七大浪费识别表ZSZB0164
七大浪费识别

制程能力不足,生产方式及管理方式不当
过量浪费
定义
1.生产多于下游客户所需 2.生产快于下游客户所需
改善原则: ✓ 不预测生产 ✓ 不过量生产 ✓ 不过早生产
➢ 现象:
① 生产过多:制造比订单更多的数量 ② 生产过早:交货期未到,提早生产等待交货
➢ 影响:
1. 提早吃掉了材料费及人工费 2. 把等待的浪费隐藏起来了 3. 工程间积压了在制品、产生搬运、堆积等 4. 形成呆滞品、废品库存的机会
表现:
• 步行到复印机、办公用品集中供应地、传真机所在地和办公室其他地方 • 查找文件、档案 • 报销跑来跑去
人才浪费
定义
由于未使员工参与、未倾听员工意见而造成未能善用员工 的时间、构想、技能,使员工失去改善与学习的机会
➢ 现象: • 不让员工参与改进 • 不听取员工的想法 • 不采纳员工的建议 ➢ 影响: • 人员的工作不是100%增值 • 未充分利用员工的聪明才智 • 员工对改进漠不关心 • 限制员工成长的机会
➢ 原因:
制程能力不足,生产方式及管理方式不当
动作浪费
定义
任何不增加产品或服务价值的人员和设备的动作 (检查、存储、搬运)
改善原则: ✓ 不插秧 ✓ 不摇头 ✓ 不弯腰
➢ 现象:
1. 寻找工具材料 2. 过度/过多的伸展/弯腰动作 3. 机器/材料距离过远(步行时间) 4. 零件在设备间传送带上的来回传送 5. 机器空转
➢ 影响:
人员耗费体力,生产周期增长
➢ 原因:
标准作业与非标准作业未分离,物料摆放位置不佳, 工作桌设计不佳
丰田屋(精益屋)
通过杜绝浪费以缩短生产流程,实现下列目标: 高效率、高品质、低成本、短交期、高安全、高士气
(精益改善)生产现场7大浪费点检表
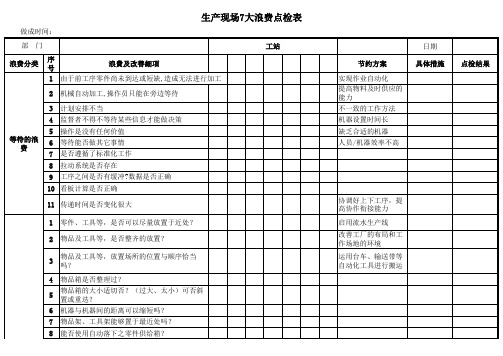
减少物料、零部件、 在制品及产成品的堆 积
根据生产目标和任务 合理安排生产
点检结果
6 次品率是多少
7 是否有引起次品的共同原因
8 库存里是否隐藏了次品
9 机器,工具,技术是否有问题
10 标准化工作是否被遵守
11 次品是由准确的依据还是凭感觉来决定
1 动作不能删除吗?
2 能够缩短移动距离吗?
3 可否以双手或手脚同时动作?
4
以双手动作是相反方向或是相对方向来进行 呢?
5
由腕到手方案
实现作业自动化 提高物料及时供应的 能力 不一致的工作方法 机器设置时间长 缺乏合适的机器 人员/机器效率不高
具体措施
点检结果
协调好上下工序,提 高协作衔接能力
启用流水生产线
改善工厂的布局和工 作场地的环境
运用台车、输送带等 自动化工具进行搬运
生产现场7大浪费点检表
做成时间:
部门
浪费分类
生产现场7大浪费点检表
做成时间:
部门
浪费分类
序 号
浪費及改善細項
1 由于前工序零件尚未到达或短缺,造成无法进行加工
工站
2 机械自动加工,操作员只能在旁边等待
等待的浪 费
3 计划安排不当 4 监督者不得不等待某些信息才能做决策 5 操作是没有任何价值 6 等待能否做其它事情 7 是否遵循了标准化工作 8 拉动系统是否存在 9 工序之间是否有缓冲?数据是否正确 10 看板计算是否正确
2 检查基准明确否?
