A注射液灭菌工艺验证方案
灭菌注射用水生产工艺验证方案
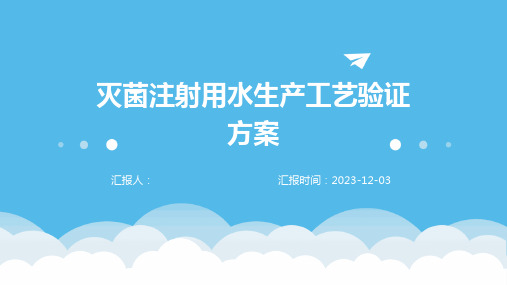
质量检测
加强产品质量检测,完善检测手段 和方法,确保产品质量符合要求。
工艺改进
根据实际情况对生产工艺进行改进 和优化,提高生产效率和产品质量 。
07
附件:相关文件与记录
工艺流程图
总结词
描述工艺流程
详细描述
附图1展示了灭菌注射用水的生产工艺流程图,包括各个关键步骤和环节,如原 料水、砂滤、活性炭过滤、超滤、紫外线消毒、终端过滤等。
针对每个关键质量特性,确定需 要验证的参数和指标。
验证方法设计
根据关键控制点和关键质量特性 ,设计适当的验证方法,包括取 样方法、检测方法、试验条件等
。
确保验证方法具有可操作性和可 重复性,同时考虑方法的灵敏度
和特异性。
参考国内外相关法规和标准,确 保验证方法的合规性和标准化。
验证标准制定
确保验证标准具有可操作性和可衡量性,同时考虑标 准的合理性和科学性。
02
数据整理要求
根据数据记录表格,在生产过程中及时、准确地收集相关数据,确保 数据的真实性和完整性。
对收集到的数据进行整理,确保数据清晰、易于分析。对于异常数据 ,进行核实并排除误差和错误。
数据分析与评估
01
02
03
数据分析方法
评估指标
评估报告
采用统计学方法对数据进行深入分析,如 趋势分析、控制图等,以揭示数据背后的 规律和趋势。
02
生产工艺流程介绍
工艺流程图
• 请在此处插入灭菌注射用水生产工艺流程图
工艺流程描述
原料水经过滤系统过 滤后,进入储罐进行 储存。
加热后的水通过管道 进入电解槽,进行电 解处理。
从储罐中取水,通过 管道进入加热器进行 加热。
注射液工艺验证方案

注射液工艺验证方案1.引言注射液是一种常见的给药方式,广泛应用于医院、诊所和家庭等场合。
为了确保注射液的质量和安全性,需要进行工艺验证。
本文档旨在提供一个注射液工艺验证方案,以确保生产过程中的一致性、可控性和有效性。
2.目的注射液工艺验证的主要目的是验证注射液的工艺参数和相关设备的性能是否符合规定的要求,以保证注射液的质量稳定和可控。
3.验证范围本工艺验证方案适用于所有注射液的生产过程,包括原料采购、生产操作、设备操作、质量控制和记录保存等环节。
4.验证计划4.1.验证目标本次注射液工艺验证的目标是验证生产过程中的关键工艺参数和设备性能,确保注射液的质量稳定和可控。
4.2.验证方法本次注射液工艺验证采用以下方法:•实验验证:通过实验验证关键工艺参数的合理性和可行性,例如温度、压力、pH值等。
•设备验证:通过设备的性能验证,包括设备的稳定性、准确性、可靠性等。
•质量控制验证:通过检查生产过程中的质量控制记录和相关文件,确保质量控制措施的有效性。
4.3.验证计划本次注射液工艺验证按照以下计划进行:1.准备工作:明确验证的目标、范围和方法,编制验证计划。
2.实验验证:准备相关样品和设备,进行实验验证关键工艺参数的合理性和可行性。
3.设备验证:对相关设备进行性能验证,包括稳定性、准确性和可靠性等。
4.质量控制验证:检查生产过程中的质量控制记录和相关文件,确保质量控制措施的有效性。
5.结果分析:对验证结果进行分析和总结,评估工艺参数和设备是否符合要求。
6.结论和建议:根据验证结果,给出相应的结论和建议,包括改进工艺参数、设备调整和质量控制改进等。
5.验证执行5.1.验证实验验证实验应按照验证计划进行,确保实验过程的准确性和可重复性。
实验过程中应注意以下要点:•实验条件控制:确保实验条件符合要求,例如温度、湿度、洁净度等。
•样品选择:选择代表性样品进行验证实验,确保实验结果的可靠性和代表性。
•数据收集:准确记录实验数据,包括工艺参数、设备性能和质量控制数据等。
灭菌注射用水生产--工艺验证方案

