHT灭菌机前,需要检查设备是否处于正常状态。
具体检查事项如下:1.检查管路是否完好无损;2.检查各传感器是否正常;3.检查气压是否符合要求;4.检查机器整体清洁程度。
如果发现设备有任何异常情况,应立即停止使用并联系维修工人进行维修处理。
准备UHT灭菌机操作所需设备在使用UHT灭菌机前,需要准备以下设备:1.待灭菌的液态产品;2.连接UHT灭菌机的管路;3.灭菌后的产品收集管路;4.可用空气瓶(若设备需要空压泵);5.清洗设备的清洗剂或溶液。
UHT灭菌机操作步骤步骤一:开启UHT灭菌机电源将UHT灭菌机的电源开关打开,并等待设备初始化完成。
步骤二:设定UHT灭菌机的操作参数根据待灭菌液态产品的性质确定灭菌的操作参数,包括表面温度、流量、时间等。
步骤三:准备液态产品将待灭菌的液态产品通过管路连接到UHT灭菌机上的进料口,并打开进料阀门,使产品流入设备内部。
步骤四:启动灭菌过程灭菌过程分为两个步骤,预热和灭菌。
在开始灭菌过程前,需要确保产品已经流经预热区域。
当设备进入灭菌阶段时,首先需要启动计时器,并根据设定参数调整温度、流量等参数,确保在一定时间内完成灭菌的过程。
步骤五:结束灭菌过程当计时器到达设定的灭菌时间后,应关闭进料阀门,并将产生的灭菌蒸汽排出设备。
如果需要对产品进行快速冷却,则需要通过建立与冷却器的连接途径来实现对产品温度的快速降低。
步骤六:清洗设备灭菌结束后,需要将UHT灭菌机内部清洗干净,以防止细菌的残留。
首先需要关闭灭菌机的电源,并清除设备内部留下的残渣。
然后使用清洗剂对设备进行彻底清洗,以去除设备中的所有污渍和细菌。
UHT(超高温瞬时灭菌系统)简介
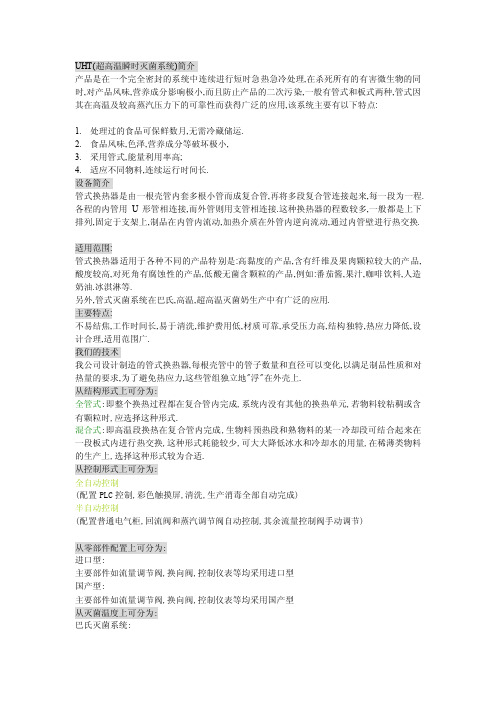
UHT(超高温瞬时灭菌系统)简介产品是在一个完全密封的系统中连续进行短时急热急冷处理,在杀死所有的有害微生物的同时,对产品风味,营养成分影响极小,而且防止产品的二次污染,一般有管式和板式两种,管式因其在高温及较高蒸汽压力下的可靠性而获得广泛的应用,该系统主要有以下特点:1.处理过的食品可保鲜数月,无需冷藏储运.2.食品风味,色泽,营养成分等破坏极小,3.采用管式,能量利用率高;4.适应不同物料,连续运行时间长.设备简介管式换热器是由一根壳管内套多根小管而成复合管,再将多段复合管连接起来,每一段为一程.各程的内管用U形管相连接,而外管则用支管相连接.这种换热器的程数较多,一般都是上下排列,固定于支架上,制品在内管内流动,加热介质在外管内逆向流动,通过内管壁进行热交换.适用范围:管式换热器适用于各种不同的产品特别是:高黏度的产品,含有纤维及果肉颗粒较大的产品,酸度较高,对死角有腐蚀性的产品,低酸无菌含颗粒的产品,例如:番茄酱,果汁,咖啡饮料,人造奶油.冰淇淋等.另外,管式灭菌系统在巴氏,高温,超高温灭菌奶生产中有广泛的应用.主要特点:不易结焦,工作时间长,易于清洗,维护费用低,材质可靠,承受压力高,结构独特,热应力降低,设计合理,适用范围广.我们的技术我公司设计制造的管式换热器,每根壳管中的管子数量和直径可以变化,以满足制品性质和对热量的要求,为了避免热应力,这些管组独立地"浮"在外壳上.从结构形式上可分为:全管式:即整个换热过程都在复合管内完成,系统内没有其他的换热单元,若物料较粘稠或含有颗粒时,应选择这种形式.混合式:即高温段换热在复合管内完成,生物料预热段和熟物料的某一冷却段可结合起来在一段板式内进行热交换,这种形式耗能较少,可大大降低冰水和冷却水的用量,在稀薄类物料的生产上,选择这种形式较为合适.