3 此工序或零件的基本功能是什么? 4 工序设计是否不合理 5 机器或工序的产能是否合适 6 零件的规格是否合要求
节约方案
日期 具体措施
点检结果
人员/机器效率不高 人机工程方面的设计 不好 不一致的工作方法
生产管理7大浪费
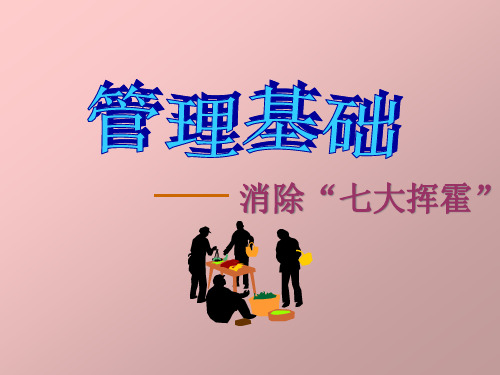
对策:
•库存意识旳改革 •U型设备配置 •均衡化生产 •生产流程调整顺畅 •看板管理旳落实 •迅速换线换模 •生产计划安排考虑库存 消化
注意:
•库存是万恶之源 •管理点数削减降低安全库存 •消除生产风险降低安全库存
6.动作旳挥霍
额外动作旳挥霍
不必要旳动作、无附加价值旳动作,及较慢旳动作
体现形式:
•工作时旳换手作业 •未倒角之产品造成不易装配旳挥霍 •小零件组合时,握持压住旳挥霍 •动作顺序不当造成动作反复旳挥霍 •寻找旳挥霍
•不良品存在库房内待修 •设备能力不足所造成旳安全库存 •换线时间太长造成次大批量生产旳挥霍 •采购过多旳物料变库存
库存是万恶旳根源
5.库存旳挥霍
过多旳库存会造成旳挥霍:
•产生不必要旳搬运、堆积、放置、找寻、防 护处理等挥霍旳动作 •使先进先出旳作业困难 •损败北息及管理费用 •物品之价值会减低,变成呆滞品 •占用厂房、造成多出旳工作场合、仓库建设 投资旳挥霍 •造成无形旳挥霍
无法确保可卖出旳产品做了太多
体现形式:
是挥霍旳源头
•物流阻塞 •库存、在制品增长 •产品积压造成不良发生 •资金回转率低 •材料、零件过早取得 •影响计划弹性及生产系统旳适应能力
适
时
J旳
I T
生
生 产
产
方
式
1.制造过多旳挥霍
制造过多是一种挥霍旳原因:
•只是提前用掉了费用(材料费、人工费)而已,并
无其他好处
对策:
•采用均衡化生产 •制品别配置—一种流生产 •防误措施 •自动化及设备保养加强 •实施目视管理 •加强进料控制
注意:
•自动化不要闲置人员 •供需及时化 •作管理点数削减
精益理念及识别七大浪费ppt课件

1.资金占用 8.重要的是掩盖了 现场的问题
7.占用其他产 品的材料、零 件 6.能源的浪费
5.废品及降价损失
2.搬运的浪 费。 3.占用场地
4.库存及管理费用
动作的浪费:任何人体或物体的动作,若没有直接产生附加 价值,或产生的附加价值与付出的劳动不成比例,这样的动 作就是浪费的动作。
识别七大浪费
自然界的规律带给我们的启发------
怎样做才能战胜竞争对手? 怎样才能提高自己的竞争力? 怎样才能获取更高的利润? 如何提高生产效率? 如何降低生产制造成本? 还有更多------
Lean Production
自働化 ------
丰田英二
JUST IN TIME
------
原则5. 取出、放回要方便
改善前 拿起放在作业台上的钳子 需要转换手势
改善后 把钳子放在漏斗型器具内使用
悬
插
挂
筒
支
架
插筒
□ 动作分析的原则
原则 6. 利用无成本的动力或重力
改善前
改善后
作业完了后,伸手放到距离 60㎝的部品箱里
作业台
部品盒
在作业台上穿个小孔,作业物品经 传送板滚到部品箱里