安徽XX生物化学有限公司灭菌注射用水生产工艺验证方案QY·TS·06·001-00批准日期:年月日实施日期年月日目录1.概述2.验证目的3.验证标准及要求4.验证适用范围5.验证组织6. 验证具备的条件7.验证规程7.1药液配制及过滤系统确认7.2洗烘瓶工序的确认7.3灌封工序的确认7.4灭菌、检漏工序的确认7.5灯检工序的确认7.6印字包装工序的确认8.成品质量的确认9.生产工艺验证综合与评价10、验证结果小结11、最终批准12.建议再验证的周期安徽XX生物化学有限公司灭菌注射用水模拟生产工艺验证方案编号QY·TS·06·001-00页数共19页制定人制定日期年月日修订日期年月日审核人审核日期年月日颁发部门质量管理部批准人批准日期年月日生效日期年月日分发部门质量保证部、中心化验室、生产部、小容量注射剂车间前言:验证是保证产品的生产过程和质量管理以正确的方式进行,并证明这一生产过程是准确和可靠的,并具有重现性,能保证最后得到符合质量标准的产品的一系列活动。
工艺验证也叫过程验证,是指产品加工的工艺过程的验证,通过工艺验证方案阐述如何进行验证并确定验证合格标准,验证时应说明所用的设备、关键工艺参数或运行参数的范准。
同生产记录相似,验证方案通常包括三大部分,一是指令阐述检查、校正及实验的具体内容;二是设定的标准,即检查及试验应达到什么要求;三是记录,即检查及试验应记录的内容、结果及评估的内容。
组织机构是管理的主体。
公司根据企业的具体情况及验证的实际需要成立了由总经理任组长的验证领导小组,下设各专业小组,产品工艺验证的各步骤都设定了具体的验证实施小组。
公司验证中心为验证的常设机构,验证期间承担验证秘书组的工作。
本验证方案没有明确指定检测方法的均指按照《中国药典》(2010版)所对应方法进行检测,取样方法没有明确说明的均按照车间实际操作取样的方法进行,验证所用容器具和工具一般只开列了实际生产中不用或易耗品,其他容器具和工具的处理方法按照车间实际生产中的处理进行。
【精品】用于最终灭菌药品注射剂的蒸汽灭菌工艺及验证指南
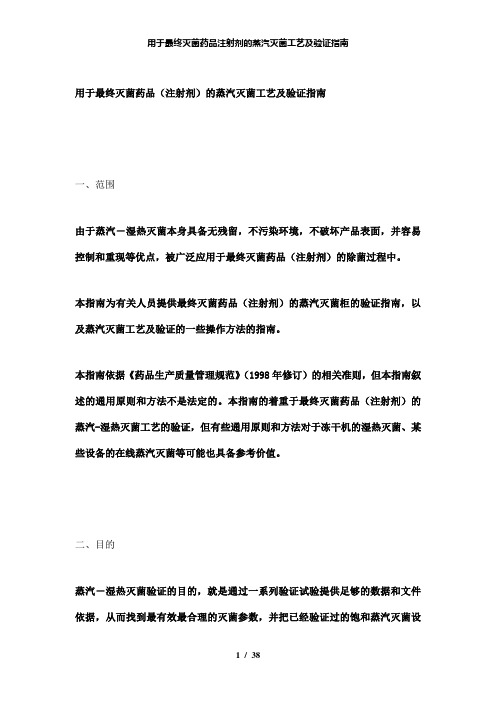
用于最终灭菌药品(注射剂)的蒸汽灭菌工艺及验证指南一、范围由于蒸汽-湿热灭菌本身具备无残留,不污染环境,不破坏产品表面,并容易控制和重现等优点,被广泛应用于最终灭菌药品(注射剂)的除菌过程中。
本指南为有关人员提供最终灭菌药品(注射剂)的蒸汽灭菌柜的验证指南,以及蒸汽灭菌工艺及验证的一些操作方法的指南。
本指南依据《药品生产质量管理规范》(1998年修订)的相关准则,但本指南叙述的通用原则和方法不是法定的。
本指南的着重于最终灭菌药品(注射剂)的蒸汽-湿热灭菌工艺的验证,但有些通用原则和方法对于冻干机的湿热灭菌、某些设备的在线蒸汽灭菌等可能也具备参考价值。
二、目的蒸汽-湿热灭菌验证的目的,就是通过一系列验证试验提供足够的数据和文件依据,从而找到最有效最合理的灭菌参数,并把已经验证过的饱和蒸汽灭菌设备和灭菌工艺参数应用到药品生产的除菌过程中去,以证明用于药品生产过程中的每一台饱和蒸汽灭菌设备都能起到灭菌的效果,并且对不同灭菌物品的灭菌过程和灭菌效果具有可靠性和重现性,即验证结果必须证明生产中所采用的灭菌过程对经过灭菌的物品能够保证残存微生物污染的概率或可能性低于百万分之一。
蒸汽-湿热灭菌周期的设计和开发与蒸汽灭菌柜的性能以及被灭菌产品的适用性有关。
蒸汽-湿热灭菌介质包含以下几种:饱和蒸汽,空气-蒸汽混合气体,过热水等等。
其中:饱和蒸汽的加热速度最快,但是对于大型的软包装产品,过热水浸泡灭菌的方法效率更高,然而在过热水灭菌法中,热量的转移很大程度上依赖于容器中介质的强制运动。
饱和蒸汽是与液体状态的水保持平衡时的水蒸汽,因此饱和蒸汽只能存在于水汽的分界线上,即温度与压力之间的关系是固定的。