从控制形式上可分为:全自动控制(配置PLC控制,彩色触摸屏,清洗,生产消毒全部自动完成)半自动控制(配置普通电气柜,回流阀和蒸汽调节阀自动控制,其余流量控制阀手动调节)从零部件配置上可分为:进口型:主要部件如流量调节阀,换向阀,控制仪表等均采用进口型国产型:主要部件如流量调节阀,换向阀,控制仪表等均采用国产型从灭菌温度上可分为:巴氏灭菌系统:适用于产品最终灭菌温度为85℃-95℃的工况,高温灭菌系统:适用于产品最终灭菌温度为117℃-125℃的工况.超高温灭菌系统:适用于最终灭菌温度为137℃-140℃的工况系统实际温度控制非常稳定,浮动范围≤1℃管式灭菌系统的基本流程产品从平衡罐泵到管式换热器,产品在该换热器中用过热水间接加热至所需的灭菌温度,在持温管中保留一段时间后迅速冷却,温度传感器检测该产品是否已达到预设的温度,以确保未经彻底灭菌的产品不得进入到灌装机中.为获得最佳的热回收,一个单一的加压热水回路起到了加热和冷却两种作用.全自动控制管式灭菌系统简介简化的操作该系统是为生产含有或不含有纤维颗粒的液体食品而设计的无菌加工系统,可实行自动原位清洗CIP,而不必依靠车间CIP系统的启动.其控制系统安装在一个不锈钢控制箱内,包括自动启动程序所需要的PLC及人机界面等,操作人员只需轻轻一按,清洗,消毒,生产便自动按照预先设置的功能进行.预设程序在设备制造商的许可下可以进行更改.该系统可以随时处理出现的故障,而不会导致不合格的产品混入.更多灵活的选择该系统可以一机两用或多用,如根据温度的变化可生产137℃的UHT奶,120℃高温短时杀菌奶,85℃的巴氏杀菌奶及95℃的酸奶.而其控制只需根据触摸屏上相应的键及文字提示作选择,即可自动完成相关的生产任务.。
牛奶热处理

牛奶热处理
牛奶热处理是指对牛奶进行加热处理,以消灭其中的微生物,延长其保存期限,改善其品质和安全性。
热处理可以分为以下几种方法:
1. 超高温灭菌(Ultra-high Temperature, UHT)处理:将牛奶
加热到 135-150℃,并在高温条件下保持1-3秒钟,然后迅速
冷却。
这种处理可以彻底杀灭牛奶中的细菌和孢子,使其能在未开封的情况下长时间储存。
UHT牛奶一般具有长久保存期限,但在热处理过程中,牛奶中的某些营养成分(如维生素C)可能会被破坏。
2. 巴氏杀菌(Pasteurization):将牛奶加热至63-72℃,并保
持该温度持续15-30分钟,然后迅速冷却。
这种方法主要用于
鲜牛奶,能够有效地杀死其中细菌和酵母,同时保持了一些牛奶的营养成分。
3. 低温灭菌(Low-temperature Sterilization):将牛奶加热到75℃,并保持该温度持续15-20秒钟,然后快速冷却。
这种方
法主要用于奶粉和儿童配方奶粉的生产,以确保其中的营养成分和功能物质的完整性。
牛奶热处理可以有效地杀灭或减少牛奶中的细菌和其他微生物,从而保证牛奶的安全性和品质。
不同的热处理方法适用于不同类型的牛奶产品,消费者可以根据自己的需求选择适合的处理方式。
UHT -高温灭菌

三、热交换方式及热交换
加热水:蒸汽直接喷射入水中。 加热产品:通过热交换器交换热量。 热交换器 1、板式换热器 2、列管式换热器 注:如果两种液体以相反方向流过热交换 器,它们之间的温差能得到最充分得利 用。
四、巴氏杀菌产品:是指可供消费者直接食用的、用牛 奶油和稀奶制成的液态产品。这类产品包括全脂奶、脱 脂奶、标准化奶和各种类型稀奶油。标准化的目的是保 证牛乳含有规定的脂肪含量