作业台
滑槽 部品盒
改善后
·作业台大
·作业台小化(2/3)
·与部品的距离远
·与部品的距离近
·水平方向放置部品,很难取 ·倾斜放置部品,容易取出
出
作业
部品
作业 台
部品 存放
台
作业
部品
作业台 (缩小2/3)
部品存 放台
(倾斜 )
□ 动作分析的原则
原则9. 器具/工具统合
管理工作七大浪费ppt课件

2019/5/29
38
方法不当也是低效率的原因之一
人 员安排不得当,会导致低效率; 计 划安排不合理,工作难以按期完成; 顺 序安排有问题,会造成主次不分,重点工作无人做。
2019/5/29
39
固步自封的僵化思想是 低效率的温床
过去的成功经验、过去行之有效的方法,会使某
些“成功”人士沾沾自喜,沉湎于过去的辉煌之中, 从而不思进取,不继续提高自己,使用原有的一套来 面对千变万化的内部和外部环境,不仅导致了低效率, 甚至会拖累整个组织的前进脚步,成为整个组织前进 的绊脚石。
2019/5/29
10
领导指示的贯彻协调不力
对公司领导的工作指示和部长会议及相关会议布 置的工作没有传达,内部没有有效的协调组织落实, 致使公司的要求在部门停滞,没有得到有效地贯彻, 形成工作盲区。
2019/5/29
11
信息传递的协调不力
•
信息在相关部门、相关人员手中停滞,使应该得
到的这些信息的相关部门掌握不到,难以有效地开展
2019/5/29
17
工作程序复杂化形成的闲置
在某些情况下,对于某些不十分重要的任务,上
级其实只承担签字的职能,但如果无上级的签字或认 可,业务就无法进行,会出现等待和停滞等浪费。原 来比较简单的事,一些部门非要写个报告,填个报表。 由于报表内容太多,即使保存后再想使用也找不到, 那么就再提供一份吧。一个有效的管理者在某种程度 上是一个规范化的高手,把复杂工作标准化,规范化、 简单化,从而使普通人可以承担原来完成不了的工作, 起到较大的作用。
2019/5/29
26
在这种无序状态中,如何通过有效的方法 ,使 无序变为相对有序,从而整合资源,发挥出最大效 率,这是中高层管理者应该注意和重点考虑的问题 之一。
精益生产之七大浪费简介1.doc
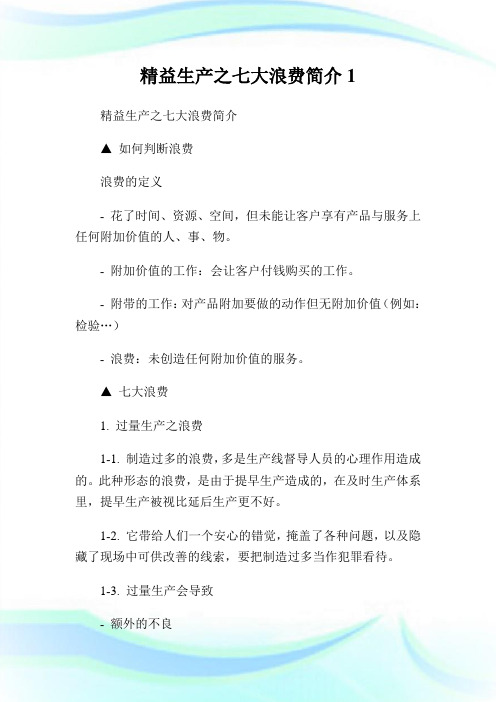
精益生产之七大浪费简介1精益生产之七大浪费简介▲如何判断浪费浪费的定义- 花了时间、资源、空间,但未能让客户享有产品与服务上任何附加价值的人、事、物。
- 附加价值的工作:会让客户付钱购买的工作。
- 附带的工作:对产品附加要做的动作但无附加价值(例如:检验…)- 浪费:未创造任何附加价值的服务。
▲七大浪费1. 过量生产之浪费1-1. 制造过多的浪费,多是生产线督导人员的心理作用造成的。
此种形态的浪费,是由于提早生产造成的,在及时生产体系里,提早生产被视比延后生产更不好。
1-2. 它带给人们一个安心的错觉,掩盖了各种问题,以及隐藏了现场中可供改善的线索,要把制造过多当作犯罪看待。
1-3. 过量生产会导致- 额外的不良- 额外的操作- 额外的空间- 过度使用机器- 额外的人员- 产生搬运和堆积。