灭菌效果是通过蒸汽,蒸汽-空气混合物,过热水等介质与灭菌物品的热传递或产生冷凝水的水合作用来实现的。
蒸汽-空气混合物与受压的水或蒸汽相比,单位体积所包含的热容量较低,但是,蒸汽-空气混合物作为灭菌戒指具有能够适当调整蒸汽-空气比例达到不同结果的优点。
注射液无菌检查的方法学验证方案

注射液无菌检查的方法学验证方案注射液的无菌性是医疗领域中最为重要的质量指标之一。
为了确保注射液的无菌性,需要进行方法学验证方案。
本文将介绍一种常见的注射液无菌检查方法学验证方案,确保验证结果准确可靠。
一、验证目的本验证方案旨在验证注射液无菌性检查的方法学准确性和可靠性。
通过验证,可以确保注射液无菌性检查的结果符合预期,并为其他类似检查提供参考。
二、验证对象本验证方案适用于各类注射液无菌性检查方法,包括但不限于常规培养法、膜过滤法、试管法等。
三、验证步骤1. 制定验证计划:明确验证的目标、方法和时间安排等。
2. 准备样品和试剂:收集需要验证的样品和所需试剂,并确认其质量符合要求。
3. 合理布局实验室:确保实验室环境符合无菌实验要求,避免干扰因素的存在。
4. 实验操作:a) 样品准备:按照标准操作程序,制备样品,确保操作无菌。
b) 检测方法操作:按照所选的检测方法,依次进行实验,确保操作无误。
c) 平行实验:为了验证结果的可重复性,进行平行实验,确保结果一致。
5. 结果分析:根据实验结果进行数据统计和分析,得出结论。
6. 结果确认:将验证结果与预期目标进行比较,确认验证是否合格。
7. 编写验证报告:将整个验证过程、操作方法和结果总结编写成验证报告。
四、验证要求1. 严格遵守无菌技术操作规范。
2. 注射液样品的选择应具有代表性和典型性。
3. 实验室环境应符合无菌要求,避免外界干扰。
4. 检测方法的选择应根据实际情况和需求进行。
5. 实验操作过程要规范、准确,确保每个步骤符合方法要求。
6. 结果分析要科学、客观,数据统计要准确无误。
7. 结果确认应根据验证目标和标准进行判断。
8. 验证报告要详细、完整,包括验证目的、方法、结果和结论等。
五、验证结果分析根据实验结果的分析,可以判断注射液无菌性检查方法是否准确可靠。
如果验证结果符合要求并且与预期目标一致,则说明所选的检查方法具有可靠性和精准性。
如果验证结果与预期目标不一致,则需要进一步分析原因,寻找解决方案。
灭菌注射用水生产工艺再验证方案

灭菌注射用水生产工艺再验证方案1. 简介本文档旨在提供灭菌注射用水生产工艺再验证方案的详细说明。
再验证是灭菌注射用水生产工艺的一个关键步骤,旨在确保生产工艺具有稳定性、可靠性和一致性。
通过再验证,可以保证生产出的注射用水质量符合国家相关法规和标准的要求。
2. 目的本再验证方案的目的是评估灭菌注射用水生产工艺的有效性和合规性。
通过再验证,可以确认生产工艺的符合性,并为可能发生的变更提供依据和指导。
3. 适用范围本再验证方案适用于灭菌注射用水的生产工艺,包括原材料选择、制备工艺、灭菌过程和包装过程等。
4. 方法4.1 数据收集收集当前生产工艺的数据,包括原材料的来源和质量、制备工艺的步骤和参数、灭菌过程的温度、压力和时间等。
4.2 数据分析对收集到的数据进行分析,评估工艺参数的稳定性和一致性。
分析结果应包括关键参数的变异系数、标准差和均值等。
4.3 数据解释根据数据分析结果,解释数据的合理性和可靠性。
检查是否存在异常或不符合要求的数据。
4.4 风险评估评估生产工艺可能存在的风险,并制定相应的控制措施。
风险评估应包括原材料的风险、工艺步骤的风险和灭菌过程的风险等。
4.5 再验证实施根据数据分析和风险评估的结果,制定再验证的实施方案,包括测试方法、样本数量和测试频率等。
实施再验证时,应严格按照方案的要求进行操作。
4.6 数据统计和分析对再验证的数据进行统计和分析,计算关键参数的变异系数、标准差和均值等。