巴氏杀菌和UHT相关知识培训
巴氏杀菌
一、巴氏杀菌的目的: 1、杀死引起人类疾病的所有微生物(即杀死所有致病 菌)。如:伤寒菌、大肠菌属、结核杆菌。 2、延长储存时间(当牛乳到达乳品厂后尽快进行热处 理。 巴氏杀菌的强度: 温度和热处理决定 了巴氏杀菌的强度。
10 min 5 min 2 min 1min 10 S 60 65 70 75 80 85 90
酒精实验是一个典型的方法,可以用其拒收所有不适宜于 UHT处理的牛乳,因为: ● 由于牛乳中产酸类细菌数过高,牛乳已酸败。 ● 牛乳盐平衡不正常。 ● 乳含有太多血浆蛋白——典型的初乳。
2、质量不良的原乳会给生产加工条件和最终产品质量带来负 面影响。酸败的牛乳热稳定性极差,会导致加工问题和沉淀, 比如焦糊在加热表面并导致生产时间缩短、清洗困难以及在 贮存中蛋白质沉淀到包装的底部。
3、巴氏杀菌乳的保质期基本上并且一直是由原乳 的质量决定的,当然最佳的技术及卫生等生产条件 是非常重要的,此外还有工厂的正确管理。
在良好的技术和卫生条件下,由高质量原料所生产 的巴氏杀菌乳在未打开包装状态下,5-7℃条件贮存, 保质期一般应该到8-10 天。
4、如果原料乳被微生物所污染,会极大地缩短其保质期, 这些微生物有能产生诸如耐热酶(蛋白酶和解酯酶)的假 单胞菌属,和/或者以芽胞状态存在的、经巴氏杀菌仍存活 的耐热芽胞,经巴氏杀菌仍存活的耐热芽胞,如蜡状芽胞 杆菌(B.cereus)和枯草芽胞杆菌。
uht灭菌工艺

uht灭菌工艺UHT(Ultra - high temperature instantaneous sterilization)是鲜奶处理的一种灭菌工艺,超高温瞬时灭菌,135-150℃,2-8秒,可无需在10℃以下冷藏保存,保质期可达1-6个月。
1、基本简介市场上的利乐砖/枕包装(常说的纸包装)的液体牛奶几乎均采用UHT。
牛奶因其富含营养成分而倍受人们的喜爱。
但也正因此,牛奶易腐败难储存。
为了牛奶饮用新鲜安全,必须对牛奶灭菌并安全包装。
2、包装牛奶中脂肪、蛋白质(氨基酸)和维生素等很容易被氧气氧化而失去营养价值和新鲜口感。
防止氧化变质的有效方法,有两种途径:1.降低流通和保存温度(通常为0-5℃),从而降低氧化速度。
2.采用阻隔性包装材料,隔断氧气进入包装内部的通道UHT奶主要用利乐砖/枕包装,即常说的纸包装UHT奶,又称常温奶、高温奶、超高温瞬时消毒(VTIS:Tetra Therm Aseptic VTIS)奶、超高温热处理奶,其生产工艺是在137~145摄氏度下加热4~15秒。
因为高温处理,牛奶的一些不耐热营养成分如维生素等会遭到破坏,其中的乳糖也会焦化,蛋白质与乳糖还会发生一定的美拉德反应,使牛奶褐变,并破坏牛奶原有的风味。
UHT奶的辨别方法是:利乐砖(枕)包装(常说的纸包装),在超市里成箱卖,无需冷藏,保质期为1-6个月。
UHT技术(常温奶主要加工技术)不会降低牛奶的营养牛奶中富含的营养很多,但最重要有四种,分别是赖氨酸(一种氨基酸)、钙、维生素B2(核黄素)和维生素B12,虽然在超高温灭菌工艺中会有一些成分失去活性,但并没有降低牛奶中的营养。
如:1.牛奶中的蛋白质经UHT技术处理后会产生变性,这属于化学变化,但蛋白质的变性对其营养价值没有影响;2.牛奶中的钙,加热并不会影响人体对它的吸收利用;3.牛奶经超高温消毒后的确会使某些对热敏感的维生素会被破坏,但破坏程度很低。