1-4. 制造过多是下列观念及政策造成的- 让作业员有生产伸缩的充分空间- 让每一制程或生产线有提升自己的生产力的利益- 因为有不良品而想提升直通率- 因为有多余的产能,所以容许机台生产多于所需之量- 为了提升稼动率,生产过多的产品1-5. 改善对策:- 生产排程- 生产平衡- 品质稳定2. 等待之浪费2-1. 等待指在制造过程中人员、物料、机器处于闲置状态,等着下一个流程或动作。
2-2. 作业员的双手停滞不动时,就是等待浪费发生的时候。
生产线不平衡、缺料、机器故障,使得作业员停滞,或者机器在进行附加价值的加工时,而作业员在旁监视,这些都是等待之浪费。
2-3. 出现等待的原因- 加工流程不顺- 机器故障率高- 人员安排不合理- 原物料/前段物料供应不足- 流程安排不合理- 转换型体2-4. 改善对策:- 生产线平衡- 派工的规划3. 无效率的制程之浪费3-1. 无效率的制程指在规定的时间、人力、资源等情况下无法达成所设定的目标。
3-2. 一般无效率制程分为两种情形:- 品质要求过高,造成损耗大量成本- 没有达到标准目标(如人均时产能)3-3. 无效率制程所造成的浪费- 多余的作业时间- 机器过度损耗- 浪费电力、气压、油等能源3-4. 改善对策:- 工厂布置分析- 布置效率- 删除、合并、简化、重组现有流程- 制程设计4. 库存之浪费4-1. 库存即原物料、半成品(线上在制品)、成品储存在固定区域或仓库。
识别消除生产中的七大浪费(经典)
等待的浪费
生产过程中设备、人员等资源的闲置和等待,导致 效率低下和成本增加。
搬运的浪费
不必要或不合理的物料、半成品、成品在生产过程 中的搬运,增加了运输成本和时间。
浪费的分类
01
02
03
04
加工的浪费
过度或不必要的加工,导致资 源浪费和产品成本的增加。
库存的浪费
过多的库存导致资金占用、管 理成本增加,同时还可能引发 品质问题。
缺陷和重修
定义
缺陷和重修是指产品不符合质量标准或 客户要求,需要进行返工或报废。
影响
降低客户满意度、增加成本、影响企 业声誉。
原因
质量控制不严格、产品设计缺陷、生 产过程中的问题。
解决方法
加强质量管理体系建设,实施严格的 质量检测和把关,提高产品设计质量 和生产过程的稳定性。
未充分利用员工才能
定义
03
02
原因
设备故障、生产不平衡、计划安排 不当。
解决方法
加强设备维护保养,实施均衡化生 产,优化计划调度。
04
过程浪费
定义
原因
过程浪费是指在生产过程中出现的各种不 合理的操作和动作。
操作不当、工艺流程不合理、缺乏标准化 作业。
影响
增加成本、降低效率、影响产品质量。
解决方法
制定标准化作业指导书,优化工艺流程, 加强员工培训和操作规范。
某服务企业在服务过程中存在一些浪费现象,如服务流程繁琐、人力资源浪费、客户沟通不畅等。为 了消除这些浪费,该企业采取了相应的措施,如优化服务流程、引入智能客服、加强员工培训等。
通过这些措施,该企业提高了服务质量和效率,减少了浪费,增加了客户满意度,最终实现了业务增 长。
生产现场七大浪费(PPT59页).pptx