与之前的数据进行对比,评估再验证结果的合格性。
5. 结果和讨论根据再验证的数据和分析结果,评估灭菌注射用水生产工艺的有效性和合规性。
讨论再验证过程中遇到的问题和挑战,提出改进建议和措施。
6. 结论通过实施再验证,我们确认灭菌注射用水生产工艺的有效性和合规性。
建议定期进行再验证,以确保工艺的稳定性和一致性。
7. 参考文献[1] 国家药典委员会. 中国药典. 北京: 化学工业出版社, 2021.[2] FDA. Guidance for Industry: Process Validation: General Principles and Practices. 2011.[3] WHO. Quality assurance of pharmaceuticals: a compendium of guidelinesand related materials. Geneva: World Health Organization, 2014.。
注射液工艺验证方案
06
附录
验证报告模板
验证方案编号
记录验证活动的唯一识别码 。
验证日期
验证活动的执行日期。
验证对象
待验证的注射液工艺流程或 设备。
验证报告模板
01
验证目的
明确验证活动的目的和预期结果 。
验证项目
02
03
验证标准
列出验证活动中执行的具体项目 和步骤。
列出用于评估验证结果的标准和 合格条件。
验证报告模板
准备资源
制定验证计划
根据验证目标,制定详细的验证计划,包括 验证方案、实施时间、人员分工等。
安排必要的设备和人力资源,确保验证过程 中的物资和场地准备就绪。
02
01
培训人员
对参与验证的人员进行培训,确保他们了解 验证的目的、方案和操作流程。
04
03
实施阶段
安装设备
根据验证计划,安装相 应的设备和仪器,确保 其正常运行。
验证时间表
制定时间表
01
根据验证计划和活动,制定合理的验证时间表,明确各项任务
的时间节点和责任人。
执行时间表
02
按照时间表的要求,严格执行各项任务,确保验证活动的顺利
进行。
调整时间表
03
在验证过程中,根据实际情况需要对时间表进行调整,以确保
验证活动的顺利进行。
03
验证实施
准备阶段
确定验证目标
明确工艺验证的具体目标,如确保工艺的稳 定性、符合质量标准等。
评估。
形成报告
撰写工艺验证报告,总结验 证过程和结果,并提出改进 建议。
报告审核与发布
组织相关人员审核报告,确 认其准确性和完整性后发布 。
XXXX注射液灭菌工艺验证方案
XXXX注射液灭菌工艺验证方案X车间XXXX药业有限公司二〇〇七年X车间XXXXXX注射液灭菌工艺验证方案编号:GY·XX·2007·01·FA起草(XXXX):年月日审核(生产部):年月日审核(质量部):年月日审核(XXXXXX):年月日批准(总工程师):年月日目录1、验证目的 (3)2、验证小组成员及职责 (3)3、验证实施 (3)4、偏差分析 (4)5、验证所用的仪器 (4)6、验证相关文件及规程 (5)7、验证结论 (5)3415689107进柜端出柜端X车间甘油果糖注射液灭菌工艺验证方案1、验证的目的为了优化XXXX注射液灭菌条件,提高无菌保证水平,保证产品质量,特进行本次验证。
2、验证小组成员及职责2.12.2职责X车间:负责验证方案、报告的起草及按验证方案进行实施生产部:负责设备的正常运行及验证用仪器的校验,验证方案、报告的审核质量部:负责验证方案、报告的审核;质检中心:负责样品的取样检验并及时出具检验报告书。
XXXXXX:负责验证方案、报告的审核,指导验证方案的实施;总工程师:负责验证方案、报告的最终审批。
2.3验证前,对验证小组成员应进行培训,并明确自己的职责。
3、验证计划在生产XXXXX注射液时,生产一批,分三柜灭菌,灭菌条件采用XXX℃,Xmin,F0:8。