牛奶中除了维B2和维B12外,其他人类所需的维生素的含量较低,而且大多数维生素的获取途径主要是蔬菜和水果。
UHT超高温瞬时灭菌机简介(1)
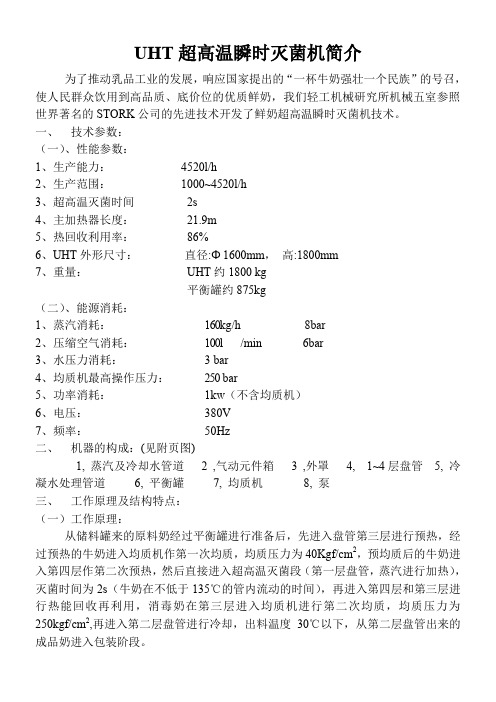
UHT超高温瞬时灭菌机简介为了推动乳品工业的发展,响应国家提出的“一杯牛奶强壮一个民族”的号召,使人民群众饮用到高品质、底价位的优质鲜奶,我们轻工机械研究所机械五室参照世界著名的STORK公司的先进技术开发了鲜奶超高温瞬时灭菌机技术。
一、技术参数:(一)、性能参数:1、生产能力:4520l/h2、生产范围:1000~4520l/h3、超高温灭菌时间2s4、主加热器长度:21.9m5、热回收利用率:86%6、UHT外形尺寸:直径:Φ1600mm,高:1800mm7、重量:UHT约1800 kg平衡罐约875kg(二)、能源消耗:1、蒸汽消耗:160kg/h 8bar2、压缩空气消耗:100l /min 6bar3、水压力消耗: 3 bar4、均质机最高操作压力:250 bar5、功率消耗:1kw(不含均质机)6、电压:380V7、频率:50Hz二、机器的构成:(见附页图)1, 蒸汽及冷却水管道 2 ,气动元件箱 3 ,外罩4, 1~4层盘管5, 冷凝水处理管道6, 平衡罐7, 均质机8, 泵三、工作原理及结构特点:(一)工作原理:从储料罐来的原料奶经过平衡罐进行准备后,先进入盘管第三层进行预热,经过预热的牛奶进入均质机作第一次均质,均质压力为40Kgf/cm2,预均质后的牛奶进入第四层作第二次预热,然后直接进入超高温灭菌段(第一层盘管,蒸汽进行加热),灭菌时间为2s(牛奶在不低于135℃的管内流动的时间),再进入第四层和第三层进行热能回收再利用,消毒奶在第三层进入均质机进行第二次均质,均质压力为250kgf/cm2,再进入第二层盘管进行冷却,出料温度30℃以下,从第二层盘管出来的成品奶进入包装阶段。
(二)设备特点:1、结构紧凑,占地面积小。
2、清洗系统CIP清洗。
(见四)3、连续生产,物料受热时间极短,故可获得优质产品。
4、采用超高温灭菌,灭菌效果特佳。
5、与高压均质机串联使用,应用范围广,比如适宜于高粘度物料灭菌。
超高温灭菌机(UHT)均质机设备操作规程

超高温灭菌机(UHT)均质机设备操作规程1、每班使用前按《预处理UHT、均质机供酸奶及清洗操作规程》对UHT,均质机清洗、消毒。
2、开机:(1)检查软水缸内是否有水,启动软水泵。
(2)均质机旁通阀处于开启状态。
(3)UHT出料阀处于回流循环位置。
(4)向UHT缓冲缸内进软化水,液位超过2/3时,开启UHT进料泵进行水循环。
(5)停止向UHT供应软化水。
(6)均质机启动;a检查电源、电压是否正常。
B检查一级、二级加压阀是否处于卸压状态。
c检查减速箱油位和油压油泵是否正常,系统油压用一级、二级油压表是否“回零”。
D打开冷却水阀门,调整柱塞冷却水量。
e接电源,按下起动器按钮,待运行指示灯亮后,机器进入正常运行状态,关毕均质机的旁通阀。
(7)打开温度控制记录仪,开启蒸汽阀,调整低压阀至合适的松紧度,按工艺要求调整温度及蒸汽压力。
(8)UHT温度调整完毕,均质机加压。
宜兴机:A一级点动,二级加压至10Mpa;B一级加压至18Mpa。
利乐机:A一级点动,二级加压至50bar;B一级加压至220bar。
(9)观察UHT,均质机运转稳定后,转换UHT缓冲缸下三通阀至进料位置,并检查好,开始杀菌,均质。