成本+%(利润)=价格
or
价格-成本=利润
4
认识浪费
传统浪费的概念:
材料,报废,退货, 废弃物
不增加价值的行 为
浪费就是指客户 不愿意为你付钱 的那些过程。
真正的价值是你 不能命令或控制 的东西,它只存 在于顾客心里。
5
认识浪费
没有功劳有苦劳
这个时代已成往事
6
认识浪费
某权威机构对企业增值与非增值活动的统 计:
18
七大浪费之二:搬运的浪费
材料放置不当 生产计划不均衡 设施布局不当 过多重复检验 工作场地有序安排不当 工序不均衡 供应链管理
19
七大浪费之二:搬运的浪费
减少搬运浪费的原则: 最短搬运距离原则:减少搬运距离 最小劳动强度原则:考虑人机工程合理性 岗位标准包装原则:适合人搬运的最佳包装 先进先出原则: 存放方式适合员工取用 分装业务外部转移原则:生产线上尽量不分装 拆包外移管理原则:物料由物流部门拆包
动作的浪费“三不”原则
本 作 业
工作 生理
辅结 地
需要
助 束场 材上 工
作 业
作 业
所 清
料厕 准所
间 休
扫备
息
不运转
非作业 时间
帮联 助系 别其 人他
非工人造成的 损失时间
设作材模停 备业料具 修等等等电 理待待待
工人造成的 损失时间
闲离其 聊岗他
15
七大浪费
七大浪费之一:等待的浪费 七大浪费之二:搬运的浪费 七大浪费之三:不良品的浪费 七大浪费之四:动作的浪费 七大浪费之五:加工的浪费 七大浪费之六:制造过多(早)的浪费 七大浪费之七:库存的浪费
11
七大浪费之一:等待的浪费
七大浪费识别与原因分析、改善对策总结
七大浪费识别与原因分析、改善对策总结浪费的定义:一切不创造价值的活动,换言之:不能够提高附加价值的部分。
1、最大的浪费:生产过剩的浪费生产过剩的表现形式“过量生产MUDA”会产生新的MUDA(二次的MUDA)①材料、部品被提前吞吃;②电、空气等能源的浪費;③货架与箱子的增加;④搬运者、运输的增加;⑤会把等待的浪费隐藏起来,掩盖稼动率不足的问题;⑥使先进先出的工作产生困难;⑦会造成库存空间的浪费;⑧ LEAD-TIME变长(在库增加)。
到销售为止的时间变长(转换为钱的速度减慢即现金流减缓)生产过剩的发生原因过量生产的MUDA是所有MUDA产生的原因:①对于机械故障、不良等的安心保证;②错误的稼动率向上、外观的能率向上;③生产线停线是罪恶的想法;④作业员太多(没有按照TACT-TIME进行生产);⑤业务订单预测有误;⑥生产计划与统计错误。
解决对策①顾客为中心的弹性生产系统;②单件流生产线;③看板管理的贯彻;④快速换线换模;⑤少人化的作业方式;⑥均衡化生产。
注意点①设备余力并非一定是埋没成本;②生产能力过剩时,应尽量先考虑减少作业人员,但并非辞退人员,而是更合理、更有效率地应用人员。
2、最恶的浪费:库存的浪费库存浪费的表现形式①不良品存在库房内待修;②设备能力不足所造成的安全库存;③换线时间太长造成每次大批量生产的浪费;④采购过多的物料变成库存。
造成二次浪费:①产生不必要的搬运、堆积、放置、找寻、防护处理等浪费的动作;②使先进先出的作业困难;③损失利息及管理费用;④物品之使用价值会减低,变成呆滞品;⑤占用厂房、造成多余的工作场所、仓库建设投资的浪费;⑥造成无形的浪费。