灭菌岗位装灭菌车时,采用####方式,灭菌柜最冷点(出柜门左下角)不得放置灭菌车,出柜后对产品快速冷却。
灭菌过程中统计各温度探头的升温时间、降温时间、开始转灭菌时最低温度、各探头最大F0。
并将灭菌报表附到验证报告中。
灭菌结束,双倍留样。
生物指示剂试验:在灭菌前,取30瓶未压盖的半成品,每瓶中放入一支美国3M(明尼苏达矿业制造)公司的嗜热脂肪杆菌芽孢生物指示剂(孢子含量1.4×106个/支)。
压盖后,按照下图放入灭菌柜中,每柜放10支。
灭菌结束后,取出生物指示剂,做好标记,送XXXX按照《嗜热脂肪杆菌芽孢生物指示剂使用操作规程》进行培养,并出具检验报告书。
注射剂工艺验证方案
注射剂工艺验证方案注射剂是一种广泛应用于医疗领域的药物剂型,其制备过程需要经过严格的工艺验证。
工艺验证是验证制药工艺的可控性和合规性,确保药物产品的质量和安全性。
以下是一份注射剂工艺验证方案,旨在确保注射剂制备过程的可靠性和一致性。
一、验证目标:验证注射剂工艺中以下关键参数的可控性和符合要求性。
1. 每批原料的质量与规格。
2. 注射剂的配方和配比。
3. 工艺参数,如溶解时间、混合时间、搅拌速度等。
4. 温度、湿度和压力的控制。
5. 注射剂容器和包装物的适用性。
二、验证内容:1. 原料验证:采购原料时应与供应商确认其质量和规格,并进行质量评估和鉴定。
对每批原料进行进货检验,确保其符合要求。
2. 配方验证:根据药物配方书进行注射剂的配方,并确保配比准确。
验证注射剂的理化性质是否符合药物质量标准。
3. 工艺参数验证:设定合适的工艺参数,如溶解时间、混合时间、搅拌速度等,并进行验证。
在验证过程中,需确保产品的一致性和质量稳定性。
通过实验和数据分析,确定最佳工艺参数。
4. 温湿度和压力验证:验证生产环境中的温湿度和压力是否符合要求。
通过持续监测和记录,确保环境条件的稳定性。
5. 注射剂容器和包装物适用性验证:验证使用的注射剂容器(如玻璃瓶、注射器等)和包装物(如密封袋、纸箱等)是否符合药物质量标准和无菌要求。
三、验证方法:1. 原料验证:对每批原料进行进货检验,包括外观检查、质量评估和化学性质测试。
向供应商索取原料的质量证书和相关的法规文件。
2. 配方验证:通过实验室测试验证药物配方的准确性和其它性质的合规性。
根据实验结果进行必要的调整。
3. 工艺参数验证:通过样品制备和实验测试,验证每个工艺参数的影响和合适性。
使用统计方法和数据分析来确定最佳的工艺参数。
4. 温湿度和压力验证:使用仪器和设备对生产环境中的温湿度和压力进行实时监测和记录。
将数据与规定的要求进行比较,确保环境条件的稳定性。
5. 注射剂容器和包装物适用性验证:通过实验室测试和相关实验方法,验证注射剂容器和包装物的适用性。
注射剂灭菌和灭菌工艺研究及验证指导原则
注射剂灭菌和灭菌工艺研究及验证指导原则
注射剂是一种常见的药物剂型,其灭菌是保证药品质量和安全的重要
环节。
注射剂灭菌工艺研究及验证指导原则是指在注射剂生产过程中,对灭菌工艺进行研究和验证,以确保注射剂的灭菌效果符合要求,从
而保证药品的质量和安全。
注射剂灭菌工艺研究及验证指导原则包括以下几个方面:
一、灭菌工艺研究
灭菌工艺研究是指对注射剂灭菌工艺进行研究,以确定最佳的灭菌工
艺参数。
灭菌工艺参数包括灭菌温度、灭菌时间、灭菌压力、灭菌介
质等。
在灭菌工艺研究中,需要进行灭菌效果试验,以确定最佳的灭
菌工艺参数。
二、灭菌工艺验证
灭菌工艺验证是指对注射剂灭菌工艺进行验证,以确保灭菌效果符合
要求。
灭菌工艺验证需要进行灭菌效果试验和生物指示剂试验。
灭菌
效果试验是指对注射剂进行灭菌处理后,检测灭菌效果的试验。
生物
指示剂试验是指使用生物指示剂对注射剂进行灭菌处理,以检测灭菌
效果的试验。
三、灭菌工艺指导原则
灭菌工艺指导原则是指对注射剂灭菌工艺进行指导的原则。