(10)等循环管排出物料后,及时调整出料口三通阀至出料位置。
(11)根据工艺需要调整冰水阀的大小,使出口奶液符合工艺要求。
3、关机:(1)向UHT小缓冲缸中加入软化水。
(2)转换UHT小缓冲缸下三通阀,用水顶出设备中的奶液。
(3)设备中的奶液压完后,调整UHT出口阀门,放掉压奶水。
(4)卸掉均质机一级压力,卸掉均质机二级压力,卸掉系统油压,停油压泵,停均质机,打开均质机旁通阀,关闭冷却水。
(5)用水对UHT进行冲洗后,停进料泵。
软水泵。
4、注意事项:(1)机器设备运行时,操作人员不得离开岗位,发现异常(如声音异常,压力指示异常等)立即停机待故障排除后重新启动。
(2)均质机停用三天后或经修理后需要必须用手盘车,确认正常后方可启动。
超高温灭菌乳
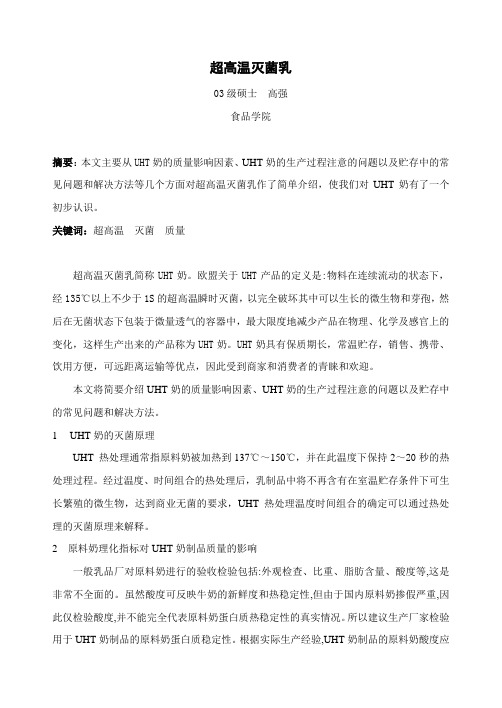
超高温灭菌乳03级硕士高强食品学院摘要:本文主要从UHT奶的质量影响因素、UHT奶的生产过程注意的问题以及贮存中的常见问题和解决方法等几个方面对超高温灭菌乳作了简单介绍,使我们对UHT奶有了一个初步认识。
关键词:超高温灭菌质量超高温灭菌乳简称UHT奶。
欧盟关于UHT产品的定义是:物料在连续流动的状态下,经135℃以上不少于1S的超高温瞬时灭菌,以完全破坏其中可以生长的微生物和芽孢,然后在无菌状态下包装于微量透气的容器中,最大限度地减少产品在物理、化学及感官上的变化,这样生产出来的产品称为UHT奶。
UHT奶具有保质期长,常温贮存,销售、携带、饮用方便,可远距离运输等优点,因此受到商家和消费者的青睐和欢迎。
本文将简要介绍UHT奶的质量影响因素、UHT奶的生产过程注意的问题以及贮存中的常见问题和解决方法。
1UHT奶的灭菌原理UHT 热处理通常指原料奶被加热到137℃~150℃,并在此温度下保持2~20秒的热处理过程。
经过温度、时间组合的热处理后,乳制品中将不再含有在室温贮存条件下可生长繁殖的微生物,达到商业无菌的要求,UHT 热处理温度时间组合的确定可以通过热处理的灭菌原理来解释。
2 原料奶理化指标对UHT奶制品质量的影响一般乳品厂对原料奶进行的验收检验包括:外观检查、比重、脂肪含量、酸度等,这是非常不全面的。
虽然酸度可反映牛奶的新鲜度和热稳定性,但由于国内原料奶掺假严重,因此仅检验酸度,并不能完全代表原料奶蛋白质热稳定性的真实情况。
所以建议生产厂家检验用于UHT奶制品的原料奶蛋白质稳定性。
根据实际生产经验,UHT奶制品的原料奶酸度应控制在17°T以下,而pH值应在6.6~6.8。
3 原料奶的微生物指标对UHT奶制品质量的影响3.1 细菌总数对UHT奶制品质量的影响由于UHT设备对细菌营养细胞的杀灭效率远远高于对芽孢的杀灭效率,因此若原料奶中仅细菌总数高,对UHT设备的杀菌效率影响不大。
但细菌总数高会导致以下情况发生:(1)细菌总数高,其中的致病菌可能产生非常耐热的毒素,这些毒素经超高温处理后仍有少量残留,消费者饮用了这种产品后,会导致中毒。
- 1、下载文档前请自行甄别文档内容的完整性,平台不提供额外的编辑、内容补充、找答案等附加服务。
- 2、"仅部分预览"的文档,不可在线预览部分如存在完整性等问题,可反馈申请退款(可完整预览的文档不适用该条件!)。
- 3、如文档侵犯您的权益,请联系客服反馈,我们会尽快为您处理(人工客服工作时间:9:00-18:30)。
第十五章超高温(UHT)灭菌杀菌是食品加工中极为重要的一道工序,在原始社会里,人类就不知不觉地对食品进行了杀菌处理。