隐藏的问题点①没有管理的紧张感;②设备能力及人员需求误判;③对场地需求的误判;④产品品质变差的可能性;⑤容易出现呆滞物料。
库存浪费的发生原因①视库存为当然;②设备配置不当或设备能力差;③大批量生产,重视稼动时间;④物流混乱,呆滞物品未及时处理;⑤提早生产;⑥无计划生产;⑦客户需求信息未了解清楚。
公司内部存在的七种浪费
1.七种浪费之一:等待的浪费
等待就是闲着没事,等着下一个动作的来临,这种浪费是无庸置疑的。 造成等待的原因通常有:作业不平衡、安排作业不当、停工待料、品质 不良等。
另有一种就是“监视机器”的浪费,为了使自动设备能正常运转,例如: 排除小故障、补充材料等等,通常还会另外安排人员站在旁边监视。所 以,虽然是自动设备,但仍需人员在旁照顾,特称之为“闲视”的浪费。 当制造部在生产新产品发生一些问题时,生产技术部和品管部是否能立 即解决而不需要现场人员长时间等待? 如何减少这种等待需要大家加以反思。 反思在KTC中是否存在的等待浪费现象?
2.七种浪费之二:搬运的一旁的搬运过程 如:搬运的距离很远; 小批量的运输; 出入库次过多等。
搬运的浪费若分解开来,又包含放置、堆积、移动、整理 等动作的浪费
有些人想到用输送带的方式来克服,这种方式仅能称之为 花大钱减少体力的消耗,但搬运本身的浪费并没有消除, 反而被隐藏了起来。
何谓浪费
何谓浪费:
不产生任何附加价值的
动作、方法、行为和计划
用不同的评判标准去判断 一个动作、行为、方法或计划时, 所得到的浪费程度都会不同。
现场活动包括“有附加价值的”和“没有附加价值的”活动,那些不产生附加价 值的活动应坚决予以消除
生产现场中的七种浪费概述 精益生产方式中所指出的浪费,和大家日常生活中所提到的浪费有着截 然不同的含义,即:在工业生产中,凡是不能直接创造价值的一切活动, 均视为浪费。 精益生产方式将所有浪费归纳成七种: ■等待的浪费; ■搬运的浪费; ■不良品的浪费; ■动作的浪费; ■加工的浪费; ■库存的浪费; ■制造过多(早)的浪费。
6.七种浪费之六:库存的浪费(5) Ⅵ.设备能力及人员需求的误判: 由于库存量的存在,设备能力不平衡时也看不出(库存越多,越不容易看 出来)。人员是否过剩,也无法了解。由于有较多的库存,供应部门需要 增加人员,制造一线需要更多的人员来生产产品用于补充库存,需要增添 设备来保证生产库存所需要的设备能力,从而形成新一轮的浪费。 到底为什么要有库存量,最大的理由是“怕出问题”——出现故障怎么办? 会不会因部分设备出问题,而影响整条生产线或工厂的生产呢? 于是乎为了不使影响扩大,库存便成了必要,众多的问题也被隐藏起来, 所有进步、赚钱(发现问题、解决问题就是赚钱)的步调自然变慢了。无 怪乎精益生产方式称库存为万恶之源,绝对不允许它存在,如果现在已经 有了库存,也要行进一切办法,将之降低,力争零库存。 (注:零库存的“零”并非指数学意义上的“完全没有”的意思,而是指 把库存“尽量减到最少的必要程度”。)