灭菌工艺指导原则包括以下几个方面:
1. 灭菌工艺应符合国家相关标准和规定。
2. 灭菌工艺应根据注射剂的特点进行研究和验证。
3. 灭菌工艺应确保灭菌效果符合要求。
4. 灭菌工艺应定期进行验证,以确保灭菌效果符合要求。
总之,注射剂灭菌工艺研究及验证指导原则是保证注射剂质量和安全的重要环节。
在注射剂生产过程中,需要严格按照灭菌工艺研究及验证指导原则进行操作,以确保注射剂的灭菌效果符合要求,从而保证药品的质量和安全。
- 1、下载文档前请自行甄别文档内容的完整性,平台不提供额外的编辑、内容补充、找答案等附加服务。
- 2、"仅部分预览"的文档,不可在线预览部分如存在完整性等问题,可反馈申请退款(可完整预览的文档不适用该条件!)。
- 3、如文档侵犯您的权益,请联系客服反馈,我们会尽快为您处理(人工客服工作时间:9:00-18:30)。
A注射液灭菌工艺验证方案公司名称目录1.概述2.验证目的3.验证依据4.支持文件5.验证小组成员及职责6. 生物指示剂验证试验方法7.验证合格标准7.1A注射液生产全过程部分微生物污染监控措施7.2灭菌釜技术要求7.3湿热灭菌工艺的生物学验证技术要求7.3.1沸腾试验阴性7.3.2沸腾试验阳性8.湿热灭菌验证操作步骤8.1 X.PSM.B型旋转水浴式灭菌釜确认8.1.1概述8.1.2运行确认8.1.3空载热分布8.1.4满载热分布8.1.5热穿透试验8.1.6升温速率试验8.2生物指示剂验证(挑战性试验)9.取样计划及样品编号10.验证结果、分析及评价10.1 A注射液工艺优化、偏差处理及整改措施汇总10.2 A注射液灭菌前药液微生物限度警戒线及行动线的确认11.验证培训12.验证合格证书13.附件附件1A注射液无菌保证与国际GMP差距附件2 生物指示剂制备方法附件3 A注射液灭菌工艺验证预试验取样计划(系列)附件4 A注射液灭菌前不同工艺环节的药液生物负荷及沸腾试验调查总结附件5 A注射液湿热灭菌工艺验证待确认修改的相关SOP目录附件6 A注射液湿热灭菌工艺验证待建立相关SOP目录14.附录:附录1 A注射液射液灭菌前药液生物负荷及无菌保证值汇总表附录2 灭菌釜运行测试记录附录3 空载热分布汇总记录附录4 满载热分布汇总记录附录5升温速率试验记录附录6 A注射液灭菌工艺微生物学验证记录附录7 A注射液灭菌工艺验证取样计划及项目编号附录8 A注射液灭菌工艺验证取样记录附录9 偏差处理记录附录10验证培训记录附录11验证合格证书1.概述:中国药典(05版)要求无菌制剂必须满足SAL≤10-6无菌保证水平[可用公式(F0- D污121℃×lgN)/D污121℃≥6表示,见 C-P216,3-14]。
A注射液采用湿热终端灭菌,其灭菌程序参数设定为 116℃,30min(经计算所得F0=9.48,实测F0值在10-14之间,2009年灭菌釜验证数据),属于残存概率灭菌范围(8≤F0<12)。
其最终产品的无菌质量取决于灭菌前产品中生物负荷、孢子耐热性及灭菌工艺的杀灭效果,所以产品应采用控制灭菌前药液的含菌量(生物负荷)的灭菌工艺。
灭菌制剂的无菌保证水平(SAL, sterility assurance level)是指灭菌后制剂中微生物的残存概率。
任何灭菌工艺均应当能使产品中的污染菌含量下降至一个菌后,再下降6个对数单位,才能保证产品经过灭菌后其中非无菌品概率不超过1/百万(即SAL ≤10-6)。
由于无菌检查的局限性,灭菌后含有残活微生物的样品往往难以被抽检到。
因此,灭菌制剂的无菌保证不能仅仅依赖于最终产品的无菌检查结果,而必须依靠生产过程中采用合格的灭菌工艺、严格的GMP管理。
对比国际GMP,A注射液无菌保证存在缺陷及整改措施、整改计划如《A注射液无菌保证与国际GMP差距》(附件1)所示。