在科学技术飞速发展的今天,人们对食品杀菌意义的认识和应用也得到了不断地完善和提高。
第一节超高温灭菌的基本原理关于超高温(UHT)灭菌,尚没有十分明确的定义。
习惯上,把加热温度为135~150℃,加热时间为2~8s,加热后产品达到商业无菌要求的杀菌过程称为UHT灭菌。
UHT灭菌的理论基础涉及两个方面。
一是微生物热致死的基本原理;二是如何最大限度保持食品的原有风味及品质。
一、UHT灭菌的微生物致死理论依据按照微生物的一般热致死原理,当微生物在高于其耐受温度的热环境中时,必然受到致命的伤害。
加热促使微生物死亡的原因是由于高温导致蛋白质的不可逆变化,随后一些球蛋白变得不溶解,酶失去活力,从而造成新陈代谢能力的丧失,因此,细胞内蛋白质凝固变性的难易程度直接关系到微生物的耐热性,而且这与杀菌条件的选择密切相关。
大量实验证明,微生物的热致死率是加热温度和受热时间的函数。
(—)微生物的耐热性腐败菌是食品杀菌的对象,其耐热性与食品的杀菌条件有直接关系。
影响微生物耐热性的因素有如下几方面:(1)菌种和菌株(2)热处理前菌龄、培育条件、贮存环境(3)热处理时介质或食品成分,如酸度或PH值(4)原始活菌数(5)热处理温度和时间,作为热杀菌,这是主导的操作因素。
(二)微生物的致死速率与D值在一定的环境条件和一定温度下,微生物随时间而死亡时的活菌残存数是按指数递减或按对数周期下降的。
这一规律为通常大量的试验结果所证实。
若以纵坐标表示单位物料内随时间而残存的活细胞或芽孢数的对数值,横坐标表示热处理时间,则可获得如图15-1所示的微生物致死速率曲线。
图15-1 微生物致死速率曲线如图所示,设A为加热开始时活菌数所代表的点,B为加热后菌数下降1个对数周期时的点,其相应的加热时间为3.5min,C为加热后菌数下降2个对数周期时的点,其相应的加热时间为7.0min。
显然,细菌任意时刻的致死速率可以用它残存活菌数下降1个对数周期所需的时间来表示,这便是图中所示D 值的概念。
D 值是这一直线斜率绝对值的倒数,即∣斜率∣=CC C B ''=D D 110log 10log 23=- D 值反映了细菌死亡的快慢。
D 值愈大,细菌死亡速度愈慢,即细菌的耐热性愈强,反之则死亡速度愈快,耐热性愈弱。
由于致死速率曲线是在一定的加热温度下做出的,所以D 值是温度T 的函数(常写成D T ),上述比较只能以同一加热温度为前提,例如以D 110℃来作比较。
必须指出,D 值不受原始菌数的影响,换言之,原始菌数不影响其个别细菌按指数死亡的规律。
因此,如果将不同原始菌数的曲线画在同一的图15-1上,便得到一组平行的直线族。
另外,D 值要随其他各种影响微生物耐热性的因素而异,只能在这些因素固定不变的条件下才能稳定不变。
(三)微生物的热力致死时间与Z 值微生物的热力致死时间(Thermal Death Time )就是在热力致死温度保持不变条件下,完全杀灭某菌种的细胞或芽孢所必需的最短热处理时间。
微生物热力致死时间随致死温度而异,两者的关系曲线称为热力致死时间曲线,如图15-2,它表达了不同热力致死温度下细菌芽孢的相对耐热性。
图15-2 热力致死时间曲线如同对致死速率曲线的处理一样,若以横坐标为热处理温度,纵坐标为热致死时间(TDT )的对数值,就可以在对数坐标图上得到一条形为直线的热力致死时间曲线。
同样,如图 15-2 所示,此直线斜率绝对值的倒数Z 值表明了热致死时间缩短一个对数周期所要求的热处理温度升高的度数。