本次验证克服A注射液以往的灭菌工艺验证,尚未能够提供产品满足SAL≤10-6无菌保证水平的证据的缺陷。
为确保每批产品无菌保证水平达到药典要求,解除潜在的产品质量安全风险、确保临床安全用药,特设计重新进行A注射液灭菌工艺验证。
通过灭菌工艺验证寻找影响微生物污染的关键质量控制点,采取合理、科学的纠偏措施,达到灭菌工艺能够稳定控制灭菌前药液的含菌量(生物负荷)的效果,将各种纠偏措施形成书面SOP并在正常生产时实施操作,使灭菌前药液生物负荷值处于控制水平线以下,为证实确保成品SAL ≤10-6提供验证证据。
作为本次湿热灭菌验证的预试验:(1)已设计与生产同步进行了A注射液灭菌前药液含菌量等检测方法学确认,详见《A注射液灭菌前药液含菌量等检测方法学确认报告》。
(2)已设计与生产同步进行了预试验《A注射液灭菌前不同工艺环节药液生物负荷及沸腾试验调查》(附件3),按照《A注射液灭菌工艺验证预试验取样计划》(系列,附件4)进行取样检测;调查结果详见《A注射液灭菌前不同阶段的药液生物负荷及沸腾试验调查总结》(附件5)。
(3)已设计与生产同步进行了《小容量注射液车间HVAC系统再验证》,重点:增加对洁净区关键区域如配制、灌装、百级层流罩下的动态监控(浮游菌、沉降菌、悬浮粒子),确认车间洁净区生产环境动态变化下对灭菌前药液生物负荷的影响规律。
已将欧盟GMP无菌制剂生产要求的洁净区“动态”验证技术要求写入该验证方案。
(4)已设计与生产同步进行了《洁净氮气系统再验证》,重点:确认灌装直接接触药液的洁净惰性气体的洁净度符合要求;监控灌装前后(最差状况)的洁净惰性气体微生物负荷。
因此,本次验证区分为三部分:第一部分:确认现有硬件条件下,A注射液灭菌前不同阶段的药液生物负荷及沸腾试验的规律,分析、确认关键质量控制点,在不影响产品其他质量指标的前提下,进行硬件或者工艺参数或者人员操作方法的缺陷分析、改造及纠偏,并确认和评价其纠偏措施的整改效果,以使产品灭菌前药液生物负荷实现稳定可控。
第二部分:对灭菌釜性能进行再确认(一年一次,由制造商进行)。
第三部分:对A注射液进行湿热灭菌工艺微生物学验证,包括:——选择适宜的生物指示剂进行挑战性试验。
——建立、确认产品无菌保证的相关企业内部控制标准(如灭菌前药液生物负荷警戒标准、纠偏标准,沸腾试验等),并通过验证形成日常监控的SOP。
——发现污染菌耐热性大于生物指示剂时,分离污染菌孢子,制备浓度适宜的生物指示剂,再次重复进行验证。
2.验证目的2.1确认灭菌釜性能是否仍然符合技术要求和工艺目标。
2.2选择适宜的生物指示剂,在灭菌釜各冷点进行最差状况的挑战性试验。
2.3对预试验监测结果进行关键质量控制点的分析,确认适宜的纠偏整改措施,优化工艺条件、加强过程控制。
2.4确认在现有灭菌工艺条件下,有关产品无菌保证的相关企业内部控制标准(如灭菌前药液生物负荷警戒标准、纠偏标准,沸腾试验等),形成SOP,进行日常监控。
2.5确认原辅料质量标准、洁净区环境、工艺用水等的微生物监控计划(检测频率及限度值)能否符合产品无菌保证和质量属性,确认设备清洁程序、维修保养程序、灭菌操作工序等是否需要修订。
3.验证依据及参考资料::《现代医药工业微生物实验室质量管理与验证技术》,潘友文,2004年4.支持文件:X.PSM.B540型旋转式水浴灭菌器操作程序——文件受控号X.PSM.B540型旋转水浴灭菌釜维修保养程序——文件受控号A注射液半成品检验操作程序——文件受控号A注射液检验操作程序——文件受控号无菌检查法检验操作程序——文件受控号微生物限度检查法检验操作程序——文件受控号取样管理规程——文件受控号《灭菌釜性能再确认报告》(当年度)待验证修订/确认的GMP文件——见附件5,A注射液湿热灭菌工艺验证待修改相关程序目录(如《配制灌注系统清洗、消毒程序》,《洁净区环境监控管理规程》,《灭菌釜冷却水质量标准》等)《A注射液灭菌前药液含菌量检查方法等确认报告》为本次验证制定的程序文件目录:5.验证小组成员及职责:6. 生物指示剂验证试验方法6.1生物指示剂的选择:由于A注射液灭菌程序为116℃×30min,属于残存概率灭菌范围(8≤F0<12),在湿热灭菌工艺验证预实验沸腾试验阴性的前提下,拟使用市售标准生物指示剂。