图15-2中,设A ,A ′为热致死时间相差1个对数周期的两个点,其相应的热致死时间的对数值分别为logTDT A =log102,logTDT A/=log101相应的热力致死温度分别为T A ,T A ′,则∣斜率∣=Z Z Z TDT TDT A A 110log 10log log log 12=-=-' 某微生物菌种的杀菌特性曲线——热力致死时间曲线可由点、斜率两个参数来确定。
因此除了由斜率决定的Z 值外,尚需寻求一个标准点。
这个标准点通常选用121℃时的TDT 值,并用符号“F ”表之,单位为min ,称为F 值。
有了Z 、F 两个参数,该菌种在任何杀菌温度T 下的TDT 值可表为 ()T ZF TDT -=1211log (15-1) 必须强调指出,热力致死时间(TDT )这个概念的提出隐去了细菌死亡按指数规律的实质,也避开具体运用概率说明细菌死亡的方法,而是模糊地以实际试管试验法所确定的所谓“完全灭菌”为依据。
因此采用TDT法不能清楚地说明诸如杀菌终点、原始菌数不同时出现的耐热性差异及TDT试管试验法中常见越级现象等实际问题。
根据式(15-1)可知,决定细菌耐热特性的是F和Z两个参数。
对于不同菌种,一般两者都不相同;对于同一菌种,也只能在其一数值相等的条件下,由另一条来比较它们的耐热性。
故F值只能用于Z值相同时细菌耐热性的比较。
Z值相同时,F值大的细菌的耐热性比F值小的强。
同样,F 值相同时,Z值大的细菌的耐热性比Z值小的强。
为了比较,也可人为的规定Z的标准值,一般取Z=10℃。
(四)UHT杀菌的品质保证大量实验表明,采用UHT瞬时杀菌技术也可最大程度地保持食品的风味及品质。
这主要是因为微生物对高温的敏感程度远远大于食品成分的物理化学变化对高温的敏感程度。
例如,在乳品工业生产灭菌乳的过程中,如果牛乳在高温下保持较长时间,则可能产生一些化学反应。
例如蛋白质和乳糖发生美拉德反应,使乳的颜色变褐;蛋白质发生分解反应,产生不良气味;糖类焦糖化产生异味等。
此外还可能发生某些蛋白质变性而产生沉淀。
这些都是生产灭菌乳所不允许的,应力求避免。
图15-3表示牛乳灭菌和发生褐变时的温-时曲线。
图15-3 牛乳灭菌及褐变的时间-温度曲线1-变褐的最低时间-温度条件 2-灭菌的最低时间-温度曲线图中实线为牛乳褐变的温-时下限,虚线为灭菌的温-时下限。
从图中可以看出,若选择灭菌条件为110-120℃,15-20min,则两线之间间距甚近,说明生产工艺条件要有十分严格的措施来维持,这在实际上很难办到。
而选择UHT灭菌条件137-145℃,2-5s时,两线之间间距较远,说明产生褐变及其他缺陷的危险性较小,生产工艺条件较易控制。
在这种杀菌条件下,产品的颜色、风味、质构及营养没有受到很大的损害。
所以,该技术比常规杀菌方法能更好地保存食品的品质及风味。
二、超高温灭菌时间和温度意义从杀死微生物的观点来看,热处理强度是越强越好,时间是越长越好。
但是,强烈的热处理对食品的外观、风味和营养价值会产生不良后果。
如牛乳中蛋白质在高温下变性;强烈的加热使牛乳风味改变,首先是出现“蒸煮味”,然后是焦味。
因此,时间和温度组合的选择必须考虑到微生物和产品质量两方面,以达到最佳效果。
食品加工中灭菌的目的并不是使每单个包装的产品都不含残留的微生物,因为采用加热方法来致死微生物,要达到绝对无菌的理想状态是不可能的。
实际上,灭菌加工只要保证产品在消费者食用前不变质就行。