生物指示剂应具备孢子稳定、耐热性强于被灭菌物品中常见的污染菌、系非致病菌、易于培养等特征。
本次验证用标准生物指示剂(BI)参数:菌种:嗜热脂肪杆菌ATCC7953。
DB:1.7,标准生物指示剂在121℃时下降一个对数单位所需要的时间,分钟。
浓度:103cfu/支。
批号:1001111。
有效期:一年。
供应商:上海鸿雍生物科技有限公司。
F 0值:F≥8。
存活时间:121℃饱和蒸气下存活时间不少于3.9分钟。
死亡时间:121℃饱和蒸气下死亡时间不少于19分钟。
标定结果:在药液D值为0.9。
6.2生物指示剂的使用方法:应将挑战菌接种到药液,接种BI后的安瓿灭封后(F0值8≤X<12)放置冷点处(不少于20个),经最低灭菌程序后,应无菌检测全部呈阴性,详见A注射液灭菌工艺微生物学验证记录。
7.验证合格标准7.1A注射液生产全过程部分微生物污染监控措施:A注射液湿热灭菌生产全过程部分微生物污染监控措施如表1所示:表1:7.2灭菌釜技术要求:如表2所示,详见《灭菌釜性能再确认报告》(当年度)。
表2:7.3湿热灭菌工艺的生物学验证技术要求:7.3.1连续进行五批次产品在设定条件下灭菌后,应: 灭菌前药液生物负荷值: 警戒限(CFU/20ml )≤50纠偏限(CFU/20ml )≤100(即lgN 0≤2) 沸腾试验:阴性或阳性。
阳性时应检测污染菌D A 值,污染菌D A 值应小于标准生物指示剂D BI 值。
接种挑战菌的药液(BI )检测(验证期间):20支/釜,应全部阴性。
无菌保证值:SAL ≤10-6(或者SAL ≥6)。
7.3.2 SAL 判断或计算方法如表所示:其中:SAL :无菌保证值。
-lg :微生物存活概率。
lgN 0:药液灭菌前污染菌污染水平。
D A :灭菌前药液的污染菌芽孢在121℃时下降一个lg 值所需要的时间,分钟;沸腾试验阴性时取0.5计算,沸腾试验阳性时按照所测得的污染菌D A 值计算。
F 0:产品设定的F 0值(也可以使用实际测得的F 0)。
[计算]假设:N0=1000个孢子数,沸腾实验检测阴性,DA=0.5,F=9.48,求SAL?∵SAL= (F0/DA-lgN)=(9.48/0.5-3)=15.96>6,∴产品准予放行。
沸腾试验阳性时,DA取实际检测值代入上式计算即可。
7.3.3取样细则:(1)取灌装前、中、终端各3支样品,分别编号为批号+A1(3支相同,前端)或批号+A2(3支相同,中端)或批号+A3(3支相同,终端);取样人员应在安瓿上写明标记。
(2)灌装前端取样灌装第1、2、3支密封后药液;灌装中端请取样人员与工段长或灌封人员共同判断并连续灌封取样;灌装终端取连续灌封的最后3支药。
(3)取样送样应在前、中、终端各3支标记样品各自临近灭菌前取出,迅速送QC生测人员,按照《A注射液灭菌前药液含菌量检查及污染菌的耐热性检查操作程序》(ZKSN-23-9)进行检验,检测结果应记入A注射液射液灭菌前药液生物负荷及无菌保证值汇总表(附录1)。
(4)取样人员应逐项填写取样记录,并取样完毕递交车间工艺员。
7.3.4警戒与纠偏:当灭菌前药液生物负荷值超过警戒线时,应对主要污染菌作鉴别;含菌量一旦超过纠偏限度,立即通知车间,调查偏差原因,并采取相应纠偏措施,并再次进行连续五次的合格验证。
当沸腾试验阳性时,需要对阳性菌做鉴别;如果阳性菌系非芽孢杆菌,则可判为试验过程中的污染即假阳性;如阳性菌为芽孢杆菌,则应对污染菌做定量沸腾试验测定该污染菌的相对耐热性(DA)。