一个基本的要求就是致病菌的存活和生长的可能性必须小到可以忽略的程度。
肉毒梭状芽孢杆菌通常被认为是对公共健康危害最大的微生物,大多数保持灭菌就是基于它的致死率而设计的。
在灭菌乳制品中,肉毒梭状芽孢杆菌存活繁殖及生长而产生能危害公共健康的毒素量的概率是很低的,实际上这种情况从未发生过。
热处理系统的设计可以完全排除由其他残留致病菌所能导致的对公共健康的危害性。
导致产品变质的微生物包括加工过程中残留的耐热微生物或灭菌后再污染的微生物,再污染的微生物包括热敏性和耐热性微生物(如芽孢)。
污染的芽孢一般来说比加工过程中残留的耐热性差。
为了衡量超高温工艺效果,现引入杀菌效率(SE)一词。
杀菌效率是以杀菌前后孢子数的对数比来表示的:SE=LG[原始孢子数/最终孢子数]把已知数量的枯草杆菌的孢子移植到原乳中,然后用超高温设备处理,实验结果如下:杀菌温度不同、时间相同(4S)时,其杀菌效率接近,见表15-1表15-1杀菌温度不同、时间相同(4s)的杀菌效率超高温灭菌处理牛乳必然使一部分微生物残存,也就是说绝对无菌是不能保证的。
在这种情况下,人们认识到加工原料中含有能存活于灭菌过程后的微生物数目的重要性,并且微生物的残存与加工产品的量和包装容积有关。
假设我们要加工大量产品,如加工10000L的产品,其中含耐热芽孢100cfu/ ml,若灭菌效率SE 为8,则整批产品中的残留芽孢数为:10000 ×1000 ×100/108=10(个)只要产品是从整体形式存在,那么这种计算是成立的。
然而若将产品分装于1L容器中,并进行相同的热处理,那么每个容器中处理前含有1000×100=105个芽孢,灭菌后,每个容器中含105/108=10-3(1/1000)个芽孢。
那么每个容器中含有1/1000个芽孢的实际意义就是每1000个容器中必然含有1个芽孢。
一般灭菌乳成品的商业标准为:不得超过1/1000孢子数。
这一点在产品以整体形式才采取相同的灭菌效率加工时同样可以加以证实。
例如通过超高温加工,整批产品中将有10个芽孢残存。
如将产品在理想的无菌灌装状态下分装与10000个1L容器中。
这10个芽孢将被分散到10000个容器中去。
理论上,一个以上的芽孢有可能进入同一个容器中,然而当残留芽孢数与容器数相比很小时,从统计学上讲,一个容器中含有1个以上芽孢的可能性可忽略不计。
因此我们可以假设10个芽孢代表着10个含有单个芽孢的容器,或者说10000个容器中含有10个芽孢。
我们假设残存的每个芽孢在条件适宜时足以使产品变质,因此每个容器内含1/1000个芽孢就等于1000个容器中含一个芽孢,因而就会导致1000个产品中有1个变质,或者说是有0.1/100的产品变质。
这一计算不论对于罐内保持灭菌还是超高温灭菌结合无菌灌装都是同样有效的。
第二节超高温灭菌在乳制品中的应用一.UHT乳的加工原理超高温灭菌法(UHT)是英国于1956年首创,在1957~1965年间,通过大量的基础理论研究和细菌学研究后,才用于生产超高温灭菌乳,关于超高温灭菌乳在灭菌过程中对于微生物学和物理化学方面的变化及基本加工原理等,1965年英国的Burton提出了详细的研究报告,其基本点是细菌的热致死率随着温度的升高大大超过此间牛乳化学变化的速率,例如维生素的破坏,蛋白质变性及褐变速率等。
研究认为在温度有效范围内,热处理温度每升高10℃,乳中所含幼稚菌孢子的破坏速率提高11~30倍,即:Q t+10/Q t=10~30而根据Vant .Hoff规则,温度每升高10℃,反应速率约增大2~4倍。